|
Главная страница ДонНТУ |
| Страница магистров ДонНТУ
Механический факультет
Специальность: "Металлорежущие станки и инструменты"
Тема магистерской работы: "Обоснование выбора компоновок технологического оборудования
и транспортно-накопительных систем,
систем загрузки в гибкие производственные системы
для деталей типа плит".
Руководитель: проф. Калафатова Л.П.
Актуальность работы:
   Бурное развитие информатики и микропроцессорной техники подняло на принципиально новый уровень решение многих задач управления технологическими и производственными процессами. Тенденция перехода к автоматизированному производству затронула многие сферы хозяйства, в том числе и машиностроение. В основе автоматизации процессов лежит частичное или полное отстранение человека от непосредственного участия в производственном процессе.
   В современных условиях прогрессивным может быть только такое производство, которое способно учитывать изменение спроса заказчиков и может быстро переходить на выпуск новой продукции. В результате удается избежать выпуска не находящей спроса продукции бесполезного расходования ресурсов.
   Развитие автоматизации на ранних этапах характеризовалось отсутствием мобильности, динамичности - создание жестких автоматических линий, предназначенных для массового производства (срок окупаемости таких линий составляет не менее 8 - 10 лет).
   Однако единичное и мелкосерийное производство оставались практически неавтоматизированными. Именно поэтому возникла принципиально новая концепция автоматизированного производства - гибкие производственные системы (ГПС). Начальным этапом формирования направления автоматизации этих типов производств можно считать 60-е годы, когда впервые было сформулировано понятие "гибкое производство".
   Под гибкостью станочной системы понимают ее способность быстро перестраиваться на обработку новых деталей в пределах, определяемых техническими возможностями оборудования и технологией обработки группы деталей. Высокая степень гибкости обеспечивает более полное удовлетворение требований заказчика, оперативный переход к выпуску новой продукции, сохранение оправданного характера мелкосерийного производства, автоматизацию технологической подготовке производства на базе вычислительной техники, снижение затрат на незавершенное производство.
   Гибкое автоматизированное производство должно обладать следующими признаками:
   - гибкость состояния системы, то есть способность хорошо функционировать при различных внешних (появление нового ассортимента изделий, изменение технологии и др.) и внутренних (сбои в системе управления станками, отклонения во времени и качестве обработки и т.д.) изменениях;
   - гибкость действия, то есть обеспечение возможности легко включать в систему новые станки и инструменты для увеличения ее мощности в связи с увеличением объема производства;
   - гибкость системы группирования, то есть возможность расширения семейства обрабатываемых деталей;
   - гибкость технологии, определяющая способность системы учитывать изменения в составе выполнения технологических операций;
   - гибкость оборудования, которая характеризуется способностью системы справиться с переналадками в станках;    - гибкость транспортной системы, выражающаяся в бесперебойной и оптимальной загрузке металлорежущего оборудования по определенной, наперед заданной стратегии управления;
   - гибкость системы обеспечения инструментом;
   - гибкость системы управления, обеспечивающая наиболее рациональное построение маршрутов обработки и транспортных потоков с точки зрения различных критериев;
   - организационная гибкость производства, заключающаяся в возможности простого и незамедлительного перехода на обработку любой из освоенных системой деталей.
   Необходимость присутствия большинства из перечисленных выше признаков было положено в основу при проектировании гибких производственных систем, предназначенных для обработки деталей типа плит в условиях серийного производства. Решение задачи проектирования эффективных производственных систем для механической обработки деталей типа плит, которые находят широкое применение в различных отраслях промышленности, отличаясь многообразием конструкций, является достаточно актуальной.
   Учитывая, что в большинстве случаев плиты используются при изготовлении различного типа прессов, пресс-форм, элементов гидравлики, к ним предъявляются повышенные требования по точности и качеству обработки поверхностей. В настоящее время плиты изготавливаются преимущественно на универсальных станках фрезерной и сверлильной групп, что требует значительных затрат машинного и особенно вспомогательного времени. Детали этого типа могут обладать значительными размерами и массой, необходимостью удаления больших припусков, что является причиной роста усилий резания при фрезеровании и часто приводит к значительным погрешностям при обработке, поломке инструмента, а, следовательно, и к браку деталей. Все это отрицательно сказывается на автоматизации производства плит.
