ЭЛЕКТРОННАЯ БИБЛИОТЕКА
Каракуц Ирины Сергеевны
Л.П. Калафатова, канд. техн. наук, Донецк, Украина
The articles formed layer increased imperfection is the glass based materials mechanical treatment characteristics. The imperfection degree, which depends on the cutting forces level, can he a treatment technology processes design efficiency criterion. Grinding process force characteristics can be defined by conditions, applied technology environment type and properties, diamond tool certain cutting quality provision.
Известно, что при шлифовании технических ситаллов степень дефектности обработанной поверхности определяется уровнем и направлением силового воздействия на материал при резании, зависящих от входных параметров технологического процесса обработки. Одним из этих параметров является уровень режущих свойств алмазного инструмента, обеспечиваемый за счет применения определенного способа правки.
Экспериментально установлено, что при реализации жесткой схемы шлифования ситалла, отличающейся постоянным значением кинематических параметров процесса резания, режущая способность
(Q, мм3/с) правленого круга, характеризуемая объемом сошлифованного материала в единицу времени, снижается и за 10 мин работы круга падает в 30-50 раз. Этот процесс сопровождается резким увеличением радиальной составляющей силы резания
Py (в 3 - 5 раз), направленной непосредственно в формируемую поверхность и определяющей, в основном, уровень ее дефектности.
В условиях реализации упругой схемы врезного торцового шлифования образцов ситалла АС-418 при шлифовании кругом, правленым бруском, с постоянным давлением 0,4 МПа 16 кратное снижение производительности наступает уже через 10 мин работы. Об этом свидетельствуют данные, приведенные на рисунке (левая ветвь графика). Для того, чтобы поднять уровень производительности при работе затупленным кругом, необходимо существенно, не менее чем в три раза, повысить величину усилия прижима круга к образцу, то есть давление в зоне обработки (правая ветвь графика). Образцы, при шлифовании которых с разными давлениями и при разной режущей способности круга были получены одинаковые значения производительности, исследовались по параметрам дефектности с использованием ранее разработанной методики [1].
Анализ микрофотографий дефектной поверхности образцов ситалла показал, что потеря кругом режущей способности по мере затупления не приводит к существенному изменению картины дефектности обработанной поверхности при условии постоянства давления в зоне шлифования. Однако повышение давления, связанное с необходимостью поддержания производительности процесса шлифования на определенном уровне при работе затупившимся кругом, сопровождается резким ростом дефектности обработанной поверхности ситалла. С ростом давления меняется характер дефектов. Они становятся более массивными (размеры единичных дефектов достигают 200 мкм и более), концентрируясь, в основном, по бороздам – канавкам, оставленным изношенными зернами инструмента на поверхности образцов. Причем следы дефектов, копирующих топографию микрорельефа круга, проникают вглубь образца, начиная от исходной поверхности вплоть до глубины залегания
hd=180-200 мкм. Полученные результаты свидетельствуют о необходимости введения в технологический процесс обработки ответственных изделий из ситаллов операций правки алмазного инструмента.
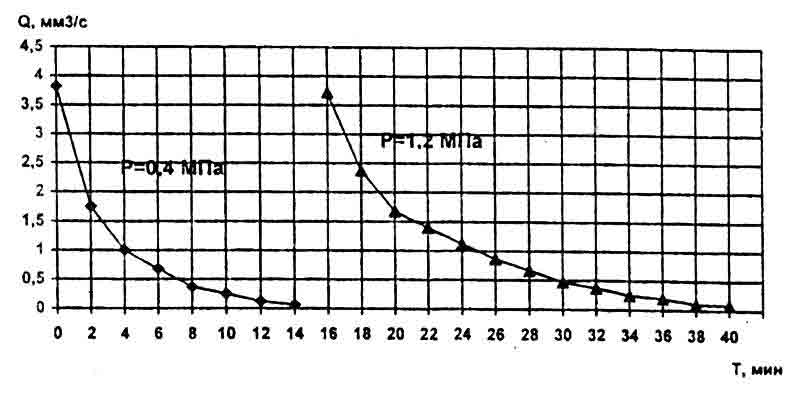
Рисунок – Изменение производительности шлифования ситалла во времени при обработке с различными давлениями. Скорость шлифования м/с, инструмент - алмазные круги
12 А2 200x76x20x5 АС6 100/80 - 4 - MB 1
Исследовались традиционно применяемый на большинстве стеклообрабатывающих предприятий способ правки абразивными брусками и разработанный способ правки свободным абразивом [2]. Оба варианта правки осуществлялись при рабочей частоте вращения шпинделя станка. Способ правки свободным абразивом реализовывался с помощью специальной установки, предусматривающей подачу абразивной суспензии в зазор между правящимся кругом и притиром. Варьируя размер зазора и зернистость шлифовального порошка, можно обеспечить необходимую величину межзеренного пространства в алмазоносном слое круга, при котором достигается требуемый уровень производительности процесса абразивной обработки.
