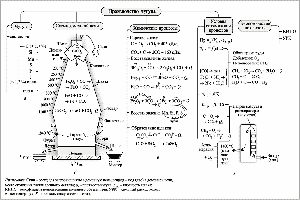
Now in the conditions of vast market of raw materials and decline of cost of cast-iron in the world market of black metals a task of multiplying profitability of production, and also achieving of greater flexibility of process, is actual for providing the stability of enterprise’s work of on the whole.
Perfection of management methods and introduction of the modern informatively-designing systems is one of major directions of improvement of technically-economic indexes of melting, quality of the smelted cast-iron and safety of work of high furnaces.
The ultimate goal of system’s complex control of high furnaces systems development is creation of the control system, providing normal work of production on the whole at a minimum unit cost taking into account limitations, conditioned the requirements of technology and possibilities of equipment. In area of blast-furnace process control it is necessary nowadays to approach maximally the management of blast-furnace operations to automated one on the basis of development of facilities of receipt of objective information about the parameters of technological process and present possibilities of the use of modern hardwares
Automated technological complex of high furnace as an object of control and management is characterized by the followings signs:
• the large volume of the controlled variables and signs of calculations;
• low transparency of process, for lack of direct checking of development of the separate stages of process of smelting of cast-iron feature;
• deep intercommunication of all processes of melting at narrow-mindedness of resources on a management;
• the presence of casual measuring hindrances of different nature and character, that reduces quality of information.
In the analysis of work of high furnace it is necessary to examine it as the guided technological system. The subsystems of measuring, evaluations, storages, treatments, presentations of information, and also intellectual control systems, must be used for its management. The distinctive feature of these systems concludes in that for making of managing influences in them must be drawn on complex of mathematical models of technological processes, different forms and methods of extraction, storage, treatment and representation of knowledge. The structure of the modern automated control the blast-furnace melting system is simplified it is possible to present a chart, resulted on a picture 1. The indexes (by an objective function, criteria) of technological efficiency of work of stove, technological personnel and informative system are the following: specific expense of coke, productivity of stove, output of standard cast-iron on maintenance grey in cast-iron, temperature of liquid products of melting in accordance with the requirements of subsequent steel-smelting production. Thus must be executed limit on technology of the blast-furnace melting, that is to say minimum probability of hit of the technological state of stove is well-to-do, in the so-called, critical areas (critical, emergencies office hours). Work of aggregates of complex is under the permanent supervision of removable technologists after which a leading role is at the decision of many tasks of management. In this connection it is necessary to attribute such technological complex to the class of interactive human-machine, automated informatively-managing applications.
The purpose of task is a receipt of necessary result, that is to say the qualities of cast-iron with minimization of prime price, and receipt of possibility of adjustment of results at the change of parameters of entries of task.
in beginning
A blast-furnace process is an aggregate of the mechanical, physical and physical and chemical phenomena, which run in a working high furnace. Charge materials, such as coke, iron containing components and gumboil which are loaded in a blast-furnace as a result of running of blast-furnace process turn into cast-iron, slag and blast-furnace gas.
In a chemical relation a blast-furnace process is restorative-oxidizing: iron is restored from oxides, and repairers oxidize. However blast-furnace process is used to call a restoration one, because its purpose consists in the renewal of oxides of iron to the metal.
The aggregate for realization of blast-furnace process is a mine type stove. Working space of high furnace in horizontal sections has a round form, and in a vertical cut it has an original outline, which is called a profile.
The major condition of realization of blast-furnace process in working space of stove is continuous meeting motion and co-operation of going down charge materials, loaded in stove through koloshnik, and ascending stream of gases, appearing in a furnace at burning of carbon of coke in heated to a 1000 - 1200 0Ñ air (blowing) which is forced in overhead part of furnace through furmy located on its circumference. To the blowing technical oxygen, natural gas, aquatic steam, can be added.
A coke enters furnace heated to 1400 - 1500 0Ñ. In the areas of burning the carbon of coke co-operates with oxygen of blowing. Appearing in the areas of burning dioxide of carbon at a high temperature and surplus of carbon is unsteady and grows into the oxide of carbon. Thus, outside the areas of burning a furnace gas consists only of oxide of carbon, nitrogen and two-bit of hydrogen, appearing at decomposition of aquatic steams or natural gas. Mixture of these gases, heated to 1800 - 2000 0Ñ, goes up and passes warmly to materials, which are gradually going down in a furnace as a result of burning down of coke, formations of cast-iron and slag and their periodic release from a high furnace. Thus gases cool down to 200 - 450 0Ñ, and the oxide of carbon, taking away oxygen from the oxides of iron, grows partly into dioxide of carbon, maintenance of which in blast-furnace gas on an exit from a stove achieves 14 - 20 %.
