Abstract
This master's work is not completed yet. Final completion: May 2020. The full text of the work and materials on the topic can be obtained from the author or his head after this date.
Content
- Introduction
- 1. Theme urgency
- 2. Goal and tasks of the research
- 3. Approach to the implementation of a system for applying a pattern to a PC surface based on a two-coordinate system of CD drives
- 3.1 Analysis of the methods of preparation for subtractive production of PCB
- 3.2 Design features of the device for drawing
- Conclusion
- References
Introduction
Currently, in most cases, for the installation of electronic devices and blocks of computer technology, a printed circuit with a minimum number of conductors is used constructively. To use surface mounting based on SMD elements, high accuracy requirements are imposed on printed circuit boards, but in some cases it is possible to reduce the number of PCB layers to one-sided or two-sided. When designing such printed circuit boards, the ability to quickly manufacture prototypes of circuit boards for research and tuning circuits with the possibility of obtaining them in the laboratory at low cost is of great importance.
Thus, the urgent task of creating a methodology for building systems that allow you to quickly design nodes with printed wiring to study the implementation of individual functions of computing devices.
1. Theme urgency
In this paper, we analyze various approaches to the creation of software preparation systems for circuits with a limited number of elements. It is justified to build a system for applying a PCB drawing on the basis of typical hardware nodes of peripheral equipment of personal computers. A hierarchical system based on a standard PC and an Arduino control controller is proposed as the software basis for control.
The construction of systems based on standard widespread hardware elements is relevant from the point of view of ensuring their widespread adoption in most scientific laboratories involved in the design and study of computer hardware nodes and their peripheral equipment. The low cost and availability of all components of the system allows you to effectively use them as part of the educational process for the training of circuit engineers.
2. Goal and tasks of the research
Development of a methodology for constructing PCB drawing application systems for medium-complexity computing equipment circuits is the goal of research.
Main tasks of the research:
- Analysis of existing solutions for automating the receipt of PCB drawings.
- Assessing the optimality of building drawing systems taking into account the economic factor and minimizing the time to create a system.
- Search and identification of structural and hardware solutions to the problem of constructively obtaining PCB drawings.
- Analysis of the parametric capabilities of the drawing system based on the hardware components of CD drives.
- Development of a layout for studying the characteristics of the drawing system based on the hardware components of CD drives.
Research object: hardware implementation of devices based on components of a CD drive.
Research subject: language means for automating the preparation of drawings of printed circuit boards, as well as hardware and software for physical drawing of a pattern on the surface of printed circuit boards.
As part of the master's work, it is planned to obtain relevant scientific results in the following areas:
- Analysis of language tools with the development of methods for preparing PCB drawings for implementation as part of a system based on unified computer components.
- Determining the applicability of the proposed system for the preparation and application of PCB drawings, taking into account their low cost and implementation on industrially manufactured hardware components.
- A study of the characteristics of the PCB drawing system built on the basis of a PC and an Arduino microcontroller.
For experimental evaluation of the theoretical results obtained and the formation of the foundation for subsequent research, it is planned to develop experimental models based on the hardware based mechanics of CD-ROM drives as practical results with the following properties:
- Using the instrumental language for constructing the coordinate pattern of a PCB electronic circuit.
- Prompt transfer of the coordinate pattern to the environment of the control controller.
- Providing positioning of PCB blanks for double-sided mounting.
- Obtaining on the surface of the PCB a picture with parameters sufficient for various types of installation of the microchip implementation of the electronic component.
3.Approach to the implementation of a system for applying a pattern to a PC surface based on a two-coordinate system of CD drives
3.1 analysis of the methods of preparation for subtractive production of PCB
The standard plotter has large dimensions of the workspace, but this is not required for pilot production. The main disadvantage is the difficulty in positioning the foil blank on the plotter plane without interfering with the plotter design, and this in most cases will lead to a violation of the possibility of further using it as a standard plotter.
It is rational to design a specialized device for the operational preparation of software for experimental radio engineering devices or computing units of specialized monitoring and control systems having small dimensions. This will allow for the design, debugging and configuration to use a modular approach, that is, separate functional units constructively placed on separate software. In the process of research, refinement and tuning, such dedicated structural and functional modules are easy to replace without changing the overall design of the designed device.
The developed device should have a sufficiently small size, have high reliability. To implement a certain accuracy class for manufacturing PCB, a writing device with a pen thickness sufficient to apply conductors with a minimum width should be used. By changing the thickness of the pen of the writing device, it is possible to adjust the accuracy of the manufacture of the pattern of conductors of the PCB and provide flexibility in the choice of class.
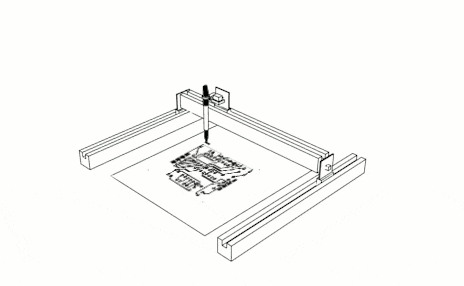
Figure 4 — Drawing a picture of the conductors of a printed circuit board on a CNC plotter
(animation, 16 frames, 10 reps, 97,9 KB)
3.2 Design features of the device for drawing
The basic requirements for creating a device for applying patterns of conductors to the surface of workpieces for chemical or electrochemical production of PCB:
- maximum utilization of finished assemblies;
- forming a common design in the laboratory;
- device parameters for drawing accuracy must satisfy the selected accuracy class;
- receiving positive and negative drawings of conductors of designed PCB;
- providing the ability to re-apply the drawing with positioning over the previously obtained image of the conductors of the printed circuit boards.