Практическая ценность:
   Отличительными чертами организации гибкого производства являются
следующие:
-интеграция технической подготовки и производства в единую производственную систему, что позволяет обеспечить непрерывность процесса от момента возникновения идеи до выхода готовой продукции. Конструкторская и технологическая подготовка, организация и нормирование труда, внутризаводское планирование, технический контроль и система управления перестают быть дискретными, разорванными процессами. В условиях ГПС происходит параллельное, одновременное выполнение различных частей этих процессов, а во многих случаях и органичное их слияние в единый комплекс;
-обработка деталей полностью в ГПС означает, что весь технологический процесс механической, а в отдельных случаях и термической обработки деталей совершается на ГПС при "неизменности объекта обработки, рабочего места и исполнителей", так как не отдельный станок, а вся ГПС и вся занимаемая ею площадь с различным оборудованием становятся рабочим местом. Это обеспечивается и главной отличительной особенностью концепции гибкого производства - концентрацией как можно более полной обработки каждой детали на одном обрабатывающем центре (ОЦ). В этом принципиальное отличие гибкого производства от поточного. Первое характеризуется параллельной обработкой различных деталей на одном рабочем месте, второе - обработкой одной детали на нескольких специализированных рабочих местах, расположенных в последовательности технологического процесса;
-стирание границ между производствами: массовым, серийным и единичным. Массовое производство характеризуется узкой специализацией отдельных рабочих мест при выполнении одной постоянно повторяющейся операции, высокой степенью автоматизации и предназначено для выпуска продукции узкой номенклатуры. Серийное производство характеризуется закреплением за каждым рабочим местом нескольких операций, между выполнением которых требуется переналадка или переустройство рабочего места. Оно предназначено для выпуска ограниченной продукции с заданной регулярностью чередования номенклатуры. Единичное производство характеризуется отсутствием какого-либо закрепления операций за отдельным рабочим местом, высокой долей ручного труда, выполнением различных операций при отсутствии какой-либо регулярности чередования операций и широкой номенклатурой выпускаемой продукции. Гибкое производство - прежде всего высокой степенью автоматизации, равной массовому производству, выполнением разных операций на одном рабочем месте(без переналадки), достаточно широкой номенклатурой деталей, одинаково экономично обрабатываемых любыми партиями при отсутствии требований к какой-либо регулярности чередования операци;.
-сокращение длительности производственного цикла обеспечивается обработкой детали в одну операцию от запуска до выпуска без перерывов и полной автоматизацией транспортно-складских процессов. Сокращаются рабочий период за счет применения станков типа ОЦ (автоматизация смены инструмента, смены заготовки детали, позиционирования и т.д.), длительность контрольных и транспортных операций за счет их совмещения, а также сокращения межоперационных и междусменных перерывов.
   Опыт эксплуатации ГПС в различных странах дает возможность провести сравнительный анализ преимуществ и недостатков гибкого производства по сравнению с традиционной организацией производства..
   Преимущества гибкого производства.
- Повышение мобильности производства (сокращение сроков освоения новой продукции, возможность обеспечения быстрой приспособляемости производства к изменению объекта изготовления, сокращение времени подготовки производства в среднем на 50%, уменьшение наименований и количества необходимого инструмента, сокращение времени установки заготовок на станке и т.д.);
- Повышение производительности труда (рост производительности труда на всех стадиях производства, сокращение времени цикла обработки каждой детали за счет автоматизации установки и снятия заготовок, обеспечение длительной работы без присутствия человека или при ограниченном количестве операторов, повышение коэффициента сменности);
- Повышение качества продукции (увеличение надежности управления станками, обеспечение стабильности качества продукции, сокращение времени сборки изделий, снижение брака и затрат на его ликвидацию, автоматизация контроля размеров обрабатываемых деталей непосредственно на станке);
- Снижение затрат на производство (снижение себестоимости продукции за счет роста производительности труда, сокращение сроков технической подготовки и вспомогательных работ, сокращение расходов на содержание производственных и вспомогательных площадей, снижение срока окупаемости).
   Проблемы и трудности всегда имеют место при внедрении новой техники, однако для ГПС они могут быть более значительными, так как это новая концепция производства. Рассмотрим их подробнее:
- Большие первоначальные капитальные вложения, связанные с приобретением и пуском ГПС.
- Сложности при проектировании и внедрении системы управления;
- Проблемы подготовки кадров - рабочий перестает быть оператором, знающим одну специальность, он должен владеть рядом профессий;
- Сложность проектирования ГПС и выполнения технико-экономического анализа.
