Система Lean production и возможности ее применения в Украине
Введение
В последние годы в Украине, как и в странах бывшего Советского Союза, существенно возрос интерес к вопросам менеджмента, управления предприятиями, преобразованиям организационных структур компаний. К сожалению, этот интерес проявился лишь в последнее время.
В мировой практике за последнее время было создано множество новых концепций и методов менеджмента: реинжиниринг бизнес-процессов (BPR), Всеобщее Управление Качеством (TQM), сбалансированная система показателей (BSC), статистическое управление процессами (SPC), коучинг, модели международных стандартов ИСО 9000, ИСО 14000, ХАССП, «Пять S», «Шесть сигм» и многое другое. К сожалению, страны постсоветского пространства не имеют своих разработок в этой отрасли. Нет традиций, школ, опыта предшественников, нет налаженных систем менеджмента. Поэтому украинским управленцам предстоит многое освоить из зарубежных методик, чтобы выжить и сохранить конкурентоспособность.
Концепция «Бережливое Производство и Мышление» (Lean Thinking and Manufacturing) занимает одно из наиболее видных мест среди современных предложений по менеджменту.
Однако культура нашей страны в целом очень далека от понятия «бережливость». Об этом может свидетельствовать то, что у нас стружка хранится в цехах, а заготовки металла – на открытом воздухе; заборы строятся из натурального дерева, а мебель – из опилок; один цех находится в нескольких километрах от другого. Честно говоря, найти разумное объяснение этому невозможно [1].
Конкурентное преимущество украинских предприятий может быть обеспечено только высоким качеством и низкими издержками. Поэтому сегодня нужно пересмотреть всю организацию производства с тем, чтобы исключить все виды потерь. При этом еще раз хочется подчеркнуть необходимость интегрированного подхода, включающего качество и концепцию, методы и инструменты бережливого производства [1].
Исходя из проблематики функционирования украинских предприятий, специалисты в области менеджмента качества считают, что освоение концепции бережливого производства и применение ее методов является чрезвычайно важным фактором для улучшения деятельности всех звеньев производственной системы [1].
Целью данной работы является раскрытие сущности концепции бережливого производства, а также анализ возможностей внедрения и функционирования бережливого производства на предприятиях Украины.
История возникновения системы
«Бережливое производство» – японская технология менеджмента, это философия организации и ведения бизнеса, которая вбирает в себя практически все аспекты деятельности компании, включая стратегическое развитие и управление маркетингом [2].
Отцом-основателем бережливого производства считается Тайити Оно (1912 – 1990), начавший работу в Toyota Motor Corporation в 1943 году, интегрируя лучший мировой опыт. В середине 1950-х годов он внедрил систему TPS (Toyota Production System), которая в западной интерпретации стала известна как Lean production, Lean manufacturing, Lean. Идеи Lean были высказаны еще Генри Фордом, но они не были восприняты бизнесом, поскольку значительно опережали время [2].
Сначала Lean применяли в отраслях с дискретным производством, прежде всего в автомобилестроении. Затем концепция была адаптирована к условиям непрерывного производства, а потом ее стали внедрять в торговле, сфере услуг, коммунальном хозяйстве, здравоохранении, вооруженных силах и государственном секторе.
Постепенно Lean вышел за рамки предприятия. Теперь Lean охватывает потребителей его продукции, поставщиков. Во многих странах распространению бережливого производства оказывается государственная поддержка [2].
Цель концепции «бережливого производства» – избавиться от всех видов потерь и добиться максимальной эффективности использования ресурсов.
Особенность концепции «бережливого производства» – поступательное и непрерывное совершенствование всех бизнес-процессов организации, направленных на повышение удовлетворенности клиента.
Подход концепции «бережливого производства» – использование здравого смысла в организации функционирования предприятия.
Суть концепции бережливого производства
Основная идея этой концепции заключается в следующем: если какое-то действие, операция или процесс не добавляет ценности продукту с точки зрения клиента, то это действие, операция или процесс рассматриваются как потери, то есть приносящие убытки компании. Причем все потери делят на две категории [3].
