Реферат за темою випускної роботи
Цей реферат використано у якості прикладу з дохволу його атвора, магістра ДонНТУ Євгена Татолова.
Оригінал: http://masters.donntu.ru/2011/fknt/tatolov/diss/
Зміст
- Вступ
- 1. Актуальність теми
- 2. Мета і задачі дослідження
- 3. Опис способів контролю робочої поверхні алмазного шліфувального круга
- 4. Опис конструкції пристрою для профілографірованія робочої поверхні алмазного шліфувального круга
- Висновки
- Перелік посилань
Введення
Шліфування алмазним кругом є досить складним і дорогим процесом, що вимагає грамотного поводження з алмазним інструментом і розуміння природи зносу шліфувальних кругів. Для запобігання передчасного руйнування ріжучої поверхні алмазного круга необхідні відомості про геометричні характеристики робочої поверхні, інтенсивності зносу абразиву й зв'язування, відхилення геометрії кола і його пористості [1].
Одним з методів визначальним дані параметри є метод профілографірованія. Цей метод є різновидом мікрометричного методу вимірювання зносу.
На профілографи вимірюється величина, так званого «первинного зносу» - за який приймається різниця в висоті мікронерівностей від лінії западин до гребінця - заміряну на одному і тому ж ділянці в різні моменти випробування. Для вимірювання зносу методом профілографірованія використовують профілограф-профілометри.
Даний метод полягає в наступному. З одного і того ж мікроділянки досліджуваної поверхні знімаються профілограми до початку випробування і після.
На профілограми контури одних і тих же западин залишаються постійними, а виступи, внаслідок зносу, змінюють свою висоту. Визначаючи загальне зменшення виступів від лінії западин, отримуємо величину первинного зносу. У разі, якщо вона перевищує висоту нерівностей в якості постійної бази, від якої проводиться вимірювання, вибирається неробочий ділянку досліджуваної поверхні.
Недоліком методу є неможливість зняття профілограми до і після випробування з одного і того ж перетину, що призводить до появи похибки у визначенні величини лінійного зносу. Ця похибка тим більше, чим менше сама величина зносу в порівнянні з величиною нерівностей поверхні [2].
1. Актуальність теми
Технологічний процес шліфування є одним з широко поширених в машинобудуванні. Так, у вітчизняному машинобудуванні частка шліфувальних верстатів становить 12%, а в автомобілебудуванні - до 25% .. До шліфувального круга, як до ріжучого інструменту, пред'являються великі вимоги щодо підтримки гостроти різальних крайок і збереження необхідної форми профілю круга. Алмазне шліфування є складним дорогим процесом, що вимагає грамотного застосування алмазного інструменту і розуміння природи зносу шліфувальних кругів.
Шліфувальні алмазні кола складаються з робочого алмазного шару і корпусу. Алмазний шар складається з наповнювача, зв'язки і самого алмазного порошку. Тому для запобігання несвоєчасного руйнування ріжучої поверхні алмазного круга необхідні відомості про стан робочої поверхні круга, а саме: число зерен на одиниці робочої поверхні, щільність розподілу вершин зерен по висоті робочої поверхні, висота робочого шару, стан вершин алмазних зерен. Також до шліфувального круга, як до ріжучого інструменту, пред'являються великі вимоги щодо підтримки гостроти різальних крайок і збереження необхідної форми профілю круга. Якщо міцність закріплення абразивних зерен в інструменті нижче міцності самих зерен, то зношування відбувається за рахунок викришування зерен, а коло працює в режимі самозатачіванія. Самозатачіванію називають властивість кола зберігати працездатність внаслідок утворення нових різальних крайок в процесі обробки. Якщо міцність абразивних зерен виявиться нижче міцності їх закріплення в шліфувальному колі, то зношування відбувається частково за рахунок крихкого руйнування і сколювання зерен, а частково - в результаті їх стирання оброблюваних матеріалом. Таке зношування носить назву затупления кола і полягає в утворенні майданчиків зносу на поверхні абразивних зерен і зменшенні ріжучої здатності інструменту, що проявляється у збільшенні сили різання до двох разів. Крім того, нерівномірний знос кола призводить до зміни його профілю. Нестабільність робочих характеристик шліфувального круга, зміна їх під час обробки заготовок призводить до зміни якості поверхні шару деталі. Тому виникає необхідність в правки шліфувального круга.
