Реферат за темою випускної роботи
Зміст
- Вступ
- 1. Технологічний процес як об'єкт автоматизації. Мета проектування і вимоги до пристрою автоматизації
- 2. Критичний огляд існуючих рішень і вибір базової апаратури автоматизації
- 3. 3 Обґрунтування напрямку автоматизації технологічної установки
- 4 Алгоритмізація блоку контролю лінійності вибою
- 5 Розробка структурної схеми блоку контролю лінійності вибою
- Висновки
- Список джерел
Вступ
Питання проведення своєчасної механізації технологічних установок, модернізації або заміні застарілого обладнання, впровадження комплексної автоматизації на підприємстві Н даний момент надзвичайно актуальні. Даний підхід дозволить підвищити ефективність і інтенсифікацію технологічних процесів, а отже поліпшити продуктивність шахти в цілому.
В даний час велика кількість аварій на очисних ділянках шахт відбувається через значні викривлення лінії вибою, що в свою чергу призводить до значних спотворень става призабійного конвеєра, пориву його ланцюгів і, до багатоденних простоїв лави, а, значить, і значних матеріальних втрат.
Вирішити це питання можна шляхом оперативного контролю за відстанню пересування кожної секції кріплення і відповідно става конвеєра з певним кроків і видачі відповідних сигналів управління на початок і кінець пересування механізованого кріплення. Розроблюваний блок повинен працювати в складі базової апаратури автоматизації механізованого комплексу і доповнювати його функціонально.
Таким чином, питання розробки пристрою автоматичного контролю лінійності забою дуже актуальне в даний час.
Технологічний процес як об'єкт автоматизації. Мета проектування і вимоги до пристрою автоматизації
Експлуатація забійних машин, комплексів і агрегатів пов'язана зі значними труднощами, зумовленими їх безперервним переміщенням, різноманітними гірничо–геологічними умовами, пилогазовим режимом шахти, її мікрокліматом та іншими факторами. Рішення задачі автоматизації забійних машин дозволить:
- підвищити продуктивність машин шляхом більш повного використання потужності їх електродвигунів;
- звільнити машиніста від функцій управління машиною з подальшим виведенням його з забою;
- підвищити якість видобутого вугілля і знизити його собівартість;
- поліпшити динамічні якості машин, їх надійність і продовжити термін служби;
- включити забійні машини в підсистему АСУ
очисні вибої
.
Системи автоматизації гірничих машин повинні задовольняти ряду вимог, пов'язаних зі специфікою шахтних умов роботи, і загальних вимог, що пред'являються до систем управління. Вони повинні задовольняти правилам безпеки, бути надійними в роботі, забезпечувати автоматичне регулювання швидкості подачі комбайна і положення виконавчих органів в профілі шару з метою виключення обробки різцями бічних вміщають порід. Системи автоматизації виїмкових машин повинні забезпечувати автоматичне відключення комбайна: при зупинці забійного конвеєра, догляді комбайна від пересунутих секції кріплення на відстань більш заданого, наявності перешкод на машинній дорозі, перевищенні допустимої концентрації метану на вихідному струмені і в місці роботи комбайна, припиняти подачу води в зрошувальний пристрій комбайна після досягнення ним вихідного положення по кінцях лави.
Система автоматизації виїмкового комбайна повинна також забезпечувати: миттєвий останов комбайна при установці швидкості подачі в нульове значення; розвантаження тягового органу при зупинці комбайна з подальшим стопоріння приводний зірочки механізму подачі; зниження швидкості подачі до нуля при пуску комбайна і тривалих перевантажень електродвигунів, а також фіксацію нульової швидкості подачі; двосторонній гучномовний зв'язок і сигналізацію в лаві.
Система автоматизации рабочего цикла забойной машины содержит систему автоматического регулирования (САР) нагрузки электродвигателей; систему автоматического управления перемещением машины в профиле пласта; средства автоматического контроля местонахождения горной машины и наличия препятствий на ее пути. Работа выемочной машины в автоматическом режиме, кроме того, должна согласовываться с работой гидрофицированной крепи, скребкового конвейера и средствами его автоматической передвижки.
