Применение марковских полей для распознавания текстурных изображений сталей
Спорыхин В. Я., Меркулов Д. А., Иванова К. Е. фрагмент статьи, написанной для сборника раучных работ стулентов и аспирантов Донецкого национального технического университета
Общая постановка проблемы
Черные металлы являются основным материалом, который используют в различных отраслях промышленности: в машиностроении, авиастроении и судостроении, для изготовления металлоконструкций для промышленного и жилищного строительства, транспортных коммуникаций и техники.
Металлургические заводы Донбасса предоставляют свою продукцию не только в страны бывшего СНГ, но и за рубеж. При этом продукция должна быть качественной, чтобы не потерять клиентов и сохранить свою конкурентоспособность на мировом рынке. Поэтому задача получения комплекса свойств того или иного металла становится еще более актуальной, так как позволяет найти равноценный отечественный заменитель иностранным маркам стали как по составу, так и по свойствам. Одним из самых важных аспектов решения данной задачи является контроль качества выпускаемой продукции. Однако в условиях Донецка, например на ЗАО ММЗ «Истил (Украина)» существует только одна центральная лаборатория, которая осуществляет контроль соответствия выплавленной стали заказу покупателя. К тому же контроль проводится по ограниченному числу характеристик путем визуального сравне-ния проверяемого образца с эталоном. Таким образом, создание автоматизированной системы металлографического анализа срезов сплавов на основе обработки их изображений является актуальной задачей.
Постановка задач исследования
Для построения системы металлографического анализа срезов стали необходимо решить следующие основные задачи:
- выполнить анализ производственного цикла выплавки стали и проанализировать процесс контроля качества выпускаемой металлургической продукции;
- выделить основные этапы металлографического анализа и проанализировать основной из них – этап определения размера зерна стали;
- определить наиболее оптимальные методы распознавания текстуры металлографического изображения среза;
- выбрать наиболее оптимальные методы определения размера зерна стали.
Решение задач и результаты исследования
Процесс выплавки стали начинается с заказа сплава и заканчивается проверкой готовой продукции. Этот процесс включает следующие основные этапы:
1. Оформление предварительного заказа на необходимую марку стали и с соответствующих требований к ней. Передача основных требований к продукции в технический отдел.
2. Отделом договорной документации составляется договор с заказчиком. Параллельно составляется спецификация на выплавку заказа, где указываются все требования к продукции.
3. Далее спецификация передается в цех на выплавку заказа. После выплавки отбираются образцы продукции для контроля на соответствие спецификации, которые передаются в центральную контрольную лабораторию.
4. Результаты проведения анализа формируются в виде протокола испытаний, который передается в цех производства и отгрузки готовой продукции. Сертификатчики цеха вносят данные из протокола испытаний в сертификат качества.
5. Далее лаборатория вносит данные анализа в статистическую базу.
Контроль качества выпускаемой продукции еще называется металлографическим ана-лизом, который включает в себя несколько этапов. Среди них можно выделить контроль до-кументации на продукцию (спецификация, сертификат и т. д.), отбор проб для анализа, оп-ределение химических, механических, геометрических параметров пробных срезов. Состав анализа, перечень основных его этапов и их последовательность представлена на рис. 1.
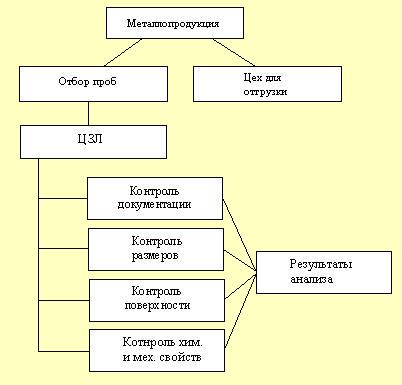 Рисунок 1. Типовая схема организации металлографического анализа.
Рассмотрим более детально последовательность проведения металлографического анализа. Основным этапом металлографического исследования является металлография – позволяет получить информацию о морфологии элементов структуры [2]. Этапы металлографии:
1. Электронная микроскопия. Для исследования металлов применяется обычно сканирующий электронный микроскоп, в котором пучок электронов с помощью системы развертки сканирует поверхность образца.
2. Микромеханические испытания. Основной характеристикой металлов и сплавов являются их механические свойства, т. е. способность выдерживать нагрузки и деформироваться. Разработано большое количество стандартных методов механических испытаний.