2. Мета і завдання дослідження
Метою роботи є проектування пристрою для автоматизованого контролю робочої поверхні алмзного шліфувального круга і дослідження його вихідних характеристик
Об'єктом дослідження явлется пристрій для автоматизованого контролю робочої поверхні алмазного шліфувального круга.
Предметом дослідження є контроль робочої поверхногсті методом профілографірованія
3. Опис способів контролю робочої поверхні алмазного шліфувального круга
Для відновлення ріжучої здатності шліфувальних кругів, їх геометричної форми і мікропрофілю робочої поверхні періодично проводять правку, т. Е. Призводять коло в працездатний стан. Існує велика кількість методів вимірювання ступеня зносу шліфувального круга, які розглянуті нижче.
Непрямий спосіб вимірювання ступеня зносу алмазних шліфувальних кругів шляхом вимірювання сили різання. Сили різання при шліфуванні впливають на якість обробленої поверхні, а також за рівнем сил можна оцінити ступінь зносу алмазного круга і своєчасно вдатися до відновлення його ріжучих властивостей. Експериментальне визначення величини і характеру зміни сил різання при шліфуванні вироблялося багатьма дослідниками із застосуванням різних вимірювальних засобів. На перших етапах дослідницьких робіт визначали силу різання через вимірювання потужності, що розвивається електродвигуном при шліфуванні за допомогою ватметра. Величину тангенціальної складової сили різання визначають розрахунковим шляхом [ 1 ]:
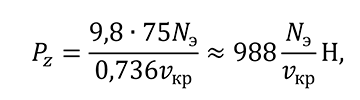
де N е -Ефективна потужність в кВт, що розвивається на шпинделі; & Nu; кр -Окружні швидкість кола в м / с. Розглянутий метод простий, але не дозволяє виміряти складові сили різання і не точний, тому що визначає повну потужність, включаючи і втрати на тертя в механізмах верстата.
Для безпосереднього вимірювання складових сил можна використовувати динамометричні пристрої. Динамометр може бути виготовлений у вигляді пружної муфти з плоскими радіально-розташованими пружинами [ 1 ]. Можна так само використовувалися дротові датчики опору, встановлені на двох центрах (передньому і задньому) верстата. Два динамометричних центру дозволяють фіксувати силу різання в процесі шліфування при будь-якому положенні шліфувального круга щодо оброблюваної деталі. Однак, даний метод можна застосовувати тільки при установці деталі в центрах.
Спосіб безконтактного вимірювання ступеня зносу алмазних шліфувальних кругів шляхом вимірювання вібрації шліфувального круга [ 2 ]. При зміні стану робочої поверхні круга виникають вібрації, викликані як вібраціями безпосередньо самого шліфувального круга, так і механізмами верстата.
Переміщення в технологічній системі при виникненні вібрації засновані на вимірі відстані між шліфувальним кругом і датчиком ємнісним методом. Схема вимірювання показана на малюнку 1. датчиком місткості утворений металевою пластиною 1 з пристроєм 2 для вимірювання початкового зазору & Delta; і поверхнею шліфувального круга 3, яку попередньо змочують електропровідної рідиною. Як електропровідної рідини використовують емульсію або водопровідну воду. При вимірі шліфувальний круг приводять в обертання. В якості приводу використовують або спеціальний стенд (при установці шліфувального круга на оправлення), або привід верстата (при вимірюванні безпосередньо на шпинделі верстата). При наявності відносних коливань між поверхнею кола і пластиною 1 змінюється величина зазору & Delta ;, що призводить до зміни ємності зазору між пластиною 1 і вологою поверхню шліфувального круга 3. Зміна ємності за допомогою спеціального підсилювача 4 перетворюється в електричний сигнал, який записується реєструючим приладом 5 ( див. мал. 1).
Це спосіб є безконтактним способом вимірювання ступеня зносу шліфувальних кругів і майже не знаходить практичного застосування, так як має низьку точність вимірювання. Даний метод є непрямим принципом вимірювання ступеня зносу кола, що відрізняється складністю обробки результатів вимірювання та значними погрішностями, що не дозволяє оцінити нерівномірність зносу. Неточність у вимірі викликані залежністю зазору від стану рідини, яка неконтрольовано змінюється.
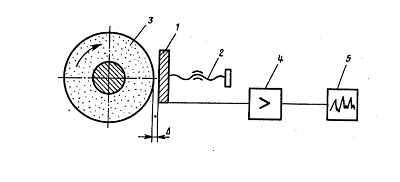
Малюнок 1 - Схема вимірювань вібрацій шліфувального круга.
