Abstract
Contents
- Introduction
- 1. Individual assignment
- 1.1 Synchronization and methods of its implementation. Model description
- 1.2 Modeling of the process of self-synchronization of the TGU generator with the grid
- 1.3 Modeling of the process of precise synchronization of TGU with the network
- References
Introduction
Electricity generation - a process caused by parallel operation of individual generators, as well as power plants within an electric power system (EPS). Synchronization - an algorithm of actions to switch synchronous generators on for parallel operation, is an integral part of the power generation process. Synchronization can be performed either manually by personnel or with the use of automatic devices. However, this operation is extremely responsible, as incorrect switching on of generators is accompanied by consequences: large equalizing currents, de-energization of power plant busbars, damage to switching equipment or the synchronous generator itself. At the moment synchronization can be carried out by two traditional methods: precise synchronization (TS) and self-synchronization (SS). Both methods have their own disadvantages. For the method of precise synchronization is the duration of the operation due to the need to meet certain requirements: equality of amplitudes of electromotive forces (EMF), rotational speeds, coincidence of phases of EMF of the generator and the system at the moment of switching on the switch, for the method of self-synchronization - large values of equalizing currents at the moment of switching on and voltage reduction at the busbars of the power plant. An urgent issue is the development of special devices that will carry out the synchronization process fully automatically, having a reaction speed inaccessible to humans. At the same time, the device should be able to use not only two traditional methods, but also some intermediate method that eliminates their disadvantages and takes into account the operating mode of the equipment. Creation of such a synchronization system will make it possible to solve the problem of possible consequences of switching on a synchronous generator into the grid, the severity of which is due to both the influence of the human factor and the chosen method of switching on. Thus, synchronization should occur with minimal consequences for the power plant and not violate the stability of the EES. The purpose of this study is to develop an automatic digital synchronization device with the ability to switch on generators by different methods in both normal and emergency operation modes. Such a device will create optimal conditions for switching on the unit, excluding the error introduced by the non-ideal reaction of the personnel, which minimizes the possible consequences for both the generator and the power plant as a whole.
1. Individual assignment
1.1 Synchronization and methods of its implementation. Model description
Modern electric power industry is characterized by active use of distributed generation units, development of the concept of active consumers and control based on intelligent approaches [1-2]. Active consumers can be divided into industrial and household consumers. The former are large industrial enterprises with their own generation sources. Household consumers can include "smart home" and "smart city" systems with intelligent control technologies that take into account the peculiarities of their operation and user requests. Such technologies can be built on the basis of fuzzy logic [3]. Turbine-generator set generator switching on for parallel operation with the industrial network can be accompanied by jolts of equalizing current and active power, as well as oscillations. To reduce the intensity of these undesirable processes, the generator should be synchronized beforehand. Synchronization is an algorithm of actions for switching on synchronous generators for parallel operation, is an integral part of the power generation process. Synchronization can be performed either manually by personnel or with the use of automatic devices. Synchronization can be carried out either manually by personnel or using automatic devices. However, this operation is extremely responsible, as incorrect switching on of generators is accompanied by consequences: large equalizing currents, de-energization of power plant busbars, damage to switching equipment or the synchronous generator itself. At the moment synchronization can be carried out by two traditional methods: precise synchronization and self-synchronization. Both methods have their own disadvantages. For the method of precise synchronization is the duration of the operation due to the need to meet certain requirements: equality of amplitudes of electromotive forces (EMF), rotational speeds, coincidence of phases of EMF generator and the system at the time of switching