|
Introduction
Transport chain pulling body
represented a wide variety. This includes pipes of different
lengths used in the mining industry and in agriculture, grain
elevators, all kinds peregruzhateli; conveyors snow, road
construction, mining and other machinery.
The most responsible and demanded the vehicle with the chain
pulling authority on the territory of Ukraine is a bottom
scraper conveyor. Also, it is the conditions of the downhole
scraper conveyors are the most difficult due to high loads, the
aggressiveness of the environment in which it operates.
Scraper bottom line has a great impact on the continuity of the
mechanized sector, which accounts for 55% of the total duration
of outages lava. Of these, 50% of outages occur due to the fault
of scraper conveyor. Troubleshooting-related downtime scraper
conveyor is one of the most labor intensive, with 53% of the
total labor accounted for troubleshooting related to the
traction chain. Thus, increasing the durability of the traction
chain, as well as improving its operating performance will
improve the sustainability of the mechanized sector, which has a
positive impact on productivity. In many cases the causes of the
dynamic loads are oscillatory processes resulting kinematics
gearing Star - chain. Especially dangerous oscillatory processes
causing resonance.
Analysis of
publications
The wide
introduction of conveyor belts in coal mines contribute to the
scientific, experimental and design work performed by the
research, engineering and training institutes.
Of paramount importance
in the development of konveyerostroeniya are works on the
theory, design, maintenance of conveyors Corresponding Member
Kor. Of USSR prof. AO Spivakovsky, a founder of Russian school
on the conveyor transport. A great contribution to science made
by underground conveyor transport of the academician of USSR
prof. NS Polyakova, as well as a number of other Soviet foreign
scientists.
As a result of efforts
uchenyx, research institutions and groups of plants are now
fully konveyerizirovan transport coal from the faces, which is
mainly used scraping conveyors.
In response to the
increasing concentration of coal mining on a small number of
sites of high losses in production at one site as a result of
any accident, for example, due to break the chain, significantly
increased, even with short duration outages. Reasons for
withdrawal of the circuits are very different, but the chain of
unacceptable or destroyed under the influence of frequently
repeated moderate dynamic loads.
Dynamics conveyor chain
pulling body began to develop in the 30-ies of the XX century.
G. Ganfshtengelem was obtained Analytical dependence for
determining the dynamic forces on the towing authority conveyor
[4], in which the value of the dynamic forces provided directly
proportional to the square of the speed of the conveyor. Later
it turned out that the proposed theory is valid only for small
slow-moving conveyor.
In the late 40-ies of the
AO Spivakovsknm and VD Kruzhkovym studies have been carried out
dynamic efforts in the towing body scraper conveyor.
Oscillograms obtained from measurements of effort using load
cells showed that the frequency variations in tractive effort is
proportional to the chain of stars at the turn of one tooth, and
the amplitude of oscillation depends on the pre-tension the
chain. At the same time, study AA Dolgolenko, which was first
considered as a traction chain conveyor system with distributed
parameters showed a significant effect of dynamic
characteristics of the traction on the vibrational processes
[5]. As a result, he had proposed a method of determining
dynamic forces in the traction chain according to their elastic
properties. The theoretical study A. A. Dolgolenko played a
crucial role in the development of the theory with the conveyor
chain pulling body.
The most complete study
of the dynamics of the traction chain scraper conveyors, as
validated by numerous experimental data, were conducted IG
Shtokman [6]. As a result, have developed the theory of the
dynamics of the traction circuit and the calculation of the
dynamic efforts and recommendations on the choice of parameters
scraper conveyor.
Dynamics scrapers, plate,
and band-chain conveyors with the influence of dissipative
forces was investigated in the works of C. Sc. In. K. Smirnov.
r. Sc. VP mole [7], D. M, Belenky [8, 9] and the Professor. VN
Matsenko [10].
A topical issue
The coal industry is the basis for a long
period the economy not only to the Donetsk region, but the whole
of Ukraine. Coal is one of the main natural wealth of our nation
and is the main source of energy independence of Ukraine. To
maintain the competitiveness of coal compared to other more
efficient fuels such as oil and natural gas, the energy market
to representatives of Ukrainian industry and research
institutions have to constantly improve the mechanical
installation for the extraction of coal, while addressing issues
to increase their productivity, reliability and durability, as
well as reduce costs, which in turn reduces the cost of coal.
