Abstract
Содержание
Introduction
The work is devoted to improving the digital combined thermal protection of an asynchronous motor with a squirrel-cage rotor, which combines two methods for determining the heating temperature of the machine windings based on monitoring operating parameters in real time. In the first method, the temperature of the rotor winding is calculated indirectly based on the results of comparing the active resistance of a squirrel-cage rotor in the initial and current states. In the second method, to determine the heating temperature of the stator and rotor, a simplified thermal model is used, based on the calculated values of the current power losses in the electric motor windings. The performance of the proposed combined thermal protection of an asynchronous machine was tested on a PC using mathematical modeling methods for a deep-slot asynchronous motor type VEM DKKAJ 4020-4 with a rated power of 1000 kW and a stator voltage of 6 kV.
1. Theme urgency
Currently, due to the relative simplicity of the design and relatively high reliability, the main type of electric motors (EM) of alternating current, most widely used as electric drive machines and mechanisms of installations of the auxiliary systems of thermal and nuclear power plants, as well as various industrial enterprises, are asynchronous motors (AM). ) with a squirrel-cage rotor (SCR) [1]-[5]. Failure-free operation throughout the entire service life declared by the manufacturer depends on the quality of manufacture of the asynchronous machine, on the quality of operation, as well as the quality of the relay protection and automation devices (RPiA) used (timely response in abnormal and emergency operating modes (ER)). As rightly shown in [4], existing devices and systems of relay protection and automation of motors with short-circuit protection are capable of protecting the cable-motor connection not from all possible abnormal and emergency RRs, such as, for example, when asymmetry of the supply voltage occurs, during multiple starts following one another etc. One of the ways to solve the urgent problem of improving relay protection and automation systems for motors with short circuit protection is the further modernization of thermal protection (TP) of asynchronous machines.
2. An approach to the unification of synthesis of Moore FSM on FPGA
In this work, we will use as a basic algorithm the combined thermal protection (CTP) algorithm of an IM with a CPP, proposed in [2]. The key feature of this KTZ is the combination of two approaches to determining the heating temperature, based on the simultaneous use of a thermal model of the machine and an improved algorithm for indirectly determining the KZR temperature based on measurement data at each step of the microcontroller operation of operating parameters - instantaneous values of phase currents (ia, ib, ic), phase voltages (ua, ub, uc) and slip values (s). In order to optimize for microprocessor systems of small and medium computing power, this work proposes an improvement of the basic KTZ algorithm by upgrading the module for indirectly determining the heating temperature of the winding of a squirrel-cage rotor of the machine. To simplify the implementation on a microprocessor platform, we will use an algorithm for indirectly determining the heating temperature of the winding of the KZR IM, based on a single-circuit equivalent equivalent circuit (ESC) taking into account losses in the steel of the stator magnetic circuit and taking into account the skin effect in the rotor winding.
Approximate values of the TM parameters can be found for the thermal resistances of the stator ?1 and rotor ?2 from equations (2) for the steady-state nominal mode of the electric motor, assuming that the temperature derivatives are equal to zero (p?S = 0, p?R = 0) , there is no heat exchange between the stator and the rotor (?3 = ?), and the heating temperatures of the stator winding VS and the rotor winding VR are equal to the nominal ones.
The calculated values of the parameters of the thermal circuit in the TM are refined in the process of conducting corresponding experiments on the electric drive. The block diagram of the improved combined protection is shown in Figure 3, and represents a sequence of computational operations performed by the microcontroller in one working cycle. As can be seen from Figure 1, the block diagram includes: • a block for measuring the parameters of the current mode (block 1); • source data block (block 2); • sequence of computational operations using an algorithm for indirectly determining the heating temperature of the rotor, based on algebraic equations with determination of the input resistance of the IM based on measurement data of the parameters of the current mode (blocks 3-8); • block for calculating losses in the machine (block 9); • differential equations of a two-mass thermal model of an asynchronous motor (block 10). In order to improve the quality of indirect calculation of the heating temperature of the rotor VR, the determined input resistances of the machine were averaged (block 5), similar to [6]. The performance of the proposed improved KTZ IM with KZR was tested on a PC using mathematical modeling methods for a deep-slot asynchronous motor type VEM DKKAJ 4020-4 produced by the German company VEM Group® with a rated power of 1000 kW and a stator voltage of 6 kV, the catalog data of which is given in the table, and the calculated according to the method described in [7]
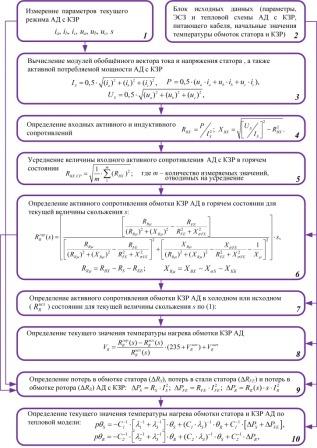
Figure 1 – Block diagram of combined thermal protection of IM with KZR
As an example, the normal operation mode under load and the subsequent increase or increase in load on the machine shaft for an IM with a KZR type VEM® GmbH DKKAJ 4020-4 were simulated. The correct operation of the improved KTZ was checked by comparing the value of the heating temperature of the IM (VR), determined by the algorithm (see Fig. 3) with the value of the temperature determined by a predetermined law (VS*, VR*), similarly to [2]. Dependences on time (t) of the stator current of phase “a” (ia), angular frequency of rotation of the rotor (?), heating temperature of the stator winding and SCR, determined by the thermal model (?S, ?R) and heating temperature of the squirrel-cage rotor winding, determined indirectly by based on the comparison of the active resistances of the CZR in hot and cold (initial) states (VR) for an IM with the CZR type VEM IE3-W41R 280 S2 are presented in Fig. 2.
