Автореферат
Актуальность
Предприятия коксохимической промышленности тесно связаны с угольной промышленностью, а также с металлургической промышленностью, поэтому большая часть предприятий этих отраслей находится в Донецкой области. Эта тесная связь обеспечивает большую часть катастрофической экологии Донецкого региона. Чрезвычайно важным фактором, существенно влияющим на территориальную организацию всей социально-экономической жизни и эффективность производства, является экологическая обстановка. В последние десятилетия в Украине она существенно ухудшилась. Одним из основных факторов, повлиявших на экологическую обстановку, является использование коксохимической промышленностью устаревших технологий.
Коксохимия - одна из отраслей промышленности, значительно загрязняющая окружающую среду. В Донецкой области инфраструктура коксохимической промышленности представлена 7 крупными предприятиями из 13 функционирующих на Украине: ОАО «Авдеевский коксохимический завод», ОАО «Донецккокс», ОАО «Маркохим», ОАО «Енакиевский коксохимический завод», ОАО «Макеевский коксохимический завод», ОАО «Ясиновский коксохимзавод», АОЗТ «Коксан» [1]. Состав выбросов отличается широким спектром загрязнителей. Процесс производства кокса сопровождается образованием твердых и жидких отходов, сточных вод и газообразных выбросов в атмосферу, являющихся источниками загрязнения окружающей среды.
Длительный мониторинг загрязнения окружающей среды возле предприятий коксохимического производства показал нестабильность его распределения, как в пространстве, так и во времени. Поэтому исследование изменения экологической ситуации на коксохимических заводах, как составляющей части промышленной нагрузки в Донбассе является очень актуальным.
Идея работы. Главными факторами ухудшения экологии коксохимического производства являются качество угля и нестабильность работы предприятий.
Целью работы является изучение взаимосвязи состава и интенсивности загрязнения от технологии переработки и качества углей.
Задачи работы
-
Изучение зависимости состава и объема выброса по стадиям технологического процесса коксохимического производства.
-
Оценка вклада каждого источника выброса в суммарном загрязнении окружающей среды коксохимическим заводом.
-
Исследование распределения серы в углях.
-
Изучение качества углей поступающих на предприятие.
-
Разработка рекомендаций по снижению экологических последствий коксохимического производства.
Объект научного исследования
Авдеевский коксохимический завод относится к числу крупнейших коксохимических предприятий Европы, который входит в десятку наиболее опасных экологических предприятий Донецкой области.
Предметом исследований является экологическая оценка качества сырья для коксохимической промышленности.
Научная ценность (новизна) работ
Научная ценность работы заключается в связи выбросов коксохимического предприятия с качеством углей поступающих из Донецкого угольного бассейна.
Практическое значение работы
Результаты работы могут быть использованы в учебном процессе, а также на коксохимических предприятиях для оценки качества углей и экологических последствий их использования.
Апробация результатов работы
VII международная научно-практической конференция-выставка «Экологические проблемы индустриальных мегаполисов». Доклад на тему: Влияние коксохимического производства на окружающую среду.
Публикации: подготовлена к публикации статья «Основные источники загрязнения окружающей среды коксохимическим производством».
Обзор состояния исследований по данной теме
Охрана окружающей среды от загрязнения вредными выбросами коксохимических предприятий в настоящее время стала одной из важнейших проблем.
Технические направления в проектировании коксохимических предприятий кроме экономических и технологических проблем, призваны решать задачи эффективной защиты воздушного бассейна. Эти факторы учитываются как при проектировании, так и при расширении (реконструкции) действующих коксохимических производств.
Процесс производства кокса, улавливание и переработка химических продуктов сопровождаются образованием твердых и жидких отходов, сточных вод и газообразных выбросов в атмосферу, являющихся источниками загрязнения окружающей среды.
Основным направлением в решении проблемы защиты окружающей среды является совершенствование технологических процессов с доведением их до безотходного или малоотходного производства. Однако, учитывая, что существующая технология коксования сохранится в ближайшие годы, основной задачей по защите окружающей среды в коксохимическом производстве является вывод из эксплуатации устаревших агрегатов и оборудования и замене их современными, оснащенными эффективными природоохранными установками.
