Литература
Актуальность работы
Автоматизация управления технологическими процессами и производством играет важную роль в непрерывном увеличении выпуска продукции в нашей стране. Интенсификация и усложнение технологических процессов, рост единичной мощности агрегатов и повышение требований к качеству готовой продукции в соответствии с международными стандартами делают невозможным управление агрегатами без систем автоматизации.
В настоящее время производится комплексная автоматизация, при которой на автоматическое управление переводятся как основные, так и вспомогательные процессы, агрегаты, участки предприятия.
В нашей стране теоретическим и практическим вопросам автоматизации производственных процессов придается большое значение. Новые возможности для высокоэффективной автоматизации технологических процессов в металлургии открывают внедрения новейших приборов и средств автоматизации, автоматизированных систем управления технологическими процессами (АСУ ТП), применение микропроцессоров, микро-ЭВМ, робототехники. Поэтому для широкого внедрения автоматики необходимо знание основ автоматизации технологических процессов.
Обзор существующих решений
В настоящее время на большинстве нагревательных печей о температуре металла, находящегося в печи, в большинстве случаев судят по температуре рабочего пространства зон. Часто в одной зоне монтируют несколько чувствительных элементов датчиков температуры с целью контроля равномерности температуры зоны либо получения раздельных сигналов для измерения и регулирования.
Регулирование температуры осуществляется путем изменения тепловой нагрузки зоны. При этом в одних системах регулирования температуры зоны регулятор температуры управляет подачей топлива, а в других – подачей воздуха. В первом случае пропорционирование количеств топлива и воздуха достигается воздействием регулятора соотношения на подачу топлива, во втором – на подачу воздуха.
Одним из эффективных и доступных способов снижения удельных затрат тепловой энергии в металлургическом производстве является совершенствование управления процессом сжигания топлива в рабочем пространстве печей.
Известные в настоящее время системы регулирования соотношения топлива и воздуха делятся на разомкнутые и замкнутые.
Разомкнутые системы, обеспечивающие регулирование режима сжигание топлива на основе информации о расходах топлива и воздуха, подводимых к печи, имеют ряд недостатков, связанных с невозможностью учета выбивания воздуха из воздуховодов на участках, расположенных после измерительного устройства; невозможностью учета люфтов в сочленении регулирующего органа с исполнительным механизмом.
Замкнутые по регулируемой величине системы автоматического регулирования обеспечивают более высокое качество управления по сравнению с разомкнутыми системами, т.к. в них обеспечивается автоматическая компенсация всех возмущений и существует возможность оценить результат нанесения управляющих воздействий.
Одной из реальных возможностей построения замкнутой системы управления режимом сжигания топлива является использование автоматических газоанализаторов для контроля состава продуктов сжигания топлива.
Существенной особенностью устройств автоматического газового анализа является их значительная инерционность. Именно поэтому динамические характеристики замкнутых систем определяются инерционностью газового анализа и не соответствуют динамике режима сжигания топлива.
Для многозонных нагревательных пламенных печей построение замкнутой системы регулирования процессом сжигания топлива усложняется тем, что эти объекты имеют единую систему удаления продуктов сжигания из всех зон и весьма трудно определить по составу отходящих продуктов сгорания, в какой из зон произошло нарушение горения.
Наряду с системами, имеющими в своем составе газоанализатор, были предприняты попытки создания замкнутых систем экстремального регулирования. Теоретической предпосылкой для реализации таких систем является экстремальная зависимость температуры факела от коэффициента расхода воздуха в рабочем пространстве зоны печи. Однако практическое опробование такой системы обнаружило ее непригодность для эксплуатации из-за того, что автоматический оптимизатор не обеспечивал выделение полезного сигнала об изменении средней температуры факела на фоне случайных колебаний излучения факела и измеренные значения его температуры оказались соизмеримыми со средним изменением температуры факела, вызванным допустимым отклонением соотношения между расходами топлива и воздуха.
В силу перечисленных факторов, замкнутые системы автоматического регулирования режимом сжигания топлива в рабочем пространстве пламенных нагревательных печей широкого распространения не получили. В настоящее время основными являются разомкнутые системы управления режимом сжигания топлива, которые достаточно эффективно используются на нагревательных печах, оборудованных двухпроводными горелками типа «труба в трубе». Основным условием использования разомкнутых систем управления являются точный учет и компенсация всех внешних возмущений. Во-первых, необходимо свести к минимуму люфты в сочлени регулирующего органа с исполнительным механизмом или же предусмотреть алгоритмы, позволяющие их учесть. Во-вторых, необходимо ввести поправки в показания расходомеров для приведения измеренных величин к нормальным условиям при отклонении значений давления и температур газа и воздуха. При выполнении этих условий становиться очевидным известные преимущества разомкнутых систем, упрощается система автоматизации, ее надежность и эффективность. Удовлетворительное решение такой задачи стало возможным только при использовании средств цифровой вычислительной техники.
