Abstract
Content
Introduction
Theme urgency
1. Description of the technological process of ventilation of dead‐end workings
2. Purpose, functions and tasks of the ACS
3. The concept of ACS TP ventilation of a dead‐end coal mine
4. ACS design
5. Current results of the work
Conclusion
Literature
Introduction
Currently, the level of accidents and industrial injuries at coal enterprises remains quite high, despite its slight decrease over the past few years. It follows from this that the currently used means of monitoring and controlling the ventilation process do not always provide reliable and effective protection [1].
Thus, the most important direction in the field of automation of technological processes in the coal industry is the creation of integrated general‐mine control systems that ensure the prompt adoption of optimal control decisions at various hierarchical levels, the forecast of the development of dangerous situations, the maintenance of a rational mode of operation of controlled facilities, the reduction of forced downtime of equipment and improving the level of safety of mining operations.
These circumstances justify the urgency of developing an adaptive control system for a frequency‐controlled asynchronous electric drive of a local ventilation fan using fuzzy set rules, which simultaneously regulates the composition of the mine atmosphere in order to ensure the safety of mining operations and regulates fan performance in order to ensure energy conservation.
Thus, the purpose of the development is to increase the efficiency of the process of ventilation of the mine preparatory workings by improving the automatic control system of the local ventilation fan, which will increase the safety and efficiency of mining operations.
Theme urgency
When carrying out preparatory workings at gas mines with the help of tunneling combines, it is possible to release methane in excess of permissible norms according to Safety rules, which is unsafe for workers, reduces the productivity of mechanization means, there is a possibility of gasification, which can lead to an emergency situation. One of the ways to prevent accidents, to stabilize the modes of operation of mechanization means in the preparatory mine development is to control the ventilation process. The existing systems of automatic ventilation of a coal mine most often use suboptimal operating modes, therefore, the development of a flexible (adaptive) system for automatic control of a local ventilation fan is an urgent topic of research today.
1. Description of the technological process of ventilation of dead‐end workings
The process of ventilation of the preparatory production of a gas coal mine is an important technological process that ensures the supply of sufficient air to the bottom for the work of workers and the normalization of the parameters of the mine atmosphere with an increase in the concentration of methane in excess of the permissible norms according to safety rules in coal mines. In accordance with the requirements, it is forbidden to ventilate the preparatory workings of a gas coal mine due to the general diffusion, excluding dead ends up to 6m long adjacent to the shafts. Ventilation of preparatory mine workings should be carried out with the help of local ventilation fans (LVF). Axial and centrifugal fans with electric and pneumatic drives are used for ventilation of preparatory mine workings, in a special design for mines dangerous for gas and dust. Axial fans of the VM series have found the greatest use. Centrifugal fans are also used to ventilate large‐length workings, for example, VMTs‐6, VMTS‐8, VMTSG‐7 fans, which have a large flow (up to 20 m3/s) and develop high pressure (up to 600‐900 kPa). Air is supplied to the face through a ventilation pipeline with a diameter of up to 800 mm [2].
Schemes of ventilation of dead‐end workings due to the general depression are shown in Fig.1.
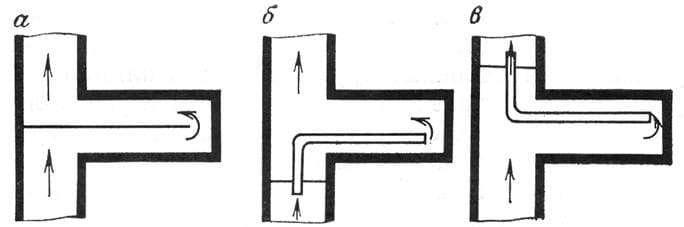
Figure 1 — Ventilation schemes of dead‐end workings:a) due to a general‐duty depression with the use of a longitudinal partition; b) a ventilation pipe supplying air to the face; c) sucking air out of the face
When ventilating workings with the help of local ventilation fans, the following ventilation methods are used: injection, suction and combined.
The injection method of ventilation is the most common. Its advantage lies in the fact that the ventilation of the bottomhole space is carried out by an active jet of fresh air coming out of the pipeline at high speed. According to the Safety Rules in gas coal mines, the end of the pipeline should be located at a distance of 8 m from the bottom, and in non‐gas and ore mines - at a distance of 12 and 10 m, respectively.
The advantages of the injection method of ventilation also include the fact that fresh air enters the bottomhole space (where there is maximum gas emission and people are located), which facilitates the creation of safe working conditions. As the air moves from the face to the mouth, gas is released from the surface of the production into it. The gas content in the outgoing stream continuously increases until the air exits into the production, which is ventilated due to a general depression.
