Реферат за темою випускної роботи
Зміст
- Вступ
- 1. Актуальність теми
- 2. Мета і задачі дослідження
- 3. Огляд досліджень та розробок
- 4. Схема живильника на пневмоприводi
- Висновки
- Перелік посилань
Вступ
Технічне переозброєння металургії в найближчі роки буде здійснюватися в умовах стабілізації, а в подальшому і зниженні обсягів виробництва основних видів металопродукції і визначатися головним завданням – задоволення потреби народного господарства в чорних металах необхідної якості і сортаменту при значному підвищенні ефективності виробництва і використання металу в споживаючих галузях.
1. Актуальність теми
До числа найважливіших стратегічних завдань, що стоять перед чорною металургією можна віднести:
– зниження металоємності виробництва приблизно в 2 рази;
– підвищення продуктивності праці в галузі вдвічі;
– докорінне оновлення основних виробничих фондів і підвищення економічної ефективності роботи галузі в умовах ринкової економіки і самофінансування;
– комплексне вирішення питань соціального розвитку, охорони навколишнього середовища, раціонального використання природних ресурсів і відходів виробництва.
Зазначені завдання повинні вирішуватися в процесі технічного переозброєння, реконструкції та оновлення кожного металургійного підприємства і, зокрема, кожного конкретного цеху. При цьому в переважній більшості випадків не стоїть завдання нарощування обсягів виробництва продукції на окремих підприємствах, хоча потужність і продуктивність реконструюються і нових агрегатів і навіть цехів можуть збільшуватися. У кожному конкретному випадку головними завданнями є підвищення якості та розширення сортаменту металопродукції, поліпшення умов і зростання продуктивності праці, вирішення проблем охорони навколишнього середовища і підвищення ефективності виробництва.
У звʼязку з цим особливо актуальними стають вибір і економічне обґрунтування варіантів реконструкції обʼєктів металургійного виробництва зокрема конвертерного цеху. Сипучі матеріали в конвертері подаються системою стрічкових конвеєрів і живильників, розташованих в ізольованій ділянці конвертерного прольоту. Для збереження поточного запасу сипучих матеріалів в районі кожного конвертера є по чотири витратних бункера. Два бункера загальною ємністю 200 м3 заповнені вапном, бункер корисною ємністю 70 м3 заповнений залізною рудою і бункер ємністю 32 м3 заповнений плавиковий шпат. З конвеєра, що подає сипучі матеріали в конвертерний прогін, сипучі матеріали скидають на пересувний реверсивний конвеєр, розташований над бункерами і розподіляє по ним матеріали. Матеріали з бункерів видаються за допомогою живильників [1].
2. Мета і задачі дослідження
Метою роботи є підвищення ефективності системи завантаження сипучих матеріалів в сталеплавильний конвертер
Обʼєктом дослідження є процесси подачі та завантаження сипучих матеріалів
Предметом дослідження є параметри системи подачі та завантаження сипучих матеріалів.
3. Огляд досліджень та розробок
В бункерах встановлені живильники продуктивністю по 220 м3/год, а під бункерами руди і плавикового шпату – живильники продуктивністю по 720 м3/год. Живильники подають матеріали на ваги дозатори 3–5 т. Крім загальних для всіх конвеєрів перевантажувальних бункерів, в районі кожного конвеєра встановлено по два проміжних бункера 4, що містять запас феросплавів на одну плавку. Матеріали з бункерів подаються в ківш з допомогою поворотною тічки.
Модель кисневого конвертера приведена на рис. 1.
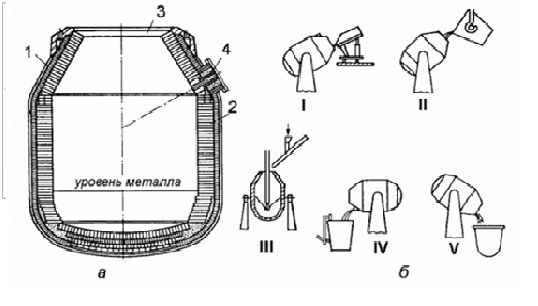
Рисунок 1 – Схема конвертера (а) основні періоди плавки (б): I – завантаження брухту; II – заливка чавуну;
III – завантаження шлакоутворюючих добавок і продування киснем; IV – слив стали; V – слив шлаку; 1 – кожух;
2 – футерування; 3 – горловина; 4 – бічний отвір випуску сталі (річка)
Система завантаження матеріалів в конвертер (рис. 2) повинна забезпечувати зберігання оперативного запасу матеріалів:
– набір, дозування і завантаження порцій матеріалів в певний час і в певній послідовності без зупинки продувки;
– можливість швидкого варіювання програми завантаження;
– автоматизацію всіх виконуваних процесів;
– мале виділення пилу в атмосферу цеху і в газоотводящий тракт.
