Abstract
Content
- Introduction
- 1. Practical significance
- 2. Goal and tasks of the research
- 3. Review of the literature
- 3.1 Basic facts about concrete
- 3.2 Cellular concretes
- 3.3 The application of microsilica as the additive
- Conclusion
- References
Introduction
Concretes are the manufactured rock materials received as a result of curing of carefully mixed and packed admixture of a mineral or organic cementing agent with water, the small or large fillers taken in certain proportions [1].
In modern building the requirements shown to concrete as one of the basic building materials, have grown so that classical composition of concrete cannot ensure required properties. So for the directed regulation of these properties the modifying additives are entered into a concrete mix. They can change technological possibilities and raise building-technical characteristics of concrete, and also impart new properties to it.
As one of the components of complex additives microsilica can be used [1]. Due to unique properties and multifunctional action it can provide the compressive strength exceeding hardness of not modified concrete.
Microsilica is a waste product therefore production of the building materials incorporating microsilica is connected with waste recycling of a technogenic product. Studying of physical and chemical features of various technogenic products of the industry, their influence when using them as the additive on an operating ability, development of the compositions and research of influence of microsilica additives on the main properties of heat-insulating concrete, cement mortar is an actual and perspective problem. It is caused by the question of the recycling of technogenic products after their usage.
1. Practical significance
The practical significance of the work is acquisition of materials with the improved characteristics with use of technogenic wastes.
2. Goal and tasks of the research
The aim of the work is a research of microsilica influence on the main properties of heat-insulating concrete and studying of possibility of a temperature rise while using concrete.
The research task is development of the heat-insulating concrete compositions containing the additives of microsilica, and usage of the main characteristics of concrete of the offered composition (hardness, heat conductivity, application temperature).
3. Review of the literature
3.1 Basic facts about concrete
Concrete – is one of the most ancient building materials. The passageways of the Egyptian labyrinth are made from it (3600 years BC), a Great Wall part (III century BC), a number of constructions on the territory of India, Ancient Rome and in other places [1].
However the use of concrete and reinforced concrete for mass building has begun only in second half of XIX century after the production and organisation of industrial portlandcement, which became the basic cementing material for concrete and reinforced concrete constructions [2].
During the eighties of XX century prof. A.R. Shuljachenko developed the theory of reception and hardening of hydraulic cementing materials and cements and he proved that on their basis durable concrete designs can be received. Under its management the production of high-quality cements was organized. Prof. K.A. Beleljubsky in 1891conducted the wide research and the results promoted introduction of reinforced concrete constructions in building. Prof. I.H. Maljuga in 1895 in the work Compositions and ways of manufacturing of a cement slurry (concrete) for reception of the greatest strength
proved fundamental laws of hardness of concrete. In 1912 capital work by Zhitkevich Concrete and concrete works
were published.
At the beginning XX-th century there were a lot of works on technology of concrete abroad. The most important among them were works of R. Fere (France), O. Grafa (Germany), I. Bolome (Switzerland), D. Abrams (USA).
Soon the technology of concrete will have the further development. The main directions in this research are: increase of efficiency and quality of prefabricated reinforced concrete constructions and products, decrease of specific quantity of metal and labour input of their production; development and the organization of mass production of effective kinds of binding material, high-quality sealers, complex chemical additives; radical improvement in a reinforced-concrete production technique and concrete designs production by massive adoption of new more modern production processes, the high-production automated equipment, robots and manipulators, perfect control systems and quality management of end product on the basis of development of the method allows to forecast properties of the concrete, wide use of computing machinery; application of resource-saving and nonwaste technologies; wide use of secondary products and industry waste, use of all reserves of production for economy of material resources, power resources and a manpower [1].
3.2 Cellular concretes
Cellular concretes are the manufactured rock materials consisting of a hardened astringent (or mix of cementing and a filler) with evenly distributed in it air cells.
For the first time cellular concretes were received in the end of XIX century. Their industrial production began in the twenties of ХХ century. In 1924 in Sweden the way of acquisition of aerocrete on the basis of cement, lime and various additives with application as aluminium bronze gas-generating agent was offered. later in Denmark the foam concrete was invented. In the thirties the ways of cellular concretes acquisition on the basis of cement, lime and a milled quartz sand with the subsequent autoclaved processing of moulded products were offered.
In our country the output of wide range of products from cellular concretes is mastered. Many types of the cellular concretes are known, different in the various ways of reception of a cellular structure, cementing agent sorts, conditions of moulding, hardening etc.
