Abstract
Content
- Introduction
- 1. Theme urgency
- 2. Goal and tasks of the research
- 3. Liquid aluminum and its properties
- 3.1 The influence of hydrogen on the quality of aluminum products.
- 3.2 Saving argon as a factor in energy saving
- 4. Saving argon as a factor in energy saving
- Conclusion
- References
Introduction
At the moment, the main method for producing argon is by the method of low-temperature rectification of air with the production of oxygen and nitrogen and the associated extraction of argon. Its extraction is difficult, so the air is preliminarily converted into a liquid state and argon is released from it. This process is multiple. Argon in metallurgy is most often used for blowing liquid metal for the purpose of refining from harmful impurities and the chemical composition of the melt by the volume of the liquid bath. In this regard, there is a reason for saving argon due to its high cost. An important factor in energy saving is the reduction of argon consumption to the optimum level.
1. Theme urgency
The refining effect of argon, as a rule, is not fully used due to the insufficient kinetic conditions for the interaction of argon bubbles with liquid metal for the full realization of the thermodynamic possibilities of the transition of CO molecules (during decarburization) and Í2 (during degassing) into argon bubbles. This is mainly caused by the insufficient surface of the gas-metal phase interface and their short interaction time. Both are due to the excessively large bubble size. Therefore, when flushing metal with argon in a ladle, it is very important to ensure the maximum reduction in bubble size.
Then there is a huge increase in their total surface, i.e. surface of the gas-metal interaction, and an increase in the residence time of the bubbles in the metal, since the speed of the rise of small bubbles is much less than that of large ones. According to Stokes, the bubble rise rate is proportional to the square of the bubble radius. The master's work is devoted to the urgent scientific task of developing a unified approach to argon purging
2. Goal and tasks of the research
Purpose of the work: substantiation of the energy-saving mode during the intensification of the diffusion process under the conditions of out-of-furnace degassing of the aluminum melt from dissolved hydrogen by blowing with argon.
Main tasks of the research:
- thermotechnical aspects of argon production;
- properties of liquid aluminum;
- the effect of hydrogen on the amount of aluminum products;
- current state of the art on the intensification of heat and mass transfer processes during out-of-furnace degassing of liquid metals from hydrogen by blowing with argon and vacuum;
- Design of alternative variants of basic stages of unified Moore FSM synthesis process and estimate of it's efficiency. substantiation of the energy-resource-saving mode of out-of-furnace degassing of liquid aluminum from hydrogen under conditions of intensification of the process of heat and mass transfer in the melt using a mathematical model
3.Liquid aluminum and its properties
The third energy level of the aluminum atom contains three electrons, and in chemical compounds it is usually trivalent. Crystallizes in a face-centered cubic lattice. Aluminum is chemically active. Even under normal conditions, it interacts with atmospheric oxygen, becoming covered with a very thin and durable film of Al2O3. It protects aluminum from further oxidation and gives it a fairly high corrosion resistance, and also weakens its metallic luster. Its corrosion resistance is due to its cleanliness. Of all the impurities found in aluminum, iron is the most harmful.When heated in a finely divided state in air, aluminum ignites and burns with the release of a large amount of heat. When heated above 800 ° C with the formation of aluminum nitride, AlN interacts with aluminum nitrogen. The interaction of aluminum with carbon begins at 650 ° C, but at 1400 ° C it proceeds vigorously with the formation of aluminum carbide Al4C3. Aluminum dissolves in hydrochloric acid and alkali solutions.Dissolution in sulfuric acid and dilute nitric acid is slow. Applications: Possesses a number of properties that distinguish it favorably from other metals. It is light in density, good ductility, and it is also non-toxic, non-magnetic and corrosion-resistant to a number of chemicals. Found exceptionally wide application in various branches of modern technology.
