Реферат по теме выпускной
работы
Содержание
1. Введение
2. Предмет и объект исследований
3. Новизна работы
4. Актуальность темы
5. Практическая значимость результатов
6. Обзор разработок и исследований по теме
6.1 Обзор разработок и исследований на локальном уровне
6.2 Обзор разработок и исследований на национальном уровне
6.3 Обзор разработок и исследований на мировом уровне
7. Обзор основных вопросов
8. Имеющиеся результаты
9. Заключение
Литература
Известь потребляется различными отраслями промышленности, и поэтому к ее качеству
предъявляются разнообразные требования.
В сталеплавильном производстве применяется известь с очень низкой реакционной активностью
(мертвообожженная), которая не взаимодействует с влагой воздуха и не содержит гидрата окиси
кальция, в результате разложения которого в сталеплавильных печах выделяется водород.
В мартеновском производстве используется и слабообожженная известь (недопал) ввиду того, что
выделяющаяся в ванне двуокись углерода способствует лучшему перемешиванию расплава.
Для электрометаллургических процессов требуется известь с очень низким содержанием остаточной
СО2, что способствует снижению расхода электроэнергии в электродуговых печах.
Получение продукта с заданными свойствами, отвечающего требованиям различных отраслей народного
хозяйства, требует разработки соответствующих технологических режимов и конструкций печей.
Перечисленные выше типы печных агрегатов имеют существенные недостатки, связанные с повышенным
расходом топлива и непостоянным качеством выпускаемой продукции.
Отразить актуальность сравнения ресурсо-энергосберегающих
показателей альтернативных вариантов производства извести, необходимость
разработки рекомендаций по развитию технологий производства извести в Украине.
Новизна работы заключается в том, что предлагаются для внедрения в
производство извести современные энерго-ресурсосберегающие технологии,
которые позволяют достичь планируемых целей и задач этой работы.
Производство флюсов является одной из наиболее масштабных и
острых проблем черной металлургии в особенности при производстве особо чистых сталеи.
Одновременно существуствует проблема рационального использования минералов,
важнейшими из которых являются металлургические или флюсовые известняки.
Несмотря на распространенность известняков в природе, запасы флюсовых известняков ограничены.
В процессе производства извести неизбежно образуются побочные продукты и отходы,
которые, с одной стороны, составляют крупные потери минерального сырья и, с другой,
наносят огромный ущерб окружающей среде.
При добыче и переработке известкового сырья образуется значительное количество мелких фракций.
Крупность известняка в процессе производства извести зависит от типа применяемого обжигового агрегата.
В настоящее время используют печи для производства кусковой извести. Мелкую фракцию отправляют в отвалы,
что оказывает отрицательное влияние на состояние окружающей среды и снижает выход известняка.
В дипломной работе планируется провести анализ ресурсосбережения и энергосбережения производства извести,
представить возможные варианты и технологические схемы подготовки и утилизации вторичных материальных и
энергетических ресурсов известкового производства.
Результат данной работы — разработка технологических методов
для внедрения в условиях производства извести. Использование этих
методов позволит предприятию организовать более эффективное производство
извести, обеспечив минимальное негативное воздействие производства на окружающую
среду, позволит снизить возможные экологические платежи за выбросы, снизит себестоимость
продукции за счет снижения энергозатрат и уменьшения экологических выплат.
В Донецком национальном техническом университете физико-металлургического факультета на
кафедре «Рудно-термические процессы и малоотходные технологии»
велись разработки по добыче, использованию и применению флюсов.
Одна из таких разработок представлена ниже.
Организация ресурсосбережения при добыче и использовании флюсов в черной металлургии
В состав шихты металлургических
пределов входят основные флюсы: известняк и продукт его обжига — известь.
Все стадии подготовки и производства флюсов отрицательно воздействуют на
состояние окружающей природной среды. Добыча известняков сопровождается
изменением естественных гидрогеологических условий. Это ведёт к нарушению
режима водоёмов и деформации земной поверхности. Снизить влияние открытых
разработок на гидросферу возможно за счёт создания надёжной водозащиты
карьера от поверхностных и подземных вод.
