Реферат по теме выпускной работы
Содержание
- Введение
- 1. Цель и задачи
- 2. Преимущества процесса брикетирования
- 3. Требования к шихте и готовым брикетам
- 3.1 Характеристика брикетируемых материалов
- 3.2 Требования к металлургическим свойствам брикетов
- 4. Схема технологического процесса
- 5. Эффективность применения брикетов
- Выводы
- Список источников
Введение
Создание и внедрение более рациональных и экологически чистых производств является основной задачей современного человечества, столкнувшегося с проблемой глобального экологического загрязнения и истощения планеты. Так, например, чёрная металлургия является одной из самых материало- и энергоёмких, а также экологически вредных отраслей промышленности. Общий расход материально-сырьевых ресурсов по циклу от добычи руды и угля до прокатки составляет до 7 т на 1 т готового проката [1]. На металлургическом комбинате полного цикла мощностью 5 млн. т проката в год образуется 2,3 млн. т шлаков, 0,8 млн. т пыли, шламов и окалины, 25 тыс. т соединений серы, 120 тыс. т окислов углерода, азота и других элементов [2]. Поэтому вопрос рационального использования природных ресурсов, а также комплексной переработки отходов – наиболее актуален на сегодня для данной отрасли промышленности.
Наиболее приемлемой не только с экологической, но и с экономической точки зрения является утилизация отходов внутри собственного производства, так как это позволяет использовать их в виде относительно дешевого сырья, что способствует значительному снижению затрат на шихту, повышению качества и конкурентоспособности продукции, а главное, уменьшению себестоимости готовой продукции.
1. Цель и задачи
Магистерская работа посвящена исследованию процесса брикетирования как одного из универсальных направлений подготовки металлургических отходов.
Основная цель – разработка рациональной технологии подготовки и брикетирования железосодержащих отходов металлургического производства.
Новизна заключается в том, что в работе предложена универсальная схема получения железосодержащих брикетов из отходов Донецкого металлургического завода, с целью последующей их переработки на предприятии.
В работе поставлены следующие основные задачи:
- Рассмотреть основные виды отходов, образующихся на ПрАО «Донецксталь МЗ», изучить их особенности (физико-химические свойства, гранулометрический состав и др.);
- Проанализировать требования, предъявляемые к металлургическим брикетам, и на основании этого выбрать наиболее приемлемую схему подготовки отходов предприятия;
- Разработать технологическую линию по производству железосодержащих брикетов;
- Определить эколого-экономический эффект, получаемый за счет использования брикетов в доменном и сталеплавильном процессах.
2. Преимущества процесса брикетирования
На сегодня выделяют три основных способа окускования в металлургии – это агломерация, окатывание и брикетирование. Большое распространение получили первые два. Это связано, прежде всего, с высокой производительностью агломерационных машин, а также с возможностью получения продуктов высокого качества.
В последнее время из-за нехватки природных запасов, а также чрезмерного накопления отходов, в металлургии все чаще стали применяться тонкофракционные материалы – концентраты глубокого обогащения, а также шламы и пыли. Однако, их использование в агломерационном процессе и при производстве окатышей, ограничено, так как приводит к ухудшению качества готового продукта.
Так, например, добавление шламов в аглошихту составляет до 15% от общей массы, поскольку превышение этого количества ведет к ухудшению показателей спекания, росту вредных примесей в агломерате, нарушению правил санитарной гигиены и техники безопасности на рабочих местах, загрязнению оборудования и воздушного бассейна. А подготовка (обезвоживание и термическая сушка шламов, окомкование пыли, обезмасливание шламов прокатного производства, обесцинкование шламов и пылей) металлургических отходов для добавления в аглошихту или окатыши требует сравнительно высоких капитальных и эксплуатационных затрат.
К тому же, для предприятий, не имеющих собственных аглофабрик, возвращение отходов в собственное производство в виде сырья делается в принципе невозможным. Поэтому сегодня набирает популярность такой метод окускования как брикетирование.
