Повышение эффективности
алмазного шлифования труднообрабатываемых материалов за счет совершенствования
конструкции шлифовальных кругов и способов их правки
Стрелков В.Б. Матюха П.Г.
http://masters.donntu.ru/2000/mehf/strelkov/rabota/stat3.htm
А Н Н О Т А Ц И Я
В работе приведен анализ современных конструкций шлифовальных кругов на металлической связке, проанализированы
непроизводительные потери алмазов, вызванных погрешностью установки
шлифовального круга на фланцы, путем сравнения напряжений в быстровращающихся
кольцах доказана возможность выполнения шлифовальных кругов сборными,
проанализированы возможные объемы сокращения алюминиевого сплава расходуемого на
корпуса в результате применения сборных кругов. Представлены конструкции кругов
со сменными алмазоносными кольцами, приведена конструкция фланца для повышения
точности установки круга.
Введение.
Шлифование алмазными кругами является одним из наиболее эффективных способов обработки труднообрабатываемых
материалов. Эффективность алмазного шлифования зависит не только от правильного
назначения режимов резания, но и конструкций шлифовальных кругов, а также
способов их правки на шлифовальном станке. Так при установке шлифовального круга
на фланцы наличие гарантированного зазора между поверхностью посадочного
отверстия круга и поверхностью неподвижного фланца обуславливает появление
эксцентриситета и радиального биения рабочей поверхности круга. Образование
радиального биения приводит к непроизводительным потерям алмазов, которые
неизбежно возникают в процессе правки.
Выполнение алмазного круга с алюминиевым корпусом приводит к повышенному расходу алюминия, т.к. в инструментальных
кладовых находятся большое количество кругов не применяющихся в производственном
цикле.
Непроизводительные потери алмазов могут возникнуть и в процессе эксплуатации, когда, например, осуществляется врезное шлифование одним кругом деталей различной длины. В этом случае, при правке
уступа, удаляются алмазы не осуществляющие процесс резания.
В связи с вышеперечисленным возникает необходимость в исследовании непроизводительных потерь алмазов и разработке
мероприятий по повышению эффективности алмазного шлифования.
1. Анализ современных конструкций алмазных шлифовальных кругов на
металлической связке и постановка задач исследований.
Алмазные круги широко используют в машиностроении. Их применяют для круглого наружного и внутреннего, плоского,
фасонного, бесцентрового шлифования деталей, заточке и доводке лезвийного
режущего инструмента, резке и обработке неметаллических материалов. Алмазными
кругами эффективно обрабатывают твердые сплавы, керамику, ферриты, ситаллы,
фарфор, кремний, германий, стекло, пластмассы, бетон и железобетон, кварц,
мрамор, гранит, туф, известняк и другие материалы, применяющиеся в различных
отраслях промышленности.
Производительность, качество обработки и эффективность процесса алмазного шлифования находятся в непосредственной
зависимости от того, насколько обосновано выбрана характеристика шлифовального
круга, которая включает параметры инструмента, определяющего его строение,
состав, свойства, форму, размеры и точность исполнения.
Алмазные шлифовальные круги изготовляют по ГОСТ 16167-70 – 16180-70, алмазные отрезные круги по ГОСТ 10110-71, алмазные отрезные сегментные круги по ГОСТ 16115 – 16116-70, алмазные шлифовальные
головки по ГОСТ 17116-71 – 17121-71.[1,2]
В соответствии с этими стандартами круги и головки, помимо буквенного обозначения их формы (АПП, АЧК, АГЦ и т.д.) имеют
еще и шифрованное цифровое обозначение каждого типоразмера инструмента (Рис.
1.1-1.4).
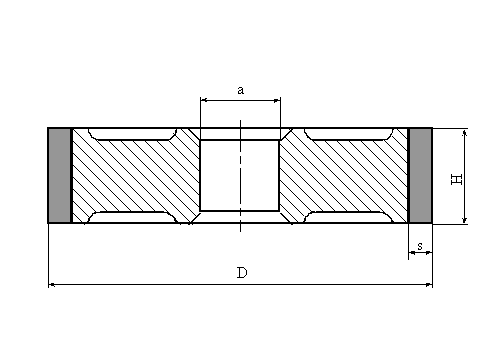
Рисунок 1.1 – Плоский алмазный шлифовальный круг прямого профиля.
Обозначение кругов (цифровое): Предельные
размеры, мм:
АПП – 2720-0000; 2720-0167; D
= 16 /500;
(исполнение 1) 2720-0344; Н = 3
/50;
ЛПП – 2720-0345; S =
2 /5.
(исполнение 2) 2720-0370.ЛПП – 2720-0251; b =
3 /305;
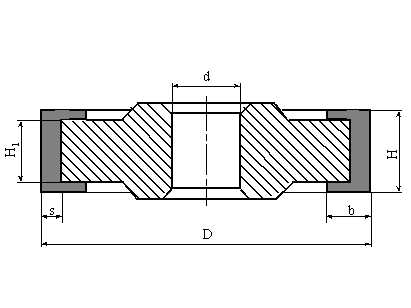
Рисунок 1.2 – Плоский алмазный
шлифовальный круг прямого профиля трехсторонний.
Цифровое обозначение кругов: Предельные
размеры, мм:
А2ПП – 2720-0201; D = 125 /250; H = 7 /20;
2720-0223. d = 32 /127; H1 = 7 /20;
b = 4 /12; S = 2 /4.
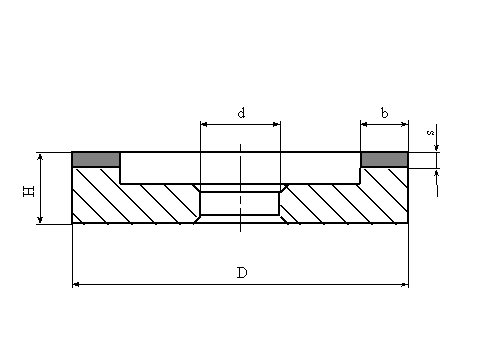
Рисунок 1.3 – Плоский алмазный
шлифовальный круг с выточкой.