В книге «Технология коксохимического производства» Г.Д. Харламовича, А.А. Кауфмана даны представления о научных основах коксохимического производства, принципах создания и проектирования оптимальных технологий, перспективах развития коксохимии, особенностях и направлениях эффективной эксплуатации основных пределов коксохимического предприятия и принципах подбора условий такой оптимальной эксплуатации.
В книге «Технология коксохимического производства» Р.Е. Лейбовича, Е.И. Яковлева изложены основы технологии коксохимического производства. Рассмотрена сырьевая база коксования, свойства каменных углей и технологические схемы подготовки углей при коксовании, включая их обогащение. Приведены основные данные о получении угольной шихты и кокса постоянного качества, технологии улавливания и переработки химических продуктов, получаемых из угольной шихты при её коксовании в современных угольных печах. Рассмотрены вопросы охраны окружающей среды.
На состав выбросов влияет качество углей поступающих на коксохимические заводы.
В.Я.Долгий, А.А.Кривченко, В.А.Долгая рассматривали, показали качества углей (зольность, влажность, сернистость, выход летучих веществ, теплота сгорания), добытых на шахтах Украины. Они отметили, что основной проблемой качества углей поступающих на производство, является высокое содержание в них серы.
Изучению генезиса, содержания и распределения серы посвящены работы Кизильштейна Л.Я., Юдовича Я.Э. и другие. Они отличают наличие нескольких групп элементов, в том числе и серы, которые концентрируются в различных частях углей.
Изучением серного колчедана (пиритной серы) занимались Клер В.Г., Дорофеев А.П., Румянцева О.Г. и другие.
Работа С.Г.Аронова освещает вопросы использования для коксования донецких газовых и длиннопламенных углей. В работе рассматриваются процессы термического разложения углей и образования кокса, газа и химических продуктов коксования. Обобщение данных приводит к выводу о целесообразности и большой народнохозяйственной эффективности применения газовых и длиннопламенных углей для коксования.
Работа А.З. Юровского посвящена установлению взаимосвязи между разновидностями серы (общей, органической и колчеданной). Подтверждено, что в углях малосернистых количество органической серы превышает количество колчеданной. С увеличением содержания колчеданной серы повышается и количество серы органической, но темпы нарастания последней заметно более медленны. В углях многосернистых и высокосернистых колчеданная сера определенно доминирует над органической серой.
Г.П. Пушкарев, В.Д. Плетень рассматривали мероприятия по снижению загрязнения окружающей среды в коксохимическом производстве, а именно:
- внедрение глубокой очистки газа от сероводорода, с целью обеспечения допустимых концентраций на границе санзоны;
- строительство установок биохимической очистки фенольных вод, для уменьшения выбросов в атмосферу при тушении кокса;
- сухое тушение кокса, при котором значительно сокращается число выбрасываемых ингридиентов.
Обзор работ по вопросам обогащения угля позволил установить, что сегодня большое внимание уделяется выявлению причин образования пиритной серы и делаются попытки её извлечения.
Методика исследований
-
Характеристика технологического процесса коксования углей, выявление загрязнений на каждой стадии
-
Обработка данных качественного состава углей поступающих на коксохимическое предприятие
-
Исследование распределения серы в углях
Полученные результаты
На Авдеевский КХЗ поступают рядовые угли марок ДГ, Г, Ж, К, ОС и Т из различных угленосных районов Донбасса, содержание серы которых колеблется в больших пределах – от 0,7 до 5,2 % (табл.1).