3.1 The influence of hydrogen on the quality of aluminum products.
[1]. In practice, the hydrogen content in aluminum depends on the type of melting and can reach 0,5 ñì3/100 ã = 2,4×10-3 %(by weight). When cooled and crystallized, hydrogen is released with the formation of pores in the aluminum ingot. The pores range in size from 5 to 1000 microns. In addition, with an increased hydrogen content, nuclei of hydrogen bubbles (flockens) are formed. Typically, the pressure in the flock is greater than the strength of the aluminum, which causes defects. If the pores are located near the surface, then when heated, bubbles form, which is dangerous for thin sheets in autumn. Deeply lying pores negatively affect the quality of aluminum during deformation (hot rolling). These pores are the places of rupture, and in high-strength aluminum alloys - sources of cracks. With an increase in the hydrogen content, the elongation decreases, the yield stress decreases, the specific viscosity decreases
3.2 Saving argon as a factor in energy saving
The raw material for producing argon is atmospheric air containing in a chemically unbound state oxygen, nitrogen, argon, carbon dioxide, krypton, xenon, neon and other gases. Therefore, the separation of argon from air requires less energy consumption than when it is obtained from a substance containing it in a bound state. The most economical way to separate air is its low-temperature rectification, based on the difference in boiling points of the constituent parts of liquid air.This process requires preliminary air liquefaction. Liquefaction of air and its separation by rectification are processes that include heat and mass transfer, evaporation and condensation, expansion and contraction of gases and liquids. Various machines and devices are used to carry out these processes. [9-10].
4. Saving argon as a factor in energy saving
The raw material for producing argon is atmospheric air containing in a chemically unbound state oxygen, nitrogen, argon, carbon dioxide, krypton, xenon, neon and other gases. Therefore, the release of argon from air requires less energy consumption than when it is obtained from a substance containing it in a bound state. Consider the basics of the air throttling process. Throttling consists in reducing the pressure in the gas stream when it is passed through a device that creates a resistance. In this case, there is no exchange of energy in the form of work and heat with the environment. The throttling of real gases is usually accompanied, as D. Joule established, by a change in temperature. This phenomenon is called the Joule-Thompson effect. A diagram of the throttling process is shown in Fig. 4.1 [11].
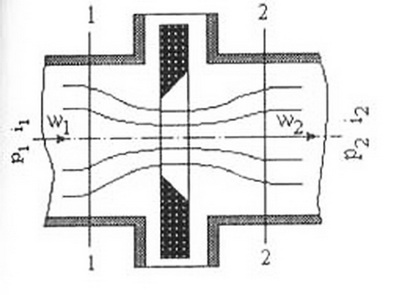
Figure 4.1 – Gas throttling process diagram
When the gas pressure changes from p1 to p2, its temperature changes from 1 to 2. Since there is no energy exchange with the environment, the enthalpy of the gas before throttling and after it remains unchanged ³1 = ³2. Let us consider the change in the magnitude of the throttling effect under various conditions on the s - t diagram of a real gas, (Fig. 4.1) on which the lines of constant enthalpy are plotted. [12
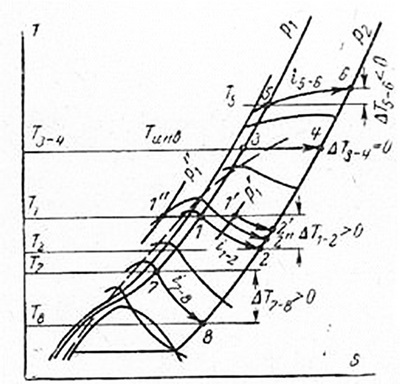
Figure 4.2 – Change in throttling effect depending on temperature and pressure
When the air is throttled from the initial pressure p1 and temperature T0 (point 1) to pressure p2, the final state will correspond to point 2, which lies at the intersection of isobar p2 with the line of constant enthalpy ³1 = ³2, since the enthalpy value after throttling will not change. Point 2 lies on the T2 isotherm. Therefore, the temperature change T (1-2) = T(1-) T2 can be determined from the diagram. As seen in Fig. 4.2, all lines of constant enthalpy have a maximum, which in the high temperature region moves towards lower pressures, becomes less pronounced and, finally, at a temperature Tinv (T (3-4) = 0) disappears. If we connect the maxima of these lines, we get the inversion curve shown in Fig. 4.2 by a dashed line that divides the diagram into two areas.
