Донецкий национальный технический университет
Герчиков Виталий Иванович
Исследование и обоснование структуры и параметров электронной системы измерения статических и динамических нагрузок при испытании стальных канатов
Специальность "Электронные системы" - 7.090803
Автореферат магистерской выпускной работы
Руководитель - Зори Анатолий Анатольевич
Донецк 2002
E-mail: gerchikov_vitaliy@torba.com
Актуальность темы
В настоящее время широко обсуждается вопрос о прочности, сроках службы и работоспособности стальных канатов в шахтных подъёмных установках, лифтах и других механизмах. Причиной этого является малый срок службы канатов по сравнению с другими основными деталями и узлами подъёмных устройств. Поэтому необходимо достаточно точно определять максимальные разрывные усилия, которые могут выдерживать стальные канаты, чтобы предотвращать нежелательные последствия аварийных ситуаций. Проблема заключается в определении момента начала порыва каната при динамических нагрузках, которые он может испытывать в реальных условиях эксплуатации.. В связи с этим решение задачи точного определения допустимой нагрузочной способности стальных канатов как в статическом так и в динамическом режимах является весьма актуальным.
Цель работы
Разработка структурной и принципиальной схемы электронной силоизмерительной системы для испытания стальных канатов с возможностью прогнозирования порыва. Исследование динамических процессов, возникающих в канате при разрушении.
Проблемы измерения силы
Измерение силы связано с рядом особенностей, которые можно свести к четырем основным проблемам [1, стр. 16-17]:
• Требуемая степень точности. Измерения сил должны производиться, как правило, со значительно более высокой точностью, чем измерения других механических величин. Это необходимо учитывать как при любом теоретическом анализе, так и при практическом использовании силоизмерительных устройств. При теоретическом решении вопросов измерения силы во многих случаях уже на первом этапе нельзя ограничиваться описанием задачи только в первом приближении.
• Векторный характер измеряемой величины. Задачей устройства для измерения силы является преобразование векторной величины (силы) в скалярную величину, т. е. такую, которая однозначно описывается только одним параметром. Это требование приводит в конце концов к основным проблемам измерения силы.
• Ограниченность механических напряжений в реальных материалах. Когда говорят просто о силе, то всегда подразумевают, что эта физическая величина приложена в одной точке. Но на практике такой подход — это лишенная всякого смысла идеализация, так как реальные материалы могут выдерживать только ограниченные механические напряжения. Поэтому для измерения сил всегда необходимы определенные участки поверхности. Строго говоря, по существу мы имеем дело не с силоизмерительной техникой, а лишь с техникой измерения суммарных значений полей механических напряжений. С этим связаны также весьма сложные и еще далеко не изученные в количественном отношении явления распределения сил.
• Различное поведение отдельной измерительной системы и той же системы, встроенной в измерительную установку. Силоизмерительная система в принципе вполне охарактеризована, если известна зависимость между процессами на ее силовоспринимающих поверхностях и выходной величиной или она описывается математически. Когда такая система встраивается в полный технический силоизмерительный комплекс, может произойти существенное изменение указанной зависимости. В общем, суммарная характеристика становится сложнее, однако она может и упроститься.
Из перечисленных проблем видна сложность подробного освещения рассматриваемой области. Таким образом, становится понятным, почему до сих пор практически отсутствуют достаточно полные, обобщающие работы по всему кругу соответствующих вопросов. Это относится прежде всего к теоретическому анализу проблем, который может в значительной степени способствовать их пониманию.
Назначение
Система предназначена для использования в составе разрывных силоизмерительных установок при испытании стальных канатов на предприятиях, выпускающих канатную и сталепроволочную продукцию. Система выполняет следующие функции:
1) Измеряет максимальные разрывные усилия при статических и динамических
нагрузках;
2) Определяет максимальное число циклов нагружения при динамических нагрузках;
3) Прогнозирует срок службы каната.
Система рассчитана для испытаний стальных канатов, диаметры которых составляют 7.8, 10.5, 12.0 мм. В соответствии с ГОСТ 3077 - 80 разрывные усилия стальных канатов маркировочной группы 1570 лежат в диапазоне от 29.9 до 72.0 кН.
Содержание работы
Область данных измерений достаточно специфична и требует особого подхода к решению этой задачи. Рассмотрим процессы и явления, возникающие в стальном канате под действием приложенной силы. В процессе эксплуатации каната его проволоки испытывают напряжения растяжения, изгиба, кручения, контактного нагружения и др. Роль этих напряжений на процесс износа каната различна, процесс разрушения каната той или иной конструкции, имеющей различное число проволок в пряди и прядей в канате, также неодинаков. Существенное влияние на механическую прочность, срок службы каната оказывает материал, процесс свивки и целый ряд других технологических факторов.
