M.L. Camara, V.V. Dorokhov (UGANC, Conakry, République de Guinée)
E. Sydorova, V.A. Bogouslavskiy (UNTD, Donetsk, Ukraine)
(«Monde scientifique et technique à travers des recherches des étudiants». Випуск 3. – Донецьк: ДонНТУ, 2006, p.73-80)
L’article exploite le pouvoir du plan régulier à plusieurs variables pour déterminer l’influence des 5 facteurs technologiques sur 6 paramètres de qualité de surface afin d’optimiser l’aptitude au service d’une pièce cylindrique en acier non allié mi-dur usée, rénovée à l’aide des couches d’Al2O3 déposées par la méthode de détonation et usinée par la rectification.
1. INTRODUCTION
Le rétablissement des surfaces usées par apport des matériaux additifs est une activité très
complexe. Une bonne cohésion des couches déposées associée au durcissement superficiel se réalise
par détonation des poudres dures [1-3]. La finition des surfaces rétablies par cette méthode
s’effectue de préférence par rectification, dont les conditions optimales sont encore insuffisamment
étudiées. Le but du présent travail est l’étude expérimentale de l’influence des conditions de rectification
des dépôts d’alumine sur l’état de surface et la détermination des meilleures conditions de
rectification des pièces recouvertes. L’utilisation de l’alumine dans cette recherche présente un intérêt
particulier pour la Guinée comme pays producteur de l’alumine.
2. PARTIE EXPERIMENTALE
2.1. Matériaux et matériel
Les échantillons cylindriques à recouvrir sont en acier au carbone C45 trempé et revenu au
préalable jusqu’à 42...45 HRC. La poudre d’alumine (pureté 99,3%, granulométrie < 0,15 mm et
densité 0,98 g/cm3) mélangée avec des gaz combustibles et comburants a été projetée au moyen
d’un appareil appelé complexe détonateur. La rectification des échantillons s’est effectuée sur la
rectifieuse cylindrique de précision 3A151 garantissant la circularité jusqu’à 0,8 μm. Les mesures
de rugosité ont été réalisées à l’aide du profilographe, permettant de révéler plusieurs caractéristiques
de rugosité dans des larges intervalles.
2.2. Méthode d’expérimentation et réalisation des expériences
Vu la complexité de l’objet d’étude [4], l’expérimentation a été basée sur les principes des
plans d'expériences [2, 5] qui donnent les meilleures conditions pour l’optimisation et réduisent
considérablement le nombre d’expériences.
Le paramètre à optimiser dans la présente recherche est la rugosité qui se caractérisent par
6..10 paramètres selon les normes nationales. On a retenu comme les paramètres d’optimisation
y1...y6 toutes les six caractéristiques de rugosité prévues dans les normes GOST: trois paramètres
d’amplitude Ra, Rz, Rmax et trois paramètres de pas S, Sm, Tp (p=30%). Les paramètres cités se
définissent simultanément à partir d’un diagramme tracé par profilographe.
La rugosité d’une surface rectifiée est définie par plusieurs conditions technologiques parmi
lesquelles on a choisi pour optimiser 5 principaux paramètres (facteurs contrôlés ou variables): x1 -
profondeur de passe (P); x2 – avance de la pièce (A); x3 - marque de la meule (ME); x4 - vitesse de
la pièce (VP) et x5 - marque du réfrigérant (RE). La vitesse de la meule était constante Vm = 27 m/s.
Les limites choisies de variation des facteurs recouvrent leur domaine d’utilisation le plus pratiqué
(tableau 1). Pour les deux facteurs qualitatifs on a retenu:
les meules plates en carbure de silicium 63C et diamant artificiel AC avec la grosseur du grain
de 40 à 160 μm, le grade tendre M3 et la structure ouverte 9 pour l’agglomérant vitrifié K10;
- les émulsions réfrigérantes de marques Acvol10 (A10), Akvémous (Ak), Ykrenol1 (Ukr1) et
OSM1
Tableau 1 – Niveaux de facteurs et intervalles de leur variation
Le modèle présumé du processus dans le domaine expérimental étant non linéaire, donc on a
choisi 4 niveaux de facteurs qui sont présentés dans le tableau 1 sous une forme codée: -3, -1, +1, +3.
