Реферат за темою випускної роботи
Зміст
- Вступ
- 1. Літературний огляд
- 1.1 Види окислювачів для ПВР
- 1.2 Аміачна селітра і її властивості
- 1.2.1 Поліморфізм АС
- 1.2.2 Гігроскопічність
- 1.2.3 Злежування АС
- 2. Експериментальна частина
- 2.1 Електризація ПВР
- 2.2 Удосконалення ПВР на основі аміачної селітри
- Висновки
- Перелік посилань
Вступ
Промислові вибухові речовини знайшли широке застосування в різних галузях промисловості. За допомогою буропідривних робіт видобувається близько 70% корисних копалин, проводиться більше 90% виробок на гірничорудних підприємствах і майже 70% – на вугільних шахтах Донецького басейну. Зараз неможливий розвиток гірничої промисловості, будівництво великих споруд, гребель, доріг в горах, на болотах без використання вибухових речовин (ВР). За допомогою ВР ведеться сейсмічна розвідка корисних копалин, масовими вибухами розкривають на великій глибині в земних надрах поклади руд. Люди навчилися колосальними вибухами змінювати рельєфи гір і створювати перешкоди грязьовим зсувам, швидко ліквідувати наслідки гірських обвалів і землетрусів, гасити лісові пожежі, зварювати тонкі листи різнорідних металів, зміцнювати сталеві конструкції.
У зв'язку з цим вкрай актуальною є робота в напрямку підвищення безпеки, ефективності, економічності, збільшення коефіцієнта використання потенційної енергії вибухових речовин.
Промислові ВР (ПВР) – це вибухові речовини, які характеризуються зниженою чутливістю до зовнішнього впливу і відносно невисокою вартістю. Вони повинні безвідмовно детонувати від засобів ініціювання, не мати шкідливого впливу на організм людини під час виготовлення і роботи з ними.
Як відомо, вибухове перетворення всіх сучасних промислових ВР базується на окисленні горючих елементів киснем. Тому всі без винятку вибухові механічні суміші повинні складатися не менше ніж з двох (вибухових або невибухових) компонентів, а саме: пального та окислювача. Окислювачі – речовини, які містять надлишковий кисень і здатні легко його віддавати (аміачна, калієва, натрієва селітри). Склад і властивості окислювача будуть безперечно впливати на властивості вибухової речовини. Саме тому дослідження впливу складу окислювача на властивості ПВР є актуальною темою.
Метою роботи є дослідження впливу складу окислювача на властивості промислових вибухових речовин.
Для досягнення поставленої мети необхідно вирішити наступні завдання:
- Провести аналіз досліджень і публікацій для з'ясування основних видів окислювачів, які використовуються в ПВР.
- Розглянути вплив різних окислювачів на властивості вибухових речовин.
- Розглянути можливість створення нових більш екологічних і ефективних ПВР.
1. Літературний огляд
1.1 Види окислювачів для ПВР
У якості окислювача в складі промислових вибухових речовин може використовуватися аміачна селітра та інші рідкі та тверді речовини.
Вибухові суміші на основі аміачної селітри є найбільш поширеними промисловими ВР. Це пояснюється доступністю селітри, широкої виробничою базою її виготовлення, а також порівняною безпекою переробки сумішей на її основі. У вибухових сумішах аміачна селітра виконує роль окислювача, а пальним можуть бути різноманітні органічні сполуки, в тому числі вибухові з негативним кисневим балансом, такі як тротил, дінітронафталін та інші, а також металеві порошки алюмінію.
Окрім аміачної селітри до складу промислових ВР в якості окислювача можуть бути введені інші рідкі і тверді сполуки. Їх відносну ефективність можна оцінити за енергетичними характеристиками сумішей стехіометричного складу, що містять одне й те ж пальне. У таблиці 1 приведені результати розрахунку енергетичних характеристик сумішей з тротилом, за критерій ефективності прийнята величина ідеальної роботи вибуху, відносна ефективність виражена у відсотках до ідеальної роботи суміші тротилу з аміачною селітрою, прийнятою за 100.
