Abstract on the topic of master's work
Contents
- Introduction
- 1. Automatic control system for technological process and controller's management
- 2. Functional diagram of stand
- 2.1 SCADA-system WinCC
- 2.2 Frequency converter of the Control Technics firm
- 2.3 Programmable logic controller VIPA
- 2.4 The executive body
- 3. Distributing of functions in the multi level control system
- Conclusions
- References
Introduction
Actuality of the theme in the fact that modern automatic control system for technological process (ACS TP) is a multi level human-machine control system [1]. Creating complex automated process is carried out using automated information systems, data collection and computing systems that are constantly being improved with the evolution of hardware and software [2].
The level of development of modern computer technology makes it possible to implement complex control algorithms in real time. Digital control systems have several advantages compared to analog, which is reflected in the simplicity and flexibility in the implementation of control algorithms. On the basis of digital technology is possible to build multilevel, distributed control systems, the interaction between them is carried out over computer networks [3].
Modern electric drive is a complex electromechanical system consisting of a transformational equipment, control and information devices and electrical machines [4]. In recent times more common electric drive with digital control, the work is determined by a microcontroller that generates the required algorithms and control laws. Thus, the functioning of modern electro-mechanical system with digital control depends not only on serviceability of the individual blocks and parts of the system, but also the correctness of the software used, matching and controlling the operation of these units.
So knowledge of these components is very important for professional direction Electromechanics
, and for the formation of necessary skills, it is indispensable in the teaching of modern specialized laboratory equipment.
Purpose of work – development of a laboratory stand for study and research of multi level control systems AC drive.
1. Automatic control system for technological process and controller's management
Continuous time picture of the development automatic control system for technological process can be divided into three stages due to the appearance of qualitatively new scientific ideas and techniques. In the course of history changed the nature of objects and methods of control, automation, and other components that constitute the modern management system [5].
The first stage reflects the introduction of automatic control systems. Objects control at this stage are the individual parameters, installation, plant. Solution of problems stabilization, program management, tracking changes from person to automatic control systems. In humans, there are functions of the calculation tasks and settings adjustments [6].
The second stage – the automation of technological processes. The object of control is dispersed in space system. With the help of automatic control systems realized more and more complicated control laws, solved the problem of optimal and adaptive control, carried out the identification of the object and the system state.
The third stage – automatic control system for technological process – characterized by the introduction of process control computers. First – the application of microprocessors to use in certain phases of the control of computer systems, then – the active development of human-machine control systems, engineering psychology, methods and models of operations research, and finally – on the basis of supervisory control of automated information systems, data acquisition and advanced computing systems [7].
From stage to stage change and human functions (operator / manager), designed to provide routine operation of the process. The circle of problems solved at the level of control. Narrow line process control need a set of tasks is replenished qualitatively new tasks before having ancillary or related to a different level of management.
A controller in the multi level automated technological process control system gets information from the monitor of computer or from the electronic system of displaying information and affects objects being from it on considerable distance, by the telecommunication systems, comptrollers, intellectual executive mechanisms.
The SCADA (Supervisory Control And Data Acquisition is controller's management and data capture) conception is fated by all process control systems and results of scientific and technical progress. The SCADA-technology application allows to attain the high level automation in the decision of tasks development of the control systems, collection, treatment, transmission, storage and displaying of information [8].
Friendliness of human-machine interface (HMI/MMI – Humain/Маn Machine Interface), given SCADA-systems, plenitude and evident of represented on the screen of information, availability of «levers» management, comfort of the use by prompts and help system and etc promote efficiency of co-operation controller with the system and take to the minimum its critical errors at the management [9].
In SCADA is currently the main and most promising method of automated control of complex dynamic systems (processes) [10].
2. Functional diagram of stand
Figure 1 shows the functional diagram of the stand for the study of multi-level control system AC motors. It includes a personal computer running SCADA-system WinCC (1), programmable logic controller company VIPA (2), the frequency converter firm Control Techniques – Unidrive SP (3), induction motor (4).
