Главная страница ДонНТУ
Страница магистров ДонНТУ
Поисковая система ДонНТУ
Главная страница
Английский язык
АВТОРЕФЕРАТ ВЫПУСКНОЙ РАБОТЫ МАГИСТРА
Дорожкиной Инны Николаевной
Тема магистерской работы:
"Структурное и параметрическое обеспечение сборки резьбовых соединений на машинах роторного типа"
Руководитель:Водолазская Н.В.
факультет: механический
1 ВВОДНАЯ ЧАСТЬ
Эффективность изготовления выпускаемых машин зависит от уровня подготовки сборочного производства. В настоящее время имеет место тенденции относительного увеличения трудозатрат на сборку. Это объясняется специфическими особенностями технологии сборочных процессов, трудоемкость которых в машиностроении составляет в среднем 20-50% от трудоемкости изготовления изделий, занимая второе место после механической обработки [1,2].
Совершенствование процессов автоматизации сборочных работ, способствующее повышению производительности труда, уменьшению трудоемкости производства и снижению себестоимости продукции – важнейшая задача.
Системный подход к совершенствованию процессов автоматизации сборочных работ обусловил необходимость обратить самое пристальное внимание на собираемость деталей, оптимизацию технологического процесса сборки и разработку надежного, работоспособного сборочного оборудования [3].
Актуальность темы. Технологический процесс автоматической сборки от технологического процесса ручной и механизированной сборки. При ручной сборке необходимые простейшие инструменты (гаечный ключ, отвертка и тп.), а при автоматической сборке тех же изделий нужен сложный комплекс автоматических устройств выполняющих все переходы сборки. В связи с этим особую актуальность приобретают вопросы создания оборудования, обеспечивающего кратчайшие сроки качественную сборку изделий. При решении этой задачи перспективным направлением является широкое внедрение промышленные производства технологических систем непрерывного действия, выполненных на базе роторных автоматов и автоматических роторных линий.
Еще в 50-х годах началась интенсивная разработка роторных машин и автоматических линий, заменивших в ряде производств существовавшее ранее оборудование и обеспечивших сокращение производственных площадей и рабочей силы в 4-5 раз, а продолжительность производственного цикла и объем незавершенного производства-в сотни раз.
Были созданы и обеспечили высокую эффективность роторные линии для изготовления пластмассовых деталей прессованием и литьем, деталей приводных цепей и их сборки, для химических источников тока, узлов полупроводниковых приборов, деталей подшипников качения и т. д.
Роторные машины при всей их эффективности представляют собой лишь начальную стадию развития машин, характеризуемых непрерывным движением предметов обработки, и что их развитой формой являются так называемые роторно-конвейерные машины, отличие которых от роторных состоит в отделении инструмента от исполнительных органов машин [4] .
Первые образцы роторно-конвейерных линий подтвердили, что им свойственны совершенно новые технико-экономические показатели.
Каждый сборочный процесс рассматривается как единство и взаимосвязь трех компонентов автоматизации, технологического процесса и средств, обеспечивающих выполнение поставленной задачи. В качестве средств были выбраны автоматические роторные системы. Одним из направлений их усовершенствования является использование двух принципов компактности и функционально ориентированной структуры и разрабатываемые на основе этих принципов компоновки роторных сборочных машин. Особенностью роторного оборудования является отсутствие этапа изготовления опытного образца для проверки компоновочных решений. Поэтому при создании автоматических сборочных систем роторного типа приобретает большое значение разработка алгоритмов и методики проектирования.
В качестве объекта автоматизации были выбраны резьбовые соединения как наиболее распространенный вид разъемных соединений, встречающееся во всех изделиях промышленности. Снижение трудоемкости сборки резьбовых соединений является еще одним аргументом в вопросе выбора по отношению к другим видам работ. Актуальность выбора объектом автоматизации резьбовых соединений подтверждает и тот факт, что в среди множества работ, посвященной автоматизации сборочных процессов, вопросы автоматизации сборки резьбовых соединений нашли недостаточное отражение по ряду причин: из-за разнообразия конструкций резьбовых соединений, сложности ориентации и базирования и тп. Существуют проблемы, требующие детальных разработок, а именно: отсутствует системный подход к анализу и синтезу процесса автоматизированной сборки резьбовых соединений, влияющие на процесс сборки, на конечный результат, а также создавать обобщенные модели и алгоритмы, описывающие весь процесс и отдельные его составляющие.
Актуальной научной задачей для сборки резьбовых соединений является проведение структурно функциональных исследований автоматических роторных систем и создание на основе их синтеза вариантов компактной структуры высоко эффективных технологических систем.