На малюнку 1 приведена технологічна схема очисних робіт разом із засобами механізації.
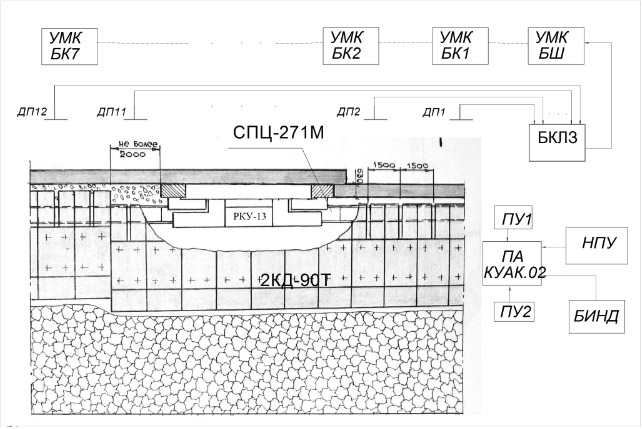
Малюнок 1 – Технологічна схема очисного вибою
На даний момент більшість апаратур автоматизації забійних машин і комплексів розраховано на регулювання навантаження на очисний комбайн, здійснення вірного алгоритму пуску/зупинки механізмів очисного вибою, забезпечення необхідних захистів і блокувань для безпеки праці робітників вибою і створення локальної системи автоматизації АСУ ТП очисний забій
.
Однак однією з проблем, які фігурують на даний момент при експлуатації очисних комплексів є нерівномірне пересування секцій кріплення, а слідом за ними і призабійного конвеєра, до якого секції пристиковані, після проходу комбайна. Це призводить до вигину конвеєра, розриву ланцюгів і його заклинювання, що негативно позначається на продуктивності роботи всього забою в цілому, призводить до зупинки роботи лави на кілька днів і значних матеріальних втратах.
Отже, метою досліджень є підвищення безпеки та ефективності роботи механізованого комплексу шахти шляхом вдосконалення його системи автоматизації.
Оскільки вдосконалення системи автоматизації піде за принципом розробки нового блоку контролю пересування секцій кріплення, то останній призначений для роботи в складі базової апаратури управління і повинен значно розширювати її функціональні і захисні можливості, а також мати досить високі експлуатаційні показники (надійність, простота обслуговування, і т . Д.).
Сформулюємо основні вимоги до розроблюваного пристрою:
- Забезпечувати управління переміщенням секцій кріплення;
- Оперативно контролювати місце розташування кожної секції кріплення; -
- Забезпечувати легкість і зручність експлуатації;
- Забезпечувати можливість експлуатації в екстремальних умовах (надзвичайна загазованість, 90% вологості, запиленість і т. п.);
- Забезпечувати можливість роботи в складі базової апаратури автоматизації очисних комбайнів;
- Мати мінімальні масогабаритні показники і собівартість;
- Задовольняти вимогам вибухозахисту та іскробезпеки.
2. Критичний огляд існуючих рішень і вибір базової апаратури автоматизації
Для очисного комбайна уніфікованого ряду РКУ–13 з гідравлічним механізмом подачі застосовується комплекс автоматизації типу КУАК.02. Комплекс забезпечує наступні основні функції:
а) з управління:
- пуск і відключення комбайна і конвеєра;
- завдання напрямку і швидкості руху комбайна;
- зміна положення виконавчих органів;
- відключення механізмів забою;
- заборона пуску комбайна і конвеєра при ремонтних роботах;
- контроль за роботою елеетрогідророзподільників;
- вибір режиму управління;
б) щодо захисту:
- від перекидання електродвигуна при затягнутому пуску;
- від зниження тиску води в системі зрошення та охолодження;
- від перегріву обмоток електродвигуна;
б)з діагностики:
- запам'ятовування причин відключення комбайна і розшифровка на табло;
- фіксування поломок окремих вузлів і видача рекомендації щодо їх усунення;
- контроль технічного стану окремих вузлів і блоків за допомогою світлодіодних індикаторів.