If the supply of the discharge fan installed on the through-working is greater than the flow rate of the air supplied through it, then part of the outgoing air will be sucked back in by the fan and sent through the pipeline to the bottom. This phenomenon is called air recirculation. To prevent recirculation, Safety regulations prescribe installing a fan at a distance of > 10 m from the mouth of the ventilated workings. At the same time, the fan supply should be <70% of the air flow moving through the through‐working.
The disadvantage of the injection method of ventilation is that during blasting, the poisonous gases of the explosion move along the development. Therefore, people can enter the production only when the content of toxic gases in it in terms of conditional carbon monoxide is 0.008% by volume.
The scheme of ventilation of workings by the injection method using a local ventilation fan is shown in Fig.2.
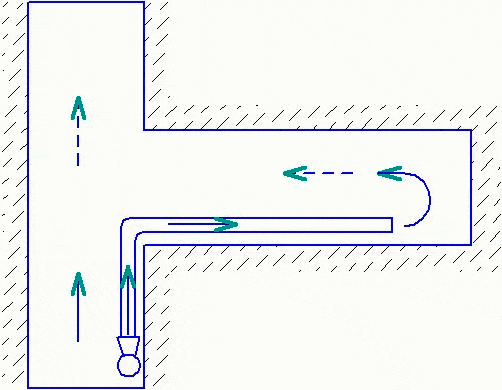
Figure 2 — Scheme of ventilation of workings by injection method using a local ventilation fan (animation: 3 frames, 28 KB)
The suction method of ventilation is used in coal and ore mines that are not dangerous for gas. Its advantage lies in the fact that stale air is discharged from the bottom‐hole space through the pipeline, and since fresh air enters the face through the development, most of it is not gassed. The efficiency of ventilation of the workings by the suction method depends on the distance between the end of the suction pipeline and the face. As this distance increases, a stagnant zone forms in the bottom‐hole part and the duration of ventilation of the workings increases sharply.
The main disadvantage of this method of ventilation is the difficulty of maintaining the distance from the face, since the end of the pipeline is located in the zone of the spread of pieces of rock and the probability of its damage is very high.
The scheme of ventilation of workings by suction and injection‐suction method is shown in Fig.3.
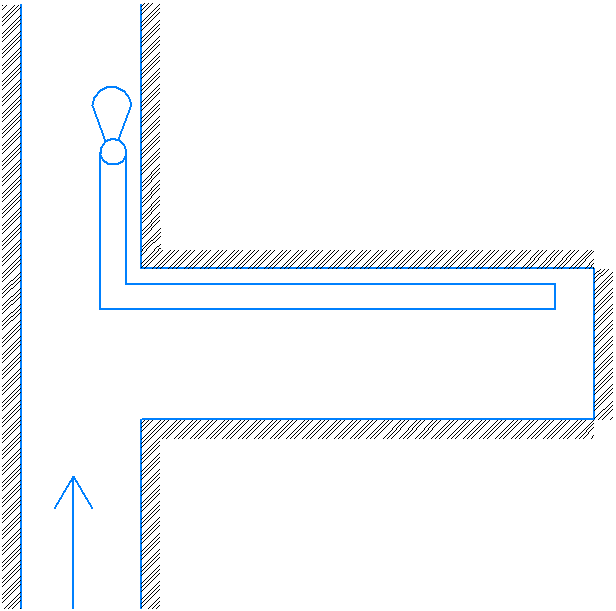
Figure 3 — Scheme of ventilation of workings by suction and injection-suction method using a local ventilation fan (animation: 4 frames, 14 KB)
The combined (injection‐suction) method of ventilation is more often used for high‐speed sinking in non‐gas mines. It combines the advantages of the injection method (active mixing of gases in the bottomhole zone) and suction (limited volume of ventilation). With the combined method of ventilation, one or two fans are used. In the case of using one fan, it works initially for suction, and after removing the highly concentrated gas cloud from the bottom through the pipeline into the outgoing jet, the fan switches to injection. When using two fans, the main fan is installed near the mouth of the mine (at a distance of >10 m) and works on suction. The second fan (auxiliary) is supplied with a short discharge pipeline and installed in the mine near the bottom. The supply of the discharge fan should be 20-30% less than the amount of air that enters the suction pipeline. To prevent the spread of the gas cloud towards the mouth, sometimes a jumper is installed in the mine at a distance of 30-50 m from the face [2].
2. Purpose, functions and tasks of the ACS
The goal is to save energy costs and maintenance of the local ventilation fan, prolong the service life of the ventilation system of the tunneling workings due to the introduction of an adaptive system for automatic ventilation of the tunneling workings.
The functions that the ACS must perform with a local ventilation fan:
Management functions:
⁃automated control and real‐time management of the process of supplying fresh air to a dead‐end production;
⁃automated frequency‐controlled control of the local ventilation fan, including redundant;
⁃continuous monitoring of air velocity in the pipeline at the bottom of a dead‐end mine;
⁃continuous monitoring of the dust level in the tunneling.