Потери первого порядка – это то, от чего нельзя избавиться. Например, расчет заработной платы сотрудникам компании. С точки зрения клиента, этот процесс не добавляет ценности продукту, но без него невозможно поддерживать работоспособность компании. Его нельзя убрать, его можно только оптимизировать.
Потери второго порядка устранимы. В компании «Toyota» они классифицируются следующим образом:
1. Перепроизводство. Это следствие образа мышления руководителей производства, главным приоритетом для которых является наиболее полная загрузка оборудования и персонала. Результатом всего этого является:
- преждевременный расход сырья и материалов;
- неоптимальное использование рабочей силы;
- необходимость закупать дополнительное оборудование;
- увеличение используемых площадей;
- рост процента отчислений (например, налога на имущество);
- чрезмерное увеличение запасов;
- увеличение транспортных и административных издержек.
Известный специалист Масааки Имаи в своей книге «Гемба Кайдзен» указывает, что перепроизводство – наихудший вид потерь, который дает обманчивое ощущение безопасности, скрывает всевозможные проблемы и «затуманивает» информацию, которая могла бы помочь реализовать положительные изменения на производстве. Перепроизводство должно рассматриваться как преступление.
2. Избыточные запасы. Сырье и материалы, готовая и недоделанная продукция, запасные части и материалы для ремонта оборудования и помещений, хранящиеся на складе, не добавляют ценности продукту с точки зрения клиента. Компания «Toyota» в основном решила проблему запасов, выстроив отношения с поставщиками по системе Just-in-Time (точно в срок). Готовая продукция также отправляется клиентам прямо из цеха.
Подавляющее большинство предприятий, работающих в Украине, рассматривает запас как защиту от неопределенности (неопределенности спроса и цикла поставок), поэтому говорить о полном избавлении от запасов не приходится. Вопрос заключается в том, какое оптимальное количество запасов должно находиться на предприятии и в каком виде. Задача менеджмента в данном случае состоит в проведении изменений процессов таким образом, чтобы достигнуть баланса производительности между подразделениями (цехами, рабочими участками). Достижение такого баланса автоматически приводит к снижению запасов.
3. Брак. Очевидные потери, оттягивающие на себя материальные и человеческие ресурсы. Философия Lean говорит о том, что следует построить такую систему, в которой любое отклонение от нормы будет сразу бросаться в глаза.
«Toyota» имеет в этом направлении большое достижение – контроль за тем, чтобы продукция с дефектом не перешла на следующий участок. Устранение дефекта производится в месте его обнаружения собственными силами и с помощью специальных групп реагирования. В данном случае ярко отслеживается концепция TQM (Total Quality Management) в действии. Ответственность за качество возлагается на сотрудников всех уровней – сверху донизу, а для этого уже требуется полное изменение сознания персонала, принятие философии качества.
4. Лишние операции и перемещения на рабочем месте. Если работник занимается поиском нужного документа или идет за инструментом за несколько метров от своего рабочего места, это также не добавляет ценности продукту с точки зрения клиента. Верный способ избежать данного вида потерь – правильно, то есть рационально организовать рабочие места.
5. Излишняя обработка. Попытка установить более жесткие допуски, чем этого требует спецификация заказчика, например, при механической обработке, повышает возможность возникновения брака, зачастую требует использования другого, более дорогостоящего инструмента (в том числе для контроля операции) и, возможно, более высокой квалификации исполнителей. Кроме того, при анализе производственных потоков обнаруживаются операции, без которых можно обойтись, сохранив качество продукта на прежнем уровне.
6. Простои. Время ожидания прибытия продукции с предыдущего этапа производственного процесса. В большинстве случаев возникает при наличии дисбаланса производительности между производственными участками, рабочими местами и цехами. Простои также возникают из-за поломок оборудования. Чтобы уменьшить негативные последствия таких ситуаций, создают запасы незавершенной продукции. Усилия для позитивных изменений в данном случае нужно направлять на обеспечение сбалансированности работы оборудования и осуществление превентивных мер, позволяющих предупредить неплановую остановку оборудования. В данном случае именно такой подход диктует философия Lean. Наличие на предприятии сверхпроизводительного оборудования не всегда есть благо, чаще всего именно оно и приводит к дисбалансу и возникновению дополнительных запасов.