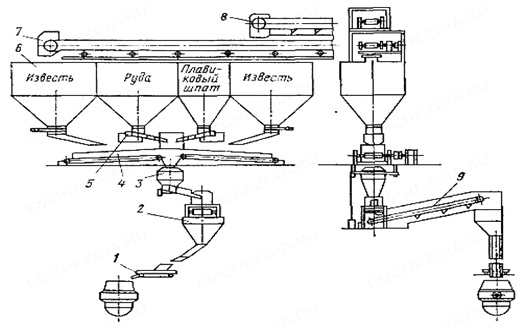
Рисунок 2 – Система завантаження сипучих матеріалів в цеху з 100–130 т конвертерами
Системи завантаження розрізняються пристроєм, числом і компонуванням окремих елементів, бувають одно– і двосторонні, з індивідуальними і загальними для двох конвертерів витратними бункерами, з проміжними бункерами і без [2].
4. Схема живильника на пневмоприводi
Більшість промислових підприємств країн СНД працюють на морально застарілому обладнанні зробленому 10 і більше років тому. Основними недоліками є низька ремонтопридатність в звʼязку з відсутністю запчастин, відносно малий рівень продуктивності і самого якості продукції, що випускається, простої через вихід з ладу будь–яких окремих вузлів устаткування, великі кількість часу на пошук несправності.
Для вирішення цієї проблеми найкращим способом є установка більш сучасного обладнання замість застарілого. Саме тому, взявши за приклад систему подачі і завантаження в конвертер сипучих матеріалів металургійного заводу можна замінити застарілі узликонвертерного цеху, а саме живильники які встановлені після бункерів з вапном, плавиковий шпат і рудою.
Живильники являють собою механічні пристрої, які забезпечують стабільність регульованого вантажопотоку з бункера на конвеєри. В даний час вони працюють з електроприводом, двигуни якого працюють в запиленому середовищі, шар пилу може досягати до 3 см. Наслідком цього виникає локальний перегрів лобових частин обмоток і передчасний вихід з ладу електродвигуна. Саме це знижує надійність і показники якості роботи всієї системи подачі і завантаження сипучих матеріалів в конвертер і, як результат якість стали на виході з конвертера.
Передбачається управління шиберами за такою пневматичної схемою приводу (рис. 3) [3]. В автоматизованій системі управління будуть використані електропневматичні елементи і контролер [4].
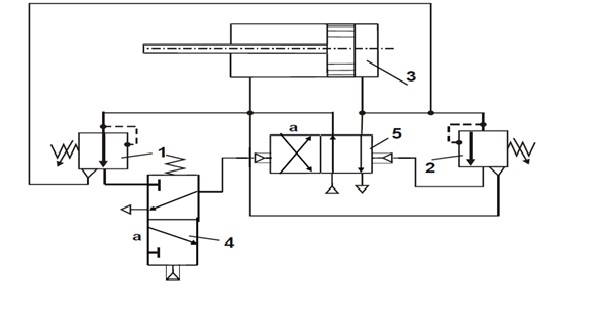
Рисунок 3 – Схема управління пневмопривідом затвора з контролем по тиску в робочій порожнині пневмоцилиндра: 1,2 – клапани послідовності; 3 – пневмоцилиндр; 4 – пневмотумблер; 5 – головний пневморозподільник.
Висновки
Завдання подальшої роботи полягає в обґрунтуванні параметрів системи автоматичного управління приводами затворів подачі і завантаження в конвертер сипучих матеріалів на базі електропневматичних елементів приводу і вільно програмованого контролера. При написанні даного реферату магістерська робота ще не завершена. Остаточне завершення: червень 2021 року. Повний текст роботи та матеріали по темі можуть бути отримані у автора або його керівника після зазначеної дати.
Перелік посилань
- Целиков А. И. Машины и агрегаты металлургических заводов. В 3–х томах. Т2. Машины и агрегаты сталеплавильных цехов. Учебник для вузов / А.И. Целиков // – М.; Металлургия 1988. – 432с.
- Михайловский В. Н. Основы проектирования металлургических заводов. Определение объёмно–планировочных решений, состава и количества основного технологического и подъёмно–транспортного оборудования сталеплавильных цехов: учеб.пособие./В. Н Михайловский// Спб.: Изд–во Политехн. ун–та, 2013.–215с.
- Лаптева Н. Е. Пневмопривод и средства автоматики 2009.
- Шахматов Е. В. Пнеммопривод и средства автоматики: учеб. пособие – Самара: Издательство СГАУ, 2006 – 112с.
- Пневматические распределители [Электронный ресурс]. Режим доступа:
https://pnevmex.ru/catalog/pnevmaticheskie-raspredeliteli/. - Шиберные задвижки [Электронный ресурс]. Режим доступа:
http://armatek.ru/about/truboprovodnaya_armatura/shibernye_zadvizhki/. - Расчет пневомоцилиндра [Электронный ресурс]. Режим доступа:
https://emc.kiev.ua/%D1%80%D0%B0%D1%81%D1%87%D0%B5%D1%82-%D0%BF%D0%BD%D0%B5%D0%B2%D0%BC%D0%BE%D1%86%D0%B8%D0%BB%D0%B8%D0%BD%D0%B4%D1%80%D0%B0/.