Основными загрязняющими веществами при открытом способе добычи известняков
являются пыль и вредные газы. Мощнейшим источником выброса их в атмосферу
является взрыв горной массы. За один массовый взрыв в атмосферу выбрасывается
100—125 т пыли и 6000—10000 м3 газов. Основные мероприятия по
снижению пылегазовыделений при этом следующие: орошение подготовленных
к взрыву участков и прилегающей к ним зоны и применение взрывчатых веществ
с положительным кислородным балансом (аммиачная селитра), при взрыве которых
выделяются не пыль и ядовитые газы, а кислород. Для снижения пыления при
погрузочно-разгрузочныx работах, горную массу необходимо увлажнять водой методом орошения.
Открытый способ разработки месторождений известняков сопровождается образованием
значительного количества вскрышных пород, идущих в отвалы. Так площадь, занимаемая отвалами ОАО
Новотроицкое рудоуправление составляет 6 млн.т, в которых заскладировано более 250 млн.т таких отходов.
Эти материалы являются ценным сырьём для строительной промышленности и могут использоваться в качестве
бутового камня, щебня, материала для приготовления бетонов, устройства балластного слоя железнодорожных путей,
строительства автомобильных дорог и других целей.
Основным направлением по охране земель при открытой разработке
месторождений известняков является уменьшение объёма выработанного
пространства и сокращение площадей, отводимых под отвалы, за счёт увеличения доли
внутренних отвалов и оптимизации параметров внешних. Для снижения пыления поверхности
отработанных отвалов необходимо производить биологическую рекультивацию их поверхности.
Обогащение известняков осуществляется на дробильно-обогатительных фабриках (ДОФ)
флюсо-добывающих предприятий. Основными стадиями обогащения являются дробление, классификация
и на некоторых предприятиях промывка.
Ресурсосберегающая технология обогащения известняков
предусматривает комплексное использование некондиционного известняка и хвостов обогащения в
стройиндустрии и в сельском хозяйстве, а также перевод обогатительных фабрик на бессточную технологию.
Для улучшения условий труда помещения ДОФ оборудуются аспирационными системами, после которых
образуется значительное количество пыли. Для устранения вторичного пыления при разгрузке
пылеуловителей предлагается применять технологическую схему с увлажнением пыли в специальных
вибрационных смесителях-увлажнителях, которые прошли промышленное опробование при увлажнении
металлургических гидрофобных пылей на отечественных и зарубежных предприятиях. Уловленную и
увлажненную пыль возможно использовать в технологическом потоке ДОФ для дальнейшей утилизации
в смежных отраслях промышленности.
Рисунок 1 — Печи для обжига
Производство извести осуществляется на известково-обжиговых участках металлургических предприятий,
с применением различных агрегатов, работающих с использованием твёрдого топлива,
что сопровождается выбросами в атмосферу токсичных газов. По экологическим и
технологическим соображениям такие печи, должны быть выведены из эксплуатации,
а взамен необходимо ввести печи, работающие на природном газе, что позволит
снизить выбросы вредных газов в атмосферу. Основными современными агрегатами,
отвечающими этим целям являются вращающиеся печи и печи кипящего слоя.
После очистки технологических газов, отходящих от этих агрегатов образуется пыль.
Образование пыли зависит от типа обжиговой печи. В газе после вращающихся печей
содержится до 100 г/м3 пыли, а после печей кипящего слоя ещё больше. Кроме отсевов
извести (0—8 мм) на известково-обжиговых участках образуется аспирационная известково-известняковая
пыль (0—3 мм).
Указанные отходы после соответствующей подготовки целесообразно использовать
в аглопроизводстве для интенсификации процесса спекания аглошихт
и для подготовки влажных шламов к утилизации.
Основным интенсификатором аглопроцесса является отсев извести.
При использовании крупной извести целесообразно осуществлять её измельчение.
Измельчение извести до 3—0 мм при подаче её в аглошихту или до 12 мм
при подаче в концентраты и шламы на складах позволит резко повысить эффективность
её использования, снизить её расход на 10—20 %, уменьшить потребность
в твёрдом топливе путём высокослойного спекания, а также интенсифицировать
процесс агломерации и повысить прочность спека [1,1—2]. Таким образом, при добыче,
подготовке и рациональном использовании флюсов в производстве чёрных металлов
и в других смежных отраслях промышленности можно достичь оптимальной степени ресурсосбережения.
В Украине имеется огромное количество разработок по получению комплексных флюсов для
кислородно-конвертерной плавки. Все разработки содержат ценный научно-технический потенциал.
ЕМЗ
На Енакиевском металлургическом заводе во вращающейся известково-обжигательной печи
исследовался процесс получения комплексного флюса на основе извести при обжиге известняка с окалиной.