Charge materials load in a blast-furnace stove through a backfilling vehicle by separate portions – serves. They are disposed on koloshnik as the alternated layers of coke, ore or agglomerate and gumboil during work on a not fully gumboiled agglomerate. The load of serves is made through 5 - 8 min. as far as koloshnik becomes free as a result of lowering of materials.
In the process of heating of going down materials takes place deleting from them of moisture and volatile matters of coke and decomposition of carbonates. The oxides of iron under the action of gases of restorations gradually pass to the high degrees of oxidization to lower one, and then – in metallic iron on a chart: Fe2O3 → Fe3O4 → FeO→ Fe.
The newly recalled iron is noticeable filled with carbon as early as the hard state. As far as the iron is filled with carbon temperature of melting of him falls down. At a temperature a 1000 - 11000Ñ renewal of iron is almost closed and begin to be restored more hardly recalled elements as silicon, manganese and phosphorus. Iron filled with carbon, containing about 4 % carbon and the several of silicon, manganese and phosphorus, melts at the temperature of 1130 - 11500Ñ and flows down as drops of cast-iron in a furnace. In the lower half of mine begins the formation of liquid slag from component parts of empty sort of ore and gumboil. The unrecalled oxides of iron and manganese are instrumental in a drop in the temperature of melting of slag. In a flowing down downward slag under the action of increasing temperature all ore and gumboil gradually melt, as well as ash after the combustion of coke.
At co-operating of liquid products of melting with a burning hot coke there is the increased renewal of silicon in zaplechikakh and furnace, manganese and phosphorus from their oxides, dissolved in a slag. Here taken in a metal during melting sulphur passes to the slag. Iron and phosphorus of stove are fully restored and pass to cast-iron, and degree of renewal of silicon and manganese and linen of deleting from cast-iron of sulphur in a large measure depend on temperature terms, chemical composition of slag and its amount.
Liquid cast-iron and slag is divided in a furnace due to different specific the masses. As far as an accumulation them in a furnace cast-iron is produced through cast-iron letka, and slag - through letka (overhead slag) of slags and cast-iron letku during the issue of cast-iron (lower slag).
All transferred processes flow in a high furnace simultaneously, having mutual influence.
in beginning
Calculation of blast-furnace charge is made at planning of high furnaces, change of condition of melting, to replacement of one materials other, during the translation of stove on smelting of other type of cast-iron.
Calculation of charge is taken to determination of expense of separate materials for smelting of unit of cast-iron of the set composition, certain composition of slag, providing properties, necessary for smelting of this brand of cast-iron and even high-performance work of stove.
A calculation is usually executed on unit of the smelted cast-iron. At a necessity an input in the charge of a few ore sorts or their substitutes between them must be correlated from the condition of providing of the required middle maintenance of iron or other of elements in mixture or in accordance with a plan of their supplies on a factory.
In accordance with maintenance of separate elements in cast-iron and distributing from between cast-iron, a slag and gas determine the expense of materials (iron-stone, agglomerate, okatyshi, manganese ore and other), containing these elements, on unit of cast-iron (without taking into account moisture and bearing-out). Then osnovnost' of slag is set for providing of necessary properties, including its desulfurizing capabilities and the expense of gumboil is determined on unit of cast-iron.
After determining the amount of all slagmaking elements the output of slag and maintenance of separate constituents in it is calculated.
Adopting the size of coke serve, determine an expense in the serve of separate constituents of charge, thus charges each of them undertake taking into account the bearing-out of moisture. For a transition from the calculation on unit of cast-iron to the calculation in a serve the got sizes of charges of materials must be multiplied, on attitude of the accepted size of coke serve toward specific expense of coke.
The calculation of amount of blowing can be based on balance of nitrogen, oxygen and carbon or oxygen and nitrogen. The calculation of amount of blowing on balance of oxygen and carbon taken for basis is based on that, the part of carbon of coke and coalcontaining additions, given in stove installed gas at direct renewal of silicon, manganese, phosphorus and iron, during desulfurizing of cast-iron, and also passes to cast-iron and expended on formation of methane. Rest of carbon oxidizes oxygen of blowing to ÑÎ. Thus the necessary amount of oxygen is determined, and at the known maintenance him in blowing – amount of the last one.