Найбільш високі показники мають суміші на основі рідких окислювачів, які перевершують амоніти за працездатністю в 1,42-1 66 разів.
З приведених в табл. 1.1 окислювачів крім аміачної селітри в складі промислових ВР застосовують солі хлорної і хлорнуватої кислот (перхлоратні і хлоратні ВР), нітрати лужно-земельних і лужних металів. Останні вводяться до складу деяких водонаповнених ВР для підвищення щільності, а також в селективно-детонуючі запобіжні ВР.
Окислювач | Вміст тротилу, % | Теплота вибуху, кДж/кг | Об’єм газів вибуху, л/кг | Повна ідеальна робота вибуху, кДж/кг | Відносна ефективність до тротилу,% |
Чотирьохокис азоту (N2O4) | 48,4 | 7930 | 650 | 5950 | 166 |
Перекис водню (Н2O2) | 41,3 | 7080 | 835 | 5680 | 159 |
Азотна кислота моногидрат (НNO3) | 46,3 | 6360 | 695 | 5090 | 142 |
Перхлорат амонію (NH4ClO3) | 31,5 | 5710 | 745 | 4620 | 129 |
Перхлорат натрію (NaClO4) | 41,4 | 6170 | 450 | 4360 | 122 |
Аміачна селітра (NH4NO3) | 21,3 | 4310 | 892 | 3570 | 100 |
Натрієва селітра (NaNO3) | 38,8 | 4960 | 420 | 3420 | 95,5 |
Калієва селітра (KNO3) | 35,0 | 4370 | 380 | 2940 | 82 |
Перхлоратні ВР – суміші, в яких як окислювач використовуються солі хлорної кислоти – перхлорати калію, натрію або амонію. Вибухові суміші, що містять перхлоратні солі, відрізняються дуже високою чутливістю до тертя і удару, тому вони практично не застосовуються.
Перхлорати як окислювачі дають великий енергетичний виграш в порівнянні з аміачною селітрою. Так, стехиометрічні суміші селітри з тротилом мають теплоту вибуху 4190 кДж/кг, з парафіном – 3770 кДж/кг; ті ж пальні з перхлоратом амонію утворюють суміші з теплотою вибуху відповідно 5550 кДж/кг і 5230 кДж/кг.
Традиційні способи флегматизації нітросполук і їх сумішей введенням в них низькоплавких органічних речовин (парафіну, церезину, воску і т. п.) не тільки не знижують чутливість перхлоратних солей і їх композицій, але, навпаки, підвищують її. Найбільш сильним флегматізатором є желатинована вода, яка знижує чутливість до удару перхлоратних солей з 80-100 до 40-60 %.
Перхлорати калію і натрію утворюють менш чутливі суміші, ніж чим перхлорат амонію. При вибуху вони утворюють тонкодисперсні хлориди металів, що діють як інгібітори. Тому їх вводять в деякі запобіжні ВР.
Відомі патенти США, Великобританії, в яких пропонуються способи приготування різних складів на основі азотної кислоти. Подібні склади були відомі ще і на ранній стадії розвитку промислових ВР. Найбільша кількість тепла в системах кислота-тротил виділяється при вмісті тротилу 35-40%. Найбільш доступними і економічно вигідними є композиції на основі желатинованої поліакрілом кислоти з феросплавами, теплота вибуху яких 8370-9210 кДж/кг (12500-13820 кДж/л). Теплота вибуху сумішей азотна кислота-алюміній може досягати 11720 кДж/кг.
Висока летючість азотної кислоти, її агресивність і низька живучість гелю на її основі стримують практичне використання таких складів.