Protective functions:
⁃automatic voltage removal from the electrical equipment of a dead‐end production in case of violation of its normal ventilation mode;
⁃alarm about emergency situations
Information functions:
⁃issuance of information on the state of ventilation of dead‐end workings, operation of fans, etc.;
⁃archiving of information;
⁃remote transmission of readings from sensors to the control controller;
⁃integration into the control system as the control unit of the controlled point.
To implement the formulated functions of the ACS, it is necessary to solve the following tasks:
⁃to study the dead‐end production of a coal mine as an object of management. Formulate the purpose and functions of the ACS with a local ventilation fan;
⁃to carry out a review and analysis of modern ways of managing LVF. To propose a variant of the LVF ACS concept;
⁃to obtain a mathematical model of dead‐end mining and LVF, as well as to develop algorithms for controlling the ventilation system, taking into account the characteristics of coal mines;
⁃formulate requirements for the technical means of ACS and develop a functional scheme of automation, a complex of technical means;
⁃formulate requirements for occupational safety and health during installation and operation of the developed ACS with a local ventilation fan.
3. The concept of ACS TP ventilation of a dead‐end coal mine
When developing an automatic fan control system for local ventilation, one of the most important stages of system synthesis is the analysis of the ventilation process as an object of control, i.e. identification of the process structure, determination of input and output variables, finding mathematical dependencies between input and output variables of the technological unit under consideration.
Technological parameters are physico‐chemical quantities that characterize the state of the control object (for example, temperature, pressure, rotation speed, etc.). In addition to technological parameters, control objects are characterized by disturbing and controlling influences. Impacts are factors that change the state of the technological process in the control object [3].
Usually, the main parameters that most fully characterize the state of the process are selected from the technological parameters, the value of which can be controlled using special technical means. Such parameters are called adjustable.
Disturbing effects (loads) are factors whose change is random, difficult to predict. Such factors include, for example, outdoor air temperature, voltage fluctuations in the power grid, etc.
Control actions – actions on the control object carried out by special technical means or by the operator in order to compensate for the influence of disturbing influences or changes in the operating modes of the control object.
Analyzing the above methods of ventilation of dead-end workings, it can be concluded that the injection method of ventilation of tunneling workings is more efficient and economically profitable [4]. Taking into account the above, we will highlight the main regulated variables of the technological process:
⁃the concentration of methane gas and dust in the bottom of the mine and on the outgoing jet.
The controlling influence is:
⁃the speed of air movement in the mine.
The main disturbing effect is:
⁃the release of gas and dust from rocks during tunneling activities.
Thus, the scheme of the technological process of ventilation of a dead-end mine as a control object has the form shown in Fig. 4.
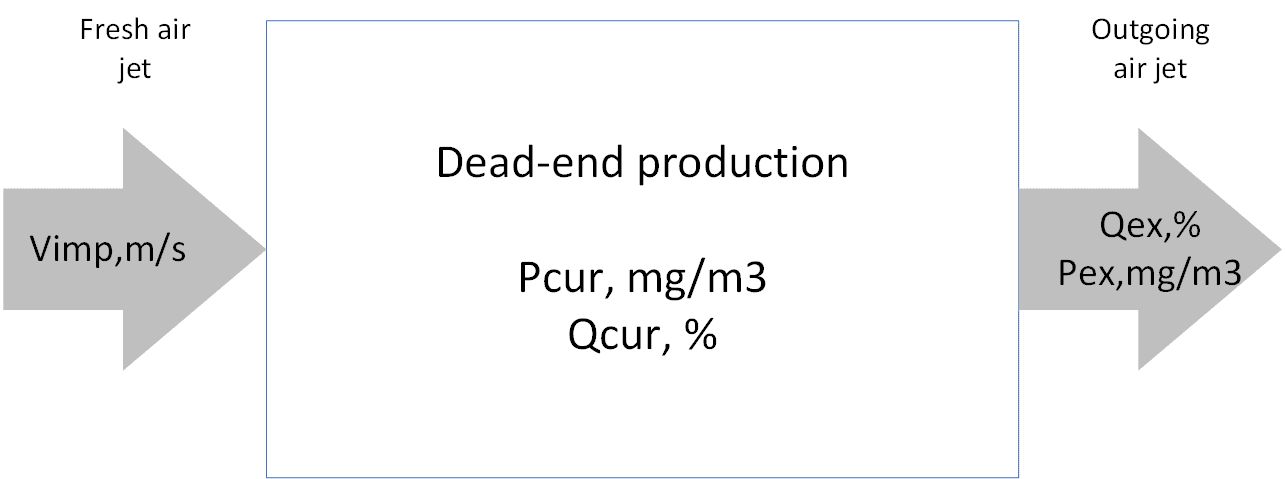
Figure 4 — Analysis of the technological process of ventilation of a dead‐end mine as an object of management with respect to material flows
This analysis will make it possible to set the task of managing the object in question and to build an automatic fan control system for local ventilation of a coal mine. To formalize the concept of building this system, we will consider and analyze the existing control systems for the technological process of ventilation of dead-end production, from the point of view of determining their advantages and disadvantages. Such an analysis will make it possible to justify the chosen automation solution, which will improve the quality and efficiency of the process of ventilation of a dead‐end coal mine.