The calculation of amount and composition of top gas is based on balance of elements, entering in the complement of formative him components. Hydrogen, entering blast-furnace stove, passes to gas as steams of water at the processes of restorations, as methane, and other passes its amount top gas out of connections with other elements.
Amount of dioxide of carbon in top gas is determined the on its maintenance in charge materials, products of their decomposition, and also to education in the reactions of renewal of oxides.
Containing of oxide of carbon in top gas is determined coming from the amount of its containing at burning of carbon in the furnace of stove, brought in with charge materials, in the reactions of direct renewal taking into account an expense on the reaction of indirect renewal.
Financial balance of the blast-furnace melting for a working high furnace is made on results measuring and analyses, for what on possibility the expense of all materials, loaded in stove, and got products of melting is exactly taken into account for the certain span of time (usually for a few days), which the expense of every material and output of slag is determined on the basis of, top gas and dust on unit of cast-iron.
While calculating the financial balance for the designed terms it is sufficient to use the information, got from the calculations of charge, top gas and blowing. Balance must meet with very small (to 1 %) divergence. Its growing is the result of wrong analysis of raw materials (a sum of maintenance of components is not 100 %) or errors in calculations.
Thermal balance is characterized by the economy of work of high furnace and takes into account correlation of amount of heat, appearing in a high furnace as a result of flowing of one or another processes, brought in a blast-furnace stove with charge materials and blowing with the amount of heat, expended on endotermall processes, taken away with the products of melting and lost in an environment and with cooling water. But one of major descriptions of work of high furnace is calculated information of thermal balance thermal output-input ratio, equal to attitude of the used heat toward selected. Thus for not in the use in a high furnace warmly adopt its losses with top gas, dust, by cooling water and in external space. The value of thermal output-input ratio is ordinary makes 78-87 % at smelting of remade cast-iron.
in beginning
Among developments of the software products given at the market there are the systems executing partly similar, but they have disadvantages such as absence of possibility of complete calculation of interesting indexes and, that is not unimportant, in these packages a design is not foreseen with the use of dust coal fuel (DCF).
In this work it is suggested to build a mathematical model describing part of blast-furnace process, taking into account influencing of DSF, which would correspond the features of work of JSC «DMZ». This model must take into account:
• calculation of technically-economic indexes of the blast-furnace melting (expense of coke, productivity) at the change of blow parameters’, properties of coke and composition of iron-ore part of charge; • íèçêîé ïðîçðà÷íîñòüþ ïðîöåññà, èç-çà îòñóòñòâèÿ âîçìîæíîñòè íåïîñðåäñòâåííîãî êîíòðîëÿ ðàçâèòèÿ îòäåëüíûõ ñòàäèé ïðîöåññà âûïëàâêè ÷óãóíà;
• calculation of properties of primary and eventual slag, which desulfurize the capabilities of eventual slag and prognostication of maintenance grey in cast-iron;
• design of the dynamical gas mode of the blast-furnace melting.
This task can be broken up on the stages:
1. Calculation of charge
- determining the amount of agglomerate and limestone;
- expense of charge materials taking into account moisture and bearing-out;
- balance grey;
- determining the amount, composition and properties of slag.
2. Calculation of amount of blowing, amount and composition of top gas:
- balance of carbon;
- calculation of amount of blowing;
- amount and composition of top gas.
3. Financial balance of the blast-furnace melting:
- enters blast-furnace stove;
- appears in a high furnace;
- divergence of balance.
in beginning
While analyzing these stages it is possible to draw the conclusion, that the effective decision of this task can be executed by the system which is taking into account all these factors in a complex. For the construction of such system it is necessary to develop a mathematical model. The analysis of the stages showed that the methods of the linear programming can be used in a model.
This model will be the basis for the system of support of decision-making on optimization of work of high furnace.
On the basis of foregoing it is possible to draw conclusions that the existent mathematical models of high furnace can not enough adequately correspond the work of high furnace with insufflation of dust coal fuel. For adequate determination of parameters of work of high furnace the creation of mathimatically-simulation model is needed to be taken into account the technological changes of DSF application.
in beginning
|