Размер фракции известняка и окалины составлял 25—60 и 0—5 мм соответственно.
Вращающиеся печи отапливаются природным газом с применением горелки типа «труба в трубе».
Совместный обжиг известняка с окалиной при той же производительности печи по извести требует
дополнительного расхода тепла, который должен быть компенсирован увеличениемрасхода природного газа [4, 597].
Однако, за счет высокой температуры отходящих газов расход газа не изменялся.
Продукт обжига представляет куски извести, покрытые прочной железистой оболочкой.
Степень черноты материала при обжиге чистого известняка составляет 0,27, а при обжиге
известняка, покрытого окалиной, 0,80. Небольшое ядро «недопала», наблюдаемое в обычной извести,
отсутствует в извести, покрытой оболочкой ферритов.
ДонНИИчермет и ЕМЗ
Донецкий научно-исследовательский институт черной металлургии (ДонНИИчермет) и
Енакиевский металлургический завод для ускорения шлакообразования предложили различне способы:
улучшение качества извести (увеличение ее реакционной способности, предварительное измельчение,
применение доломитизированной извести), заливка в конвертер готовых жидких шлаков, использование
конечных шлаков предыдущей плавки, применение специальных плавней и флюсов, изготовление и применение
искусственных флюсов (агломерата, окатышей, брикетов, специальных сортов извести), вдувание пылевидной извести.
Разнообразие предлагаемых решений объясняется трудностью придания основному шлакообразующему материалу (флюсу)
свойств, которые диктуются особенностями современного кислородно-конвертерного производства.
Разработанная технология получения флюса представляет собой дополнение к процессу обжига извести
во вращающейся известково-обжигательной печи [6, 410—412]. Главной ее особенностью является нанесение на поверхность
извести пылевидных флюсующих добавок (железорудного концентрата, колошниковой пыли). На Енакиевском
металлургическом заводе была сооружена опытная установка для получения конвертерного флюса. Покрытие,
образующееся на извести, улучшает условия транспортирования и хранения флюса. Истираемость флюса
получилась примерно вдвое меньшей, чем чистой извести. Количество влаги, поглощенной флюсом за первые
сутки, не превышает 2 %. Присутствие ферритов «разрыхляет» структуру извести и препятствует образованию
сплошной пленки двухкальциевого силиката.
ДонНИИчермет
Донецким научно-исследовательским институтом черной металлургии (ДонНИИчермет) разработана технология
производства конвертерного железофлюса из замасленной окалины методом горячего окомкования. Выход окалины
с развитием прокатного производства постоянно увеличивается. Окалина мелких фракций скапливается
в отстойниках в виде пастообразной нетранспортабельной массы и содержит обычно до 15 % смазочных масел
и 20 % влаги. Содержание железа в окалине обычно составляет 70 %. Технология обеспечивает эффективную переработку
окалины различных фракций с высоким содержанием влаги и масел [5, 32—33]. технология производства железофлюса заключается
в окомковании пересыпающихся шихтовых материалов расплавами, образующимися на их поверхности при обработке шихты
высокотемпературным факелом. Перед оплавлением поверхности шихтовые материалы последовательно проходят все
стадии сушки до декарбонизации, при этом масло сначало испаряется, а потом сгорает в высокотемпературной
окислительной зоне над слоем шихты. Так как использование замасленной окалины в исходном состоянии в
процессе горячего окомкования затруднительно, ее предварительно смешивают с 20 % (по массе) извести.
Благодаря гидратации извести влагой окалины последняя приобретает сыпучесть и удовлетворительную
транспортабельность. Технология наряду с утилизацией окалины обеспечивает существенное снижение
материалоемкости кислородно-конвертерного и прокатного производств.
США
В США предложены способы получения ферроизвести во вращающейся печи. По одному способу во вращающуюся
печь загружают известняк и окатыши диаметром 9,5—15,9 мм, изготовленные из окалины и известняка фракции
6,3—12,7 мм. Вращающаяся печь имеет длину 44 м и диаметр 2,75 м. Расход материалов в зоне загрузки составляет:
окатышей 500 кг/час, известняка 18200 кг/час [4, 49]. температуру обжига поддерживают в пределах 1300-1375оC.
