Abstract on the topic of the work
Content
- Introduction
- Purpose and research objectives
- Relevance of the study
- The object and subject of the study
- Problems in the design and operation of arc steelmaking furnace complexes
- Systematic approaches in the modeling of arc steelmaking furnaces
- Conclusion
- List of used literature
Introduction
In the modern metallurgical industry, the arc steelmaking furnace is one of the most widely used tools for steel production. It provides high efficiency and precision in the processing of raw materials, and also allows you to obtain steel of the required characteristics. However, the development and optimization of an arc steelmaking furnace is a complex and time-consuming process. In this article, we will consider the importance of modeling in the design and development of arc steelmaking furnaces [1].
Modeling is an integral part of the steelmaking furnace design process. It allows engineers and metallurgists to predict and analyze the behavior of the system at different stages of the steelmaking process [2]. Modeling allows you to determine optimal parameters such as current distribution, electrode shape, electrode size and location, charge feed rate and other parameters that affect the operation of the furnace. Using different models can significantly reduce the time and cost of testing and trial operation of a steelmaking furnace [3].
One of the main components of the modeling of an arc steelmaking furnace is mathematical modeling based on physical principles and equations describing the processes occurring inside the furnace. The model can be created using various software packages such as ANSYS, COMSOL, Autodesk and others. Mathematical models make it possible to predict electromagnetic and thermal fields in the furnace, as well as temperature distribution, charge melting rate, formation of gas bubbles and other physical characteristics of the steelmaking process [4].
In addition to mathematical modeling, computer modeling using three-dimensional CAD programs is an important tool for modeling. This allows engineers to create virtual furnace models, visualize them, and conduct virtual experiments to determine optimal furnace configurations [5]. Computer modeling also helps to assess potential problems and risks associated with the furnace design, such as corrosion, uneven temperature distribution or electric current.
Purpose and research objectives
Purpose: The purpose of this topic is to develop a mathematical model of an arc steelmaking furnace for the analysis and optimization of its operation.
Objectives: The task of the study may be related to the study of the effects of various factors on the operation of the furnace, such as electric current, temperature, melt composition, etc. This can help in determining the optimal conditions for the steel melting process.
In general, the study of the simulation of an arc steelmaking furnace aims to optimize the steel melting process, increase the efficiency of the furnace and ensure high product quality.
Relevance of the study
The topic of modeling an arc steelmaking furnace is relevant and in demand in modern metallurgy.
Modeling of an arc steelmaking furnace allows you to optimize the steel melting process, improve the quality of the metal produced and increase the efficiency of the furnace. Using mathematical models and numerical methods, it is possible to analyze the thermal, electrical and hydrodynamic processes occurring in the furnace and predict their characteristics.
The simulation of an arc steelmaking furnace can be used to optimize the furnace design, select melting parameters, and control the process. The model also allows for various research scenarios, such as changes in the composition of the charging material, the impact of external factors and the use of new technological solutions.
In addition, modeling makes it possible to predict the occurrence of defects in metal, such as gas pores, and propose measures to prevent them. This is important to ensure the quality of the metal being smelted and reduce the cost of its subsequent processing.
Using the simulation of an arc steelmaking furnace can significantly reduce the time and cost of pilot smelting, as well as reduce the risk of accidents and damage to equipment. It also helps to improve the safety of operators and reduce the impact of furnaces on the environment.
Thus, the topic of modeling an arc steelmaking furnace is relevant, since it allows to increase the efficiency and quality of the steel melting process, as well as reduce the costs and risks associated with this process.
The object and subject of the study
The object of research is a model of an arc steelmaking furnace, which can be created using various methods and software. This model includes various components and parameters such as the furnace structure, electrodes, electrical parameters, working area, material and heat flows, as well as other physical and chemical processes occurring inside the furnace.
The subject of the study is the process of modeling an arc steelmaking furnace, which includes the development of necessary mathematical models, as well as numerical modeling and analysis of the results obtained. This may include aspects such as determining the optimal furnace parameters, evaluating the influence of various factors on the steel melting process, as well as predicting furnace operation under various conditions.
The object and the subject of the study of the modeling of an arc steelmaking furnace are related to each other, since the subject of the study is part of the object of study. Modeling makes it possible to study and analyze the furnace operation process more effectively, optimize its parameters and predict its operation in various conditions. This helps to improve furnace performance, reduce energy consumption and improve the quality of the steel produced.