3. Выявление и определение величины зерна сплава. На этом этапе определяются:
- величина действительного зерна после горячей деформации или любой термической обработки;
- склонность зерна к росту – определение величины зерна после нагрева при температуре и времени выдержки, установленных нормативно-технической документацией на стали и сплавы;
- кинетика роста зерна – определение величины зерна после нагрева в интервале температур и времени выдержки, установленных нормативно-технической документацией на стали и сплавы.
Остановимся на этапе определения роста зерна. Любой метод этого этапа основывается на анализе микрофотографии среза пробы контролируемой продукции. Следовательно, прежде чем выполнять анализ фотографии, необходимо выполнить распознавание текстуры изображения.
Текстуры являются важной характеристикой изображений естественных объектов и важным элементом зрительного восприятия. Машинному анализу текстурных изображений посвящено значительное количество исследований, существенную часть которых занимает проблема сегментации изображений по текстурным признакам.
Для распознавания текстур металлографических изображений наиболее предпочтительно применение метода случайных Марковских полей [3,4]. Марковские модели являются мощным средством моделирования распознавания образов. По своей природе Марковские модели позволяют учитывать непосредственно пространственно-временные характеристики сигналов, поэтому они получили широкое применение в распознавании изображений.
Каждая модель представляет собой набор N состояний , между которыми возможны переходы. В каждый момент времени система находится в строго определенном стоянии. В наиболее распространенных Марковских моделях первого порядка полагается, что следующее состояние зависит только от текущего состояния. При переходе в каждое состояние генерируется наблюдаемый символ, который соответствует физическому сигналу с выхода моделируемой системы. Набор символов для каждого состояния – ,количество символов – М. Выход, генерируемый моделью, может быть также непрерывным. Существуют также модели, в которых набор символов для всех состояний одинаков. Символ в состоянии в момент времени t генерируются с вероятностью:
 Набор таких вероятностей составляет матрицу  Матрица определяет вероятность перехода из одного состояния в другое состояние:

Обычно в реальных процессах последовательность состояний является скрытой от наблюдений и остается неизвестной, а известен только выход системы, последовательность наблюдаемых символов .
В распознавании образов скрытые Марковские модели применяются следующим образом [3,4]. Каждому классу і соответствует своя модель . Распознаваемый образ представляется в виде последовательности наблюдений О. Затем для каждой модели вычисляется вероятность того, что эта последовательность могла быть сгенерирована именно этой моделью. Модель , получившая наибольшую вероятность, считается наиболее подходящей и образ относится к классу j.
На обучающем наборе каждая модель реагирует на изображения-примеры с некоторой вероятностью. Отсортированные таким образом модели образуют исходное ранжирование. Для неизвестного изображения модели также ранжируются по вероятностям отклика на неизвестное изображение. Большая величина отклонения полученного ранжирования от исходного сигнализирует о том, что изображение принадлежит к неизвестному классу.
В ходе работы было выяснено, что на металлургических предприятиях Донбасса для определения размера зерна применяется только один метод из 4 основных, описанных в ГОСТе 5639-82. Это метод визуального сравнения с эталонами шкал. Величину зерна определяют визуально при увеличении 100х. После просмотра всей площади шлифа выбирают несколько типичных мест и сравнивают их с эталонами. Этот метод не только не обладает достаточной точностью результата, но и значительно увеличивает процесса всего металлографического анализа.
Выводы
При анализе изображений важной их характеристикой служит текстура, которая присутствует во всех изображениях. Но, не смотря на это, концепция текстуры не очень хорошо определена и понимается даже сегодня.
Метод распознавания изображений был выбран на основе следующих преимуществ:
- математическая структура скрытых Марковских моделей очень богата и позволяет решать математические проблемы различных областей науки;
- грамотно спроектированная Марковская модель дает на практике хорошие результаты работы;
- преимущество модели состоит в том, что разметка и каждая текстура характеризуется своими Марковскими случайными полями, не зависящими друг от друга. Это позволяет легко модифицировать распознающую систему.
Наиболее важной проблемой в анализе и классификации изображения на сегодняшний день является классификация текстур, которые расположены под различными углами и в разном масштабе. Эту проблему также можно решить с помощью разновидностей Марковских моделей.
Также в работе обосновывается необходимость разработки данной подсистемы, несмотря на существование программных пакетов, которые решают проблему распознавания металлографических изображений.
|