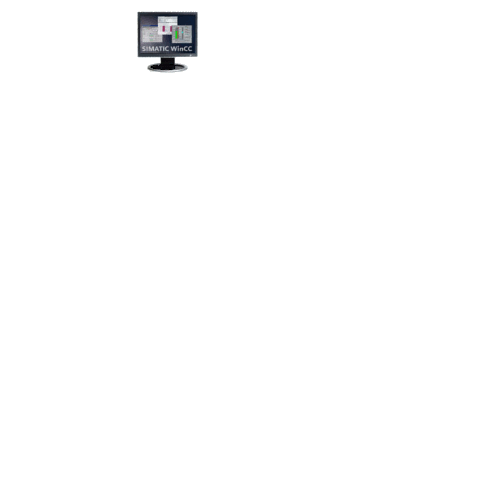
Picture 1 – The functional diagram of stand
2.1 SCADA-system WinCC
SCADA – a software package designed to develop or provide real-time systems for collecting, processing, displaying, and archiving information about the object of monitoring or management.
SCADA-systems solve the following tasks:
- data exchange with communications device with the object (CDO, that is, industrial controllers and input/output cards) in real time through the driver;
- information processing in real time;
- logical control;
- display on the monitor screen in an easy and understandable for human form;
- maintaining a database of real-time process information;
- alarm system and control by the anxious reports;
- preparation and generation of reports on the progress of the process;
- implementation of networking between SCADA and personal computer.
Thanks to the powerful integrated database for data archiving process, a large number of tools for processing, transmission and analysis of information and open interfaces for integration was chosen SCADA-system from Siemens – WinCC.
SIMATIC WinCC are base functional modules:
- WinCC Explorer – a quick overview of all project data, global settings, startup and mode editors Runtime, system configuration
client-server
. - Graphics Designer – design mnemonic diagrams using the standard elements of the built-in library of objects.
- Alarm Logging – collect and archive messages. WinCC supports two methods to generate posts using the tag and the PLC in the form of message packets. Messages can generate audio signals.
- Tag Logging – collect, archive and compression of the measured values. The database is based on MS SQL Server. Backing up a loop, or event-driven system. Archiving can be done entirely separate tags or blocks of PLC data. The data from the archive can be displayed in the form of curves or tables. You can create long-term data archives.
- Report Designer is the generation of reports in a freely programmable format, guided by events or at times. The generation of protocols reports, measured sizes and user reports is possible. In a report it is possible to plug information from the CSV files and databases. The preview of reports and saving of them in a file is possible.
- Global Scripts is programing of actions, producible with graphic objects, and also scripts executed in the background mode.
- Menus & Toolbars is editor allowing to create user menus and tool bars for mnemonic diagrams and pop-up windows.
- User Administrator is comfortable management by rights for access of users.
- Basic Process Control is set of instruments, such as autoconstruction hierarchies of mnemonic diagrams, synchronization of time in the system, configuration projects with a few monitors, autoconstruction of screen.
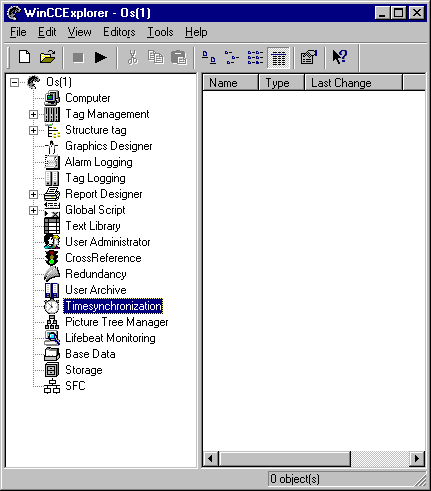
Picture 2 – WinCC Explorer
2.2 Transformer of frequency of the Control Technics firm
Unidrive SP is universal transformer of frequency, which can be basis of the technological process control system [11]. (pic. 3)
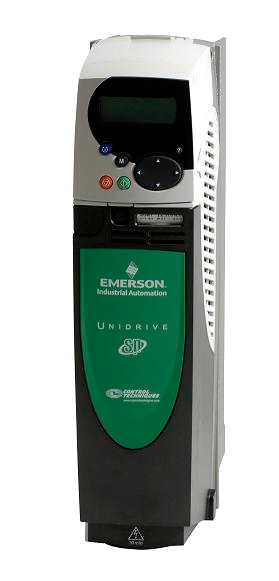
Picture 3 – Unidrive SP
Basic features transformer of frequency of the Unidrive SP series:
- auto-tuning function allows you to create an accurate model of the actuator by measuring the moments of inertia and the load without rotation of the shaft and the rotation;
- open architecture design allows you to easily expand the functions of the drive by connecting additional modules – I/O modules, embedded controllers, communication modules;
- access to basic and advanced menus with built-in panel;
- change the function of switching frequency from 3 to 18 kHz;
- a built-in braking transistor;
- the ability to connect via Modbus RTU RS 485 via RJ45 connector is standard;
- the presence of five analog inputs, seven digital inputs / outputs and an output breaker.