Цифровое обозначение кругов: Предельные
размеры, мм:
АПВ – 2723-0001; D = 80 /300; H = 18,5 /32;
2723-0116. d = 20 /127; S = 1,5 /5.
b = 3 /60;
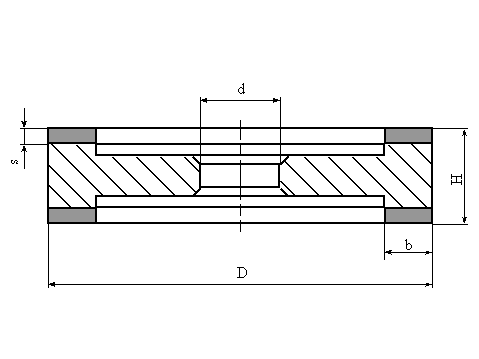
Рисунок 1.4 – Плоский алмазный
шлифовальный круг с двухсторонней выточкой.
Обозначение кругов (цифровое): Предельные
размеры, мм:
АПВД – 2723-0131; D = 100 /250;
2723-0197; d = 20 /127;
ЛПВД – 2723-0223; b =
3 /20;
2723-0239. H = 6 /25;
S = 1 /5.
Алмазные круги всех форм и размеров
(кроме А1ПП и Л1ПП) состоят из корпуса, который изготовляют из стали,
алюминиевого сплава или керамики и алмазоносного слоя, содержащего зерна
алмазного порошка, связку и в ряде случаев наполнитель. Алмазные шлифовальные
головки состоят из рабочей части, покрытой алмазоносным слоем и хвостовика.
Алмазные круги изготавливают на органической, металлической и керамической
связках.
Рядом эксплуатационных преимуществ
обладают алмазные круги с прерывистой поверхностью (рис.1.5 – 1.6). Применение
прерывистых алмазных кругов приводит к снижению температуры в зоне резания,
улучшению качества обработки, увеличению эффективности шлифования.
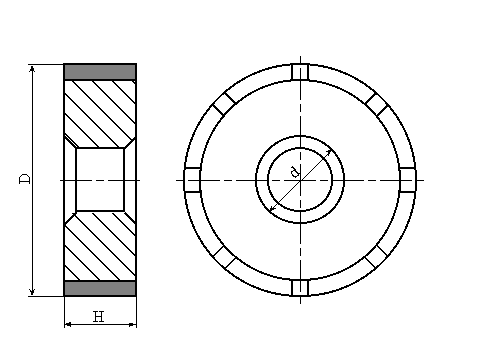
Рисунок 1.5 – Прерывистый алмазный
шлифовальный круг формы АПП.
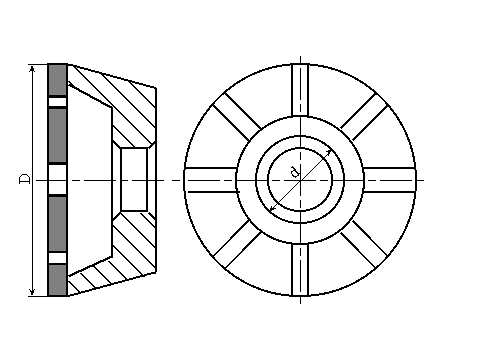
Рисунок 1.6 – Прерывистый алмазный
шлифовальный круг формы АЧК.
Определенные достоинства имеют чашечные
алмазные круги с эксцентричным расположением алмазоносного слоя.
Перспективными являются алмазные круги с
упорядоченным расположением зерен, которое обеспечивает их геометрическую
ориентацию и расстановку на рабочей части инструмента по заданной программе.
Инструменты с упорядоченным расположением зерен по сравнению с обычными
алмазными кругами отличаются повышенной производительностью, более низким
удельным расходом алмазов; их применение способствует снижению температуры в
зоне обработки.
В соответствии с техническими
требованиями корпуса алмазных шлифовальных кругов изготовляют из сталей марок
Ст.3, 20, 25 и 30 или из алюминиевого сплава марок АК6 или Д16. Сплавы АК6 и Д16
применяют обязательно, если алмазоносный слой круга крепят к корпусу с помощью
переходного элемента (кольца), для изготовления которого используют стали марок
Ст.3, 20, 25 и 30. Между алмазоносным слоем и корпусом круга (переходным
кольцом) допускается наличие промежуточного безалмазоносного слоя. Как
показывает анализ конструкций шлифовальных кругов, можно отметить недостаток,
связанный с его установкой на станок.
Известно что, шлифовальный круг средних и
больших размеров закрепляется на станке с помощью переходных фланцев, при этом
точность изготовления посадочного отверстия круга выполняется по Н7, а фланцев
по f7. То есть
посадка круга на фланцы осуществляется с гарантированным зазором.
В процессе установки круга зазор
распределяется неравномерно, в результате чего образуется эксцентриситет
вызывающий дисбаланс круга и радиальное биение рабочей поверхности круга (РПК).
Дисбаланс круга с переходными фланцами устраняется путем статистической
балансировки. При этом предельные допустимые значения смещения центра тяжести
круга относительно оси вращения составляют 40, 32, 25 и 20 мкм для кругов,
имеющих массу, соответственно, до 1, свыше 1 до 3, свыше 3 до 10 и свыше 10 до
50 кг.
Радиальное биение РПК устраняется правкой
круга, при которой алмазы, не осуществив никакой работы, переводятся в шлам.
Непроизводительные потери алмазов могут возникнуть в процессе эксплуатации
кругов, когда выполняется врезное шлифование деталей различной длины, в этом
случае на рабочей поверхности возникает уступ, который в последствии удаляется
правкой. Удаление уступа требует не только затрат времени на правку, но и
увеличивает расход алмазов, снижается производительность и увеличивается
себестоимость обработки.
Существенным недостатком существующих
алмазных шлифовальных кругов, по нашему мнению, является неразъемное крепление
кольца с алмазоносным слоем к корпусу круга. В результате на хранении в
инструментальных кладовых находится большое количество дорогостоящего
алюминиевого сплава не находящегося в производственном цикле. Последний
недостаток может быть устранен созданием сборных шлифовальных кругов, состоящих
из металлических колец с алмазоносным слоем и корпуса, который может быть
установлен на фланцы с высокой точностью.
В связи с приведенным выше, в работе
ставятся следующие задачи:
- Проанализировать непроизводительные
потери алмазов, вызванных погрешностью установки шлифовального круга на
фланцы.
- Путем сравнения напряжений в
быстровращающихся кольцах доказать возможность выполнения шлифовальных кругов
сборными.
- Проанализировать возможные объемы
сокращения алюминиевого сплава расходуемого на корпуса в результате применения
сборных кругов.
- Исследовать интенсивность образования
уступов при алмазном шлифовании титанового сплава с электроэрозионным
воздействием на РПК.
- Разработать конструкцию круга с
регулируемой высотой и сменными алмазосодержащими кольцами.
2. Снижение потерь алмазов,
за счет повышения точности установки круга на фланцы.
