Реферат по теме выпускной работы
Содержание
- Введение
- 1 Технология проведения горячего ремонта кладки камер коксования методом керамической наплавки
- 2 Описание технологического процесса приготовления керамической смеси
- 2.1 Дробление кремния
- 2.2 Измельчение и помол кремния
- 2.3 Сушка исходных компонентов керамической смеси
- 2.4 Рассев исходных компонентов керамической смеси
- 2.5 Дозировка и смешение компонентов смеси
- 2.6 Затаривание готовой продукции
- Выводы
- Список литературы
Введение
Длительная эксплуатация коксовых батарей порождает проблему стойкости кладки камер коксования, поэтому сохранность кладки, максимально возможное удлинение срока ее службы – весьма актуальная задача, от успешного решения которой зависят важнейшие технико-экономические показатели работы отрасли.
Последние десятилетия в отечественной коксохимии и в странах с развитой коксохимической промышленностью широким фронтом ведутся работы по совершенствованию методов и технологий профилактического ремонта кладки камер коксования, особенно горячих ремонтов – с целью увеличения стойкости наносимого ремонтного слоя, снижения трудовых, материальных затрат, а также затрат времени на проведение ремонтов [1].
В настоящее время в активе коксохимиков имеется значительный арсенал методов горячего ремонта кладки коксовых печей и устройств для его осуществления. Традиционные способы горячего ремонта – мокрое и полусухое торкретирование; они распространены повсеместно. Мокрое торкретирование долгое время было единственным промышленным способом профилактического ремонта кладки камер коксования из-за дешевизны, простоты осуществления, неприхотливого оборудования. Однако, недостаточная стойкость ремонтного слоя, термические удары, происходящие при нанесении мокрой керамической смеси на раскаленную поверхность кладки, заставили искать более совершенные способы осуществления профилактических ремонтов [2].
Многочисленные разработки (как за рубежом, так и в нашей стране) новых современных способов горячего ремонта, свободных от указанных выше недостатков, присущих мокрому и полусухому торкретированию, можно сгруппировать следующим образом:
- Методы напыления (
припыливания
) огнеупорного материала на кладку с последующим спеканием его за счет аккумулированного кладкой тепла или тепла пламени горячего коксового газа, ацетилена и др. - Методы факельного торкретирования, заключающиеся в расплавлении огнеупорного порошка за счет тепла высокотемпературного пламени горения пропана в кислороде и нанесении его на ремонтируемую поверхность.
- Методы керамической наплавки (
cварки
), заключающиеся в том, что сухой огнеупорный мертель в смеси с металлическим порошком подается струей кислорода на раскаленную поверхность кладки, происходит экзотермическая реакция окисления металлической составляющей керамической смеси в кислороде, под действием выделяющегося тепла огнеупорная часть керамической смеси расплавляется и вместе с продуктами реакции окисления металлов составляет расплав, заполняющий дефекты кладки. - Методы плазменного торкретирования, в которых для расплавления огнеупорного материала используется тепло плазмы инертных газов [1].
1 Технология проведения горячего ремонта кладки камер коксования методом керамической наплавки
Способ горячего ремонта кладки камер коксования методом керамической наплавки – это сложный физико-химический процесс.
Сущность данного метода заключается в следующем: сухой торкрет-порошок в среде чистого кислорода наносится на поврежденный участок кладки коксовой печи с температурой не ниже 700-800 °С. За счет выделения тепла химических экзотермических реакций между кислородом и топливной составляющей керамической смеси (алюминиевая пудра, кремний кристаллический) происходит расплавление ее огнеупорных компонентов (динасовый мертель или кварцевый песок, молотый диабаз) с последующим заполнением дефектов кладки [3]. При затвердевании расплава, благодаря определенному сочетанию компонентов керамической смеси, образуется монолитная структура, по-своим свойствам близкая к материалу кладки с керамической связью между шамотным кирпичом кладки и ремонтным слоем, что позволяет получить высокую стойкость и прочность нанесенного таким способом покрытия [4].
Процесс нанесения наплавки представлен на рисунке 1[11].