Процесс брикетирования имеет ряд существенных преимуществ:
- предъявляет менее жесткие требования к качеству сырья, позволяет окусковывать материалы широких классов крупности менее 10 мм, практически в любых пропорциях и составах;
- процесс брикетирования технологически прост;
- брикетная установка является мобильной и не занимает большую площадь;
- при брикетировании сохраняются свойства компонентов, входящих в брикеты;
- брикетирование с экологической точки зрения является более чистым способом окусковання;
- брикеты расширяют сырьевую и топливно-энергетическую базу металлургии [3].
Проблемным вопросом, который требует дополнительного изучения, является выбор связующего, которое отвечало бы заданным прочностным свойствам брикета и обладало приемлемой ценой.
Опытом многих металлургических компаний установлено, что процесс брикетирования наиболее полно реализуется совместно с другими методами окускования – агломерацией и грануляцией с обжигом. Они не конкурируют между собой, а экономически выгодно дополняют друг друга.
Брикетирование отходов металлургического производства уже давно и достаточно прочно укоренилось в развитых странах мира. Однако на Украине оно не получило столь широкого распространения и в настоящее время не превышает 2 %, хотя потребность в таком методе окускования может быть на порядок выше [4].
3. Требования к шихте и готовым брикетам
В настоящее время существуют различные схемы брикетирования, сильно отличающиеся друг от друга. Так, например, различают способы «холодного» и «горячего» брикетирования, проходящие соответственно при обычных и высоких температурах. Также брикетирование со связующим или без, при различном давлении прессования, с разными способами упрочнения сырых брикетов (термическое и химическое) и др.
При выборе оптимальной схемы производства брикетов для Донецкого металлургического завода необходимо учесть ряд факторов: характер и объем образующихся полезных отходов, область дальнейшего использования брикетов, а также предъявляемые к ним требования, затраты предприятия на реализацию данного проекта, его экономическая и экологическая эффективность и пр.
3.1 Характеристика брикетируемых материалов
Основные отходы, образующиеся на ЧАО «Донецксталь – МЗ» и нуждающиеся в утилизации, принадлежат доменному, сталеплавильному и прокатному производствам. Это колошниковая пыль, пыль центральной вытяжной станции и аспирационных установок, шламы мокрой газоочистки доменного газа, отсевы кокса и извести, а также пыль ЭСПЦ, окалина и чугунная стружка (Таблица 1)
Таблица 1 – Химический состав отходов
Материал | FeO | Fe2O3 | SiO2 | CaO | MgO | Al2O3 | MnO | C | S |
Колошниковая пыль | 42.1 | 53.76 | 12.0 | 11.56 | 0.9 | 1.13 | 0.26 | 10.69 | 0.4 |
Доменный шлам | 42.2 | 57.88 | 8.36 | 5.74 | 1.1 | 1.36 | 0.2 | 9.79 | 0.7 |
Пыль ЦВС | 50.2 | 68.54 | 3.7 | 1.2 | 0.4 | 0.9 | 0.95 | 4.95 | 0.9 |
Пыль ЭСПЦ | 49.6 | 65.17 | 7.28 | 6.5 | 1.0 | 0.8 | 1.52 | 1.21 | 0.6 |
Известковая пыль | 1.1 | 1.5 | 5.2 | 66.7 | 0.6 | 0.5 | - | - | 0.1 |
Окалина | 70.0 | 36.2 | 2 | 1.7 | 0.3 | 0.5 | 0.8 | - | 0.04 |
Эти отходы должны отвечать определенным требованиям. Так, шламы, используемые при окусковании, должны иметь:
- влажность не более 8-12 %;
- крупность после сушки не более 6 мм;
- минимальное приведенное содержание железа не менее 45 %;
- содержание цинка: при использовании брикетов в доменном производстве – не более 1 %, в сталеплавильном – не регламентируется.