2.1. Анализ
непроизводительных потерь алмазов, вызванных погрешностью установки
шлифовального круга на фланцы.
Шлифовальный круг закрепляется на станке
с помощью переходных фланцев. Для определения величины алмазоносного слоя,
удаляемого в процессе правки, воспользуемся техническими условиями ГОСТов
2270-78, 16181-82Е, регламентирующие величину полей допусков на посадочные
размеры кругов и неподвижного фланца.[1,2]
Анализируя эти отклонения (для фланцев
f7, для кругов
Н7) можно заметить, что установка шлифовального круга на фланец осуществляется
по посадке с гарантированным зазором. Наличие гарантированного зазора
способствует появлению радиального биения при установке круга на фланцы, которое
должно быть устранено во время правки.
Определим величину алмазоносного слоя,
удаляемого при правке, с целью устранения радиального биения (рис. 1.1).
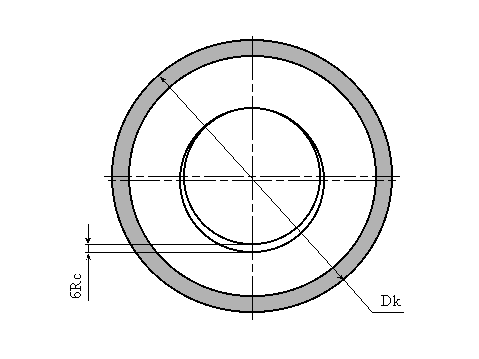
Рисунок 2.1 – Образование радиального
биения при установке круга на фланцы.
Объем удаляемого алмазоносного слоя при
правке определяется по формуле
, мм3, (1.1)
где Dk –
диаметр шлифовального круга,
мм;
Вк – высота шлифовального
круга, мм;
d R – величина радиального зазора, мм.
Вследствие того, что статистическое
распределение размеров при изготовлении цилиндрических поверхностей подчиняется
нормальному закону[3], то при расчете величины радиального зазора будем использовать середину
полей допусков на посадочные размеры круга и фланца
, (1.2)
где ЕС, ес – середина поля допуска
соответственно для круга и фланца, мм.
; .
Здесь ES, es – верхнее отклонение для
круга и фланца, мм;
EJ, ei – нижнее
отклонение для круга и фланца, мм.
Тогда
. (1.3)
Подставляя (1.3) в (1.1)
получим
. (1.4)
По величине алмазоносного слоя определим
вес алмазов, содержащихся в этом объеме
, карат, (1.5)
где 0,878* 10-3 – масса
алмазов в 1 мм3 алмазоносного слоя, г;
0,2 – масса одного карата алмазов,
г;
a - коэффициент, учитывающий концентрацию алмазов
(при 100% a =1).
Тогда, с учетом стоимости Ц одного карата
алмазов [4],
стоимость потерянных алмазов при правке составит
, у.е., (1.6)
где Ц – стоимость одного карата алмазов,
у.е.
Рассмотрим пример расчета стоимости
удаляемых алмазов при правке круга 1А1 250* 76* 16/ 5 АС6 160/125-4-М1 по следующим исходным данным:
Dk =
250, Вк = 16, ES = 0,030, EJ = 0, es = -0,030, ei
= -0,060.
Величина радиального биения при установке
круга на фланцы
мм.
Объем алмазоносного слоя, удаляемого
правкой круга
мм3.
Масса удаляемых алмазов
карат.
Стоимость удаляемых алмазов
у.е.
Таким образом, потери на операции правки,
только за счет удаляемых алмазов при устранении радиального биения круга 1А1
250* 76* 16* 5 АС6 160/125-4-М1
составляют 0,2 у.е.
Аналогично были проведены расчеты потерь
на операции правки за счет удаленных алмазов для кругов других геометрических
размеров зернистости и марок алмазных зерен (таблица 1).
Таблица 1 -
Погрешность установки шлифовального
круга на фланцы, объем удаляемого слоя в процессе правки и стоимость потерь на
операции правки.
№
пп
|
Марка алмаза
|
Рaзмер круга
|
Предельные отклонения
посадочного отверстия круга, мкм /3/
|
Предельные
отклонения
диаметра посадочного фланца,
мкм /2/
|
Среднее значе-ние ра-диаль-
ного биения d Rc, мм
|
Объем удаля-емого алмазов
носного слоя, мм3 Vас
|
Масса удаляемых алма-зов,
карат G
|
Зернистость,
мкм
|
Цена 1 карата,
руб.
Ц
|
Стои-мость удаля-емых
алма-зов,руб. С
|
верхнее отклоне-ние
ES
|
нижнее
отклоне-ние EJ
|
верхнее
отклоне-ние es
|
нижнее
отклоне-ние ei
|
1
|
2
|
3
|
4
|
5
|
6
|
7
|
8
|
9
|
10
|
11
|
12
|
13
|
|
|
250х76х x16x5
|
30
|
0
|
-30
|
-60
|
0,060
|
376,8
|
1,66
|
160/125
|
0,12
|
0,2
|
250/200
|
0,25
|
0,42
|
400/315
|
0,50
|
0,83
|
1.
|
АС6
|
300хI27х40х5
|
40
|
0
|
-43
|
-63
|
0,083
|
1563,7
|
6,86
|
I60/I25
|
0,12
|
0,82
|
250/200
|
0,25
|
1,71
|
400/315
|
0,50
|
3,43
|
|
|
400х203х40х5
|
46
|
0
|
-50
|
-96
|
0,096
|
2411,52
|
10,59
|
I60/I25
|
0,12
|
1,27
|
260/200
|
0,25
|
2,64
|
400/315
|
0,50
|
5,29
|
|
|
250х76 x16x5
|
30
|
0
|
-30
|
-60
|
0,060
|
376,8
|
1,66
|
160/125
|
0,40
|
0,66
|
250/200
|
0,80
|
1,33
|
400/315
|
1,20
|
1,99
|
2.
|
ACI5
|
300х127х40х5
|
40
|
0
|
-43
|
-63
|
0,083
|
1563,7
|
6,86
|
160/125
|
0,40
|
2,74
|
250/200
|
0,80
|
5,48
|
400/315
|
2,2
|
8,23
|
|
|
400х203х40х5
|
46
|
0
|
-50
|
"96
|
0,096
|
2411,52
|
10,59
|
60/I25
|
0,40
|
4,23
|
250/200
|
0,90
|
8,47
|
400/315
|
1,20
|
12,7
|
|
|
250х76х16х5
|
30
|
0
|
-30
|
-60
|
0,060
|
376,8
|
1,66
|
160/125
|
0,50
|
0,83
|
250/200
|
1,00
|
1,66
|
400/315
|
1,40
|
2,32
|
3.