Структурна схема комплексу КУАК.02 наведена на малюнку 2.
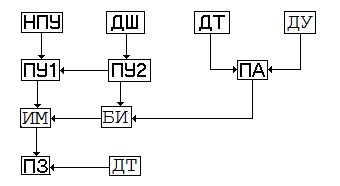
Малюнок 2 – Структурна схема КУАК.02
Склад апаратури КУАК.02: два пульта управління ПУ1 і ПУ2, носимий пульт управління НПУ, коробка розподільна КР, блок індикації Бі, панель захисту ПЗ, панель апаратів ПА, датчики швидкості ДС, рівня ДУ, датчик струму ДТ і термодатчик ДТм, ім–виконавчі механізми.
Принцип дії апаратури. Швидкість переміщення комбайна, напрямок його пересування, включення і відключення комбайна і конвеєра задається з основного пульта ПУ1 (див. 2.1). Після включення комбайна швидкість подачі зменшується до нуля, а потім плавно зростає з встановленої уставки (Vпуст=1,9 м/хв). При русі комбайна апаратура здійснює контроль сили струму приводного електродвигуна за допомогою датчика струму ДС. При збільшенні навантаження на електродвигун вище заданої уставки апаратура зменшує швидкість подачі комбайна. При різкому збільшенні навантаження спрацьовує апарат КОРД, який розташовується на панелі захисту ПО, і комбайн зупиняється. Управління ріжучими органами комбайна здійснюється з пульта ПУ1.
Особливістю комплексу КУАК.02 є те, що регулятор навантаження побудований на базі мікропроцесорних елементів, а також можливість управління комбайном за допомогою інфрачервоного випромінювання. Апаратура розташовується на очисному комбайні. Принцип дії полягає в наступному. Швидкість переміщення комбайна, його напрямок, включення і відключення комбайна і конвеєра здійснюється з основного пульта ПУ1. Після включення комбайна швидкість подачі зменшується до нуля, а потім плавно зростає з встановленої уставки (м / хв). При русі комбайна апаратура здійснює контроль сили струму приводного електродвигуна за допомогою датчика струму ДТ. При збільшенні навантаження на електродвигун вище заданої уставки апаратура зменшує швидкість подачі комбайна. При різкому збільшенні навантаження спрацьовує апарат КОРД, який розташовується на панелі захисту ПЗ, і комбайн зупиняється. Управління ріжучими органами комбайна здійснюється з пульта ПУ1..
Індикація про режими роботи комбайна висвітлюється в блоці індикації Бі. Апаратура також контролює рівень, тиск і температуру масла в гідросистемі подачі комбайна.
Воно призначене для управління механізмами очисного комплексу по допоміжних жилах силового кабелю або комбайна за допомогою додаткового кабелю, прокладеного по лаві, від очисного комбайна на штрек.
Працює разом з електрообладнанням ділянки – магнітними пускачами, станціями управління, а також разом з апаратурою сигналізації та зв'язку. Апаратура виконує 25 функцій з управління, захисту, блокування.
На апаратурі управління є лицьова панель, кнопки Пуск
, Стоп
і індикація, розділяється на п'ять груп: харчування, комбайн, конвеєр, лебідка, Насосні станції.
