Abstract on the topic of the final work
Table of Contents
- Introduction
- 1. Relevance of the topic
- 2. Purpose and objectives of the study, planned results
- 3.Research and development overview
- 3.1 Analysis of the local ventilation fan as an automation object
- 3.2 Development of algorithm and circuit design device of the automated control system of the drive of the fan of local ventilation
- Conclusions
- List of sources
Introduction
Ventilation of mines and mines dangerous for gas and dust is one of the most important objects of automation, since with an ever–increasing degree of mechanization, the intensity of the introduction of mining operations, an increase in the capacity and depth of mines, which are accompanied by a significant increase in the release of harmful gases and dust in the mine atmosphere. That is why the improvement and research of the automated control system of the local ventilation fan is of great economic importance.
1. Relevance of the topic
To ensure the effective operation of the mine, it is necessary to carry out timely automation of technological processes using modern automation systems. Carrying out preparatory workings is associated with the manifestation of almost all natural and industrial hazards. Thus, during the preparatory workings, up to 35% of methane and coal dust explosions, 60% of gas–dynamic phenomena, and more than 9% of exogenous and endogenous fires occur. One of the ways to prevent these factors is to supply the required amount of air to the preparatory production in normal and emergency ventilation mode.[1]
2. Purpose and objectives of the study, planned results
The purpose of the development is to increase the efficiency of the technological process of ventilation of mine workings by developing an automated control system for the drive of a local ventilation fan. The developed automated control system should provide control and management of the ventilation process, both in normal and emergency modes of operation
Main tasks in the framework of the master's work:
- analysis of the process of ventilation of mine preparatory workings as an object of automatic control;
- overview of existing automatic ventilation control systems for mine preparation workings;
- Analytical study of the functional properties of ventilation units in the control of ventilation of the preparatory mine workings;
- development of a mathematical model of automated control;
- development of structural and functional schemes of the automated control system, the algorithm of its operation;
- development of a schematic diagram of an automated control system.
Object of study: local ventilation fan.
Subject of research: development and research of an automated control system for the drive of a local ventilation fan
3. Research and development overview
3.1 Analysis of the local ventilation fan as an automation object
3.1 Analysis of the local ventilation fan as an automation object
Ventilation of dead–end mine workings is one of the most important objects of automation, since the increasing degree of mechanization of coal mining, an increase in the capacity and depth of the mine are accompanied by a significant increase in the release of hazardous gases, dust and heat into the mine atmosphere.
In mines and mines that are dangerous for gas, the control of the methane content in the mine air is one of the main conditions for ensuring the safety of work. At the same time, the widespread use of electric energy and the conduct of blasting operations necessitate continuous and automatic monitoring of the methane content with the transmission of relevant information to the mine Manager. Installation of local ventilation fans should ensure: continuous and uninterrupted supply of the required amount of air to underground workings; the ability to control performance in the presence of a reserve of not less than 20% of the maximum flow; the transition from one fan to another and, if necessary, their joint work; possibility of reversal of air flow to not more than 10 min while maintaining a flow rate at least 60% of normal; the necessary control parameters of the operation; stable and efficient operation at simplicity and ease of use[2]
If a dead–end mine is ventilated with a VMP, then they must work continuously–this applies to gas and non–gas mines. To prevent re–suction with the help of the VMP of air coming from the dead–end mine (recirculation mode), the fan is installed in the mine, ventilated by a General shaft fan, no closer than 10 meters from the mouth of the passable dead–end mine.Ventilation of dead–end workings can be carried out in two ways: at the expense of a General mine depression, as well as with the use of parallel auxiliary workings; installation of local ventilation fans.Depending on the conditions of penetration, injection, suction and combined ventilation methods are used.The injection method of ventilation (figure 1) is the most common.[3]
The injection method is used in workings where combustible or toxic gases, as well as deoxygenated air, are released from the walls, roof or soil. In other cases, you can use any method of ventilation. The advantages of this method consist in intensive mixing of air in the bottom–hole space and diluting it with fresh air coming from the end of the air pipeline. The jet coming from the face goes out along the development to the mouth, capturing along the way all harmful and explosive gaseous impurities released from the walls, roof and soil of the development. The advantages include the fact that it is possible to use flexible (cloth rubberized and other) pipelines that are convenient in operation.[4]
The fan supply should not exceed 70% of the air flow in the workings at the place of its installation, which will ensure that the outgoing air flow from the dead–end workings along the workings section between the VMP and the mouth of the dead–end workings is illuminated at an average air speed of at least 0.15 m/s. To increase the reliability and safety of ventilation of dead–end workings, a backup VMP with backup power is installed along with the current one. Meeting these requirements will ensure the safe operation of the VMP.