Цель магистровской работы: повышение эффективности и качества сборки резьбовых соединений на машинах роторного типа, на основе разработки структурного и параметрического обеспечения.
Объект исследования – процесс проектирования сборочного оборудования машин для сборки резьбовых изделий.
Предмет исследования – совокупность проектных процедур разработки компоновки машин для сборки резьбовых изделий.
Методы исследования. Для исследования процесса проектирования компоновок роторных машин для сборки резьбовых изделий использовались методы системного анализа, теории сложных систем, математической логики. В основу исследований переходов сборки резьбовых изделий при выборе компоновки роторной машины положены технологические методы дифференциации и концентрации операций. Методы принятия технических решений использованы для формирования рациональной последовательности автоматизированного синтеза принципиальной компоновки.
1. Впервые разработана классификация резьбовых изделий с позиции автоматизации сборочного процесса, позволяющая установить границы применяемости видов сборки.
2. Описание технологического процесса сборки резьбовых изделий, выполняемых на роторных машинах.
3. Для процесса автоматизированного проектирования роторно-сборочной системы впервые разработан комплекс математических моделей и алгоритмов реализации этих процедур, которые учитывают основные технологические конструкторские и экономические факторы, влияющие на производительность системы.
Практическое значение полученных результатов. Разработанные методы синтеза позволяют проектировать конкретные варианты автоматических роторных систем, обеспечивающих высокую производительность сборки резьбовых изделий, компактность сборочной системы в пространстве и функциональную ориентацию ее структуры. На основе разработанных исследований подготовлен комплекс методического, информационного и программного обеспечения процесса проектирования компоновок роторных машин для сборки резьбовых соединений.
Актуальность выбора объекта автоматизации резьбовых соединений подтверждает и тот факт, что среди множества работ, посвященных вопросам автоматизации сборочных процессов, а именно, ученных: Арпентьева Б. М., Зенкина А. С. [1,5], Гельфанда М. Л., Ципенюка Я. И. [6,7,8,9,], Жабина А. И., Мартынова А. П. [2,10], Захарова Н. В., Тимофеева Ю. В. [11], Кошкина Л. Н., Клусова И. А., Прейса В. В. [12,13,14,15,16], Корсакова В. С. [17,18], Косилова В. В. [19,20], Лебедовского М. С. [21,22,23,24], Михайлова А. Н., Тернюка Н. Э. [25,26,27], Новикова Н. П. [28] др.
Вопросы автоматизации сборки резьбовых соединений нашли недостаточное отражение последующим причинам: разнообразие конструкций резьбовых соединений и присоединяемых элементов; сложность ориентации и базирование резьбовых соединений; срыв первых витков резьбы при наживлении необходимость в стапорении; сложности транспортирования резьбового узла.
В основном внимание уделялась расчетам нагрузок на резьбовые соединения [5,29]. Аналитических зависимостей для расчетов крутящих моментов [30], и разнообразным конструкциям резьбозавертывающих устройств [7,8,9,31], которые можно использовать лишь при малой механизации сборочных операций. И хотя в работах Якимовича В. А., Головащенко В. Е., Кулинича В. Я.[32], и др. представлен обширный материал по вопросу автоматизированной сборки резьбовых соединений, существует целый ряд проблем, требующих детальных разработок.
2 ОСНОВНАЯ ЧАСТЬ
2.1 АНАЛИТИЧЕСКИЙ ОБЗОР СОВРЕМЕННОГО СОСТОЯНИЯ ВОПРОСА ИССЛЕДОВАНИЯ.
2.1.1 АНАЛИЗ ПРОЦЕССА АВТОМАТИЗАЦИИ СБОРКИ ИЗДЕЛИЯ «ВЕНТИЛЬ АВ – 013М» И ТРУДОЕМКОСТИ СБОРОЧНЫХ РАБОТ
Сборка изделий является завершающим этапом производственного процесса, с которым человек сталкивался еще в период создания первых орудий труда. Сборочные процессы, в процессе эволюции усложнялись и совершенствовались. Исследователи выделяют три этапа истории сборки представленные на рисунке 1:
Рисунок 1 – Эволюция сборки [18]
Эти этапы взаимосвязаны и неотделимы между собой. Сборка – это часть технологического процесса изготовления изделия, которым заканчиваются работы по соединению отдельных деталей в узлы и компоновки последних для придания изделию готового вида в соответствии с его функциональным назначением [18, 33, 34, 35].
