D. MAZURKIEWICZ
Lublin University of Technology, ul. Nadbystrzycka 36, 20-618 Lublin, Poland
Problems of numerical simulation of stress and strain in the area of the adhesive-bonded joint of a conveyor belt
Belt conveyors are commonly used in-factory transportation devices built of sections of belt (e.g., a fabric-rubber belt) bonded into a continuous loop. Conveyor belt joints are exposed to substantial dynamic loads during the long time of their operation. Taking into account the fact that ensuring a high durability of conveyor belt joints is tantamount to guaranteeing their reliable operation and that the results of research conducted so far fail to provide unambiguous solutions to a number of problems that emerge in this case, it is advisable that advanced studies using computer techniques should be conducted within this area. Of particular help in the search for new structures and optimum methods for joining conveyor belt sections is finite element analysis, which, however, entails a number of problems. This paper describes the circumstances of occurrence of these problems and potential solutions to them. One important problem in FEM modeling is appropriate definition of the models of the analyzed materials. In the case of conveyor belt adhesive-bonded joints composed of rubber and a gum rubber adhesive, the analyses found in the literature, as a general rule, assume the hyperelastic material model based on the Mooney-Rivlin law, which, however, is a fairly arbitrary choice made without verification against actual strength test data. Rubber is a unique material, capable of very large deformations, by virtue of which it is counted among hyperelastic materials. Such materials require appropriate constitutive models and a reliable choice thereof in each particular case. Adequately precise modeling of the behavior of rubber materials still remains an open question. However, access to strength test data makes it possible to check experimentally which of the available theoretical models best reproduce the behavior of the modeled material. For that purpose, the available hyperelastic material models were tested separately for each constituent rubber material of the analyzed conveyor belt adhesive joint. The models were assessed with regard to the degree of their conformity with experimental data by analyzing the behavior of the hyperelastic material in a given case based on the constructed reaction curves using selected strain energy potentials for the available test data.
Keywords: adhesive-bonded joint, rubber material models, hyperelastic materials, numerical modelling
1. Introduction
Belt conveyors are basic in-factory transportation devices that are used by various production and service companies. Belt transport, due to a number of its merits, is used in numerous branches of industry, including, among others, mineral processing plants, metals-producing, extractive, cement-and-lime, and paper industries, sea and inland ports, construction industry, power plants, transshipment points, as well as agriculture and sugar plants. Belt conveyors (Figure 1) enable fast and efficient transport of loose materials of different physical-mechanical properties, with a low degree of their degradation during high-speed and long-distance transfer [1–7].
Conveyor belts, which are continuous loops, are made up of sections joined by cold vulcanization (bonding) or heat curing. Joining of belts using these methods is a toilsome activity, which, however, ensures a high, though not always sufficient, strength of the joint. In high-performance belt transport systems, multi-ply belts are joined using stepped lap joints (Figure 2). Joining of belt sections is an important issue and a problem for persons working in belt conveyor maintenance services as belts require constant shortening, lengthening, or relocation, which is connected with making ever new joints, not only as a result of service activities. The particular significance of this issue does not only follow from the growing number of long conveyors which transport, at a high speed, vast bulks of different kinds of materials, but is also connected with the large number of new belt section joints made every year. According to data from FTT Stomil Wolbrom plc. [8], this company’s service currently makes an average of over 1000 belt joints a year both in Poland and abroad.
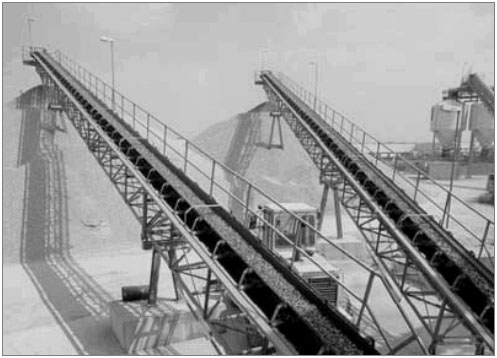
Fig. 1. A typical belt conveyor structure used for in-factory transport [9]
The quality of joints made in that way is often different even for one conveyor as it depends on a number of factors including the structure of the joint, the joining method, and the properties of the materials used as well as the care on the part of the staff to retain the technological parameters of these materials as included in the manufacturers’ instructions manuals.
