Система Lean production та можливості її використання в Україні
Введення
В останні роки в Україні, як і в країнах колишнього Радянського Союзу, істотно зріс інтерес до питань менеджменту, управління підприємствами, перетворення організаційних структур компаній. На жаль, цей інтерес з’явився лише останнім часом.
У світовій практиці було створено безліч нових концепцій та методів менеджменту: реінжиніринг бізнес-процесів (BPR), Загальне Управління Якістю (TQM), збалансована система показників (BSC), статистичне управління процесами (SPC), коучинг, моделі міжнародних стандартів ІСО 9000, ІСО 14000, ХАССП, «П'ять S», «Шість Сигм» та багато іншого. На жаль, країни пострадянського простору не мають своїх розробок у цій галузі. Немає традицій, шкіл, досвіду попередників, немає налагоджених систем менеджменту.
Тому українським управлінцям слід багато освоїти із зарубіжних методик, щоб вижити і зберегти конкурентоспроможність.
Концепція «Бережливе Виробництво і Мислення» (Lean Thinking and Manufacturing) займає одне з найбільш важливих місць серед сучасних пропозицій з менеджменту.
Однак культура нашої країни в цілому дуже далека від поняття «бережливість». Про це може свідчити те, що у нас стружка зберігається в цехах, а заготовки металу – під відкритим небом; паркани будуються з натурального дерева, а меблі – з тирси; один цех знаходиться в декількох кілометрах від іншого. Чесно кажучи, знайти розумне пояснення цьому неможливо [1].
Конкурентна перевага українських підприємств може бути забезпечена тільки високою якістю та низькими витратами. Тому сьогодні потрібно переглянути всю організацію виробництва з тим, щоб виключити всі види втрат. При цьому ще раз хочеться підкреслити необхідність інтегрованого підходу, що включає якість і концепції, методи та інструменти бережливого виробництва [1].
Виходячи з проблематики функціонування українських підприємств, фахівці в галузі менеджменту якості вважають, що освоєння концепції бережливого виробництва та застосування її методів є надзвичайно важливим фактором для покращення діяльності всіх ланок виробничої системи [1].
Метою даної роботи є розкриття суті концепції бережливого виробництва, а також аналіз можливостей впровадження та функціонування бережливого виробництва на підприємствах України.
Історія виникнення системи
«Бережливое виробництво» – японська технологія менеджменту, це філософія організації та ведення бізнесу, яка вбирає в себе практично всі аспекти діяльності компанії, включаючи стратегічний розвиток та управління маркетингом [2].
Батьком-засновником бережливого виробництва вважається Тайіті Оно (1912 – 1990), який почав роботу в Toyota Motor Corporation в 1943 році, інтегруючи кращий світовий досвід. У середині 1950-х років він впровадив систему TPS (Toyota Production System), яка в західній інтерпретації стала відома як Lean production, Lean manufacturing, Lean. Ідеї Lean були висловлені ще Генрі Фордом, але вони не були сприйняті бізнесом, оскільки значно випереджали час [2].
Спочатку Lean застосовували в галузях з дискретним виробництвом, перш за все в автомобілебудуванні. Потім концепція була адаптована до умов безперервного виробництва, а потім її почали впроваджувати в торгівлі, сфері послуг, комунальному господарстві, охороні здоров'я, збройних силах і державному секторі.
Поступово Lean вийшов за межі підприємства. Тепер Lean охоплює споживачів його продукції, постачальників. У багатьох країнах поширенню бережливого виробництва надається державна підтримка [2].
Мета концепції «бережливого виробництва» – позбутися усіх видів втрат і досягти максимальної ефективності використання ресурсів.
Особливість концепції «бережливого виробництва» – поступове і безперервне вдосконалення всіх бізнес-процесів організації, спрямованих на підвищення задоволеності клієнта.
Підхід концепції «бережливого виробництва» – використання здорового глузду в організації функціонування підприємства.
Суть концепцїї бережливого виробництва
Основна ідея цієї концепції полягає в наступному: якщо якась дія, операція або процес не додає цінності продукту з точки зору клієнта, то ця дія, операція або процес розглядаються як втрати, тобто як такі, що приносять збитки компанії. Причому всі втрати поділяють на дві категорії [3].
