Abstract
Content
- Introduction
- 1. A goal and objectives
- 2. Advantages of the process of briquetting
- 3. Requirements for the charge and ready briquettes
- 3.1 Characterization of materials
- 3.2 Requirements for metallurgical properties of briquettes
- 4. Process flow diagram
- 5. The efficiency of briquettes
- Conclusions
- References
Introduction
Creation and implementation of more sustainable and environmentally friendly production is the main task of modern humanity, faced with the problem of global environmental pollution and depletion of the planet. For example, steel is one of the most material-and energy-intensive and polluting industries. The total consumption of raw material resources, the cycle from the extraction of ore and coal to rolling up to 7 tons per 1 ton of finished steel [1]. On a full cycle of metallurgical plant capacity of 5 million tons of steel per year produced 2,3 million tons of slag, 0,8 million tons of dust, sludge and scale, 25 tons of sulfur compounds, 120 tons of oxides of carbon, nitrogen and other elements [2]. Therefore, the issue of rational use of natural resources, as well as the integrated waste management – the most relevant today for the industry.
The most acceptable is not only environmentally, but also from an economic point of view is the recycling of waste within its own production, as it allows you to use them as a relatively cheap raw materials, thereby significantly reducing the cost of raw mix, improve product quality and competitiveness and, more importantly, reduce the cost of the finished product.
1. A goal and objectives
Master's thesis is devoted to research briquetting process as one of the generic training areas of metallurgical wastes.
The main goal – developing a rational technology of preparation and briquetting of ferrous metallurgical wastes.
The novelty lies in the fact that in the proposed universal scheme for iron briquettes from waste Donetsk Metallurgical Plant, for the purpose of their processing at the plant.
In this paper, the following main tasks:
- To examine the main types of waste produced at PJSC "Donetskstal MZ", to study their characteristics (physical and chemical properties, particle size, etc.);
- Analyze requirements for metallurgical briquettes, and on this basis to select the most appropriate scheme of training of waste the company;
- Develop a process line for production of iron briquettes;
- Determine the environmental and economic benefits derived through the use of briquettes in the blast furnace and steelmaking processes.
2. Advantages of the process of briquetting
At present, there are three basic ways receipt of pieces in the industry – this agglomeration, granulation and briquetting. There was widespread first two. This is due primarily to the high productivity of sintering machines, as well as the possibility of obtaining products with high content of iron and other mineral components.
Recently, due to lack of natural resources, as well as excessive accumulation of waste in the industry have been increasingly applied dust materials – concentrates deep concentration, as well as sludge and dust. However, their use in the sintering process and the production of pellets is limited, since it leads to a deterioration in the quality of the finished product.
Briquetting process has a number of significant advantages:
- imposes less stringent requirements for the quality of raw materials allows granulate broad classes of size less than 10 mm in almost all proportions and compositions;
- from a technological point of view, is simple;
- briquette plant is mobile and does not occupy a large area;
- saved for briquetting properties of the components contained in the pellets;
- from an environmental point of view is much cleaner way to agglomeration;
- pellets expand the raw material and fuel and energy base metals [3].
Experience of many steel companies found that the best performing implemented in conjunction with other methods of agglomeration. They do not compete among themselves, and cost-effective complement each other [4].
3. Requirements for the charge and ready briquettes
Currently, there are various schemes of briquetting, very different from each other. For example, how to distinguish between "cold" and "hot" briquetted passing, respectively, at normal and high temperatures. Also briquetting with a binder or without compression at different pressures, with different ways of hardening the raw briquettes (thermal and chemical), etc.
3.1 Characterization of materials
The main waste generated by PJSC "Donetskstal – Ministry of Health," and in need of disposal, owned domain, steelmaking and rolling processes. This flue dust, dust, exhaust the central station and aspirating systems, sludge from a wet gas cleaning blast furnace gas, coke screenings, as well as EAF dust, slag and iron filings (Table 1).