Табл. 1. Качественные показатели углей поступающих на Авдеевский КХЗ
Марка угля |
Зольность, Аd,% |
Среднее значение зольности,% |
Массовая доля общей серы Sdt, % |
Средняя массовая доля общей серы Sdt, % |
Марка ДГ |
32,1-44,0 |
38,0 |
1,1-1,7 |
1,4 |
Марка Г |
25,5-50,0 |
37,8 |
1,1-4,7 |
2,9 |
Марка Ж |
22,6-54,0 |
38,3 |
1,0-5,2 |
3,1 |
Марка К |
30,5-45,0 |
37,8 |
0,7-3,2 |
2,0 |
Марка ОС |
37,0-46,0 |
41,5 |
2,3-3 |
2,7 |
Марка Т |
38,0-42,0 |
40,0 |
1,5-2,2 |
1,9 |
Основным свойством коксующихся углей является спекаемость. Это - способность угля при нагревании без доступа воздуха образовывать из разрозненных зерен твердый остаток. Это свойство определяется с помощью специального показателя – толщина пластического слоя, измеряется в мм. Расчет этого показателя для определения марки углей выполняют пластометрическим методом (метод Сапожникова Л.М. и Базилевич Л.П.) [2].
Наиболее высокий показатель коксуемости имеют угли марки Ж (толщина пластического слоя 25-35мм). Они являются главным компонентом шихты, обеспечивая хорошую спекаемость и прочность кокса. Однако при повышенном их содержании кокс получается трещинный и мелкокусковый. Угли марки К, также характеризуются хорошей спекаемостью. Толщина пластического слоя составляет 18-24 мм. Коксовые угли в шихте придают коксу высокую механическую прочность и однородную кусковатость. Отощенно-спекающиеся угли (марка ОС) – одна из лучших отощающих компонентов в коксовых шихтах. Толщина пластического слоя составляет 6-12 мм. Для газовых углей (марка Г) характерна небольшая толщина пластического слоя 10-15мм. Применение газовых углей в шихтах коксохимических заводов, производящих металлургический кокс, повышает конечную усадку коксового пирога и способствует легкой выдаче его из печи, а также увеличивает выход газа и химических продуктов. При повышенном содержании газовых углей в шихте выход кокса уменьшается. Угли длиннопламенные газовые (марка ДГ) являются переходными между углями марок Д и Г. От длиннопламенных углей они отличаются наличием спекаемости (толщина пластического слоя 6-9 мм), а от газовых – более незначительной хрупкостью и повышенной механической прочностью. Угли марки ДГ относят к группе энергетических углей. Для участия в коксовых шихтах они мало пригодны, т.к. образующийся кокс отличается низкой механической прочностью и повышенной реакционной способностью. Длиннопламенные угли (марка Д) не спекаются или имеют небольшую спекаемость (у=0-5 мм) и относятся к энергетическим углям. Угли тощие (марка Т) характеризуются отсутствием спекаемости. Используются в качестве отощающей добавки в шихте.
Изменение толщины пластического слоя от марок углей показано на рис. 1.
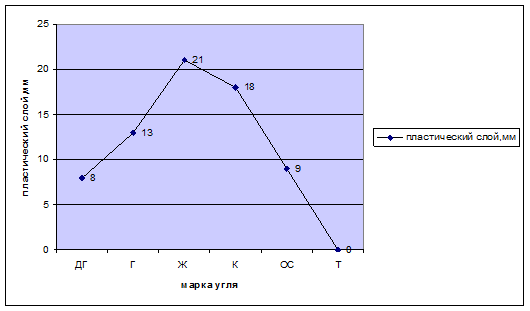
Рис. 1. Зависимость толщины пластического слоя от марки угля
Дозирование углей различных марок имеет большое значение для последующего составления угольной шихты заданного состава. Соотношение марок углей в шихте зависит от качества выплавляемой руды. Для получения высококачественного кокса необходимо производить шихтовку (смешивая угли марок ДГ, Г, Ж и ОС). Измельчение шихты проводится для повышения её однородности, что способствует улучшению качества кокса. При этом отощенные спекающиеся угли являются отощаюшим компонентом шихты, снижающим трещиноватость кокса, способствуют увеличению его крупности.
После шихтования углей ДГ, Г, Ж и ОС смесь должна иметь содержание серы не более 2,2%. Это достигается путем шихтования в пределах одной марки. Таким образом, качество получаемой шихты для коксования зависит не только от точной дозировки компонентов шихты, но и от постоянства качества углей (сернистость, зольность).