Ферроизвесть содержит около 2 % оксидов железа. Отличительной особенностью другого способа является
введение во вращающуюся печь доломита (13 т/ч) и прокатной окалины (2—3,5 т/ч). При температуре
обжига около 1100оC получают ожелезненный флюс, содержащий 1,07 SiO2; 22,29 % Fe2о3; 42,26 % CaO;
33,13 % MgO; 0,014 % S. Полученный ожелезненный флюс в количестве 68 кг/т загружаемой шихты может
быть использован для рафинирования металла в конвертере.
Россия
На ОАО «Северсталь» успешно используется технология применения ожелезненного известково-магнезиального
флюса в конвертерной плавке. Этот материал повышает стойкость футеровки конвертера в 1,5—1,7 раза при
поддержании по окончании продувки металла содержания магния в шлаках более 8 %. Использование в
конвертерной плавке доломитизированной извести (60 % СаО; 30 % MgO) в количестве до 30 кг/т стали
привело к росту стойкости футеровки до 3000 плавок. В условиях ОАО «Северсталь» введение обоженного
доломита с одновременным торкретированием и «намораживанием» шлакового гарнисажа на футеровку
конвертера ее стойкость достигла 4500 плавок. Скорость износа футеровки, в особенности изготовленной
из периклазоуглеродистых огнеупоров, зависит от содержания оксидов железа и магния в шлаке.
Чем больше насыщен шлак оксидами магния, тем меньше активность оксидов железа. При концентрации
оксидов магния в шлаке выше предела насыщения оксид магния начинает выделяться из шлака.
В этом случае на футеровке могут возникать наросты. Поэтому уменьшение активности железа
шлака только добавками магнийсодержащих материалов приводит к изменению происходящих при
продувке процессов, ухудшая технологические показатели плавки. Одним из эффективных способов
повышения шлакообразования и повышения реакционной способности шлака с одновременным увеличением
в нем количества оксидов магния — использование в конвертерной плавке ожелезненного известково-магнезиального флюса,
оксиды железа которого препятствуют образованию силикатов кальция и магния. Флюс изготавляют из доломита и
железистого конвертерного шлама. Обоженный доломит легко разрушается, а ожелезненный флюс имеет высокую
прочность и устойчивость к истиранию.
[3, 46—48].
Япония
Фирма «Син ниппон сэйтэцу», Япония, разработала установку для обработки твердых отходов
прокатного производства, в котрой в качестве теплоносителя используют горячее доменное дутье.
С дутьем уносятся органические вещества в газообразной форме, при этом неорганические отходы
превращаются в железосодержащий шлак [4, 47].
В Японии запатентован способ обезжиривания замасленной окалины путем подачи последней в разгрузочный
конец вращающейся печи при агломерации рудных материалов. Выделяющиеся пары масел в окислительной зоне
служат дополнительным топливом, а нагретую окалину вместе с возвратом вводят в аглошихту [4, 47].
СХЕМА ПРОИЗВОДСТВА ИЗВЕСТИ
Природный мел с природной влажностью 25% и суммарным содержанием карбонатов
кальция и магния 92—97% добывается открытым
способом и автотранспортом доставляется на основное производство.
Основное производство состоит из стадий:
1. Участок приема природного мела и приготовление мелового шлама;
2. Участок хранения запаса готового шлама;
3. Печное отделение;
4. Подъемно-транспортная система готовой продукции;
5. Силосный склад готовой продукции;
6. Отделение обеспыливания отходящих газов;
7. Вспомогательные производства.
Рисунок 2 — Схема производства извести
Природный мел с автотранспорта разгружается в приемный карман глиноболтушки,
туда же подается вода в необходимых количествах.
При работе глиноболтушки куски мела с помощью перемешивающего устройства измельчаются,
переходят во взвешенное состояние, в глиноболтушке получается меловой шлам.
имеющий сметанообразную консистенцию. Для придания шламу необходимой подвижности в него добавляется пластификатор.
Готовый шлам самотеком поступает в промежуточный сборник шлама,
представляющий собой железобетонную емкость. По мере накопления, шлам из промежуточного сборника откачивается одним из
насосов в вертикальный шламбассейн.
Готовый шлам во время нахождения в промежуточном сборнике шлама и горизонтальном шламбассейне
перемешивается с помощью подачи сжатого воздуха через барботеры.
Участок хранения запаса готового шлама состоит из двух
железобетонных шламбассейнов и насосной шлама.
Печное отделение включает в себя:Печь обжига,Барабанный холодильник.