Для обсічення гучномовного зв'язку по лаві пропонується застосувати комплекс пристроїв управління забійними машинами КУЗ.03. Апаратура КЗЗ призначена для пуску і зупинки комбайнів, конвеєрів, маслостанцій з абонентським постом зв'язку, подачі і контролю проходження попереджувального сигналу перед включенням і початком переміщення, акустичного контролю роботи комбайна і двостороннього напівдуплексного гучномовного зв'язку між абонентами очисного вибою і штрека. Область застосування: очисні вибої, небезпечні по газу і пилу, спільно з апаратурою УМК, КД–а, ЦПУ, САУК. Виготовляється в 3–х модифікаціях: КУЗ.01, КУЗ.02, КУЗ.03. КУЗ.03 забезпечує двосторонній напівдуплексний зв'язок абонентів очисного вибою. Може застосовуватися для організації зв'язку на конвеєрних лініях або в інших протяжних гірничих виробках. КУЗ замінює апаратуру зв'язку АС–3см. У КЗЗ відсутній підсилювач потужності СГС, що підвищує надійність застосування більш сучасної динамічної головки з більш широкою смугою пропускання сигналів. Робітники мають однакову можливість користуватися зв'язком незалежно від місцезнаходження абонентського поста гучномовного зв'язку. Склад: блок живлення (БП) і 30 абонентських постів (ПА).
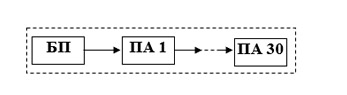
Малюнок 3 – Структура комплексу КУЗ.03
Як елемент, що перетворює кількість обертів барабана в рух, використовується цифровий лічильник, двійковий код на виході якого пропорційний цьому переміщенню, що дуже зручно адже не вимагає додаткового перетворення сигналу з датчика. До даного лічильника пред'являються вимоги щодо збереження інформації при можливих перервах харчування. З цією метою кожен датчик забезпечується додатковим електроблоком, з розташованим всередині нього акумуляторну батарею, про недоліки застосування якої говорилося раніше. Крім того, для контролю посування конвеєра використовуються лічильники, ємність яких повинна забезпечувати збереження величини посування конвеєра протягом усього терміну експлуатації системи.
3. Обґрунтування напрямку автоматизації технологічної установки
Як показує досвід експлуатації очисних комплексів в шахтах, на даний момент ще не вирішена одна проблема – проблема викривлення лінії посування механізованого комплексу, що відбувається через відсутність оперативного контролю за посування секцій кріплення і призводить до значних перекосів става конвеєра і поривів ланцюгів.Вирішення цього завдання дуже актуально, і на даний момент майже не має аналогів в промисловості. У работедостаточно широко досліджується математична модель лінії очисного вибою і системи автоматичного забезпечення її прямолінійності, отже в якості базових доцільно прийняти саме ці дослідження. Згідно в якості критерію ефективності функціонування системи управління запропоновано використовувати абсолютне відхилення фактичної від заданої лінії вибою, що необхідно мінімізувати на інтервалі, заданому ближніми і далекими межами вибою. Математичне вираження критерію записується у вигляді:
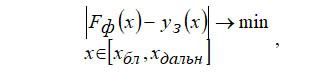
Формула – 1
На критерій (1) накладаються обмеження, викликані вимогами експлуатації:
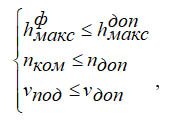
Формула – 2
Математичний опис лінії очисного вибою здійснено шляхом його подачі у вигляді інтерполяційного сплайна, заданого на сітці її окремих значень, отриманих за результатами маркшейдерських вимірів або за показаннями датчиків величини зрушення конвеєра. При такому описі, лінія очисного вибою може бути представлена як безперервна функція:

Формула – 3
Бажане положення лінії очисного вибою описується задає лінійкою & ndash; прямий, що лежить під заданим кутом по відношенню до осі:

Формула – 4
Неузгодженість заданого і фактичного станів ліній забою:
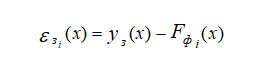
Формула – 5
Значення функції обчислюються з умови досягнення мети (1) з урахуванням можливостей системи подачі конвеєра на забій:
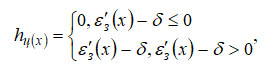
Формула – 6
Моделювання стріли прогину здійснюється методом ітерацій. В результаті моделювання був встановлений факт, що при зміні заданих параметрів прямолінійності, можливе накопичення стріли прогину і її перевищення допустимих меж, що суперечить обмеженню (2). Таким чином, розроблена система контролю за прямолінійністю вибою дозволяє забезпечити необхідну кривизну лінії очисного вибою, усунути простої вибою через перевищення допустимого ступеня кривизни, а, значить, її раціонально впровадити в промислове використання. До розроблюваного пристрою автоматичного контролю кривизни лінії очисного вибою слід поставити наступні вимоги:
1. оперативний контроль пересування секцій кріплення і призабійного конвеєра з відповідним кроком протягом всієї довжини лави;
2. контроль ступеня відхилення лінії забою від встановленої норми;
3. можливість ручного зміна уставок спрацьовування;
4. зручний інтерфейс оператора;
5. ссучасна елементна база;;
6. якомога менші габарити;
7. Рівень і вид вибухозахисту виконавчого пристрою РВ ІВ ІА, ДСВ –РО ІА;
8. Ступінь захисту від вологи і пилу виконавчого пристрою IP –54, ДСВ –IP –32.