Колошниковая пыль, выносимая потоком газов через колошник доменной печи и осаждаемая из газа в пылеуловителях, по составу приблизительно соответствует составу шихты, но содержит еще 9-11 % С и до 12 % СаО – это делает ее ценнейшим сырьем для брикетов [5].
По фракционному составу наиболее приемлемыми являются материалы крупностью 0-5 мм. Так как наличие в сырье преимущественно крупных зерен приводит к образованию структуры брикетов с большими пустотами, которые необходимо заполнять связующими. Это не только удорожает стоимость брикетов, но и делает их малопрочными и термически неустойчивыми. Большое содержание в отходах пылевидных классов требует интенсивного перемешивания компонентов шихты, повышения расхода связующих и давления прессования.
Особое значение для рудных концентратов и отходов производства имеет влажность. Наличие в брикетируемом материале более 6-8 % влаги отрицательно влияет на прочность брикетов.
Одним из важных компонентов брикетируемой шихты является связующее – вспомогательный материал, улучшающий слипаемость частиц и повышающий прочность брикетов до заданного уровня. Оно должно соответствовать следующим требованиям:
- обеспечивать высокую холодную и горячую прочность при минимальном расходе;
- обеспечивать быструю схватываемость;
- вносить минимальное количество вредных, балластных и других примесей, небезопасных для обслуживающего персонала и снижающих качество конечного продукта;
- быть распространёнными и обладать невысокой стоимостью;
- не требовать сложных приёмов и операций по их использованию;
- обеспечивать максимальную влагостойкость брикетам.
Связующее является определяющим условием прочности и в значительной мере – восстановимости брикетов. Добавление его в шихту строго регламентировано. Так, при увеличении расхода связующего, брикеты становятся более прочными, но их себестоимость возрастает, к тому же, снижается содержание железа и других полезных компонентов [6].
Для достижения заданных требований, все шихтовые материалы подвергают предварительной подготовке. Подготовка отходов к брикетированию является достаточно трудоемким и затратным процессом, состоящим из следующих технологических операций:
- выравнивание влажности, химического и фракционного составов путём специальной (послойной) укладки сырых и сухих компонентов шихты;
- для переувлажнённого сырья следует предусмотреть его химическую или тепловую сушку;
- гашение извести, используемой в качестве связующего;
- удаление инородных фракций и металлических включений размером более 10 мм, которые могут привести к поломке бандажей пресса;
- доизмельчение сырья избыточной крупности и др.
3.2 Требования к металлургическим свойствам брикетов
Как и к другим шихтовым материалам, к брикетам предъявляются жесткие требования не только по химическому и гранулометрическому составам, но и по физико-механическим свойствам.
Брикеты могут иметь разнообразный химический состав, с различным использованием легирующих добавок и флюсов. Включение того или иного компонента зависит от требований металлургического передела, в котором планируется дальнейшее их использование. Чаще производят двух-или-трехкомпонентные брикеты. Чем меньше компонентов и чем ближе они по составу друг к другу, тем более гомогенная шихта, а значит выше качество брикетов. К тому же увеличение количества материалов приводит к усложнению технологии подготовки и усреднения шихты.
Основными регламентирующими параметрами металлургических брикетов является их механическая и термическая прочность, пористость и плотность, атмосферостойкость. В то же время каждый металлургический процесс предъявляет дополнительные требования к брикетам.
В частности, брикеты, удовлетворяющие требованиям доменной плавки, должны быть устойчивы при температуре 900-1300 °С, иметь сопротивление сжатию выше 58 Н/см2, обладать высокой пористостью и газопроницаемостью и, вместе с тем, быть водоустойчивыми. Размягчение материалов, предназначенных для доменной плавки, должно осуществляться в интервале температур от 1050 до 1200 °С.
Брикеты для сталеплавильного производства должны выдерживать нагревание до 1500 °С в течение трёх минут и при этом не разваливаться на куски, а также иметь пористость не более 5-10 %, их сопротивление сжатию должно быть не ниже 25 Н/см2 [7].