When managing a complex object, such as a dead‐end mine operating in non-stationary conditions, regulators implementing classical PI or PID laws of regulation have found wide application. Modern controllers of foreign and domestic manufacturers: Remikont, Aries, Siemens, Microl, etc., as a rule, the Ziegler‐Nichols method is implemented to control the object. [5] It should be noted that this method assumes the output of the object to the area of self‐oscillations, due to the transition to the P‐law and a rough variation of the gain of the Raman. However, the ventilation of a dead‐end coal mine does not allow self‐oscillation of the control system. Thus, the task of finding the optimal method of adjusting the regulators remains open. Fuzzy models and control algorithms have recently become widely popular. Fuzzy control is based not so much on the use of analytical or theoretical models, but on the practical application of the knowledge of qualified specialists, presented in the form of linguistic bases of rules. Fuzzy control is effective in cases of non‐deterministic parameters of objects, when there is a certain experience of experts in managing and configuring an automated control system (ASR). [6] The theory of fuzzy logic allows you to use the knowledge of specialists — adjusters in order to improve management processes and assist (supervisory mode) in setting up standard regulators. Based on the above, the task of creating a PID controller adaptation method that implements the experience of adjusters becomes relevant [7,8].
Having analyzed the work of the previously developed system, it is necessary to improve the security control system for conducting dead‐end workings for the implementation of management and control processes. Introduce fuzzy logic methods into management processes. The concept of the ACS TP ventilation of dead-end workings of a coal mine is shown in Fig.5.
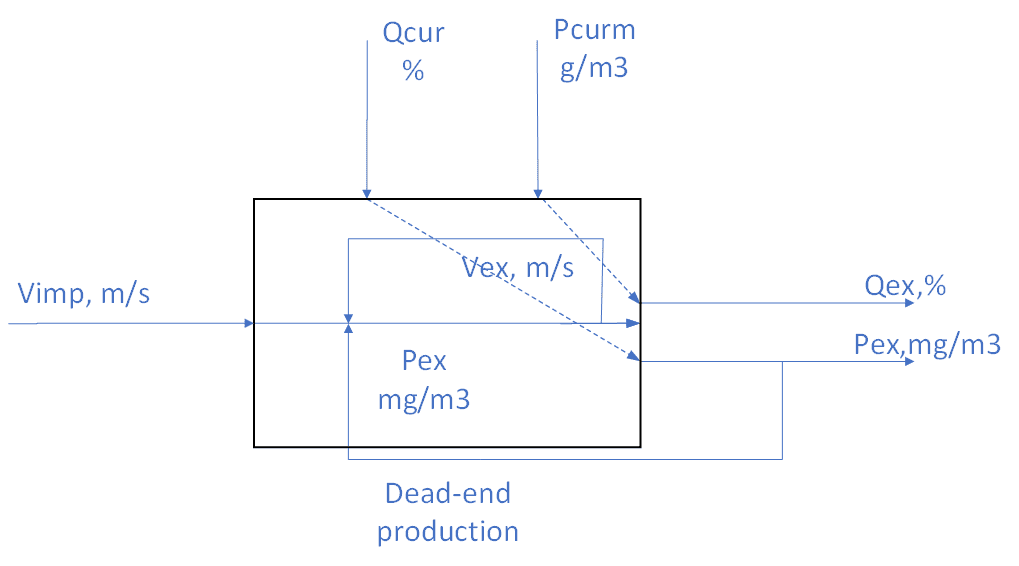
Figure 5 — Analysis of the technological process of ventilation of a dead‐end mine as a control object
The concept of the ACS is to maintain two main parameters of the dead‐end production atmosphere: the concentration of methane and the amount of dust. A closed ACS consists of two main feedbacks (hereinafter OS) – the concentration of methane and the amount of dust; and one local (corrective) OS – the speed of air supplied to the production. The main disturbing effects of the system are the release of methane gas and dust during mining operations.
4. ACS design
The implementation of the ACS TP concept of ventilation of dead-end workings of a coal mine, shown in Figure 5, will achieve the following results:
⁃improving the safety of workers in underground mine workings by improving the ventilation of dead‐end faces;
⁃increasing the productivity of mining mechanisms and creating favorable climatic conditions for workers in the mine;
⁃ensuring the required indicators of gas concentration, air velocity and the amount of dust in the working area, due to the automatic ventilation control system of dead‐end workings.
The expected results of the project are of great importance for solving industrial problems of the development of an automatic ventilation system of mine workings. The introduction of new and more reliable technologies will significantly reduce the number of accidents in the coal mining industry.