the switch; for the method of self-synchronization - large values of equalizing currents at the time of switching and reducing the voltage at the bus bars of the power plant. To simplify the study of different synchronization options, a model of the process of switching on the power plant generator under study for parallel operation with the system is developed in MATLAB environment using Simulink and Sim Power Systems simulation packages or without them. The main task of the model is graphical visualization of all possible variants of synchronization in the form of dependencies. The use of the model is to vary the initial conditions preceding the switching on of the generator breaker. The differential equation describing the dynamics of the process of changing the power and torque on the shaft of a steam turbine without intermediate steam extraction has the following form:
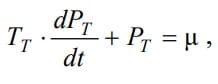
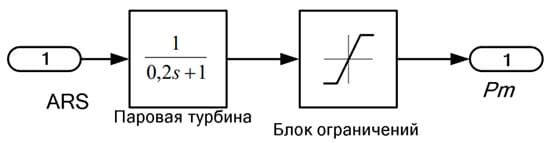
Figure 1 - Schematic diagram of steam turbine model without intermediate steam extraction: s - complex variable
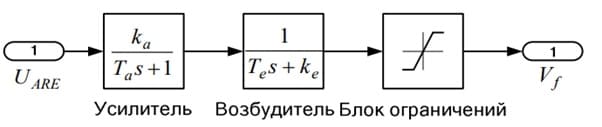
Figure 2 - Structural diagram of the excitation system model: UARE - signal coming from the ADF; Vf - signal coming to the generator excitation winding
Для стабилизации напряжения на выводах генератора ТГУ, демпфирования колебаний ротора, повышения устойчивости и устранения самораскачивания применяются АРВ сильного действия. At present microprocessor-based ARVs are developed and successfully operated. Structural schemes and description of used models of ARVs and ARFs are presented in [4-6]. For modeling of asymmetry and distortion of the voltage curve shape, the model of a standard three-phase power supply installed on 110 kV busbars was used. The 3rd and 5th harmonics of the supply voltage were modeled. Power quality indicators (PCE) in the 110 and 10 kV network in the form of asymmetry and harmonic coefficients obtained as a result of distortion source modeling are presented in figure 3.
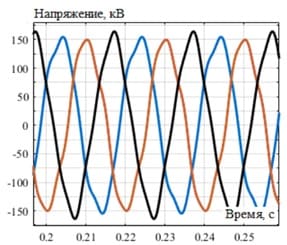
Figure 3 - Oscillograms of supply voltage at 110 kV busbars
1.2 Modeling of the process of self-synchronization of the TGU generator with the grid
When a generator is self-synchronized, its rotor is accelerated by the turbine to a speed close to synchronous and is connected to the grid without excitation. Then, voltage is applied to the rotor winding, and the electric torques arising in the generator ensure that the generator is pulled into synchronism. At the subsequent opening of the turbine control valve, the generator starts to deliver the load current to the grid. When modeling the synchronization processes, we used a classical VRA, which is a proportional-integral-differential (PID) controller, as well as an autoprognostic VRA, a detailed description of which is presented in [7]. The tuning of the PID and VRA was chosen based on practical considerations The results of modeling the process of self-synchronization of the generator with the grid are presented in Figure 4 in the form of comparisons of oscillograms of mechanical power on the turbine shaft with the classical and autoprognostic VRA. In the simulation, the load of the TGU generator was 46 %. Oscillograms of the TGU generator currents are presented in Figure 5, where it can be seen that at the moment of generator connection there is a current jolt (the generator current amplitude reaches at the moment of switching on six times the operating current value). According to the results of modeling it is possible to note a decrease in the inertia of the object when using autoprognostic VRA (transient time for mechanical power on the turbine shaft is reduced by 3.33 times), however, the value of overshoot slightly increases.
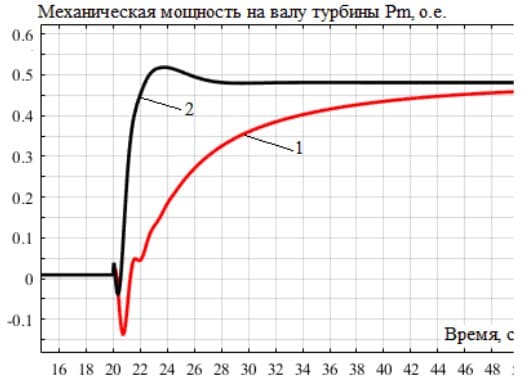
Figure 4 - Variation of mechanical power at the shaft of the TGU turbine: 1 - using standard VRA (transient time 20 s); 2 - using autoprognostic VRA (transient time 6 s)
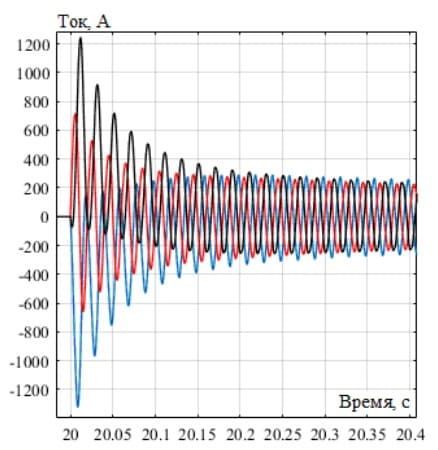
Figure 5 - Oscillograms of instantaneous values of phase currents of the TGU generator
1.3 Modeling of the process of precise synchronization of TGU with the network
With precise synchronization, the generator rotor is accelerated by the turbine and excited. The following conditions must be met before the generator can be connected to the mains: the generator voltage is adjusted to the mains voltage; - the generator frequency is equalized with the mains frequency; the generator frequency is equalized with the mains frequency; the moment of time is chosen when the angle between the generator and mains voltage vectors is equal to zero. The above conditions are easier to perform automatically, for which we have developed a model of auto-synchronizer that controls the regulators and generator breaker. The schematic of the AC model is shown in Fig. 6.