To ensure proper strength of a typical adhesive joint, a number of studies and analyses are normally carried out in the areas of maintenance, joining technology, and the possibilities of monitoring and assessment of the durability of the joint in industrial conditions [6, 7, 11–16]. It results from the broad range of issues connected with adhesive bonding which involve the theory of adhesion, adhesive manufacturing technology, and adhesive joining technology. As Godzimirski [17] observes, when an analysis of the strength of adhesive joints is carried out, an account should be taken not only of their short-term strength, but also of their long-term strength, fatigue strength, resistance to dynamic loading, the effect of aging on their load capacity, etc.
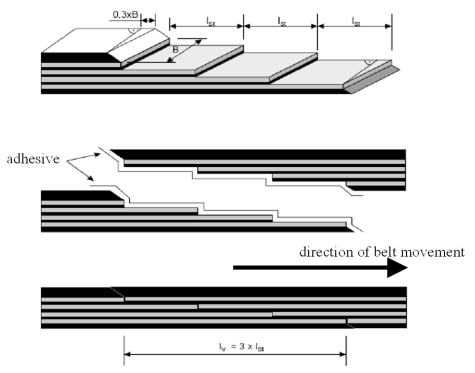
Fig. 2. A diagram of a method of joining a four-ply belt in accordance with a brochure of Metso Minerals company [10]
These problems are particularly important in the case of conveyor belt joints, which are exposed to significant dynamic loads over the long period of their operation. Taking into account the fact that ensuring a high durability of conveyor belt joints is tantamount to guaranteeing their reliable operation and that the results of research conducted so far fail to provide unambiguous solutions to a number of problems that emerge in this case, it is advisable that advanced studies using recent developments in computer techniques should be conducted within this area. Of particular help in the search for new structures and optimum joining of conveyor belt sections is finite element analysis, which, however, entails a number of problems, the circumstances of the occurrence of which and potential solutions to which are described in this publication.
2. The goals of numerical analysis of belt joints
The most important problems of belt transport in the current period are issues concerning the necessity to reduce energy consumption and to increase durability. Particularly significant is the strength and durability of conveyor belt joints since, despite numerous research and implementation studies, it still constitutes an important problem that every belt conveyor user has to face. One of the possibilities of increasing the durability of the belt and its joints is, among others, reduction of longitudinal stresses in the belt. According to Jabłoński [18, 19], studies of fatigue life of joints indicate a strong effect of longitudinal stresses in the belt on its durability and strength. That is why a lot of design work is being carried out which aims at working out appropriate tensioning device solutions. A second potential direction of research in this case is one aimed at increasing the durability and strength of the joint between belt sections by means of analysis and assessment of the distribution of stresses in the joint and the influence that the very structure of the joint has on them. In this case, interesting results may be expected from the use of the finite element method.
In all types of structures in which adhesive-bonding has been used as a method for joining elements, the durability of the joint should be treated as one of the basic indexes of their operational usefulness. A potential solution to this problem is looking for the indispensable information by analyzing the distribution of stresses and strains in the joining area using numerical methods. It can be expected here that identification of stresses and strains in the adhesive joint will allow its appropriate design, selection of constituent materials and their properties, and will make possible specification of the manner in which the joint should be made in a purely structural context. An appropriate analysis may be conducted by means of numerical modelling using the classical method of finite elements, which is a calculation method based on matrix arithmetic [20]. The relations between forces and displacements are expressed in this method by means of the stiffness matrix, whose constituent elements include material constants describing the mechanical properties of the modelled materials.
