Abstract
Content
- Introduction
- 1. Theme urgency
- 2. Purpose and objectives of the study, planned results
- 3. Research and development overview
- 3.1 General information about concrete
- 3.2 Fiber, its varieties and use as an additive
- Conclusions
- List of sources
Introduction
At the present stage of development of building technologies, one of the most promising materials is fiber-reinforced concrete (Fig. 1). Given the novelty and promising nature of this building material, you can indicate a large number of possibilities for its use.
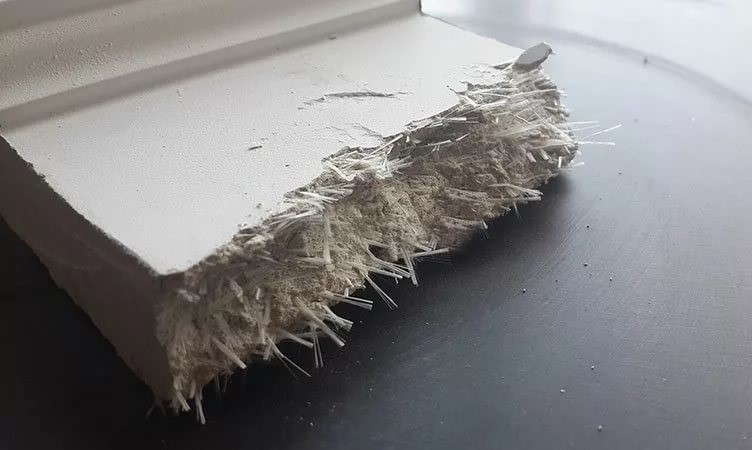
Figure 1 – Fiber-reinforced concrete
Fiber-reinforced concrete belongs to a new generation of concretes that have emerged as a result of the development of innovative technologies that are gradually replacing the existing types. This element is a type of fine-grained cement concrete, in which the fibers are evenly distributed, serving as a reinforcing component.
1. Theme urgency
The relevance of the topic is due to the fact that the use of fiber in concrete provides higher concrete characteristics in terms of such characteristics as tensile strength, bending, shear strength, impact and fatigue strength, crack resistance, frost resistance, water resistance, heat resistance and fire resistance. Such properties contribute to the possibility of separating fiber-reinforced concrete into an independent group of structural materials, differing in design features and properties.
2. Goal and tasks of the research
The purpose of the work is to determine the influence of various types of fibers on the strength characteristics of fiber-reinforced concrete.
The main tasks are to determine the optimal amount of fiber that needs to be added to concrete to improve its strength characteristics.
3. Research and development overview
3.1 General information about concrete
Concrete is an artificial stone material obtained as a result of hardening of a rationally selected, thoroughly mixed and compacted mixture of a mineral or organic binder with water, small and large aggregates, taken in certain proportions. Before hardening, this mixture is called concrete mix (Fig. 2).
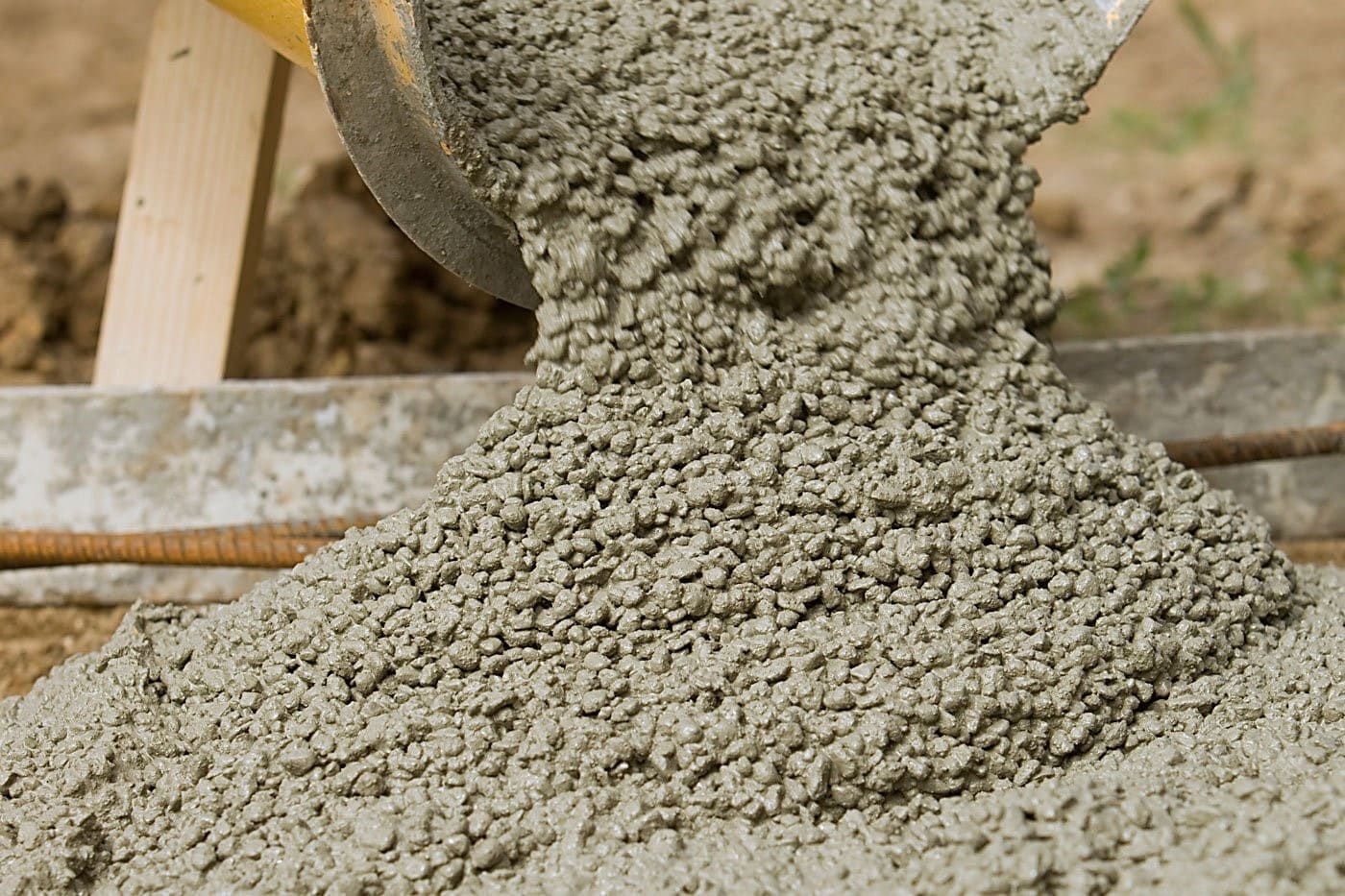
Figure 2 – Concrete mix