7. Лишние перемещения. Транспортировка и перемещения – существенная часть производственного процесса, однако с точки зрения клиента, все внутренние перемещения и транспортировка не добавляют ценности продукту. Клиенту все равно, на какие расстояния и какими способами перемещается продукт. На некоторых предприятиях длина потока может составлять несколько километров, иногда более десяти. И если подходить к изменениям с точки зрения философии Lean, то сокращение длины потока может привести к весьма впечатляющим результатам по сокращению общего времени производства, уменьшению потерь от ущерба вследствие транспортировки, сокращению запасов и производственных площадей. Все это значительно влияет на общие финансовые результаты компании.
8. Утрата сотрудниками творческого подхода. Весьма серьезный вид потерь, влияющий на общее положение компании. Если человеку все равно, чем он занимается, то ждать от него ответственности за результат не приходится, не говоря уже об ответственности за качество выполняемой им работы [3].
Технология внедрения Lean production
Технология бережливого производства сводится к реализации всего пяти последовательных шагов, которые на первый взгляд выглядят подкупающе просто:
-определение ценности, которую хочет получить клиент;
-создание процесса получения этой ценности;
-организация непрерывного движения этого процесса;
-внедрение принципа вытягивания (вместо выталкивания);
-непрерывное совершенствование всех элементов системы [4].
Схематично последовательность внедрения системы lean production представлена на рисунке 1.
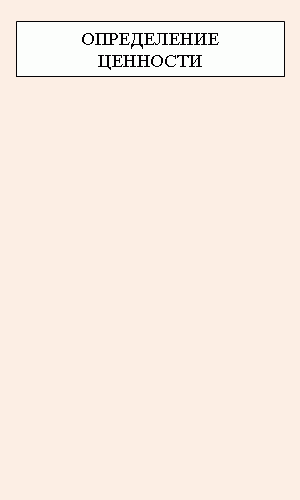
Рисунок 1 – Последовательность внедрения бережливого производства (анимация: объем – 37 кБ; размер – 500x300 пикселей; количество кадров – 9; задержка между кадрами – 100 мс; задержка между последним и первым кадрами – 200 мс; количество циклов повторений – 7)
На поверку все эти шаги оказываются далеко не такими простыми, как кажется на первый взгляд [4].
Первостепенной задачей является определение ценностей. В соответствии с моделью Н. Кано, у клиента присутствуют три уровня ценностей. Первый уровень – это те свойства, требования или возможности, которые для клиента представляются само собой разумеющимися. Он считает, что они должны выполняться «по умолчанию». Но ведь у поставщика продукции или услуги могут быть другие представления о том, что само собой разумеется. В этом заключается первая трудность [4].
Второй уровень – измеримые ценности. Это могут быть, например, характеристики некоторого продукта, такие как скорость автомобиля. Измеримые ценности изначально необходимо каким-то образом измерить. Поэтому в этом случае необходим выбор конкретных показателей (мер), выбор средств и методов измерения, установление эталонов (если возможно), оценивание метрологических характеристик [4].
Существует также и третий уровень: ценности, о которых сам клиент еще не знает. Точнее, он, скорее всего, имеет смутные представления о каких-либо качествах, которые он хотел бы видеть в продукции. Чаще всего бывает, что потребитель еще не сформировал свои требования, поэтому ни он сам, ни производитель не могут четко выразить то, что сделает продукцию ценной на рынке. Тем не менее, для производителя вопрос о требованиях (ценностях) третьего уровня – ключевой. Если бы производителю удалось проникнуть в подсознание клиента и прочесть его скрытые заветные желания, то он смог бы предвосхитить их, поразить клиента и сделать его лояльным по отношению к себе навсегда. Только, к сожалению, это остается достаточно трудной задачей [4].
