Реферат по теме выпускной работы
Содержание
- Введение
- 1. Актуальность темы
- 2. Цель и задачи исследования, планируемые результаты
- 3. Обзор исследований и разработок
- 3.1 Ленточный конвейер как объект автоматизации
- 3.2 Обзор существующей аппратуры автоматизации конвейерного транспорта
- 4. Эксплуатационные требования к устройству автоматизации
- Выводы
- Список источников
Введение
Работу современных промышленных предприятий без использования конвейеров представить себе очень трудно – они позволяют автоматизировать производственный процесс и сделать его более эффективным. Ленточный конвейер – транспортирующее устройство непрерывного действия. Ленточные конвейеры являются наиболее распространенным типом машин конвейерного транспорта. Практически во всех отраслях промышленности используются ленточные конвейеры, которые обеспечивают непрерывность процессов транспортировки различных видов грузов и материалов. Из всего парка конвейерных установок около 90 % составляют ленточные конвейеры. Преимущество ленточных конвейеров перед другими способами транспортировки заключается в том, что благодаря значительной скорости движения ленты обеспечивается высокая эффективность и производительность технологических процессов, в малом потреблении энергии, простоте, надежности и долговечности конструкции устройства.
Для машин непрерывного действия характерно перемещение насыпных или штучных грузов по заданной трассе без остановок. Транспортирующие машины отличаются высокой надежностью, удобством эксплуатации и обслуживания, имеют большую длину транспортирования, работают в автоматическом режиме в комплексе с технологическим оборудованием, обеспечивают высокую производительность благодаря непрерывности процесса транспортирования. Одновременно с транспортированием грузов на ленточных конвейерах могут выполняться определенные технологические операции. Часто ленточный конвейер является одной из частей транспортирующего устройства какой-либо машины или механической системы
1. Актуальность темы
Известен ряд аппаратуры для оптимизации конвейерной линии: АУК-1М, САУКЛ, АУК.3 МС КУБ-КТ, ELSAP. На основании данной аппаратуры мы можем наблюдать недостатки аппаратуры АУК-3: У нее отсутствует: контроль температуры приводных барабанов, контроль натяжения ленты, блокировка при обрыве ленты, блокировка при наложенных тормозах.
Магистерская работа посвящена повышение экономической эффективности и срока эксплуатации аппаратуры за счет внедрения разработанного расширения для основного блока управления.
2. Цель и задачи исследования, планируемые результаты
Целью исследования является разработка дополнение к блоку управления
Основные задачи исследования:
- Выполнить аналитический обзор аппаратов шахтной автоматизации.
- Разработка функциональной схемы.
- Разработка структурной схемы.
- Разработка принципиальной схемы.
- Разработка прототипа печатной платы.
- Разработка алгоритма функционирования блока управления.
- Расчет экономической эффективность данного блока управления
Объект исследования: автоматизированная конвейерная линия.
Предмет исследования: блок управления АУК-3
В рамках магистерской работы планируется получение актуальных научных результатов по следующим направлениям:
- Разработка функциональной схемы расширения основного блока управления
- Разработка структурной схемы расширения основного блока управления
- Разработка принципиальной схемы расширения основного блока управления
- Разработка прототипа печатной платы для расширения основного блока управления
- Разработка алгоритма функционирования блока управления
3. Обзор исследований и разработок
3.1 Ленточный конвейер как объект автоматизации
Технологический процесс конвейерного транспорта шахты является одним из важнейших в угольной промышленности, а так же наиболее востребованным среди остальных способов транспортирования грузов в шахте. Поэтому задача автоматизации процесса конвейерного транспорта актуальна. Ленточные конвейерные лини благодаря своим качествам (значительная производительность, большая длина транспортировки, способность непрерывно передвигать грузы, пригодность автоматизации и дистанционному управлению, высокая безопасность работ и др.), являются наиболее эффективным средством перемещения насыпных материалов на шахтах (рудниках). Они используются не только для транспортировки насыпных грузов, но и для перевозки людей [1].