|
АС20
|
300х127х40х5
|
40
|
0
|
-43
|
-63
|
0,083
|
1563,7
|
6,86
|
I60/I25
|
0,50
|
3,43
|
250/200
|
1,00
|
6,86
|
400/315
|
1,40
|
9,6
|
|
|
400х203х40х5
|
46
|
0
|
-50
|
-96
|
0,096
|
2411,52
|
10,59
|
160/120
|
0,50
|
5,29
|
250/200
|
1,00
|
10,50
|
400/315
|
1,40
|
14,82
|
Как видно из приведенных данных,
непроизводительные потери на операции правки для круга 1А1 250? 76? 16? 5 АС6 160/125-4-М1, используемого при бесцентровом шлифовании, составляет
около 15 у.е. без учета затрат на операцию правки, что говорит о необходимости
поиска путей улучшения центрирования круга при его установке на
фланцы.
2.2. Конструкция фланца для
повышения точности установки круга.
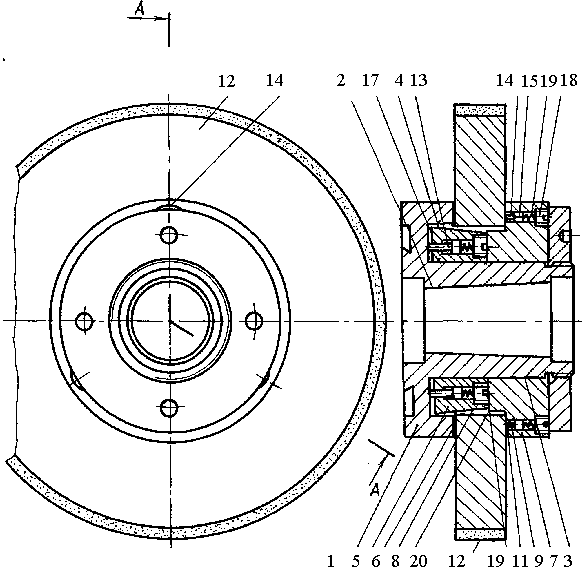
Рисунок 2.2 – Устройство для закрепления алмазного круга с
самоцентрированием.
Устройство для закрепления шлифовального
круга с самоцентрированием (рис.1) [5] состоит из неподвижного фланца 1 с коническим
отверстием 2 для установки на шпиндель станка цилиндрической поверхности 3 и
проточкой 4, выполненной в зоне перехода цилиндрической поверхности 3
установлены центрирующие кольца 5 с конической наружной поверхностью 6 и
подвижный фланец 7. Между торцовыми поверхностями 8 и 9 фланцев 1 и 7 установлен и зажат с помощью гайки 10
через прокладки 11 алмазный круг 12. В отверстиях 13 и 14 центрирующего кольца 5
и подвижного фланца 7 установлены толкатели 15, поджимаемые пружинами 16 к
торцовой поверхности 17 проточки 4 и торец шлифовального круга 12, винты 18,
служащие для регулирования силы поджима толкателей.
Торцовая часть 19 центрирующего кольца 5
контактирует с торцовой поверхностью 20 буртика подвижного фланца 7.
Закрепление шлифовального круга в
предлагаемом устройстве осуществляется следующим образом. Алмазный круг 12
устанавливается посадочным отверстием на коническую поверхность 6 центрирующего
кольца 15 и цилиндрическую поверхность буртика подвижного фланца 7, размер
которой обеспечивает гарантированный зазор с поверхностью посадочного
отверстия.
От действия пружин 16 толкатели 15
максимально выступают из отверстий 12 и 14. При вращении гайки 10 торцы фланцев
1 и 7 начинают сближаться, в результате чего в контакт с торцовой поверхностью
круга вступают толкатели 15 на торцовой поверхности подвижного фланца 7. Круг 12
начинает перемещаться в осевом направлении центрируясь по конической поверхности
6. После того, как зазор между конической поверхностью 6 и поверхностью
посадочного отверстия шлифовального круга будет выбран, круг будет перемещаться вдоль оси в том
же направлении уже совместно с центрирующим кольцом 5 (жесткость пружины в
отверстиях подвижного фланца выбираются большей, чем жесткость пружин в
отверстиях базирующего кольца).
После того как шлифовальный круг подойдет
к торцовой поверхности неподвижного фланца, происходит его окончательное
центрирование относительно оси неподвижного фланца. При дальнейшем вращении
гайки круг все с большей силой прижимается к неподвижному фланцу, фиксируя его
положение. Когда положение центрированного круга надежно зафиксировано, торцовая
поверхность буртика 20 вступает в контакт с торцовой поверхностью 19
центрирующего кольца 5 и начинает его перемещать в осевом направлении, уводя
коническую поверхность от поверхности посадочного отверстия, изолируя круг от
массы станка.
Окончательное закрепление круга
осуществляется силой трения на торцовых поверхностях фланцев, создаваемой силой
затяжки гайки.
Таким образом, рекомендуемые для
применения фланцы с самоцентрированием для крепления алмазных кругов, позволяют
осуществить закрепление и центрирование кругов, что будет способствовать
сокращению времени на установку, уменьшению погрешности установки и расхода
алмазоносного слоя в процессе предварительной правки.
3. Снижение расхода алюминия
в шлифовальных кругах различной высоты.
3.1. Исследование напряжений
вызванных центробежными силами в кольце шлифовального
круга.
При шлифовании на элементарный объем
круга действует центробежная сила инерции прямо пропорциональная квадрату
угловой скорости и расстоянию до центра вращения. Действие этой силы приводит к
возникновению напряжений между элементарными объемами, которые при определенных
условиях могут превысить допустимые, что в конечном итоге приведет к разрыву
круга. В силу этого, прежде чем работать кругами на повышенных скоростях резания, их
необходимо проверить на прочность.
Исходными данными при расчете являются
геометрические размеры круга, его угловая скорость и мощность главного привода,
определяемые технической характеристикой станка.
В быстровращающемся круге будут возникать
радиальные и окружные напряжения, зависящие от внутреннего диаметра круга. Их
величина рассчитывается по следующим известным зависимостям [6]:
, (3.1)
, (3.2)
где s r – радиальное
напряжение, МПа;
s t – окружное напряжение, МПа;
g – плотность материала круга, кг/м3 (7,8?