Рідкі вибухові суміші на основі чотириокису азоту, тетранітрометану і 98% азотної кислоти, використовуваних як окислювач, і керосину (пального), характеризуються високою детонаційною здатністю. Критичний діаметр детонації таких сумішей 1,2-2 мм. Суміші подібного роду використовувалися в технології вибухового буріння [1].
Через зручність, доступність, порівняну безпечність переробки найпоширенішим окислювачем у ПВР є аміачна селітра. Тому її властивості будуть розглянуті детальніше.
1.2 Аміачна селітра і її властивості
Аміачна селітра – технічна назва нітрату амонію NH4NO3, молекулярная масса которого 80,05. молекулярна маса якого 80,05. В чистому вигляді вона містить 35% азоту, 5% водню та 60% кисню, 20 % якого виділяються у вільному стані при повному її розкладенні. Температура плавлення: 169,6 °С – чистого безводного нітрату амонію, 160 °С та 140 °С технічної селітри з вмістом вологи відповідно 1,7 та 2,5% [2].
Аміачна селітра є білою кристалічною речовиною, що одержується взаємодією аміаку з азотною кислотою за рівняннямию
Випускається у вигляді гранул або кристалів. Гранули аміачної селітри, що утворюються при кристалізації її розплаву, є капілярно-пористим тілом. Максимально можлива щільність кристалів 1,725 г/см3. Практично вона нижча через наявність раковин та інших дефектів в кристалічній решітці [1].
Аміачна селітра раніше застосовувалася в чистому вигляді як малочутлива ВР при масових вибухах; теплота вибухового перетворення селітри 1600 кДж/кг, працездатність в свинцевій бомбі 165-230 см3. Теплота утворення – 355 кДж/ моль.
При вибуху селітра розкладається за рівнянням
При недостатньому ініціюванні, а також при тепловому вибуху вона може розкладатися і за іншими рівняннями з меншими тепловими ефектами і з виділенням токсичних оксидів азоту. Цим, зокрема, пояснюється виділення оксидів азоту при неповноцінних вибухах ВР на основі аміачної селітри.
Чутливість селітри до детонаційного імпульсу залежить від вологості, розміру гранул та щільності. Детонації сухої тонкоподрібненої АС при щільності 0,8 г/см3, за даними А.Ф. Бєляєва, стійко поширюється у відкритих зарядах діаметром близько 100 мм. Детонація з розміром часток 1 мм та вологістю 1% затухає у відкритому заряді діаметром 300 мм. АС з вологістю 3% не вибухає в зарядах ще більших діаметрів. Чутливість до вибуху підвищується в результаті локального розчинення та наступної перекристалізації селітри, що призводить до пористості.
За даними М. Кука, швидкість детонації подрібненої АС в залежності від діаметру заряду d приймає значення наведені в таблиці 1.2.
d, мм | 100 | 150 | 200 | 250 | 300 | 460 |
D, км/с | відмова | 1,4 | 1,6 | 1,8 | 1,15 | 2,75 |
На детонаційну здатність АС впливає міцна оболонка. У неруйнівній оболонці зареєстрована стійка детонація селітри в зарядах діаметром 5 мм.
Критичний діаметр водостійкої селітри в залежності від ступеню подрібнення та вмісту гідрофобних добавок складає 50-80 мм, а тонко дісперсного пилу – 20-30 мм.
Швидкість детонації селітри без добавок в металічній трубі діаметром 40 мм склала 1,95 км/с, водостійка селітра в цих умовах детонувала зі швидкістю 2,57 км/с, а її пил – з швидкістю 3,4 км/с. При введенні до селітри органічних добавок чутливість до детонації збільшується.
До механічних дій водостійка селітра, особливо її пил більш чутлива, ніж звичайна селітра, але менш чутлива порівняно з тротилом та амонітом 6ЖВ.
Через малу чутливість та низьку енергію вибуху аміачна селітра має знижену здатність до передачі детонації на відстань.
