Вплив деяких факторів на довговічність сталевих канатів
Автор: І. Г. Міренський; д.т.н. В. М. Шавкун (ХНАГХ)
Источник: Міренський І.Г., Шавкун В.М. Вплив деяких факторів на довговічність сталевих канатів // Коммунальное хозяйство городов (84). – с. 390-397.
Анотація
Розглядається вплив факторів технологічного й експлуатаційного характеру на до-
вговічність сталевих канатів. Пропонуються шляхи підвищення ресурсу скручених ви-
робів, наводиться оцінка їх ефективності.
Для більшості конструкцій вантажопідйомних, будівельних і транспортних машин у житлово-комунальному господарстві канат у
вигляді скрученого виробу є невід’ємною частиною і найчастіше його застосовують як гнучкий елемент. Робота канату та пов’язаних з ним механізмів значно залежить від правильності його конструктивного використання з урахуванням умов експлуатації і точності розрахунку на міцність.
В умовах експлуатації зазначених машин сталеві канати підлягають розтягу та згину. Окремі елементи крученого виробу, що являють собою гвинтові спіралі, зазнають згин, кручення, розтяг і зминання. У процесі роботи обладнання на канат діють знакозмінні навантаження, що викликають втомлюваність вихідного матеріалу, яка є однією з основних причин руйнування сталевих канатів при їх тривалої експлуатації. До втомлюваних явищ додається зношування дротів канату внаслідок їх взаємного тертя в місцях дотику та додаткового зношування зовнішних елементів гнучкого виробу, що стикаються з пове-
рхнею струмка блоку та барабану.
Довговічність сталевих канатів залежить від факторів виробничо го та експлуатаційного характеру. Враховуючи багатофакторність, надати рекомендації, які б ураховували специфіку всіх цих факторів, неможливо. Разом з цим можна намітити шляхи підвищення строку служби сталевих канатів за рахунок поліпшення технології виробництва існуючих конструкцій, правильного їх вибору, технічно грамотної експлуатації та розробки нових конструкцій кручених виробів із урахуванням специфічних умов експлуатації.
До технологічних факторів відносяться якість дроту, матеріали, що застосовуються для змазування, характер звивання та ін. Вихідним матеріалом для виробництва канатів є сталевий дріт. Відомо, що поверхневі шари дроту після волочіння схильні до розтягуючих залишкових напружень, а центральні – до стискуючих. Наявність розтягуючих напружень різко знижує втомлювану міцність дроту і, як наслідок, довговічність канатів.
Одним із найбільш простих способів зняття розтягуючих напружень в поверхневих шарах дроту є його рихтування, яке за існуючою технологією здійснюється після протягування. Треба зазначити, що застосування такого рихтування не вносить змінення в напружений стан дроту, який виникає в процесі волочіння, і крім того, знижує границю його міцності. Виконані дослідження впливу рихтування дроту в процесі волочіння показали поліпшення механічних властивостей вихідного матеріалу при збереженні міцності [1]. Разом з цим, були визначені оптимальні параметри настроювання запропонованої конструкції рихтувального пристрою (відстань між осями роликів складає 10-15 d, де d – діаметр дроту) та раціональну кількість (шість) роликів на кожному пристосуванні. Для підтвердження отриманих теоретичних положень було виготовлено з рихтувального в процесі волочіння дроту дослідні зразки канатів діаметром 17,5 мм типу ЛД-Р і випробувано на портальних кранах. Результати експлуатації показали, що дослідні канати мають на 17-27 % більшу працездатність у порівнянні з виробами з дроту, виготовленого за звичайною технологією.
У процесі виготовлення, експлуатації і збереження канат підлягає змазуванню. При виготовленні змазують осердя розігрітим консистентним мастилом перед подачею на канатозвивальне обладнання, а дроту – в процесі скручування пасм шляхом подачі розігрітого мастила в конус звивання. Зовнішню поверхню каната змазують перед намотуванням на прийомну катушку. У зв’язку з великим різновидом умов експлуатації сталевих канатів для вантажопідйомного обладнання установлюють певну періодичність їх змазування та відповідні змазки. При повторному змазуванні потрібно забезпечити суцільний шар із змазки, оскільки наявність місць без нього призводить до точкової корозії і, як наслідок, знижує довговічність виробу. Встановлено, що строк служби змазувальних канатів на 20-40 % більший, ніж виріб без мастила [2-4]. Параметри звивання гнучких виробів регламентуються стандартом, відповідно до якого канат повинен мати по довжині рівномірний крок звивання всіх елементів.
