Ãëàâíàÿ ñòðàíèöà ÄîíÍÒÓ
Ñàéò ìàãèñòðîâ ÄîíÍÒÓ
Ïîèñêîâàÿ ñèñòåìà ÄîíÍÒÓ
Ãëàâíàÿ ñòðàíèöà
Àâòîðåôåðàò ìàãèñòåðñêîé ðàáîòû
Ýëåêòðîííàÿ áèáëèîòåêà
Àííîòèðîâàííûå ññûëêè
Ðåçóëüòàòû ïîèñêà
ÈÍÄÈÂÈÄÓÀËÜÍÎÅ ÇÀÄÀÍÈÅïî òåìå ìàãèñòåðñêîé ðàáîòû:
"Îïðåäåëåíèå òåõíè÷åñêîãî ñîñòîÿíèÿ øåñòåðåííûõ êëåòåé ïðîêàòíûõ öåõîâ ïî âðåìåíûì ðåàëèçàöèÿì âèáðàöèîííîãî ñèãíàëà"
Êóðèøåâîé Å. Ï.
Ðóêîâîäèòåëü: äîöåíò Ñèäîðîâ Â. À.
Analysis of vibration signal time realization
Sidorov V., Kuvatov A., Kurisheva E.
(DonNTU, close corporation "MMW "Istil (Ukraine)", Donetsk, Ukraine)
The methods of vibration signal time realization analysis for estimation of the technical state of mechanical equipment are offered.
1. The problem and its connection with scientific and practical tasks. The main way to receipt information about the technical state of mechanical systems is vibration measuring. Determination of the most effective methods of vibration signal time realization analysis let to estimate the technical state of mechanisms which are working in brief mode.
2. Analysis of researches and publications. In works [1 — 4] were explored the most complete measuring of vibration total level, measuring of vibration signal parameters, spectral analysis of vibration signal. Transitional processes which are the feature of metallurgical equipment require the analysis of time signal for the control of rapid passing processes. Existent technical decisions do not allow effectively using diagnostic information about time realization.
3. Statement of the problem. It is necessary to develop the methods of analysis of vibration parameters time signal, which will allow to get and use the most effectively information about the technical state of mechanical equipment which are working in brief mode.
4. Exposition of material and result. The most informing method of getting information about the technical state of mechanical equipment is analysis of vibration signal parameters now. Different methods is used for solving practical and research tasks of different level: analysis of mechanisms noises, measuring of vibration total level, measuring of vibration parameters, analysis of vibration signal spectrum and analysis of time realization.
Development of vibrometery methods began from analysis of polyharmonical signals forms [5]. Realization of practical tasks of equipment technical state recognition demanded measuring of mean-square vibration parameters, that was confirmed by the conformable level of device providing development. Distinction of disrepairs on first stage of development answers possibilities of vibration spectral analysis, solved in use of computer technologies. Expansion of diagnosing objects, the necessity of mechanisms working in the brief mode actual state recognition requires to develop methodology of vibration signal time realization analysis on new modern level of practical tasks solving requirements.
Measuring of vibration total level allows to determine the category equipment technical state, using the methods of mutual, relative or absolute comparison. Measuring of vibration signal parameters is used for estimation of the equipment bearing elements technical state. The spectral analysis of vibration signal provides exposure, identification of damages and possibility of their progress trends analysis since the earliest stage. Analysis of time realization is used rarely which allow to discuss about stability of flowing processes in a mechanism.
Solving the tasks of damages recognition using device of spectral analysis of long-term mechanisms vibration parameters is examined in many works [1 — 4]. Practical realization of recommended approaches with high exactness allows to diagnose mechanisms of rotor type. In the same time there are a lot of machines working in brief and repeatedly brief mode of loading. Metallurgical machines of considerable sizes, large power of drive, considerable, often unstable dynamic loadings, and also lifting machines of mountain enterprises, having similar characteristic are delivered to this class of equipment. In this case determination of technical state has difficulty because of unforeseeable influence of workloads. Above all things there are drive mechanisms of billet mills and bloomers working rollers, scissors of hot cutting, mechanisms of metallurgical faucets, skip winches, lifting gears.