This control system will eliminate human errors when monitoring the concentration of gas in dead‐end workings. The quality indicators of the system being developed are an order of magnitude higher than those of the systems currently in use. Reducing the time of the transition process, as well as the accuracy of the measured value, will lead to more optimal indicators of gas contamination and air consumption in the bottom. The introduction of an automatic ventilation control system for dead‐end mine workings creates prerequisites for optimizing existing work complexes.
The specifics of each specific control system is determined by the hardware and software platform used at each level. The three‐level structure of the complex of technical means (CTS) of ACS In MP is shown in Fig.6.
The upper level of the management hierarchy is a workstation of the ventilation operator, implemented on the basis of an office PC.
The middle level of the management hierarchy includes control devices based on the SIEMENS S7‐200 industrial controller. The middle control level of the local controller receives information from field-level devices.
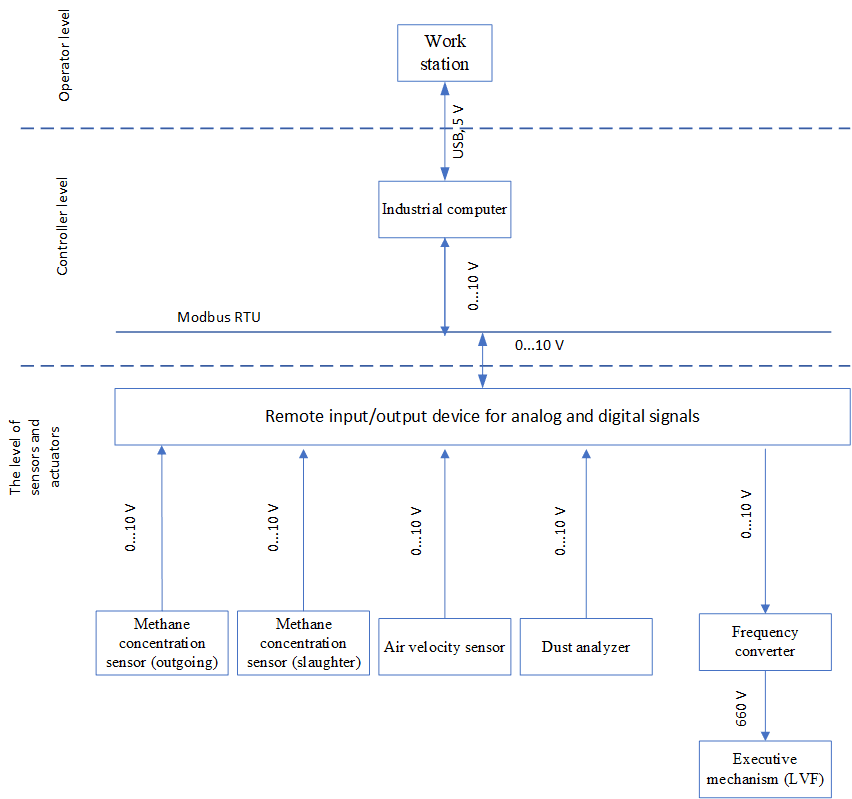
Figure 6 — Scheme of the CCC ACS LVF
The field level is built on the basis of instrumentation and control equipment, represented by methane concentration sensors, air velocity sensors, a dust analyzer, a PMV frequency converter [9,10] and an actuator (LVF). The main controls are interconnected by communication channels based on the Modbus RTU standard.
The algorithm of the system is as follows:
⁃field level sensors (methane concentration, dust and air velocity) measure the corresponding values of the mine atmosphere and transmit them to the controller via an input/output device via a twisted pair (RS‐485) and a Modbus RTU network interface;
⁃the controller, in turn, receives the measured data, processes it and transmits it to the workstation via the USB interface for data visualization on the dispatcher monitor;
⁃The PLC, based on the data received from the sensors, according to a certain algorithm (laid down by the system developer), generates a control action and sends it to the Modbus RTU network;
⁃The remote I/O device redirects this control action from the Modbus network to the frequency converter;
⁃the frequency converter, in turn, based on the data obtained, directly controls the actuator (local ventilation fan), due to which the microclimate indicators in the dead‐end development change. Changes occur until we get such indicators that will meet the Safety Rules of mining operations.