Table 1 – Chemical composition of certain types of waste
Material | FeO | Fe2O3 | SiO2 | CaO | MgO | Al2O3 | MnO | C | S |
Kol. dust | 42.1 | 53.76 | 12.0 | 11.56 | 0.9 | 1.13 | 0.26 | 10.69 | 0.4 |
Blast-furnace shlam | 42.2 | 57.88 | 8.36 | 5.74 | 1.1 | 1.36 | 0.2 | 9.79 | 0.7 |
Dust PCV | 50.2 | 68.54 | 3.7 | 1.2 | 0.4 | 0.9 | 0.95 | 4.95 | 0.9 |
EAF Dust | 49.6 | 65.17 | 7.28 | 6.5 | 1.0 | 0.8 | 1.52 | 1.21 | 0.6 |
Lime dust | 1.1 | 1.5 | 5.2 | 66.7 | 0.6 | 0.5 | - | - | 0.1 |
Scale | 70.0 | 36.2 | 2 | 1.7 | 0.3 | 0.5 | 0.8 | - | 0.04 |
These wastes must meet certain requirements. Thus, the sludge used for agglomeration should have:
- Humidity of no more than 8-12%;
- Particle size after drying is not more than 6 mm;
- The minimum reduced the iron content of at least 45% [5].
For the fractional composition most suitable materials are of size 0-5 mm.
Of particular importance for ore concentrates and waste has a moisture content. The presence of material more than 6-8% moisture affects the strength of the briquettes.
One important component briquettes – supporting material. It must meet the following requirements:
- To provide a high strength hot and cold with a minimum flow rate;
- To provide rapid bonding strength
- To make the minimum number of harmful, ballast and other impurities, unsafe for staff and reduce the quality of the final product;
- To be common and have a low cost [6].
To achieve the specified requirements, all charge materials are subjected to preconditioning. Preparing wastes for briquetting is quite time-consuming and costly process, which consists of the following operations:
- Alignment of moisture, chemical and fractional composition by a special (layered) laying damp and dry components of the charge;
- For waterlogged material should be provided to chemical or thermal drying;
- Slaked lime, used as a binder;
- Removal of foreign factions and metallic inclusions larger than 10 mm, which can cause damage to the tires press;
- Regrinding the excess of raw material particle size, etc.
3.2 Requirements for metallurgical properties of briquettes
As with other materials to the briquettes strict requirements not only on the chemical and compositions, but also on physical and mechanical properties.
The main parameters governing the metallurgical briquettes is the mechanical and thermal strength, porosity and density, and weathering. At the same time every metallurgical process imposes additional requirements for the briquettes.
In particular, the pellets that meet the requirements of the blast furnace must be stable at a temperature of 900-1300 °С, a resistance to compression above 58 Н/см2. Softening of the materials for blast furnace should be carried out at temperatures ranging from 1050 до 1200 °С.
Briquettes for steelmaking to withstand heat up to 1500 ° C for three minutes and does not crumble to pieces, and have a porosity of no more than 5-10% of their compressive strength shall be not less than 25 Н/см2 [7].
The form of pellets significantly affects not only their strength but also on the duration of the metallurgical processing. The briquettes are oval and spherical (Picture 1) are more tolerant of pressure and when the load is taking a more comfortable position, distributing the load evenly on the entire array is located below. Sharp protrusions briquettes are more prone to chipping, so no sharp edges, edges and ledges in blocks increases their strength.
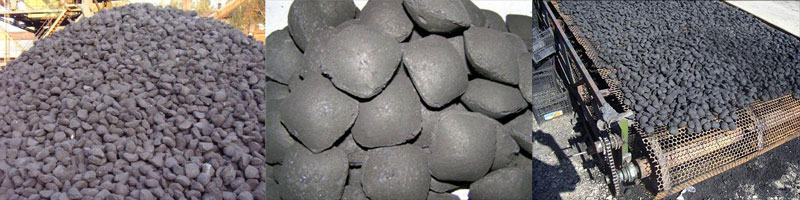
Picture 1 – Optimum form of metallurgical briquettes
4. Process flow diagram
Based on this analysis, given the set of requirements, the most appropriate scheme is adopted the "cold" briquetting with a binder – lime. Slaked lime is relatively cheap, strong enough and well miscible binder and simultaneously fluxing material. To achieve the necessary strength of briquettes in an amount up to 10% by weight of the charge [8].
The proposed method of briquetting consists of the following operations (Picture 2):
- Storage of the mixture components;
- Dosing and mixing of raw materials;
- Pressing the resulting mixture into briquettes given shape;
- The processing of "raw" briquettes (drying, carbonation);
- Delivery to the consumer.
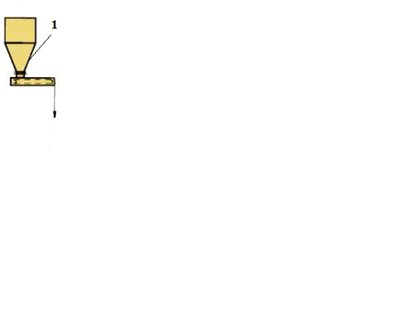
1 – the bunker with the charge 2 – bunker with a binder, 3 – a bowl of water, 4 – mixing dry and moist mixture, 5 – crushers, 6 – press, 7 – rumbling, 8 – back 9 – part of curing, 10 – ready-made bricks.