1.2.1 Поліморфізм АС
Залежно від температури аміачна селітра може існувати в декількох модифікаціях (табл. 1.3) [2]. Було виявлено ще чотири модифікації нітрату амонію. Модифікації VI, VIII і IX існують при високому тиску (86-270 МПа), модифікація VII – при температурі 170 °С. Детально модифікаційні переходи досліджені А.Е. Никіфоровим.
Переходи зворотні і протікають з не дуже великим рихленням структури в полікристалічних зразках. Виключення складає III модифікація. Прямий перехід в II і IV модифікації ускладнений через порівняно великий термодинамічний бар’єр, особливо в сухій речовині. Зволоження полегшує перехід через рекристалізацію. За певних умов можливий прямий перехід з модифікації II в IV. При циклічних нагріваннях розпушування заряду збільшується. Перехід з модифікації IV в III супроводжується збільшенням об'єму, за уточненими даними А.Е. Никіфорова, на 0,0240 см/г3 (4,14%), з V модифікації в IV відповідно 0,016-0,018 см/г3, або до 3%.
При температурних змінах через поліморфні переходи в масі селітри (сумішевих ВР) виникає напруга, яка може привести або до зчеплення порошкоподібних частинок (злежування, спікання), або до розпушування і зростання сформованих зарядів. Оскільки низька вологість (нижче 0,1%) гальмує найбільш небезпечний перехід з модифікації IV в III, то одним із способів фізичної стабілізації є підсушування (у виробничих умовах), або введення водовбирних добавок. Можливі метастабільні переходи з модифікації II в IV або навіть з II в V за рахунок введення цих добавок, а також стабілізація однієї модифікації в широкому діапазоні температур (±60°), наприклад, введенням азотнокислого калію (KNO3 ).
Таблица 1.3 – Характеристика кристалічних модифікацій нітрату амонію
Модифікація | Структура кристалів | Температурні межі, °С | Теплота переходу, ккал/кг | Зміна об’єму, % | Щільність, г/см3 |
I | Кубічна | 169,6-125,8 | 16,75 | -2,13 | 1,55 |
ІІ | Тетрагональна | 125,8-84,2 | 12,24 | -1,33 | 1,6 |
III | Ромбічна | 169,6-125,8 | 16,75 | -2,13 | 1,55 |
ІV | Ромбічно-біпірамідальна | 32,3-(-18) | 4,99 | -3,3 | 1,7 |
V | Гексагональна | ниже -18 | 1,6 | +1,65 | 1,72 |
В роботі [6] досліджувалися модифікаційні переходи аміачної селітри марок А, ЖВ та селітри стабілізованої оксидами міді, нікелю та цинку за допомогою методів диференціальної скануючої калориметрії, диференціального термічного аналізу.
На рис. 1.1 показані криві ДСК/ДТА порошків НА марок А, ЖВ і фазостабілізованого НА в широкій області температур до розкладання зразків НА. Ендотермічні ефекти на кривих ДТА відповідають фазовим, поліморфним переходам і розкладанню НА.
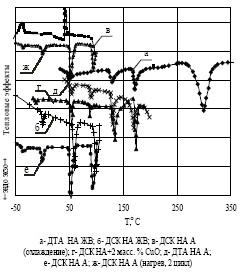
Отримані результати в цілому відповідають даним для чистого НА, за винятком яскравого вираженого зсуву області поліморфного переходу фази IV-III в область Т=50-52 °С. ДСК НА марки ЖВ показують відсутність поліморфних переходів у області температури менше +50 °С, а також поліморфного переходу при Т=84 °С (II-III), який однозначно виявляється в зразках НА марки А.
1.2.2 Гігроскопічність
Аміачна селітра відрізняється високою гігроскопічністю, що є однією з причин її злежування.
Відносна вологість повітря при якій речовина не зволожується і не підсихає, називається гігроскопічною точкою. Гігроскопічна точка є функцією температури, що виходить з визначального рівняння:
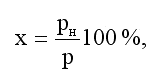
де рн – парціальний тиск водяної пари над насиченим розчином речовини;; р – парціальний тиск насиченої водяної пари при даній температурі; х – відносна вологість повітря, %.