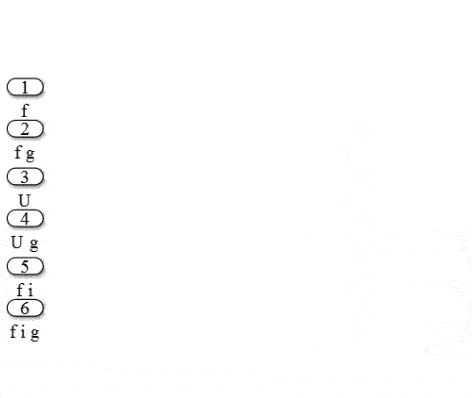
Figure 6 - Schematic of synchronous generator AC model in MATLAB
(animation: 5 frames, 6 repetition cycles, 146 kilobytes)
Inputs 1 and 2 of the AC are supplied with the mains and generator frequency, respectively, inputs 3 and 4 are supplied with the effective value of the mains and generator voltage. At inputs 5 and 6 the phase of the mains and generator voltage is supplied. Then the modules of frequency, voltage and phase differences are determined and the following conditions are checked: frequency difference should not exceed 0.01 Hz; voltage difference should not exceed 5% of the nominal voltage; phase angle between the generator and mains voltage vectors should not exceed 0.1 el. deg. If all conditions are met at the output of the logic element "and" forms a signal (logical one), authorizing the inclusion of the TGU on parallel operation with the industrial network (output 1 breaker, Fig. 6). Fixing the position of the generator breaker "on" is performed in the presence of current flowing from the generator. In the process of synchronization AC influences ARRS (output 2 ARRS in Fig. 6) and ARE (output 3 ARE) through proportional coefficients Ku and Kf of phase angle mismatch signals and values of generator and mains voltages. This effect changes the corresponding frequency and voltage setpoints of the generator regulators. The simulation was performed under the same conditions as for self-synchronization. The simulation results are presented in Figures 7-10 in the form of oscillograms of frequency, currents and powers in the SES. In the simulation, the load of the TSU generator was carried out smoothly, after switching on to parallel operation with the industrial network, and eventually amounted to 70%.
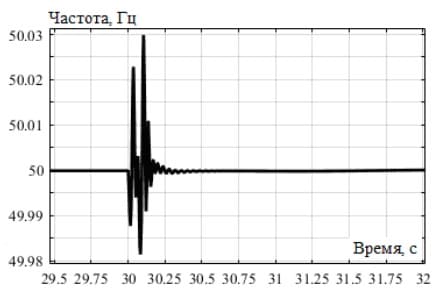
Figure 7 - Oscillogram of voltage frequency variation on TGU busbars
The method of precise synchronization allows to avoid equalizing currents and power shocks when switching on the synchronous generator TSU for parallel operation with the industrial network, which is evident from the oscillograms of currents and powers shown in Fig. 9 and Fig. 10. It should be noted that the exact synchronization of the generator with the network significantly reduces the deviation of frequency from the nominal value (Fig. 8). Loading of the CCGT generator up to 70% allowed to reduce the active power overflow from the electric power system (EPS) through the 110 kV input by 7 times due to the additional power coming from the turbine generator through the 10 kV input.