   Исходя из того, что основной характеристикой гибкого производства является степень гибкости, которая может изменяться от нуля до абсолютной гибкости, все существующие виды могут быть разделены на четыре основные группы:
   Первая группа основывается на жесткой технологии производства, когда технологическое оборудование предназначено для выполнения одной детали, по окончании выпуска которого оно не может быть использовано для изготовления нового изделия. Обычно это специальное оборудование, станки и автоматические линии из специальных станков, используемые в массовом производстве. В этом случае какая-либо степень гибкости отсутствует.
   Вторая группа основывается на перестраиваемой технологии производства, при этом оборудование при замене отдельных его компонентов может использоваться для изготовления нового изделия или группы изделий. Примерами такого оборудования могут служить автоматические линии из агрегатных станков, созданные по агрегатно-модульному принципу.
   Третья группа основывается на переналаживаемых технологических процессах и соответствующем оборудовании, предназначенном для одновременного выпуска группы деталей. Для перехода на изготовление какой-либо одной группы деталей требуются перестройка, регулировка отдельных узлов, механизмов, замена некоторых устройств. Степень гибкости при переналадке может быть довольно высокой. К этой группе относится большинство "гибких" автоматических линий, созданных на базе агрегатных станков со сменяемыми головками, автоматизированные технологические комплексы.
   Четвертая группа основывается на гибкой технологии производства и оборудования, приспособленном для высокого уровня автоматизации. В этом случае для чередования выпуска группы деталей, изделия или перехода на выпуск нового изделия переналадка не требуется, так как оборудование автоматически переналаживается с обработки одного вида изделий на обработку другого по командам системы управления.
Основные исследования:
   В настоящее время в зависимости от уровня организационной структуры производства и ступеней автоматизации принята следующая терминология (ГОСТ 26228-84).
   Гибкий производственный модуль(ГПМ)- это ГПС, состоящая из единицы технологического оборудования, оснащенная автоматизированным устройством программного управления и средствами автоматизации ТП, автономно функционирующая, осуществляющая многократные циклы и имеющая возможность встраивания в систему более высокого уровня.
   В общем случае средство автоматизации ГПМ могут включать в себя накопители, спутники, устройства загрузки и выгрузки, замены технологической оснастки, удаления отходов, а также автоматизированного контроля, устройства переналадки и т. д
   Гибкая автоматизированная линия (ГАЛ), Гибкий автоматизированный участок (ГАУ) - это ГПС, состоящая из нескольких ГПМ, объединенных автоматизированной системой управления. В ГАЛ технологическое оборудование расположено в принятой последовательности технологических операций, а ГАУ функционирует по технологическому маршруту, в котором предусмотрена возможность изменения последовательности использования технологического оборудования.
   Гибкий автоматизированный цех (ГАЦ) -это гибкая производственная система, которая представляет собой совокупность ГАЛ и (или) ГАУ, предназначенную для изготовления изделий заданной номенклатуры.
   Гибкий автоматизированный завод (ГАЗ) - это ГПС, которая представляет собой совокупность ГАЦ, предназначенную для изготовления изделий заданной номенклатуры. ГАЦ может содержать также отдельно функционирующие неавтоматизированные участки, а ГАЗ - такие участки и цехи.
   По ступеням автоматизации ГПС подразделяются на гибкие производственные комплексы (ГПК) и гибкие автоматизированные производства (ГАП).
   Гибкий производственный комплекс определяется как ГПС, состоящая из нескольких гибких производственных модулей, объединенных автоматизированной системой управления и автоматизированной транспортно-складской системой (АТСС), автономно функционирующая в течение заданного интервала времени и имеющая возможность встраивания в систему более высокой ступени автоматизации.
   Гибкое автоматизированное производство представляет собой ГПС, состоящую из одного или нескольких ГПК, объединенных автоматизированной системой управления производством и транспортно-складской автоматизированной системой, и осуществляющую автоматизированный переход на изготовление новых изделий с помощью автоматизированной системы научных исследований (АСНИ), систем автоматизированного проектирования (САПР) и автоматизированной системы технологической подготовки производства (АСТПП).
   Совокупность взаимосвязанных автоматизированных систем, осуществляющих проектирование изделий, технологическую подготовку их производства, управление гибкой производственной системой и автоматическое перемещение предметов производства и технологической оснастки, образует систему обеспечения функционирования технологического оборудования ТПС. В систему обеспечения функционирования технологического оборудования ГПС входят: АСНИ, САПР, АСТПП; автоматизированная система управления предприятием (АСУП), АТСС, автоматизированная система инструментального обеспечения (АСИО), система автоматизированного контроля, (САК), автоматизированная система удаления отходов (АСУО) и т.д.