Во многом эти параметры зависят от размеров и формы брикетов, которые могут быть различными – от блока 600х300х200 мм и массой 70-100 кг, до гранул диаметром 5-10 мм и массой до 10 г. Размер окускованного сырья для условий доменной плавки ограничивают некоторыми предельными значениями. Так, с учетом возможностей выноса потоком газа, газопроницаемости, восстановимости и других условий его минимальный размер составляет 10-12 мм, а максимальный – 60-100 мм.
Форма брикетов влияет существенным образом не только на их прочность, но и на продолжительность металлургической обработки. Брикеты овальной, чечевидной и сферической формы (Рисунок 1) более терпимы к давлению и при приложении нагрузки принимают более удобное положение, распределяя усилие равномерно на весь расположенный ниже массив. Острые выступы брикетов более подвержены сколам, поэтому отсутствие острых ребер, кромок и выступов в брикетах повышает их прочность.
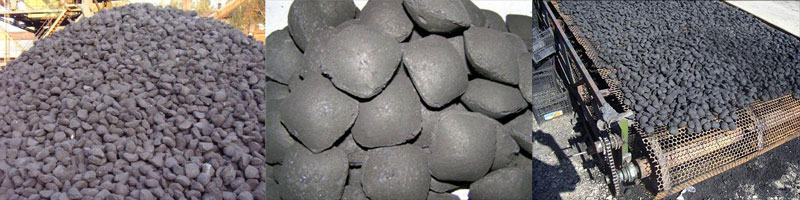
Рисунок 1 – Оптимальная форма металлургических брикетов
4. Схема технологического процесса
На основании проведенного анализа, с учетом поставленных требований, наиболее приемлемой принята схема «холодного» брикетирования с использованием в качестве связки – извести. Гашёная известь является сравнительно дешёвым, достаточно прочным и хорошо смешивающимся связующим и одновременно флюсующим материалом. Для достижения необходимой прочности брикетов ее добавляют в количестве до 10 % от массы шихты [8].
Предлагаемый способ брикетирования состоит из следующих основных операций (Рисунок 2):
- Хранение компонентов шихты;
- Дозирование и смешивание сырьевых материалов;
- Прессование полученной шихты в брикеты заданной формы;
- Обработка «сырых» брикетов (сушка, карбонизация);
- Доставка потребителю.
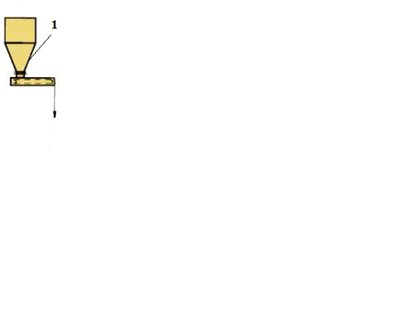
1 – бункер с шихтой; 2 – бункер со связующим; 3 – емкость с водой; 4 – смеситель сухой и увлажненной шихты; 5 – пресс; 6 – грохот, 7 – возврат; 8 – дробилка; 9 – участок набора прочности; 10 – готовые брикеты.
Рисунок 2 – Схема технологического процесса производства брикетов
Хранение материалов, которые прошли предварительную подготовку, осуществляется на открытых или закрытых площадках. Тонкодисперсные материалы, для предотвращения их пыления, хранятся в закрытых бункерах. Длительное хранение гашёной извести даже в закрытых бункерах для предотвращения её карбонизации не рекомендуется.
Питание и дозировка являются важными операциями по подготовке шихты к брикетированию. Постоянное, устойчивое питание способствует равномерной работе оборудования, а правильная дозировка обеспечивает не только заданный химико-минералогический состав брикетов, но и высокую прочность [9].
Перемешивание шихты происходит в специальном двухвальном смесителе: сначала в сухом виде, а затем с добавлением влаги или пара, если это необходимо. Подготовленная смесь направляется на пресс.
