Реферат по теме выпускной работы
Содержание
- ВВЕДЕНИЕ
- 1. МАТЕРИАЛЫ И ТЕХНОЛОГИИ ИЗГОТОВЛЕНИЯ ЩЕЛЕВЫХ СИТ ДЛЯ ГРОХОЧЕНИЯ И ОБЕЗВОЖИВАНИЯ МИНЕРАЛЬНОГО И ОРГАНИЧЕСКОГО СЫРЬЯ.
- 2.CВАРКА НЕРЖАВЕЮЩИХ СТАЛЕЙ
- 2.1. Влияние чистоты газа на сварку
- 2.2. Режимы сварки
- 3.ОБРАБОТКА РЕЗУЛЬТАТОВ
- ВЫВОДЫ
- Список источников
ВВЕДЕНИЕ
Щелевые сита используются, главным образом, в качестве поверхностей для технологического применения в процессах сгущения, обезвоживания, прессования, высушивания, ферментации в пищевой перерабатывающей промышленности, сахароварении, солодоварении и во многих других отраслях (пивоварении, кондитерском производстве, мясоперерабатывающей промышленности и пр.). А также они применяются в химической, фармацевтической и перерабатывающей промышленности для схожей технологии, при обогатительных процессах угольной и горнорудной промышленности, при обезвоживании разных суспензий и шлама на станциях очистки сточных вод и т. д. [1].
Щелевые поверхности сит выдерживают значительную нагрузку на единицу площади (до нескольких сот кг). Рабочая поверхность гладко обработана, она обладает ровной, цилиндрической или другой формой (конусы, круглые, параболические поверхности и т.п.). Для увеличенных нагрузок и для повышения прочности поверхности сит в технологическом оборудовании необходимо применить упрочняющие технологии.
1. МАТЕРИАЛЫ И ТЕХНОЛОГИИ ИЗГОТОВЛЕНИЯ ЩЕЛЕВЫХ СИТ ДЛЯ ГРОХОЧЕНИЯ И ОБЕЗВОЖИВАНИЯ МИНЕРАЛЬНОГО И ОРГАНИЧЕСКОГО СЫРЬЯ
Шпальтовые сита представляют собой плоские карты с гладкой поверхностью и собираются из отдельных проволочных колосников фасонного профиля с вырезами, проушинами или витками для несущих либо соединительных реек или шпилек, располагаемых на определенном расстоянии друг от друга перпендикулярно к направлению колосников [2]. Для изготовления проволочных колосников сеток должна применяться:
- Проволока из стали марок 08Х18Н10, 12Х18Н9, 12Х18Н9Т, 12Х18Н10Т, 10Х17Н13М3Т термически обработанная светлого отжига или травленая по НТД;
- Проволока из стали марки 12X13 термически обработанная оксидированная по ГОСТ 18143;
- Проволока низкоуглеродистая из сталей 08кп; 10; 15; 20 по НТД.
Для сеток с размером щели до 0,3 мм включительно должна применяться стальная проволока, термически обработанная, светлого отжига, повышенной точности - низкоуглеродистая по ТУ 14-4-1563, высоколегированная по ТУ 14-4-1571 и латунная полутвердая или мягкая повышенной точности проволока по ГОСТ 1066 [3].
2. CВАРКА НЕРЖАВЕЮЩИХ СТАЛЕЙ
Хромистые стали склонны к подзакалке на воздухе, которая в сильной степени зависит от содержания углерода. Лучше всего свариваются стали с очень низким содержанием углерода (≤ 0,08% С), например сталь 0Х13. Сталь марки 1Х13 сильнее подзакаливается, так как при нагреве около 1000°С она становится полностью аустенитной и при охлаждении даже на воздухе происходит γ - М-превращение.
При сварке ферритных сталей с 14-28% Cr сварные швы получаются хрупкими и часто растрескиваются. Поэтому сварку сталей следует производить в подогретом состоянии при ≈ 200°C, но разогрев металла во время сварки должен быть минимальным. Лучшие результаты получаются при электродуговой, чем при газовой сварке. После сварки сварное соединение рекомендуется нагреть до 720-780°C и быстро охладить.