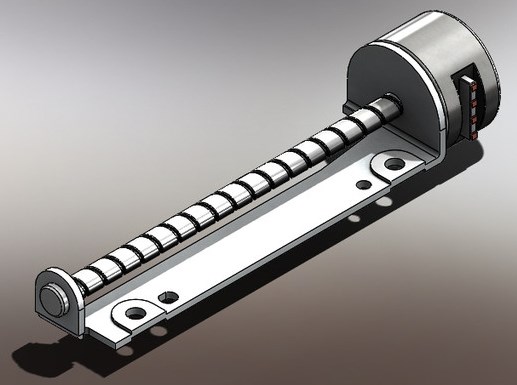
Figure 5 — CD-ROM drive stepper motor
All these requirements can be provided by a device in the form of a two-coordinate computer-controlled plotter with a special design for securing blanks and using various drawing devices. According to the requirement to make the most of ready-made structural units, the motors for the device will be taken from CD-ROM drives that are not relevant today (Fig. 5).
The hardware of the system will be represented by the Arduino platform with extensions and physical modules. Arduino is a tool for designing electronic devices that interact more closely with their physical environment than standard personal computers. In this work, we will use the version of the Arduino UNO platform - the most popular version of the Arduino base platform with a USB interface and the ability to connect a wide variety of expansion cards. This platform is designed for physical computing with open source software, built on a simple PCB with a modern environment for software development. [6].
Arduino uses an Atmega328 microcontroller, which has 32 KB of flash memory [7]. This will be quite enough to carry out the tasks assigned to the platform - performing the functions of the CNC host.
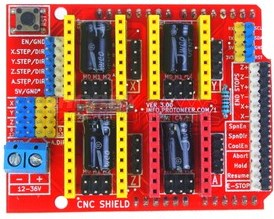
Figure 6 — Arduino CNC Shield v3
Arduino microcontrollers are distinguished by pre-needled therein loader. Using this loader, the user downloads a program to the microcontroller without using conventional hardware programmers and connects to your computer via the USB interface [8].
Motor control will be through the A4988 model stepper motor driver. The CNC Shield v3 expander board will help connect the driver to the Arduino Uno board (Fig. 6). CNC Shield has four slots for connecting four motor drivers[9]. The slots marked in yellow are responsible for the X, Y, Z axes, the red slot for the A axis. A axis can duplicate one of the X, Y, Z axes using an additional motor and driver. That is, the input signal comes the same, and the drivers and stepper motors are different, but they move the same.
Conclusions
The design of hardware for elements of calculators and peripheral equipment requires a number of experimental studies of the proposed circuit solutions. Efficiency in preparing the hardware environment of research stands is the key to ensuring high design efficiency, reducing timelines and increasing the reliability of design decisions.
The master's thesis is devoted to the urgent scientific task of creating hardware and software environments for the operational creation of research stands for computer hardware. In the framework of the studies performed:
- The analysis and justification of the choice of instrumental language environment for the preparation of coordinate drawings PCB;
- The structure of a two-level computing environment for the automation system for applying drawings on the surface of the software has been developed;
- The choice of the composition and characteristics of the unified hardware components of the module for physical drawing of the drawing on the surface is substantiated;
- A workpiece positioning system was developed as part of the drawing module on the surface;
- Experimental studies of a pilot plant for automating the application of a PCB drawing were carried out.
Further research focuses on the following aspects:
- Qualitative improvement of the proposed approach to drawing using various types of writing instruments.
- Development of tools to improve the efficiency and accuracy of positioning workpieces in a device using optical matrices.
- Using a multi-pen writing tool.
References
- Брусницына, Л. А. Технология изготовления печатных плат : [учеб. пособие] / Л. А. Брусницына, Е. И. Степановских ; [науч. ред. В. Ф. Марков]; М-во образования и науки Рос. Федерации, Урал. федер. ун-т. — Екатеринбург : Изд-во Урал. ун-та, 2015.
- Галецкий Ф., Лейтес И., Петров Л. Разработка технологий изготовления высокоплотных печатных плат [Электронный ресурс] // РТС Инжиниринг : сайт. URL: www.rts-engineering.ru/Plat/...
- Капица М. Активация поверхности диэлектрика // Технологии электронной промышленности. 2005. № 5. С. 22–25.
- Барановский И. Современный дизайн и технологии печатных плат: вопрос-ответ. Финишные покрытия плат. Особенности применения // CHIP NEWS, Украина. 2009. № 4 (84), май.
- Федулова А. А., Котов Е. П., Явич Э. Р. Химические процессы в технологии изготовления плат. М. : Радио и связь, 1981.
- Happy Holden. The HDI Handbook. First Edition, 2009.
- Методы изготовления печатных плат. [Электронный ресурс]. – URL: https://pcbdesigner.ru/pcb/....
- Захарченко К.С. Система автоматического управления оптимальным температурным режимом в помещении с удаленным заданием параметров / Захарченко К.С., Достлев Ю.С.// Материалы IX Международная научно-техническая конференция
Информатика, управляющие системы, математическое и компьютерное моделирование
(ИУСМКМ-2018). — Донецк: ДОННТУ, 2018. — с. 424-427 - Официальный сайт Ардуино, [Электронный ресурс]. – URL: arduino.ru/About