Гігроскопічні точки Г аміачної селітри при різних температурах мають (у % відносної вологості) наступні значення (табл. 1.4):
t, °C | 10 | 15 | 20 | 25 | 30 | 40 | 50 |
Г, % | 75,3 | 69,8 | 66,9 | 62,7 | 59,4 | 52,5 | 48,4 |
Додавання в плав аміачної селітри розчинних неорганічних солей, як правило, знижує гігроскопічну точку порівняно з чистою сіллю. Так, додавання 1,2% нітрату магнію знижує гігроскопічну точку при 25 °С до 57,3% [3].
1.2.3 Злежування АС
Злежування – це здатність деяких порошкоподібних речовин втрачати при зберіганні сипкість та перетворюватися у щільну масу. Іноді це явище називають також спіканням
. Але під спіканням більшою частиною розуміють втрату сипкості, викликану нагрівом.
Однією з причин злежуваності є рекристалізація водорозчинних компонентів. При зволоженні ВР деяка частина солей (нітрати амонію, хлористого натрію або ін.) переходить в розчин. Потім при підсиханні або пониженні температури з насиченого розчину виділяються нові кристали, які цементують масу в міцний конгломерат. Цьому процесу сприяють капілярні сили, які зближують зволожені частинки. Тому злежуванні, крім втрати сипучості, часто порошок самоущільнюється, тобто відбувається об'ємна усадка. Описаний процес має місце при помірному зволоженні гідрофільних матеріалів. При великому вмісті вологи зменшення розчинності при пониженні температури може виявитися недостатнім для цементації маси утворенням нових кристалів з розчину.
Злежування за описаним механізмом посилюється при зовнішньому тиску, наприклад, при штабелюванні матеріалу, упакованого в м'яку тару (паперові, пластикові мішки), або при внутрішній напрузі, викликаній в результаті поліморфних перетворень аміачної селітри із збільшенням об'єму ВР. В цьому відношенні особливо небезпечний нагрів аміачної селітри вище за температуру +32 °С, при якій вона з βформи переходить в γ-форму із збільшенням об'єму на 2,5%. Деякі дослідники виявляли злежування в результаті поліморфних перетворень при температурі +32 °С тільки вологої селітри; за відсутності вологи злежування при нагріві не відбувалося. Також злежування збільшується при збільшенні подрібненості гранул аміачної селітри.
Найбільшу злежуваність мають речовини з середніми значеннями гігроскопічної точки 50-70 %, здатні періодично зволожуватися і підсихати із зміною вологості повітря. Саме такими є основний компонент промислових ВР - аміачна селітра.
На злежуваність можуть впливати розміри і форма часток ВР. Зі збільшенням розмірів зменшується питома поверхня порошку, а отже, і число можливих вузлів зчеплення. З тієї ж причини порошок, що складається з часток сферичної форми, менше злежується, ніж порошки, що містять частки з пласкими поверхнями. Гладка поверхня утворює менше можливостей для злежування, ніж шорстка [1].
Детально механізм злежування гранульованої аміачної селітри розглянуто в роботі [4]. Якщо привести в зіткнення один з одним декілька гранул, як це має місце в шарі речовини, то між ними виникає деяка кількість одиничних зв’язків, яка дорівнює числу точок зіткнення гранул. Чим вище міцність одиничних зв’язків, тим більше механічна міцність шару, а отже, тим значніше злежуваність.
Проте, як показує досвід, якщо насипати тонким шаром сухі гранули, то міцність виникаючих при цьому одиничних зв’язків така мала, що не виникає помітної міцності шару, і він розсипається при видаленні обмежуючих стінок.
