|
Лапенко Алексей Павлович
Факультет экологии и химической технологии
Кафедра прикладной экологии и охраны окружающей среды
Специальность: Технология тугоплавких неметаллических и силикатных
материалов
Тема квалификационной работы магистра:
Изучение возможности использования аргиллита для получения цементных вяжущих материалов
Научный руководитель: профессор, доктор химических наук Шаповалов Валерий Васильевич
Реферат по теме выпускной работы
Оглавление
Введение
Обзор исследований по теме в ДонНТУ
Обзор исследований по теме в Украине
Обзор исследований по теме в мире
Выполненная работа
Основные результаты
Заключение
Литература
Введение
По различным данным к настоящему времени в отвалах угольных шахт Украины скопилось более 1 млрд. т отходов. Однако объем использования промышленных отходов незначителен - 5-6% от их выхода. Экологический эффект, получаемый при утилизации отходов, складывается из многих факторов, часто специфических для того или иного вида отходов.
При этом известно, что использование отходов в 2-3 раза дешевле, чем природного сырья [1]. Расход топлива при использовании отдельных видов отходов снижается на 10-40%, а удельные капиталовложения на 30-50%.
На территории Донецкой области насчитывается более 1,5 тыс. отвалов угольных шахт, в каждом из них в среднем 1,144 млн. м3 породы. Терриконы разбросаны по всей территории области и занимают площадь около 800 га.
Выполненные исследования химического состава ряда породных отвалов шахт Донецкого региона дают представления о химическом составе терриконов. Выяснилось, что в терриконах содержатся не только токсические, но и потенциально ценные химические элементы. Порода содержит повышенное количество угля - от 5 до 46%, а также сырье для производства алюминия (Al2О3) - до 15 % и германия - до 55 г/т. Основную массу составляют оксиды кремния и железа, щелочноземельные же компоненты (СаО и МgО) - не превышают 5 % [2].
Также следует обратить внимание на содержащийся в породе уголь, который в зависимости от его количества может позволить частично снизить расходы топлива на обжиг цементного сырья [3].
Анализ химического состава показал, что большинство горных пород, содержащихся в отвалах, пригодны для использования их в качестве глинистого сырья при производстве портландцемента и некоторых других цементных вяжущих материалов. На глинистое сырье для производства портландцемента нет установленных стандартом технических требований. Однако, на основании практического опыта установлены следующие ориентировочные требования к химическому составу глинистых пород, определяющие целесообразность их использования: количество СаО не ограничивается; допустимое содержание MgO зависит от содержания его в известковом компоненте и ограничивается условием получения клинкера для портландцемента с содержанием MgO не более 5%, а для магнезиального портландцемента - не более 10%; количество SiO2, Al2O3, Fe2O3 в сочетании с известковым компонентом должно обеспечивать получение необходимых значений коэффициента насыщения, кремнеземного и глиноземного модулей в сырьевой смеси и клинкере (с учетом возможности введения корректирующих добавок)[4]. Желательно, чтобы Na2O и K2O в сумме не превышали 3 - 4%, а SO3 было не более 1%. Увеличение содержания SiO2 достигается добавкой высококремнеземистых веществ - трепела, опоки, диатомита [5]. Недостаточное количество в сырьевой смеси окиси железа компенсируется добавкой колчеданистых огарков, железной руды; добавка высокоглиноземных глин (бокситов) позволяет повысить содержание в клинкере глинозема.
Карбонатные породы в природе встречаются в виде известняков, мела, известкового туфа, известняка-ракушечника и мрамора. Все приведенные разновидности карбонатных пород находят применение в портландцементном производстве, за исключением мрамора. Наиболее применимы известняки и мел, представляющие собой осадочные горные породы. Осадочное происхождение известняков и мела обусловливает разнообразие их химического состава и физических свойств [6]. Химически чистый углекислый кальций содержит 56% СаО и 44% СО2. Но таких известняков в природе нет. Наряду с СаСО3 природные известняки содержат кремнезем, глинозем, окиси железа, окись магния и др.
В качестве известкового компонента могут быть использованы различные горные породы с повышенным (в сравнении с классическим цементным сырьем) содержанием карбоната кальция. Такие горные породы широко распространены на территории Донецкой области и иногда представляют собой отходы: вскрышные породы при разработке различных полезных ископаемых [7].
Существует четыре главных технологических способа производства цемента - сухой, полусухой, полувлажный и мокрый процесс.
Обычно все эти процессы включают в себя следующие подпроцессы:
Карьерные работы
Подготовка сырья
Подготовка топлива
Спекание цементного клинкера
Подготовка минеральных добавок
Размол цемента
Транспортировка цемента
Карьерные работы. Природное сырье, например, известняк или мел, известковая глина и глина или сланец добываются в карьерах, которые, в большинстве случаев, расположены поблизости от цементного завода. После добычи сырье измельчается непосредственно в карьере и транспортируется на цементный завод для промежуточного хранения, гомогенизации и дальнейшей переработки [9].