Briefness of mechanism work in the mode of stationary loading, the changes of loading elements during the cycle of work result in the ambiguous reading of spectral analysis information. This mode forces to work without averaging or with the least of averagings. Sure it influences on repetition of the got results. At comparison of vibration signals spectrums (fig. 1, 2, 3, 4) we mark considerable distinctions in the got spectrums and coincidence of peak values on frequency of 2,03 Hz in the same time have different amplitude values (accordingly: 0,89 mm/s, 1,39 mm/s, 0,95 mm/s, 0,85 mm/s). Also is possible to see on spectrograms increase of vibroactivity in the bar 20…50 Hz, which have different mean-square value in this bar. The ambiguousness of analysis results does not allow to estimate aggregate technical state.
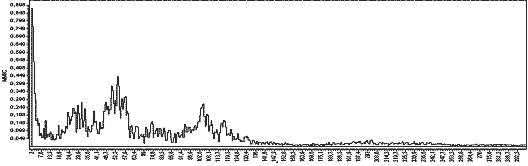
Figure 1 — Spectrum of vibrosignal, taken from the frame of pinion stand 900 during a rolling. Number of averagings — 4 (mean-square value V in the bar 2…400 Hz — 2.7 mm/s)
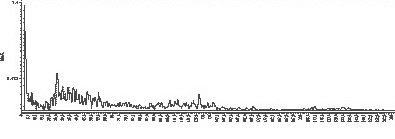
Figure 2 — Spectrum of vibrosignal, taken from the frame of pinion stand 900 during a rolling. Number of averagings — 4 (mean-square value V in the bar 2…400 Hz — 2.8 mm/s)
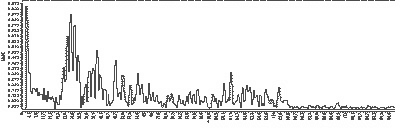
Figure 3 — Spectrum of vibrosignal, taken from the frame of pinion stand 900 during a rolling without averaging (mean-square value V in to the bar 2…400 Hz — 3.6 mm/s)
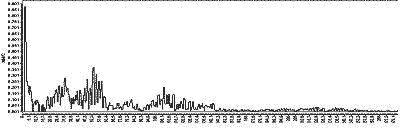
Figure 4 — Spectrum of vibrosignal, taken from the frame of pinion stand 900 during a rolling without averaging (mean-square value V in to the bar 2…400 Hz — 2.1 mm/s)
The use of diagnosing test mode (determination of mechanism technical state in the mode of idling) does not allow to judge about character of mechanism workloads perception. Increase of current characteristics of electric motors of machines in 2…3 times during a working process is usually marked. Mechanical loadings considerably increase too. Consequently, absence of machine technical state control during work can result in substantial errors at determination of actual state and ability of mechanism to execute the set functions.
At diagnosing of mechanical systems the high informing of transitional processes is the known fact (acceleration, braking, change of loading). Exactly in this period there is closing of gaps which are the first symptom of damages. Complication of decision in this way is aggravated by the change of vibrations frequency because of increase or reduction of process speed, by instability of loadings (distinctions of rolled sheets, change of metal temperature) and subjectivity of management process. Analysis of vibration signal time realization is the optimum decision.
Preliminary we will consider nature of mechanical vibrations origin on example of one mass system (fig. 5). Parameters of this system are: mass — m, inflexibility — c, coefficient of air-cushionment — h. Vibrations of the system are possible at influence of force — F, which is variable to direction of vibrations. Force F can be permanent, however parameters of contacting surfaces can be the reason of its periodic change. For example, gravity at contiguity with threadbare surface of bearing at the rotation of shaft is a source of vibrations. Frequency characteristics in this case will specify the character of damages.