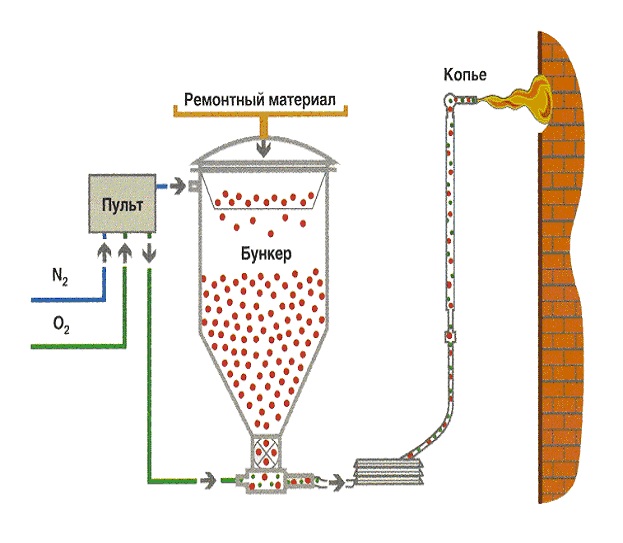
Рисунок 1 – Технологическая схема процесса нанесения керамической смеси
Качество наплавки зависит не только от состава керамической смеси, но и от таких параметров как расход кислорода, скорость нанесения наплавляемой керамической смеси, температура кладки камер коксования, состояние поверхности ремонтируемой зоны, а также от субъективных причин, таких как подготовленность персонала к работе новым аппаратом (рис.2)[5].
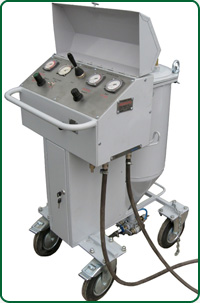
Рисунок 2 – Установка для керамической сварки МаКС
Таблица 1 – Основные технические характеристики установки МаКС
Наименование | Единица измерения | Значение |
Объём бака ремонтного материала: полный / рабочий | л | 37–30 |
Производительность | кг/ч | до 160 |
Давление газов на входе, не более: МПа (кгс/см²) | кислород | 0,60÷0,63 |
азот | 0,70÷0,80 | |
Расход газов при давлении 0,6÷0,8 МПа (6÷8 кгс/см²) | м³/мин | 0,4÷0,7 |
Дальность подачи ремонтного материала | м | до 20 |
Габариты, В×L×H | мм | 510×780×1000 |
Низкая температура кладки камер коксования, а также плохо зачищенные от графитовых отложений ремонтируемые участки кладки приводят к плохому сцеплению материала кладки с наплавкой, что снижает прочность сцепления с кладкой. Повышенный расход кислорода приводит к снижению огнеупорности, а большая скорость нанесения наплавляемой массы к непроплавленности, рыхлости и высокой пористости наплавки. Поэтому очень важен выбор оптимального режима проведения керамической наплавки [4].
Необходимым условием нормального протекания процесса керамической наплавки является соответствие стехиометрическому соотношению весовых расходов смеси и кислорода при температуре кладки камеры коксования не ниже температуры начала экзотермических реакций горения топливной составляющей.
Установлено, что температура начала экзотермической реакции горения алюминия совпадает с его температурой плавления, т.е. составляет 660 ° С.
Следовательно, для успешного и стабильного проведения процесса керамической наплавки необходимо, чтобы температура ремонтируемой кладки коксовой печи была не ниже 700-800 °С [6].
Известно, что расход любого газа, а также сыпучих мелкодисперсных материалов, транспортируемых газом, зависит от его давления, причем с увеличением давления увеличивается расход. Транспортировка смеси по системе в данном способе осуществляется сжатым воздухом. Поэтому основными параметрами процесса керамической наплавки является давление кислорода и давление сжатого воздуха в аппарате для нанесения покрытия.
Выбор оптимальных значений основных параметров процесса керамической наплавки был сделан после проведения серии экспериментальных наплавок на опытном стенде.
Внешний вид шамотной футеровки промышленной печи представлен на рисунке 3 [12].
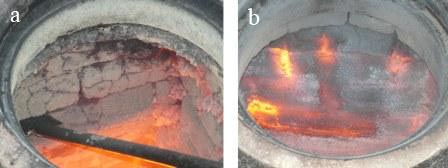
Рисунок 3 – Внешний вид шамотной футеровки промышленной печи до (а) и после (b) ремонта методом керамической наплавки
Немаловажное значение в проведении керамической наплавки имеет дисперсность составляющих компонентов керамической смеси и наличие в ней посторонних примесей.
