Abstract
Content
- Introduction
- 1. Theme urgency
- 2. Goal and tasks of the research
- 3. Technologies for producing piezoceramic materials
- 3.1 Co–deposition method
- 3.2 Semi–ceramic technology
- 3.3 Ceramic technology
- 4. Comparative analysis of methods for obtaining piezoceramic materials
- Conclusion
- References
Introduction
Piezoceramics is one of the most promising materials of the 21st century. The reason for this view is that the remarkable properties inherent in piezoelectric ceramics are still not fully demanded by science, technology and technology. Piezoelectric ceramics is a hard, chemically inert material that is insensitive to moisture and other atmospheric influences.
Among the numerous technological factors influencing the production process of piezoceramic materials is the dispersion of the charge. Obtaining materials with ultrafine dispersion (consisting of particles with a size of several micrometers and less) is very important, since many characteristics of materials depend on the degree of grinding. Nanotechnology is considered in relation to the production of fundamentally new or to the multiple improvement of the consumer properties of existing materials for structural and functional purposes.
1. Theme urgency
Obtaining materials with ultrafine dispersion is very important, since many characteristics of materials, for example, the synthesis temperature, depend on the degree of grinding. Thus, for the materials of the LZT system, a decrease in the synthesis temperature is an important factor, if we take into account the fact that the volatility of lead increases significantly with increasing temperature. To date, in the literature, questions about the effect of dispersion on technological parameters and properties of piezomaterials are not fully covered. Carrying out research on the study of the size effect in piezoceramic materials, along with their practical value, are extremely relevant.
2. Goal and tasks of the research
The aim of the study is to study the effect of the dispersed composition of the charge on the technological parameters of production when obtaining materials of zirconate - lead titanate using various technologies.
Main tasks of the research:
- Consideration various technologies for obtaining piezoceramic materials and conducting their comparative analysis.
- Determine the influence of methods for obtaining a multicomponent charge on the formation of the perovskite structure.
- To investigate the dependence of the dispersity of the charge and synthesized powders — material properties.
- Search for ways to intensify the production of powders using ceramic technology.
- Summarize the results.
3. Technologies for producing piezoceramic materials
The fundamental difference between existing technologies lies in different methods of preparing a mixture of initial components: from solutions - co-precipitation, spray drying of solutions, cryochemical technology; from solutions and oxides - semi-ceramic technology; from a mechanically prepared mixture of oxides and carbonates - ceramic technology and others [1, 2].
3.1 Co–deposition method
The co-precipitation method is based on the interaction of alkaline agents with aqueous solutions of salts containing cations of different metals in the ratio that must be obtained in the finished material (figure 1) [3]. Solutions of alkalis, soda, ammonium hydroxide and its mixtures with ammonium carbonate, etc. are used as precipitants. The deposition conditions are selected so as to ensure the quantitative separation of metal compounds from aqueous solutions. The sparingly soluble compounds formed during this process are separated from the mother liquor and subjected to heat treatment.
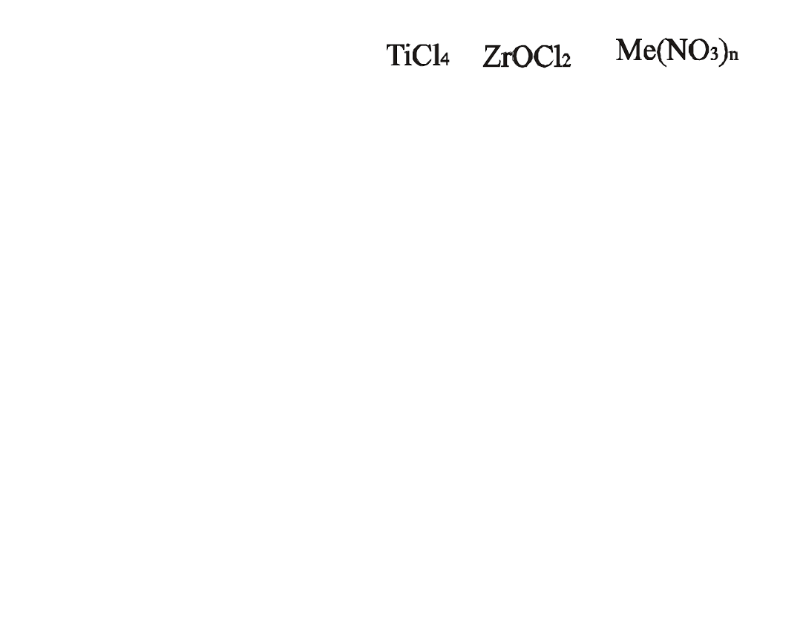
Figure 1 – Scheme of an industrial plant for obtaining materials using co-deposition technology:
1,2,3,4 — collections of solutions; 5,6,7,8 — automatic dispensers; 9 — mixers of solutions; 10 — pump; 11 — pressure tank;
12 — collection of precipitating solution; 13 — precipitator reactor; 14 — drum vacuum filter 15 — for synthesis; 16 — precipitator; 17 — mixture of solutions
3.2 Semi–ceramic technology
The semi-ceramic method simplifies the precipitation and homogenized paste steps inherent in the coprecipitation method. There are three ways of separating compounds from solutions into oxides and carbonates:
— by dewatering suspensions (by evaporation or spray drying);
— hydrolysis of alcoholates;
— by interacting with the precipitant.