Стали с 15-17% Cr иногда при сварке подкалиаются. Чтобы это избежать, рекомендуется применять стали с присадкой титана или ниобия, а в случае стали с 13% Cr – с присадкой 1% Al [4].
Аустенитные стали обладаю пониженной температурой плавления (1400°С), более низкой теплопроводностью и высоим коэффициентом линейного расширения, чем углеродистые стали. Поэтому при сварке этих сталей расплавление идет быстрее с большим перепадом температуры от сварного шва к основному металлу. Нестабилизированные титаном или ниобием стали типа 00Х18Н10, 0Х18Н10, Х18Н9 при сварке приобретают склонность к межкристаллитной коррозии и тем больше, чем выше содержание углерода [4].
2.1. Влияние чистоты газа на сварку
Обычно сварку вольфрамовым электродом в среде инертного газа (TIG) целесообразно использовать при сварке металлов толщиной до 7,0 мм. Если толщина не превышает 1,5 мм, применение других способов дуговой сварки нецелесообразно из-за риска образования прожогов. При аргонодуговой сварке в среде аргона или гелия наблюдается минимальный угар легирующих элементов и повышается стабильность дуги.
Сварку аустенитных нержавеющих сталей можно выполнять непрерывно горящей, либо импульсной дугой. Благодаря особенностям теплового воздействия импульсная дуга позволяет уменьшить ширину околошовной зоны и коробление свариваемых деталей, а также сварить металл малой толщины и обеспечить хорошее формирование шва.Чем ниже содержание Н2О в составе защитной среды, тем выше показатель теплопроводности дуги, за счет чего обеспечивается более высокая температура сварочной ванны. Таким образом применение аргона высокой чистоты способствует более полному газовыделению из расплава в зоне сварки, следовательно, снижается вероятность образования пор[5].
Режим подачи аргона и его количество в горелке должны быть оптимальными и стабильными. Необходимо особо отметить, что увеличение скорости подачи газа зачастую не улучшает, а иногда и ухудшает качество защитной среды. При высоком давлении и большой скорости газа в горелке возникает турбулентный поток, что вызывает смешивание аргона с воздухом в зоне сварки [5].
2.2 Режимы сварки
Режим автоматической и механизированной сварки плавящимся электродом в защитных газах характеризуется диаметром проволоки, напряжением на дуге, скоростью подачи проволоки и связанной с ней силой тока, расходом защитного газа.Ориентировочные режимы автоматической и механизированной сварки плавящимся электродом приведены на рисунке 2.1.
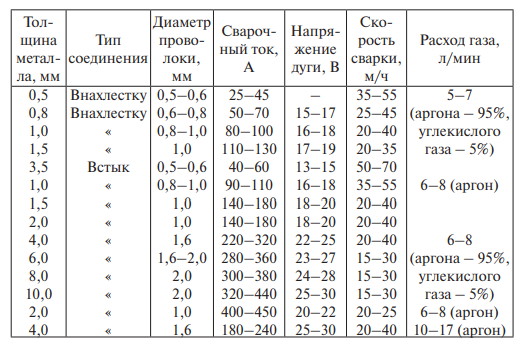
Рисунок 2.1 – Режимы автоматической сварки стыковых соединений из аустенитных хромоникелевых сталей плавящимся электродом (проволока Св-04Х19Н11М3)[5]
Независимо от размеров свариваемого изделия оптимальной скоростью подачи проволоки диаметром 0,8–1,2 мм можно считать 400 м/ч. Сила сварочного тока при этом будет около 120–140 А [6].
Выбор марки проволоки определяется маркой свариваемой стали, способом сварки и условиями, в которых работает сварная конструкция.Проволока диаметром до 1,6 мм, предназначенная для автоматической аргонодуговой сварки, нагартовывается растяжением с целью придания ей большей жесткости для лучшего прохождения между роликами и в мундштуке. Очень важно получить нагартовку постоянную по длине и определенной степени [6].
