Classification, purpose and principle of operation of semi-gantry cranes
Content
- Introduction
- 1. Classification of hoisting machines
- 2. Appointment of a semi-gantry crane
- 3. Description of the design and principle of operation of the semi-gantry crane
- Conclusions
- References
Introduction
In the problem of the implementation of scientific and technological progress, a significant role is assigned to lifting and transport engineering, which has been tasked with the widespread introduction in all areas of the national economy of comprehensive mechanization and automation of production processes, the elimination of manual loading and unloading operations and the elimination of heavy manual labor when performing basic and auxiliary technological operations.
It is vitally necessary to increase the production of progressive means of mechanization of hoisting and transport, loading and unloading and storage operations. Modern flow technological and automated lines, interdepartmental and intrashop transport require the use of various types of hoisting and transport machines and mechanisms that ensure the continuity and rhythm of production processes. Therefore, lifting and handling equipment has now become one of the main decisive factors that determine production efficiency.
The correct choice of material handling equipment affects the normal operation and high productivity of the production. It is impossible to ensure its stable rhythm at the modern stage of intensification without the coordinated and trouble-free operation of modern means of mechanization of intrashop and inter-workshop transportation of raw materials, semi-finished products and finished products at all stages of processing and storage. [1]
Modern high-performance hoisting machines working at high speeds and high lifting capacities are the result of the gradual development of these machines over time. Even in ancient times, 4000 years before our era, ancient Chinese culture knew the use of the simplest lifting devices – levers and pulleys used to lift water from wells and in the construction of structures.
The pace of development of lifting and transport engineering, the introduction of progressive machines and equipment and means of mechanization, the work being done to improve the technical level of the equipment produced has made it possible to significantly increase labor productivity.
Specialized design organizations, together with machine-building plants, have created a number of high-performance, economical and easy-to-use machines and devices for the mechanization of loading and unloading operations.
The main trends in the development of lifting and transport engineering are:
- creation of qualitatively new types of lifting and transporting machines and mechanisms, as well as wide modernization of existing machines and installations to ensure mechanization and automation of loading and unloading, transport and storage operations in all areas of the national economy;
- increasing the carrying capacity and reliability of machines while significantly reducing their metal consumption due to the use of new kinematic schemes, more advanced calculation methods, the use of rational lightweight rolled profiles, new materials (alloyed steels, light alloys and plastics) and progressive mechanical engineering technology (new methods of heat treatment, application of hardening coatings, etc.);
- increasing the productivity of equipment due to the use of a wide regulation of the speed of mechanisms, automatic and remote control using microprocessor and electronic computers, both for controlling the operation of machines, and for calculations and design.
Modern production of hoisting-and-transport machines is based on the creation of block structures, which allow obtaining a high technical and economic effect in the manufacture and operation of these machines. [2].
1. Classification of hoisting machines
Hoisting machines are designed to lift, move and deliver cargo to the required place served by the machine. They serve the production processes in the shops of factories and at construction sites, install and assemble industrial equipment, carry out loading and unloading operations in warehouses and are part of the comprehensive mechanization of production processes in all sectors of the national economy. The designs of these machines are extremely varied. They can be classified according to design characteristics, purpose, and the nature of the work they perform.
There are many types of hoisting machines, the designs of which depend on the type of load, application conditions and degree of complexity. The lifting machine may include several working mechanisms:
- load lifting mechanism;
- crane movement and rotation mechanism;
- mechanism for changing the hook reach.
They can be in various combinations, but all hoisting machines have a lifting mechanism.
The most common hoisting machines are hoisting cranes, cyclic machines designed to lift and move in space a load held by a load gripper.
Cranes move the load in different directions in space. They can be divided into two main classes: with a free suspension of the load and with a rigid suspension and controlled gripping of the load.
Depending on the area of service and design, cranes are divided into two main groups: span and jib. The cranes of the first group cover the span and serve the area along this span, are the cranes of the second group equipped with a boom and are mainly mobile? over long distances - and stationary (much less often). Spans are installed on crane beams in buildings or in open areas. They serve a rectangular area in width and span length. Span cranes are available as bridge, gantry, semi-gantry and bridge-cable cranes. [3].