Фотоелектричний метод безконтактного вимірювання ступеня зносу шліфувального круга [ 3 ]. На мал. 2 зображена принципова схема вимірювального пристрою при вимірюванні ступеня зносу алмазно-абразивного круга.
Фотоелектричний пристрій для безконтактного вимірювання ступеня зносу робочого інструмента містить оптико-електронний блок, що включає в себе два освітлювача 1, об'єктив 2, польову діафрагму 3, конденсатор 4, два фотоприймача 5 і блок 6 порівняння; реєстратор, виконаний у вигляді стрілочного індикатора 7; і два світловідбивних елемента 8 і 9, виконані у вигляді пластин.
Світловідбиваючі елементи 8 і 9 закріплені на бічній поверхні круга 10, причому елемент 8 розміщений в зоні зносу, а елемент 9 - поза нею. Пристрій працює наступним чином: перед початком вимірювань схема налаштовується таким чином, щоб на виході блоку 6 порівняння сигналу не було, тобто показання індикатора 7 було нульовим. У міру зношування круга 10 зі зменшенням його розмірів зменшується і площа відображає елементу 8, оскільки він розміщений по краю кола. При цьому сигнал, який зчитується фотоприймачем, реєструючим величину потоку елемента 8, зменшується, а сигнал, отриманий іншим фотоприймачем від базового відображає елементу 9, залишається незмінним. Баланс схеми порушується, на виході блоку 6 порівняння з'являється вихідна напруга, за величиною якого і судять про зниження зносу алмазно-абразивного круга 10.
Фотоелектричний метод є безконтактним методом, простий в реалізації, але головний недолік - відносно невелика точність. В якості випромінювача світлового потоку використовується поверхню робочого інструменту. Для підвищення точності вимірювання ступеня зносу інструментів з низькою відбивною здатністю пристрій забезпечений двома відображають світловий потік елементами, один з яких розміщений в зоні зносу, а другий - поза нею і є базовим. Розглянутий метод дозволяє визначити тільки лінійний знос, але не характеризує стан робочої поверхні шліфувального круга.
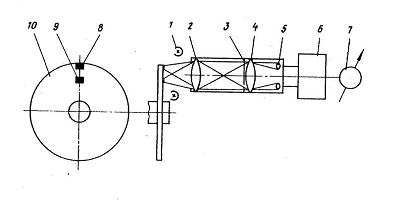
Малюнок 2 - Фотоелектричний пристрій для безконтактного вимірювання ступеня зносу шліфувального круга.
Пневматичний метод безконтактного вимірювання ступеня зносу шліфувального круга [ 4 ]. Відомий спосіб безконтактного вимірювання ступеня зносу алмазних шліфувальних кругів за допомогою пневматичного датчика. Пропонований метод полягає в тому, що до торця шліфувального круга підводиться сопло, через яке подається повітря під тиском, витрата підводиться повітря визначають за рахунок різниці показань длинномера пневматичного датчика. Як вимірювальної бази приймають робочу поверхню алмазного шліфувального круга. Це дозволяє підвищити точність вимірювання зносу шліфувального круга в процесі роботи.
Оптичний метод вимірювання ступеня зносу шліфувального круга [ 5 , 6 ]. Більшість оптичних методів засновані на лазерної тріангуляції. Основні елементи установки: лазерний діод і позиційно-чутливий детектор (ПЧД) з підсилювачем і двома лінзами (мал. 3).
Датчик кріпиться на двох осях блоку крокової приводу з можливістю переміщення в напрямку, перпендикулярному до поверхні шліфувального круга і в осьовому напрямку. Даний метод дозволяє проводити вимірювання при швидкості круга до 300 м / с. Так само можливо визначити радіальне биття.
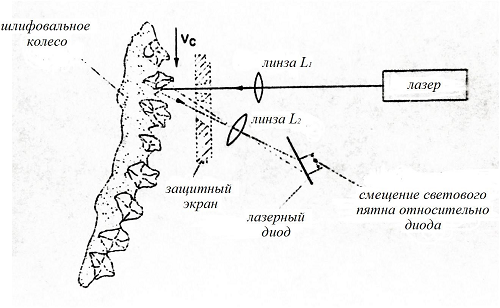
Малюнок 3 - Оптична установка для вимірювання ступеня зносу шліфувального круга.