"Корректирующие" материалы, такие как глинозем, железная руда или кремнезем могут быть необходимы в химическом составе сырьевой смеси в соответствии с требованиями процесса и технических требований к продукту. Количество корректирующих материалов обычно очень мало по сравнению с общими объемами основного сырья. В больших объемах используется вторичное (или альтернативное) сырье, отходы производства, чтобы заменить природное сырье и "корректирующие" материалы [9].
Таким же образом как традиционное сырье, эти материалы могут подаваться на дробилку карьера или непосредственно в процессе подготовки сырья на цементном заводе.
Подготовка сырья. После промежуточного хранения и усреднения, сырье сушится и перетирается в определенных и хорошо контролируемых пропорциях в мельницах, в результате чего получается сырьевая "мука" для сухого (и полусухого) процесса. При мокром (и полумокром) процессе сырье - катализированная суспензия, измельчается с определенным количеством воды для получения жидкого цементного теста [9].
В зависимости от технологического процесса может быть использована дополнительная ступень, например, подготовка гранул из сырьевой смеси - сухого тонко размолотого вещества (полусухой процесс), или получение фильтрационного осадка в процессе осушения жидкого раствора в фильтрующем прессе (полувлажный процесс). Получающийся промежуточный продукт - то есть сырьевая мука или жидкое цементное тесто (или их производные) - сохраняется и далее гомогенизируется в бункерах сырьевой смеси или шламовых бассейнах, в результате чего достигается и поддерживается необходимый однородный химический состав перед отправлением в печь. Как правило, приблизительно необходимо около 1.6 тонны (сухого) сырья для производства одной тонны клинкера [10].
Подготовка топлива. Обычное топливо, используемые в европейской цементной промышленности - главным образом каменный уголь, топливный мазут и необработанная нефть. Природный газ преимущественно используется на заводах постсоветского пространства. Альтернативные виды топлива - неорганические топлива, производимые из индустриальных отходов - широко используются в наши дни вместо традиционных видов ископаемого топлива, только за рубежом.
Подготовка топлив - измельчение, высушивание, измельчение, и усреднение - обычно производится на месте. Для этого нужны угольные мельницы, бункера и помещения для хранения твердого топлива, резервуары для жидкого топлива и соответствующий транспорт и системы подачи к печам.
Потребление топлива в значительной степени зависит от основного технологического процесса, применяемого при спекании цементного клинкера.
Спекание цементного клинкера. Готовое сырье поступает в печи, где подвергается процессу обжига, состоящему из последовательных ступеней высушивания, подогрева, прокаливания (например, при процессе декарбонизации), и спекания (или “клинкеризации”, например, при обжиге клинкера при температуре до 1450 ° C). Спекшийся клинкер охлаждается потоком воздуха до 100-200 °C в устройствах, называемых холодильниками и транспортируется к месту хранении. Холодильники бывают различных типов, но наиболее часто применяются рекуператорные и колосниковые [11].
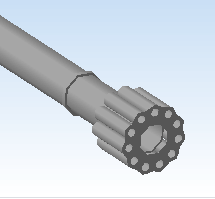 Рис. 1 - Модель рекуператорного холодильника (анимация; 9 кадров; без задержки; бесконечная)
Обычно применяются вращающиеся печи с или без так называемых теплообменников (в более современных системах - "декарбонизатор") в зависимости от основного процесса. Сама вращающиеся печь представляет собой наклонную стальную трубу, футерованную огнеупорными материалами с соотношением длины к диаметру около 1/4. Небольшой наклон (от 2.5 до 4.5 %) вместе с медленным вращением (0.5 - 4.5 оборотов в минуту), позволяют перемещать обрабатываемые материалы достаточно долго для достижения термической конверсии требуемых процессов. Часто, для интенсификации процессов, внутри печи предусмотрены цепные завесы [9].
Высокая температура отходящих из печи газов используется для сушки сырья, твердого горючего или минеральных добавок в мельнице. Отработанные газы проходят через электростатические осадители или рукавные фильтры перед выпуском в атмосферу.
Помол цемента. Портландцемент производится путем совместного размола клинкерного цемента с небольшим количеством гипсового камня на цементном заводе. Цементы с добавками содержат другие элементы, например, доменный гранулированный шлак, природный или индустриальный туф, активные минеральные добавки (диатомит, трепел, опоку) или инертные наполнители, такие как известняк [9].
Минеральные добавки, чаще всего, вводятся при дроблении вместе с клинкером.
Размалывающие установки могут быть расположены отдаленно от производства клинкера.