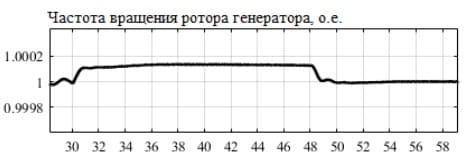
Figure 8 - Variation of rotor speed of the generator rotor of the TGU at precise synchronization with the grid
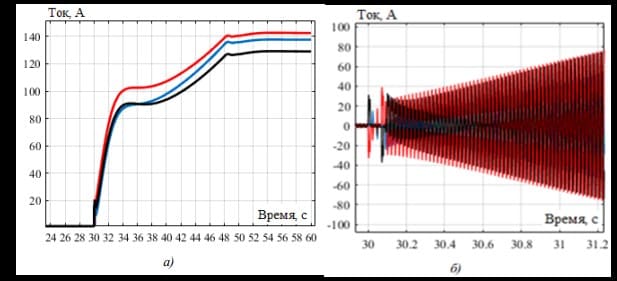
Figure 9 - Oscillograms of effective (a) and instantaneous (b) values of phase currents of the TGU generator
When the CCGT generator is switched on to parallel operation with the industrial grid and its utilization is up to 70%, a noticeable improvement of the PCE is observed.
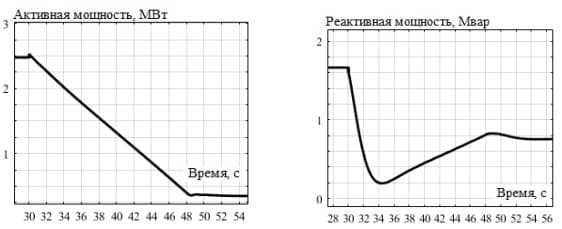
Figure 10 - Oscillograms of active and reactive power at the 110 kV input
The results of computer modeling allow us to draw the following conclusions:
- Application of autoprognostic VRA provides significant improvement of damping properties and reduction of inertia of a turbine-generator set connected to the SES of an industrial enterprise.
- The autoprognostic VRA of the synchronous generator of the TGU can be recommended for increasing the efficiency of the rotor speed regulation system and controlling the control valves of the steam turbine in the process of self-synchronization of the generator with the grid.
- The method of precise synchronization with the use of auto-synchronizer allows to avoid equalizing currents and power shocks when switching on the synchronous generator TSU for parallel operation with the industrial network.
- When the TGU is switched to parallel operation with the industrial grid, a significant improvement in the PCE is observed:
• The reverse sequence asymmetry factor at 110 kV busbars is reduced by 7 %; the same indicator for 10 kV busbars is 20 %;
• total harmonic coefficients on 110 kV busbars are reduced by 9...12 %, and on 10 kV busbars - by 20 %.
References
- Y.I. Morzhin, Y.G. Shakaryan, Y.N. Kucherov, N.I. Voropai, S.N. Vasiliev, S.N. Yadykin Smart Grid Concept for Unified National Electrical Network of Russia. Preprints of proceedings of IEEE PES Innovative Smart Grid Technologies Europe 2011, Manchester Dec. 5-7 2011. Manchester, GB: IEEE // The University of Manchester, 2011. Panel session 5 D. Р. 1-5.
- И.О. Волкова, М.В. Губко, Е.А. Сальникова Активный потребитель: задача оптимизации потребления электроэнергии и собственной генерации // Проблемы управления. 2013. № 6. С. 53-61.
- Н.А. Седова, В.А. Седов Управление умным домом с использованием нечеткой логики // Энергетика, Информатика, Инновации-2016: сб. тр. междунар. науч.-технической конф. Смоленск, 2016. Т. 1. С. 336-339.
- Ю.Н. Булатов, А.В. Крюков, Ч.З. Хынг Автоматические регуляторы для установок распределенной генерации // Системы Методы Технологии. 2014. № 3 (23). С. 108-116.
- Ю.Н. Булатов, А.В. Крюков, Чан Зюй Хынг. Применение сетевых кластеров (microgrid) в системах электроснабжения железных дорог. Братск: БрГУ, 2016. 178 с.
- Ю.Н. Булатов, А.В. Крюков Интеллектуальная настройка регуляторов установок распределенной генерации // Информационные и математические технологии в науке и управлении. 2017. № 3 (7). С. 122-135.
- Yu.N. Bulatov, A.V. Kryukov, Nguen Van Huan. Distributed generator rotor speed automatic prognostic controller // Scientific Bulletin of NSTU. 2017. № 1 (66). P. 15-25..