Based on the block diagram of the complex of technical means, we will develop a functional scheme of the system (Fig.7)
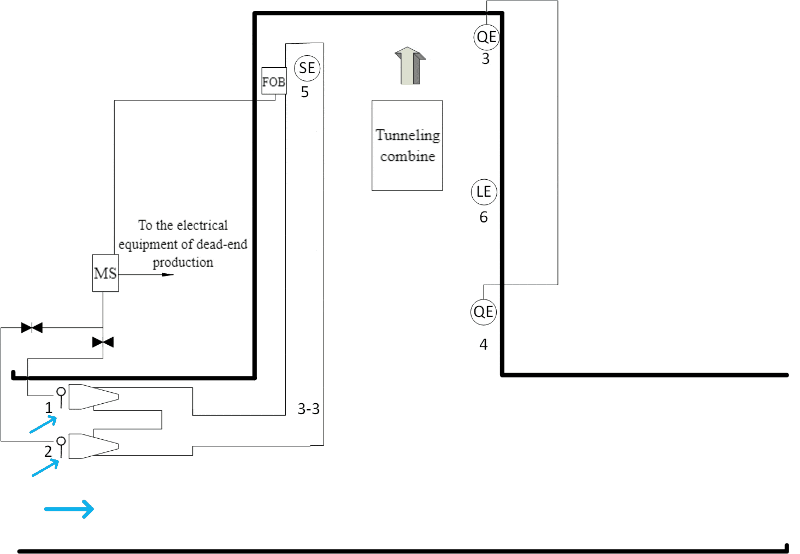
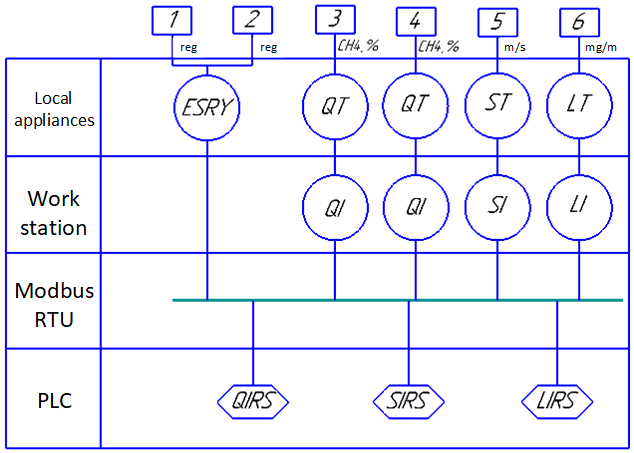
Figure 7 — Functional diagram of the automatic adaptive ventilation control system of the tunneling (animation: 10 frames, 148 KB)
Figure 7 shows the following designations: Q – concentration measurement; L – measurement of the amount of dust in the air; T – remote data transmission; I – indication; S – speed/frequency measurement; R – registration; C – regulation; Y – conversion; 1‐2 – LVF working and standby; GP – main the starter.
5. Current results of the work
Based on the developed concept of the ACS of the local ventilation fan, a block diagram is drawn up (Fig.8).
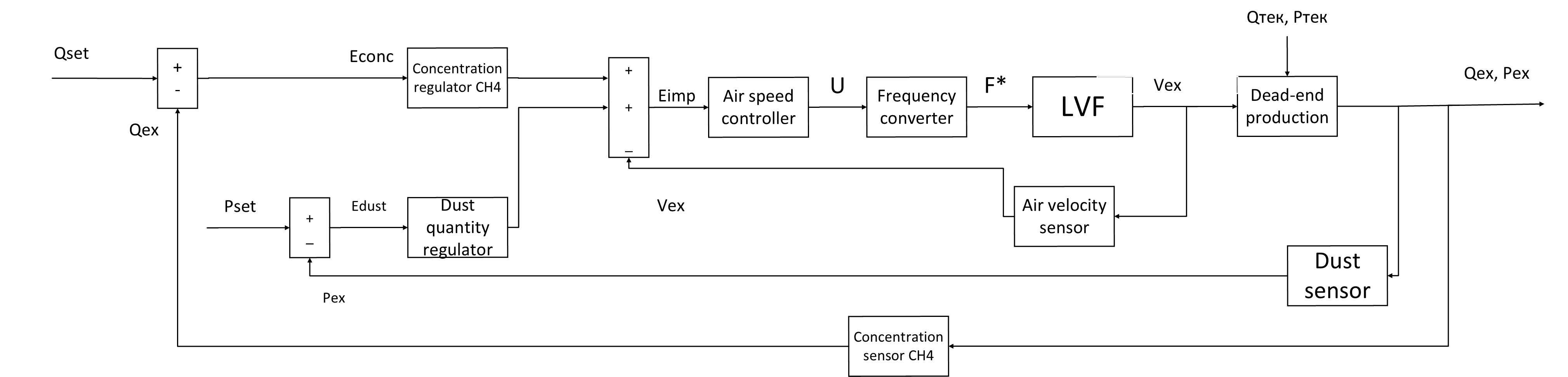
Figure 8 — Block diagram of the local ventilation fan control system
Figure 9 shows a block diagram of the ACS simulation by a local ventilation fan in Simulink.