For work in open areas and in closed rooms, gantry cranes are used (Fig. 1), their bridge rests on two vertical trusses that move along rails laid at ground level.
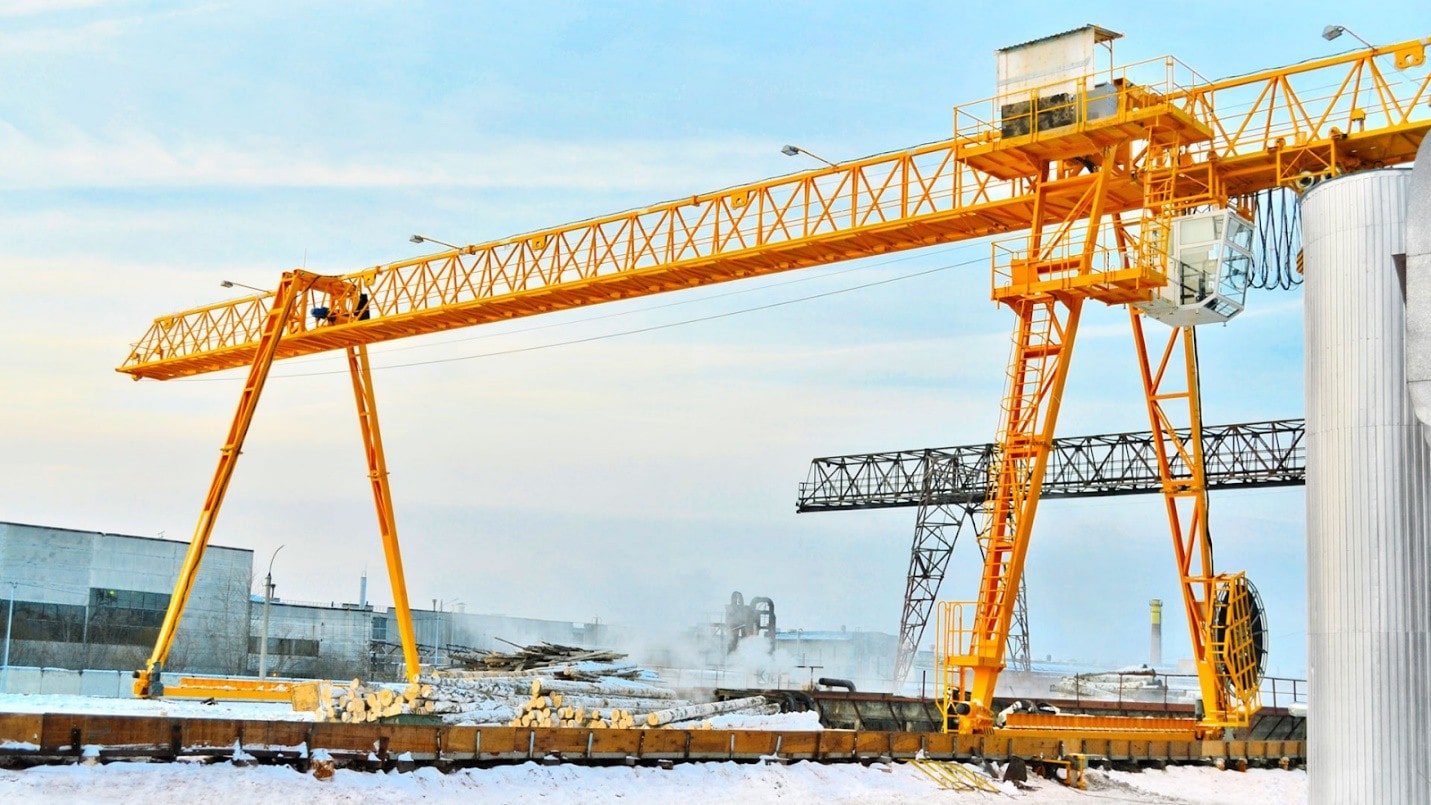
Figure 1 – Gantry crane
Cranes, in which only one side rests on a support stand (or stands), and the other on undercarriages, are called semi-gantry (Fig. 2). For such cranes, two levels of track are laid: one at ground or floor level, the second at a higher height, on an overpass or columns. The range of application and design features of semi-gantry cranes are generally similar to those for gantry cranes, however, they usually have a lower lifting capacity (16-20 t) and a lower lifting height. Spans: 12-20 m. [4]
Designed mainly for loading and unloading and installation work in open areas, as well as for special work – maintenance of hydraulic structures, assembly of ships, etc. The cranes are non-cantilever, one- and two-cantilever and can block railway tracks, motorways and warehouse areas.
