Abstract
Content
- Introduction
- 1. Relevance of the topic
- 2. Goals and objectives of the study, planned results
- 2.1 Analysis of existing aluminum processing methods
- 2.2 Microwave oven, and using microwave energy to melt metals
- Conclusion
- References
- The volume of household waste is continuously increasing both in absolute terms and per capita;
- the composition of waste is becoming more complex, including an increasing number of environmentally hazardous elements;
- the attitude of the population with increasing environmental awareness towards traditional methods of garbage collection is becoming more and more negative;
- The economics of waste management is becoming more complex, the cost of waste disposal is increasing.
- reducing environmental damage due to less metal pollution;
- saving up to 95% of energy when using recycled aluminum; door–to–door use of materials saves up to 40% of water in the production of containers;
- prevention of up to 85% of harmful emissions into the atmosphere and water pollution;
- reducing carbon emissions by up to 97% — combating the greenhouse effect. [2]
- Analysis of existing aluminum processing methods.
- Comparative analysis of aluminum extrusion.
- Microwave oven, and the use of microwave energy to melt metals.
- The plate was removed from the working chamber, as well as the engine that rotated it.
- The cooling system has been completely replaced to replace the broken one.
- installation of two fans to blow air from the environment onto the magnetron. The third is located on top and blows hot air out of the internal space where all the electronics are located;
- adding an AC voltage converter from 220 volts to DC rating of 13.3 volts, which is used to power the fans. The converter has a fuse.
- simplicity of the furnace device and process technology;
- lowest cost;
- less fatigue and more fun;
- minimum workspace;
- easy to manage.
- Утилизация алюминивых банок [Электронный ресурс]. URL: https://supernatural-word.ru/...
- Переработка алюминиевых банок: алгоритм утилизации на предприятиях и в домашних условиях [Электронный ресурс]. URL: https://rcycle.net/metally/...
- TALAT Lecture 3710 [Электронный ресурс]. URL: https://aluminium-guide.com/...
- SCIENTIFIC AMERICAN September 1994 [Электронный ресурс]. URL: https://paginas.fe.up.pt/...
- Материалы XXI Республиканской научно–технической студенческой конференции. Е. О. Филоненко магистрант, В. В. Ошовский канд. хим. наук, доц., ГОУВПО
Донецкий национальный техническийуниверситет
, ДНР. - Неразрушающий контроль: справочник: В 7 т. Под общ. ред. В. В. Клюева. Т. 2: В 2 кн. –М.: Машиностроение, 2003. – 688 с.
Introduction
Problems of recycling are relevant in any country, in any city. An ecological catastrophe is inevitable with the constant accumulation of municipal solid waste (MSW). Many types of MSW decompose within 300—400 years. The problem of household waste is currently becoming more and more relevant for a number of reasons:
One of the types of MSW are aluminum cans.
Recycling of aluminum cans is a well–established process in most countries of the world. The most technologically advanced countries recycle one hundred percent of used aluminum containers. A used aluminum can can be recycled multiple times. As cans are recycled, waste disposal costs for consumers and industry are reduced. If all aluminum cans were recycled, there would be no need for destructive aluminum ore mining because supply would always match demand. [1]
1. Relevance of the topic
Aluminum cans are the most common form of processed aluminum available for recycling, making them the subject of an aluminum recycling program.
When returning aluminum cans to storage, aluminum can manufacturers want to use recycled aluminum because it takes 95% less energy to turn it into another aluminum can than it takes to mine aluminum ore and make a can from scratch. Because it takes 95% less energy to process a recycled can, manufacturers also emit 95% less manufacturing emissions.
The main manufacturing methods for aluminum cans — round and rectangular — are shown in Figure 1.