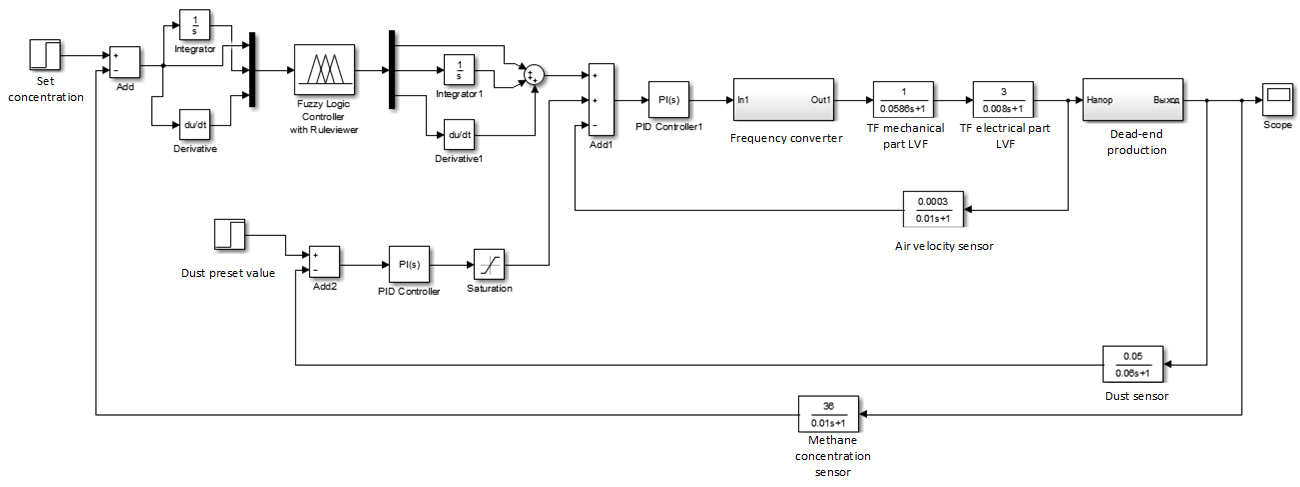
Figure 9 — Block diagram of the ACS with a local ventilation fan in Matlab‐Simulink
Using the developed ACS model in the Simulink package (Fig.9), we will conduct a study of the quality of transients when changing the disturbing effect.
As a result of modeling the operation of the system under the action of disturbances, graphs of transients are obtained, which are shown in Fig.10…12.
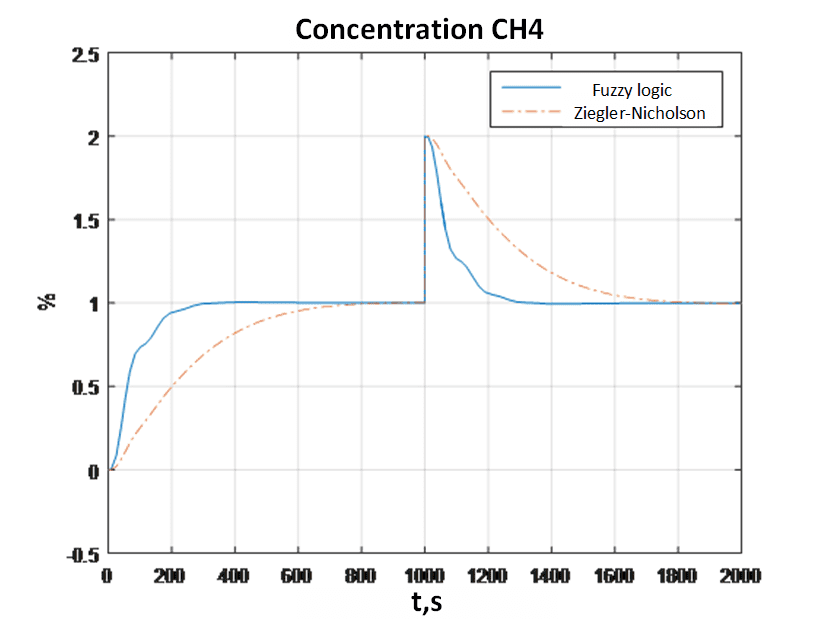
Figure 10 — The transient process of methane concentration with a change in the disturbing effect
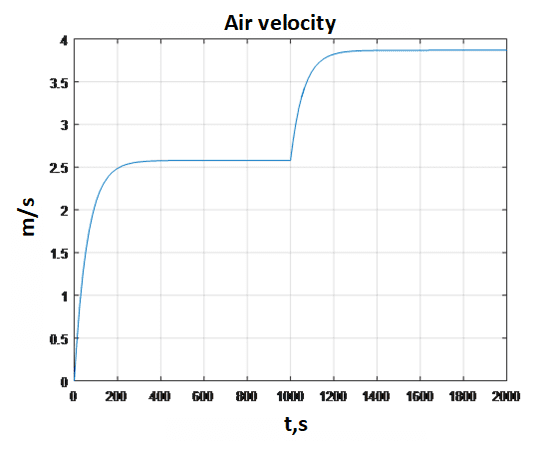
Figure 11 — The transient process of air velocity with a change in the disturbing effect
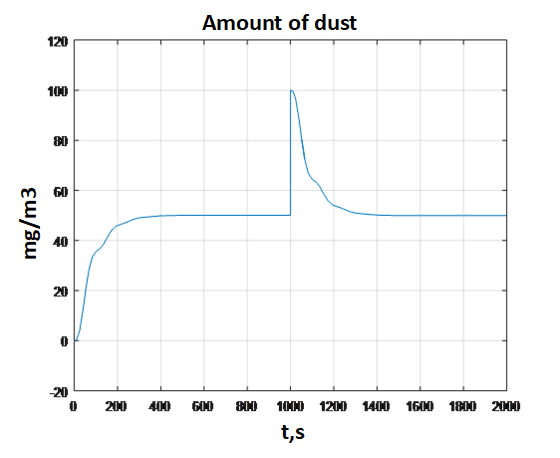
Figure 12 — The transient process of the amount of dust with a change in the disturbing effect
After analyzing the obtained graphs, we can conclude that the developed system remains stable and the quality indicators of transients satisfy the proposed ones. Also, it can be seen from the above figures that the system with the adjustment of regulators by fuzzy logic copes faster with disturbing influences and does not bring the system to critical values.