Анализ наиболее интересных событий, связанных со сборочным производством [36, 37] показывают, что первые попытки автоматизации сборочных работ были предприняты в конце 18 века (1784 г.), дальнейшее развитие автоматизации произошло в начале 20 века (1903-1913 г.г.) и в 30-ые годы с появлением роторных сборочных машин. Однако теоретических основ их применения для большинства сборочных операций не существует и по настоящее время. Для разработки таких основ необходимо исследовать общие характеристики, трудоемкость сборочного процесса. В машиностроении трудоемкость сборочных работ составляет 20-70% [33, 35, 37] от трудоемкости изготовления изделий, занимая второе место после механической обработки. Трудозатраты на сборку в настоящее время увеличивается.
Такое положение объясняется проблемами экономического развития Украины, а также специфическими особенностями механизации и автоматизации сборочных процессов. Эффективным путем снижения трудоемкости сборочных работ для массового и крупносерийного производства является применение технологической оснастки на основе агрегатирования сборочного оборудования [37, 38]. Пользуясь этим принципом, из сравнительно ограниченного числа деталей удается создавать самые разнообразные сборочные приспособления.
Таким образом, тип производства оказывает решающее влияние на технологию и организацию сборочных работ, на разработку технологических процессов [33, 34, 35]. В зависимости затрат времени на сборочные работы от типа производства (в процентах от общей трудоемкости изготовления машин) представлены на рисунке 2 :
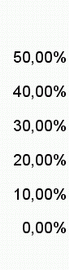
Рисунок 2 – Диаграмма распределения трудоемкости по типам производства [33]
Основная часть сборочных работ, в условиях единичного и мелкосерийного типов производств, выполняется на общей сборки, лишь малая доля осуществляется под отдельными сборочными единицами. С увеличением серийного производства сборочные работы все больше раздробляются по отдельным сборочным единицам, и в условиях массового и крупносерийного типов производств узловой сборки становиться равным или даже превосходит объем общей сборки, что способствует механизации и автоматизации сборочных работ.
Основная часть (50-85%) [2, 37] слесарно-сборочных работ представляет собой ручные работы, требующие больших затрат физического труда высокой квалификации рабочих.
Особенно это характерно для условий единичного и мелкосерийного производства, доля продукции которого в общем, объеме выпуска машиностроительных изделий наибольшая, а уровень механизации слесарно-сборочных работ весьма низок.
В условиях единичного и мелкосерийного производства специфика сборки машин характеризуется, трудностями механизации и автоматизации из-за частой смены номенклатуры изделий, а это требует применения широко универсальных технологических средств, при их применении на конкретных технологических операциях реализуется лишь небольшой процент их технологических и технических возможностей. В результате определенной непредсказуемости (в условиях рыночной экономики) номенклатуры деталей предприятие вынуждено иметь заведомо избыточный набор технологических средств, некоторая часть которых может оказаться невостребованной. Таким образом, необходимость изготовления деталей широкой номенклатуры вынуждает предприятие иметь большое разнообразие технологических средств [17]. К числу проблемам следует отнести также недостаточную специализацию, низкий уровень унификации и стандартизации, малую изученность процессов, что приводит к низкой собираемости сборочных единиц ѕ явлению, когда сборка сопровождается весьма значительным объемом пригоночно-доделочных работ, трудоемкость которых превышает трудоемкость собственно сборочных операций.
Сложившуюся сборочного процесса изделий единичного и мелкосерийного производства целесообразно представить на основе группирования по видам работ[2]:
1. слесарно-доделочные работы (зачистка заусенцев, опыливание, сверление отверстий, нарезание резьбы и пр.);
2. пригоночно-поводочные работы (пригонка поверхностей, непредусмотренная технологическим процессом сборки, а также «нормальные» пригоночно-доводочные операции, предусмотренная ТУ на сборку;
3. слесарно-вспомогательные работы (изготовление прокладок, пружин, шайб и других деталей);
4. балансировка деталей и сборочных единиц;
5. собственно-сборочные работы;
6. обкатка и испытание сборочных единиц и изделий;
7. разборка и демонтаж изделия;
8. консервация и упаковка.
По сохранению целостности при сборке соединения подразделяются на разъемные и неразъемные [33, 34, 35, 39]. Количество разъемных соединений в современных машинах и механизмах составляет 65-85% от всех соединений. Для общего машиностроения число соединений указанных видов можно выделить соотношением 0,45:0,35:0,15:<0,05(рисунке 3).