Отправка цемента. Цемент может быть отправлен, насыпью, или упакованный в мешки и уложенный в штабеля для отправки. Использование видов транспортировки зависит от местных условий и требований.
Обзор исследований по теме в ДонНТУ
В ДонНТУ подобные исследования не проводились. Однако интерес представляет работа магистра Папуной Н. В. В своей работе «Переработка терриконов методом агломерации» она исследовала условия получения аглопорита из отходов угледобывающей промышленности [12].
Обзор исследований по теме в Украине
Анализ литературы, а также поиск в Интернете показал, что подобные исследования в Украине не проводились. Южгипроцемент совместно с Днепродзержинским заводом установили возможность добавления в сырьевую смесь отходов углеобогащения.
Обзор исследований по теме в мире
Проблема рациональной утилизации промышленных отходов и ТБО успешно решается за рубежом. Все горючие отходы сжигаются в цементных печах, которые выгодно отличаются от печей мусоросжигательных заводов тем, что в них теплотехнический процесс проходит при более высокой температуре до 1700 - 1800 °С в щелочной среде (избыток оксида кальция), предотвращающей образование диоксинов.
Это обеспечивает снижение до минимума содержание вредных веществ в отходящих газах, а также химическое связывание в основных клинкерных минералах части вредных веществ, выделяемых из отходов.
Исследования и практика отечественных и зарубежных цементных предприятий показали, что в цементных печах успешно могут быть использованы горючие отходы. Найдены пути утилизации шлаков и шламов металлургии, химических предприятий, золошлаковых отходов теплоэлектростанций, отходов целлюлозно-бумажной и гидролизной промышленности, нефтепереработки - гудронов, нефтешламов, смеси отработанных нефтепродуктов, изношенных автопокрышек и других топливосодержащих отходов.
Номенклатура утилизируемых отходов:
Железнодорожные шпалы, пропитанные антисептиками;
Нефтешламы;
Отработанные минеральные масла;
Отработанные растительные масла;
Песок, загрязненный маслами или мазутом;
Опилки, обтирочный материал, бумага замасленные;
СОЖ, эмульсии;
Жиры, отходы жироуловителей;
Пищевые продукты;
Отходы кухонь и предприятий общественного питания;
Отходы производства вкусовых добавок;
Осадки очистных сооружений гальванических и травильных производств, гальваношламы;
Отходы катализаторов;
Отходы ЛКМ, клеев, мастик, незатвердевших смол;
Отходы затвердевших пластмасс и полимерной пленки;
Золы, шлаки и пыль от топочных установок и от термической обработки отходов;
Отходы пивоваренного, спиртового и ликероводочного производства;
Мебель, отходы древесины;
Древесные отходы с пропиткой, покрытиями, содержащие полимерные смолы и др.;
Разнородные отходы бумаги, списанная документация;
Отходы фото- и кинопленки, рентгеновская пленка;
Абразивные материалы;
Горелые земли;
Грунт, в том числе загрязненный опасными веществами;
Резиновые изделия, потерявшие потребительские свойства;
Обрывки тканей, спецодежда, обувь, средства индивидуальной защиты;
Неликвидная продукция.
Выполненная работа
Был проведен химический анализ аргиллита (исследуемой породы), по результатам которого рассчитан состав исходной смеси для получения цементного клинкера, а также определен химический состав готового клинкера. В качестве известкового компонента был выбран мел. Параллельно, на приборе Торопова, была определена удельная поверхность исходных компонентов.
На основании этих данных были рассчитаны основные характеристики цементного клинкера: коэффициент насыщения, кремнеземный и глиноземный модуль. На диаграмме для сравнения также приведены рекомендованные Гипроцементом значения этих характеристик.
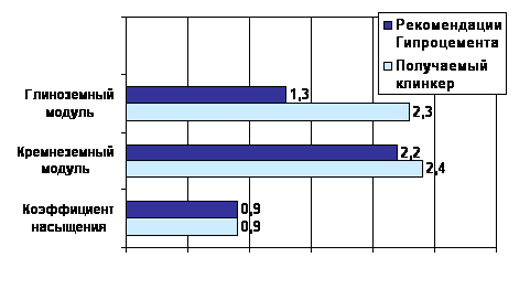 Рис. 2 - Основные характеристики получаемого цементного клинкера
Мы видим, что только значение глиноземного модуля значительно отличается от рекомендованного. Глиноземный модуль - это отношение оксида алюминия содержащегося в клинкере к содержанию оксида железа [2].
Из этого следует, что корректировать состав исходной смеси можно либо уменьшением содержания оксида алюминия, либо введением дополнительного количества оксида железа. Работы ведутся в обоих направлениях.
У нас кафедре разработана технология извлечения из отходов добычи угля оксида алюминия - сырья для производства металлического алюминия. Остаток от извлечения предлагается использовать для получения цементного клинкера.
