Abstract
Contents
- 1. Relevance of the topic
- 2. Blast furnace smelting, main stages and goals
- 3. The influence of carbon on the quality and properties of the resulting steel
- 4. Chemical reactions of reduction of iron oxides using coke nut
- List of sources
1.Relevance of the topic
It is known that the cost of cast iron depends by 35-45% on the cost of the main blast furnace fuel - coke, therefore scientists and researchers around the world continue to work on reducing its specific consumption in blast furnaces (Figure 1).
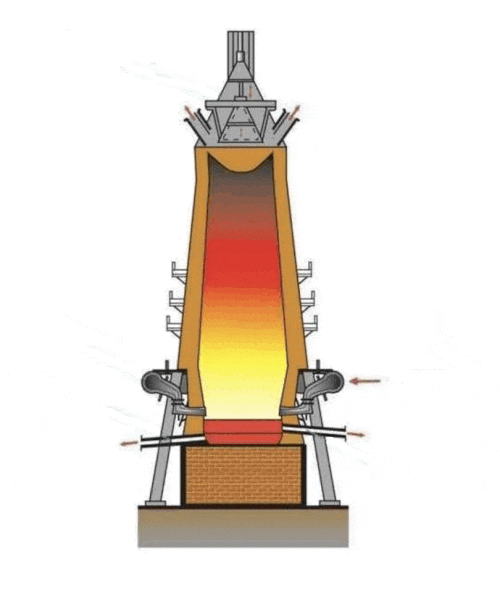
Figure 1 – Burnt furnace
(Animated figure. File size 66.96 KB; number of frames - 6; number of playback cycles - 3.)
One of the most common ways to reduce the specific consumption of coke is its preliminary preparation according to its fractional composition. Screening event coke of such fractions as <25 mm and >80 mm, allows you to improve the quality of skip coke in terms of such indicators as mechanical strength (M40, M25, M10), hot strength (CSR) and reactivity (CRI). The use of such an event has a beneficial effect on progress of blast furnace smelting: gas dynamics of the charge column improves and specific consumption decreases skip coke.
It is known that the most effective coke fraction for medium- and large-volume blast furnaces is 40-80 mm, the use of which ensures reaching the maximum level of productivity. Preparation of coke according to its fractional composition for blast furnace smelting predetermines the formation of a large amount of coke screenings with a fraction of less than 40 mm. As one of the options for the rational use of coke screenings, it is proposed to reseed it with the separation of the so-called coke nut and then load it into a blast furnace mixed with the iron ore part of the charge.
The first experiments in the use of spit nuts date back to the middle of the last century. The coke nut was first used at the Dnepropetrovsk Metallurgical Plant in 1967. Coke nut of fraction 10-40 mm in the amount of 93-97 kg/t of pig iron was loaded into blast furnaces in a mixture with sinter [1]. Experiments have shown that the introduction of coke nuts in an amount of 16.3-17.6% of the specific coke consumption reduces the total consumption of solid fuel by 1.8-9.9%.
Substantial studies of the effect of mixing coke with iron ore materials were carried out under the guidance of prof. IN AND. Loginova. It has been shown that when mixing coke with agglomerate, the gas-dynamic resistance of the charge decreases by 12-25% compared to layer-by-layer laying, and an increase in the degree of CO gas utilization by 1-3% is observed. Due to the reasons listed above, blast furnace productivity increased by 1.5-4.0% while coke consumption decreased by 4-8%.
2. Blast furnace smelting, main stages and goals
Blast smelting is an important process in steel production that is used to produce iron and steel from iron ore materials such as iron ore and slag (Figure 2). This process is a key step in the metallurgical industry and plays an important role in the production of a variety of metal products [2]. The blast furnace smelting process includes the following main steps.