Опытным путем установлено, что крупность частиц керамической смеси должна составлять не более 1,5 мм, а содержание влаги менее 1 %.
Успешное проведение горячих ремонтов указанным методом в значительной степени зависит от качества смеси, а это накладывает определенные условия и требования к исходным компонентам, процессу приготовления и используемому оборудованию [2].
Смесь готовится механическим смешением сухих порошков в определенной пропорции. Отсутствие сложных физико-химических превращений в процессе приготовления керамической смеси делает ее производство доступным на любом коксохимическом заводе. Однако первоначальное предположение, что без должной организации и подготовки процесса приготовления можно получить качественную смесь, не оправдалось. Возникла необходимость в централизованном ее производстве с подбором необходимого оборудования и разработкой технологического регламента.
Основными стадиями процесса приготовления керамической смеси являются: дробление, измельчение и помол кускового кремния, сушка и рассев исходных компонентов, дозировка и смешение исходных компонентов смеси. Для выполнения указанных операций используется, в основном, стандартное типовое оборудование: щековая и молотковая дробилка, вибромельница, смеситель [7].
2 Описание технологического процесса приготовления керамической смеси
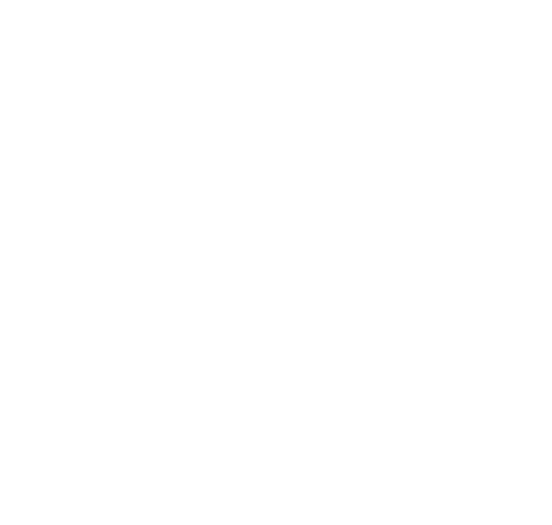
Рисунок 4 – Технологическая схема приготовления керамической смеси
Основными технологическими операциями по приготовлению смеси являются:
2.1 Дробление кремния
Дробление кускового кремния осуществляется на щековой дробилке. Доставка партии кремния со склада к дробилке происходит с помощью погрузчика. Загрузка кускового кремния в загрузочное окно дробилки производится вручную. Дробленный кремний из выходной щели дробилки поступает в приемную емкость и затем направляется на стадию измельчения.
Режим работы дробилки периодический. Количество дробленного кремния в каждом конкретном случае устанавливается отдельным распоряжением начальника участка и зависит от потребности в смеси. Возможна наработка дробленного кремния с запасом от потребности [3].
Ширина выходной щели дробилки устанавливается механизмом регулирования таким образом, чтобы обеспечить минимальный размер (не более 10 мм) кусков дробленного кремния на выходе из дробилки.
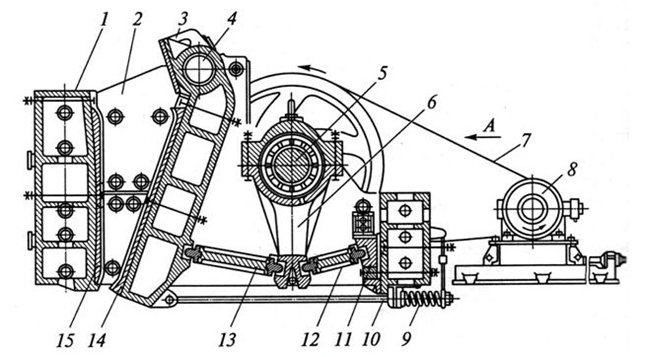
Рисунок 5 – Щековая дробилка
1 – стенка корпуса, 2 – боковая щека, 3 – подвижная щека, 4 – ось, 5 – вал, 6 – шатун, 7 – ременная передача, 8 – электродвигатель, 9 – пружина, 10 – тяга, 11 – упор, 12,13 – распорная плита, 14,15 – дробящие плиты
Дробилка снабжена двумя блокировкам, которые отключает привод дробилки в следующих случаях:
- при попадании в дробилку материала с большой прочностью (более, чем 250 МПа) или куска металла;
- при открывании дверцы, имеющейся в ограждении привода дробилки.