   Особую роль в ГПС играет АТСС - система взаимосвязанных автоматизированных транспортных и складских устройств для укладки, хранения, временного накопления, разгрузки и доставки предметов труда, технологической оснастки и удаления отходов.
   В общем случае ГАП (рис.1) включает следующие функциональные компоненты: технологическую подсистему - ТП, подсистему управления, подсистему автоматизированной технологической подготовки производства, подсистему сервиса, состоящие, в свою очередь, из модулей.
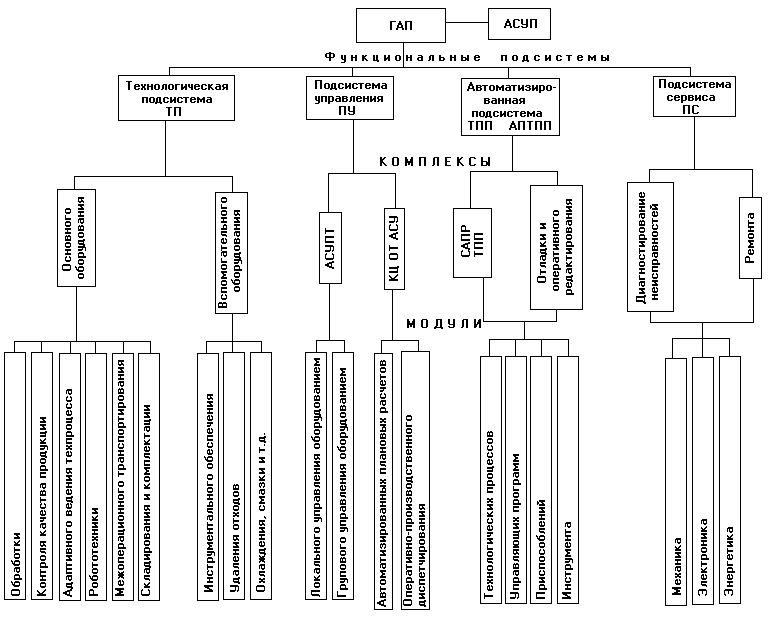
Рисунок 1- Функциональные компоненты ГАП
   Технологическая подсистема ГАП - это совокупность основного и вспомогательного технологического оборудования и реализованного на нем технологического процесса производства, включая контроль и перемещения.
   Основной структурной единицей ГАП является гибкий производственный модуль (для механообработки часто употребляется термин "обрабатывающая технологическая ячейка").
   Важнейшие характеристики ГАП - производительность, гибкость, живучесть определяются, во-первых, характеристиками основного (станки) и вспомогательного (промышленные роботы, накопители, системы автоматизированного контроля и измерений и др.) оборудования, составляющего ГПМ и, во-вторых, удачностью компоновки оборудования в ГПМ.
   Кроме того, ГПМ должен реализовывать процесс переналадки оборудования по безлюдной схеме, т.е. переналадка должна осуществляться программным способом путем смены управляющих программ для локальных систем управления (ЛСУ) оборудованием.
   Подсистема управления ГАП - это совокупность иерархически организованных и взаимодействующих между собой комплексов короткоцикловой организационно-технологической автоматизированной системы управления (КЦ ОТ АСУ) и автоматизированной системы управления технологическими процессами (АСУТП), реализующих функции планирования, контроля, оперативного диспетчирования, группового и локального управления оборудованием.
   Подсистема технологической подготовки производства ГАП - это автономная часть общей системы ТПП предприятия, включающая комплекс систем автоматизированного проектирования и отладки технологических процессов и управляющих программ, приспособлений и инструмента и средства оперативного их редактирования (корректировки).
   Подсистема сервиса ГАП - это комплексная система обеспечения высоких надежностных характеристик ГАП, выполняющая функции поддержания работоспособности всего оборудования и его систем управления, а также быстрого восстановления работоспособности при возможных отказах и сбоях.
   Функции ГАП:
- Производственная функция - это реализация технологической подсистемой в автоматизированном (автоматическом) режиме технологического процесса по выпуску определенной продукции. В составе производственной функции решаются следующие задачи (на примере машиностроения и др.):
-комплектация, складирование, манипулирование и транспортирование, буферное накопление заготовок, приспособлений и инструментов;
-обработка;
-контроль продукции;
-контроль параметров технологического процесса и состояния инструмента;
-уборка отходов (стружки, облоя, литников и т.д.);
-подача вспомогательных материалов (СОЖ, смазки, формовочных материалов и т.п.);
-диагностирование состояния и обнаружение неисправностей оборудования;
-прочее (подготовка заготовок и инструмента, очистка, мойка, консервация, упаковка и т.п.).