Метод профілографірованія . Даний метод відноситься до експериментального визначення характеристик робочої поверхні круга. Лінійний знос кола вимірюється за допомогою спеціального стаціонарного пристосування в 6 фіксованих точках по периферії і в трьох точках вздовж котра утворює кола з точністю 0,001 мм. Вимірювання діаметра шліфувальних кругів менше 50 мм в процесі його роботи виробляли мікрометрами з похибкою ± 0,004мм. Характер зносу алмазних зерен досліджується по фотографіях, отриманим на металографічному мікроскопі ММР зі збільшенням 200х - 500х.
На кафедрі ДонНТУ було розроблено спеціальний пристрій (мал. 4) для запису ріжучого профілю алмазного круга на металевій зв'язці з виділенням зерен із загального рельєфу кола. Воно побудоване на базі профілограф-профілометра 4, електронного блоку 3 і пристосування 2. Інформація виводиться на стрічку самописного приладу профілограф-профілометра 5. На пристосуванні 2 розташовується датчик профілограф-профілометра, який реєструє коливання коромисла з лопаткою, яке, що переміщається відповідно до зміни профілю круга.
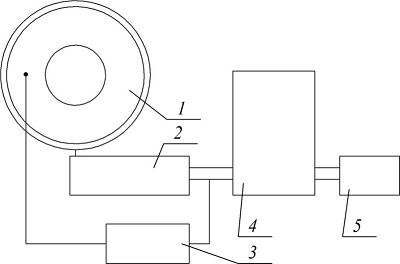
Малюнок 4 - Структурна схема пристрою для запису ріжучого профілю алмазного круга.
Тут же розташовується привід обертання кола, що складається з малооборотних двигуна, блоку редукції і приводного КАПРОЛОНОВИЄ ролика. За допомогою зниженою редукції досягається дуже мала частота обертання алмазного круга - 1 оборот за 10 годин для кола діаметром 200 мм, що відповідає лінійної швидкості переміщення, рівної 1 мм / хв. Така швидкість трасування кола відповідає швидкостям протягання датчика, що застосовуються при профілографірованіі поверхні деталі. Перед записом профілю робочої поверхні круга проводилася тарировка всього вимірювального пристрою. Для цього використовувалася мікрометрична скоба з ціною поділки 2 мкм. Довжина профілограми становила не менше 15-20 мм робочої поверхні круга.
Привід обертання кола має можливість зміщення у вертикальному напрямку, що дозволяє його використовувати для різних розмірів алмазних кіл. Як контактує елемента застосовується лопаточка, виконана із загартованої сталі. Товщина її становить 0,05 мм, а ширина варіювалася в межах від 0,1 до 0,7 мм в залежності від зернистості круга і завдань досліджень. Запис алмазних зерен відтворює зображення набору частинок, що знаходяться в пересічної площини щупа, в спотвореному вигляді. Профілограмма поверхні кола є площиною ортогональних проекцій всіх елементів структури, що містяться в обсязі, відсікає краями щупа. Аналіз одержуваного рельєфу кола по профілограмі вимагає застосування методів стереологіческой реконструкції поверхні, яка аналогічна аналізу структури фольги при електронній мікроскопії.
Недоліком цього методу є можливість здійснення вимірювання тільки при відсутності процесу різання і швидкості кола 0,01 м / с.
4. Опис конструкції пристрою для профілографірованія робочої поверхні алмазного шліфувального круга
Дослідження положення алмазних зерен РПК проводять на вимірювальному комплексі, який дозволяє реєструвати рельєф робочої поверхні кругів на металевій зв'язці методом профілографірованія з подальшою реєстрацією даних на ПЕОМ. Вимірювальний комплекс включає пристрій для закріплення шліфувального круга з вузлом його обертання, комплект приладів профілометра-профілографа (пристрій для профілографірованія і блок посилення), комп'ютер, обладнаний перетворювачем аналогового сигналу в дискретний, і дисплей і дозволяє реєструвати рельєф робочої поверхні кругів на металевій зв'язці з виділенням рельєфу зерен і зв'язки. принципова схема комплексу представлена ??на мал. 5 і його принцип дії на мал. 6.
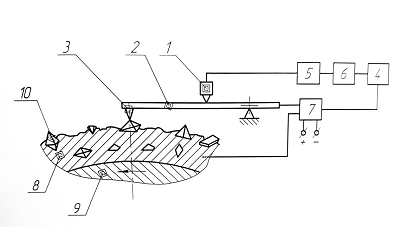
Малюнок 5 - Схема пристрою для реєстрації рельєфу ріжучої поверхні алмазних кругів на металевій зв'язці.