Picture 2 – The scheme of the technological process of production of briquettes
Storage of materials that have been pre-training, carried out on the open or closed sites.
The mixing of the charge is a special twin-shaft mixer, first dry, then with the addition of water or steam, if necessary. The prepared mixture is sent to the press [9].
Pressing Briquette is a major, major link in the process of briquetting of defining the essence of the method of agglomeration.
Roller presses (Picture 3) are most common. They have a high capacity of up to 100 tons of briquettes per hour or more, and develop high compaction pressure (150 MPa) to obtain a sufficiently strong briquettes, easy to operate and is easily automated [10].
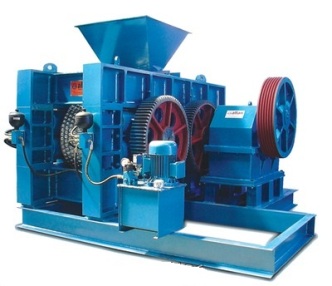
Picture 3 – Roller press
The process of extrusion is that the charge directed into the gap between two rollers rotating in opposite directions. When you rotate the rollers is the convergence of cells, the capture of the charge and its seal. With further rotation of the rollers apart, and the pellets under its own weight and a small extension after removal of the pressure drop of the cell.
When pressing on the bricks formed edges, burrs, which are the extraction of the product break off and fall. Some of the bricks on a roll of the cells are destroyed. This leads to the formation of a number of little things, which is defective product. Its advisable to weed out and return to the process, which increases its efficiency, and prevents dusting with a further motion for briquettes production line.
Hardening of briquettes is the final link in the process of briquetting.
Carbonation, the interaction of CaO with carbon dioxide is an effective way of hardening the briquettes. It is advisable to conduct a special belt dryers, using, for example, flue gas containing 20-25% СО2. At atmospheric pressure and temperature of 60-65 ° C the duration of carbonization is approximately 2-2,5 hours [11].
Proper organization of shipments of finished briquettes can reduce their losses from damage during loading and unloading and transportation [12].
5. The efficiency of briquettes
When you add briquettes in the blast furnace increases its performance. This occurs by improving the gas permeability of the charge column of the domain, resulting in increased consumption of blast furnace dust removal decreases and reduces the consumption of coke [13].
Steelmaking imposes less stringent requirements on the mechanical strength of briquettes, so they use it gives the best results, and therefore more common than in the blast furnace.
Use of briquetted iron waste as a working product in steel production is now not only a common method of disposal of dust, but also one of the methods of extraction of zinc. A rational scheme of recycling zinc-containing dust, electric plant, Donetsk metallurgical plant is presented below (Picture 4).
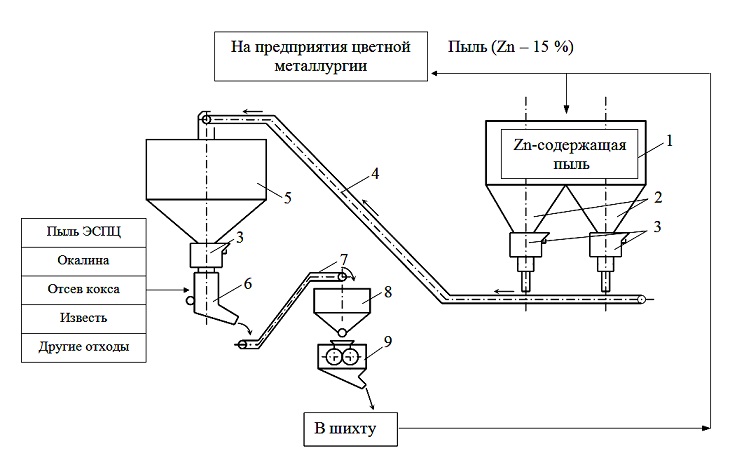
1 – bag filter, 2 – bunker, 3 – rotary feeders, 4 – scraper conveyor, 5 – storage bunker, 6 – vibration damper, 7 – a conveyor belt, 8 – tank mixtures, 9 – roller press.