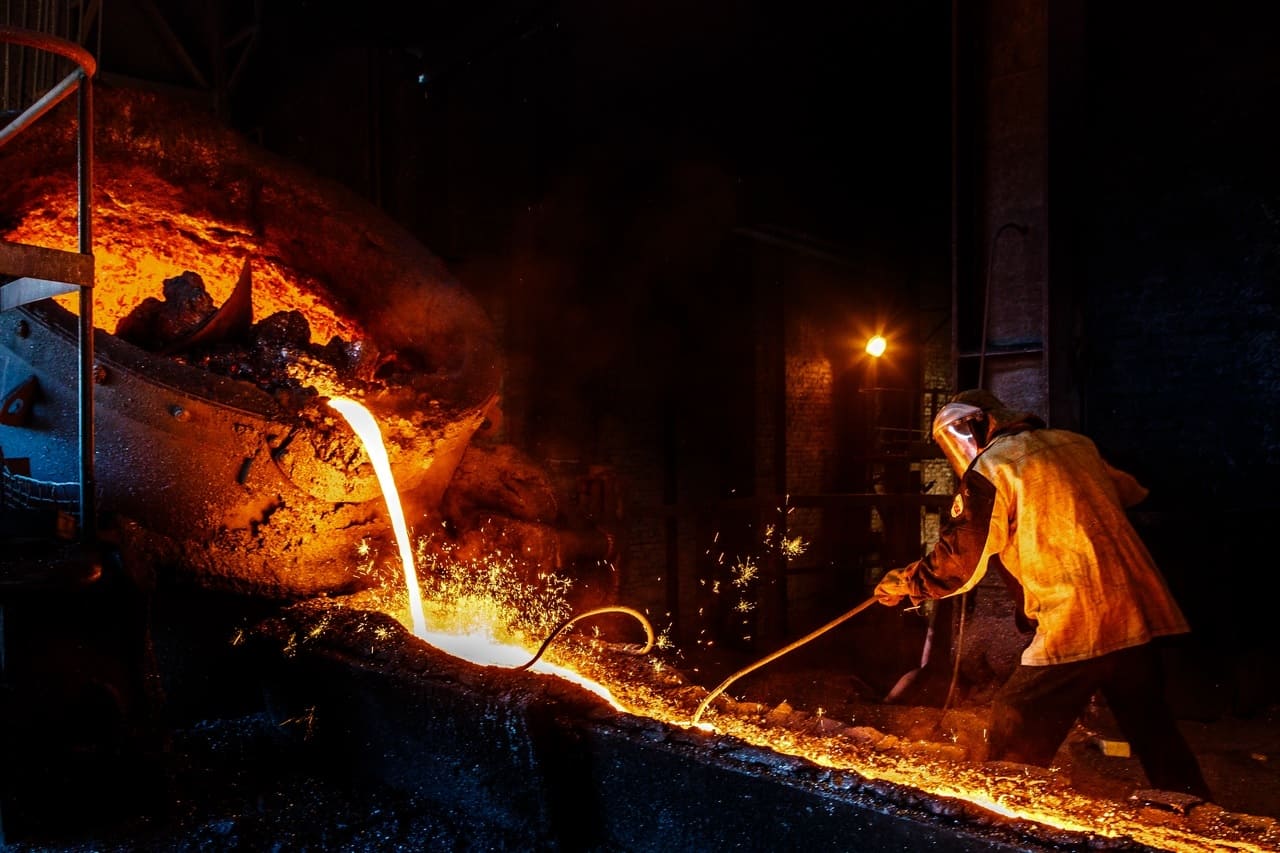
Рисунок 2 – Blast furnace smelting process
- Preparation of Raw Materials: At the beginning of the process, it is necessary to prepare raw materials including iron ore and coke (heat-treated coal), as well as additives such as lime and other materials, to achieve the required chemical composition.
- Loading Raw Materials: The prepared raw materials are loaded into the blast furnace, a large vertical vessel in which the smelting will take place.
- Roasting and reduction: the process begins with the firing of raw materials using hot air and oxygen. As a result of this process, the materials oxidize and the cast iron becomes a liquid.
- Steel Formation: To form steel, necessary alloying elements are added and reduction is carried out to reduce the carbon and other impurities in the cast iron. This makes it possible to obtain steel with the desired mechanical properties.