Втрати першого порядку – це те, чого не можна позбутися. Наприклад, розрахунок заробітної плати співробітникам компанії. З точки зору клієнта, цей процес не додає цінності продукту, але без нього неможливо підтримувати працездатність компанії. Його не можна ліквідувати, його можна тільки оптимізувати.
Втрати другого порядку можуть бути усунені. У компанії «Toyota» вони класифікуються наступним чином:
1. Перевиробництво. Це наслідок способу мислення керівників виробництва, головним пріоритетом для яких є найбільш повне завантаження обладнання та персоналу. Результатом всього цього є:
- передчасна витрата сировини і матеріалів;
- неоптимальне використання робочої сили;
- необхідність закуповувати додаткове обладнання;
- збільшення використовуваних площ;
- зростання відсотка відрахувань (наприклад, податку на майно);
- надмірне збільшення запасів;
- збільшення транспортних та адміністративних витрат.
Відомий фахівець Масааки Імаі в своїй книзі «Гемба Кайдзен» вказує, що перевиробництво – найгірший вид втрат, який дає оманливе відчуття безпеки, приховує всілякі проблеми і «затуманює» інформацію, яка могла б допомогти реалізувати позитивні зміни на виробництві. Перевиробництво має розглядатися як злочин.
2. Надлишкові запаси. Сировина та матеріали, готова і недороблена продукція, запасні частини та матеріали для ремонту обладнання і приміщень, що зберігаються на складі, не додають цінності продукту з точки зору клієнта. Компанія «Toyota» в основному вирішила проблему запасів, побудувавши відносини з постачальниками за системою Just-in-Time (точно-в-строк). Готова продукція також відправляється клієнтам прямо з цеху.
Переважна більшість підприємств, що працюють в Україні, розглядає запас як захист від невизначеності (невизначеності попиту та циклу поставок), тому говорити про повне позбавлення від запасів не доводиться. Питання полягає в тому, яка оптимальна кількість запасів повинна знаходитися на підприємстві і в якому вигляді. Завдання менеджменту в даному випадку полягає в проведенні змін процесів таким чином, щоб досягти балансу продуктивності між підрозділами (цехами, робочими ділянками). Досягнення такого балансу автоматично призводить до зниження запасів.
3. Брак. Очевидні втрати, що відтягують на себе матеріальні та людські ресурси. Філософія Lean говорить про те, що треба побудувати таку систему, в якій будь-яке відхилення від норми буде одразу кидатися в очі.
«Toyota» має в цьому напрямку велике досягнення – контроль за тим, щоб продукція з дефектом не перейшла на наступну ділянку. Усунення дефекту здійснюється в місці його виявлення власними силами та за допомогою спеціальних груп реагування. У даному випадку яскраво відстежується концепція TQM (Total Quality Management) у дії. Відповідальність за якість покладається на співробітників всіх рівнів – від верху до низу, а для цього вже потрібна повна зміна свідомості персоналу, прийняття філософії якості.
4. Зайві операції та переміщення на робочому місці. Якщо працівник займається пошуком потрібного документа або йде за інструментом за кілька метрів від свого робочого місця, це також не додає цінності продукту з точки зору клієнта. Вірний спосіб уникнути даного виду втрат – правильно, тобто раціонально організувати робочі місця.
5. Зайва обробка. Спроба встановити більш жорсткі допуски, ніж цього вимагає специфікація замовника, наприклад, при механічній обробці, підвищує можливість виникнення дефектів, часто вимагає використання іншого, більш дорогого інструменту (в тому числі для контролю операцій) і, можливо, більш високої кваліфікації виконавців. Крім того, при аналізі виробничих потоків виявляються операції, без яких можна обійтися, зберігши якість продукту на попередньому рівні.