103 кг/м3);
w – угловая скорость круга, С-1;
g – ускорение свободного падения,
м/с2
(9,8 м/с2);
m – коэффициент Пуассона (0,3 – для
стали);
Rн–
наружный радиус шлифовального круга, мм;
rb –
внутренний радиус шлифовального круга, мм;
r – текущий радиус шлифовального круга,
мм.
Используя паспортные данные станка модели
3Е183А, определим окружную скорость шлифовального круга диаметром 300
мм.
- Мощность главного привода – 7,5
кВт.
- Наружный диаметр шлифовального круга –
300 мм.
- Частота вращения шпинделя – 1672
об/мин.
- Размер конуса шпинделя по ГОСТ
2323-76
диаметр – 80мм;
длина – 80мм.
м/с ,
При расчете угловой скорости с целью
создания определенного запаса принимаем Vp =
35 м/с
, С-1 ,
где Vp – окружная скорость шлифовального круга, м/с;
RH – наружный радиус шлифовального круга, м (из паспорта
станка).
С целью определения размера кольца с
алмазоносным слоем требуемой высоты расчет напряжений будем осуществлять,
изменяя внутренний диаметр шлифовального круга 2rb , при этом
наружный диаметр остается постоянным и равным 2Rн = 300мм. Внутренний диаметр будем
изменять от 280 до 203 мм с шагом 20 мм.
Расчеты напряжений выполним в трех
точках: на наружном диаметре, внутреннем диаметре и на диаметре наибольших
радиальных напряжений.
Для определения радиальных и окружных
напряжений воспользуемся зависимостями (3.1) и (3.2), подставляя вместо текущего
радиуса величины внутреннего радиуса rb и
наружного RH. Значение текущего радиуса, на котором действуют максимальные радиальные
напряжения, определяем по формуле [7]
.
Рассмотрим пример расчета радиальных и
окружных напряжений в кольце следующих размеров: RH =150 мм;
rb
=140 мм.
а) Расчет напряжений на наружном диаметре
шлифовального кольца
s r = 0
МПа.
б) Расчет напряжений на внутреннем
диаметре шлифовального кольца
s r = 0
МПа.
в) Расчет напряжений в точке максимальных
радиальных напряжений
мм;
МПа;
МПа.
Распределение рассчитанных напряжений,
выполненных на ПЭВМ, приведено на рис.3.1 из которого видно, что максимальные их
значения от действия сил инерции, будут возникать на внутренней поверхности
шлифовального кольца.
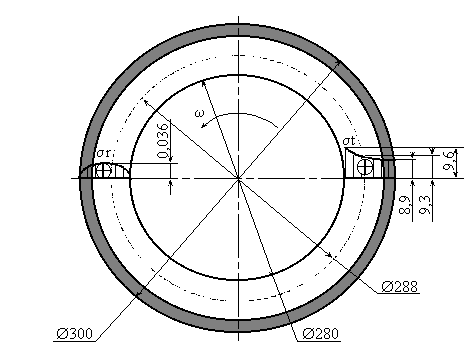
Рисунок – 3.1 Эпюры
напряжений, возникающих в шлифовальном кольце под действием сил
инерции.
Аналогично были рассчитаны напряжения для
колец других размеров (табл.3.1), величины которых зависят от внутреннего
радиуса (рис.3.2). Из приведенных графиков видно, что с увеличением внутреннего
радиуса максимальные окружные напряжения увеличиваются, а максимальные
радиальные напряжения уменьшаются (рис.3.3).
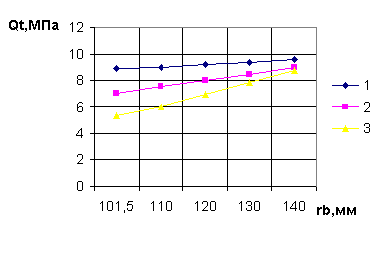
Рисунок 3.2 – Влияние радиуса внутренней
поверхности шлифовального кольца на величину окружных напряжений s t. Наружный радиус
Rн =
150 мм.
1. Величина окружных напряжений на
внутренней поверхности кольца;
2. Величина окружных напряжений на
наружной поверхности кольца;
3. Величина окружных напряжений в точке
максимальных радиальных напряжений;
Рисунок 3.3 – Влияние радиуса внутренней
поверхности шлифовального кольца на величину максимальных
радиальных напряжений s r . Наружный радиус
Rн =
150 мм.
Как видно из приведенных расчетов
напряжений (см.табл.3.2), возникающих под действием центробежных сил инерции,
величина этих напряжений значительно меньше допустимых напряжений на разрыв. Для
изготовления колец рекомендуются стали Ст.3, стали 20 [8], тогда для стали с самыми
низкими допускаемыми напряжениями на [9] разрыв Ст.3 s р = 160
МПа.
Следовательно, кольца с алмазоносным
слоем при обработке крепежных деталей на бесцентрово-шлифовальном станке
являются высоконадежными и исключают опасность разрыва. Поэтому выбор размеров
кольца при заданном режиме может осуществляться исходя из конструктивных
соображений.
3.2. Определение возможных
объемов сокращения алюминиевого сплава расходуемого на корпуса в результате
применения сборных кругов.
Для проведения расчетов будем
использовать круг алмазный синтетический 250* 76* 15* 4 АС-15 (рис.2.1). Инструмент изготовлен на
полтавском заводе шлифовальных инструментов.
Анализируя размеры алюминиевого диска,
подсчитаем его объем:
, мм3
где R – радиус алюминиевого
диска;
r – радиус отверстия .
, мм3 .
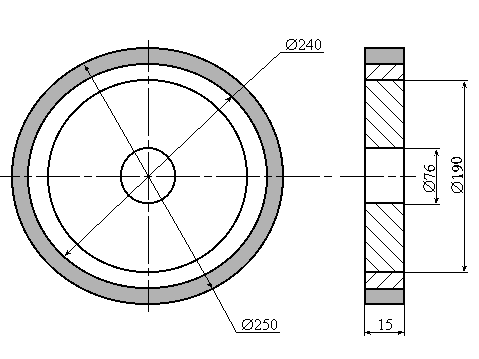
Рисунок 3.4 – конструкция стандартного
алмазного шлифовального круга.
Проведем сравнительный анализ
относительно 10 кругов. Используемый объем алюминиевого сплава расходуемого на
изготовление 10 кругов составит:
V10=3570650 мм3.
При использовании сборных кругов
требуемый объем алюминия для корпуса составит:
, мм3 .