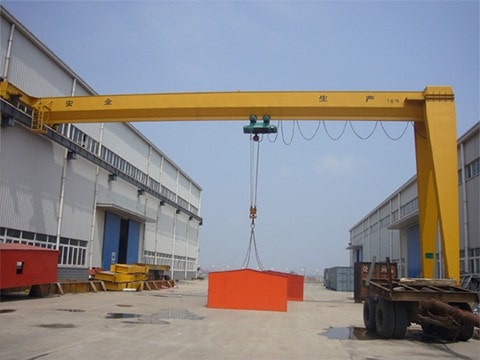
Figure 2 – Semi Gantry Crane
The range of gantry crane applications is extremely wide. Cranes of this type are effectively used to carry containers, piece or timber cargo of small volume and significant tonnage:
- at railroad warehouses, river and sea cargo ports, transshipment points and cargo terminals;
- in industrial buildings and closed workshops;
- at construction and installation works at industrial and civil facilities;
- for sectional assembly in shipbuilding;
- for the maintenance of hydroelectric power plants.
General purpose cranes are manufactured with a lifting capacity of 5 ... 50 tons; special cranes up to 500… 2000 tons. The span of the cranes reaches 140 m, the lifting height – up to 80 m; trolley speed – up to 10 m/s [5].
In accordance with the intended use, gantry and semi-gantry cranes are divided into:
- construction and assembly (span 60-80 m, lifting capacity on average 300-400 tons, lifting loads to a height of 20-30 m);
- general purpose cranes, or reloading cranes (lifting capacity from 3.2 to 50 tons, span size – 10-40 m, lifting height 7-16 m);
- cranes for special purposes.
All types of gantry and semi-gantry cranes can be classified according to the nature of the lifting bodies, the construction of the crane structure, the way of movement of the load trolleys, the method of assembly and disassembly. By the type of bridge support, cranes can be with both rigid or with one rigid and the other flexible support. [6]
In gantry cranes with large spans (Lk> 30 m) and especially in dock levelers, one of the vertical trusses is made in the form of a spatial structure, and the second is a flat structure.
The vertical girder crane bridge is attached in two ways:
- with a spatial truss – rigidly, with a flat – hinged;
- with a spatial truss – with the help of a sliding support that allows the bridge to rotate relative to the pin, with a flat one – with a spherical hinge (Fig. 3).
Metal structures of cranes are of the following types: truss (from pipes and profiles) and bridge (solid and from single pipes of large diameter).
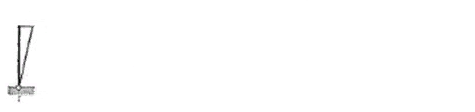
Figure 3 – Crane bridge fixing schemes
(animation consists of 9 frames with a delay of 500 ms between frames, the number of playback cycles is 3, the size is 17 kilobytes)
Cabins in cranes are placed on a rigid support (with spans up to 25 m) or on a moving cart. The standard service life of the gantry and semi-gantry cranes is 20 years, the MTBF is 3000 working cycles. They are able to function effectively at temperatures from -40 to +40 degrees. [7]
Control of gantry and semi-gantry cranes can be carried out both from a specialized cabin (stationary or mobile, providing a better view), as well as from the floor or using a radio control panel. The last two options make it possible to attract ordinary workers trained to perform the functions of drivers as crane operators.
The main parameters of lifting machines are: lifting capacity, lifting speed, lifting height, duration of activation.
2. Appointment of a semi-gantry crane
A semi-gantry crane is a bridge-type lifting device in which the load-bearing elements of the crane structure are supported on one side directly on the crane runway (like overhead gantry cranes), and on the other side on the supporting legs, like gantry cranes.