Un plan complet classique à 4 niveaux pour 5 facteurs nécessite 45 = 1024 expériences, sa
réalisation étant irréelle donc on a recouru à un plan fractionnaire [6] faisant 1/64 fraction du plan
complet 45 désigné 45-3 qui ne requiert que 16 essais, ce qui correspond au nombre des coefficients
b0...biii de régression prévisionnelle du 3-ème degré sans interactions entres les 5 facteurs:
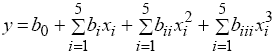
Deux facteurs dans ce modèle mathématique sont qualitatifs (marques de meule et de réfrigérant),
ce qui nécessite le codage de leur fonction non linéaire. Les niveaux codés des facteurs xi
sont désignés successivement: -3, -1, +1, +3. Les niveaux des fonctions quadratiques qi et cubiques
ci pour chaque facteur xi sont codés au moyen des formules données dans le tableau 2.
Tableau 2 – Codification des niveaux de facteurs
La matrice du plan d’expériences retenue est représentée dans le tableau 3 sans facteurs dépendants
(fonctions quadratique et cubique des facteurs contrôlés xi.). Ce plan fractionnaire répond
aux exigences d’orthogonalité et de symétrie. Il est légèrement sursaturé car le nombre de coefficients
recherchés (16) est supérieur au nombre d’expériences plus 1 (N+1=17).
Tableau 3 – Matrice du plan d’expériences et résultats obtenus
L’ordre de réalisation des expériences (colonne 2 du tableau 3) était arbitraire (randomisation)
avec 4 échantillons pour chaque essai, donc les paramètres de rugosité sont définis par les
moyennes arithmétiques de 4 échantillons.
3. TRAITEMENT DES RESULTATS ET LEUR INTERPRETATION
L’analyse du plan d’expériences réalisé s’est effectuée à l’aide du logiciel «Statistica 99»
élaboré par StatSoft Inc (USA). Avec son module de régression multiple et la méthode «pas à pas
ascendante» on a établi les coefficients de régression (tableau 4) pour le niveau de confiance fixé à
95 % (1-p = 0,95).
Toutes les dépendances de régression obtenues se caractérisent par une bonne corrélation
dont le coefficient est toujours supérieur à 0,999. Une bonne adéquation des modèles obtenus était
aussi prouvée par réparations aléatoires des résidus autour de la ligne de régression. Selon la matrice
de corrélations, les effets cubiques les plus forts exercent ME3, P3, VP3 et RE3 sur tous les paramètres
d’amplitude, mais pour le taux de longueur portante Tp (p=30%), qui caractérise très bien
la surface réelle de contact de pièces conjuguées, les fonctions cubiques les plus corrélées sont ME3,
RE3, A3 et VP3. Pour les pas du profil Sm et S les facteurs signifiants ne sont que la marque de la
meule ME et la vitesse de rotation de la pièce VP.
Tableau 4. Coefficients de régression et de corrélation des modèles mathématiques
L’interprétation des modèles mathématiques établis qui sont toujours de l’ordre 3, prévoit
quelques étapes. D’abord on peut constater selon les grandeurs des coefficients de régression que
les facteurs les plus influençant sont: la marque de la meule, la profondeur de passe et la vitesse de
la pièce. Puis, avec les équations de régression obtenues on a simulé les paramètres d’état de surface
y1...6 pour toutes les 1024 combinaisons possibles des conditions de coupe dans le domaine étudié.
Les tableurs simulés permettent facilement de procéder à l’optimisation du régime de coupe et à la
visualisation des effets des facteurs.
Sur les figures 1...8 sont présentés certains graphiques de surface Ra et Tp construits pour 2
facteurs variables et 3 autres facteurs fixés aux niveaux les plus favorables.