Constructions made of inorganic binders (cements, lime, gypsum binders) are mainly used in construction. These concretes are closed with water. Inorganic binders and water are the active components of concrete. As a result of the reaction between them, a cement stone is formed, which binds the aggregate grains into a single monolith.
Aggregates do not chemically interact with concrete components (except for silicate concrete obtained by autoclave treatment), so aggregates are also called inert materials. They significantly affect the structure and properties of concrete, playing the role of skeleton, skeleton, significantly reduce the deformation of concrete during hardening and under the influence of load and the environment. Mostly local rocks and production wastes (slags, etc.) are used as aggregates.
The use of these cheap aggregates reduces the cost of concrete, because aggregates and water make up 85-90%, and cement - 10-15% by weight of concrete. To reduce the density of concrete and improve its thermal properties, artificial (expanded clay, aggloporite, thermosite, granulated slag, expanded vermiculite, perlite, polystyrene, etc.) and natural (tuff, pumice, shell rock, etc.) porous aggregates are used.
To regulate the properties of concrete and concrete mix, various chemical additives and active mineral components are introduced into their composition, which accelerate or slow down the setting of concrete mix, make it more plastic and workable, accelerate concrete hardening, increase its strength and frost resistance and other properties.
Concretes on mineral binders are capillary-porous bodies, the structure and properties of which are significantly influenced by both the internal processes of interaction of concrete components and the interaction of the environment. With increasing age of concrete, its strength, density, resistance to environmental influences increase. On organic binders (bitumen, synthetic polymer resins, etc.) the concrete mixture is obtained without the introduction of water, which provides high density and impermeability of concrete.
Concrete is a brittle material: its compressive strength is several times higher than its tensile strength. To absorb tensile stresses, concrete is reinforced with steel rods to obtain reinforced concrete.