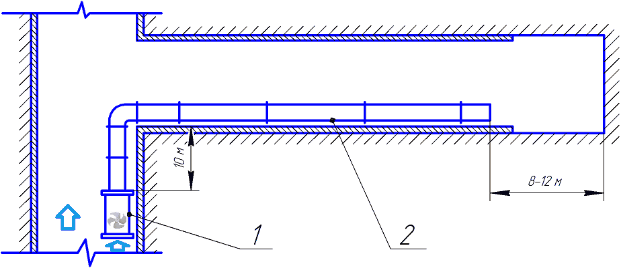
Figure 1 – Technological scheme of the injection method of ventilation
(animation: 7 frames, 5 cycles of repetition, 129 kilobytes)
The technological ones include gassing caused by coal (rock) and gas emissions during concussion blasting, as well as increased gas release during work to prevent sudden coal and gas emissions (hydrofluidization of cavities in coal pillars, etc.), during preliminary loosening, wetting, blasting coal, coal mining by combines, coal unloading from bunkers, roof rock collapses in the worked–out space and planned stops of ventilation degassing and gas–sucking installations.[5]
The main measures to prevent gassing of mine workings are:
- General or local (at gas sources) increase in air velocity;
- reduction and redistribution of gas release into mine workings by changing the schemes, methods of ventilation and degassing of coal seams and side rocks.
In order to avoid breaking the flexible pipeline when starting the local ventilation fan, the combined pipeline can only be used in conjunction with a special start–up control device that ensures a smooth increase in pressure and air flow in the pipeline when starting the local ventilation fan.
The normalized service life of various types of pipelines varies within 16–28 and 14–26 months, respectively, in dry and watered workings, in raw–from 14 to 26 months. In case of violation of the operating mode of pipelines, their service life is reduced by 2 times or more.
Therefore, to increase the reliability of flexible ventilation pipes, it is necessary to ensure a smooth start of the fan drive. Performing a smooth start with the required efficiency is possible only with the use of automatic fan drive control systems, in which the subjectivity factor introduced by the operator is minimal.
The ventilation parameters of dead–end workings provide for two main modes of operation:
- normal operation of the main (backup) local ventilation fan with continuous automatic control of the ventilation of the bottom–hole area;
- monitoring and control of the operating and standby local ventilation fan when they are switched on in normal or emergency modes.
The following methods of starting a local ventilation fan with an electric drive are possible:
- Pulse start using starters: pulse duration in the range from 1.5 to 3.0 seconds; pause duration between pulses from 6 to 10 seconds; number of pulses.
- Smooth start when using frequency converters: the duration of acceleration of the engine in the range from 30 to 120 seconds.
- Direct start–up of the backup local ventilation fan when the working one is switched off is carried out automatically, without smooth filling of the air duct.
Methods 1 and 2 provide for smooth filling of the pipeline with air to prevent water hammer, and the start according to method 3 is carried out when the working fan is turned off for a time not exceeding 10 seconds, which eliminates the possibility of water hammer. However, when the efficiency of using the resource of ventilation equipment is close for all start–up methods, method 2 provides a smooth increase in the voltage supplied to the motor, which leads to a decrease in starting currents and dynamic loads on the electric motor, increasing its service life.
The automatic control system for the local ventilation fan drive must be designed for operation in the following conditions:[6]
- explosive, aggressive environment;
- ambient air temperature from +4° to +40 ° C;
- monthly average relative humidity of 100% at +20 ° C;
- significant dust content;
- increased abrasive wear of work surfaces;
- limited working space.
Main functions performed by the automated control system for the local ventilation fan drive:
- automatic fan drive control;
- soft start of the electric drive of the local ventilation fan (local ventilation fan);
- control of the operation parameters of the electric drive local ventilation fan;
- automatic start of the backup electric drive local ventilation fan;
- monitoring the level of methane concentration in the air entering the dead–end production;
- providing communication with the remote control of the mining dispatcher using the RS 485 communication interface, via the ModBus Protocol.
3.2 Development of algorithm and circuit design device of the automated control system of the drive of the fan of local ventilation
To improve the efficiency of airing of mine workings is necessary to automatically manage the process of ventilation depending on the current values of parameters of the mine atmosphere generation, her zagazirovanie, the air supply to the face and efficiency of the fans. Figure 2 shows an algorithm for the operation of an automated fan drive control system.