В настоящее время получили широкое распространение системы с реализацией прямого цифрового управления технологических параметров. Использование такого управления повышает точность реализации управляющих воздействий, способствует улучшению качества регулирования и снижает материальные затраты на создание технического обеспечения.
Постановка задачи
Задача оптимального управления технологическими объектами состоит в обеспечении такого ведения технологического процесса, который позволяет получить продукцию требуемого качества при минимальных удельных затратах. Однако эта задача не рассматривается в полном объеме, что объясняется трудностью и громоздкостью строгой математической постановки, которая усложняется еще и тем, что ряд важных параметров, влияющих на ход технологического процесса, являются случайными величинами. Применительно к задаче управления режимом сжигания топлива в пламенных нагревательных печах случайной величиной является, например, время пребывания металла в рабочем пространстве, т.е. время нагрева.
Исходя из того, что разрабатываемая подсистема управления режимом сжигания топлива будет работать в составе АСУТП участка нагревательных печей, то принципы оптимизации управления температурным режимом печей в данной работе не рассматриваются. Используется лишь имитационная модель нагрева металла для получения необходимых параметров нагрева для дальнейших расчетов. Также полагается, что распределение теплового потока вдоль рабочего пространства печи является оптимальным, и изменение температуры поверхности нагреваемых заготовок соответствует этому распределению.
Обычно управление режимом сжигания топлива сводят к решению задачи о полном его сжигании в зонах печи, а качество этого процесса оценивают по энергетическим параметрам: температуре газовой среды, тепловому потоку на металл или теплопоглощению металла, исходя из того, что зависимость этих параметров от коэффициента расхода воздуха (
) носит экстремальный характер. Т.е. теоретический максимум характеристики приходится на значение
, равное 1.0, соответствующее полному сжиганию топлива. Как показывают исследования, максимальная температура в зонах печи, при сжигании газообразного топлива, достигается при значениях
, равных 1.05-1.15, из-за различных условий смешения топлива и воздуха в горелках различного типа и из-за разного теоретического количества воздуха, необходимого для полного сжигания различных видов газообразного топлива. С другой стороны, в пространстве зон печи присутствует избыточный атмосферный воздух, проникающий из окружающей среды через окна посада и выдачи (в прямоточно-противоточных печах эти участки рабочего пространства характеризуются пониженным значением внутреннего давления), а также через элемент кладки. Поэтому считается, что в реальных условиях полное сжигание топлива достигается при
, равном 1.0, что соответствует теоретическому значению.
Однако коэффициент расхода воздуха влияет не только на теплообмен, но и на массообмен в печах: изменение величины
сопровождается изменением печной атмосферы. При
в печи создается восстановительная атмосфера, а при
- окислительная, которая приводит к повышенному окислению металла и существенному ухудшению экономических показателей работы агрегата. Практическую ценность представляет только та постановка задачи оптимального управления, которая учитывает окисление метла, хотя не всегда потери от окалинообразования превосходят затраты на топливо. Очевидно, что имеется наилучшая комбинация управлений (т.е. расходов топлива и воздуха по зонам), при которой соблюдается заданный температурный режим нагрева и минимизируются затраты на топливо и окалинообразование.
Учет влияния предыдущих зон сжигания топлива на оптимальное значение коэффициента расхода воздуха
в рассматриваемой зоне
При рассмотрении значений
в реальном ходе технологического процесса, необходимо учитывать состав и количество продуктов сжигания, поступающих в рассматриваемую зону из предыдущей или предыдущих зон, т.к. значения
для различных зон различны.
Описанную коррекцию удобно проводить в последовательности, обратной ходу технологического процесса (т.к. отвод продуктов сжигания топлива осуществляется в промежутке между методической и первой сварочной зонами). Удобство заключается в том, что продукты сжигания топлива, покидающие томильную зону, состоят из продуктов сжигания топлива, подведенного только в это зону. Очевидно, что при рассмотрении томильной зоны коррекция не требуется. При рассмотрении процессов во второй сварочной видно, что продукты сжигания, уходящие из нее будут состоять из суммы продуктов сжигания газа в этой зоне и продуктов сжигания газа, поступающих из томильной зоны.