Для измерения сил используют различные физические эффекты, для которых характерна определённая зависимость между силой и другой величиной, например деформацией (относительной или абсолютной), давлением, пьезоэлектричеством, магнитострикцией и т.д. Наиболее распространённым способом измерения силы является использование упругой деформации [2, стр. 37-38].
Под деформацией (относительной) понимают отношение:
, |
(1) |
где de - относительная деформация;
DL = (L - L0) - разница между начальной длиной (базой) L0 на недеформированном участке и его
длиной L после приложения к нему силы, действующей в продольном направлении.
В качестве чувствительного элемента первичного измерительного преобразователя используются полупроводниковые тензорезисторы. В отличие от других чувствительных элементов они обладают рядом преимуществ, которые заключаются в следующем:
1) малые размеры и масса;
2) динамическая и статическая характеристики одинаковы;
3) измеряют статические и динамические нагрузки;
4) большая чувствительность;
5) отсутствие гистерезиса;
6) диапазон измеряемых сил от 10кН до 5МН.
Однако у полупроводниковых тензорезисторов имеется один недостаток, который заключается в значительной температурной зависимости их сопротивления от температуры. По условиям проведения испытаний, температура в лабораторных помещениях должна находиться в диапазоне 14 - 28 °С. При таких незначительных колебаниях температуры и применении несложных схемных решений, заключающихся в компановке тензорезисторов и термокомпенсирующих элементов, в первичном измерительном преобразователе (ПИП) можно практически исключить влияние температуры. Тензорезисторный ПИП [2, стр. 104-108], приведенный на рис. 1, включается в измерительный канал, состоящий из нормирующего усилителя, линии связи, фильтра и согласующего усилителя.
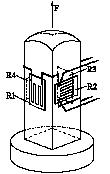
Рисунок 1 - Тензорезисторный ПИП
R1, R3 - тензорезисторы в направлении действия силы;
R2, R4 - тензорезисторы в направлении, перпендикулярном действию силы
При проведении статических испытаний на разрыв в целом, измерительная задача разрешима с помощью вышеописанного ПИП. Однако при необходимости определения частичного порыва (выхода из строя проволок, одной или нескольких прядей) задача значительно усложняется, а при динамических испытаниях иногда становится неразрешимой. Даже применение микропроцессоров и сложного программного обеспечения не всегда позволяет решить эту задачу.
С целью определения возможности обнаружения разорванных проволок каната, было проведено исследование изменения электромагнитных характеристик концевых участков канатов в процессе их разрушения пульсирующей нагрузкой [4, стр. 209-212]. Измерения выполнялись датчиком, представляющим собой катушку индуктивности, которая устанавливалась внутри конической втулки. При питании датчика переменным током в отрезке каната, заключённого внутри конической втулки создавалось переменное магнитное поле. Резкие изменения магнитного сопротивления концевого участка каната при обрывах проволок позволили осуществить эффективный контроль числа оборванных проволок. На рис. 2 приведен график относительного изменения реактивного сопротивления магнитной цепи e при разрушении проволок образца каната.
Рисунок 2 - Изменения реактивного сопротивления магнитной цепи
при разрушении проволок образца каната
Из графика следует, что в моменты обрыва проволок происходят резкие изменения реактивного сопротивления магнитоупругого датчика, обусловленные изменением усилий в стальном канате.
Исследования процессов, протекающих в отрезке каната в момент обрыва проволоки, выполнялись с помощью описанного выше датчика, питаемого постоянным током и намагничивающего отрезки каната в продольном направлении. Изучение осциллограмм импульсов, генерируемых датчиками, показало, что при обрыве проволока совершает свободные продольные затухающие колебания, а вдоль каната распространяется ударная волна, что и является причинами резких изменений магнитного сопротивления концевого участка. При этом постоянные магнитные потоки изменяются, под действием разрывов проволок каната, и в обмотках датчиков индуцируется импульс э.д.с., который может быть зарегестрирован одним из известных методов.
Для наглядности процессов, протекающих в магнитоупругом датчике при разрушении каната, воспользуемся методом моделирования на ЭВМ. Цифровое моделирование обладает универсальностью, гибкостью и экономичностью.