3. Numerical analysis of stress and strain in the conveyor belt joint
Numerical analysis used in developing new design solutions for belt joints is aimed, among others, at estimating the possibility of using the developed FEM model of a joint for predicting the durability and strength of the joint as well as the possibility of using it at the stage of structural designing of the joint. It can be expected that the use of FEM-based numerical simulation in this case will enable precise analysis of stress distribution in the joining area of the selected conveyor belt, thus making possible the identification of areas of stress concentration or a stress distribution that would be unfavorable from the point of view of joint durability. It is believed [21] that this method can be treated as a significant expansion and supplementation of the analytical methods for assessing stress and strain, and as one that simultaneously allows reliable and precise determination of the share of the individual stress components, which, as a rule, constitutes important information in the design and optimization of adhesive joints. Of no mean significance is also the possibility this type of modelling gives of predicting the strength of adhesive joints of different geometry and different constituent material parameters without the need to use troublesome and, in the case of conveyor belts, expensive destructive tests.
To conduct a strength analysis based on determining stress and strain in the area of the analyzed adhesive joint connecting conveyor belt sections, two models of the joint were worked out and subjected to numerical analysis according to the assumed goal using material data obtained during strength tests. At the stage of numerical modelling, von Mises stresses (reduced stresses) were analyzed, which in a uniaxial stress state (stretching of the belt joint) caused identical effort as the corresponding complex stress state represented by them. The reduced stresses in the analyzed case were determined on the basis of the Huber-Mises-Hencky (H-M-H) hypothesis:

where:
are principal stresses.
3.1. The scope of calculations and numerical characteristics of an adhesive joint
The finite element method, belonging to a group of most popular computer-aided methods used for solving mechanical issues, consists in replacing a continuous model of the analyzed mechanical system with its discrete model (Figures 3 and 4), which in a mathematical description assumes the form of a set of algebraic Equations [22].
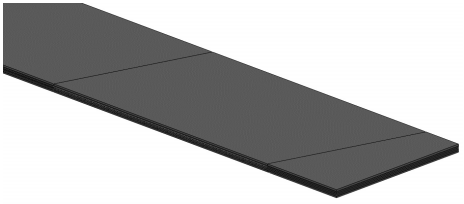
Fig. 3. A general view of a fragment of a spatial FEM model of an adhesive-bonded joint of a conveyor belt
An important issue in FEM modelling is appropriate definition of the models of the analyzed materials. In the case of rubber and gum rubber adhesives, the analyses found in the literature usually employ the hyperelastic material model based on the Mooney–Rivlin law [11, 23–27], which, however, is a fairly arbitrary choice made without verification against actual strength test data.
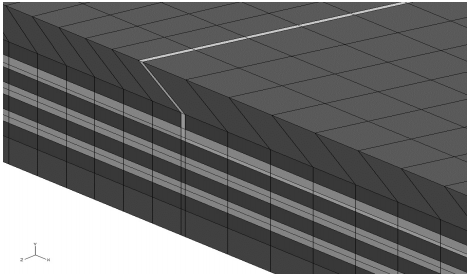
Fig. 4. A fragment of a sample spatial model of an adhesive-bonded joint
Rubber, however, is a unique material, capable of very large deformations, by virtue of which it is counted in the category of hyperelastic materials, requiring appropriate constitutive models and a reliable choice of those models in each particular case. Hyperelasticity is defined [28] as the ability of a material to undergo large elastic deformation under small forces, without losing its original properties. A hyperelastic material shows non-linear behaviour, which means that its deformation is not directly proportional to the load applied. Linear models of elasticity, totally inadequate in the discussed case, assume a linear strain-stress relation and small deformation values. Rubber, on the other hand, as a material having a high elastic deformation, is analyzed as a separate material group. That is why in the last decade a number of publications [26–31] have been devoted to the issues of rubber materials, their models, and the modelling of their behaviour in different structures and conditions. In spite of this significant number of publications in reputed international scientific journals and books, adequately precise modelling of the behaviour of rubber materials, as Diani et al. [26] note, still remains an open question. What we have at our disposal are a number of mathematical models describing the behaviour of such materials, which were developed over the past century starting from the time when Mooney presented his theory of large elastic deformations.