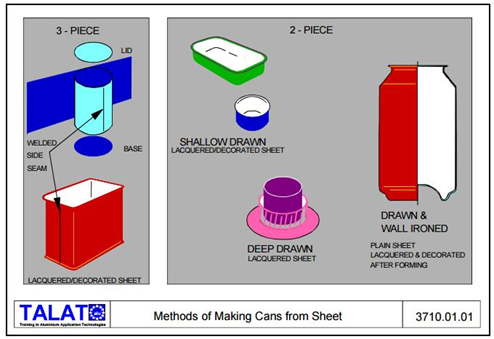
Figure 1 — Methods for making cans from aluminum sheet. [3]
Basic elements and details.
Aluminum beer cans (and for carbonated drinks too) must withstand internal overpressure up to 6 atmospheres. Therefore, the design of the can includes a thick domed bottom and rather thin walls, which, however, with the help of internal pressure, provide the can with sufficient structural strength. A general view of a typical beer can and the purpose of its various elements is shown in Figure 2.
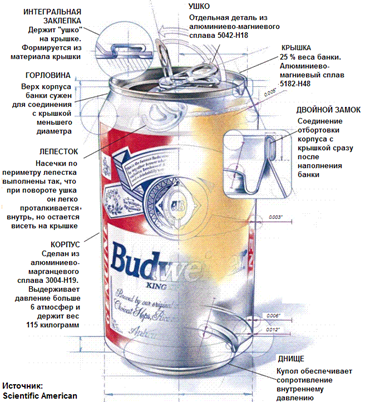
Figure 2 — Construction details of an aluminum can and their functions. [5]
The production of secondary aluminum is costly, it does not allow economically processing low–grade aluminum raw materials and obtaining a new product ready for use in the metallurgical industry, for example, in the production of various steel grades.
Production of a briquette from aluminum scrap, for example, used aluminum cans, foil, aluminum alloy shavings, allows you to reduce the cost of a briquette by recycling used aluminum cans and waste from metallurgical production.
The method of obtaining the proposed briquette is simple, versatile, productive, as it provides a short manufacturing cycle, does not require complex special equipment for its implementation, meets the modern requirement for production flexibility, allows for small capital investments to establish mass or small–scale production within the framework of small and medium business.
Recycling aluminum cans and tin containers has a number of advantages:
2. Goals and objectives of the study, planned results
Tasks:
Research object: aluminum cans.
Subject of research: the process of improving methods for obtaining aluminum from recycled materials.
2.1 Analysis of existing aluminum processing methods
Based on the practice of using existing recycling technologies, the traditional stages of processing secondary (aluminum) metal–containing raw materials can be represented in the following enlarged diagram (Figure 3).
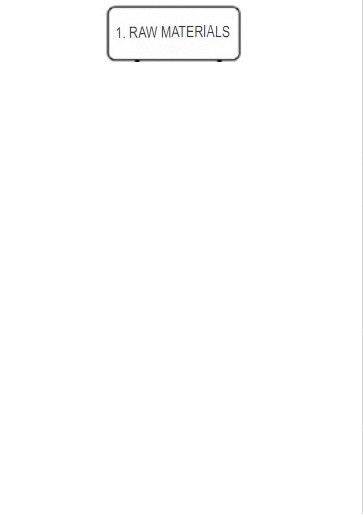
Figure 3 — Processing stages of secondary (aluminum) metal–containing raw materials. [5]
(animation: 4 frames, 5 loops, 135 kilobytes)
Household aluminum packaging arriving for recycling is shredded and sent to the sorting line. At the stage of primary sorting, the raw material is checked with a magnetic separator for the presence of magnetic metals. Next, heavy impurities are separated. Then the paint and varnish coatings are removed, since their presence causes metal loss due to ignition during the melting process.
The main stage is metal smelting. In relation to metal raw materials of secondary use (tin cans), the following melting methods can be distinguished: in a vacuum induction furnace; in a vacuum arc furnace with a consumable electrode; electron beam remelting; plasma–arc remelting; electroslag remelting. For the remelting of aluminum scrap and waste, one–, two– and three–chamber reverberatory furnaces and electric induction crucible furnaces are used.
