Literature
Introduction
According to various reports so far in the dumps of coal mines in Ukraine has accumulated more than 1 billion tons of waste. However, the volume of industrial waste is negligible - 6.5% of their output. Ecological effect obtained in the disposal of waste, made up of many factors, often specific to a particular type of waste.
It is known that the use of waste 2-3 times cheaper than natural resources. Fuel consumption when using certain types of waste is reduced by 10-40%, and the specific investment by 30-50%.
On the territory of Donetsk region has more than 1,5 thousand heaps of coal mines, each of them an average of 1,144 million m3 of rock. Pit heaps scattered throughout the region and cover an area of about 800 hectares.
Investigation of the chemical composition of several rock dumps of mines in the Donetsk region give a clear picture of the chemical composition of waste heaps. It was found that waste dumps contains not only toxic, but potentially valuable chemical elements. The rock contains higher amount of coal - from 5 to 46%, as well as raw materials for production of alumina (Al2O3) - up to 15% and Germany - up to 55 g / t. Constitute the bulk of oxides of silicon and iron, alkaline same components (CaO and MgO) - do not exceed 5%.
You should also pay attention to is contained in the rock coal, which depending on its quantity may allow the partial reduction of fuel consumption for roasting cement raw materials.
Analysis of chemical composition showed that most of the rocks contained in the dumps, are suitable for use as a clay raw materials in the manufacture of Portland cement and other binders.
Work accomplished
Chemical analysis of mudstone was conducted (the study species), which is calculated according to the results of the initial mixture for cement clinker, as well as determined the chemical composition of finished clinker. As the lime component was selected chalk. In parallel, the device Toropova was determined the specific surface area of the initial components.
Based on these data we calculated the main characteristics of cement clinker: the coefficient of saturation, silica and alumina module. The figure for comparison also shows the recommended Giprotsementom values of these characteristics.
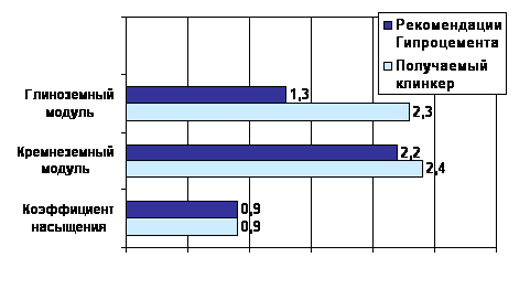
Fig. 1 - Basic descriptions of the got cement clinker
We see that only the value of the alumina module differs significantly from the recommended. Alumina modulus - the ratio of aluminum oxide contained in the clinker to the content of iron oxide.
From this it follows that the correct composition of the initial mixture can be either a decrease in the content of aluminum oxide, or by introducing an additional amount of iron oxide. Work carried out in both directions.
Our department has developed a technology of extracting coal waste aluminum oxide - a raw material for production of aluminum. The remainder of the extraction is proposed to use for cement clinker production.
The second area was a mixture whose composition was injected an additional amount of iron oxide.
Mixtures fired in electric resistance furnaces. Moreover, firing was conducted on two thermal regimes.
Until the temperature both modes coincide with the rate of rise of temperature from 800 to 1100 degrees reduced for the calcining process.
When the firing temperature for the second was made of isothermal exposure, which was not available for the first composition.
Burnt brick smashed into pieces and cooled in special circumstances.
Then the clinker is crushed together with gypsum, sifted through a sieve № 008.
In addition, measured the specific surface obtained cement.
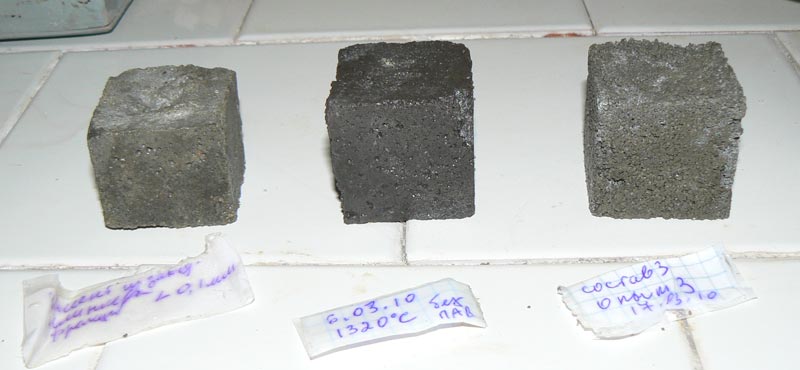
Fig. 3 - Blocks for the test of durability on the compression
Then cement production by the standard method molded samples for testing their compressive strength.
Main results
Cement production shows a rather high strength characteristics. Terms of cement production has not been fully matched. In the future we plan to hold a series of experiments with different temperatures and burning conditions, different values of the main characteristics of cement clinker production. Also planned for experimentation with different modes of grinding (milling time change, the change in intensity grinding, use of different intensifiers, etc.).
After reaching the values of the strength of the resulting cement respective brand M300 and above, will conduct experiments on conformity to the properties of the cement as specified in the "ДСТУ Б В.2.7-46-96".
Conclusion
Performing the work envisaged and concrete results will develop technology recycling waste heaps that for the Donetsk region is an environmental priority.
In the course of the experiments were obtained skills Toropova device for measuring the specific surface substances mastered the basic technique for testing of cement to meet "ДСТУ Б В.2.7-46-96". Program was written in Visual Basic for Application, with the help of which were calculated raw mix for cement (up to four-component mixtures, inclusive). Culated the main characteristics of the resulting cement clinker: the coefficient of saturation, alumina and silica-ins.
Literature
- Бурковський Ю.А. Сухой способ производства портландцементного клинкера. - Госстройиздат, 1958.- 267с.
- Бутт Ю.М. Технология вяжущих веществ. - М.: Высшая школа, 1965.-619с.
- Власов П.А. Транспорт и хранение цмента. - Госстройиздат, 1959.-227с.
- Коновалов П.Ф. Физико-химические исследования цементов. - Госстройиздат, 1960.-427с
- Окороков С.Д. Расчет портландцементной сырьевой шихты. - Стройиздат, 1975.-329с
- Пащенко А. А. Мясникова Е. А. Теория цемента. - К.: Будівельник, 1991. - 168с.
- Бутт Ю. М. Тимашев В. В. Портландцемент. - М.: Стройиздат, 1974. - 328с.
- ДСТУ Б В.2.7-46-96. Будівельні матеріали. Цементи загальнобудівельного призначення. Технічні умови. - Київ: Держкоммістобудування України, 1996. - 72 с.
- Краткий справочник технолога цементного завода под ред. проф. И. В. Кравченка М.: Стройиздат, 1974. - 304с
- Колокольников В. С. Производство цемента. - М.: Высшая школа, 1967.-303с.
- Урьев Н. Б, Дубинин И. С. Коллоидные цементные растворы. - Л.: Стройиздат, 1980. - 192 с.
- Квалификационная работа магистра Папуна Н. В. Переработка терриконов методом агломерации. Портал магистров ДонНТУ [Электронный ресурс] Режим доступа: www/URL: http://masters.donntu.ru/2008/fizmet/papuna/library/index.htm