Створення значної механічної міцності шару гранульованої аміачної селітри при постійному числі одиничних зв'язків вимагає значного збільшення міцності останніх. Це може мати місце при збільшенні поверхні контакту між окремими гранулами, що можна досягти:
- шляхом пластичної деформації гранул під впливом зовнішнього навантаження (рис. 1.2в) (рис. 1.2в);
- шляхом створення кристалічних перемичок між гранулами за рахунок утворення кристалів з маткового розчину, якщо останній яким-небудь чином потрапив в міжгранульний простір (рис. 1.2с);
- шляхом одночасної дії пластичної деформації гранул і утворення кристалічних перемичок між гранулами (рис. 1.2d).
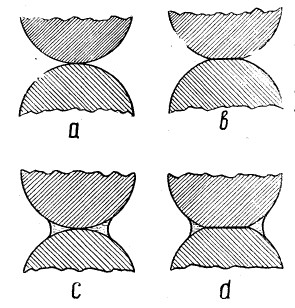
Обволікаючі, нерозчинні у воді масла, парафін, керосин і інші домішки знижують злежування гігроскопічної речовини, покриваючи її частинки негігроскопічною плівкою. Внаслідок цього знижується швидкість поглинання вологи. Окрім цього, плівка гідрофобної речовини ізолює частинки речовини одну від одної і нові кристали, що утворюються, менш міцно зв'язують масу речовини.
У теорії кристалізації відомий принцип зміни активними домішками розмірів і форми кристалів, наприклад, добавками поверхнево-активних речовин (0,01-0,1%), зокрема фарбників. Відповідно ці добавки можуть впливати і на процес злежування. Загальним для структурної характеристики фарбників, ефективно змінюючих розміри кристалів, є присутність в них сульфогрупп і катіонної групи виду NH2 або OH. Найефективніше знижують злежування аміачної селітри фуксин кислотний з класу тріфенілметанових фарбників і кислотний червоний амарант з класу азобарвників.
Практикують також такі способи зниження злежуваності, як зміщення поліморфних перетворень АС в область вищих температур. Це досягається веденням до кристалів селітри хлористого калію чи калієвої селітри [5].
2. Експериментальна частина
2.1 Електризація ПВР
У виробничих умовах накопичення зарядів статичної електрики може досягати таких меж, при яких розряд їх здатний запалити або викликати вибух чутливих до іскрових розрядів речовин. Крім того, при електризації можуть створюватися технологічні перешкоди, такі, як налипання продуктів на стінки апаратів і трубопроводів, грудкування порошків, утруднення при просіюванні і ін. Тому явище електризації необхідно враховувати при виготовленні і застосуванні ВР і забезпечувати, де це необхідно, відповідні заходи захисту.
Для оцінки вірогідності і небезпеки електризації при застосуванні промислових ВР враховують не тільки електричні характеристики ВР, але і умови їх застосування, які можуть істотно впливати на утворення і накопичення зарядів статичної електрики при роботі з ВР [7].
2.2 Удосконалення ПВР на основі аміачної селітри
Одним з найбільш поширених вибухових речовин на основі АС є грамоніт 79/21. Граммоніт 79/21[1] речовина другого класу, призначений для вибухових робіт в кар'єрах, рудниках і шахтах, не небезпечних по газу і пилу при ручному і механізованому заряджанні сухих і мокрих (зневоднених) шпурів, свердловин і камер. Для ініціювання електродетонатором і детонуючим шнуром вимагає проміжного детонатора, в якості якого на відкритих роботах достатньо однієї шашки типу Т-400г, а на підземних роботах одного стандартного патрона амоніту будь-якої марки. Випускається в непатронірованном вигляді і може використовуватися у всіх кліматичних регіонах країн СНД.
В ході багаторічної практики використання грамонітів виявлені такі недоліки: злежуваність, запилювання і електрізованість.
Злежуваність грамоніту 79/21 з'являється через гігроскопічності аміачної селітри та її здатність до поліморфних перетворень. Злежуваність призводить до зависання речовини в бункерах, зводоутворенню, при пневмнозаряджанні свердловин ускладнюється транспортування вибухівки трубопроводами та шлангами до місць заряджання.