Так как на один корпус, последовательно
устанавливаем металлические кольца с алмазоносным слоем, то получим существенную
экономию дорогостоящего алюминия.
Общий выигрыш составит:

Следовательно, достигается 85%-я экономия
алюминиевого сплава. Отсюда можно сделать вывод, что при использовании корпуса и
десяти алмазоносных колец (их количество практически неограниченно при
последовательной установке), мы получаем 85% экономию алюминия.
3.3. Новые конструкции
кругов со сменными алмазоносными кольцами.
Сборный абразивный круг [10] состоит из корпуса 1
(рис. 3.5) в виде усеченного конуса с базирующей поверхностью 2, на которую
установлено абразивонесущее кольцо 3, имеющее аналогичную посадочную коническую
поверхность 4.
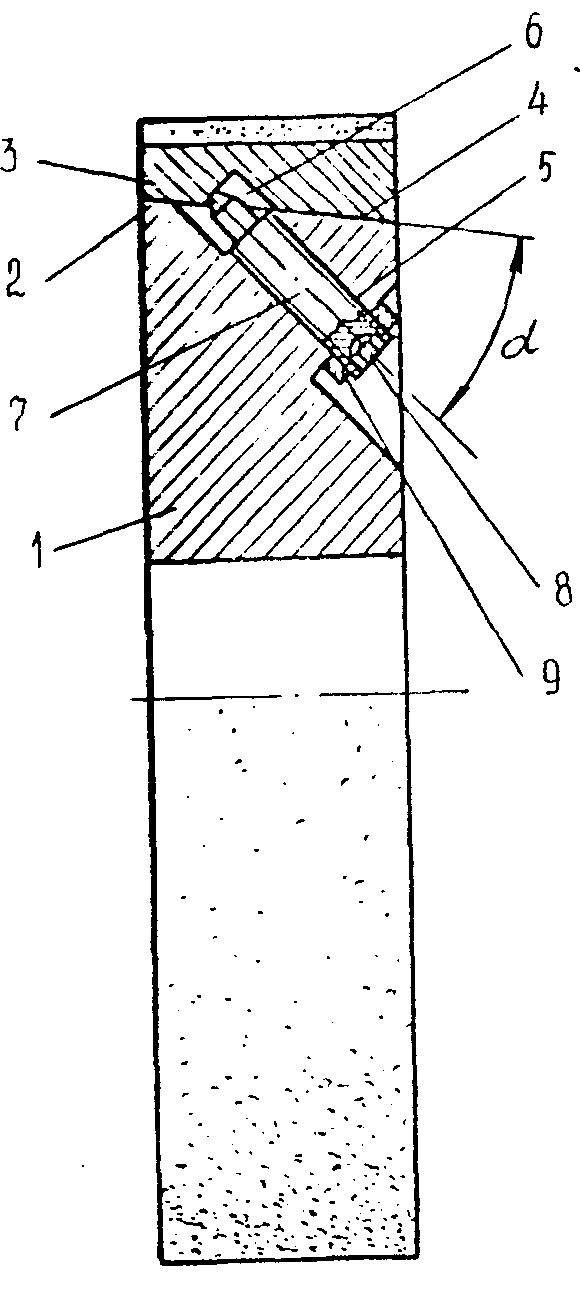
Рисунок 3.5 – Сборный шлифовальный
круг.
В торцовой поверхности корпуса 1
выполнены резьбовые отверстия 5, расположенные под углом a к образующей
поверхности 2. Посадочная поверхность 4 абразивонесущего кольца 3 снабжена
кольцевой канавкой 6, с поверхностью которой контактируют торцовые поверхности
винтов 7 (фиксаторов), служащие для закрепления абразивонесущего кольца 3 на
корпусе 1. Винты снабжены шестигранным углублением 8 под ключ. Гайка 9 служит
для законтривания винта 7.
Закрепление абразивонесущего кольца
осуществляется следующим образом.
Перед закреплением кольца 3 винты 7,
установленные в резьбовые отверстия 5 корпуса 1, выкручены настолько, чтобы они
не выступали за коническую базирующую поверхность 2.
Абразивонесущее кольцо 3 устанавливается
своей посадочной поверхностью 4 на базирующую поверхность 2 корпуса 1. Затем
ключом, установленным в шестигранное углубление 8, начинается последовательное
закручивание винтов 7. В процессе закручивания торцовая поверхность винта
вступает в контакт с поверхностью кольцевой проточки 6 и, смещая абразивонесущее
кольцо 3 относительно корпуса 1, создает на конических поверхностях 2 и 4
нормальную силу, способную исключить проворот абразивонесущего кольца на корпусе
1. После закрепления кольца 3 винты 7 законтривают гайкой 9.
Раскрепление кольца осуществляется после
ослабления затяжки гайки 9 выкручиванием винтов 7 до их исходного положения,
когда они не выступают за коническую базовую поверхность 2. После этого
абразивонесущее кольцо 3 снимается с корпуса (угол конуса поверхностей 2 и 4 не
самотормозящий).
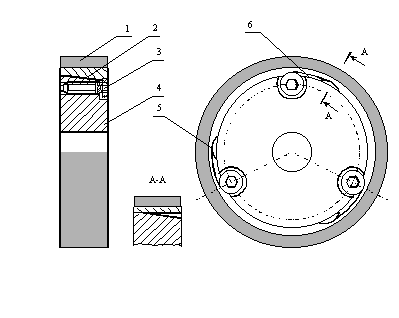
Рисунок 3.6 – Сборный шлифовальный
круг.
Сборный абразивный круг (рис.3.6) состоит
из корпуса 4 в виде усеченного конуса с базирующей поверхностью 2, на которую
установлено абразивонесущее кольцо 1, имеющее аналогичную посадочную коническую
поверхность и сквозную проточку 5.
В торцовой поверхности корпуса 1
выполнены резьбовые отверстия. Посадочная поверхность 2 абразивонесущего кольца
1 снабжена канавкой 6, с поверхностью которой контактирует поверхность шляпки
винтов 3 (фиксаторов), служащие для закрепления абразивонесущего кольца 1 на
корпусе 4. Винты снабжены шестигранным углублением под ключ.
Закрепление абразивонесущего кольца
осуществляется следующим образом.
Перед закреплением кольца 1 винты 3,
установленные в резьбовые отверстия корпуса 4, выкручены настолько, чтобы они
выступали за торцовую поверхность корпуса 4.
Абразивонесущее кольцо 1 устанавливается
своей посадочной поверхностью 2 на базирующую поверхность корпуса 4, сквозные
проточки кольца в этот момент находятся напротив шляпок зажимных винтов.