4. Алгоритмізація блоку контролю лінійності вибою
В даному розділі необхідно розробити алгоритм автоматизації і надати його блок-схему. Алгоритм функціонування роботи пристрою контролю лінійності забою представлений на рис. 4. Робота пристрою наступна: спочатку відбувається подача напруги живлення на схему –блок 2, після чого здійснюється введення початкових уставок роботи блоку – N – кількість датчиків пересування в залежності від довжині лави (оскільки згідно доцільно встановлювати датчики через кожні 20 м, то максимальна кількість датчиків приймаємо 12 шт), m – кількість імпульсів від датчика за одну нормальну пересування, – максимально допустима похибка пересування (блок 3).
У блоці 4 реалізований цикл опитування кожного датчика пересування.
У цьому циклі відбувається наступне:
блок 5-видається дозвіл на початок пересування конвеєра з кріпленням-значить включається і–і гідродомкрат пересування;
блок 6-на блок управління надходить сигнал з i-го датчика пересування;
блок 7 вважається кількість імпульсів з датчика до тих пір, поки їх кількість не стане більше або дорівнює заподіяного;
блок 8 в цей час видається дозвіл на пересування крепи;
блок 9 при достатньому переміщенні конвеєра видається сигнал на заборону переміщення;
блок 10 відключення i-го гідродомкрата пересування.
Далі в блоці 11 відбувається перевірка або в допустимих межах лежить викривлення лінії вибою при переміщенні i–го ділянки конвеєра, і в разі неприпустимо великого викривлення видається аварійний сигнал блок 13).
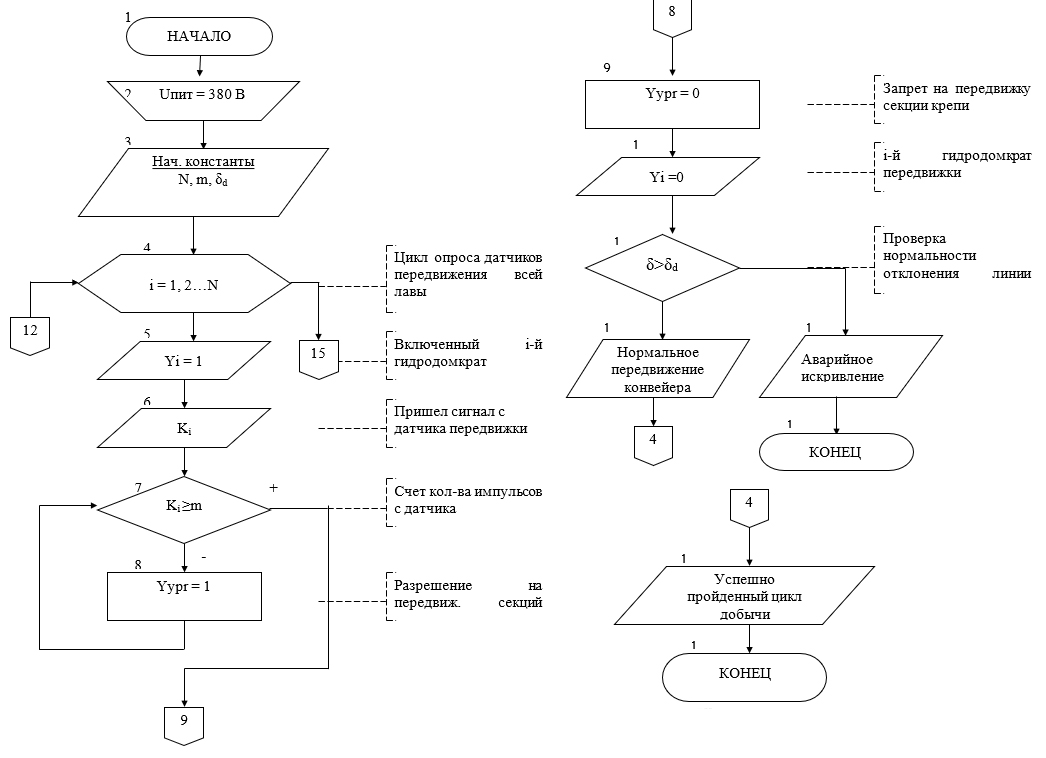
Малюнок 5 – Блок–схема роботи блоку контролю лінійності забою