Conclusion
To meet the requirements of various consumers, argon production technology must provide both high quality and low cost argon. The process of obtaining technically pure argon consists of three stages: a) extraction of crude argon from the air; b) purification of raw argon from oxygen; c) purification of argon from nitrogen. Raw argon is extracted from the air in two stages: 1) obtaining an air separation apparatus in a rectification column and sampling an argon fraction containing from 5 to 12% argon. 2) enrichment of the resulting argon fraction, carried out in a special argon column.The resulting crude argon containing 70-95% Ar (the remaining 30-5% are nitrogen and oxygen) serves as the initial product, after purification of which from oxygen and nitrogen, commercially pure argon is obtained. Argon has many practical applications. This paper discusses its use in the technology of out-of-furnace degassing of liquid aluminum from hydrogen by blowing with argon, which was first developed by a group of scientists led by Academician V.L. Naidek.
When writing this essay, the master's work has not yet been completed. Final completion: May 2021. The full text of the work and materials on the topic can be obtained from the author or his manager after that date.
References
- Arsentiev, P.P. Argon in metallurgy / P.P. Arsentiev. - M .: Metallurgy, 1971. - 120 p.
- Bornatsky, I. I. Out-of-furnace refining of iron and steel / I. I. Bornatsky, V. I. Machikin, V. S. Zhivchenko. - Kiev: Technique, 1979 .-- 167s.
- Belov, I. V. Effect of mass transfer in the system of gas bubbles and liquids / I. V. Belov, E. V. Prokolov // Journal of Applied Mechanics and Technical Physics. - 1969. - No. 1. - p. 116 - 121.
- Brandt, B.B., Perazich D.I., Regime of liquid flow around large gas bubbles, Inzhenerno-fizicheskii zhurnal. - 1966. - T. 10. - No. 2. - S. 197 - 200.
- Levich V.G. Physicochemical hydrodynamics / V.G. Levich. - M .: Fizmatgiz, 1959 .-- 537 p.
- Shifrin V.M., Kadinov E.I. Investigation of the efficiency of metal degassing when blowing it with argon in a ladle / V.M.Shifrin, E.I.Kadinov // Izvestiya vuzov. Ferrous metallurgy. - 1975. - No. 12. - p. 59-64..
- Pozdeev, NPInfluence of argon consumption on degassing. melt in vacuum / N.P. Pozdeev, A.G. Shalimov, I. V. Khalyakin // Theory of metallurgical processes. - M .: Metallurgy 1975. - No. 3. - p. 23 - 33
- Berdnikov, V.I. Behavior of hydrogen when blowing steel with an inert gas / V.I.Berdnikov // Izvestiya vuzov. Ferrous metallurgy. - 1972. - No. 8 - p.21 - 25.
- Turkan, S. Entgasung von Metall – schmelzen mit Blasenschwarmen / S. Turkan, K. Lange // Stell Res. – 1985. – Bd. 56. – ¹ 5. – P. 247 – 253.
- Naydek V.L., Narivsky A.V. Degassing of aluminum alloys by vacuum-plasma treatment of their melts // Processes of casting. - 2008. - No. 3. - from. 35-38.
- Zakharov N.I., I.V. Volkova Physical model of diffusion interaction of argon bubbles with aluminum melt // Engineering Physics Journal.-2017.-t.90.-¹4.-p.1036-1038
- Zakharov N.I. Intensification of heat and mass transfer processes in the refining of liquid steel from gases.-Donetsk: Digital Printing House.-2016.-204s..