Поворачиваем абразивное кольцо до упора, шляпки фиксаторов входят в канавки
абразивонесущего кольца. Затем ключом, установленным в шестигранное углубление,
начинается последовательное закручивание винтов 3. В процессе закручивания
шляпка винта вступает в контакт с поверхностью проточки 6 и, смещая
абразивонесущее кольцо 1 относительно корпуса 4, создает на конических
поверхностях 2 нормальную силу, способную исключить проворот абразивонесущего
кольца на корпусе 4.
Преимущества данной конструкции –
простота изготовления, высокая технологичность, малое количество
деталей.
4. Снижение
непроизводительных потерь алмазов при врезном шлифовании.
4.1. Исследование
интенсивности образования уступа на рабочей поверхности круга при врезном
алмазном шлифовании.
Интенсивность образования уступа
исследовали при плоском врезном шлифовании образца из сплава ВТ14, ширина
которого была меньше высоты шлифовального круга 1А1 250? 75? 15? 5 АС6 160/125-4-М2-01 [11]. Шлифование осуществляли с различными схемами
подвода технологического тока – в зону резания, в автономную зону, а также без
введения тока на плоскошлифовальном станке модели 3Г71, модернизированном для
осуществления электроэрозионных воздействий на режущую поверхность круга
(РПК).
При шлифовании с электроэрозионным
воздействием на РПК в зоне резания шлифовальный круг 1 подключается к
положительному полюсу источника технологического тока, а магнитная плита 4 с
установленными на ней струбциной 3 и образцом 2, - к отрицательному полюсу
(рис.1,а).
При шлифовании с электроэрозионным
воздействием на РПК в автономной зоне, положительный полюс источника
технологического тока подключается к шлифовальному кругу, а отрицательный – к
электроду, расположенному в автономной зоне, не совпадающей с зоной резания
(рис.1,б).
Перед экспериментом круг правили
электроэрозионным способом с использованием источника технологического тока
модели ИТТ-35. Охлаждение 0,3%-ным водным раствором кальцинированной
соды.
Интенсивность образования уступа
оценивали удельной высотой уступа К, представляющей собой высоту уступа,
образующегося при сошлифовывании 1 мм3 обрабатываемого
материала, шириной круга, равной 1 мм.
,
где h –
высота уступа, мкм;
Вd – ширина
шлифуемой поверхности;
V – объем
сошлифованного материала, мм3.
Высоту уступа h определяли по
профилограмме пластинки, обработанной врезным шлифованием поверхностью круга,
имеющей уступ.
Объем сошлифованного материала
рассчитывали по формуле
, мм3,
где L –
длина образца, мм;
Hн, Hк –
высота образца до и после шлифования,
мм.
Как показали эксперименты, результаты
которых приведены в табл. 1, на интенсивность образования уступа оказывает
влияние схема подвода технологического тока, а также напряжение холостого хода.
Так, наибольшая интенсивность образования уступа наблюдается при подводе
технологического тока в зону резания. Это объясняется тем, что инициирование
электрических разрядов при подводе тока в зону резания происходит за счет
кратковременного
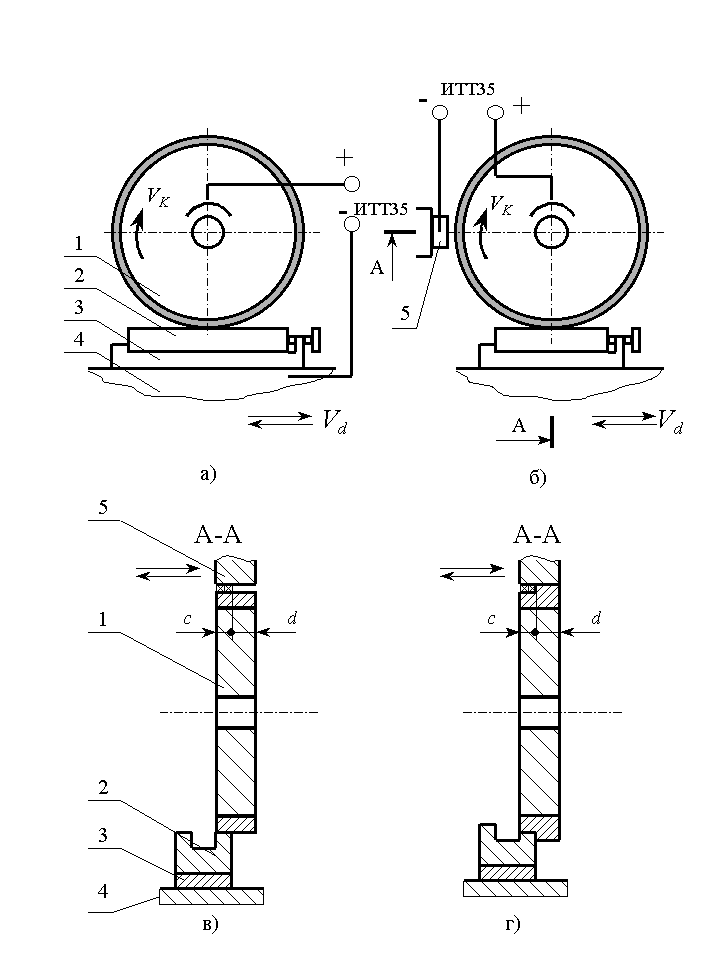
Рисунок 4.1 – Схемы врезного шлифования с
электроэрозионным воздействием не РПК в зоне резания (а) и в автономной зоне (б,
в, г).
замыкания стружками межэлектродного
промежутка (МЭП). В результате при подводе технологического тока в зону резания
количество стружек, инициирующих разряды, превышает количество стружек,
достигающих межэлектродного зазора между автономным электродом и связкой круга
при подводе технологического тока в автономную зону. Поэтому при одном и том же
напряжении холостого хода (за счет различного электрического сопротивления
межэлектродного промежутка) средний ток при воздействии на РПК с подводом
технологического тока в зону резания превышает средний ток при электроэрозионных
воздействиях с подводом энергии в автономную зону, вызывая при этом более
интенсивный износ шлифовального круга и образование уступа на рабочей
поверхности инструмента.
По этой причине наименьшая интенсивность
образования уступа наблюдается при шлифовании с подводом энергии в автономную
зону с Uхх= 35 В и алмазном шлифовании без тока.
Таблица 2 – Интенсивность образования
уступа на рабочей поверхности круга при шлифовании сплава ВТ14 кругом АС6
160/125-4-М2-01 (Ширина шлифуемой поверхности образца 7,5мм, источник
технологического тока – блок питания ИТТ-35).