The most widespread are two–chamber reverberatory furnaces, combining the functions of a melting unit and a mixer for adjusting the chemical composition and storing metal for the casting period. These furnaces are universal, they are used for melting all types of aluminum scrap and waste. About 80% of secondary aluminum alloys are smelted in these furnaces. The capacity of the melting chamber of two–chamber furnaces is from 10 to 30 tons. Fireclay bricks are used for laying furnaces.
Electric crucible furnaces are usually used for processing small charge — shavings and scraps of sheet metal or profile. The electric furnace consists of the following main units: a steel casing, a crucible, an inductor, a furnace cover with a lifting and turning mechanism. The furnace is tilted using a hydraulic mechanism, the electrical conduit to the furnace is carried out by flexible water–cooled cables.
As an alternative, rarely mentioned, one can note a method based on the use of microwave radiation in the melting process.
The subsequent stages of the technological process (Figure 3), as a rule, are additional in the general scheme of processing. Improving the quality of aluminum alloys obtained from scrap and waste in reverberatory and electric furnaces is achieved by refining the melt from harmful impurities and non–metallic inclusions.
Obtaining the finished product is carried out by extrusion on extrusion presses or casting into ingots. Actually, the main interest of the study is focused on the search for a possible alternative, and maybe even in the future more efficient or economical, method of metal smelting and its instrumentation, which can be the melting of aluminum waste in a microwave oven. [5]
2.2 Microwave oven, and the use of microwave energy to melt metals
Industrial microwave ovens have not found any other purpose than to quickly heat up food. However, their cost is much higher than household models. The experimental setup was based on a household microwave oven with a faulty cooling system. Magnetron power 1200 W.
Various design changes have been made:
Replacement includes:
The installed components and assemblies of the cooling system are machine–made. The connecting wires have a section sufficient for stable operation without creating a fire hazard.
Thermal sensors are installed in the hottest places and turn off the power to the oven when heated above 150 degrees Celsius. These factors contribute to the safe operation of the plant.
The melting crucible was handmade from a bar of electrode graphite and is a small cup.
The next stage is the creation of a heat–insulating furnace, in which a crucible with metal is placed. In our case, the oven was built in the working chamber of the experimental setup from blocks of mineral wool.
As a result of the performed operations, the Resonant Microwave Crucible Furnace 1 model (hereinafter referred to as RMTP–1) was created.
The melted metal is placed in the melting crucible. The crucible is placed in a heat–insulating furnace, which is placed in the working chamber of the experimental setup. Other similar materials can be used as the furnace material.
If the metal has a melting point below 800 degrees Celsius (Aluminum, Duralumin, Zinc), then it is permissible to use a heat–insulating furnace without refractory coatings. For frequent melting, in order to increase the resistance of the inner part of the furnace to burnout, it is enough to cover it from the inside with a refractory coating, when the coating burns out, a new layer is applied.
The melting of metals and alloys (Bronze, Brass, Copper, Cast Iron), with a melting point above 800 degrees Celsius, requires knowledge of the composition and work with special refractories.
Foucault eddy currents are created in it to melt the metal. [6] Foucault currents arise under the influence of an alternating electromagnetic field and, by their physical nature, do not differ in any way from induction currents arising in linear wires. They are vortex, i.e. closed in a ring.
The electrical resistance of a massive conductor is small, so the Foucault currents reach a very high strength.
The benefits of using this setup:
Conclusion
Thus, aluminum cans and their metal recycling are not as harmful to the environment as primary ones. The amount of garbage accumulated on the planet is decreasing. When recycling recyclables, the percentage of emissions of greenhouse gases that accelerate the process of global warming is lower. Even harmless aluminum has a detrimental effect on nature, which cannot cope with human waste. For those involved in the processing of aluminum waste, there is another significant plus – a well–established production can bring impressive income.