На втором шаге главной задачей является создание процесса получения ценности. При его разработке важно избегать, по возможности, операций, которые не создают добавленной ценности для клиента. При этом достаточно часто возникают препятствия в виде других сторон, кроме клиента, заинтересованных в бизнесе производителя. Обычно рассматривается пять групп заинтересованных сторон, а именно: потребители, собственники, поставщики, общество, сотрудники. Здесь важно уйти от конфронтации и построить менеджмент, опирающийся на поиски согласованности и гармонии между всеми заинтересованными сторонами.
Создание процесса получения ценности начинается с наведения порядка и наглядной демонстрации неудобств, вызванных большими запасами. Для этого необходимо внедрить концепцию Пять S, чтобы каждый работающий смог понять и прочувствовать необходимость самоорганизации и исключения превышения некоторого разумного минимума [5].
Параллельно необходимо провести работу по делегированию полномочий и доведению стратегических целей от высшего уровня вплоть до рабочих, в соответствии с их квалификацией и способностями. Эта работа сочетается с постановкой маркетинга и выстраиванием цепочек внутренних потребителей и поставщиков, ориентированных на потребителей [5].
Третьим пунктом является внедрение процесса создания продукции или услуг, обеспечивающих ценностями все заинтересованные стороны. Любая остановка процесса в любом месте означает неизбежные потери. Поэтому важно добиться того, чтобы предотвратить любые задержки. Цепочки внутренних потребителей и поставщиков необходимо превратить в последовательности процессов. Это даст возможность сформировать потоки создания ценностей, как для внутренних, так и для внешних потребителей. Эти потоки нужно распространить также на поставщиков. Фактически речь идет о подготовке к внедрению бережливого производства по всем предприятиям и сетям поставщиков. Превращение сетей поставок в потоки означает также непрерывность движения перерабатываемых в процессах ресурсов в ритме, задаваемом потребителями по принципу вытягивания. Таким образом, автоматически получается система «точно в срок». Все это приводит к созданию тотальной системы вовлечения работников в процессы создания ценностей в соответствии с целями предприятия [4,5].
Поскольку достигнуть такой согласованности непросто, используется четвертый этап. Принцип вытягивания означает, что никакие действия не предпринимаются, пока следующая стадия процесса не сообщит, что она готова принять исходное сырье. Тогда заметно сократится потребность в хранении запасов и в незавершенном производстве. Мероприятия по внедрению бережливого производства осуществляются уже на основе тотальных инициатив по повышению качества и уменьшению издержек. Искусное направление этих инициатив в сторону поддержания непрерывного движения потока с помощью инфраструктуры (оборудования и оптимально планируемых помещений) приводит нас к технологии TPM (Total Productive Maintenance)[5].
Пятый шаг сам по себе является постоянным – это непрерывное совершенствование. Не удивительно, что никогда не удается сразу создать процесс, оптимальный раз и навсегда. Его приходится все время совершенствовать. Это объясняется, прежде всего, тем, что меняется внешняя среда, совершенствуются технологии, соревнуются конкуренты. Если главная цель производителя – удовлетворение требований потребителя, то он неизменно должен совершенствовать и развивать свою производственную систему [4].
По завершении всех пяти этапов на предприятии создается бережливый процесс. Это значит, что в результате высвобождается не менее половины ресурсов всех видов, которые раньше требовались для достижения того же самого результата. И это только начало. Дальнейшее совершенствование способствует получению еще порядка 40 % от исходных ресурсов. Опыт показывает, что при последовательном и усердном внедрении на это требуется около двух лет [4].
Такая последовательность действий ведет к тому, что на предприятии начинает работать система тотального обеспечения качества и уменьшения издержек. Рабочие, инженеры и менеджеры, направляя свои усилия на устранение причин несоответствий и лишних и вредных издержек, в рамках периодических мероприятий по прорывным улучшениям способны совместными усилиями создать бережливое производство как высшую форму эффективного бизнеса. Естественно, все вышесказанное касается не только производственных, но и других процессов на предприятии [5].