Величина кроку звивання зовнішнього дроту в пасмах повинна складати не більше 9 розрахункових діаметрів пасм у канатах з лінійним дотиком (ЛД) дротів і в семипасмних металевих осердях, 11 – у канатах з точковим дотиком (ТД), а також тригранопасмних і однопасмних металевих осердях. У спіральному канаті зазначений параметр звивання не перевищує 11 розрахункових діаметрів. Щодо кроку звивання пасм у канаті, то він має складати не більше 6,5 діаметрів канатів у шестипасмних кручених виробах, стренгах і металевих осердях; 7 – у канатах з кількістю пасм більше шістьох, а також виробах по трійного звивання: 7,5 – у фасонопасмних канатах і 16 – стренгах плоского канату. Відносно вибору раціональних параметрів звивання кручених виробів і з метою підвищення їх працездатності розроблено ряд рекомендацій, серед яких необхідно відзначити наступні. Так, П.П.Нестеровим [1] запропоновано всі повиви пасм типу ТД звивати з однаковими початковими напруженнями у крайніх волокнах дротів при відносних здовженнях у межах εзв = (2,35...3,24) %. Виходячи з умов щільного звивання, Д.Г.Житков [1] рекомендує наступні відносні здовження – εзв = (1,7...2,0) %. При визначенні зусиль у шарах сталевих канатів електромагнітним методом В.С.Дирацу [1] прийшов до висновку, що при виробництві пасм слід виходити з рівності кутів звивання без обмеження відносного здовження. У цьому напрямку особливої уваги заслуговує також робота, виконана П.П.Нестеровим і Б.Д.Тиховидовим [1]. У результаті проведених досліджень визначе-
но, що незалежно від конструкції каната слід приймати раціональне значення відносного здовження крайнього волокна дротів, що виходять на поверхню канату εзв= (2,4...3,4) %, при рівності кутів звивання.
Раціональни параметрами, які відповідають зазначеним рекомендаціям, є :
- для канатів типу ТД крок звивання дроту в пасми першого та
другого повивів повинний дорівнювати відповідно 6,1 d1 і 7,25 d2, а
пасм у канат – h =7,0 dк ;
- для канатів типу ЛД-О і ЛД-Р крок звивання дротів у пасму h =8,0 dп і пасм у канат – h = 6,5 dк.
Достовірність рекомендуємих параметрів підтверджена результатами оцінки напрацювання дослідних зразків кручених виробів у лабораторних і промислових умовах на різних типах підйомного обладнання. Відповідно до вимог стандартів, дроти в пасмах канатів і їх пасми повинні мати однаковий натяг при навантаженні. Це можливо лише тоді, коли довжина елементів кручених виробів (дроту, пасм) буде однаковою. У випадку різних довжин при осьовому навантаженні відбудеться перенапруження коротких дротів і пасм, а елементи з надмірною довжиною мають тенденцію до вспучування.
Відомо кілька методів дослідження розподілу зусиль між елементами каната, зокрема, вирізання шарів при розтягу виробу, так званий касетний метод, а також магнітної сепарації та прямої електро тензометрії. Слід зазначити, що ці методи лише фіксують з певною ступеню точності дійсну картину розподілу зусиль в елементах канатів при осьовому розтягу. Для регулювання натягу пасм у канатозви вальних машинах застосовують гальмування за допомогою мотузкових гальм, при цьому контроль за натягом у процесі звивання повністю відсутній. Оскільки отримати рівномірний натяг усіх пасм каната при
такій технології неможливо, було розроблено низку конструкцій приладів, які дозволяють вимірювати зазначений параметр.
Недолік таких приладів полягає в тому, що закладена схема вирівнювання натягу пасм задовольняє вимогам регулювання лише окремих складових і не дозволяє контролювати заданий натяг у процесі звивання каната. З метою усунення вказаного недоліку розроблена та пройшла заводські випробування електронна система автоматичного регулювання натягу пасм, що відрізняється від відомих схем наявністю реле контролю перевантаження і дискретної системи опитування з видачею сигналу інформації на пульт керування канатозвивальної машини. Робота запропонованої системи автоматичного регулювання здійснюється наступним чином (рис.1).