Прессование брикетов является важнейшим, главным звеном процесса брикетирования, определяющим сущность данного метода окускования. Оно придаёт брикетам нужную форму, объём и плотность, что во многом определяет их конечную прочность. Прессование включает такие операции, как подача шихты на прессование, подпрессовка (предварительное уплотнение) шихты, заполнение прессующих ячеек, уплотнение шихты и извлечение брикетов.
Вальцовые прессы (Рисунок 3) являются наиболее распространёнными. Они обладают высокой производительностью до 100 т брикетов в час и более, развивают большие давления прессования (до 150 МПа), позволяющие получить достаточно прочные брикеты, просты в управлении и легко автоматизируемы [10].
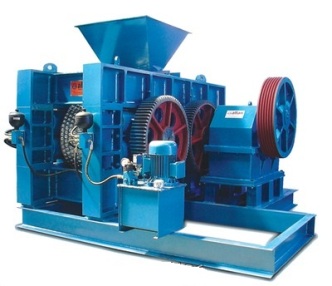
Рисунок 3 – Вальцовый пресс
Процесс прессования заключается в том, что шихта направляется в зазор между двумя вальцами, вращающимися навстречу друг другу. При вращении вальцов происходит сближение ячеек, захват шихты и её уплотнение. При дальнейшем вращении вальцы расходятся, и брикеты под собственным весом и небольшим расширением после снятия давления выпадают из ячеек.
Наряду с простотой формообразования вальцовые прессы имеют и недостатки: отсутствие полного закрытия формующих элементов, а также необходимость подпрессовки.
Отсев и возврат мелочи. При прессовании на брикетах образуются кромки, заусенцы, которые при извлечении и падении продукта обламываются. Некоторые брикеты при выпадении из ячеек разрушаются. Это приводит к образованию некоторого количества мелочи, являющейся некондиционным продуктом. Его целесообразно отсеять и возвратить в процесс, что повышает его экономичность, а также предотвращает пыление при дальнейшем движении брикетов по технологической линии.
Упрочнение брикетов является заключительным звеном процесса брикетирования, определяющим конечную прочность брикетов. Свежеизготовленные брикеты обладают невысокой прочностью, что приводит к необходимости их упрочнения. Во время упрочнения происходят сложные физические и химические процессы, в результате которых прочность брикетов возрастает многократно.
Карбонизация, т.е. взаимодействие CaO с углекислым газом, является действенным способом упрочнения брикетов. Ее целесообразно вести в специальных ленточных сушилах, с использованием, например, дымовых газов, содержащих 20-25 % СО2. При атмосферном давлении и температуре 60-65 0С продолжительность карбонизации составляет примерно 2-2,5 часа. Добавка в брикеты материалов, выделяющих СO2, также сокращает длительность карбонизации [11].
Для повышения эффективности упрочнения наряду с интенсивной сушкой в карбонизирующей атмосфере следует применять естественную сушку карбонизацией углекислым газом, содержащимся в атмосферном воздухе, что обеспечит дополнительный прирост прочности.
Правильная организация отгрузки готовых брикетов способствует уменьшению их потерь от разрушения при погрузочно-разгрузочных работах и транспортировке.
Если установка расположена вблизи потребителя, для доставки брикетов можно использовать конвейерный транспорт, расположенный в галерее, предотвращающий попадание влаги. Последнее позволяет отказаться от бункеров готовой продукции и использования колёсного транспорта, что значительно удешевляет стоимость брикетов.
Для уменьшения боя брикетов при падении с высоты при погрузке все загрузочные узлы должны быть снабжены склизами или желобами, смягчающими удар. Места падения брикетов должны быть обрезиненными [12].
5. Эффективность применения брикетов
Использование брикетированного сырья в доменной плавке имеет существенные отличия от использования традиционных материалов. В зависимости от используемого сырья, компонентного состава и способа прессования брикетированный материал может иметь чрезвычайно разнообразные свойства – восстановимость, размягчаемость, усадку.