Вторым направлением были смеси, в состав которых вводилось дополнительное количество оксида железа.
Смеси обжигались в электрических печах сопротивления. Причем обжиг велся по двум тепловым режимам.
До температуры оба режима совпадают, причем скорость подъема температуры от 800 до 1100 градусов уменьшена, для проведения процесса декарбонизации.
При достижении температуры обжига для второго состава делалась изотермическая выдержка, которая отсутствовала для первого состава.
Обожженный клинкер разбивался на куски и охлаждался в специальных условиях.
Затем клинкер измельчался вместе с гипсовым камнем, просеивался через сито № 008.
Дополнительно измерялась удельная поверхность полученного цемента.
Из полученного цемента по стандартной методике формовались образцы для испытания их прочности на сжатие.
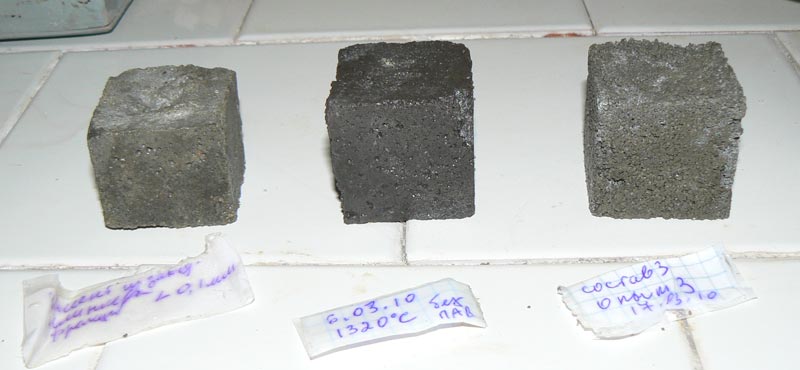
Рис. 3 - Образцы для испытания прочности на сжатие
В настоящее время испытана прочность на сжатие четырех образцов.
Основные результаты
Полученный цемент показывает неплохие прочностные характеристики. Условия получения цемента еще не до конца подобраны. В дальнейшем планируется провести ряд экспериментов с различной температурой и режимами обжига, различными значениями основных характеристик цементного клинкера. Также планируется проведение экспериментов с различными режимами помола (изменение времени помола; изменение интенсивности помола; использование различных интенсификаторов и пр).
После достижения значений прочности получаемого цемента соответствующих марке М300 и выше, планируется проведение экспериментов на соответствие свойств получаемого цемента значениям, указанным в ДСТУ Б В.2.7-46-96 [8].
Заключение
Выполнение намеченных работ и получение конкретных результатов позволит разработать технологию утилизации терриконов, что для Донецкого региона является экологической задачей номер один.
В ходе проведения экспериментов были получены навыки работы с прибором Торопова для измерения удельной поверхности веществ, освоены основные методики испытания цемента на соответствие ДСТУ Б В.2.7-46-96. Была написана программа на Visual Basic for Application, при помощи которой, были рассчитаны сырьевые смеси для получения цемента (до четырехкомпонентных смесей, включительно). Рассчитывались основные характеристики получаемого цементного клинкера: коэффициент насыщения, глиноземный и кремнеземный модули.
Литература
- Бурковський Ю.А. Сухой способ производства портландцементного клинкера. - Госстройиздат, 1958.- 267с.
- Бутт Ю.М. Технология вяжущих веществ. - М.: Высшая школа, 1965.-619с.
- Власов П.А. Транспорт и хранение цмента. - Госстройиздат, 1959.-227с.
- Коновалов П.Ф. Физико-химические исследования цементов. - Госстройиздат, 1960.-427с
- Окороков С.Д. Расчет портландцементной сырьевой шихты. - Стройиздат, 1975.-329с
- Пащенко А. А. Мясникова Е. А. Теория цемента. - К.: Будівельник, 1991. - 168с.
- Бутт Ю. М. Тимашев В. В. Портландцемент. - М.: Стройиздат, 1974. - 328с.
- ДСТУ Б В.2.7-46-96. Будівельні матеріали. Цементи загальнобудівельного призначення. Технічні умови. - Київ: Держкоммістобудування України, 1996. - 72 с.
- Краткий справочник технолога цементного завода под ред. проф. И. В. Кравченка М.: Стройиздат, 1974. - 304с
- Колокольников В. С. Производство цемента. - М.: Высшая школа, 1967.-303с.
- Урьев Н. Б, Дубинин И. С. Коллоидные цементные растворы. - Л.: Стройиздат, 1980. - 192 с.
- Квалификационная работа магистра Папуна Н. В. Переработка терриконов методом агломерации. Портал магистров ДонНТУ [Электронный ресурс] Режим доступа: www/URL: http://masters.donntu.ru/2008/fizmet/papuna/library/index.htm
|
|