Рисунок 3 – Диаграмма распределения трудоемкости по типам производства [33]
По форме сопрягаемых поверхностей соединения подразделяются на:
цилиндрические;
плоские;
комбинированные;
конические;
сферические;
винтовые;
профильные.
Показано на рисунке 4 :
Рисунок 4 – Классификация соединений по форме сопрягаемых поверхностей [33, 39]
С точки зрения автоматизации можно рассматривать каждый сборочный процесс можно рассматривать как единство и взаимосвязь трех компонентов: объектов автоматизации, технологического процесса и средств, обеспечивающих выполнение поставленной задачи.
В качестве объекта автоматизации были выбраны резьбовые соединения, так как они являются наиболее распространенным видом разъемных соединений [2, 32, 40] и встречаются практически во всех изделиях машиностроения, судостроения, автомобилестроения, и иных областях промышленности. Это следует также и из выше перечисленных классификаций, из которых, видно, что разъемные неподвижные соединения, представителями которых являются резьбовые соединения, составляют 45% (рисунке1.3).
Еще одном аргументом в вопросе выбора может служить необходимость снижения трудоемкости сборки резьбовых соединений по отношению к другим видам соединений [41]. Соотношение видов соединений по трудоемкости представлена на рисунке1.5.
Рисунок 5 – Соотношение видов соединений по трудоемкости
По вопросу автоматизированной сборки резьбовых соединений существует целый ряд проблем, требующих детальных разработок, а именно: до настоящего времени отсутствует системный подход к анализу и синтезу процесса автоматизированной сборки резьбовых соединений. Который бы позволил увидеть разнообразные группы факторов, влияющие на процесс сборки, учитывать их изменения и взаимосвязь в различных ситуациях и влияние на конечный результат, а также создавать обобщенные модели, описывающие весь процесс и отдельные его составляющие.
Для решения этих вопросов необходимо, прежде всего, провести анализ способов сборки резьбовых соединений.
2.1.2 АНАЛИЗ РЕЗЬБОВЫХ СОЕДИНЕНИЙ, ВХОДЯЩИХ В СОСТАВ СБОРОЧНОЙ ЕДИНИЦЫ «ВЕНТИЛЬ АВ – 013М»
Основным элементом при сборке резьбового соединения является деталь “Корпус”, который является элементом вентиля АВ – 013М ручного (см.рис. 6) предназначенного для установки в пневмосети, работающие на воздухе, гелии, азоте, аргоне. Он предназначен для крепления на нём деталей вентиля и присоединения непосредственно к сети, и является основным элементом вентиля.
Рисунок 6 – Вентиль АВ – 013М
Вентиль ручной имеет следующие характеристики: давление рабочей среды 40 МПа, температурный диапазон работоспособности ± 50°, условный проходной диаметр 10мм, габаритные размеры 163х160х47 мм.
Схема соединения входящих в состав сборочной единицы показана на рисунке 7.
Рисунок 7 – Схема соединений входящих в состав сборочной единицы "Вентиль АВ – 013М"
В резьбовом соединении все детали разделяются на две группы: соединяемые и соединяющие. В сборочной единице одна из деталей бывает несущей: к ней прикрепляются остальные. Несущей деталью является корпус вентиля. Поэтому соединяемые детали разделяются на основные (базовые) и присоединительные (комплектующие) [32]. К базовым деталям относятся те детали, которые, обладая большой массой и размерами, остаются обычно неподвижными в процессе сборки и являются пассивными. Именно к ним присоединяют остальные детали. Базовые детали объединяют все остальные в одну сборочную единицу или изделие. К ним относятся: клапан, втулка, винт, корпус верхний.
Соединение резьбовых деталей производится с разных направлений и под разными углами. В частности, оно осуществляется вдоль горизонтали (справа, слева, спереди или сзади), а также под разными углами к вертикали и горизонтали[6,32,37, 38, 39].
Разные детали, образующие соединение, при автоматической сборке ведут себя неодинаково [18, 32, 39]. Об их способности к осуществлению этого процесса можно судить по таким признакам:
возможность ориентирования присоединяемой детали;
возможность подачи, фиксации и базирования той же детали;
условия взаимодействия присоединяемой детали с исполнительным механизмом автомата.
Комплектующие детали-характеризуется тем, что их ввинчивают в базовые детали или навинчивают на них. Как правило, роль комплектующих деталей при сборке активная, так как именно они совершают необходимые движения – вращение и поступательное перемещение. К ним относится:
штифт;
крышка;
кольцо;
кольцо уплотнительное;
пластина;
стакан;
винт установочый;
вороток;
шайба;
гайка.