The first two methods have not received industrial use. They include, as necessary steps, the steps of evaporation, spray drying or hydrolysis of alcoholates. Such processes have a number of disadvantages that complicate their implementation in industrial production.
The third variant of the method has gained the greatest development - the isolation of compounds from solutions into the solid phase by interaction with a precipitant. [4].
3.3 Ceramic technology
The technological scheme for obtaining piezoceramic materials from a mechanically prepared mixture of oxides and carbonates (Figure 2) includes the following stages of the process: selection and preparation of raw materials; weighing the starting components and preparing the mixture for synthesis; high temperature synthesis; crushing the compounds obtained in the form of cakes; grinding and separation of powders from magnetic inclusions; averaging and certification.
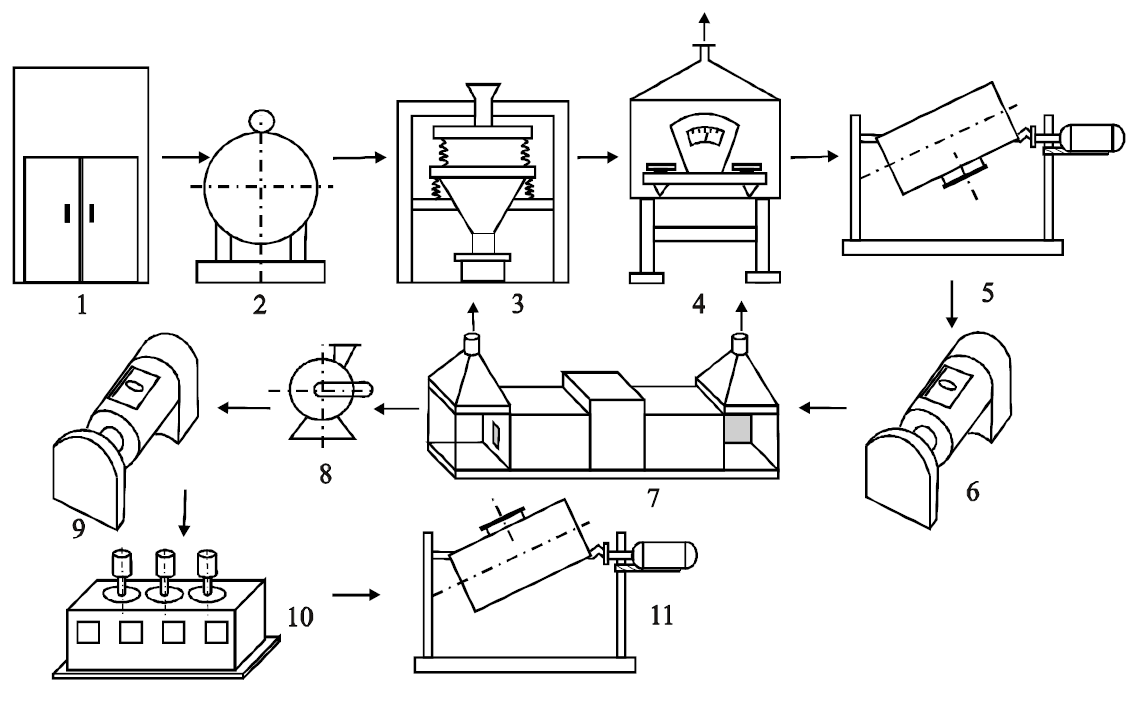
Figure 2 — Technological line for obtaining PZT materials using ceramic technology: 1 — raw material warehouse; 2 — vacuum drying oven; 3 — vibrating sieve; 4 — Libra; 5,11 — «drunken barrel» averager; 6 — charge vibrating mill; 7 — tunnel oven; 8 — hammer mill; 9 — vibratory mill for finished product; 10 — magnetic separator
The charge for the manufacture of piezoceramic material is composed of raw materials in a ratio that is determined by recalculating molar to weight percentages, taking into account the content of the main substance in each component.
The purpose of high temperature synthesis is to remove carbon dioxide from carbonates and any volatile impurities; carrying out a thermochemical reaction between the components of the resulting product; reduction of shrinkage of manufactured products during subsequent sintering. In mass production, synthesis is more efficiently carried out in tunnel furnaces due to their high productivity. To ensure the completeness of the synthesis, it is very important that the true temperature in the furnace exactly corresponds to the specified.
Before vibratory grinding, the synthesized material in the form of moderately hard cakes is crushed using a jaw or hammer crusher. The crushed material is sent to fine vibratory grinding. The main purpose of milling is to provide the surface required for the complete sintering process and high enough activity to increase the rate of heterogeneous processes.