3.3 The application of microsilica as the additive
Microsilica is used in the world building industry, namely for reception of new generation concrete with special properties:
– acquisition of superhigh-strength and high-strength concrete (compression strength 80-100 МПа, and also to 240 МПа at autoclaved processing);
– acquisition of high durability concrete (stability to sulphate and chloride aggressions, to impact of weak acids, ocean water, low and high temperatures); the microsilica additive raises water impermeability on 25-50 %, sulphate on 90-100 %; the 6 % microsilica additive provides acquisition of concrete of the mark on frost resistance F300 at W/C=0,45 [4];
– acquisition of concrete with high initial strength (so, at the cement and dust expense accordingly 594 and 100 kg/m3 receive concrete with strength: 1 days – 63 МПа, 28 days – 124 МПа, 1 year – 127 МПа;
– microsilica use allows to save to 50 % of cement in concrete without loss of their processing characteristics.
Microsilica (fig.1) consists of very small spherical parts of amorphous silica with average specific surface about 20 m2/g [6].
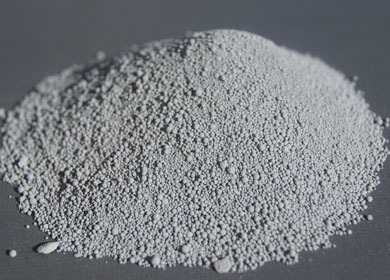
Figure 1 – By-product of pozzolanic
High properties of microsilica improve such characteristics of concrete as compression strength, adhesion strength, wear resistance, freeze resistance, chemical durability and considerably reduce permeability. It allows to stand up for a long time to external natural and industrial impacts (environments).
Besides, microsilica is actively used in production of dry building mixes, foam concretes, concrete, rubber, ceramics, facing tiles, refractory masses; for bridge building, a road making, at construction of dwelling and industrial objects, dikes and dams, drilling platforms and boreholes, collector lines and etc. [7].
Early studies of МS as additives for concrete and solutions were made in 1946. Then the first patent for modification of cement systems by introduction in their composition МS was received. From 1951 to 1952 professor Bernhardt has made experimental researches of application МS in concrete. To the beginning of 60s the technical application in manufacturing techniques of concrete and solutions began - as the modifying additive in water-proof and non-corrodible materials on a cement basis. In Canada microsilica use in concrete was approved in 1981. In the same year the first industrial mixes Portland cement/ microsilica were manufactured in Iceland. In Canada such mixes occurred in 1982. Nowadays microsilica in Europe is used everywhere - from concrete blocks to oil constructions [8].
Microsilica dioxide is usually added as an additional binding material in percentage terms from the initial maintenance of cement, depending on a type or demanded quality of concrete. The dosage can be the following:
– the concrete delivered by pump 2-3 %
– ginute of 8-12 %
– an underwater concrete of 12-15 %
At microsilica add-on in quantity to 30 % in a combination to superplasticizers it is possible to receive mixes with the relation water / cohesive material more low 0,3. Such concrete can reach very high initial strength. They have found wide application there where healing in a damp mode [6] is carried out.
Conclusion
It is known that influence of conditions and a heat treatment mode is the important factor at formation of structure of complete product, their physical-mechanical and operating ability. However more full physical - chemical researches of microsilica behavior at heating are made insufficiently.
Thus, this work is devoted to the research of possibility of heat-insulating concrete production with the improved properties with application of the additive of microsilica (ruggedness, use temperature).
This master's work is not completed yet. Final completion: December 2012. The full text of the work and materials on the topic can be obtained from the author or his head after this date.
References
- Основные сведения о бетоне [электронный ресурс] – Режим доступа: http://www.know-house.ru...
- Классификация бетона и применение в строительстве [электронный ресурс] – Режим доступа: http://betonstroy31.ru/beton...
- Ключевые пробемы пенобетона [электронный ресурс] – Режим доступа: http://bstroika.ru...
- Микрокремнезем [электронный ресурс] – Режим доступа: http://www.gcs-n.com...
- Микрокремнезем и его применение [электронный ресурс] – Режим доступа: http://www.technoros.ru...
- Микрокремнезем и его основные формы [электронный ресурс] – Режим доступа: http://vip-villas.ru...
- Развитие производства ячеистого бетона в Украине [электронный ресурс] – Режим доступа: http://eco-beton.com.ua...
- Бетоны нового поколения [электронный ресурс] – Режим доступа: http://izhbeton.ru...
- Проблемы развития производства пенобетона [электронный ресурс] – Режим доступа: http://www.fluke-net.com...
- Производство бетона. Добавки бетона [электронный ресурс] – Режим доступа: http://www.vival.ua...
- Микрокремнезем в пескобетоне (мелкозернистых бетонных смесях) для увеличения прочности бетона [электронный ресурс] – Режим доступа: http://www.voscem.ru...