Печь работает по принципу противотока. С «холодного» конца печи подается сырье в виде шлама,
на «горячем» конце печи производится сжигание природного газа. По мере продвижения материала
по печи с «холодного» конца к «горячему», он проходит четыре зоны:
• Зона сушки — здесь происходит испарение влаги из шлама, поступает в зону шлам с влажностью — 40—42% ,
в конце зоны мел с влажностью 5-12%;
• Зона нагрева — здесь происходит нагрев материала до
температуры реакции термической диссоциации;
• Зона диссоциации — здесь происходит превращение мела в известь при температурах 1150—1350°С;
• Зона охлаждения — здесь известь охлаждается потоком холодного воздуха.
Далее известь с температурой 600—800 °С поступает в холодильник барабанного типа, где охлаждается до 100°С.
С холодильника известь системой конвейеров направляется на склад готовой продукции.
На всех узлах пересылок извести предусмотрен отсос воздуха для снижения запыленности в
воздухе рабочей зоны, с последующей его очисткой в системах аспирации.
Конечный реверсивный ленточный конвейер позволяет распределять известь по силосам в зависимости от качества извести.
Отходящие газы удаляются с «холодного» конца печи проходят двухступенчатую очистку.
Первоначально дымовые газы проходят предварительную, грубую очистку в пылевых камерах,
затем окончательную в электрофильтрах. Степень очистки 99,9%. Очищенные отходящие газы
дымососом выбрасываются в дымовую трубу.
Уловленная в процессе очистки дымовых газов пыль, содержащая 30—40% извести и 60—70% мела,
собирается системой конвейеров в бункер.
Использование отходов производства извести в аглодоменном производстве
Разработаны различные варианты и технологические схемы подготовки и утилизации
вторичных материальных и энергетических ресурсов при производстве извести.
Использование отходов производства извести в аглодоменном производстве.
Для снижения влажности аглошихты используют основное количество сухих железосодержащих
отходов комбината и известковую пыль газоочистки печей кипящего слоя.
Существенный недостаток печи кипящего слоя — значительный (40—45 %) пылеунос мелких
фракций материала из печи. Улавливаемую системой газоочистки известковую пыль
(круп¬ностью 0—1 мм) выгружают из бункера в цементовоз и доставляют на аглопроизводство.
Часть ее используют при подготовке замасленной окалины, а основную массу закачивают в бункера извести
шихтового отделения аглофабрики и дозируют в шихту (рис).
1 — автотранспорт для извести;
2 — магистраль сжатого воздуха;
3 — отводы сжатого воздуха;
4 — пневмотранспорт извести;
5 — бункера извести шихтового отделения;
6 — пылеулови¬тели;
7 — конвейер шихты;
8 — приемный бункер;
9 — ленточный конвейер;
10 — склад, подготовки замасленной окалины;
11— штабель смеси окалины с известью;
12 — железнодорожный вагон;
13 — вагоноопрокидыватель;
14 — штабель рудной смеси;
15 — бункера рудной смеси шихтового отделения
Рисунок 3 — Схема использования извести на аглопроизводстве:
а — известковой пыли на аглофабрике; б — отсевов извести на аглофабрике;
в — известковой пыли при подготовке замасленной окалины.
Анализ возможных схем перевода производства извести
на новые энергосберегающие технологии позволяет рекомендовать
использование в качестве сырья природного мела влажностью 23-28%
без добавления влаги при приготовлении шлама, перевод вращающихся
печей на сухую технологию, позволяющую уменьшить удельный расход топлива
с 270—310 до 210—220 килограммов на одну тонну извести, или в среднем на 25% .
Энергосберегающая технология производства извести из тонкомолотого известняка
При добыче и переработке известкового сырья
образуется значительное количество мелких фракций.
Крупность известняка в процессе производства извести
зависит от типа применяемого обжигового агрегата.
В настоящее время используют печи для производства кусковой
извести. Мелкую фракцию отправляют в отвалы. В то же время при
производстве железорудных окатышей в технологии внепечной обработки
чугуна и стали применяют мелкодисперсную известь с размером частиц менее 100 мкм,
которую получают путем помола кусковой извести в мельничных агрегатах.
При этом необходимо использовать дезагрегирующие добавки, что снижает качество
извести и повышает ее себестоимость. Кроме того, процесс помола сопряжен с проблемами
экологического характера. Таким образом, производство извести из мелких фракций известняка целесообразно
как с экологической, так и с экономической точки зрения.
Технология получения извести из брикетированной меловой крошки
Цели технологии:
— Получение качественной извести из меловой крошки, образующейся при добыче кускового мела.