- Огнеупоры для промышленных агрегатов и топок: Справочное издание в двух книгах. Кн. 1 Производство огнеупоров / [И.Д. Кащеев, В.Г. Алфеева, М.Г. Ладыгичев и др.]. – М.: Интермет Инжииринг, 2000. – 663 с.
- Огнеупоры для промышленных агрегатов и топок: Справочное издание в двух книгах. Кн. 2 Служба огнеупоров / [И.Д. Кащеев, В.Г. Алфеева, М.Г. Ладыгичев и др.]. – М.: Интермет Инжииринг, 2002. – 656 с.
- Пак 3.П., Щепетьева Н.П. Экзотермический процесс горения порошкообразного материала – основа эффективного метода ремонта промышленных печей // Материаловедение. 1999. №5.
- Ухмылова Г.С. Продление срока службы коксовых батарей / По материалам IV Европейского конгресса по коксохимическому и доменному производствам // Кокс и химия. 2001. №4. С. 21-24.
- Новые возможности керамической сварки при горячих ремонтах огнеупорной кладки высокотемпературных промышленных агрегатов [электронный ресурс]. – Режим доступа: http://www.npomegatek.ru...
- Щепетьева Н.П., Кёниг А.А., Гришкин В.П., Ходарев Д.В., Кривошеин В.Т. Керамическая сварка – современная технология горячего ремонта футеровок высокотемпературных промышленных агрегатов // Кокс и химия. 2006. № 9. С. 42-46.
- Горячие ремонты коксовых печей керамической наплавкой и смесями СВС / А.Н. Патрушев, В.М. Неволин, В.В. Дябин, Ю.Л. Крутский и др. // Кокс и химия. 2000. №1. С. 16-19.
- Волков А.П., Пушкарев А.А., Хлопотов С.С. Ремонты кладки печных камер коксовых батарей с применением технологии фирмы
Fosbel
// Кокс и химия. 2005. №7. С. 18-20. - Щепетьева Н.П., Кёниг А.А., Гришкин В.П., Ходарев Д.В., Кривошеин В.Т. Новые возможности керамической сварки при горячих ремонтах огнеупорной кладки высокотемпературных промышленных агрегатов // Чёрная металлургия. 2006. № 6. С. 23-26.
- Ухмылова Г.С. Горячий ремонт кладки коксовых печей в сжатые сроки / По материалам IV Европейского конгресса по коксохимическому и доменному производствам // Кокс и химия. 2001. №7. С. 20.
- Технология керамической наплавки [электронный ресурс]. – Режим доступа: http://www.npomegatek.ru...
- Технология керамической наплавки как способ продления срока службы стекловаренных печей [электронный ресурс].– Режим доступа: http://www.npomegatek.ru...
2.2 Измельчение и помол кремния
Измельчение и помол кремния до класса -1,5 мм производится в вибромельнице. Дробленный кремний вручную загружают в камеру при остановленном двигателе через смотровой люк, предварительно сняв быстросъемную крышку. При этом соседний патрубок крышки камеры закрыт заглушкой. Он используется в случае применения жидких сред. Загрузив в вибромельницу 1,0–1,2 м³ кремния и закрыв люк быстросъемной крышкой, включают двигатель на 3 часа [1].
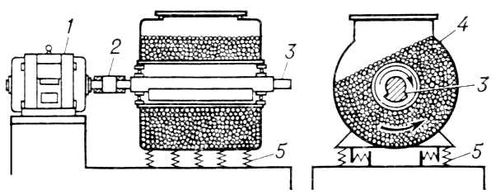
Рисунок 6 – Вибромельница
1 – электродвигатель, 2 – муфта, 3 – вал, 4 – барабан, 5 – пружина
По истечении времени обработки выключают двигатель, открывают выгрузочную решетку, сняв быстросъемную заглушку решетки. Соединяют разгрузочный патрубок с тарой герметичным рукавом, закрепив его хомутом на патрубке, после чего включают двигатель на время, необходимое для выгрузки кремния.