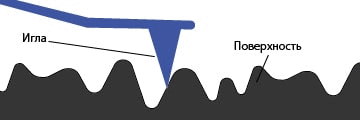
Малюнок 6 - Принцип дії профілографа
(анімація: 5 кадрів, 10 повторів, 44.8 кілобайт)
Вимірювальний комплекс працює наступним чином. При обертанні кола 9 обмацує голка 3 огинає профіль робочої поверхні круга, здійснюючи коливання коромислом 2 щодо осі гойдання. Ці коливання сприймаються датчиком 1, сигнал від якого надходить на вхідний порт комп'ютера 4 через блок узгодження і перетворювач 6 безперервного електричного сигналу в дискретний.
Коли обмацував голка 3 знаходиться на алмазному зерні 10, сигнал від датчика надходить на блок узгодження 5, де він зменшується до рівня в ... 5 В, потім він потрапляє в перетворювача 6, в якому безперервний електричний сигнал від датчика перетворюється в дискретний, а потім на порт комп'ютера 4. Одночасно на цей же порт надходить сигнал від ключового елемента 7, який надає сигналу відповідний алмазному зерну код «1». На дисплеї комп'ютера відображається рельєф алмазного зерна відповідним кольором або товстою лінією (рис. 7).
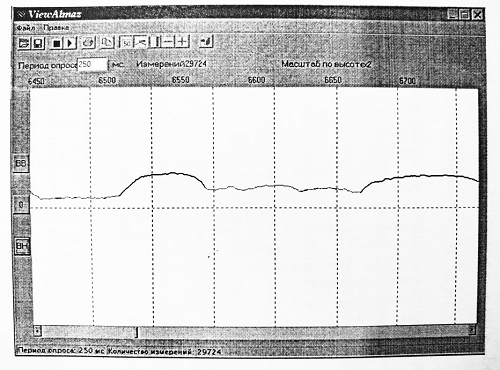
Малюнок 7 - Вікно програми для реєстрації параметрів РПК з фрагментом профілограми рельєфу алмазних зерен (жирна лінія) і рельєфу зв'язки (тонка лінія)
При сходженні обмацує голки 3 з зерна 10 вона потрапляє на струмопровідну зв'язку 8 і сигнал від датчика продовжує надходити на порт комп'ютера через блок узгодження 5 і перетворювач 6 безперервного електричного сигналу в дискретний. В цей же час на порт комп'ютера через ключовий елемент 7 надходить сигнал, відповідний металевій зв'язці з кодом «0».
На дисплеї комп'ютера відображається рельєф металевої зв'язки відповідним кольором або тонкою лінією.
Таким чином, профілограмма містить інформацію про параметри РПК.
Для перетворення аналогових сигналів величиною 0 ... + 5 BВ цифрові коди для запису в ПЕОМ використовується багатофункціональний пристрій NVL08. Вихідний диференційний сигнал електронного блоку профілографа величиною кілька вольт має рівень щодо землі близько 140 ... 170 B. Для узгодження його з входом NVL08 був виготовлений пристрій, схема якого показана на рис. 8.
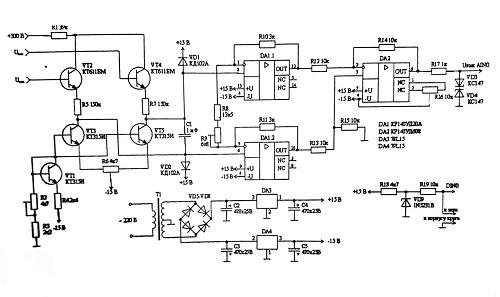
Малюнок 8 - Принципова електрична схема узгоджувального пристрою
На транзисторах VT1 - VT5 зібрана схема, знижує вхідна напруга. Транзистори VT3, VT4, бази яких підключаються до виходів електронного блоку профілографа, служать повторителями напруги, що не неподобство роботу електронного блоку (вхідний струм складає десятки мікроампер). Транзистор VT1 з резисторами R2 i R4 служить для завдання струмів транзисторів VT3 і VT5. Ці транзистори працюють в режимі джерел струму і забезпечують спільно з резисторами R5 i R7 зміщення синфазного сигналу від високого (140 ... 170 В) до приблизно нульового рівня з невеликим зменшенням корисного (диференціального) сигналу. Резистор R6 служить Для установки нуля на виході схеми. На операційних підсилювачах DA1.1, DA1.2 DA2 реалізується віднімання сигналів перетворення диференціального сигналу в заземлений сигнал необхідної величини (Регулювання здійснюється резистором R9). Для обмеження сигналу на входах DA1.1 і DA1.2 встановлені діоди VD1 і VD2. Резистор R17 і стабілітрони VD3 i VD4 служать для обмеження напруги на вході NVL08 до п'яти вольт. Пристрій на елементах R18, R19 і VD9 видає сигнал, рівний одиниці, коли голка знаходиться на алмазі, і дорівнює нулю, коли голка стосується зв'язки ..