Для сборки резьбовых соединений применяются различные виды устройств, которые включают в себя следующие группы:
1) загрузочные – служат для накопления и перемещения в пространстве собираемых объектов (лотки, бункеры и др.);
2) установочные – служат для правильной взаимной установки базовых и присоединительных объектов с требуемой точностью и фиксации в требуемом положении;
3) ориентирующие – предназначены для придания объектам сборки требуемого положения в пространстве;
4) рабочие – служат для выполнения конкретных соединений (наживления, завертывания, предварительной и окончательной затяжки и стопорения);
5) контрольные – служат для проверки момента затяжки и др. требуемым показателям качества (испытательные стенды, устройства для контроля и др.);
6) комбинированные – соединяют в себе два и более из рассмотренных выше типов приспособлений (вибробункер с встроенным ориентирующим устройством и т. п.).
Основными инструментами для механизированной и автоматизированной сборки резьбовых соединений являются разнообразные типы гайковертов, патронов резьбозавертывающих головок, полуавтоматов и автоматов, конструкции которых выбирают в зависимости от способа сборки, основные разновидности которых можно представить следующей схемой (рис. 8).
Рисунок 8 – Схема основных разновидностей способов сборки резьбовых соединений
Из достаточно большого количества представленных способов сборки выделим только такие, которые обладают преимуществами, делающих их особенно рациональными и эффективными для массового производства, а именно, способы сборки с помощью автоматизированных и автоматических систем.
2.2 ОБЩАЯ ЧАСТЬ
2.2.1 АНАЛИЗ ТЕХНОЛОГИЧНОСТИ
Деталь корпус, относится к классу призматических деталей. Изготавливается из стали 12Х18Н10Т ГОСТ4543-71, которая имеет следующий химический состав: С=0.12%, Cr=18%, Ni=10%, T»1%, S=0.02%, P=0.035%. Данная сталь относится к конструкционным жаропрочным сталям и имеет такие физико-механические свойства: sв=530МПа, sт =236МПа, удовлетворительно обрабатывается резанием.
На чертеже детали имеются все виды, сечения и разрезы, необходимые для представления конструкции детали. Размеры проставлены с отклонениями, параметры шероховатости соответствуют точности поверхностей. Допуски формы и расположения поверхностей достаточно обоснованы и не вызывают трудностей при их достижении (увязанные поверхности обрабатываются на одном установе). В конструкции данной детали не имеются лишних элементов.
Конструкция детали позволяет вести обработку, как на универсальном оборудовании, так и на специализированном. Обработка детали возможна с применением универсального и специального режущего и мерительного инструмента доступ, которого к обрабатываемым поверхностям свободен. На детали все элементы технологичны, кроме отверстия, т. к. отверстия находится на цилиндрической поверхности. Самыми точными поверхностями являются отверстия Ф13h8 и Ф22h8. Их получаем сверлением, зенкерованием и развёртыванием. Поверхности резьбовые М36х2-6g и М22х1,5-6g получаем двукратным точением, а резьбу нарезаем резцом. Квадрат 38h12х38h12 получаем фрезерованием на горизонтально-фрезерном станке с использованием специальной фрезы.
Деталь жесткая и это не ограничивает выбор режимов резания. Нет смысла заменять её сборной.
Все поверхности детали доступны и не вызывают трудностей в обработке.
Требования по радиальному биению 0,05мм можно обеспечить при обработке заготовки в трёхкулачковом патроне.
Несмотря на указанные недостатки, деталь является технологичной.
2.2.2 ОПРЕДЕЛЕНИЕ ТИПА ПРОИЗВОДСТВА
По заданной годовой программе выпуска деталей Nг=100000 шт./год и заводским данным по трудоёмкости изготовления детали определяем:
Тип производства [42]:
Такт выпуска деталей:
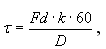
где: Fd – действительный годовой фонд времени при двухсменной работе,
Fd =3890 ч.
D – годовая программа выпуска деталей D=100000
t=1,9 мин.
к=0,8 – поправочный коэффициент.
Коэффициент серийности [42]:

где: tшс=3,25 мин – среднее штучное время изготовления детали по данным заводского технологического процесса.
Кс=0,57 , что соответствует массовому типу производства.
2.2.3 ВЫБОР МЕТОДА ПОЛУЧЕНИЯ ЗАГОТОВКИ
При выборе заготовки для заданной детали назначаем метод её получения, определяем конфигурацию, размеры, допуски и припуски на обработку и составляем технические требования, предъявляемые к заготовке.