6. Простої. Час очікування прибуття продукції з попереднього етапу виробничого процесу. У більшості випадків виникає при наявності дисбалансу продуктивності між виробничими ділянками, робочими місцями і цехами. Простої також виникають через поломки обладнання. Щоб зменшити негативні наслідки таких ситуацій, створюють запаси незавершеної продукції. Зусилля для позитивних змін у цьому випадку потрібно направляти на забезпечення збалансованості роботи обладнання та здійснення превентивних заходів, що дозволяють запобігти неплановій зупинці обладнання. В даному випадку саме такий підхід диктує філософія Lean. Наявність на підприємстві надпродуктивного обладнання не завжди є на користь, найчастіше саме вона і призводить до дисбалансу і виникнення додаткових запасів.
7. Зайві переміщення. Транспортування та переміщення – істотна частина виробничого процесу, однак з точки зору клієнта, всі внутрішні переміщення та транспортування не додають цінності продукту. Клієнтові все одно, на які відстані і якими способами переміщується продукт. На деяких підприємствах довжина потоку може складати декілька кілометрів, іноді більш десяти. І якщо підходити до змін з точки зору філософії Lean, то скорочення довжини потоку може призвести до вражаючих результатів. Все це значно впливає на загальні фінансові результати компанії.
8. Втрата співробітниками творчого підходу. Досить серйозний вид втрат, що впливає на загальний стан компанії. Якщо людині все одно, чим вона займається, то чекати від неї відповідальності за результат не доводиться, не кажучи вже про відповідальність за якість виконуваної нею роботи [3].
Технологія впровадження Lean production
Технологія бережливого виробництва зводиться до реалізації всього п'яти послідовних кроків, які, на перший погляд виглядають досить просто:
- визначення цінності, яку хоче отримати клієнт;
- створення процесу отримання цієї цінності;
- організація безперервного руху цього процесу;
- впровадження принципу витягування (замість виштовхування);
- безперервне вдосконалення всіх елементів системи [4].
Схематично послідовність впровадження системи lean production зображена на рисунці 1.
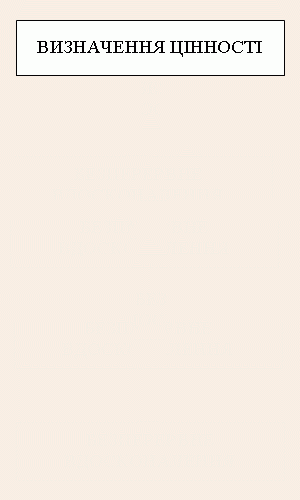
Рисунок 1 – Послідовність впровадження бережливого виробництва (анімація: об'єм – 58 кБ; розмір – 500x300 пікселей; кількість кадрів – 9; затримка між кадрами – 100 мс; затримка між останнім та першим кадрами – 200 мс; кількість циклів повторень – 7)
Насправді всі ці кроки виявляються далеко не такими простими, як здається на перший погляд [4].
Першочерговим завданням є визначення цінностей. У відповідності з моделлю Н. Кано, у клієнта присутні три рівня цінностей. Перший рівень – це ті властивості, вимоги або можливості, які для клієнта представляються зрозумілими. Він вважає, що вони повинні виконуватися самі собою. Але ж у постачальника продукції або послуги можуть бути інші уявлення про те, що є зрозумілим. В цьому полягають перші труднощі [4].
Другий рівень – вимірювані цінності. Це можуть бути, наприклад, характеристики деякого продукту, такі як швидкість автомобіля. Вимірювані цінності спочатку необхідно якимось чином виміряти. Тому в цьому випадку необхідний вибір конкретних показників, вибір засобів і методів вимірювання, встановлення еталонів (якщо можливо), оцінювання метрологічних характеристик [4].
Існує також і третій рівень: цінності, про які сам клієнт ще не знає. Точніше, він, швидше за все, має смутні уявлення про які-небудь властивості, які він хотів би бачити у продукції. Найчастіше буває, що споживач ще не сформував свої вимоги, тому ні він сам, ні виробник не можуть чітко висловити те, що зробить продукцію цінною на ринку. Тим не менше, для виробника питання про вимоги третього рівня є ключовим. Якби виробникові вдалося проникнути в підсвідомість клієнта і прочитати його приховані заповітні бажання, то він зміг би передбачити їх, вразити клієнта та зробити його більш лояльним по відношенню до себе назавжди. Тільки, на жаль, це залишається досить важким завданням [4].