№ п/п
|
Способ подвода техно-логи-
чекого тока
|
Режимы
обработки
|
Объем сошлифо-ванного
материала, V,мм3
|
Величина уступа на рабочей
поверхнос-ти круга, h,мкм
|
Удельная высота уступа,
К, 
|
механические
|
электрические
|
Vк , м/с
|
Vd , м/с
|
t , мм
|
Uxx , В
|
Jср ,А
|
1
|
В зону
резания
|
35
|
6
|
0,005
|
35
|
3,5
|
2234
|
32
|
107,4·10-3
|
2
|
50
|
7
|
2143
|
62
|
217,0·10-3
|
3
|
58
|
11
|
927
|
67
|
542,0·10-3
|
4
|
65
|
16
|
517
|
46
|
667,0·10-3
|
5
|
В автоно-мную
зону
|
35
|
1,5
|
6526
|
8
|
9,1·10-3
|
6
|
50
|
2,5
|
5850
|
10
|
12,8·10-3
|
7
|
65
|
4
|
6487
|
34
|
39,3·10-3
|
8
|
Без тока
|
-
|
-
|
13235
|
6
|
3,4·10-3
|
В процессе экспериментов было обнаружено,
что электроэрозионные воздействия на поверхность круга, не участвующую в работе,
при подводе тока в автономную зону отсутствуют, наоборот, она засаливается
материалом автономного электрода.
Для выяснения физической природы такой
особенности рассмотрим рис.1 в, г, на котором представлено сечение А-А зон
правки и шлифования на рис.1, б в начале (рис.1в) и в конце (рис.1 г)
шлифования.
Как видно из рисунка, в начале шлифования
электрическое сопротивление МЭП неравномерно, так как в зоне c в зазор попадают
стружки, а в зоне d они отсутствуют (см. рис.1 в). По этой причине
электрические разряды, проходящие по пути наименьшего электрического
сопротивления, возникают лишь в зоне
c,
осуществляя удаление связки. В результате удаляются и алмазы, образуя уступ. При
этом межэлектродный зазор увеличивается, а средний ток начинает
уменьшаться.
Чтобы увеличить средний ток, электрод
перемещается в радиальном направлении к центру круга и часть рабочей поверхности
круга d
(см. рис.1,г) начинает обрабатывать соответствующую поверхность автономного
электрода. В это же время на участке c прекращают инициироваться разряды, осуществляющие
электроэрозионное удаление связки.
Описанные явления полностью
подтверждаются как видом РПК (участок d покрыт материалом электрода, а участок
c -
удаленной связкой), так и видом электрода (участок c поверхности имеет
следы электрических разрядов, а участок
d
имеет светлый вид шлифованной поверхности).
Таким образом, избежать образования
уступа на РПК при шлифовании образца, длина которого меньше высоты круга, с
помощью различных схем электроэрозионных воздействий на РПК, осуществляемых
одновременно с обработкой образца, невозможно. Наоборот электроэрозионные
воздействия стимулируют образование уступа.
Для уменьшения отрицательного влияния
образования уступа на производительность и себестоимость обработки
рекомендуется:
- обработку осуществлять алмазным
шлифованием с периодической правкой РПК электроэрозионным способом;
- удалять уступы с использованием
высокопроизводительных комбинированных способов правки (А.С. №1555072, №1514589,
№1355393).
Полностью исключить образование уступа на
РПК возможно использованием при обработке шлифовальных кругов с плавно
регулируемой высотой (А.С. №1645125А1), что позволяет превратить существующий
дискретный ряд по высоте кругов в непрерывный.
З А К Л Ю Ч Е Н И
Е
Результаты проведенных исследований
позволяют сделать следующее заключение:
- повышение точности установки круга на
фланцы по радиальному биению позволяет значительно уменьшить непроизводительные
расходы алмазов (до 0,2 у.е. на кругах средних размеров);
- доказана возможность выполнения алмазных
шлифовальных кругов сборными, т.к. напряжения в быстровращающемся кольце в
результате центробежных сил, почти в 20 раз меньше допустимых;
- выполнение алмазного шлифовального круга
сборным позволяет сократить расход алюминиевого сплава на 85%;
- разработаны конструкции сборных
шлифовальных кругов;
- устройство для точной установки корпуса
на фланцах.
В дальнейшем планируется представить
методику расчета сил закрепления кольца на корпусе.
ПЕРЕЧЕНЬ ССЫЛОК
1. ГОСТ 2270-78. Инструмент абразивный.
Основные размеры элементов крепления. Издательство стандартов, 1978г. - 16
с.
2. ГОСТ I6181-82E. Круги алмазные
шлифовальные. Технические условия. Издательство стандартов, 1982г. - 19
с.
3. Якушев А.И. Взаимозаменяемость,
стандартизация и технические измерения : Учебник – 5-е изд., перераб. И доп. –
М.: Машиностроение, 1979г – 344 с.
4. Прейскурант № 18-07-1981.
5. А.с. 1444136А1 Устройство для
крепления абразивного круга П.Г. Матюха, В.Р. Габитов, В.А. Каплун Опубл. 1988г.
Бюл.№46.
6. Феодосьев В.И. Сопротивление
материалов: учебник для втузов - 9-е изд., перераб.- М.: Наука, 1986г. - 512
с.
7. Казаков В.Ф. Шлифование при повышенных
скоростях резания. К.: Техника, 1971г. - 172 с.
8. Ящерицын П.И., Дорофеев В.Д., Пахалин
Ю.А. Электроэрозионная правка алмазно-абразивных инструментов. - М.: Наука и
техника, 1981г. - 232 с.
9Расчет и конструирование. Справочник. В
Э-зст Псд ред. проф. д.т.н. . Детали машин. заслуженного деятнауки и техники
РСФСР Н.С.Ачеркана. Изд. 3-е, перераб. Т.2 - М.: . машиностроение-440 с., 1968г.
10. А.с. 1771940 (СССР) В 24D 5/06 АБРАЗИВНЫЙ КРУГ.
МатюхаП.Г. Опубл. 1992г. Бюл.№40.
11. Цокур В.П., Матюха П.Г., Стрелков
В.Б. Интенсивность образования уступа на рабочей поверхности круга при врезном
алмазном шлифовании / Прогрессивные технологии и системы машиностроения. Сб.
научн. Трудов. – Донецк: ДонГТУ, 2000г. Вып.10, С. 253 – 257.
|
|