- Информационная функция - это реализация подсистемой управления ГАП и АСТПП процессов сбора, обработки и выдачи информации о состоянии элементов ГАП и результатах производства руководству и потребителю, линейному и функциональному персоналу, смежным управляющим звеньям, подсистемам сервиса, внешнего обеспечения и другим в автоматизированном (автоматическом) режиме.
В составе информационной функции решаются такие задачи:
-подготовка данных для формирования сменно-суточных заданий (ССЗ) и календарного плана-графика выпуска продукции;
-сбор сведений об отклонениях от нормальных параметров производства;
-учет хода производства и коррекция календарного плана в случае -отклонения первого от запланированного;
-подготовка и передача информации в смежные управляющие системы;
-комплектация и оптимизация загрузки всех модулей, учет выработки и зарплаты, демонстрационное оповещение и т.д.;
регулирование (диспетчирование) в реальном масштабе времени работы как отдельных подсистем и модулей, так и в ГАП в целом.
Содержание работы:
- Аналитический обзор методов решения задач, связанных с оптимизацией состава технологического оборудования (ТО) ГПС.
(Методы: системного анализа; моделей объёмного баланса; моделей теории массового обслуживания; имитационное моделирование);
- Обоснование структурно-компоновочного варианта ГПС для обработки деталей типа плит по критерию минимальных затрат
    2.1.Разработка групповой технологии обработки деталей и проектирование комплексной детали;
     2.1.1.Разработка группового маршрутного технологического процесса обработки деталей;
   В этой части составляется матрица группового маршрутного технологического процесса для трех деталей типа "вал", для которых проектируется автоматизированная линия.
     2.1.2.Разработка операционного технологического процесса обработки детали-представителя;
   Из трёх имеющихся деталей, выбирается деталь-представитель, которая имеет наибольшее количество характерных для этих трёх деталей поверхностей. Для детали-представителя составляется операционный технологический процесс обработки.
    2.2.Анализ возможных вариантов ГПС по критерию минимальных затрат на обработку детали-представителя;
    2.3.Выбор оптимального структурно-компоновочного варианта ГПС, исходя из критерия минимальных затрат.
- Обоснование и выбор рациональной структуры транспортно-накопительной и загрузочной систем для предполагаемого варианта ГПС по обработке деталей типа плит.
- Разработка модели системы управления разработанной ГАЛ в Matlab. Разработка быстродействия системы управления.
Выводы:
   В заключении можно сказать, что данный метод оптимального проектирования, в котором в качестве целевой функции выступает фактор минимума приведенных затрат при обеспечении заданной производительности, в условиях рыночной экономики наиболее востребован.
   В результате пошагового отбора из нескольких сотен возможных структурно-компоновочных вариантов построения линии обработки валов выбирается оптимальный по всем параметрам вариант.
   Важную роль в повышении эффективности проектируемой ГАЛ играет правильный выбор типа транспортно-загрузочной системы (ТЗС) линии.
   Минимальная стоимость ТЗС положительно влияет на общую стоимость АЛ выбранного варианта, что сокращает значение приведённых затрат. Кроме того, правильный выбор типа ТЗС во много раз сокращает количество конкурирующих вариантов.
   Применение системы управления увеличивает стоимость АЛ, однако значительно увеличивает её производительность, улучшает условия технической эксплуатации АЛ, позволяет осуществлять автоматическую диагностику неисправностей. Это в свою очередь уменьшает количество брака, уменьшает количество остановов производства.
Литература:
- Автоматизация типовых технологических процессов и установок: уч.для ВУЗов / А.И.Корыгин и др. – М.: Машиностроение, 1988.
- Блехерман М.Х. Гибкие производственные системы: организационно-экономические аспекты.-М.Машиностроение.1988.
- Проектирование автоматизированных линий / А.И.Дащенко, А.П.Белоусов. - М.: Высшая школа, 1983.
- Технологические основы гибкого автоматизированного производства / Е.С.Пуховский. - К.: Вища школа.Головное издательство, 1989.
- Транспортно-накопительные системы для ГПС. -Ленинград: Машиностроение,1989..
|