Picture 4 – Integrated circuit utilization of electric dust
Captured by a bag filter dust from the hopper through a rotary feeders is fed to the scraper conveyor, which is transported to the storage bin. From the hopper through the spout dry dust is fed into the mixer, vibratory humidifier, in which the dust is moistened with water and mixed with other wastes. Hydrated mixture is fed to an intermediate belt conveyor hopper, from which it comes in a roller press. Finished pellets transported to the charge separation electric shop, and fed into the furnace together with the charge.
After several cycles of zinc in the dust will rise and when you reach a certain concentration, suitable for the extraction of zinc, it is removed from the cycle and sent to the non-ferrous metals as a valuable secondary raw materials.
Experience in the use of briquettes in steel production shows that the addition of briquetted material substantially improve the technical and economic indicators (reducing the duration of melting, contribute to the rapid putting in slag reduce metal waste, reduce consumption of scrap metal) [14].
Conclusions
Literary analysis of domestic and foreign experience in the field of briquetting shows that:
- Briquetting process to reduce human pressure on the environment by recycling of metallurgical wastes.
- The introduction of briquette production helps to reduce dust and gas emissions produced by traditional methods of agglomeration of iron ore.
- If you use steel pellets in blast furnace production is observed: a significant increase in productivity, saving raw materials, reducing energy consumption, increase yield, improve the quality of the metal.
- Using the briquetting process for recycling of electric dust can arrange recycling of zinc accumulation and its further use in non-ferrous metallurgy.
- Organization of briquette factories to reduce the cost of the final product due to the return of useful materials in the manufacturing process, as well as by reducing payments for waste disposal.
References
- Банный Н.П. Экономика чёрной металлургии СССР / Н.П. Банный, А.А. Федотов, П.А. Ширяев и др. – М.: Металлургия, 1978. – 344 с.
- Буторина И.В. Основы устойчивого развития металлургического производства / И.В. Буторина. – Донецк: Каштан, 2005. – 332 с.
- Вегман Е.Ф. Окускование руд и концентратов / Е.Ф. Вегман. – 3-е изд., перераб. и доп. – М.: Металлургия, 1984. – 256 с.
- Равич Б.М. Брикетирование в цветной и чёрной металлургии / Б.М. Равич. – М.: Металлургия, 1975. – 232 с.
- Фоменко А.И. Утилизация шламов металлургических производств / А.И. Фоменко // Изв. вузов: Чёрная металлургия. – 2001. – № 11. – С. 70-71.
- Тюренков Н.Г. Брикетирование руд / Н.Г. Тюренков. – М.: Металлургиздат, 1948. – 128 с.
- Ожогин В.В. Взаимосвязь показателей механической прочности брикетированных материалов / В.В. Ожогин // Вісник Приазов. держ. техн. ун-ту: Зб. наук. пр. – Маріуполь, 2006. – Вип. 16. – С. 17-21 [электронный ресурс] – Режим доступа: eIRPSTU
- Корж А.Т. Особенности технологии подсушки шламов известью / А.Т. Корж, А.Ф. Голубов // Чёрная металлургия: Бюл. ЦНИИЧермет. – 1971 – № 5. – С. 49-50.
- Носков В.А. Валковый пресс для брикетирования мелкофракционных отходов производства и сырья / В.А. Носков // Металлург. и горноруд. пром-сть. – 1999. – № 2 – С. 100-102 [электронный ресурс] – Режим доступа: MetalJournal
- Ожогин В.В. Совершенствование ресурсосберегающей технологии получения и использования высокопрочных шламовых брикетов в аглодоменном производстве: дис. канд. техн. наук: 05.16.02. – Мариуполь, ПГТУ, 2004. – 207 с.
- Пат. 2083681 РФ, МПК6 С21С5/06, С22В1/24, 1/242. Брикет для производства чугуна и стали / Агеев Е.Е., Бондарев Ю.А., Булгаков В.Г. и др.; опубл. 10.07.1997.
- Носков В.А. Экспериментальные исследования основных параметров и режимов брикетирования мелкофракционных техногенных отходов в валковых прессах / В.А. Носков, Б.Н. Маймур, В.И. Петренко и др. // Металлург. и горноруд. пром-сть. – 1999. – № 6. – С. 104-107 [электронный ресурс] – Режим доступа: MetalJournal
- Информационно-рекламный проспект фирмы "Sahut-conreur" [электронный ресурс]. – Режим доступа: Sahut-conreur
- Ожогин В.В. Рециклинг пылевидных отходов сталеплавильного производства / В.В. Ожогин // Бюл. науч.-техн. и эконом. информ.: Чёрная металлургия. – 2006. – № 8. – С. 72-74.