Преимущество ленточных конвейерных линий – это то, что они достаточно просты в установке их несложной конструкции. Гибкая бесконечная лента огибает приводной барабан и натяжной барабан, а в пролете между ними опирается на ряд роликовых опор, установленных с определенным интервалом на раме. Материал поступает на ленту через загрузочную воронку и разгружается через приводной барабан [2].
Характерной особенностью шахтных конвейерных линий является высокая неравномерность грузопотока, вызванная фактом обслуживания очистного и подготовительного забоев [3]. Именно технологические паузы в работе механизмов являются причиной переменного грузопотока. Неравномерность поступления груза ведет к нерациональному использованию мощности привода (при недогрузке), а также чрезмерному износу тягового органа и снижению надежности АД (при перегрузе) [4].
Проанализировав рабочий режим и вероятные аварийные ситуации в работе ленточного конвейера, можно сделать вывод, что критическая нагрузка на ленту и послабление натяжения ленты являются наиболее распространёнными аварийными ситуациями, в виду непостоянного грузопотока с добычного или подготовительного участка.
Нагрузка на ленту или погонный вес груза может регулироваться путём изменением скорости движения ленты с помощью управления приводным двигателем конвейера перобразователем частоты, либо путём изменения массового расхода груза из бункера снижением рабочего сечения с помощью управляемой задвижкой.