У разі нормального пересування відбувається індикація нормального пересування конвеєра (блок 12). У блоці 15 відбувається завершення циклу, блок 16 – кінець роботи блоку.
5. Разработка структурной схемы блока контроля линейности забоя
Рассмотрим построение структурной схемы блока автоматического контроля линейности забоя, которая приведена на на малюнку 5
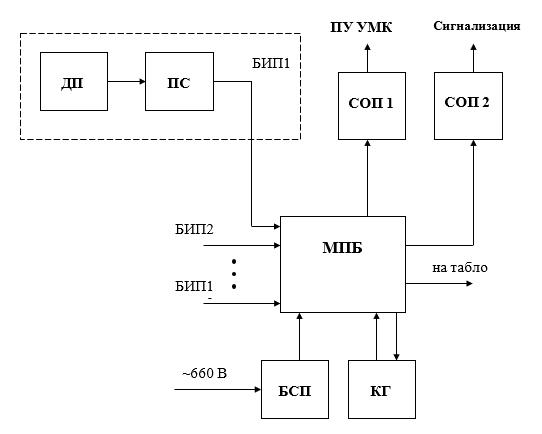
Малюнок 6 – Структурна схема блоку контролю лінійності вибою
Блок контролю лінійності складається з 12 блоків вимірювань пересування біп, блоку живлення стабілізованою напругою БСП, кварцового генератора КГ, 2–х блоків сімісторних оптопар СОП і мікропроцесорного блоку МПБ. Один блок вимірювання переміщення видає інформацію про пересування крепи і конвеєра, в його склад входить ДТП–датчик переміщення і ПС–блок перетворення сигналу (посилення сигналу). Мікропроцесорний блок управління може приймати інформацію максимально від дванадцяти блоків обробки даних, тобто про відстань пересування крепи і конвеєра в дванадцяти точках.
Мікропроцесорний блок управління обробляє отримані дані від датчиків переміщення. Отримані дані аналізуються і результат обробки виводиться на блок індикації, реалізовано в якості табло. При аварійних режимах, коли величина пересування в контрольованій точці значно відхиляється від встановлених норм відповідно до алгоритму, то мікропроцесор видає сигнал на пульт управління УМК про необхідність зупинки роботи очисного комплексу, оскільки подальше пересування може привести до пориву ланцюга конвеєра. Також у разі значного відхилення пересування норми видається відповідна Сигналізація Згідно розробленої структурної схеми блоку контролю пересування розроблена функціональна схема розроблюваного пристрою, наведеної на малюнку5.