При добавлении брикетов в доменную печь увеличивается ее производительность. Происходит это, за счет улучшения газопроницаемости столба доменной шихты, вследствие чего увеличивается расход дутья, уменьшается вынос колошниковой пыли и снижается расход кокса.
На сегодняшний день запатентовано значительное множество различных брикетов, предназначенных для использования в доменном переделе, и способов их производства. Наиболее характерными являются железорудные офлюсованные брикеты, офлюсованные рудно-угольные брикеты, железофлюсовые брикеты различных составов, брикеты из колошниковой пыли, шламоуглеродные и другие [13].
Сталеплавильное производство предъявляет менее строгие требования к механической прочности брикетов, поэтому их использование там даёт лучшие результаты, а потому более распространено, чем в доменном производстве.
Использование брикетированных железосодержащих отходов в качестве оборотного продукта в сталеплавильном производстве в настоящее время является не только распространённым способом утилизации пыли, но и одним их способов извлечения цинка. Рациональная схема переработки цинксодержащей пыли электросталеплавильного цеха Донецкого металлургического завода представлена ниже (Рисунок 4).
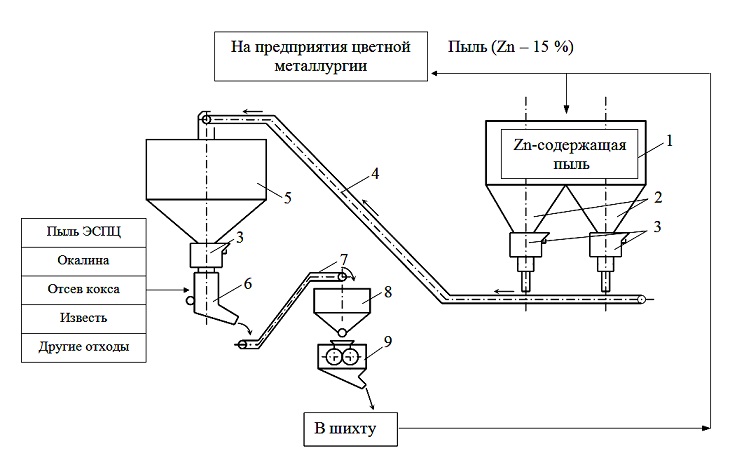
1 – рукавный фильтр, 2 – бункер; 3 – шлюзовые дозаторы, 4 – скребковый конвейер, 5 – накопительный бункер, 6 – вибро-увлажнитель, 7 – ленточный конвейер, 8 – бункер смеси; 9 – вальцовой пресс.
Рисунок 4 – Комплексная схема утилизации электросталеплавильной пыли
Уловленная в рукавном фильтре пыль из бункеров через шлюзовые дозаторы подается на скребковый конвейер, которым транспортируется в накопительный бункер. Из бункера сухая пыль через дозатор подается в вибрационный смеситель-увлажнитель, в котором пыль увлажняется водой и смешивается с другими отходами. Увлажненная смесь подается ленточным конвейером в промежуточный бункер, из которого она поступает в вальцовый пресс. Готовые брикеты транспортируют в шихтовый отделения электросталеплавильного цеха и подаются в печь вместе с шихтой.
После нескольких циклов содержание цинка в пыли возрастет и при достижении определенной концентрации, пригодной для извлечения цинка, ее выводят из цикла и отправляют на предприятия цветной металлургии как ценное вторичное сырье.
Опыт использования брикетов в сталеплавильном производстве показывает, что добавки брикетированных материалов существенно улучшают технико-экономические показатели (сокращают длительность плавки, способствуют быстрому наведению шлака, снижают угар металла, уменьшают расход металлолома) [14].
Выводы
Литературный анализ отечественного и зарубежного опыта в области брикетирования показывает что:
- Процесс брикетирования позволяет снизить антропогенную нагрузку на окружающую среду за счет утилизации металлургических отходов.
- Внедрение брикетного производства способствует уменьшению пылегазовых выбросов, образующиеся при традиционных способах окускования железорудного сырья.