Semi-gantry cranes are simply irreplaceable where the production area is small, since they do not require investments in the organization of special platforms and overpasses. A semi-gantry crane is always in demand for handling operations at container sites of railway stations; at transport enterprises and transshipment bases; at repair enterprises; at landfills for the production of reinforced concrete structures; for loading and unloading operations in industrial warehouses, in docks, on open assembly repair sites and under sheds. [8]
The semi-gantry crane, depending on the specifics of the work performed, differs in its technical characteristics - lifting capacity (t: 3.2; 5; 8; 10), the working area of the span of the supporting structure element (m: 12.5 - 32.0), lifting height lifting devices (hook, grab, magnet). Semi-gantry cranes are divided into two types – single-girder and double-girder. The semi-gantry crane is also equipped with various cab options – they can be open and closed, with manual and electric control from the floor, operating in different modes, both on direct and alternating current.
3. Description of the design and principle of operation of the semi-gantry crane
Semi-gantry cranes are an important component of mechanization during loading and unloading operations. This semi-gantry crane is used at the NPO YaMZ LLC enterprise for loading and unloading containers arriving by rail laid on the territory of this enterprise.
All containers have standard dimensions and places for coupling with load-handling devices. Used as a container for goods. At the corners of the containers there are special elements - fittings, which are used as supports for containers when stacked and as points for gripping containers when moving them.
Due to the fact that large-tonnage containers with a gross weight of 10 tons (1D) and 25 tons (1ВВ, 1В) in the CIS, as a rule, are not used, when automating loading and unloading operations, we will proceed from the fact that the entire cargo turnover at the enterprise occurs in containers 1A and 1C.
Since the turnover of goods at the enterprise is closely related to the period of the loading and unloading operations, the purpose of automation is to reduce the time spent on their implementation and replace human labor with machine labor.
The expediency of using a semi-gantry crane at the enterprise is justified by the fact that the enterprise has its own railway tracks and allows the delivery of goods directly by rail, without using road transport.
As a load-gripping mechanism in the crane, it was proposed to use a special load-gripping device - a spreader (Fig. 4). The spreader performs automatic coupling and uncoupling from the container without human intervention. When lowering the spreader onto the container, the T-pins enter the holes of the fittings and rotate 90 degrees to engage the spreader with the container. After moving the container, the pins return to their original position, freeing the container [9].
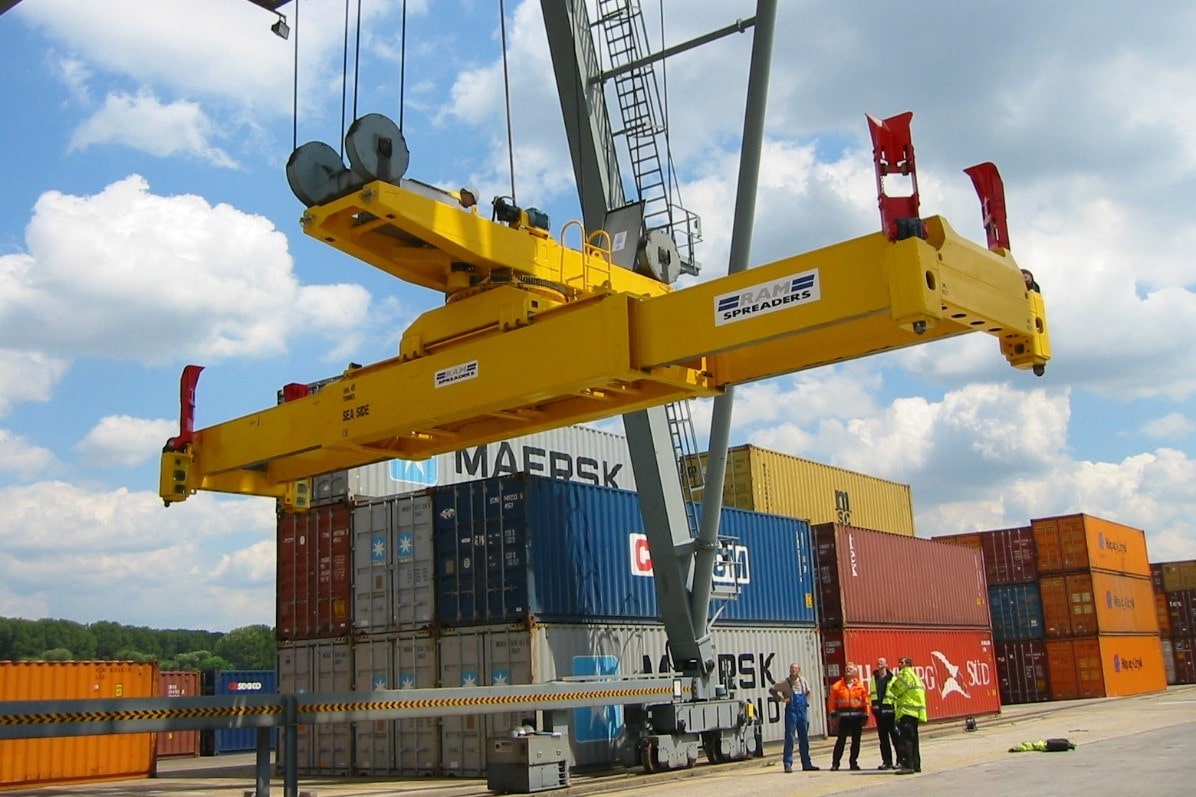
Figure 4 – Semi-gantry crane diagram