At the time of writing the abstract, the work on the master's thesis has not yet been completed. This research will be devoted to the development of algorithms and the study of the possibility of using fuzzy logic and neural networks in the tasks of setting up regulators.
Conclusion
The paper analyzes the process of ventilation of dead‐end workings as an object of automatic control. The process of controlling the ventilation system of dead-end workings of mines dangerous for gas and dust is analyzed. The systems currently used are considered, their main functions are highlighted. The main functions of the developed system are formulated. To implement the functions of the ACS, it was proposed to solve a number of tasks. Requirements for functionality, performance, reliability, safety and operation of ACS for ventilation of dead-end faces are put forward. The description of an alternative option for the construction of an ACS by a local ventilation fan is presented, based on the analysis of currently used solutions and fundamental management principles.
As a result of the analysis of the ACS currently used by the local ventilation fan, the main advantages and disadvantages of existing systems were identified. To implement the tasks set, based on the highlighted advantages, it was decided to take the APTT system as a basis. A structural diagram of the ACS with a local ventilation fan has been compiled. Mathematical models of ACS elements have been developed. A simulation model of the ACS in the MATLAB&SIMULINK package has been developed. As the control law, a PID controller is selected to regulate the concentration of methane gas, and a PI controller to regulate the air velocity, the parameters of which are configured by the fuzzy sets method. The obtained graphs of transients are analyzed. It can be seen from the graphs obtained that the developed system remains stable and the quality indicators of transients meet the requirements.
Literature
1. Шишов В.А. Современные технологии промышленной автоматизации./В.А. Шишов – Саранск: Изд‐во Мордов. ун‐та, 2007. – 250 с.
2. Правила безопасности в угольных шахтах: ПБ 05‐618‐03. - М., 2003.- 294 с.
3. С. Дасгупта, Х. Пападимитриу, У. Вазирани Алгоритмы./ С. Дасгупта и др. - McGraw Hill Education. – 2006. – 319 с.
4. Горная энциклопедия «Аа‐лава – Яшма»: Вентиляция шахты [Электронный ресурс] – Режим доступа: http://www.mining-enc.ru/ - Загл. с экрана.
5. Математическое моделирование нестационарных процессов вентиляции сети выработок угольной шахты / [И.М. Васенин, Э.Р. Шрагер, А.Ю. Крайнов, Д.Ю. Палеев, О.Ю. Лукашов, В.Н. Костеренко]. – М. : Томский государственный университет, 2011. – 155‐163 с.
6. Автоматическое региулирование вентиляционных режимов угольных шахт: Уголь Донбасса [Электронный ресурс] – Режим доступа: http://coal.in.ua/ - Загл. с экрана.
7. Денисенко В.В. ПИД – регуляторы: принципы построения и модификации. Часть 1 / В.В. Денисенко // СТА. – 2006. – №4. – С. 66‐74.
8. Денисенко В.В. ПИД – регуляторы: принципы построения и модификации. Часть 2 / В.В. Денисенко // СТА. – 2007. – №1. – С. 78‐88.
9. Пугачев Е.В. Модель системы автоматического мониторинга, прогнозирования и управления аэрогазовым режимом на угольных шахтах / Е.В. Пугачев, Е.В. Червяков, А.Е. Червяков [Электронный ресурс]. – Режим доступа: https://elibrary.ru – Загл. с экрана.
10. Берикашвили В.Ш. Электроника и микроэлектроника. Импульсная и цифровая электроника. Учебное пособие для СПО / В.Ш. Берикашвили // М. : Юрайт, 2021. – 244 с.