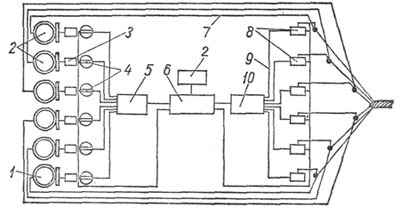
Рисунок 1 – Схема електронної системи автоматичного регулювання натягу пасм
при звиванні канату
При зміні натягу в одній із пасм 7 у датчику 8 виникає сигнал розпогодження, який по лінії зв’язку 9 поступає на схему порівняння електронного комутатора 10 дискретної дії з опитуваним пристроєм. З останнього сигнал, підсилений по напрузі та струму, подається на перемикач 5 виконавчих механізмів, що складаються з реверсивних двигунів 4, редукторів інформації і поступає на підсилювачі 6, 3 гальмових барабанів 1. У цій системі є пристрій, за допомогою якого в
схемі порівняння можна встановити заданий натяг дроту при звиванні пасм у канат, а також окремих шарів при виробництві багатошарових канатів і реле контролю 2 – задані межі змінення різниці натягу між окремими елементами крученого виробу. Результати апробації показали, що автоматичне регулювання натягу в процесі звивання різко підвищує довговічність каната.
Сталеві канати під дією атмосферних умов або агресивних вод піддаються корозії. У результаті метал, що підлягає втомлюваності, зазнає зворотніх і незворотніх змін, які призводять до зниження його витривалості. Існує кілька способів захисту канатів від корозії: оцинкування канатного дроту, застосування спеціальних канатних мастил, полімерних матеріалів і протекторного захисту. Цинкове покриття при зовнішньому зносу дроту швидко руйнується, а в лужних середовищах взагалі не захищує метал від корозії. Змазування скрученого виробу та його елементів досягає цієї мети лише тоді, коли мастило покриває всю поверхню дроту та каната. Наявність місць, непокритих мастилом, веде до створення крапкової корозії та знижен ню втомлюваної міцності каната. Широке застосування як один із методів боротьби з корозією металів і захисту різних підземних споруд одержав протекторний захист. Виконані дослідження у цьому напряму показали, що сталевий дріт із протектором (цинкові та алюмінієві дроти) значно менше піддається корозії у порівнянні з дротом без захисту. В якості корозійного середовища служили звичайна вода, розчин сірчаної кислоти різної концентрації, шахтні води та інші. З
метою перевірки ефективності запропонованого рішення була виготовлена дослідна партія канатів діаметром 25,0 мм. У зовнішньому шару кожної пасми один сталевий дріт замінювали алюмінієвим, який служив протектором (рис.2).
Зазначені канати пройшли промислові випробування на шахтному підйому, які підтвердили ефективність протекторного захисту. Для канатів, що працюють в агресивних середовищах, слід рекомендувати протекторний захист у вигляді одного алюмінієвого дроту в кожній пасмі канату. До експлуатаційних факторів відносять наявність абразивного пилу при експлуатації, що призводить до підвищеного зношу-вання дротів; присутність пару кислот і лугів у хімічних цехах і дії
морської води, що збільшує корозію вихідного елемента канату; високу температуру (металургійні крани), що погіршують умови змазування та сприяють підвищеному зношуванню дротів розгойдування вантажу при роботі крана, яке викликає додаткове тертя каната об реборди блока.
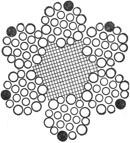
Рисунок 2 – Канат з протекторним захистом
Сталеві канати експлуатуються у самих різноманітних умовах. У вантажопідйомних машинах і на буровому устаткуванні застосовується поліспастове підвішування вантажу. Робота скручених виробів у цьому випадку здійснюється із великою кількістю перегинів на блоках при відношеннях D/d = 15...40 (де D – діаметр блока чи барабана; d – діаметр каната). На шахтному підйому канат зазначає меншу кількість перегинів при D/d = 80...120, але інтенсивність його роботи
більша. При використанні як несучий орган канатних доріг гнучкий елемент сильно зношується від котка при перекочуванні вагонеток, а в якості підтримуємого для різного вида споруди працює тільки на розтяг. Все це свідчить про те, що співвідношення кривизни згину каната на блоках або барабанах до типорозміру скрученого виробу також відноситься до зазначених факторів. Багаточисельні експериментальні дані показали, що чим менше діаметр робочого органа, тим
інтенсивніше зростає число обривів дротів. При малих відношеннях D/d (до 40) для зростання гнучкості та зменшення додаткових напружень слід вибирати канати з більшою кількістю дротів, однак не рекомендується вибирати кручені вироби з числом дротів більше 220. Зазначена кількість дротів призводить до втрати міцності при звиванні та руйнування тонких дротів від їх поверхневого зношування. Для зменшення зазначеного зношування дротів доцільно застосовувати двошарові канати, що не крутяться, які добре себе зарекомендували в експлуатації на кранах і в шахтному підйомному устаткуванні. Підвищена довговічність таких канатів пояснюється меншими контактними напруженнями завдяки більш правильної форми гнучкого виробу та
більшим числом дротів, що одночасно контактують з жолобом шківа. У них не виникають додаткові напруження від кручення, викликаємого поворотом вільного кінця каната. Матеріал жолоба блоку чинить суттєвий вплив на довговічність сталевих канатів. Виконані дослідження показали, що напрацювання канатів на блоках з сірого чавуну в середньому на 15-30 % вище, ніж сталевих.