The parameters of swaying process are determined by the following equalization, in which k is frequency of own vibrations of the system, ε is parameter determining air-cushin properties of the system:
ε = h / 2m
Damages in mechanical system could be a reason of inflexibility changes (for example, wear-out of details, weakening of screw-thread connections), change of air-cushin coefficient (because of cracks appearance), change of influencing forces (at change of contacting surfaces roughness). Distinction of technical state at the stationary vibrations process is possible at change of one of the indicated parameters, or at entering additional verifications. For example, change of system inflexibility simultaneously causes change of system own vibrations frequency. Change of air-cushin parameters will cause change of vibrations fading time in the mechanical system
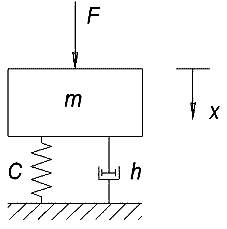
Figure 5 — The one mass system
In the same time fluctuations of mechanical system have casual character at every concrete cycle of vibrations, determined by lot of factors: value of influencing forces, contact of touching surfaces, realizing display of damages. Assumed the next dependence — large damages result in increase of swaying process parameters variation. It creates pre-conditions for recognition of mechanical system state according to analysis of vibration signal time realization.
Vibration signal time realization of mechanism working in brief mode can be described by two factors — current positive and negative values of amplitude of vibrations Ai, -Ai and proper periods of vibrations Ti (fig. 6).
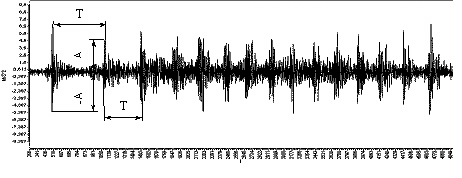
Figure 6 — Time realization of vibration signal
As a result we have two-dimensional diagnostic space, for which we can determine coordinates of explored selection (concrete aggregate of time signal realization ):
where Ak and Òk is the population mean of proper coordinates, n is amount of observations. Dispersion of k two-dimensional selection is characterized also by two values S2k(A) and S2k(Ò):
The discovery of uncasual declinations can be executed on method of averagings [1]. Distinction between selections k and l is estimated by the Student's criterion on one of chosen coordinates, for example:
Distinction in technical state of object confesses substantial (uncasual), if executed this condition: |t| >= tc(n, p), where tc(n, p) is the Student's coefficient for amount of liberty degrees n = nk + nl - 2 and confiding probability p.
Comparison of measurings results can be realized by estimation of uncasual declinations on control levels [1]. The histogram of dependence is used for this purpose: Ni = f(νi), where Ni is amount of observations in i single range; νi is range of registered values. The border of interval is determined by expression νñð + 2σ, where νñð — average value, σ — standard deviation, including more than 95% realization, can be possible value of condition parameter for explored mechanism. On fig. 7 is brought histogram; at building of histogram vibroacceleration was taken as measured parameter.