После выгрузки всего кремния двигатель отключают, а полученный продукт направляется на стадию сушки [8].
Возможно, что в молотом кремнии будет содержаться значительное количество (определяется визуально; крупных не промолотых кусочков кремния, тогда в этом случае такой продукт направляется на повторный помол, предварительно прошедший отсев на вибросите.
Повторный помол осуществляется также как и описанная выше операция измельчения и помола кремния.
2.3 Сушка исходных компонентов керамической смеси
В процессе приготовления керамической смеси сушке подвергаются следующие компоненты: кварцевый песок или динасовый мертель, молотый диабаз, молотый кремний.
Сушка производится в сушильном шкафу, режим работы периодический.
Высушиваемый материал по 120-150 кг загружается в сушильный шкаф.
В рубашку сушильного шкафа подается пар или конденсат. Сушка компонентов ведется при температуре 120 °С. Компоненты высушиваются до остаточной влажности не более 1 % (вес.). Продолжительность сушки в сушильном шкафу в зависимости от начальной влажности компонентов составляет 2,5-4,5 часа [9].
Возможно проведение сушки в естественных условиях. Высушиваемый материал равномерно рассыпается на поддонах (гладкая чистая некоррозирующая поверхность) ж в течение 2-3 суток высушивается в сухом хорошо отапливаемом помещении.
Каждый компонент – высушивается раздельно. Не допускается смешение компонентов на данной стадии. Высушенный продукт направляется на стадию рассева.
Количество высушиваемого материала определяется в зависимости от степени влажности исходных компонентов, потребности в керамической смеси.
Начальная влажность исходных компонентов, особенно кварцевого песка или динасового мертеля, доставляемых открытым способом, больше требуемой величины. Поэтому эти компоненты всегда требуют сушки. Молотый кремний, направляемый со стадии помола, а также диабаз, поступают на стадию сушки в закрытой таре и могут иметь влажность в пределах нормы. Поэтому данные компоненты подвергаются лабораторному анализу на влажность, после чего делается вывод о проведении сушки молотого кремния и диабаза [6].
2.4 Рассев исходных компонентов керамической смеси
Рассеву подвергаются следующие компоненты: кварцевый песок или динасовый мертель, диабаз, молотый кремний.
Рассев компонентов производится на вибросите, режим работы периодический. Каждый компонент подвергается рассеву в отдельности, смешение не недопускается. Рассев осуществляется на сетке из нержавеющей стали размером ячейки 1,5 мм. Класс -1,5 мм собирается в герметично закрытую тару и направляется на стадию дозировки и смешения компонентов, а класс +1,5 мм в приемную емкость и по мере накопления вывозится на свалку. Исключение из этого составляет кремний, класс +1,5 мм которого направляется на повторный помол.
Количество обрабатываемых материалов на стадии рассева определяется в каждом конкретном случае.
2.5 Дозировка и смешение компонентов смеси
Смешение всех компонентов, входящих в состав керамической смеси, производится в смесителе, периодического режима работы.
Выгрузка производится вручную, предварительно перед этим корыто смесителя наклоняется по отношению к горизонтальной плоскости на определенный угол.
Перед смешением в смеситель отвешивается на весах необходимое количество каждого компонента смеси.
2. 6 Затаривание готовой продукции
Полученная вышеуказанным способом смесь из смесителя засыпается в бумажные пятислойные битумированные мешки, которые прошиваются после затаривания. На каждый мешок наклеивается ярлык с указанием номера партии, даты изготовления, веса, наименования упакованных материалов. Бумажный мешок помещают в наружный полиэтиленовый, который заваривают или прошивают. В каждый мешок засылают 35 кг смеси [10].
Мешки со смесью формируются в партии, проводится лабораторный анализ готового продукта и со склада отправляется потребителю.
Выводы
Длительность и эффективность работы высокотемпературных промышленных агрегатов зависит от уровня их технической эксплуатации, своевременной диагностики возникающих дефектов и качественного проведения профилактических ремонтов. Своевременное выполнение необходимого объёма и применение наиболее рациональных профилактических ремонтов, таких как керамическая наплавка, позволяют значительно продлить срок службы промышленных печей [5].