Основной экологической проблемой при использовании углей является содержание серы. Это является и одним из важнейших критериев пригодности угля для коксования. В шихте содержание серы не должно превышать 2,2%.
В углях Донецкого бассейна содержание серы колеблется в широких пределах. Малосернистые (Stf 1,5%) среднекарбоновые угли распространены преимущественно в юго-западной части бассейна, в центральных и северных районах преобладают сернистые (Stf 2,5-3,5%) и высокосернистые (более 3,5%) угли [3].
Различают следующие разновидности серы в углях: сульфатная, колчеданная (пиритная), органическая и элементарная. Сульфатная сера в углях Донецкого бассейна содержится в небольшом количестве (до 0,2%). Она представлена главным образом сульфатом кальция (CaSO4) и в небольшом количестве сульфатом железа (FeSO4) и других металлов. Встречаются сульфаты в виде тонких пленок по плоскостям напластования угля. Пиритная (колчеданная) сера – основной вид минеральной серы в углях, на её долю в среднем приходится 62 % общего содержания серы. Пирит представляет включения в угле в виде примесей, доступных для обогащения механическим способом. Формы включений пирита в угольные пласты различны. Пирит, образовавшийся в период угленакопления, распределён по угольному веществу равномерно, в тонкодисперсной форме и, как правило, связан с органической массой угля. Пирит, образовавшийся после прекращения процесса угленакопления путём инфильтрации, распределён по трещинам усыхания грубодисперсно, локализовано – в виде линз, желваков, зёрен, гнёзд [4]. Органическая сера равномерно распределена по всему угольному веществу, ее невозможно выделить. При обогащении диапазон содержания органической серы в углях 0,3—0,5%, но встречается 2,5—3%. Такое бывает даже в пределах одного пласта на близлежащих участках. Это говорит о том, что органическая сера образовалась не только за счет серы исходного растительного материала. Полагают, что источниками образования вторичной серы была элементарная сера, которая при соответствующих условиях переходила в составляющую углей.
А.З.Юровский установил следующую зависимость между содержаниями общей и пиритной серы в углях Донецкого бассейна (при условии содержания общей серы не более 5%):
Sпир = - 0,38 + 0,737 Sобщ
Общее количество серы в углях распределяется почти поровну между пиритной и органической серой, а удельное количество сульфатной серы не превышает 10-15% от общей серы [5]. В углях малосернистых количество органической серы превышает количество колчеданной. С увеличением содержания колчеданной серы повышается количество серы органической, но темпы нарастания содержания последней заметно более медленны. В углях многосернистых и высокосернистых колчеданная сера определенно доминирует над органической [6].
Технологический процесс производства кокса и улавливания химических продуктов коксования на Авдеевском КХЗ включает следующие стадии (анимация):
- подготовительную;
- термическую;
- улавливающую и перерабатывающую.
Рис. 2. Технологический процесс производства кокса и улавливания химических продуктов коксования. GIF-анимация, 8 кадров, зацикленное повторение, 7,5 кб
Каждая стадия имеет как общие с другими, так и характерные только для неё загрязняющие вещества (табл.2).
Табл. 2. Элементы загрязнители по стадиям технологического процесса
Стадии |
Элементы загрязнители |
Общие |
Специализированные |
Подготовительная |
Диоксид серы
Оксид азота
Оксид углерода
|
Пыль
|
Термическая |
Бенз(а)пирен, пыль,
цианистый водород,
фенолы, аммиак
|
Улавливающая
и
перерабатывающая |
Пиридин, аммиак,
бензол, фенолы,
пары нафталина,
цианистый водород, сероводород
|
На подготовительной стадии готовится шихта для коксования. После приема угля в углеподготовительном цехе производится усреднение состава и обогащение углей. Здесь же осуществляется составление и измельчение шихты.
С целью стабилизации качества производится усреднение состава угольной шихты.