Причем их количество будет равно их сумме, а химический состав будет зависеть от значения коэффициента расхода воздуха, реализуемого в этих зонах. Таким образом, для того, чтобы суммарный состав продуктов сжигания топлива находящихся в пространстве второй сварочной зоне соответствовал бы составу, получаемому при реализации значения
для этой зоны, необходимо скорректировать это значение с учетом количества и состава продуктов сжигания, поступающих из предыдущей (в данном случае, томильной) зоны.
Для коррекции значения
в рассматриваемой зоне необходимо знать химический состав топлива и состав продуктов сгорания при различных коэффициентах расхода воздуха.
Алгоритм расчета корректируемого значения коэффициента расхода воздуха
выглядит следующим образом:
-определение значения
в рассматриваемой зоне (в качестве примера, второй сварочной зоны);
-на основании этого значения и величины расхода газа в рассматриваемой зоне определяют удельное количество продуктов сжигания топлива и абсолютное значение этой величины -
;
-на основании этого значения и величины расхода газа в предыдущей зоне и значении
, определяем удельное количество продуктов сжигания топлива
;
-составляем уравнение материального баланса в виде:
(1)
При этом возникает погрешность, т.к. количество продуктов сжигания топлива образовавшегося в рассматриваемой зоне при оптимальном значении коэффициента расхода воздуха принимается равным количеству продуктов сжигания топлива, образованному в этой же зоне при скорректированном значении коэффициента расхода воздуха. Эту погрешность можно уменьшить методом последовательных приближений. Уже на втором шаге итераций она не превышает 1%;
-определяем скорректированное значение
из уравнения (1):
Это же значение используется как первое приближение в итерационном методе, и после второго шага принимается как требуемое значение, при реализации, которого в рабочем пространстве второй сварочной зоны, в ней установится такой химический состав продуктов сжигания топлива, который соответствовал бы реализации
при автономном рассмотрении процессов, протекающих в ней.
Переходя к первой сварочной зоне необходимо учитывать, что количество продуктов сжигания уходящих из нее равно сумме продуктов сжигания в этой зоне и суммарному поступлению из второй сварочной и томильной зон.
Значение величины
корректируется здесь аналогично вышеописанному алгоритму. Данный алгоритм коррекции значения
может функционировать в подсистеме управления режимом сжигания топлива в реальном масштабе времени.
Описание результатов и планы на будущее
В объектно-ориентированной среде программирования Borland C++ Builder 6.0 была составлена программа, которая обеспечивает расчет состава продуктов полного/неполного сгорания топлива, нагрева металла, составляющих теплового и эксергетического балансов, поиск и коррекцию оптимальных значений коэффициентов расхода воздуха по зонам печи.
Расчет производился исходя из технологических характеристик семизонной методической печи с шагающими балками ЛПЦ «3000» ОАО «ММК им. Ильича». Коэффициент расхода воздуха изменялся в диапазонах 0,7..0,9 и 1,0..1,2 с шагом 0,05, а в диапазоне 0,9..1,0 с шагом 0,01.
Результаты расчета одномерной двусторонней модели нагрева металла приведены на рисунке 1.
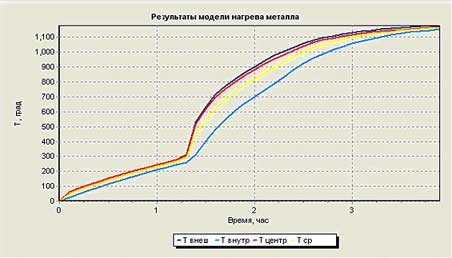
Рисунок 1 – Результаты расчета модели нагрева
Расчет составляющих теплового и эксергетического балансов произведен для зон методической печи. Рассмотрим результаты моделирования на примере первой сварочной зоны. Для нее в таблице 1 сопоставлены энергетический и эксергетический балансы при коэффициенте расхода воздуха 0,98.
Таблица 1 – Энергетический и эксергетический балансы (
)
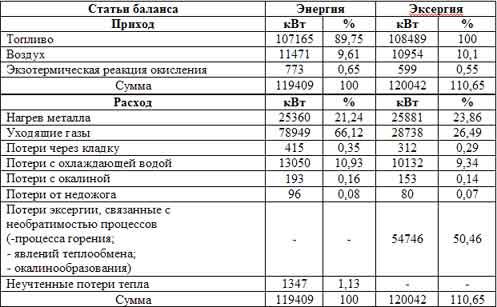
На рисунке 2 дано графическое представление данного баланса, составленное в соответствие с таблицей 1.