Бережливое производство в Украине
Концепция бережливого производства уже получила широкое распространение на предприятиях России. В большинстве случав это автомобилестроительные заводы.
В Украине принципы Lean пока имеют гораздо более скромное распространение. Но следует отметить то, что на сегодняшний день некоторые украинские предприятия уже начали внедрение элементов системы бережливого производства.
Сегодня бережливое производство внедряют на кировоградском машиностроительном заводе «Червона зірка», на предприятии по производству безалкогольных напитков «Панда» в Виннице. Уже первые этапы внедрения технологий Lean дают ощутимые положительные результаты [6].
Выводы
Концепция Lean production позволяет предприятию получить огромное количество преимуществ. Это высвобождение ресурсов, налаживание производственных потоков, заинтересованность персонала, бесперебойная работа оборудования и многое другое. Поэтому становится очевидным, что внедрение принципов Lean на украинских предприятиях очень важно для их функционирования и поддержания конкурентоспособности.
Проанализировав сложившуюся ситуацию в Украине, можно сказать, что в нашей стране уже появились реальные возможности для применения концепции бережливого производства, хотя они достаточно ограничены. Lean production уже внедряют некоторые предприятия, что стало следствием осознания важности менеджмента качества. Большим шагом вперед является тот факт, что руководители компаний понимают необходимость совершения обдуманных и систематизированных действий для улучшения работы предприятия. Однако распространение концепции Lean ограничивается финансовыми проблемами фирм и неполным осознанием важности применения системы. Некоторые руководители пытаются внедрить лишь отдельные элементы системы, надеясь получить значительный результат. Некоторые из них недостаточно ответственно и скрупулезно следят за ее внедрением, из-за чего терпят финансовые убытки.
Таким образом, можно подытожить, что для успешного внедрения системы руководство компании должно очень серьезно относиться к нововведениям, ставить цели постоянного улучшения, интересоваться опытом подобных отечественных и зарубежных предприятий. Только в этом случае использование принципов бережливого производства даст значительные результаты.
Использованная литература:
1. Вумек Дж. П., Джонс Д. Т. Бережливое производство. Как избавиться от потерь и добиться процветания вашей компании. – М.: Альпина Бизнес Букс, 2004. – 473 с.
2. Википедия: http://ru.wikipedia.org/wiki/Бережливое_производство
3. Морской В. Lean Thinking: решение проблем в производственной логистике: http://www.iteam.ru/publications/logistics/section_74/article_2483/
4. Адлер Ю. Бережливого Бог бережет. По материалам конференции «Созвездие качества'2004». Сборник тезисов докладов. – К.: Украинская ассоциация качества, Межотраслевой центр качества «Прирост», 2004. – 204 с.
5. Шехватов Д., Воронин А. Бережливое производство как элемент стратегий Кайдзен: http://www.cfin.ru/management/manufact/lean_as_kaizen.shtml
6. Куприянова Т.М., Растимешин В.Е. Как выращивается Бережливое производство: http://www.tpm-centre.ru/page.php?pageId=98&menuItemTreeCode=0810
7. Бушуев А. Стратегия, Маркетинг и Бережливое Производство: http://www.leancor.ru/article2/10011
8. Булгакова М.В. Особенности национального внедрения Lean // Методы менеджмента качества. – 2006, №10. – С. 4-9.
9. Гагарский В. Бережливое производство – ответ на вызовы кризиса: http://www.orgprom.ru/go/obj0069098568/obj0021380748/obj0011864948
10. Фомичев С.К., Скрябина Н.И., Уразлина О.Ю. «Бережливое управление»: управление потоком создания ценности // Методы менеджмента качества. – 2004, №7. – С. 5-11.
11. Цыганов И.Ю. Экономное производство – первоочередная необходимость // Методы менеджмента качества. – 2004, №4. – С. 3-6.
|