Для управління запуском аналого-цифрового перетворювача (АЦП) пристрої NVL08 і попередньої обробки результатів вимірювань розроблено програмне забезпечення, що дозволяє проводити запуск АЦП через задані проміжки часу і запам'ятовувати результати вимірювань висоти алмазних зерен і зв'язки вздовж лінії дослідження.
Виготовлене пристрій для автоматизації запису параметрів робочої поверхні алмазного круга до ПЕОМ дозволяє кардинально знизити трудомісткість досліджень параметрів РПК. Рельєф РПК оцінювали наступними параметрами: різновисотних зерен щодо найбільш виступаючого зерна, відстанню між зернами на робочій поверхні круга і величиною виступанія зерен з зв'язки [ 7 ].
Висновки
З усього вище сказаного робимо висновок, що до найбільш перспективним відноситься оптичний метод визначення характеристики робочої поверхні круга. Однак, у зв'язку з відсутністю матеріальної бази і програмного забезпечення, для обробки результату сканування практичне застосування даного методу ускладнено. З інформативною точки зору оптичного методу найбільш відповідає метод профілографірованія. За допомогою даного методу можна оцінювати такі зміни на робочій поверхні як: число зерен на одиницю робочої поверхні, щільність розподілу вершин зерен, висоту робочого шару, стан вершин алмазних зерен. Тому пристрій для автоматизованого контролю робочої поверхні алмазного шліфувального круга ми будемо робити на основі цього методу.
При написанні даного реферату магістерська робота ще не завершена. Остаточне завершення: червень 2021 року. Повний текст роботи і матеріали по темі можуть бути отримані у автора або його керівника після зазначеної дати.
Перелік посилань
- Маслов Е.Н./Теория шлифования материалов-Москва: Машиностроение, 1974-320 с.
- Авторское свидетельство №444632. СССР. Способ бесконтактного измерения вибраций шлифовального круга/ Болотов Б.Е., Трубников В. В. – №1897640/258; заяв. 28.03.73; опуб. 30.09.75.
- Авторское свидетельство №448366. СССР. Фотоэлектрическое устройство для бесконтактного измерения степени износа рабочего инструмента/ Ронталь Г.Д., Ивашев Ф. Д., Френкель Ш.Т., Вогман Г.А. - №1696795/25-28 ; заяв. 17.09.71; опуб. 30.10.74, Бюль. №40.
- Авторское свидетельство №236026. СССР. Способ бесконтактного измерения степени износа алмазых шлифовальных кругов / Мамедов Д.М., Лятифов Ф. Д., Тренин А.П., Садыхов А.И. - №1053461/25-8 ; заяв. 14.11.66 ; опуб. 24.01.69, Бюль. №6.
- Toenshoff, H. K., Karpuschewski, B., Werner,F., 1993, Fast Sensor System for Diagnosis of Grinding Wheel and Workpiece, 5th Intern. Grinding Conf., Cincinatti, Ohio, USA.
- Toenshoff, H. K., Karpuschewski, B., Hinkenhuis, H.: Regent, C.,1997, Potentiale der Uberwachung und Regelung von Schleifprozessen. VDS-Fachtagung Schleif-technik im Wettbewerb., 09.-10. Oct., Aachen.
- Гусев В.В., Молчанов А.Д. К определению микрогеометрии рабочей поверхности шлифовального круга в статике // Вісник Харківського державного технічного університету сільського господарства. Випуск 10. «ПІДВИЩЕННЯ НАДІЙНОСТІ ВІДНОВЛЮЕМИХ ДЕТАЛЕЙ МАШИН. ФІЗИЧНІ ТА КОМПЬЮТЕРНІ ТЕХНОЛОГІЇ»-Харків:ХДТУСГ.-2002.-С.379-384.