Также для решения задачи оперативного контроля параметров рабочего и аварийного режимов, была разработана печатная плата, согласно ГОСТ 10317-79 , основанной на работе программируемого микроконтроллера AtMEGA представлена на рисунке 1.
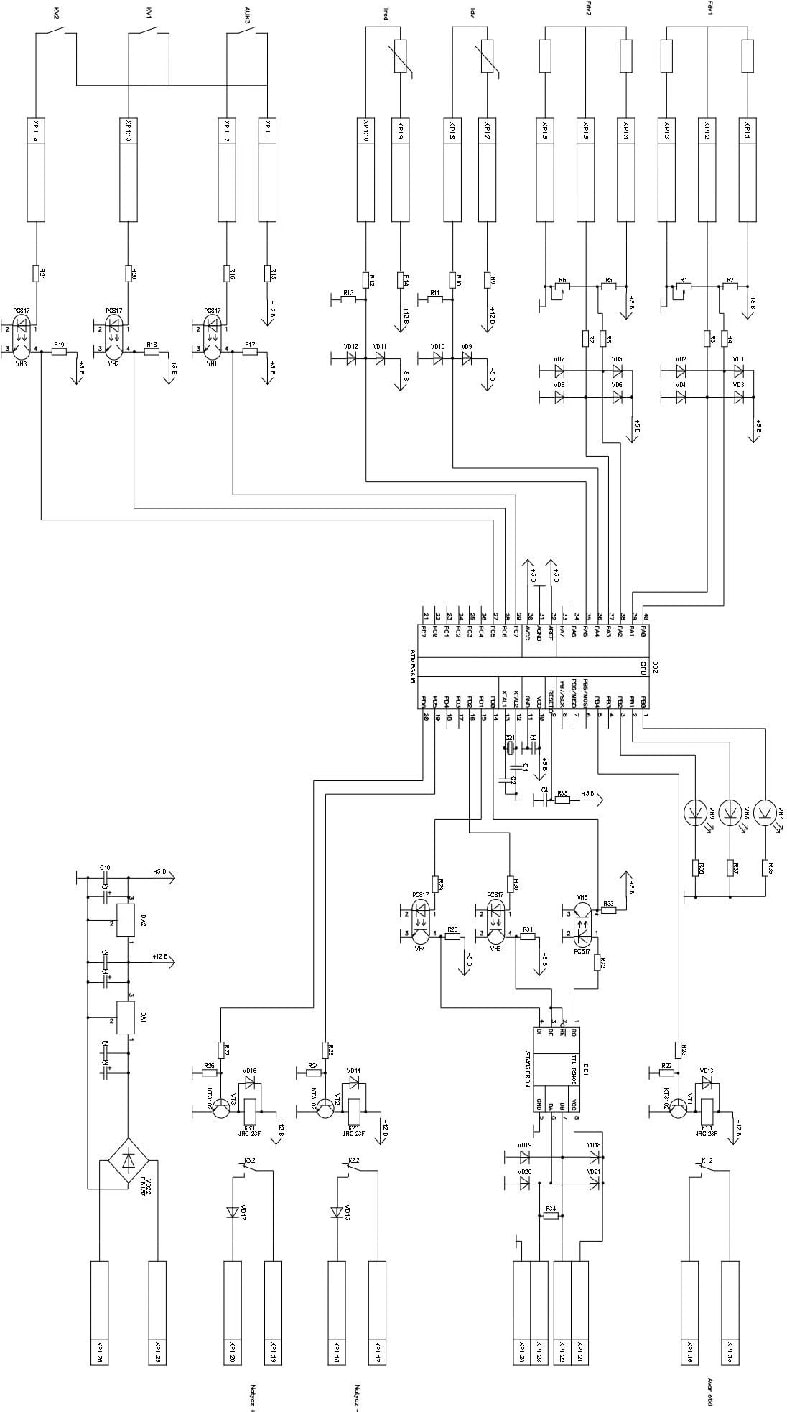
Рисунок 1 – Общий вид принципиальной схемы на основе AtMEGA
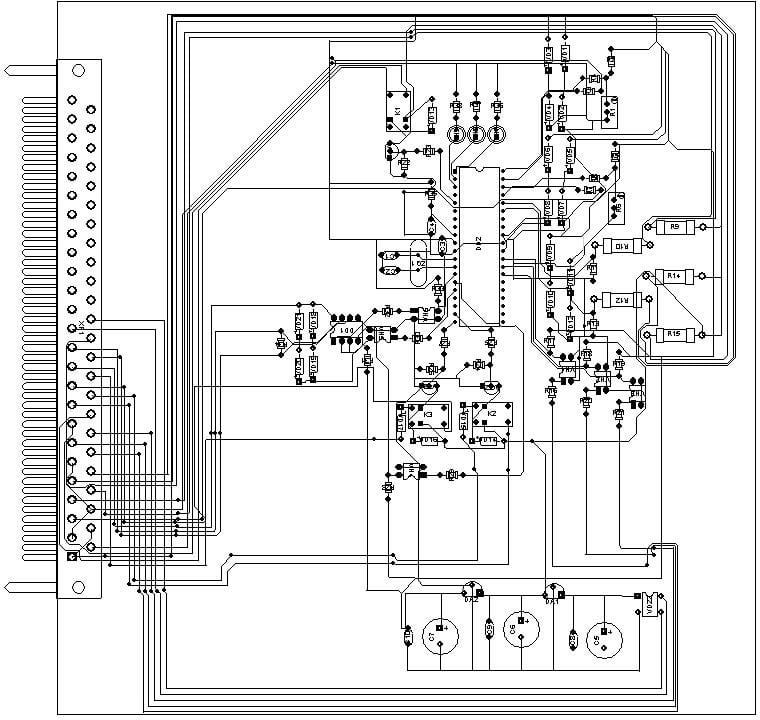
Рисунок 2 – Общий вид разработанной печатной платы
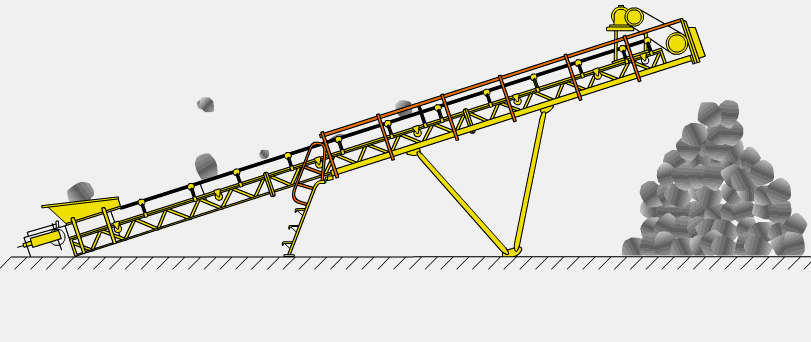
Рисунок 3 – Общий вид принципа работы конвейерной линии
3.2 Обзор существующей аппратуры автоматизации конвейерного транспорта
В настоящее время известны следующие аппаратуры автоматизации конвейерных линий:
Комплекс автоматизированного управления конвейрной линией модифицированный АУК.1М – предназначен для управления и контроля работы стационарных и полустационарных неразветвленных конвейерных линий, состоящих из ленточных и скребковых конвейеров с числом конвейеров до 10. Комплекс АУК.1М может применяться также для управления разветвленными конвейерными линиями (до трех ответвлений, каждое из которых управляется как неразветвленная конвейерная линия). Количество конвейеров в линии одного направления не более 10.