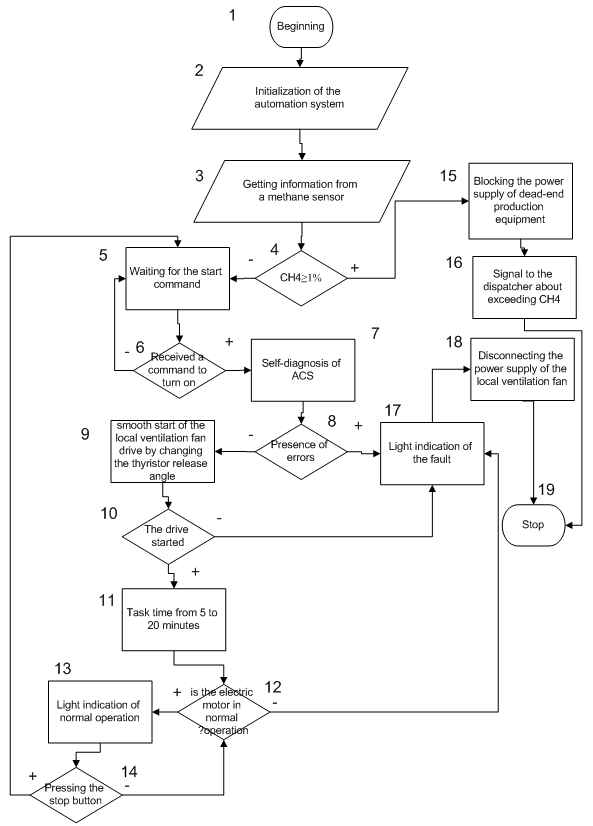
Figure 2–Block diagram of the algorithm for automatic control of the local ventilation fan drive
Descriptions of the block diagram of the algorithm for automatic control of the local ventilation fan drive:
- During the initialization of the automatic control system, the initial data is set in the control system (1)
- Receiving information from a sensor located directly at the local ventilation fan (2)
- Analysis of the received information from the sensor (3)
- If the level of methane concentration in the air is less than O1%, the automatic control system of the local ventilation fan drive is waiting for the command to turn on (4)
- If a command is received to turn on the local ventilation fan drive, the system performs a self–diagnosis mode in order to determine possible technical malfunctions of the sensors, comparing their readings with the reference range of values (7)
- In case of deviations from the range of reference values or lack of communication with the sensor (8)
- The system smoothly starts the electric drive of the local ventilation fan (9)by adjusting the opening angle of the transistors)
- Waiting for a response from the air velocity sensor installed in the ventilation pipe (10)
- Sets the time at which the air velocity sensor monitors the ventilation process of the dead–end mine (11)
- Air speed sensor survey (12)
- Designation of the normal operation of the local ventilation fan(13)
- Waiting for the stop button to be pressed(14)
- The concentration of the methane level exceeds more than 1%, and the power supply to consumers of the dead–end production is blocked(15)
- A signal is sent to the dispatcher about exceeding the methane concentration level (16)
- Fault indication light (17)
- Local ventilation fan drive power off (18)
the Functional diagram is shown in figure 3. the automatic control system for the local ventilation fan drive is a local automation system with information output to the UTAS system via the RS–485 communication interface.
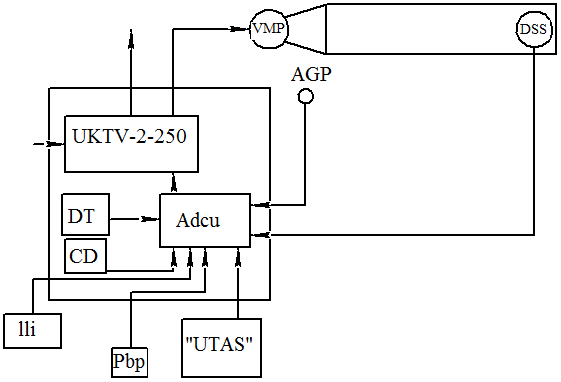
Рисунок 3 – Функциональная схема системы автоматического управления приводом вентилятора местного проветривания
Figure 3 Shows: UKTV–2–250– complete explosion–proof control Device; Pbp– push–button post; lli – local light indication; Adcu – automated drive control unit; DT– temperature sensor; CD – cooling device; DSS –air speed sensor; AGP – automatic gas protection sensor; VMP – fan local ventilation
UKTV–2–250 –the Device is designed to provide remote controlled smooth start, drive control and disconnection of three–phase asynchronous motor, used in AC networks with voltage 660/1140 In with the isolated neutral of the transformer[7].
The device is designed for operation in underground mine workings dangerous for gas (methane) and coal dust, in climatic areas with moderate, cold and tropical climates.
The device combines the functions of a starter and a thyristor regulator. The device allows to exclude transient starting torques in the motor and significantly reduce the dynamic stress.
Main functions performed:
- Ability to work in the starter mode.
- Remote control from the push–button post.
- Protection against short–circuit and overload currents in outgoing power circuits.