На другому етапі головним завданням є створення процесу отримання цінності. При його розробці важливо уникати, по можливості, операцій, які не створюють доданої цінності для клієнта. При цьому досить часто виникають перешкоди у вигляді інших сторін, крім клієнта, зацікавлених у бізнесі виробника. Зазвичай розглядається п'ять груп зацікавлених сторін, а саме: споживачі, власники, постачальники, суспільство, співробітники. Тут важливо уникнути конфронтації і побудувати менеджмент, що спирається на пошуки узгодженості і гармонії між усіма зацікавленими сторонами.
Створення процесу отримання цінності починається з наведення порядку і наглядної демонстрації незручностей, які викликані великими запасами. Для цього необхідно впровадити концепцію П'ять S, щоб кожен працюючий зміг зрозуміти і відчути необхідність самоорганізації і виключення перевищення деякого розумного мінімуму [5].
Паралельно необхідно провести роботу з делегування повноважень і доведення стратегічних цілей від вищого рівня до робітників, відповідно до їх кваліфікації та здібностей. Ця робота поєднується з постановкою маркетингу та створенням ланцюжків внутрішніх споживачів і постачальників [5].
Третім пунктом є впровадження процесу створення продукції або послуг, що забезпечують цінностями всі зацікавлені сторони. Будь-яка зупинка процесу в будь-якому місці означає неминучі втрати. Тому важливо добитися того, щоб запобігти будь-яким затримкам. Ланцюги внутрішніх споживачів і постачальників необхідно перетворити в послідовності процесів. Це надасть можливість сформувати потоки створення цінностей, як для внутрішніх, так і для зовнішніх споживачів. Ці потоки потрібно поширити також на постачальників. Фактично мова йде про підготовку до впровадження бережливого виробництва по всім підприємствам та мережам постачальників. Перетворення мереж поставок в потоки означає також безперервність руху ресурсів у ритмі, що задається споживачами за принципом витягування. Таким чином, автоматично виходить система «точно в строк». Все це призводить до створення тотальної системи залучення працівників до процесів створення цінностей у відповідності з цілями підприємства [4,5].
Оскільки досягти такої узгодженості непросто, використовується четвертий етап. Принцип витягування означає, що ніякі дії не робляться, поки наступна стадія процесу не повідомить, що вона готова прийняти вихідну сировину. Тоді помітно скоротиться потреба в зберіганні запасів і в незавершеному виробництві. Заходи щодо впровадження бережливого виробництва здійснюються вже на основі тотальних ініціатив по підвищенню якості та зменшенню витрат. Направлення цих ініціатив у бік підтримки безперервного руху потоку за допомогою інфраструктури (обладнання і оптимально спланованих приміщень) приводить нас до технології TPM (Total Productive Maintenance) [5].
П'ятий крок є постійним – це безперервне вдосконалення. Не дивно, що ніколи не вдається відразу створити процес, оптимальний раз і назавжди. Його доводиться весь час вдосконалювати. Це пояснюється, перш за все, тим, що змінюється зовнішнє середовище, удосконалюються технології, змагаються конкуренти. Якщо головна мета виробника – задоволення вимог споживача, то він обов’язково має удосконалювати і розвивати свою виробничу систему [4].
По завершенні всіх п'яти етапів на підприємстві створюється бережливий процес. Це означає, що в результаті звільнюється не менше половини ресурсів всіх видів, які раніше були потрібні для досягнення того ж самого результату. І це тільки початок. Подальше вдосконалення сприяє отриманню ще близько 40% від вихідних ресурсів. Досвід показує, що при послідовному і ретельному впровадженню на це потрібно близько двох років [4].
Така послідовність дій веде до того, що на підприємстві починає працювати система тотального забезпечення якості та зменшення витрат. Робітники, інженери і менеджери, спрямовуючи свої зусилля на усунення причин невідповідностей і зайвих та шкідливих витрат, здатні спільними зусиллями створити бережливе виробництво як вищу форму ефективного бізнесу. Зрозуміло, все вищесказане стосується не тільки виробничих, але й інших процесів на підприємстві [5].