In order for the spreader to more accurately target the container, the gripper is made swivel. In addition, it is possible to work with several types and sizes of containers. If it is necessary to operate the spreader with a different type of container (instead of the 1C container, the spreader captures the frame to work with the 1A container), the electrical connectors are connected to the frame for the pins turning mechanisms [10].
The semi-gantry container crane has one console, the lifting capacity of which is limited by 1C containers, which makes the structure cheaper. At the same time, the crane support is made in such a way that 1C containers pass through it without turning the gripper, which increases the speed of loading and unloading operations.
The purpose of this thesis is the development of a semi-gantry crane with a lifting capacity of 40 tons, which will be used at NPO YaMZ LLC for the purpose of mechanizing unloading and loading operations. In addition, one of the goals of automation is to remove maintenance personnel from the area of loading and unloading operations to prevent industrial injuries.
To achieve this goal, it is necessary to solve the following tasks:
- calculate the lifting mechanism;
- calculate the crane movement mechanism;
- calculate the swivel mechanism of the spreader;
- make verification calculations;
- check the crane for stability in working and non-working positions.
Conclusions
The purpose of this thesis is the development of a semi-gantry crane with a lifting capacity of 40 tons, which will be used at NPO YaMZ LLC for the purpose of mechanizing unloading and loading operations. In addition, one of the goals of automation is to remove maintenance personnel from the area of loading and unloading operations to prevent industrial injuries.
References
- Александров М. П. Грузоподъемные машины: Учебник для вузов. – М.: Изд-во МГТУ им. Н. Э. Баумана – Высшая школа, 2000. – 552 с.
- Дунаев П. Ф., Леликов О. П. Детали машин. Курсовое проектирование: Учеб. пособие для машиностроит. спец. техникумов. – 2-е изд., перераб. и доп. – Высш. шк.,1990. – 399 с.
- Правила устройства и безопасной эксплуатации грузозахватных кранов. – М.: Металлургия, 1981. – 168 с.
- Viswanatha Ramamurti,
Mechanics of Machines
, CRC Press, 2002. - Подъемно-транспортные установки. / Зуев Ф. Г., Лотков Н. А. – М.: Колос, 2006. – 471 с.
- Тотай А. В. Основы технологии машиностроения. Учебник и практикум для прикладного бакалавриата / А. В. Тотай. – М.: Юрайт, 2015. – 562 c.
- Холодкова А. Г. Общая технология машиностроения / А. Г. Холодкова. – М.: Academia – 224 c.
- Суслов А. Г. Основы технологии машиностроения. Учебник для бакалавриата / А. Г. Суслов. – М.: КноРус, 2013. – 333 c.
- Обоснование и расчеты параметров грузоподъемных машин: Учебное пособие для вузов / А. И. Барышев, В. А. Будишевский, Н. А. Скляров, Ю. В. Жидков; Под общ. ред. В. А. Будишевского. – Донецк: РВА ДонНТУ, 2009 – 307 с.
- Применение грузозахватных устройств для строительно-монтажных работ / Андреев А. Ф., Богорад А. А., Каграманов Р. А. – М.: Стройиздат, 1985. – 198 с.