Abstract
Содержание
Introduction
In modern steelmaking production, out-of-furnace treatment with calcium-containing flux-cored wires occupies a leading position due to the multifactorial effect of calcium on the physicochemical state of the melt, macro- and microstructure of the workpiece, quality and properties of metal products and is an integral part of the technology.
Among the calcium-containing ones, the most widespread is the wire filled with silicocalcium powder. In world metallurgical practice, at present, silicocalcium of the SKZ0 grade is the most widely used alloy for introducing calcium into steel. This is due to the fact that such a ratio of components in the alloy (30% Ca and 60% Si) provides an optimal combination of the main thermophysical parameters in ferroalloy production that affect the absorption of calcium. It should be noted that in the production of silicocalcium with a calcium content of more than 30%, costs increase sharply and at the same time difficulties arise with the separation of the ferroalloy from the slag, therefore, all world manufacturers, as a rule, limit themselves to the production of SK30 silicocalcium. At the same time, in recent years, due to the changing situation on the ferroalloy market and changes in the quality of raw materials, a tendency has emerged to use a complex filler under certain conditions, sometimes called silicocalcium SK40. There is no such brand of silicocalcium in GOSTs, and this material is not produced, but is obtained by mechanical mixing of silicocalcium and metallic calcium powders. In the process of introducing the wire, an alloy is formed and the required calcium content in the ferroalloy is achieved directly during the processing of the liquid iron-carbon melt.
1. Theme urgency
Among the currently existing technologies for deoxidation (refining from oxygen) of steel (SCAT, TN and others), one of the leading places in solving the problem under consideration is the technology of processing the PP melt (powdered calcium silicate wire). In the SCAT process, calcium-containing materials enclosed in a projectile are fired from a pneumatic gun deep into the melt at an initial velocity of 20-100 m / s, while the TN process is blown with a powder mixture in an argon stream through a water-cooled lance introduced almost to the bottom of the ladle. Among the calcium-containing ones, the most widespread is the wire filled with silicocalcium powder. In contrast to the others noted above, it includes simpler equipment, less danger to service personnel and more efficient technology.
When implemented, energy costs are lower, incl. heat energy losses. It is necessary to note the high temperature of silicocalcium, as a deoxidizing agent, when interacting with oxygen dissolved in the steel melt, which is due to the presence of a steel shell on the surface of the PP, which makes it possible to heat up during its melting when it is introduced into the metal and, therefore, to increase the temperature of this interaction.
3. Study overview
For out-of-furnace steel treatment, Fig. 1 shows a diagram of the "ladle-furnace" installation and can be microalloyed with flux-cored wire with a silicocalcium filler.
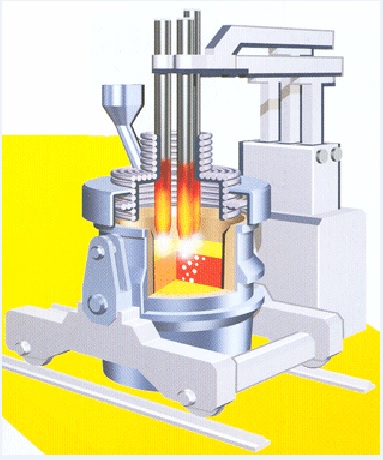
Figure 1 – General scheme of installation ladle-furnace
As a criterion for the efficiency of out-of-furnace treatment of PP steel, as is known, the degree of assimilation of the introduced elements by the steel, i.e., the ratio of the total content of the element in the metal to the amount introduced, (%) is used classically. The stages of melting PP with silicocalcium filler with a melting temperature of 1280°C have the sequence shown in Fig. 2.
At the initial moments of time, at stage I, the geometry of the PP section is characterized by two regions: 1 - solid PP filler and 2 - PP lithium shell.
Then, at stage II, as the filler melts, the third region is formed - the PP filler melt. And, finally, upon completion of the filler melting, we again return to two regions, one of which, instead of the solid phase of the PP filler, turns into its liquid state
The refining method with a silicocalcium filler PP, the shell of which is formed of a certain steel grade, was used by us to create the thermotechnical prerequisites for the deoxidation of steel by a wire with a shell of an alloying element, the melting point of which is lower than that for a steel shell, but higher than for silicocalcium. In this case, when PP is introduced into the steel melt, silicocalcium first melts, then the shell of the alloying element, and only after that the steel crust, frozen on this shell when PP is introduced into the metal.
In order to increase the efficiency of the technological process, the PCB should be fed vertically to the metal mirror, at a distance of ½ radius of the steel ladle from its side. In this case, the curvature of the PP during its motion in the melt is relatively small. If the speed of insertion of the PCB exceeds the optimum, the wire sheath may melt with a delay, causing the PCB to move back after reaching.
At the same time, the mode of PP injection for intensification of mass transfer processes should only ensure its complete melting below a certain level and there is no need for the end of the PP to reach the bottom of the ladle. Full realization of the deoxidizing effect of Ca on the steel melt is achieved not only by the optimal choice of the PP injection rate into the bath, but and taking into account the specificity of this element, for example, high reactivity to the components of the melt, etc. As a criterion for the efficiency of out-of-furnace treatment of PP steel, as is known, the degree of assimilation of the introduced elements by steel is used classically, i.e. the ratio of the total content of the assimilated element by the metal to the amount introduced, (%).
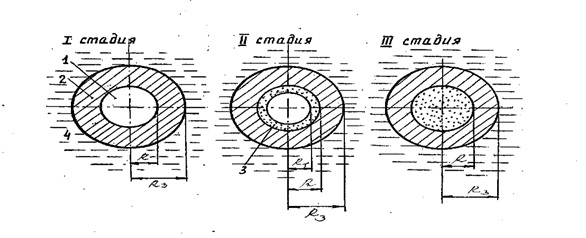
Figure 2 – Melting stages of PP with silicocalcium filler and lithium shell
Conclusion
One of the effective deoxidizers is silicocalcium. Energy-saving mode of technology in the intensification of heat and mass transfer processes in liquid steel is realized by rational choice of PP velocity, its diameter and number of wires, simultaneously introduced into the melt.