Комплекс автоматизированного управления конвейерами АУК.3 – предназначен для автоматизированного управления неразветвленными конвейерными линиями, состоящими из ленточных и скребковых конвейеров с общим числом конвейеров в линии до 10 включительно, исполнительными органами накопительных бункеров, монорельсовыми канатными дорогами (грузовыми), рельсовыми канатными напочвенными дорогами (грузовыми) и многоканатными дорогами кресельного типа. Комплекс является комплектующим изделием ленточного конвейера (линии конвейеров). Комплекс АУК.3 совместим с комплексом АУК.1М в части линии управления и связи.
Система автоматизированного управления разветвленными конвейерными линиями САУКЛ предназначена для:
- централизованного автоматизированного управления и контроля работы разветвленными и неразветвленными конвейерными линиями, состоящие из ленточных конвейеров, предназначенных для транспортирования груза и перевозки людей, с числом конвейеров, управляемых через один комплект АПУ и АЛС до 60 единиц, и неограниченным числом маршрутов;
- централизованного или местного автоматизированного управления и контроля работы отдельными конвейерами, входящими или не входящими в состав конвейерной линии;
- телеуправления и контроля состояния сопутствующим вспомогательным оборудованием (типа
шибер
,перегружатель
,питатель
); - автоматической регистрации и сохранения информации о работе конвейеров и сопутствующего оборудования, командах управления и настройках, защитных отключениях и блокировках [5].
Рассмотрим техничекские средства автоматизации ленточного конвейера:
Датчик силы сжатия и растяжения каната натяжной лебёдки K25 – предназначен для измерения величины натяжения ленты ленточного конвейера. Комбинированный датчик для измерения силы сжатия и растяжения. Четырёхпроводная шунтированная цепь, контрольное сопротивление для калибровки диапазона измерений. Унифицированный аналоговый выходной сигнал.
Весы тензометрические конвейерные автоматические СВЕДА ВК – предназначены для непрерывного измерения массы сыпучих и кусковых материалов, транспортируемых ленточными конвейерами при коммерческих, учетных и технологических операциях. Конвейерные весы для измерения массы сыпучих материалов осуществляют измерение и индикацию на цифровом табло текущей производительности конвейера и значений массы взвешиваемого материала нарастающим итогом.
Датчик контроля скорости типа ДКС – предназначен для получения электрического сигнала, используемого при контроле движения и скорости ленты ленточного конвейера в аппаратуре автоматизации. Датчик может эксплуатироваться на поверхности, в помещениях обогатительных фабрик, а также в шахтах, опасных по газу или пыли, при температуре окружающего воздуха от минус 10 до 45 °С и относительной влажности до 100% при температуре 35 °С [6].
4. Эксплуатационные требования к устройству автоматизации
Для обеспечения безопасной эксплуатации ленточных конвейеров обязательным условием является прямолинейность выработки по всей длине става конвейера и отсутствие участков с резким изменением угла ее наклона в вертикальной плоскости [7].