Бережливе виробництво в Україні
Концепція бережливого виробництва вже має широке поширення на підприємствах Росії. У більшості випадків це стосується автомобілебудівних заводів.
В Україні принципи Lean поки мають набагато більш скромне поширення. Але слід відзначити те, що на сьогоднішній день деякі українські підприємства вже почали впровадження елементів системи бережливого виробництва.
Сьогодні дбайливе виробництво впроваджують на Кіровоградському машинобудівному заводі «Червона зірка», на підприємстві з виробництва безалкогольних напоїв «Панда» у Вінниці. Вже перші етапи впровадження технологій Lean дають відчутні позитивні результати [6].
Висновки
Концепция Lean production дозволяє підприємству отримати величезну кількість переваг. Це вивільнення ресурсів, налагодження виробничих потоків, зацікавленість персоналу, безперебійна робота обладнання та багато іншого. Тому стає очевидним, що впровадження принципів Lean на українських підприємствах дуже важливо для їх функціонування та підтримки конкурентоспроможності.
Проаналізувавши ситуацію, що склалася в Україні, можна сказати, що в нашій країні вже з'явилися реальні можливості для застосування концепції бережливого виробництва, хоча вони досить обмежені. Lean production вже впроваджують деякі підприємства, що стало наслідком усвідомлення важливості менеджменту якості. Великим кроком вперед є той факт, що керівники компаній розуміють необхідність здійснення зважених і систематизованих дій для покращення роботи підприємства. Однак поширення концепції Lean обмежується фінансовими проблемами фірм і неповним усвідомленням важливості застосування системи. Деякі керівники намагаються впровадити лише окремі елементи системи, сподіваючись отримати значний результат. Деякі з них недостатньо відповідально і скрупульозно стежать за її впровадженням, через що зазнають фінансові збитки.
Таким чином, можна підсумувати, що для успішного впровадження системи керівництво компанії має дуже серйозно ставитися до нововведень, ставити цілі постійного поліпшення, цікавитися досвідом подібних вітчизняних та зарубіжних підприємств. Тільки в цьому випадку використання принципів бережливого виробництва дасть значні результати.
Використана література:
1. Вумек Дж. П., Джонс Д. Т. Бережливое производство. Как избавиться от потерь и добиться процветания вашей компании. – М.: Альпина Бизнес Букс, 2004. – 473 с.
2. Вікіпедія: http://ru.wikipedia.org/wiki/Бережливое_производство
3. Морской В. Lean Thinking: решение проблем в производственной логистике: http://www.iteam.ru/publications/logistics/section_74/article_2483/
4. Адлер Ю. Бережливого Бог бережет. По материалам конференции «Созвездие качества'2004». Сборник тезисов докладов. – К.: Украинская ассоциация качества, Межотраслевой центр качества «Прирост», 2004. – 204 с.
5. Шехватов Д., Воронин А. Бережливое производство как элемент стратегий Кайдзен: http://www.cfin.ru/management/manufact/lean_as_kaizen.shtml
6. Куприянова Т.М., Растимешин В.Е. Как выращивается Бережливое производство: http://www.tpm-centre.ru/page.php?pageId=98&menuItemTreeCode=0810
7. Бушуев А. Стратегия, Маркетинг и Бережливое Производство: http://www.leancor.ru/article2/10011
8. Булгакова М.В. Особенности национального внедрения Lean // Методы менеджмента качества. – 2006, №10. – С. 4-9.
9. Гагарский В. Бережливое производство – ответ на вызовы кризиса: http://www.orgprom.ru/go/obj0069098568/obj0021380748/obj0011864948
10. Фомичев С.К., Скрябина Н.И., Уразлина О.Ю. «Бережливое управление»: управление потоком создания ценности // Методы менеджмента качества. – 2004, №7. – С. 5-11.
11. Цыганов И.Ю. Экономное производство – первоочередная необходимость // Методы менеджмента качества. – 2004, №4. – С. 3-6.
|