3.ОБРАБОТКА РЕЗУЛЬТАТОВ
Сварной шов при сварке плавлением образуется в месте соединения металлических заготовок в результате сплавления присадочного материала со свариваемым. В получаемых сварных соединениях можно выделить три зоны, отличающиеся друг от друга структурным строением: зона наплавленного металла (шов) – I, зона термического влияния (околошовная) – II, зона основного металла – III. Структура и свойства металла последней зоны в процессе сварки не изменяются. Металл же шва и околошовной зоны претерпевает фазовые превращения вследствие нагрева и последующего охлаждения. Следовательно, качество сварного соединения в основном определяется свойствами металла этих двух зон.
Изучение микроструктуры начинают с рассмотрения микрошлифа под микроскопом до травления. Это позволяет выявить микродефекты: поры, трещины, неметаллические включения.
Cварке подвергали колосники из стали 20Х13 к которой приваривались ребра жесткости из различных проволок. Обработку вели методом TIG и MIG на установке, включающей газобаллонное оборудование, вольфрамовый электрод и устройство его перемещения.
На одной из граней образцов наносили одну или несколько упрочненных дорожек. Макроструктуру изучали невооруженным глазом и с помощью микроскопа МБС-9.
На рисунке 3.1 показано щелевое сито из которого вырезалось 18 образцов.
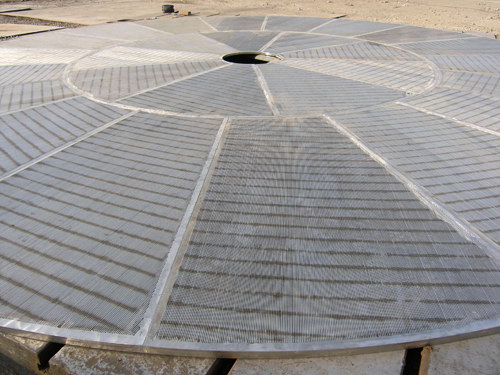
Рисунок 3.1 – Сито щелевое сварное для фильтр-чана
На образцах изготавливали поперечные шлифы по обычной методике. Подготовку поверхности, шлифование и полирование образцов ведут с помощью абразивных материалов и инструментов. Абразивные материалы представляют собой наждачную бумагу от крупного до мелкого абразива.Приготовление микрошлифов состоит из нескольких последовательных процессов: подготовки плоской поверхности, шлифования и полирования.Плоскую поверхность подготавливают на торцовой поверхности образца. Образцы обрабатывали на вращающемся шлифовальном круге.
При ручном способе шлифования на жесткую плоскую подкладку (толстое стекло), расположенную горизонтально, кладут шлифовальную шкурку. Образец ставят на бумагу заторцованной плоскостью и шлифуют последовательно во взаимноперпендикулярных направлениях с легким нажимом до полного уничтожения рисок, оставшихся после торцовки. Закончив шлифование на шкурке с самым мелким зерном, образец промывают проточной водой и полируют.Чтобы окончательно выровнять поверхность, шлиф полируют до зеркального блеска. Полирование шлифа механическим способом производится на полировальном станке. При полировании шлиф периодически поворачивают для более равномерной обработки всей поверхности.
На шлифах исследовали микроструктуру на микроскопе «Neophot–21». Структуру выявляли травителем №14 по Коваленко.На рисунке 3.2 и 3.3 показана микроструктура реберного образца № 2.