В соответствии с требованиями Правил безопасности ленточные конвейера должны оборудоваться: датчиками контроля бокового схода ленты типа КСЛ, отключающими привод конвейера при сходе ленты в сторону более 10% ее ширины; устройствами по очистке лент и барабанов; тормозными устройствами; устройствами, улавливающими грузовую ветвь ленты при ее разрыве, или устройствами, контролирующими целостность тросов и стыковых соединений резинотросовых лент в выработках с углом наклона более 10 градусов; средствами защиты, обеспечивающими отключение привода конвейера при превышении допустимого уровня транспортируемого материала в местах перегрузки, снижении скорости ленты до 75% номинальной (пробуксовка), превышении номинальной скорости ленты бремсберговых конвейеров на 8%; устройством для отключения привода конвейера из любой точки по его длине; средствами пылеподавления в местах перегрузок; средствами автоматического и ручного пожаротушения [8].
Монтаж системы автоматизации:
- перед монтажом аппаратуры и средств автоматизации проверяют комплектность, делают внешний осмотр и ревизию внутреннего монтажа. Для проверки работоспособности комплекса средств автоматизации рекомендуется полностью смонтировать всю аппаратуру и путем имитации отдельных режимов убедиться в правильном функционировании как о тдельных блоков, так и аппаратуры в целом. Для имитации необходим генератор, меняется по фиксированным частотами и усилитель;
- основные работы при монтаже электропроводок предусматривают разбивку трасс с разметкой мест установки крепежных, защитных, разветвленных и других элементов на строительных конструкциях, технологическом и другим оборудовании; подготовку трассы к установке конструкций электропроводки, пробивки проемов, отверстий, ниш; установка изделий для крепления, прокладка и закрепление проводов и кабелей в конструкциях;
- соединения и присоединения проводов и кабелей выполняют в соединительных и разветвленных коробках, внутри корпусов электроустановочных изделий, аппаратов и машин, в специальных нишах строительных конструкций. Провода и кабели соединяют и присоединяют в местах, доступных для осмотра и ремонта. В местах присоединения они не должны подвергаться воздействию механических усилий и иметь запас, обеспечивающий возможность повторного соединения; в поверхностных установках основные элементы автоматизации располагают в щитах, панелях и пультах, что является связующим звеном между объектом управления и оператором;
- в помещениях с большой запыленностью и высокой влажностью, возможностью механических повреждений аппаратов и проводов, а также для защиты обслуживающего персонала от прикосновения к токоведущим частям аппаратов и сборок применяют щиты шкафного типа;
- проводка в щитах выполняется проводами с медными жилами, прокладываемых открыто или жгутами вертикально по кратчайшим расстояниям так, чтобы не закрывать доступ к контактам и крепежных устройств. Расстояние между закрепленными жгутами на прямых участках должно быть не менее 300 мм и 5055 мм до и после поворота. Переход жгута из неподвижной части на подвижную (раму, двери, крышку и т.д.) выполняется многопроволочными проводами и должен иметь компенсатор, работающий на кручение. При повороте подвижной части жгут проводов не должен касаться элементов щита. Если это требование не выполняется, то он должен быть защищен в местах касания от повреждений [9].
Мероприятия по предотвращению пожаров:
- надежную и непрерывную защиту кабелей, электрооборудования от утечек тока на землю, замыкании, искроопасности и перегрева;
- содержание и обслуживание оборудования строго в соответствии с паспортом, особенно в отношении смазки трущихся поверхностей;
- НЕ допуск открытого огня на территории котельной;
- наличие специального противопожарного оборудования, предупреждающих плакатов и противопожарного трубопровода;
В случае возникновения пожара разрабатываются специальные организационно-технические мероприятия по спасению людей:
- план ликвидации аварий с включением в оперативную часть его наиболее вероятных случаев с комплексом мер по спасению людей и устранению последствия аварий;
- своевременный инструктаж и ознакомление персонала с их действиями при возникновении аварии;
- постоянное поддержание и контроль состояния запасных выходов в котельной;
- обеспечение всех работающих средствами индивидуальной оптового защиты, в том числе самоспасателями;
- для всех лиц, поступающих на работу, проводится инструктаж, с ознакомлением их с имеющимися средствами пожаротушения и правилами их применения;
- План ликвидации аварии существующий на шахте должен быть разработан в строгом соответствии с
Инструкцией по составлению планов ликвидации аварий
,Правил безопасности в угольных шахтах
[10].