В процессе шлифования с целью контроля состояния режущей поверхности инструмента по мере его затупления осуществлялось профилографирование рабочей поверхности круга с помощью специального записывающего устройства, фиксирующего состояние микропрофиля на одном и том же участке рабочей поверхности. Количественный анализ профилограмм рабочей поверхности кругов для рассматриваемых способов правки показал следующее. При правке свободным абразивом по сравнению с правкой абразивными брусками обеспечивается более развитый профиль режущей поверхности круга (в среднем, вылет алмазных зерен в 1,5 раза больше при увеличении на 30% количества активных зерен на единице длины трассы профилографирования). Процесс восстановления микропрофиля круга протекает более интенсивно.
В результате условия работы кругов, правленых двумя рассматриваемыми способами, не одинаковы. При шлифовании этими кругами с равными давлениями в силу того, что число зерен, их конфигурация, величина вылета над уровнем связки различны, усилия на каждом отдельном зерне и, как следствие, их воздействия на обрабатываемую поверхность будут также разниться, изменяя картину дефектности приповерхностного слоя обрабатываемого материала. Об этом свидетельствуют микрофотографии дефектной поверхности образцов ситалла, шлифованных кругами, заправленными различными способами, при обеспечении ими одинаковой производительности (Q=0,65, мм3/с). Давление в зоне обработки в обоих случаях было также одинаковым. Анализ полученных микрофотографий позволяет сделать следующее заключение.
Правка абразивным бруском деформирует поверхности алмазных зерен, снижает количество работающих зерен, увеличивает площадки контакта отдельных зерен с поверхностью обработки при общем снижении их числа, следствием чего является ухудшение условий резания. При этом возрастают нагрузки на обрабатываемый материал и увеличивается его дефектность. Дефекты концентрируются вдоль рисок, оставленных на поверхности образца плоскими поверхностями зерен инструмента. Их средние размеры находятся в диапазоне 70 - 100 мкм. Подобное распределение дефектов прослеживается на глубине до 180-200 мкм. При использовании кругов, правленых свободным абразивом, обработанную поверхность образцов на всех глубинах залегания отличает высокая плотность и малые размеры отдельных дефектов (до 20 мкм), приближающиеся по величине к размерам дефектов структуры ситалла. В этом случае дефектная область - результат взаимодействия многочисленных острых алмазных зерен с поверхностью ситалла. Алмазный инструмент, обладая большим числом активных зерен и более развитым рельефом каждого зерна по сравнению с кругом, правленым абразивным бруском, имеет гораздо большее число точек соприкосновения с обрабатываемым материалом. Следствием этого является равномерное распределение удельных давлений по поверхности контакта круга и образца при более низком уровне их значений. Глубина залегания дефектов, обусловленных обработкой, в этом случае не превышает 120 мкм, что 1,5 раза меньше по сравнению с результатами, поученными при эксплуатации кругов, правленых менее эффективным способом.
Таким образом, можно заключить, что на операциях получистового и чистового шлифования изделий из ситаллов, где окончательно формируется дефектная структура нарушенного обработкой слоя материала, с целью снижения трудоемкости последующих доводочных операций желательно предусматривать периодическую правку алмазных кругов. Причем эффективность применяемого способа правки напрямую связан с уровнем качества формируемой поверхности изделия.
Список литературы: 1. Калафатова Л.П. Диагностика дефектности обработанной поверхности технических ситаллов // Прогрессивные технологии и системы машиностроения: Сб. науч. тр./ Донецк, гос. техн. ун-т. - Донецк, 1997. Вып. 4. С.66-74. 2. А.с. 1839393 (СССР) Способ правки абразивного инструмента / В.В. Бурмистров, А.В. Байков, А.Н. Емельянов, Л.П. Калафатова, А.Д. Хроменко // Бюл. изобр. № 12. -1991.