Обогащение углей для понижения содержания в них минеральных примесей проводится методами отсадки, сепарации и флотации. Методом отсадки обогащается до 50% углей, флотации – 15%, сепарации – 35%. При переработке угля на обогатительных фабриках достигается значительное снижение серы: до 20% при обогащении на концентрационных столах и до 20—22% на отсадочных машинах. В основном удаляется колчеданная сера, содержащаяся в многосернистых углях, причем максимальный эффект обессеривания дают угли марки Ж.
В углях Донецкого бассейна преобладающее количество пирита представлено зернами размером до 15 мк, поэтому при обогащении физическими методами, используемыми в промышленном масштабе (отсадка, тяжелосредные сепараторы, гидроциклоны, противоточная сепарация и др.), снижение содержания серы в концентратах невелико. Для глубокого обогащения по сере необходимо раскрытие лиритных зерен путем дробления угля до 3 мм и менее. Эффективное обогащение по сере дробленого угля осуществляется только при таких методах обогащения, которые обеспечивают точность поддержания плотности разделения и четкость разделения мелких классов. Таким требованиям отвечают химико-гравитационный и центробежный методы десульфурации, однако они отличаются сложной технологией, большой энергоемкостью и высокой себестоимостью.
Кроме того, существуют химический и бактериологический методы обессеривания угля. Химические методы, основанные на действии окислительных и реже восстановительных агентов, приводят к переводу серы в газообразные или растворимые в водных средах продукты. Например, паровоздушная обработка при 200—350 °С углей Донбасса переводит 55% исходного количества серы в SO, с примесью SO. Под действием водных растворов окислителей (например, азотная кислота) из угля извлекаются практически все неорганические и свыше 70% органических соединений серы. Заметная степень обессеривания угля достигается при бактериологическом выщелачивании хемоавтотрофными микроорганизмами — до 90% пиритной серы [4]. Однако эти методы у нас не применяются ввиду их дороговизны.
Для обеспечения возможно более высокой плотности загрузки шихты выдерживают оптимальную степень измельчения в шихте. Оно достигается по двум схемам:
- измельчается вся масса шихты,
- учитывается различная твердость измельчаемого материала, при этом каждый компонент шихты измельчается отдельно.
Заключительной операцией приготовления угольной шихты для коксования является смешение компонентов, которое осуществляется в смесительных машинах различной конструкции. Если в процессе шихтования происходит только усреднение содержания серы в углях, то его снижение осуществляется на всех этапах производственного цикла «обогащение — коксование — доменная плавка».
При этом в атмосферу выделяется пыль, из дымовых труб гаража размораживания - диоксид серы, оксиды азота, оксид углерода.
На термической стадии угольная шихта подвергается разложению в коксовых печах, куда подается обратный коксовый газ в смеси с воздухом. Наиболее интенсивной по загрязнению атмосферы является стадия тушения кокса, на которой дополнительно выделяется пыль, диоксид серы, сероводород, цианистый водород, оксиды азота, оксид углерода, фенолы, аммиак и бенз(а)пирен.
Парогазовая смесь выделяющихся летучих продуктов (до 25 % от массы угля) отводится через газосборник для улавливания и переработки.
На стадии улавливания коксовый газ, выделяющийся в процессе коксования шихты, последовательно проходит отделения конденсации и охлаждения коксового газа, аммиачно-сульфатное и бензольное отделение, в которых улавливаются пиридин, аммиак, бензол, фенолы, цианистый водород. При этом эти же вещества выделяются из воздушек аппаратов и емкостей указанных отделений цехов улавливания и попадают в атмосферу.
На стадии переработки из смолы, образующейся в основном при пирогенетическом разложении первичной смолы в процессе коксования, при последовательном нагревании и испарении отбираются поглотительная, фенольная, нафталиновая, антраценовая фракции. При этом в атмосферу выделяются пары бензола, фенола, сероводорода, нафталина.
Промышленное использование коксового газа требует очистки от сероводорода вакуум-карбонатным способом, в специальных цехах. При этом в атмосферу выделяются диоксид серы, сероводород, цианистый водород, бензол, фенол.