Выводы
В результате выполнения данного дипломного проекта была разработана печатная плата управления работой конвейерного транспорта с применением ленточного конвейера по которым достигается его оптимальная работа.
Приняв за основу эти критерии управления был разработан блок автоматического регулирования натяжения ленты ленточного конвейера магистральной конвейерной линии, которое удовлетворяет заявленным к ней требованиям. То есть, устройство автоматизации позволяет регулировать работу магистральной конвейерной линии в соответствии с поставленной задачей оптимального функционирования конвейерным транспортом.
Разработана структурная и принципиальная схемы блока, которые отображают структуру построения устройства. Разработан алгоритм, который описывает последовательность работы блока.
И, как результат проведенной работы был разработан блок автоматического регулирования натяжения ленты ленточного конвейера магистральной конвейерной линии, который применяется в составе системы автоматизированного управления разветвленными конвейерными линиями АУК.3.
При написании данного реферата магистерская работа еще не завершена. Окончательное завершение: июнь 2024 года. Полный текст работы и материалы по теме могут быть получены у автора или его руководителя после указанной даты.
Список источников
- Стадник, Н. И. Справочник по автоматизации шахтного конвейерного транспорта / Н. И. Стадник, В. Г. Ильюшенко, С. И. Егоров и др.– Киев: Техника, 1992. – 436 с.
- Батицкий, И. А. Автоматизация производственных процессов и АСУ ТП в горной промышленности/ И. А. Батицкий, В. И. Куроедов, А. А. Рыжков. – Москва: Недра, 1991. – 303 с.
- Пейсаховича, Г. Я. Подземный транспорт шахт и рудников/ Под общей ред. Г. Я. Пейсаховича, И. П. Ремизова. – М.: Недра, 1985. – 565 с.
- Маренич, К. Н. Электрооборудование технологических установок горных предприятий: учебник для вузов / К.Н. Маренич [и др.] ; К.Н. Маренич, В.В. Калинин, Ю. В. Товстик и др. – Донецк : ДонНТУ ; Харьков : УІПА, 2009. – 372с.
- Курносов, В. И. Научные основы автоматизации в угольной промышленности: опыт и перспективы развития: монография / В. Г. Курносов, В. И. Силаев; Междунар. институт независимых педагогических исследований МИНПИ – ЮНЕСКО, ОАО
Автоматгормаш им. В. А. Антипова
. – Донецк: изд-воВебер
(Донецкое отделение), 2009. – 422 с. - Груба В. И. Технические средства автоматизации в горной промышленности. – В.И. Груба, Э. К. Никулин, А. С. Оголобченко –К.: ИСМО, 1998. – 373 с.
- Овсянников, Ю. А. Автоматизация подземного оборудования: справ. рабочего / Ю. А. Овсянников, А. А. Кораблев, А. А. Топорков. – Москва: Недра, 1990. – 287с.
- Правила безопасности в угольных шахтах [Электронный ресурс]: утв. приказом Гос. Комитета горного и тех. надзора ДНР и Министерством угля и энергетики ДНР 18.04.2016 г. № 36/208: ввод в действие 17.05.2016. – Донецк, 2016. – Режим доступа:https://doc.minsvyazdnr.ru. – Загл. с экрана.
- Каминский, М. Л. Монтаж приборов и систем автоматизации / М. Л. Каминский, В. М. Каминский. – Москва : Высшая школа, 1997. – 304 с.
- НПАОП 10.0 – 5.18 – 04. Инструкция по противопожарной защите угольных шахт.