Для получения заготовки возможны следующие методы: литьё, ковка, штамповка, резка проката.
Ковка не применяется, т.к. это экономически не выгодно, заготовка не будет соответствовать необходимой конфигурации.
Литьё не используем, т.к. сталь 12Х18Н10Т высоколегированная сталь, которая имеет плохие литейные свойства.
Использование проката ограничивается из-за формы детали и низкого коэффициента использования металла,
где: Mz – масса заготовки,
Md – масса детали,
Ким=0.18,
что недопустимо в условиях массового производства.
Применение штамповки в закрытых штампах нецелесообразно, т.к. заготовка имеет сложную конфигурацию. Из ковки и штамповки принимаем штамповку в открытых штампах, т.к. этот метод обеспечивает получение более точной заготовки, снижение значений припусков и повышение коэффициента использования металла.
В качестве экономического обоснования приведем пример расчёта стоимости штампованной и литой заготовки.
Стоимость литой заготовки:
где: Ci – базовая стоимость 1 т отливок, Ci=9800 грн [43] (c учётом коэффициента инфляции );
Q – масса заготовки, Q = 0,66 кг;
Kt –коэффициент точности, для отливок 2го класса точности Kt = 1.05 [43];
Kc – коэффициент сложности, для заготовок 2й группы сложности Kc = 0,9 [43];
Kb – коэффициент массы заготовки, для заготовки из легированной стали массой до 20 кг Kb = 0,4 [43];
Km – коэффициент материала, для легированной стали Km = 1,93 [43];
Kn – коэффициент серийности, для 1й группы серийности Kn = 0,5[43].
q – масса готовой детали;
S1 – цена 1 т отходов, S1 = 750 грн.
S = 114 грн.
Стоимость штампованной заготовки:
где:
Q = 0,66 кг,
Kt – коэффициент точности, для нормальной точности Kt = 1 [43];
Kc – коэффициент сложности, для 3й степени сложности Kc = 1, [43];
Kb – коэффициент массы заготовки, для заготовки из легированной стали массой до 20 кг; Kb = 0,75 [43];
Km – коэффициент материала, для легированной стали Km = 1,79 [43];
K = 1 [43].
Sшт = 407 грн.
Из расчётов видно, что стоимость штампованной заготовки выше стоимости отливки, однако, материал детали – высоколегированная сталь, которая имеет плохие литейные свойства. Литьё нельзя применить из-за больших технологических трудностей, возникающих при его выполнении в условиях данного предприятия.
Из всех проанализированных способов получения заготовки выбираем штамповку в открытых штампах т.к. форма заготовки максимально приближена к готовой детали, что позволяет значительно сократить припуски на механическую обработку, а также с учётом партии выпуска данных деталей это наиболее производительный метод.
Расчёт размеров заготовки:
1 Расчетная масса штамповки [43]:
mp = mд*к,
где: mд – масса детали,
к – расчётный коэффициент, к=1.5,
mp = 0,44*1,5=0,66 кг.
2 Группа стали: сталь12Х18Н10Т относится к группе М1[43].
3 Масса фигуры:
mф=((еП*(1,05*Д)2/4)*1,05*L+1.053*а2*в)*7800,
где: Д – диаметр детали,
L – длина детали,
а – ширина квадрата,
в – длина квадрата,
mф=(((3,14*(1,05*0,022)2/4)*1,05*0,016)+((3,14*(1,05*0,022)2/4)*1,05* 0,016))+((3,14*(1,05*0,036)2/4)*1,05* 0,027)+(1,053*0,0382*0,032))*7800=0,775 кг.
4 Степень сложности:
С=mp /mф ,
где:
С – расчётный коэффициент,
mф – масса фигуры, в которую вписывается деталь, mф = 0,775 кг,
С= 0,66/0,775= 0,85
Исходя из коэффициента определяем степень сложности С1[43].
5 Класс точности: принимаем Т4 [43].
6 Определяем исходный индекс: 9 [43].
На фаски, канавки, отверстия, пазы назначаем кузнечные напуски. Полученные данные заносим в таблицу 1.1:
Таблица 1.1 – Определение размеров поковки
Для упрощения формы штамповки принимаем Ф 38,8+0,8-0,4 за квадрат 40.2+0,8-0,4 .
3 ЗАКЛЮЧИТЕЛЬНАЯ ЧАСТЬ
В результате проведенных исследований выполнено следующее:
1. Решена важная народно-хозяйственная задача, состоящая в повышении эффективности роторных машин для сборки резьбовых изделий путем компоновок на базе пространственно функционального подхода;
2. Проведен анализ резьбовых соединений, входящих в состав сборочной единицы – «Вентиль АВ – 013М»;
3. Произведен анализ технологичности;
4. Выбран метод получения заготовки.