In modern conditions of production of coal scraper conveyor is
an indispensable means of transportation of coal by Lava. It is
in Lava most difficult conditions of transportation of goods,
which include: a wet environment, the aggressiveness of water
and air, in some cases even the presence of wandering currents,
as well as the lack of working space. In addition, downloading
repelled lumps of coal in the vehicle provides a high strength
construction. From the standpoint of ensuring the completeness
of the above requirements scraper conveyor is the only and
indispensable vehicle with coal. However, in terms of longevity,
continuity and economy of metal scraper conveyor has a mass of
deficiencies, a decision which will significantly improve
conditions for the operation of the conveyor, as well as lead to
a reduction in the cost of coal.
Goal and
objectives
The aim of this work
is the identification and assessment of the significance of the
criterion of resource traction harmonics of perturbations in the
drive sprocket scraper conveyor.
To achieve this goal the following basic tasks:
- Examine the kinematics of linking ring chain with a star and
to determine the source of forced oscillations of the chain;
- To develop a universal algorithm for the decomposition of
periodic functions in Fourier series in MathCAD, to obtain
spectra of frequencies of forced oscillations for different
models of conveyors;
- Get a number of frequencies of the main tone and overtones
subsequent natural oscillations in the case of a particular
line:
- Compare the obtained spectrum of its own and forced
oscillations, and to identify the frequency at which resonance
is possible, assess the resource chain considered modes.
Main part
There are several causes of dynamic loads in the chain
conveyor. One of these causes is the uneven movement of the
chain, the resulting kinematics links (Figure 1).
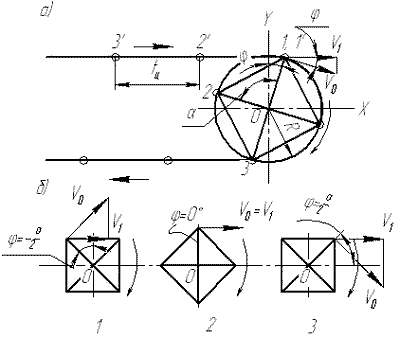 |
Figure 1 Kinematic scheme linking.
|
Figure 2 presents a spatial
model of engagement, which was built in solid modeling КОМПАС.
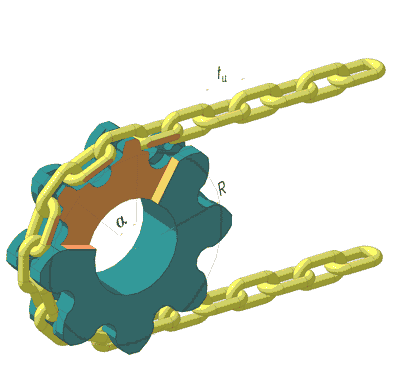 |
Figure 2 Spatial pattern linking
the chain with a star. |
Figure 3 shows the diagram of change of speed and
acceleration of the traction circuit
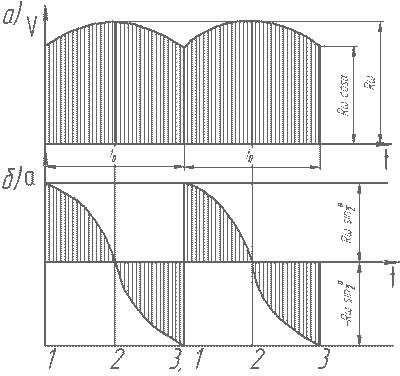 |
Figure 3 Diagram of velocity and acceleration of
the traction circuit. |
Kinematics linking showed that the function of velocity and
acceleration of the traction chains are periodic functions.
And, any periodic function can be represented as a sum of
several harmonics of the function [15]. Analyzing the
dependence for determining the dynamic loads [1], we can
conclude that the fluctuations of the chain drive asterisks
occur under the law of acceleration. Therefore, you need to
consider a series of harmonic functions of acceleration,
which is typical range of frequencies. Getting a series of
harmonic functions is based on accelerating the expansion of
this function in a Fourier series according to [15]
|
(1) |
The result of the decomposition are graphics acceleration
functions (Figure 4).