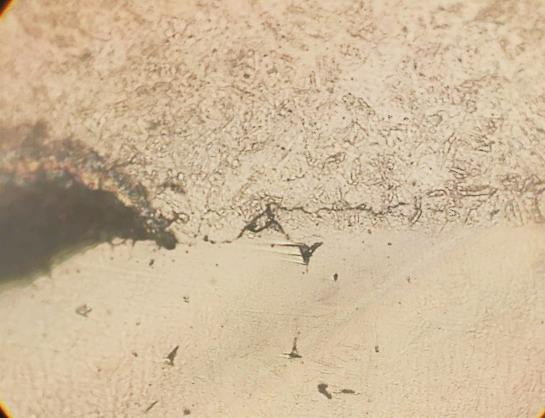
Рисунок 3.2 – Образец № 2 (присадочная проволока Св-08) х600
На рисунке 3.2 видно трещину, которая появилась после сварки.
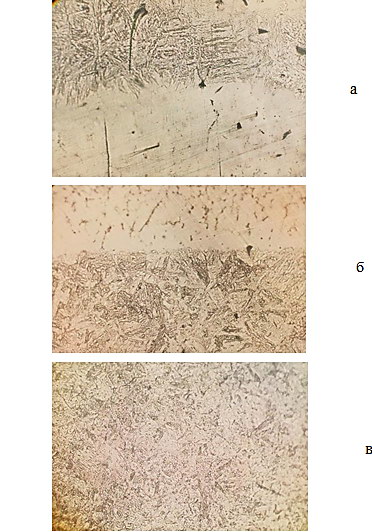
Рисунок 3.2 – Микроструктура образец № 2 (присадочная проволока Св-08) Х600
Из рисунка 3.3 а – граница ребро и сварной шов, б – сварной шов, который имеет мартенситную структуру, в - колосник из стали 20Х13, мартенситной структуры.
Выводы
Повышение содержания углерода в сталях, с одной стороны, позволяет улучшить свойства сварного соединения за счет термообработки, а с другой – ухудшает свариваемость из-за охрупчивания ЗТВ. Устранить указанные трудности позволяет правильный выбор теплового режима сварки. Недопустимыми дефектами сварных соединений и швов, выявленными внешним осмотром, являются:
- Трещины всех размеров и направлений;
- Местные наплывы общей длиной более 10 мм на участке шва 1000 мм;
- Подрезы глубиной более 0,5 мм при толщине наиболее тонкого из свариваемых элементов до 20 мм включительно;
- Поры в количестве более 4 штук на длине шва 100 мм, при этом максимальный размер пор не должен быть более 1,0 мм, при толщине свариваемых элементов до 8,0 мм включительно, и более 1,5 мм при толщине свариваемых элементов свыше 8,0 мм до 50,0 мм включительно;
- Незаваренные кратеры.
Установлено, что при использовании присадочной проволоки Св-08 на образце № 2 возникла трещина. Из фотографий микроструктуры образца № 2 структура колосника и сварного шва состоит из мартенсита.
Список источников
- Щелевые сита: Каталог продукта [Электронный ресурс]. – Режим доступа: http://www.ruseurositex.ru/docs/slotted_sieve.pdf
- Вайсберг, Л.А., Просеивающие поверхности грохотов. Конструкции, материалы, опыт применения /Л.А. Вайсберг, А.Н. Картавый, А.Н. Коровников // СПБ.: Изд-во ВСЕГЕИ. - 2005. — 252 с.
- ГОСТ 9074-85 Сетки щелевые на соединительных шпильках. Технические условия (с Изменениями N 1, 2). - Введ 1987-01-01.- М.: ИПК Издательство стандартов, 2003
- Химушин, Ф.Ф. Нержавеющие стали .- М: Металлургия, 1966. – 776 с.
- Белугин, К.Н. Преимущества использования продукта ARCAL 1 TM (99,998% Ar) для сварки аустенитных нержавеющих сталей / К.Н. Белугин, В.В. Бисин, И.М. Лозинский // Металлообработка. – 2012. - № 4. – С. 47-50.
- Масаков, В.В. Сварка нержавеющих сталей: учеб. пособие / В.В. Масаков, Н.И. Масакова, А.В. Мельзитдинова. – Тольятти: ТГУ, 2011. – 184 с.