Для достижения поставленной цели, необходимо решить следующие задачи:
разработать классификацию резьбовых деталей с позиции степени автоматизации сборочного процесса;
разработать модель сборки резьбового изделия в автоматическом цикле;
разработать структурную модель систем роторного типа для сборки резьбовых изделий – «Вентиль АВ – 013М»;
разработать компоновочную модель систем роторного типа для сборки резьбовых изделий – «Вентиль АВ – 013М».
Решению этих основных задач и посвящена данная работа.
ПЕРЕЧЕНЬ ССЫЛОК
1. Арпентьев Б. И., Земкин А. С., Куцын А. Н. Механизация и автоматизация сборочных работ на машиностроительных предприятиях. – К.: Техника, 1994. – 232 с.
2. Жабин А.П., Мартынов А.П. Сборка изделий в единичном и мелкосерийном производстве. – М.: Машиностроение, 1983. – 184 с.
3. Храбров А.С. Совершенствование процессов автоматизации сборочных работ.- Л.: Машиностроение. Ленинград. отд.-ние. 1979. – 230 с., ил.
4. Кошкин Л.Н. Роторно-конвейерные линии. – 2-е изд. стереотип. – М.: Машиностроение, 1986. – 320 с., ил.
5. Зенкин А. С., Арпентьев Б. М. Сборка неподвижных соединений термическими методами. – М.: Машиностроение, 1987. – 128 с.
6. Гельфанд М. Л., Ципенюк Я. И., Кузнецов О. К. Сборка резьбовых соединений. – М.: Машиностроение, 1978. – 109 с.
7. Гельфанд М. Л. Ручные резьбозавертывающие машины (обзор панентов). – М.: НИИ информации, 1965. – 47 с.
8. Гельфанд М. Л. Исследование резьбозавертывающих машин ударного действия. Диссертация на соискание ученой степени кандидата технических наук. М. 1968. – 139 с.
9. Ципенюк Я. И. Расчет торсионов к гайковертам ударного действия. «Строительные и дорожные машины», 1971, №2, с. 16-17.
10. Мартынов А. П. Исследование и стандартизация методов повышения качества и снижения трудоемкости сборки крупного прокатного оборудования. Диссертация на соискание ученой степени кандидата технических наук. М. 1972. – 135 с.
11. Захаров М. В., Тимофеев Ю. В. Розробка технологічних процесів складання: Навч. посібник. К.: НКМ ВО, 1992. – 152 с.
12. Кошкин Л. Н. Комплексная автоматизация на базе роторных линий. Изд-во 2-е, перераб. и доп. – М.: Машиностроение, 1972. – 351 с.
13. Кошкин Л. Н. Роторные и роторно-конвейерные линии. – М.: Машиностроение, 1982. – 236 с.
14. Клусов И. А. Технологические системы роторных машин. – М.: Машиностроение, 1976 – 231 с.
15. Прейс В. В., Комаров Г. В., Клусов И. А., Маткин Ю. Л., Варьяш Г. М. Автоматическая загрузка роторных и роторно-конвейерных линий. – М.: ВНИИТЭМР., 1990. – 56 с.
16. Прейс В. В. Технологические роторные машины: вчера, сегодня, завтра. – М.: Машиностроение, 1976. – 128 с
17. Корсаков В.С. Основные направления автоматизации сборочных процессов в машиностроении // Автоматизация сборочных процессов в машиностроении. – М.: Наука, 1979. – 9-11с.
18. Сборка и монтаж изделий машиностроения: Справочник: В 2 т. /Ред. совет: В.С. Корсаков (пред.) и др. – М.: Машиностроение, 1983. – Т.1. Сборка изделий машиностроения /Под ред. В.С. Корсакова, В.К. Замятина. 1983. – 480 с.
19. Косилов В. В. Состояние и основные направления технологии сборки в машиностроении //Комплексная механизация и организация сборочного производства на предприятиях тракторного и сельскохозяйственного машиностроения: Тез. докл. Всесоюз. науч.-техн. Совещ. – Павлодар, 1980 – с. 216-218.
20. Косилов В. В. Технологические основы проектирования автоматического сборочного оборудования. М.: Машиностроение,1976. – 248 с.
21. Лебедовский М. С., Вейц В. Л., Федотов А. И. Научные основы автоматизированной сборки. – Л.: Машиностроение, 1985. – 316 с.