- Zero protection.
- Protection in case of breakage or increase in the resistance of the grounding circuit between the device and the electric motor to a value of more than 50 Ohms.
- Protection against loss of control when the wires of the remote control circuit are closed between themselves or with the ground wire.
- Protection against self–switching of the device in case of a short–term (no more than 3 s) increase in the supply circuit voltage to 150% of the rated voltage.
- Checking the operation of the control circuits and circuits of the contactor coils without applying voltage to the outgoing connection.
- Switching off the device when the control pulses on the power thyristors disappear
- Disconnecting the device when the synchronization pulse is lost in one or more channels.
- Disconnecting the device when the thermal protection of thyristors is triggered.
- protection of the device against phase breakage. the
- Protection against breakdown of the thyristors.
- Automatic phasing of the thyristor control system relative to the phases of the supply network.
- Light signaling about the operation of protections, locks and the state of circuit elements.
The Block diagram is shown in figure 4. the system of automatic control of the local ventilation fan drive is a local automation system with information output to the UTAS system via the RS–485 communication interface.
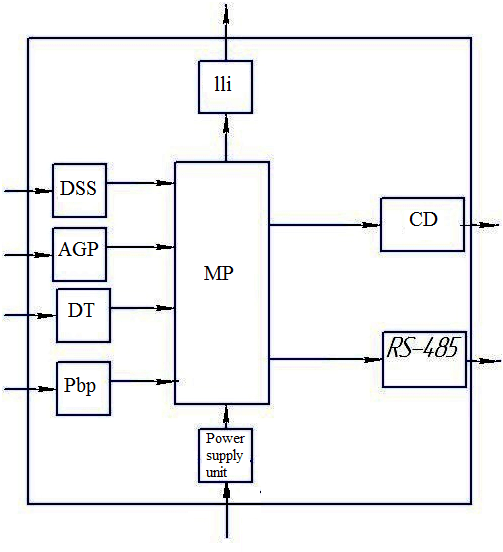
Figure 4–Block diagram of the device of the automatic drive control unit
Figure 4 shows: DSS – air flow rate sensors of the TH5921 series are designed to control the air flow rate in ventilation tunnels, exhaust pipes, AGP – automatic gas protection based on the methane sensor THM –2.8 is used to determine the level of methane concentration in the air, DT – thyristor temperature sensor is used digital temperature sensor DS18B20
Conclusions
As a result of the research work, the local ventilation fan was analyzed as an object of automation. Based on the analysis, review of literature sources,the operating modes, main features and characteristics of the local ventilation fan of the coal mine were considered.< /p>
the purpose of the work was formulated, which was to increase the efficiency of the technological process of ventilation of mine workings, and also the requirements for the automatic control system were formulated.
In the analysis, adopting these requirements was chosen as a basic instrument of automation, the algorithm of the proposed circuit solutions for the automatic control device actuator of the fan of local ventilation to improve the efficiency of the process of ventilation.
When writing this abstract, the master's work is not yet completed. Final completion: June 2021 of the year. Full text of the work and materials on the topic can be obtained from the author or his supervisor after the specified date.
List of sources
- Александров С. Н. , Булгаков Ю. Ф. , Яйло В. В. Охрана труда в угольной промышленности: Учебное пособие для студентов горных специальностей высших учебных заведений / Под общей ред. Ю. Ф. Булгакова. – Донецк: РИА ДонНТУ, 2007.– 516 с.
- Малиновский А. К. Автоматизированный электропривод машин и установок шахт и рудников / А. К. Малиновский. — Москва: Недра, 1987. — 280 с.
- Ивановский И. Г. ШАХТНЫЕ ВЕНТИЛЯТОРЫ / Учеб. пособие.— Владивосток: Изд—во ДВГТУ, 2003. — 196 с. илл. 86, табл. 7
- Голинько В. И. Вентиляция шахт и рудников: учеб. пособие / В. И. Голинько, Я. Я. Лебедев, О. А. Муха. — Д.: Национальный горный университет, 2012. — 266 с.
- Карпов И. Э. Автоматическая газовая защита и контроль рудничной атмосферы / Е. Ф. Карпов, И. Э. Биренберг, Б. И. Басовский.—Москва : Недра, 1984.—285 с
- Правила безопасности в угольных шахтах [Электронный ресурс]: утв. приказом Гос. Комитета горного и тех. надзора ДНР и Министерством угля и энергетики ДНР 18.04.2016 г. № 36 / 208: ввод в действие 17.05.2016. — Донецк, 2016. — Режим доступа:https://minsvyazdnr.ru
Научно—производственное предприятие
.– Режим доступа : http://mzsha.inf.uaМакеевский завод шахтной автоматики