At presence of magnetic admixtures material is added by separation repeatedly. After separation finally dried material, will attest, prepare to the dispatch or pass on an area on making of wares.
4. Comparative analysis of methods for obtaining piezoceramic materials
A review of the literature made it possible to establish that the methods of solution chemistry make it possible to synthesize powders of the target product with the dispersion of nanosized particles (20–60 nm), which is not provided by the ceramic technology (100 nm), under normal conditions, since the mechanically prepared mixture is the most difficult to synthesize. However, when using the methods of solution chemistry, there are a number of insurmountable difficulties that can be associated with many circumstances. In this case, ceramic technology is the most appropriate technology.
A significant increase in the reactivity of powders is achieved through the use of vortex layer devices, vibration mixing, vibration grinding in gummed vibrating mills, however, dry grinding does not allow obtaining particles less than 10 microns in size. A significant increase in the activity of the charge is achieved due to its ultrasonic treatment in water, which makes it possible to increase the content of fine particles and reduce the temperature of the beginning of the formation of a solid solution with a perovskite structure (by ≈ 100 oC)
A change in dispersion can also lead to a decrease in the spread of parameters of the finished material by approximately 2.5 times, which can be associated with a high degree of homogeneity of the charge treated with ultrasound and its high reactivity. In this work, a more detailed study of the dependence of technological parameters and electrophysical properties of piezoceramic materials with an increase in the duration of ultrasonic processing is planned.
Conclusion
Thus, on the basis of the studies carried out, it has been established that the dispersion of both the charge and the finished material affects the technological parameters and the electrophysical properties of products. It is shown that an increase in the dispersion of a mixture of initial components increases its activity, expressed in a decrease in the temperature of synthesis of solid solutions.
Technological processes for obtaining materials by methods of their isolation from solutions are described.
The stages of the technological process using ceramic technology have been characterized and fully studied, and it has been shown that this method is the only acceptable method for obtaining complex oxides of various structural types and their solid solutions and is indispensable in the search for new materials.
This master's work is not completed yet. Final completion: June 2021. The full text of the work and materials on the topic can be obtained from the author or his head after this date.
References
1. Прилипко, Ю.С., Функциональная керамика. Оптимизация технологии / Ю.С. Прилипко — Донецк: Норд–Пресс, 2007. — 492 с.
2. Приседский, В.В., Нестехиометрические сегнетоэлектрики АIIВ1vО3: монография / В.В. Приседский. — Донецк: Изд–во «Ноулидж» (донецкое отделение), 2011. — 267 с.
3. Прилипко, Ю.С., Оптимизация технологии получения пьезокерамических материалов ЦТС / Ю.С. Прилипко / В сб. Физика и техника высоких давлений. — Донецк: ФТИ, 2002. — 12 с.
4. Афанасенко, Л.Д., Исследование условий получения материалов системы ЦТС полукерамическим методом / Л.Д. Афанасенко, А.М. Гареев, А.П. Калашников // В сб. Ферритовые, сегнето–, пьезоэлектрические и конденсаторные материалы и сырье для них. — Харьков: ВНИИмонокристаллов, 1977. — С. 82–87.
5. Звоник, В.А., Влияние сырья на условия получения и свойства новой пьезокерамики / В.А. Звоник, О.С. Дидковская, Н.И. Селикова и др. // Сб.: Материалы для электронной техники. — М.: НИИТЭХИМ, 1983. — С. 3–10.
6. Алесковский, В.Б., Химия твердых веществ / В.Б. Алесковский — М.: Высшая школа, 1978. — 256 с.
7. Вербицкая, Т.Н., Влияние исходного сырья и условий синтеза на свойства материала ВК–4 / Т.Н. Вербицкая, Т.П. Майдукова, Л.А. Гришаева // Сб.: Ферритовые, сегнето-, пьезоэлектр. и конденс. материалы и сырье для них. – Харьков: ВНИИмонокристаллов, 1977. — С. 107–112.
8. Прилипко, Ю.С., Изучение влияния некоторых физических воздействий на технологические параметры получения пьезоматериалов и электрофизические свойства пьезокерамики / Ю.С. Прилипко, В.С. Салей, Н.П. Пилипенко // Наукові праці ДонНТУ. Серія: Хімія і хімічна технологія. — 2002. — Вип.44. — С.110–119.
9. Лимарь, Т.Ф., Образование PbZrO3, PbTiO3 и их твердых растворов из продуктов распылительной сушки / Т.Ф. Лимарь, В.В. Приседский // В сб. Химия и технология материалов для новой техники. М.: НИИТЭХИМ, 1980. — С. 33–41.
10. Салей, В.С., Влияние обработки ЦТС–порошков ультразвуком, СВЧ–излучением и высоким гидростатическим давлением на свойства пьезокерамики / В сб. Физика и техника высоких давлений. — Донецк: ФТИ, 2002. — Т. 12. — № 2. —– С. 46–51.