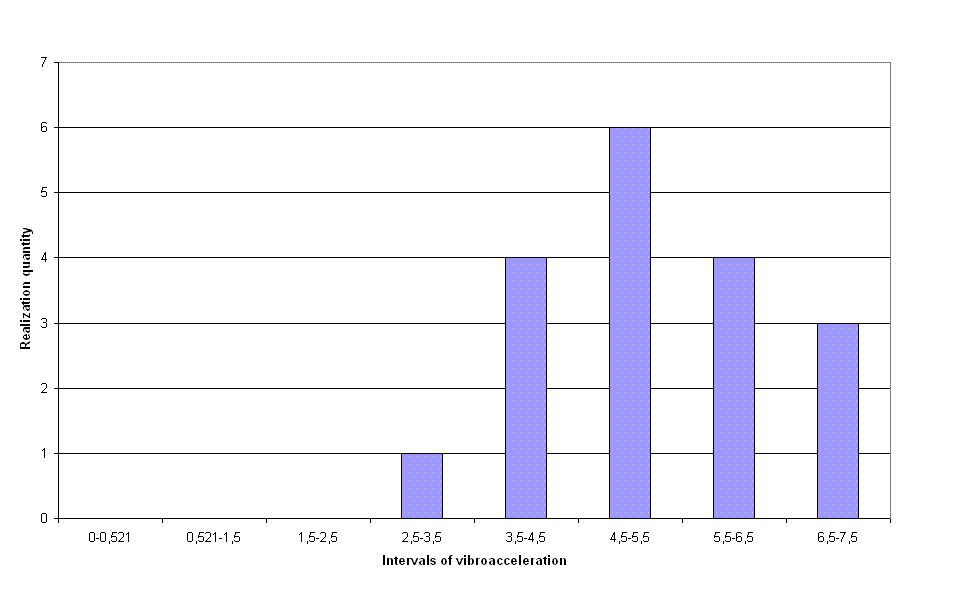
Figure 7 — Histogram
To determine scopes of technical states distinction was outspoken a hypothesis about accordance of technical state change to character of physical processes flowing in a mechanism — the change of contact character in bearing of sliding from liquid to semiliquid mode inevitably will cause the change of technical state. Probably, scope transitions must be related to distortions of distance diagnostic measure functions continuity Nν, Nν2 as step transitions. It could be explained by work of mechanism in area of unsteady equilibrium during vibration proper to scopes of technical states.
The change of the technical state will result the deviation of function Ni = f(νi) from normal distribution.
In general case in oscillating system simultaneously take place losses of energy, conditioned by different reasons [6]: by speed of deformations, inflexibility of system, dry friction, capacity for air-cushionment of vibrations. Estimating stability of air-cushion properties of mechanical system is possible at determination of decrement of vibrations δ as natural logarithm of two subsequent amplitudes relation:
δ = ln (Ai / Ai+1)
Possibility of this index measuring appears during vibration time signal realization (fig. 8).
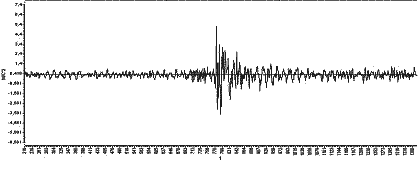
Figure 8 — Time realization of vibration signal, measured in industrial terms
5. Conclusions and direction of further researches. Was determined the possibility of technical state estimation through the vibration signal time realization analysis for machines working in brief mode. Considered the reasons of mechanical vibrations origin on example of one mass system. Considered methods of time signal analysis and recognition scopes in space of diagnostic symptom receiption.
List of sources:
1. Birger I.A. Technical diagnostics. — M.: Machine building, 1978 — 240p.
2. Vibro-acoustic siagnostics arising defects/F. Ya. Balitskiy, M. A. Ivanova, A.G. Sokolova, E.I. Homyakov. — M.: Science, 1984.
3. Kollakot R.A. Diagnosing of mechanical equipment: Translate from english. — L.: Shipbuilding, 1980 — 296p.
4. Kollakot R.A. Diagnostics of damages: Translate from english. — M.: Mir, 1989 — 512p.
5. Iorish Yu.I. Vibrometry. Measuring of vibration and shots. Basic theory, methods and devices. — M.: Mashgiz, 1963.
6. Generalised nonlinear model of energy dissipation account at fluctuations/Pisarenko G.S. — Kiev: Nauk.dumka. 1985 — 240 p.
Ãëàâíàÿ ñòðàíèöà
Àâòîðåôåðàò ìàãèñòåðñêîé ðàáîòû
Ýëåêòðîííàÿ áèáëèîòåêà
Àííîòèðîâàííûå ññûëêè
Ðåçóëüòàòû ïîèñêà