2.3 Programmable logic controller VIPA
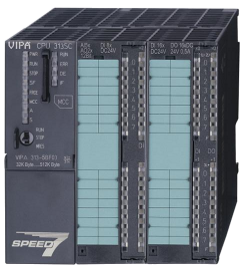
Picture 4 – VIPA 313SC Speed7
Programmable logic controllers are the basis for building automation in all industries [12]. Along with equipment manufacturers known PLCs such as Siemens, Schneider, on the market today presents new designs, different advanced technical solutions.
Programmable Logic Controller (PLC) VIPA 313SC Speed7 designed to meet the challenges of central and distributed automation system with a large number of signals critical to the execution time.
Features:
- processor is made of technology Speed7, which allows to solve tasks with much greater speed;
- high-speed expansion bus Speed-bus;
- connection to the Speed-bus high-speed modules;
- the kit includes blocks of analog and digital inputs/outputs;
- has a built-in thermocouple Rt100;
- ability to work without MCC card;
- the processor module has connectors for connection to the MPI and Ethernet;
- interchangeability of input-output modules with modules Simatic S7-300 from Siemens.
Develop a program for managing the installation of the VIPA PLC by means of hardware and software – WinPLC7. This software is designed for configuring, programming and debugging software for VIPA controllers of all series.
WinPLC7 contains all necessary instruments for creation of project:
- editor of the programs;
- emulation of the controller;
- configurator hardware;
- the character editor.
To program the automation system in a package can be used WinPLC7 three programming languages:
- Statement List (STL) is language of instructions;
- Ladder Diagram (LAD) is language of stair diagrams;
- Function Block Diagram (FBD) is language of function blocks.
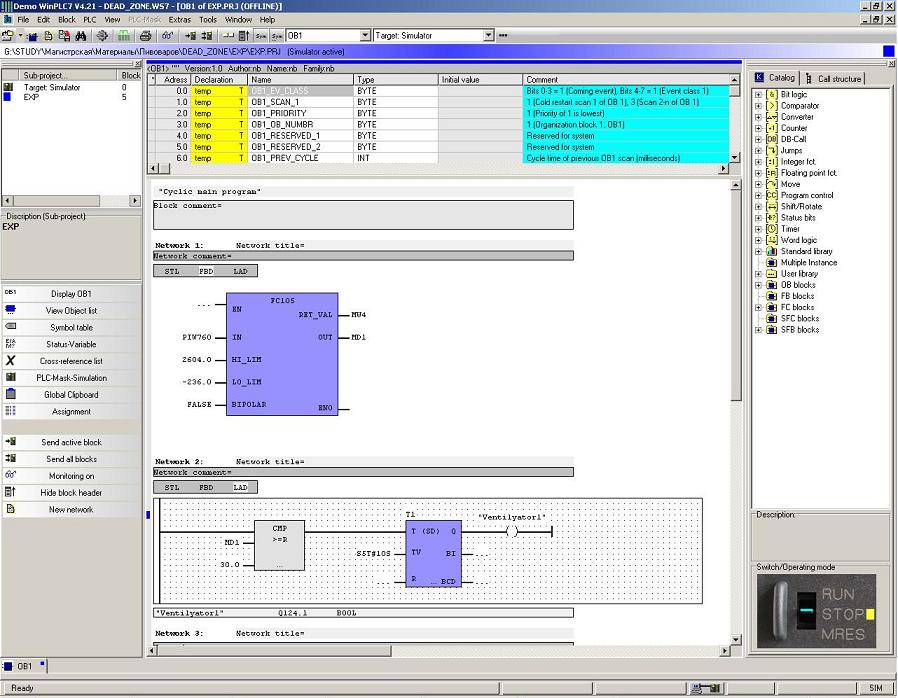
Picture 5 – The workspace software WinPLC7
2.4 The executive body
As an executive body acts as a short-circuited three-phase induction motor from Siemens. (pic. 6)
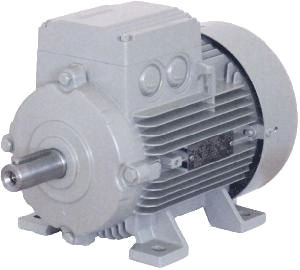
Picture 6 – The induction motor of the Siemens firm
Passport information:
f = 50 Hz
U = 230 V
P = 0,25 kW
I = 1,78 А
cosφ = 0,64
n = 685 rpm
3. Distributing of functions in the multi level control system
In a multi level system of control for every single element of its assigned specific functions [13]. Consider the functions as are assigned to each element of the stand.