22. Лебедовский М. С. Автоматизация сборки изделий. – Л.: СПЗИ, 1980. – 81 с.
23. Лебедовский М. С., Федотов А. И. Автоматизация сборочных работ. – Л.: Лениздат, 1970. – 448 с.
24. Автоматизация сборочных процессов / Лебедовский М. С., Лобзов Б. А., Муценек К. А. и др. Отв. ред. Муценек К. А. Рига: Рижский политехнический институт, 1981. – 81 с.
25. Михайлов А. Н. Разработка методов проектирования высокоэффективных поточно-пространственных технологических систем: Дис. … д-ра техн. наук. – Харьков, 1991. – 498 с.
26. Михайлов А. Н., Тернюк Н. Э. К расчету параметров маршрутизации изделий в поточно-пространственных технологических систем // Известия вузов. Машиностроение, 1990, №11. – С. 63-67.
27. Михайлов А. Н. Основы синтеза поточно-пространственных технологических систем непрерывного действия. – Донецк: ДонНТУ,2002. – 379 с.
28. Новиков М. П. Основы технологии сборки машин и механизмов. 5-е изд. М.: Машиностроение, 1980. – 592 с.
29. Крепежные детали: Справочник/ Под ред. Поливанова П. М. – М.: Машиностроение, 1967. – 247 с.
30. Мухамбетов Г. М. Исследование затяжки ответственных резьбовых соединений и пути обеспечения ее точности в условиях автоматизированной сборки. Диссертация на соискание ученой степени кандидата технических наук. Москва, 1980. – 213 с.
31. Бобриков В. Г. Ударные механизмы, применяемые в пневматических резьбозавертывающих машинах. – М.: ЦНИИТ Эстроймаш, 1971. – 38 с.
32. Яхимович В.А., Головащенко В.Е., Кулинич В.Я. Автоматизация сборки резьбовых соединений. – Львов: Вища школа. Львов. Отд-ние, 1982. – 160 с.
33. Егоров М.Е. и др. Технология машиностроения. Учебник для вузов. – 2-е изд., доп. – М.: Высш. Школа, 1976. – 534 с.
34. Маталин А.А. Технология машиностроения: Учебник для машиностроительных вузов по специальности «Технология машиностроения, металлорежущие станки и инструменты». – Л.: Машиностроение. Ленингр. отд-ние, 1985. – 496 с.
35. Лавриненко М.З. Технология машиностроения и технологические основы автоматизации. – Киев: Вища школа, 1982. – 320 с.
36. Бабушкин М.Н., Кристаль М.Г. Перспективы повышения производительности автоматических сборочных систем. //сборка в машиностроении и приборостроении/Под ред. О.А. Горленко. – Брянск: БГТУ, 2001. – 39 с.
37. Рабинович А.Н. Автоматизация механосборочного производства. – К.: Вища школа, 1969 – 542 с.
38. Белоусов А.П. Дащенко А.И. Основы автоматизации производства в машиностроении: Учебник. – М.: Высш. Школа, 1982. – 351 с.
39. Технология машиностроения: В 2 т. – Т. 1. Основы технологии машиностроения: Учебник для вузов/ В.М. Бурцев, А.С. Васильев, А.М. Дальский и др.; Под ред. А.М. Дальского. – М.: Изд-во МГТУ им. Н.Э. Баумана, 1999. – 564 с.
40. Механизация и автоматизация сборки изделий машиностроения для агро-промышленного комплекса – «Сборка-83»: Тез. докл..– М., 1983. – 148 с.
41. Водолазская Н.В., Михайлов А. Н. Моделирование качества автоматизироаного процесса сборки резьбовых соединений // Сборка в машиностроении и приборостроении: Тез. докл. Междунар. науч.-техн. сем., 2-3 окт.2001 г.. – г. Брянск: БГТУ. – 55-58 с.
42. Методические указания к выполнению курсового проекта по курсу “Технология машиностроения” /Сост.: Н.Г.Бойко, В.А.Богуславський, В.В.Польченко и др., – Донецк ДГТУ , 1995г – 52 с.
43. Справочник технолога машиностроителя. В 2-х т. Т. 1/ Под ред. А.Г.Косиловой и Р.К.Мещерякова. – 4-е изд., перераб. и доп. – М.: Машиностроение, 1985. – 656 с.
Английский язык
Вверх
Главная страница
Главная страница ДонНТУ
Страница магистров ДонНТУ
Поисковая система ДонНТУ