Дроти канатів руйнуються внаслідок стирання, змінення мікроструктури та механічних властивостей матеріалу блока. Обидві причини є результатом великих питомих навантажень на дроти з боку поверхні струмків блоків, оскільки площина контактів між ними дуже мала. Отже, найбільшим ефективним і простим заходом є збільшення площини контакту поверхонь каната і струмка блока за рахунок футеровки його жолоба, що сприяє підвищенню строків служби кручених виробів. Це пояснюється тим, що при використанні м’яких футерованих матеріалів дроти каната, не деформуючись, вдавлюються в їх поверхню і, як наслідок, тиск його на футеровку передається не тільки через первісно стискаючі дроти, але і суміжні з ними, що приводить
до зменшення питомого тиску. У цьому напряму виконано багато досліджень, присвячених вивченню впливу різних футерованих матеріалів на зносостійкість каната. Як досліджуваний матеріал використовували дуб, литтєву та набірну гуму, транспортувальні стрічки, алюміній, різні пластмаси. Аналіз отриманих результатів різними авторами свідчить, що для підвищення довговічності канатів слід футерувати струмки блоків, однак вибір матеріалу для цієї мети потрібно
здійснювати з урахуванням умов експлуатації. Футеровку алюмінієм рекомендується застосовувати для блоків кранів, канати яких підлягають діянню високих температур або працюють у дуже запиленій атмосфері. Алюміній у струмки блоків заливають у розплавленому стані або закатують за допомогою роликів. Струмок блоку потрібно розточувати з таким розрахунком, щоб після заливання й наступного проточування у нижній частині залишалася алюмінієва подушка товщиною 5-15 мм , а по блокам – 3-8 мм.
Враховуючи, що в процесі експлуатації канату нижня частина струмка зношується швидше, ніж бокові, рекомендується застосовувати литтєві профільовані сегменти у кількості 3-6 шт. на блок. Армування капроном струмків блоків виконується заливкою в розплавленому стані або з використанням капронових уставок. Заливку можна здійснювати по виточці струмка блока чи по усьому профілю, що включає покриття капроном буртів блоку. Результати виконаних досліджень показали, що зношування капронової футеровки в 3-4 рази менше у порівнянні з такими найбільш стійкими матеріалами, як текстолітова і деревинна крихти, волокніт. Найпростішим і надійним способом є футеровка струмків блоків пластмасами, що виконується уставками з поліетилену, пропилену та інших термопластичних матеріалів. Перевага футеровки уставками полягає в тому, що вона дає можливість компенсувати неточності розточування блоку, виготовлення та заміни уставок. При роботі блоків, оснащених ними, строк служби їх необмежений. Довговічність сталевих канатів на футерованих полімерними матеріалами блоках збільшується в 2,0-2,5 рази порівняно з нефутерованими.
Література
- Сергеев С. Т. Стальные канаты. – К.: Техніка, 1984. – 328 с.
- Добронравов С.С., Дронов В.Г. Строительные машины и основы автоматизации.
– М.: Высш. шк., 2003. – 575 с.
- Григоров О.В., Петренко О.В. Вантажопідйомні машини. – Харків: НТУ «ХПІ»,
2006. – 299 с.
- Додонов Б.П., Лифанов В.А. Грузоподъемные и транспортные устройства. – М.:
Машиностроение, 1990. – 248 с.
|