На ОАО «Авдеевский коксохимический завод» установлено большое количество источников выбросов загрязняющих веществ в атмосферный воздух, их разделяют на организованные и неорганизованные. Организованные выбросы загрязняющих веществ – это газоходы, воздуховоды, заводские трубы, специально отведенные от стационарных источников загрязнения. Основное загрязнение поступает из организованных источников. Неорганизованными являются выбросы, возникающие в результате негерметичности технологического оборудования, газоотводящих устройств, открытых источников.
Постоянным мониторингом проводимым предприятием установлено, что в атмосферу выбрасываются следующие вредные ингридиенты: твердые частицы (пыль), диоксид серы, оксиды азота, оксид углерода, аммиак, фенол, сероводород, цианистый водород, бензол, нафталин. Общими загрязняющими веществами для всех стадий технологического процесса являются диоксид серы, оксиды азота, оксид углерода (см. табл. 2).
Наиболее остро стоит проблема выбросов диоксида серы и сероводорода. Так в 2009 году выбросы SO2 составили 1854,371 т/год, а выбросы H2S – 27,393 т/год. Количество выбросов зависит от качества углей поступающих на коксование, технологии производства продукции завода. Трубы коксохимического завода имеют большую высоту, обеспечивающие их оседание на значительном расстоянии от источника. Воздействие выбросов завода на окружающую среду распространяется на прилегающий район на расстояние до 20-25 км.
Нами установлено, что содержание органической серы после шихтовки в пределах марок практически не снижается. Поскольку большое содержание органической серы связано с жирными углями, являющимся основным составляющим компонентом шихты, то следует контролировать район поступления угля. Для улучшения экологической ситуации рекомендовано ограничить поступления углей марки Ж из северных и центральных районов Донецкого бассейна, (Краснодонский угленосный район) имеющих высокосернистые угли.
Практические выводы и рекомендации
1. Изучена зависимость состава и объема выброса по стадиям технологического процесса.
2.Рассмотрено распределение серы в углях.
3. Оценен вклад каждого источника выброса в суммарном загрязнении окружающей среды.
4. Изучено качество углей поступающих на коксохимический завод.
5. Разработаны рекомендации по снижению экологических последствий.
Литература
-
Аналітична довідка про підприємства, які є найбільшими забруднювачами навколишнього природного середовища Донецької області - Наш край, 2008.- №16- с.2
-
Лейбович Р.Е. Технология коксохимического производства/ Р.Е.Лейбович, Е.И. Яковлева, А.Б. Филатов. – М.: Металлургия,1982. – 360с.
-
Миронов К.В. Справочник геолога-угольшика/ К.В. Миронов. – М.: Недра, 1991. - 363с.
-
Долгий В. Я. Содержание общей серы в угольных пластах на шахтах Украины/ В.Я.Долгий, А.А. Кривченко, М.Д. Шамало - «Уголь Украины», 2000. - №1- с.44-47
-
Юровский А.З. Сера каменных углей./ А.З. Юровский. – М.: 1960. - 295с.
-
Буцик Ю.В. Методика разведки угольных месторождений Донецкого бассейна/ Ю.В. Буцик. – М.: Недра, 1972. – 340с.
-
Юровский А.З. Сера каменных углей/ А.З. Юровский – М.: Издательство наук СССР, 1960. – 295с.
-
Забавин В.И. Каменные и бурые угли/ В.И. Забавин. – М.: Наука,1964. – 198с.
-
Аронов С.Г. Определение качества и пригодности углей для коксования/ Аронов С.Г. –М.: Издательство наук СССР, 1951.- 67с.
-
Аронов С.Г. Сера. Извлечение из промышленных и отбросных газов/ Аронов С.Г.– М.: Издательство наук СССР, 1940. – 180с.
-
-
Статьи об Украине. «Каменный и бурый уголь»: [Електронный ресурс]. – Режим доступа: http://www.photoukraine.com/russian/articles?id=85
|