При действии на канат случайного возмущающего фактора - растягивающих нагрузок (рис. 3) происходит изменение магнитной проницаемости магнитоупругого датчика, в соответствии с зависимостью [5]:
,
где D
m
-
абсолютное изменение магнитной проницаемости;
l
-
магнитострикция;
m
-
магнитная проницаемость ненагруженного образца;
m0
- магнитная проницаемость вакуума, равная 4×
p
×
10-7 (Вб / м2)
s
-
механическое напряжение.
Рисунок 3 - Изменение силы, действующей на образец каната
Рисунок 4 - График изменения индуктивности магнитоупругого преобразователя
Моделирование выполнялось для образца каната диаметром 7.8 мм, максимальное разрывное усилие которого составляет 29.9 кН. В момент превышения нагрузки максимально допустимого значения происходит разрушение образца каната и вдоль него распространяется продольная ударная волна, имеющая затухающий колебательный характер, которая описывается дифференциальными уравнениями второго порядка с коэффициентами, зависящими от материала каната, его структуры и геометрических размеров. График изменения индуктивности магнитоупругого преобразователя представлен на рис. 4.
Следовательно, введение в автоматизированную систему контроля магнитоупругого датчика, позволяет с высокой точностью определять максимальные разрывные усилия стальных канатов при статических и динамических испытаниях, и фиксировать моменты обрыва отдельных проволок. Имея соответствующие статистические данные результатов измерений, можно с помощью предложенной системы прогнозировать срок службы стальных канатов в зависимости от условий их эксплуатации. Срок службы определяется двумя факторами: количеством циклов нагружения и временем эксплуатации. Исследование работоспособности и установление оценки производились по фактическим материалам использования подъёмных канатов в действительных условиях работы [6, стр. 271-275]. Применение теории вероятностей и методов математической статистики позволило установить законы распределения, параметры и плотность распределения исследуемых оценок работоспособности.
Сходимость экспериментальных и теоретических распределений проверялась с помощью критерия Колмогорова. Взаимозависимость факторов устанавливалась корреляционным анализом с определением параметров по методу наименьших квадратов.
Предложена следующая оценка работоспособности подъёмных канатов, определяемая сроком службы Т:
, |
(2) |
где L -
длина вертикального пути сосуда (км);
Ц -
количество циклов нагружения (тыс.);
Т -
срок службы (тыс. дней);
Пa
i -
произведение коэффициентов влияния;
С -
константа, равная 58,0.
Вероятность нахождения величины С в интервале ±25% равна 0,923. Отклонение константы С от своего среднего значения объясняются различием качества подъёмных канатов, обусловленного технологическими процессами их изготовления. Входящие в формулу коэффициенты влияния ai приведены в специальных таблицах.
Предлагаемая оценка работоспособности подъёмных канатов позволяет сравнивать качество однотипных канатов при их работе в разных эксплуатационных условиях, оценивать и сопоставлять влияние эксплуатационного характера в случаях применения канатов одинакового качества, но работающих на разных подъёмных установках, а также прогнозировать предполагаемый срок службы при определённом количестве циклов нагружения.
Структурная схема предлагаемой системы изображена на рис. 5.
Рисунок 5 - Структурная схема автоматизированной системы контроля и управления
процессом испытания стальных канатов при статических и динамических нагрузках
Основные результаты работы
• Рассмотрены проблемы измерения динамических нагрузок при испытании стальных канатов
и возможные способы их регистрации.
• Предложена методика оценки работоспособности стальных канатов.
• Приведена структурная схема автоматизированной системы контроля и управления процессом
испытаний.
Литература
1. Бауман Э. Измерение сил электрическими методами; Под ред. И.И.Смыслова. -
М.: Мир, 1978. - 430 с.
2. Измерения в промышленности: Справочник: в 3 кн.; Под ред. П.Профоса; [2-е изд., перераб. и доп.]: Способы измерения и аппаратура. -
М.: Металлургия, 1990. - 382 с.
3. Стальные канаты / Базовая науч. исслед. лаборатория канатов каф. ПТМ Одесск. политехн. ин-та. -
К.: Техніка, 1964. - 307 с.
4. Стальные канаты. [Ред. коллегия: д-р техн. наук М.Ф.Глушко и др.]. Вып. 7. Киев, Техніка, 1970. -
370 с.
5. Гуманюк М.Н. Магнитоупругие датчики в автоматике. -
К.: Техника, 1972. - 261 с.
6. Стальные канаты. [Ред. коллегия: д-р техн. наук М.Ф.Глушко и др.]. Вып. 6. Киев, Техніка, 1969. -
354 с.