In reinforced concrete, the reinforcement is placed so that it receives tensile stress, and compressive stresses are transmitted to the concrete. The joint work of reinforcement and concrete is due to good adhesion between them and approximately the same temperature coefficients of linear expansion. Concrete protects the reinforcement from corrosion while providing a certain amount of protective layer of concrete.
The use of chemical additives and various dispersed mineral components in combination with the appropriate selection of the composition of concrete allows you to effectively manage its technology at all stages and get concrete of a given structure and properties.
3.2 Fiber, its varieties and use as an additive
Concrete has specific characteristics that define it as a brittle substance with a heterogeneous structure. The value of the limit deformation is much lower than, for example, glass, steel or polymer composites.
To increase the elasticity, it is necessary to use fibrous additives (fibers) as microreinforcement for concrete structures. This feature is widely used in the technology of construction processes, such as the preparation of cement mixtures, the manufacture of high-strength materials, etc.
Fiber is a material in the form of pieces of thread or narrow strips of organic or inorganic origin. The mechanical characteristics of fiber concrete depend on the amount and arrangement of fibers in the solution.
The method of dispersed concrete reinforcement involves arbitrary and directional orientation of the fibers. Directed involves the use of thin continuous threads, woven and nonwoven nets, plaits and other similar materials. Arbitrary (free) occurs when using rolled materials in the form of mats, canvases, veils.
Metal and non-metallic threads of different lengths and cross sections are used as fibers.
In terms of design, the greatest effect is obtained from the use of steel fibers, the modulus of deformability of which is 6 times higher than that of concrete.
The use of polypropylene can reduce the risk of cracking by 60-90% during plastic shrinkage of mixtures.
Fiberglass has low alkali resistance and is used only for pre-reinforcement in the manufacture of gypsum products or wall blocks of porous concrete.
Basalt fiber is resistant to alkaline processes. The modulus of elasticity is 15-20% higher than that of glass fibers.
Asbestos fibers are neutral to the aggressive effects of cement, they are characterized by high strength and fire resistance.
Rational choice of additives for concrete reinforcement allows to obtain products that are resistant to mechanical loads.
The introduction of modifiers in concrete in the form of fibers helps to improve performance and performance. The mechanical properties of fiber-reinforced composite materials depend on the type of additive, the volume and size of the elements.
Conclusions
The use of fiber increases the reliability of the structure by 90%, provided that the addition of good quality plasticizers.
Thanks to polypropylene fiber, the plasticity of concrete becomes several times greater. This characteristic is inherent not only in the solution, but also in the finished hardened structure of it, it can withstand shocks and suppress vibrations. This characteristic of the material is used in military facilities and in heavy industry. Fiberglass structures are excellent earthquake resistance and high explosion resistance.
Surface abrasion is a very important characteristic. Very fast wear is inherent in those concrete designs which are used in rather aggressive environment. For this reason, dams, reservoirs and water barriers are often constructed using a mixture of cement and fiber.
Also, this material has high frost resistance, and this quality is taken over by concrete. At the same time, its resistance to sub-zero temperatures becomes several times higher.
If the solution with the addition of polypropylene fiber is mixed according to the technology, the adhesion of the resulting concrete to the surface will be much improved and it will be easier to level it.
References
- Исследования применения фибробетона в строительстве [Электронный ресурс] – Режим доступа:https://elibrary.ru...
- Ежов В. Б. Технология бетона, строительных изделий и конструкций/ В. Б. Ежов – Е.: УрФУ, 2014 – 205 с.
- Фибра для бетона: виды, преимущества, применение [Электронный ресурс] - Режим доступа:https://1beton.info...
- Руководство «Фибробетон». - Австрийская ассоциация бетона и строительных технологий, 2008. – 40 с.
- EN 14889-1. Международный стандарт. Волокна для бетона - Часть 1: Стальные волокна - Определения, технические требования и соответствие. - М.: Госстандарт, 2009. – 41 с.
- EN 14889-2. Международный стандарт. Волокна для бетона - Часть 2: Полимерные волокна - Определения, технические требования и соответствие. – М.: Госстандарт, 2009. – 40 с.
- Курбатов Л.Г. Об эффективности бетонов, армированных стальными фибрами/ Л.Г. Курбатов, Ф.Н. Рабинович. // Бетон и железобетон. — 1980. — № 3. - С. 6-7