SCADA-system WinCC:
- visualization of technical process;
- storage of normative-help information;
- interface of operator;
- forming of managing influence on PLC;
- data processing from PLC.
Programmable logic controller VIPA:
- processing the signals from the sensors;
- the implementation of process control;
- issue a control action on the motor;
- processing of information feedback from the drive;
- co-operation with an operator level.
The frequency converter of the Unidrive SP:
- the voltage regulation and frequency of feeding an induction motor to keep your defined process parameters;
- implementation of energy saving features;
- optimization of speed and loading diagrams;
- self-diagnosis and diagnosis of an induction motor.
Conclusions
In the development of multi-level control raises questions that need answers:
- to find optimal solutions for hardware and software components of the interaction;
- to distribute the tasks to be undertaken at different levels according to the criteria of high performance, the use of computing power and network utilization;
- ensure high reliability of the diagnosis through the use of self and the individual components and systems in general;
- implement easy-to-use human-machine interface and the structure of accounting documents.
Important note
In the moment of writing of this abstract master's degree work is not yet finished. Final completion of work will take place in December, 2012.
References
- Густав Олссон, Джангудио Пиани. Цифровые системы автомтаизации и управления.-СП б.: Невский Диалект, 2001 – 557 с.
- Денисенко В.В. Компьютерное управление технологическим процессом, экспериментом, оборудованием. – М.: Горячая линия, Телеком, 2009.-608 с.
- Передача данных в системах контроля и управления: практическое руководство /Парк Дж., Маккей С., Райт Э.: (превод с англ. Савельева В.В) –М.: ООО «Группа ИДТ», 2007.-480 с.
- Doncker Rick, Duco W.J.Pulle, Velman Andre/ Advanced Electrical drives. Springer, London/New York, 2011. – 475 p.
- Информационный сайт o-asutp.ru [Электронный ресурс]. – Режим доступа: http://www.o-asutp.ru/asutp_...
- Бесекерский В. А. Теория систем автоматического регулирования. / Бесекерский В. А., Попов Е. П./ М., Наука, 1966.
- Simatic Totally Integrated Automation [Электронный ресурс]. – Режим доступа: http://www.ste.ru/siemens/...
- SCADA – Википедия [Электронный ресурс]. – Режим доступа: http://ru.wikipedia.org/wiki/SCADA
- Daneels A., CERN, Salter W., WHAT IS SCADA?// International Conference on Accelerator and Large Experimental Physics Control Systems, 1999, Trieste, Italy, pp.349-343
- SCADA-системы: взгляд изнутри/ Андреев Е.Б., Куцевич Н.А., Синенко О.В. – М.: Издательство «РТСофт», 2004. – 176 с.: ил.
- Расширенное руководство пользователя Unidrive SP[Электронный ресурс]. – Режим доступа: http://www.proavtomatika.ru/docs/...
- Парр. Э. Программируемые контроллеры: руководство для инженера/Парр Э. пер. 3-го англ. изд.-М.: БИНОМ, 2007.-516 с.
- Белов М.П. Инжиниринг электроприводов и систем автоматизации: учеб. пособие / Зементов О.И., Козярук А.Е. и др.; под ред. Новикова В.А., Чернигова Л.М.. – М.: Изд. центр «Академия», 2006. – 416с.