- Pouring: Once steel is produced, it is poured from the blast furnace and distilled into molds to create specific products such as bars, slabs, rods and other metal products.
- Processing and finishing: The resulting steel blanks may be subjected to additional processing processes such as rolling, heating, cooling and other operations to achieve the required dimensions and characteristics.
Blast furnace is of key importance in steel production for several reasons.
- Mass production: Blast furnace melting allows the production of steel in large quantities, which significantly reduces the cost and ensures the supply of metal to a variety of industries.industry.
- Reuse of Raw Materials: This process allows different types of iron ore materials, including lower grades, to be used and converted into high quality steel.
- Flexibility and Adaptability: Blast furnace melting allows the composition and characteristics of the resulting steel to be easily changed, making it suitable for a wide range of applications.
- Economical: The efficient process and the ability to use many types of raw materials make blast furnace smelting economical for metallurgical plants.
As a result, blast furnace smelting is an integral part of steel production and provides the global metallurgical industry with the necessary materials for construction, mechanical engineering, the automotive industry and many other areas.
3. The influence of carbon on the quality and properties of the resulting steel
Carbon plays a critical role in the blast furnace smelting process of iron ore and has a significant impact on the quality and properties of the resulting steel for several reasons.
Reduction of iron oxide: Carbon serves as a reducing agent in the blast furnace smelting process. Iron ore usually contains oxidized forms of iron such as hematite (Fe2O3) and magnetite (Fe3O4). Carbon reacts with iron oxides at high temperatures, turning them into pure iron and carbon dioxide (CO2). This process, known as reduction, extracts pure iron from [3-5] ore.
Adjusting carbon in steel: Carbon is also added to the iron during the processing process to achieve the desired carbon content in the steel. The amount of carbon in steel significantly affects its mechanical properties, such as strength and hardness. Low carbon content makes steel softer and more pliable, while high carbon content makes it hard and brittle. Maintaining an optimal level of carbon allows you to obtain steel with the desired properties.
Formation of carbon alloys: Carbon is also used to create different types of steel with different properties by adding other elements such as chromium, nickel, molybdenum and others [6]. These alloys improve the mechanical and chemical properties of steel depending on specific requirements and applications.
It is important to note that control of the carbon and other alloying elements in steel is a fundamental aspect of steel production, and it affects its quality, strength, corrosion resistance and other properties. Carbon plays a key role in this process and its levels must be strictly controlled to produce steel with the required characteristics.
Coke (or simply coke) is an important component in the blast furnace smelting process as it is used to introduce carbon into the iron [7]. Physical properties of coke nut:
- Porosity: Coke is characterized by high porosity, which makes it an excellent material for the blast furnace smelting process. This porosity allows gases to pass through easily, which is important for good air circulation and oxygen supply into the domain.
- High Density: Coke has a high density, which means it provides good support for the iron grains in the domain, which promotes a stable smelting process.
- Thermal conductivity: coke has good thermal conductivity, which allows for even distribution of heat within the domain and ensures uniform melting of iron.
Chemical properties of coke nut:
- Carbon content: Coke contains significant amounts of carbon, making it an ideal source of this element for the blast furnace smelting process. The carbon from the coke reacts with iron to form carbon iron, which is important for creating steel with the desired characteristics.
- High temperature resistance: Coke is resistant to high temperatures, allowing it to be used in blast furnace conditions where temperatures can reach several thousand degrees Celsius.
- Minimum impurities: Coke usually contains a minimum of impurities, which is important to prevent contamination of the steel during the smelting process.
Nut coke is used as fuel in a blast furnace, where it burns in the presence of oxygen, creating high temperatures and causing the necessary reaction between the carbon from the coke and the iron. As a result of this reaction, the process of iron reduction occurs, and carbon combines with iron to form carbon iron. This makes it possible to control the carbon content of the steel, which is a key factor in determining its mechanical and chemical characteristics.
Nut coke's ability to provide carbon and withstand high temperatures makes it an ideal material for high-quality and efficient blast furnace smelting.