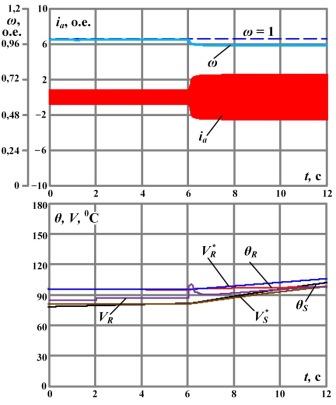
Figure 2 – Dependences on time (t) of the stator current of phase “a” (ia), the angular frequency of rotation of the rotor (?) and the heating temperature of the stator and rotor windings for an IM with a short-circuit protection type VEM DKKAJ 4020-4.
From Fig. 2 it can be seen that during the calculation process, a close coincidence of the heating temperature values of the stator and rotor windings was obtained, which confirms the correct development of the specified law of heating temperature change (VS*, VR*), which in turn confirms the correct operation of the improved combined thermal protection of the IM with the CZR.
1. An improved algorithm for combined thermal protection of asynchronous motors with a squirrel-cage rotor is proposed, in which the heating temperature of the machine windings is determined in two ways - based on real-time monitoring of operating parameters such as instantaneous values of phase currents and voltages, as well as slip values. In the first method, the temperature of the windings is calculated indirectly based on the results of comparing the stator and rotor resistances in the initial and current states. In the second case, a simplified thermal model is used for this purpose, using the calculated values of the current power losses in the stator and squirrel-cage rotor windings.
2. In order to adapt to microprocessor terminals of low and medium computing power, an upgrade of the algorithm for indirectly determining the heating temperature of the winding of a squirrel-cage rotor of an asynchronous motor is proposed through the use of algebraic equations in the process of transforming the equivalent circuit when determining the active resistance of the rotor in a hot state. To eliminate fluctuations in the calculated input rotor resistances, it is proposed to perform their averaging.
3. The performance of the combined thermal protection of an asynchronous machine presented in the work was tested on a PC using mathematical modeling methods for a deep-slot asynchronous motor type VEM DKKAJ 4020-4 with a rated power of 1000 kW and a stator voltage of 6 kV.
References
- Старшинов В.А., Пираторов М.В. Козинова М.А. Электрическая часть электростанций и подстанций [Учебное пособие] – Под ред. В.А. Старшинова. – М.: Издательский дом МЭИ, 2015. – 296 с.;
- Сивокобыленко, В. Ф. Математическое моделирование комбинированной тепловой защиты глубокопазного асинхронного двигателя / В. Ф. Сивокобыленко, С. Н. Ткаченко // Электрические станции. – 2020. – № 2 (1063). – С. 46-53.
- Zocholl S.E. On the protection of thermal processes power delivery / S.E. Zocholl, G. Benmouyal // IEEE Transactions on Vol.20, Issue 2 – 2005. – P.: 1240-1246;
- Venkataraman, B. Fundamentals of a motor thermal model and its applications in motor protection [Text] / B. Venkataraman, B. Godsey, W. Premerlani, E. Shulman, M. Thakur, R. Midence // GE Global Research. Motor Thermal Model Protection Applications. – 2008. – P. 41-55;
- Ziuzev, A. M. On Heating Induction Motor Rotor at Start-Up of High-Inertia Mechanisms [Text] / A. M. Ziuzev, V. P. Metelkov // Proceedings of 2018 17th International Ural Conference on AC Electric Drives (ACED). – 2018. – P.1-5;
- Ткаченко С.Н. Совершенствование цифровой системы защиты асинхронных двигателей с короткозамкнутым ротором системы собственных нужд электростанций / С.Н. Ткаченко, В.В. Иванов // Инновационные перспективы Донбасса. Материалы 6-й Международной научно-практической конференции. 2020. Издательство: Донецкий национальный технический университет (Донецк). 2020 – С. 170-177;
- Ткаченко С.Н. Метод идентификации параметров эквивалентных схем замещения асинхронных электродвигателей с короткозамкнутым ротором / Ткаченко С.Н. // Сборник научных трудов ГВУЗ «Донецкий национальный технический университет». Серия «Электротехника и энергетика». – выпуск 1 (16). – Донецк, 2014. – С. 210-215.