Problems in the design and operation of arc steelmaking furnace complexes
Arc steelmaking furnaces (ASF) are an integral element of the technological chain of metallurgical and machine-building industries. The installed capacity of furnace transformers varies from one to hundreds of megawatts. In the power supply system of an enterprise, a chipboard is a specific nonlinear receiver with an asymmetric and sharply variable nature of load changes. Two problems are most relevant in the design and operation of such complexes:
- Ensuring conditions for the maximum and most efficient use of electric energy in all technological modes of ASF;
- Ensuring the requirements of electromagnetic compatibility of the ASF with the power supply system.
Taking into account the tasks set, the most productive and accessible research tool is the simulation modeling method, which allows you to adequately reflect complex electrotechnological processes and significantly expand the ranges of studies of the studied object, including emergency modes [6].
Systematic approaches in the modeling of arc steelmaking furnaces
When modeling an arc steelmaking furnace, a systematic approach should be used that takes into account all the features of the ASF and assumes, firstly, the study of the object as a whole in relation to the external power system, and secondly, the presentation of the ASF as a complex electrical complex consisting of separate local subsystems (elements) with cross-connections [7]. Further, the following are highlighted as the main elements:
- External power supply system with furnace transformer and reactor;
- Electric mode control system with hydraulic electrode movement;
- A voltage stabilization and symmetry system implemented in the form of a static thyristor compensator (STC) consisting of filters and a thyristor-reactor group (TRG) with a control system.
When modeling ASF, the greatest difficulties are caused by the representation of the electric arc itself, since the model must, on the one hand, accurately and adequately reflect real physical processes, and on the other hand, be easily implementable and flexible when conducting research [8].
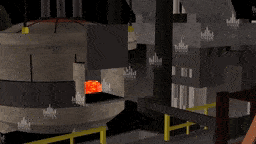
Model of an arc steelmaking furnace
Conclusion
When designing and operating ASF complexes, two problems are the most urgent. When modeling an arc steelmaking furnace, a systematic approach should be used, taking into account all the features.
List of used literature
- Свенчанский А.Д. Электрические промышленные печи. Дуговые печи и установки специального нагрева / Свенчанский А.Д., Жердев И.Т., Кручинин А.М., Миронов Ю.М. и др. — М.: Энергоиздат, 1981. 296 с. – Режим доступа: [Ссылка]
- Миронов Ю.М. Закономерности электрических режимов дуговых сталеплавильных электропечей / Миронов Ю.М. — М.: Электричество, 2006, вып. №6. С. 56-62. – Режим доступа: [Ссылка]
- Корнилов Г.П Моделирование электротехнических комплексов металлургических предприятий: учеб. пособие / Корнилов Г.П., Николаев А.А., Храмшин Т.Р., Мурзиков А.А. — М.: Магнитогорск: Изд-во Магнитогорск. гос. техн. ун-та им. Г.И. Носова, 2012. 235 с. – Режим доступа: [Ссылка]
- Тельный С.И. К теории трёхфазной дуговой печи с непроводящей подиной / Тельный С.И. — М.: Электричество, 1954, вып. №12. С. 38-42. – Режим доступа: [Ссылка]
- Макаров А.Н., Макаров В.С. Теория и практика лучистого теплообмена в дуговых сталеплавильных печах// Новые направления в электротермии: Сб. тр. № 534 / МЭИ. 1991. С. 77– 78. – Режим доступа: [Ссылка]
- Кривандин В.А., Егоров А.В. Тепловая работа и конструкции печей черной металлургии: Учебник для ВУЗов – М.: 1989. - 462 с. – Режим доступа: [Ссылка]
- Мастрюков Б.С. Теория, конструкции и расчеты металлургических печей. – М.: Металлургия, 1986. – 232 с. – Режим доступа: [Ссылка]
- Чередниченко В.С., Аньшаков А.С., Кузьмин М.Г. Плазменные электротехнологические установки: Учебник для вузов / Под ред. В.С. Чередниченко. – 3 изд., испр. и доп. – Новосибирск: Изд-во НГТУ, 2011. – 602 с. – Режим доступа: [Ссылка]
- Миронов Ю.М. Закономерности электрических режимов дуговых сталеплавильных электропечей / Миронов Ю.М. — М.: Электричество, 2006, вып. №6. С. 56-62. – Режим доступа: [Ссылка]