4. Chemical reactions of reduction of iron oxides using coke nut
The reduction process of iron oxides using coke (coke) is a chemical reaction that involves the reduction of iron oxides (Fe2O3 and Fe3O4) to metallic iron (Fe) using carbon (C) in the coke. This process is often used in the metallurgical industry to obtain pure iron from [8] ore.
Main detailed chemical reactions occurring during the reduction of iron oxides with coke:
- Reduction of iron (III) oxide (Fe2O3): 2Fe2O3 + 3C -> 4Fe + 3CO2
In this reaction, iron oxide (Fe2O3) reacts with carbon (C) in the coke. The carbon in the coke is oxidized to form carbon dioxide (CO2), while the iron oxide is reduced to metallic iron (Fe). - Reduction of iron (II) oxide (Fe3O4): 3Fe3O4 + 4C -> 9Fe + 4CO2
This reaction is similar to the first, but here iron oxide (Fe3O4) reacts with carbon (C) to form metallic iron (Fe) and carbon dioxide (CO2).
The redistribution of carbon in these reactions occurs as follows:
• at the beginning of the process, carbon is in the coke nut in the form of solid carbon (C). During the reactions, it is oxidized and converted into carbon dioxide (CO2), which is released into the atmosphere as a combustion product.
• At the same time, the carbon that was previously in the iron oxides is redistributed to the atomic level and reacts with the iron oxides. It serves as a reducing agent that donates its electrons to the iron oxides, causing the iron oxides to be reduced to metallic iron.
Thus, the carbon from the coke is involved in the reduction of iron oxides, and its atoms are redistributed to ensure the reduction of iron and the formation of carbon dioxide. This process is key to the production of pure metallic iron and other metals from ores.
The use of coke nut in the blast furnace smelting process can have a significant impact on the physical and chemical properties of the resulting steel [9-10]. It is important to note that coke is a calcium carbonate that is added to a blast furnace for various purposes such as improving the quality of steel and regulating the smelting process.
- Chemical composition.
Adding coke can change the chemical composition of the steel. Coke can introduce calcium oxide (CaO) and magnesium oxide (MgO) into the melt, which can affect volatile levels and oxygen activity in the system. This can lead to changes in the structure and properties of the steel. - Mechanical properties.
The use of coke can improve the mechanical properties of steel, such as strength and impact resistance. This is due to the formation of internal inclusions, which help improve the structure of the steel. - Content of inclusions.
Coke can also affect the number and type of inclusions in steel. It can serve as a nucleant for the formation of sulfide and oxide inclusions, which can improve control of their size and distribution. - Reduction of phosphorus content.
The introduction of coke can help reduce the phosphorus content in steel. This is important because high phosphorus content can negatively affect the mechanical properties of steel. - Final steel composition.
As a result of the introduction of coke, the final chemical composition of the steel may change. This may require additional composition adjustments to achieve the required characteristics. - Thermal conductivity and temperature distribution.
The use of coke may also affect thermal conductivity and uniform temperature distribution in the melt. This can affect the structure and physical properties of the steel.
All of these changes will depend on the specific conditions and parameters of the blast furnace process, as well as the type and quantity of coke used in the process. Therefore, it is necessary to conduct detailed studies and experiments to determine the optimal conditions for using coke to achieve the required properties of steel.
The use of coke in the blast furnace smelting process affects the physical and chemical properties of steel. Here are the changes you can observe:
- Chemical composition of steel.
Carbon: Coke may contain carbon, which changes the final chemical composition of the steel. Adding nut can increase the carbon content, affecting the hardness and strength of the steel.
Sulfur and phosphorus: coke oreNeck may also contain traces of sulfur and phosphorus, which can affect the relevant chemical properties of the steel, such as its corrosion resistance. - Mechanical properties of steel.
Strength: Adding coke can increase the strength of steel by increasing the carbon content and improving the structure.
Hardness: Changes in carbon content can also affect the hardness of the material.