Згідно рис.5 функціонально пристрій контролю лінії вибою складається з дванадцяти блоків вимірювання пересування, мікропроцесорного блоку, який здійснює обробку інформації за технологічними датчиків і видає керівні сигнали на УМК і сигналізацію через симісторні оптопари VU1, VU2 відповідно до закладеної в нього програми і реалізований на мікросхемі DD2, блоку перетворення протоколу обміну для подачі інформації на цифрове табло і реалізований на мікросхемі DD1. БІП1 складається з імпульсного датчика пересування DP1 і підсилювача А1, який служить для посилення сигналу через велику відстань передачі інформаційного сигналу, і обмежувача амплітуди ZL1 і стабілітрона STU1, які призводять інформаційний сигнал до виду, необхідного для використання в МПБ і здійснюють захист вхідних ланцюгів мікроконтролера від різких перепадів напруги з датчиків.
Висновки
Головним об'єктом дослідження даної роботи є очисний механізований комплекс шахти. Були розглянуті особливості технологічних режимів його роботи, послідовність дій при переміщенні комплексу слідом за просуванням лави, визначені точки, в яких необхідно контролювати пересування конвеєра, і визначені метрологічні вимоги до засобу вимірювання пересування.
Була розглянута апаратура автоматизованого управління роботою очисного комплексу на базі комбайна РКУ типу УМК, яка обрана в якості базової апаратури, і яка, однак, не володіє функцією контролю і захисту від вигинів призабійного конвеєра. У проекті розроблений автоматичний блок контролю лінійності вибою, розроблені структурна, функціональна, принципова електрична схеми. Розроблений пристрій можна застосовувати в системі автоматичного управління роботою очисного комплексу, як джерело вимірювальної інформації про стан викривлення лінії вибою і для попереджувальних дій в цьому напрямку. Вирішення цього питання дуже актуально для шахти і призводить до значної фінансової економії.
При написанні даного реферату магістерська робота ще не завершена. Остаточне завершення: Червень 2021 року. Повний текст роботи і матеріали по темі можуть бути отримані у автора або його керівника після зазначеної дати.
Список джерел
- Топорков А. А. Машинист горных выемочных машин: Учёб. для учащихся профтехобразования и рабочих на производстве.– М.: Недра, 1991. – 334 с.: ил.
- Комплекс автоматизированного управления АУК–3.
- Правила технической эксплуатации электроустановок потребителей и Правила техники безопасности при эксплуатации электроустановок потребителей / Глав. Упр. Гос. Энергетического надзора Минэнерго СССР.–4–е изд.–М.: Энергоатомиздат, 1989.–432с.
- Правила устройства электроустановок / Минэнерго СССР. – 6–е изд. перер. и доп. – М: Энергоатомиздат, 1985. – 640 с.
- Правила безопасности в угольных шахтах.–К.: Основа, 1996.–421 с. исслед.
- МИНПИ – ЮНЕСКО, ОАО «Автоматгормаш им. В. А. Антипова». –Донецк: Вебер, Донец. отд–ние, 2009.
- Автоматизация производства на угольных шахтах / Г.И. Бедняк, В.А., Ульшин, В.П. Довженко и др. – К.: Техника, 1989. – 272 с.
- Батицкий В.А., Куроедов В.И., Рыжков А.А., Автоматизация производственных процессов и АСУ ТП в горной промышленности: Учеб. Для техникумов. – 2–е изд., перераб. и доп. –М.: Недра, 1991.
- Электрослесарю добычного и проходческого оборудования: Справочник /Под.ред. В.А. Антипова. – Донецк: Донбасс, 1989. – 159 с.
- Груба В.И., Староверов К.С. Математическая модель фактического состояния линии забоя струговой лавы// Труды Донецкого государственного технического университета. Выпуск 7, серия горно–электромеханическая. – Донецк: ДонГТУ, 1999.– С. 69–74.