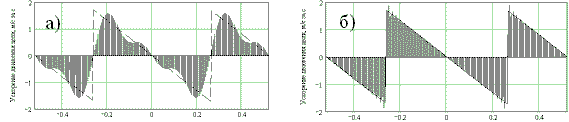 |
Figure 4 Result of approximation on
the example of accelerating conveyor
СPC 151 when the number of harmonics: K = 3
(a) and K = 30 (b). |
Also, using the dependence (2), we
obtain the frequency spectrum, the respective harmonics.
|
(2) |
Figure 5 shows the histogram frequency circuit
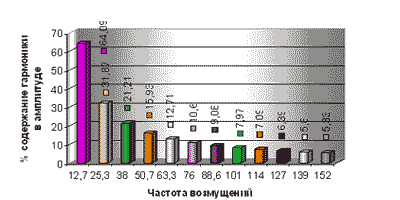 |
Figure 5 The parameters of some
harmonics
Conveyor SPC 151. |
The entire spectrum of their own ("с")
and forced ("в") oscillation is given
in Figure 6
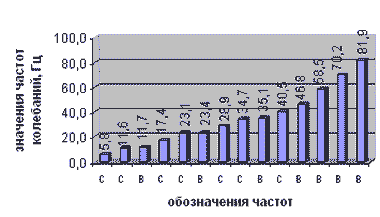 |
Figure 6 The frequencies of its
own and forced
fluctuations of the chain conveyor SPC 26. |
Below are charts of dynamic loads for different working
conditions conveyor (Figure
7).
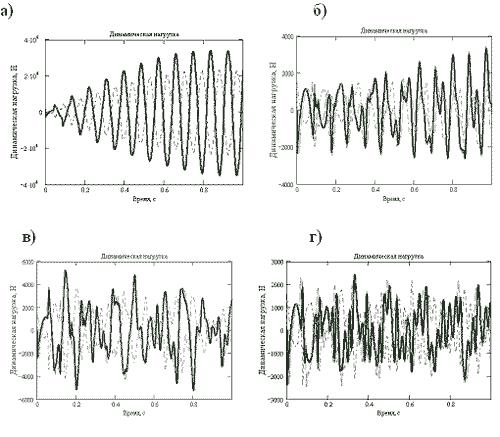 |
Figure 7 Dinamics load at
lengths conveyor 27 m(а),
54 m(б),
36 m(в) и 46
m(г). |
CONCLUSION
Substantiated the significant role of
external perturbations to drive the star scraper conveyor at
nabeganiya chain in the formation of dynamic loads on the
traction circuit. Identified the source of external
disturbances and the need to examine the whole spectrum of
frequencies, as well as their impact on the resource chain.
Now Master's work is still incomplete and
will be amended and submitted to the protection in December
2009.
REFERENCES
1.
Проектирование и конструирование транспортных машин и
комплексов: Учеб. для вузов / Под ред. И. Г. Штокмана. –М.;
Недра, 1986 - 392 с.
2. Штокман И. Г., Эппель Л. И. Прочность и долговечность
тяговых органов/ М.; Недра, 1967, 231с.
3. Галкин Н. А. Усилия в звеньях тяговой цепи на
звёздочках скребкового конвейера/ Известия вузов. Горный
журнал, 1981, №3, с. 76-79.
4.
Галфштенгель Г. Механизация транспорта массовых грузов. Ч.
I-М.
Госмашметиздат 1934
- 295 с.
5.
Долголенко А. А. Динамические усилия в замкнутых тяговых
органах подъёмно – транспортных машин.—В кн.: Новая подъёмно
– транспортная техника. М., Машгиз, 1943, с. 51 —6.1
6.
Штокман И. Г. Динамика
тяговых цепей рудничных
конвейеров М., Углетехиздат, 1969
- 290 с.
7. Смирнов В. К., Крот В. П. О динамическом расчете
скребкового конвейера.—В кн.. Вопросы рудничного транспорта,
М., Недра, 1965 №9, с.91-104
8. Беленький Д. М. Магистральные конвейеры.
M.,
«Недра», 1965 - 220 с
9. Беленький Д.
M..
Пластинчатые конвейеры. М., «Недра». 1971
- 183 с.
10. Маценко В. Н. Моделирование тягового органа цепных
конвейеров— В кн. : Разработка месторождений полезных
ископаемые №3, Киев, «Техника». 1965
- 326 c.
11.
Михайлов Ю. И., Хван А. П., Терещенко В. Н. Параметрические
колебания тяговой цепи конвейера/ Изв. вузов. Горный журнал,
1984, №4, с.65 – 68
12.
Чугреев Л. И. Динамика конвейеров с цепным тяговым органом/
М., Недра, 1976 - 162с.
13.
Берман А. В. Методика оценки
динамических нагрузок в тяговом органе.
14.
Спиваковский А. О. Общая теория конвейеров.
Учебное пособие, М. 1964
- 68 с.
15. Корн Т. М., Корт Г. А. Справочник по математике для
научных работников и инженеров/
«Лань»,
2003 – 832 с.
16.
Хорин В. Н. Скребковые забойные конвейера. М., Недра 1981 -
159 с.
|
|