Impact toughness: The behavior of steel under impact loads can change due to changes in structure and composition. - Steel structure.
Grit: The use of coke can affect the grain size of the steel, which can affect its mechanical properties.
Precipitates and inclusions: The addition of nuts can also cause the formation of new phases or inclusions in the steel structure. - Processing process.
Energy Consumption: The use of coke can affect the energy consumption during the steel smelting and forming process.
Process Efficiency: The introduction of nut can also affect the efficiency of the metal processing process, melting rate, product yield, etc.
This is not an exhaustive list of changes, and the effect of coke may depend on its chemical composition, particle size, amount added, and other factors. Results may vary depending on specific steel production conditions and processing technology.
Some general aspects of improving blast furnace technology using coke:
- Optimization of the melting process.
Analyzing and optimizing blast furnace process parameters such as temperature, pressure, and speed can significantly affect the efficiency of the process and the quality of the metal produced. - Coke quality control.
Ensuring high quality coke used in the process can improve smelting efficiency and reduce equipment maintenance costs. - Use of advanced technologies.
The introduction of modern technologies and innovative methods in metallurgy can improve productivity, energy efficiency and reduce environmental impact. - Waste management and environmental aspects.
Developing and implementing waste management programs, as well as taking into account the environmental aspects of the process, will help meet safety standards and reduce negative environmental impacts. - Personnel training and development.
Training staff on advanced techniques and technologies can improve the skills of employees, which affects the overall efficiency of production. - Strategic planning.
Developing long-term development strategies, including investments in research and development, will allow us to remain competitive in the market and cope with industry challenges. - Data monitoring and analysis.
Regular monitoring of production data and subsequent analysis allows you to identify bottlenecks in the process and make adjustments to improve efficiency.
List of sources
- Борисоглебский Ю. В., Ветюков М. М. Металлургия цветных металлов: Учебное пособие. - Л., изд. ЛПИ, 1986. - 88 с.
- Bahgat, М., Abdel Halim, K.S., El-Kelesh, Н.А., Nasr, M.I. Blast furnace operating conditions manipulation for reducing coke consumption and CO 2 emission// Steel Research International. 2012. № 83(7). P. 686-694.
- Анализ процессов доменной плавки при обогащении дутья кислородом / И.Г. Товаровский, В.П. Лялюк, А.Е. Меркулов и др. II Бюл. ин-та «Черная металлургия». 2011. № 5. С. 20-33.
- Интенсификация работы доменных печей подбором оптимального соотношения расходов природного газа и кислорода / В.А. Гостенин, С.Н. Пишнограев, А.В. Чевычелов и др.//Сталь. 2012. №2. С. 7-11.
- Интенсификация работы доменных печей путем оптимального соотношения расходов природного газа и кислорода / В.А. Гостенин, С.Н. Пишнограев, Н.С. Штафиенко и др. II Бюл. инта «Черная металлургия». 2011. № 6. С. 16-22.
- Спирин Н.А., Федулов Ю.В., Овчинников Ю.Н. Распределение технологического кислорода между печами доменного цеха II Изв. вузов. Черная металлургия. 1993. № 11-12. С. 68-72.
- Khaled S Abdel-Halim, V. N. Andronov, М. I. Nasr. Blast furnace operation with natural gas injection and minimum theoretical flame temperature II Ironmaking & Steelmaking. 2009. № 36(1). P. 12-18.
- Khaled S Abdel-Halim. Effective utilization of using natural gas injection in the production of pig iron II Materials Letters. 2007. №61(14-15). P. 3281-3286.
- Сибагатуллин С.К., Майорова Т.В. К расчету показателей хода доменного процесса при повышенном общем перепаде давления газов II Вестник Магнитогорского государственного технического университета им. Г.И. Носова. 2010. № 3. С. 16-18.
- Сибагатуллин С.К., Майорова Т.В. Увеличение работы газового потока в доменной печи с повышением общего перепада давления по высоте II Вестник Магнитогорского государственного технического университета им. Г.И. Носова. 2011. № 1. С. 14-16.