— Утилизация отходов добывающей промышленности.
— Экономия первичного сырья.
Наиболее эффективным направлением использования меловой крошки,
образующейся при добыче мела и идущей в отвал, является производство
извести. Оно может быть налажено практически на том же оборудовании,
что и производство обычной извести. Основным методом окускования меловой
крошки перед обжигом является брикетирование.
В качестве связующего лучшие характеристики обнаруживает жидкое стекло.
Возможно также использование некоторых солей.
Органические связующие менее предпочтительны, т.к. содержат серу или пиролизуются при обжиге, в результате чего брикеты могут преждевременно разрушаться.
Использование в качестве связующего отсева извести и
известковой пыли, образующихся при обжиге меловых брикетов,
объясняется необходимостью их утилизации в собственном производстве,
а также их более низкой стоимостью по сравнению с жидким стеклом.
Схема технологии представелена на рисунке.
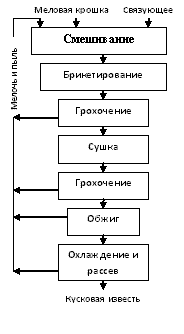
Рисунок 4 — Технология производства извести из меловой крошки
Эта технология обеспечивает максимальную
степень утилизации вторичных ресурсов в производстве
флюсов в сравнении с известными аналогами. Обеспечивает
стабильно высокое качество и низкую стоимость продукта.
По результатам анализа работы, были выделены основные существующие альтернативные варианты
производства извести из переработанных отходов:
— Энергосберегающая скоростная технология производства высококачественной порошковой извести;
— Энергосберегающая технология производства извести из тонкомолотого известняка;
— Технология получения извести из брикетированной меловой крошки.
Предложенные технологии позволяют:
— вовлечь в оборот значительное количество отходов;
— высвободить огромные площади, занятые под складирование этих отходов;
— улучшить экологическое состояние прилегающих территорий;
— повысить эффективность металлургического производства;
— получить значительный экономический эффект.
В работе рассмотрен процесс производства извести,
проведен анализ ресурсосбережения, энергосбережения при производстве,
указана ценность вторичных ресурсов, предложены технологические схемы подготовки и
утилизации ВМР и ВЭР, дана технико-экономическая оценка и экологическая
оценка эффективности
организации ресурсосбережения и энергосбережения фпроизводства извести.
1. Металлург, 8 (2004).
2. Табунщиков Н.П., Исследование шахтных известково-обжигательных печей. — М.—Л., 1977г. — 362 с.
3. Смирнов Л.А. Использование ожелезненного известково-магнезиального флюса
в конвертерной плавке // Сталь. — 2000, № 11. — С. 46—48.
4. Борисов В.М., Жук А.Д., Матюк И.Я. Перспективы использования
дисперсных отходов прокатного производства в черной металлургии (Обзор) //
Черная металлургия.- 2001, № 21 (905).— С. 45—60.
5. Гаврин Э.Г., Абросимов А.С. Производство конвертерного железофлюса
из промасленной окалины // Бюллетень.— 2005, № 2. —С. 32—33.
6. Дидковский В.К., Роговцев Н.И. Технология производства и
применения конвертерного флюса // Сталь. — 2003, № 5. — С. 410—412.
7. Металл и литьё Украины, 2—11’2002год.
8. Брусиловский Г.Н., Производство извести — М., 1954г. — 256 с.
9. Монастырев М.И., Производство извести — М., 1986г. — 208 с.
10. Табунщиков Н.П., Производство извести — М., 1974г. — 238 с.
11. Металл и литьё Украины, 3—4 ’2004год.
12. Технология производства железофлюса на
Докучаевском флюсо-доломитном комбинате [Электронный ресурс].-Режим доступа: URL:
http://www.dfdk.com.ua
13. Организация ресурсосбережения при добыче и использовании
флюсов в черной металлургии [Электронный ресурс]. — Режим доступа: URL: http://donntu.ru
14. Портал магистров Доннту, Пономарева Н.[Электронный ресурс]. — Режим доступа: URL:
http://masters.donntu
15. Производство извести [Электронный ресурс]. — Режим доступа: URL:
http://www.izvesta.com/
16. Технология производства извести [Электронный ресурс]. — Режим доступа: URL:
http://www.ptechnology.ru
17. Бойко, Федоров. Производство извести [Электронный ресурс]. — Режим доступа: URL:
http://waste.ua
|