Les valeurs optimales de ces facteurs sont différentes pour:
- minimiser Ra: P = -3 et +1 A = -3 ME = +3 et -1 VP = - 1 RE = -3
- maximaliser Tp: P = -3 A = +1 ME = -1 VP = +3 RE = +1
Les figures 1-4 montrent qu’il existe un minimum local de Ra pour la meule ME=-1. Cette
marque de la meule (SiC, taille 120 μm) peut être recommandée pour la finition (F), tandis que la
meule la plus fine en diamant de taille 40/28 μm (ME=3) manifestant toujours un minimum global
de Ra est raisonnable en cas de superfinition (S/F). On ne recommande pas la meule en diamant de
taille 100/80 μm (ME=1), conduisant toujours à l’augmentation de Ra.
L’influence pareille avec deux minimums de Ra est exercée par P (-3 et 1 sur figures 1, 5) et
RE (3 et -1 sur figure 4). Les graphiques 2, 5 et 6 montrent que la vitesse de la pièce VP correspondant
au minimum de Ra est égale à 33 m/min (VP= -1).
Une manifestation de l’influence naturelle, c’est à dire, de manière progressive est exercée par
l’avance A sur Ra (figures 3 et 6) et par la profondeur P avec la vitesse VP sur Tp (figure 8). La profondeur
de passe P = 0,015 mm, assurant un débit de coupe élevé, est recommandée pour la finition,
mais le meilleur fini (Ra min) est garanti par la plus faible pénétration P=0,005 mm (figures 1, 5).
La nature du réfrigérant joue un rôle peu important, néanmoins on peut recommander deux
marques suivantes: Acvol10 (RE=-3), et Ykrenol1 (RE=1)
Il est à noter que certaines conditions technologiques de rectification (A, VP et RE) sont différentes
pour optimiser les deux paramètres de rugosité: Tp et Ra. On peut constater aussi que
l’augmentation de l’avance jusqu’à 0,15 m/min pour l’optimum de Tp (figure 7) est avantageuse du
point de vue de la productivité de coupe.
4. CONCLUSION
Du point de vue des principaux paramètres d’état de surface, la rectification cylindrique des
pièces recouvertes d’alumine est recommandée avec les conditions de coupe suivantes:
Tableau 5 – Paramètres de rectification recommandés
La technologie de rétablissement des pièces mécaniques par projection des couches de poudres
d’oxyde d’aluminium suivie d’une rectification peut trouver une large application en Guinée
pour les pompes HMDA [7], surtout pour les axes et les bras de la charnière et de la tringle.
Références bibliographique:
- Рыжов Э.В., Суслов A.Г., Федоров В.П. Технологическое обеспечение эксплуатационных свойств деталей машин. – М.: Машиностроение, 1979.-176с.
- Душинский В.В., Пуховский E.С., Радченко С.Г. Оптимизация технологических процес-
сов в машиностроении.- К.: Технiка, 1977.-175 с.
- Новиков И.В.. Восстановление деталей дорожных машин.- М : Транспортные машины,
1965.-147 с.
- Новоселов Ю.K. Динамика формообразования поверхностей при абразивной обработке.
- Саратов: Изд-во Сарат. ун-та, 1979.-231 с.
- Plans d'expériences. Applications à l'entreprise. Saporta G., Droesbeke J.-J., Fine J. Editions
TECHNIP. 1997.-528 p.
- Plans d'expériences. Applications à l'entreprise. Saporta G., Droesbeke J.-J., Fine J. Editions
TECHNIP. 1997.-528 p.
- Бродский В.З., Бродский Л.И., Голикова Т.И. Таблицы планов эксперимента для фактор-
ных и полиноминальных моделей.- М.: Изд-во МГУ, 1982.-749 с.
- Camara M. L. Brevet d’invention N10004 OAPI. Dépôt N° PV 002 du 17 Février 1994,
Yaoundé Cameroun, publication le 29 mars 1996.- 8 p.
|
|