Сопоставление двух балансов позволяет сделать вывод, что в эксергетическом балансе оценка отдельных составляющих существенно отличается от соответствующей оценки составляющих в энергетическом балансе. Прежде всего, отметим, что в эксергетическом балансе продукты горения представлены меньшими величинами, чем в энергетическом. Энергия, переносимая потоком продуктов горения, количественно значительно меньше, чем химическая энергия топлива.
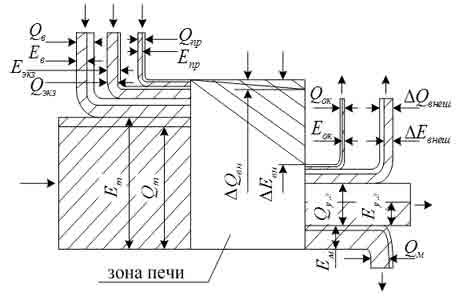
Рисунок 2 – Сравнительный баланс энергия-эксергия для первой сварочной зоны методической печи
В энергетическом балансе не видно влияния многих факторов, снижающих совершенство процесса. В частности, в статье расхода весьма существенны потери эксергии, связанные с необратимостью процессов. Тщательный эксергетический анализ позволяет обнаружить источники этих потерь и пути их понижения.
Так, например, эксергию покидающих печь продуктов сгорания можно уменьшить за счет рекуперации (благодаря рекуперации снижается температура уходящих продуктов сгорания), потери эксергии при необратимом сжигании можно уменьшить путем обогащения воздуха кислородом и подогрева составляющих (при подогреве воздуха уменьшается количество продуктов сгорания за счет уменьшения количества топлива).
В эксергетическом балансе, так же как и в энергетическом, не видно, непосредственно, то большое влияние, которое подогрев воздуха оказывает на расход топлива.
В работе были проведены несколько сравнительных экспериментов для исследования зависимости эксергетических потерь и расхода топлива от температуры подогрева воздуха. Результаты приведены на рисунках 3 и 4.
Из рисунка 3 видно, что с увеличением температуры подогреваемого воздуха расход топлива, подаваемого на зону, уменьшается, что позволяет его экономить. В результате подогрева воздуха уменьшается не только температура продуктов горения, уходящих в окружающую среду, но также и их количество (благодаря уменьшению количества топлива).
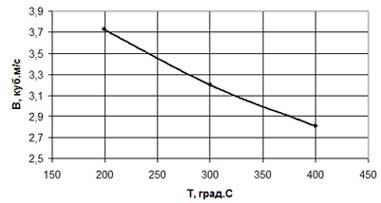
Рисунок 3 – Зависимость расхода топлива от температуры для первой сварочной зоны методической печи
При эксергетическом анализе проявляется дополнительный полезный эффект, а именно, уменьшение потерь эксергии, вызываемых необратимостью горения, что ярко отражено на рисунке 4.
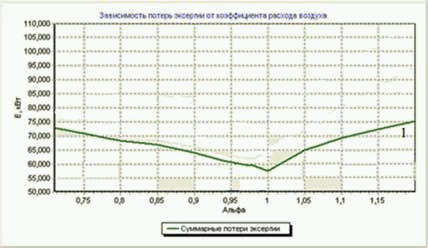
Рисунок 4 – Зависимость суммарных потерь эксергии от коэффициента расхода воздуха при различных температурах подогрева воздуха (1 - 400 C, 2 - 300 C, 3 - 200 C).
Однако, эксергия является величиной термодинамической, а не экономической. Поэтому при анализе работы технологических объектов необходимо оценивать потери, как с термодинамической, так и с экономической точки зрения. В связи с этим, необходимо составить эксерго-экономическую функцию, которая учитывает стоимости топлива и нагреваемого в печи металла, стоимостную меру ущерба от окисления металла и потери эксергии, и осуществить ее минимизацию. Результат составления данной функции будет отображаться графиком.
Литература
1. Автоматизация методических печей. Буглак Л. И. М.: “Металлургия”, 1981.
2. Глинков Г.М., Маковский В. А. АСУ ТП в агломерационных и сталеплавильных цехах. М.: Металлургия, 1981.
3. Проектирование систем контроля и автоматического регулирования металлургических процессов: Учебное пособия для ВУЗов / Глинков Г.М., Маковский В.А., Шапировский Р.М. и др. 2-е издание, переработанное и дополненное М.: Металлургия, 1986.