- При употреблении металлургических брикетов в доменном производстве наблюдается: существенное увеличение производительности, экономия первичного сырья, снижение расхода энергоресурсов, повышение выхода годного, улучшение качества металла.
- Использование процесса брикетирования для переработки электросталеплавильной пыли позволяет организовать рециклинг цинка, его накопление и дальнейшее использование на предприятиях цветной металлургии.
- Организация брикетных фабрик позволяет снизить стоимость конечного продукта за счет возвращения полезных материалов в технологический процесс, а также благодаря снижению выплат на размещение отходов.
На сегодня, в чёрной металлургии Украины, несмотря на рост потребности в новых материалах, брикетирование не находит должного внимания, которое оно по праву заслуживает. Хотя для его развития имеется широкая как сырьевая, так и технологическая база. Поэтому вовлечение в эту сферу производства современных металлургических предприятий является актуальной задачей не только экологии, но и экономики.
Список источников
- Банный Н.П. Экономика чёрной металлургии СССР / Н.П. Банный, А.А. Федотов, П.А. Ширяев и др. – М.: Металлургия, 1978. – 344 с.
- Буторина И.В. Основы устойчивого развития металлургического производства / И.В. Буторина. – Донецк: Каштан, 2005. – 332 с.
- Вегман Е.Ф. Окускование руд и концентратов / Е.Ф. Вегман. – 3-е изд., перераб. и доп. – М.: Металлургия, 1984. – 256 с.
- Равич Б.М. Брикетирование в цветной и чёрной металлургии / Б.М. Равич. – М.: Металлургия, 1975. – 232 с.
- Фоменко А.И. Утилизация шламов металлургических производств / А.И. Фоменко // Изв. вузов: Чёрная металлургия. – 2001. – № 11. – С. 70-71.
- Тюренков Н.Г. Брикетирование руд / Н.Г. Тюренков. – М.: Металлургиздат, 1948. – 128 с.
- Ожогин В.В. Взаимосвязь показателей механической прочности брикетированных материалов / В.В. Ожогин // Вісник Приазов. держ. техн. ун-ту: Зб. наук. пр. – Маріуполь, 2006. – Вип. 16. – С. 17-21 [электронный ресурс] – Режим доступа: eIRPSTU
- Корж А.Т. Особенности технологии подсушки шламов известью / А.Т. Корж, А.Ф. Голубов // Чёрная металлургия: Бюл. ЦНИИЧермет. – 1971 – № 5. – С. 49-50.
- Носков В.А. Валковый пресс для брикетирования мелкофракционных отходов производства и сырья / В.А. Носков // Металлург. и горноруд. пром-сть. – 1999. – № 2 – С. 100-102 [электронный ресурс] – Режим доступа: MetalJournal
- Ожогин В.В. Совершенствование ресурсосберегающей технологии получения и использования высокопрочных шламовых брикетов в аглодоменном производстве: дис. канд. техн. наук: 05.16.02. – Мариуполь, ПГТУ, 2004. – 207 с.
- Пат. 2083681 РФ, МПК6 С21С5/06, С22В1/24, 1/242. Брикет для производства чугуна и стали / Агеев Е.Е., Бондарев Ю.А., Булгаков В.Г. и др.; опубл. 10.07.1997.
- Носков В.А. Экспериментальные исследования основных параметров и режимов брикетирования мелкофракционных техногенных отходов в валковых прессах / В.А. Носков, Б.Н. Маймур, В.И. Петренко и др. // Металлург. и горноруд. пром-сть. – 1999. – № 6. – С. 104-107 [электронный ресурс] – Режим доступа: MetalJournal
- Информационно-рекламный проспект фирмы "Sahut-conreur" [электронный ресурс]. – Режим доступа: Sahut-conreur
- Ожогин В.В. Рециклинг пылевидных отходов сталеплавильного производства / В.В. Ожогин // Бюл. науч.-техн. и эконом. информ.: Чёрная металлургия. – 2006. – № 8. – С. 72-74.