Запилювання граммоніту з’являється при пневмотранспортуванні та пневмозаряджанні свердловин. При механізованому заряджанні необхідно вживати заходи, що попереджають розсипання, а також виділення пилу або часток ВР в навколишній простір. При цьому у всіх випадках вмісту компонентів ВР в повітрі робочої зони, незалежно від часу контакту з ними людей, не повинно перевищувати граничнодопустимих концентрацій (0,5 мг/м3).
Граммоніт 79/21 запаковується у мішки, які складаються з двох шарів: внутрішній – поліетиленовий, та зовнішній – поліпропіленовий. Через це підвищилась електризуємість граммоніту. У виробничих умовах накопичення зарядів статичної електрики може досягати таких меж, при яких їх розряд здатний запалити або викликати вибух чутливих до іскрових розрядів речовин. Крім того, при електризації можуть утворюватися технологічні перешкоди, такі як, налипання продуктів на стінки апаратів і трубопроводів, труднощі при просіюванні та ін Тому явище електризації необхідно враховувати при виготовленні та застосуванні вибухових речовин.
З метою усунення злежуваності і пилення до складу вибухових речовин додають обволікаючі добавки, наприклад, індустріальне масло (ІМ), але це призводить до збільшення електрізуемості. Для зменшення розглянутих вище недоліків було прийнято рішення про введення до складу грамонітів 79/21 огортає добавки у вигляді індустріального масла марки І-20 [8] та опудрюючої добавки у вигляді графіту марки С-1. Складалися суміші аміачної селітри з графітом, а також селітри з 0,5% мастила і графітом. Зміст графіту варіювалося від 0,24% до 1,02%.
Перевірка електрізуемості АС та сумішей на її основі проводилася наступним чином. Аміачна селітра містилася в ємність рівним шаром, товщина якого склала 15 мм. Електрізуемость перевірялася мегомметром, з електродом поверхню контакту якого становить 3,5 х3. Опір АС склало 300 кОм. Далі складалися суміші АС з графітом С-1 та індустріальним маслом. Отримані експериментальні дані наведені в таблиці 2.1
Таблица 2.1 – Електричні характеристики АС і сумішей на її основі
Склад суміші | Склад, % | Склад, г | Електризуємість, кОм |
АС | 100 | 50 | 300 |
АС+графіт | 100+0,24 | 50+0,12 | 150 |
АС+графіт | 100+0,48 | 50+0,24 | 120 |
АС+графіт | 100+0,72 | 50+0,36 | 100 |
АС+графіт | 100+0,96 | 50+0,48 | 85 |
АС+графіт | 100+1,02 | 50+0,6 | 70 |
АС+ІМ | 100+0,5 | 50+0,25 | 500 |
АС+ІМ+графіт | 100+0,5+0,24 | 50+0,25+0,12 | 300 |
АС+ІМ+графіт | 100+0,5+0,48 | 50+0,25+0,24 | 250 |
АС+ІМ+графіт | 100+0,5+0,75 | 50+0,25+0,36 | 200 |
АС+ІМ+графіт | 100+0,5+0,96 | 50+0,25+0,48 | 180 |
На рисунку 2.1 зображена графічна залежність електрізуемості від вмісту графіту в суміші. За отриманими експериментальними даними бачимо, що електрізуемость чистої АС становить 300 кОм. При додаванні індустріального масла електрізуємість різко збільшується до 500 кОм. При додаванні 0,24% графіту електрізуємість АС різко зменшується з 300 до 150 кОм. При подальшому збільшенні вмісту графіту до 1% електрізуємість поступово зменшується до 70 кОм. Склад, що містить графіт і індустріальне масло, має більшу електрізуємість ніж суміш АС і графіту. електрізуємість суміші АС + графіт + ІМ також зменшується при збільшенні вмісту графіту.
Отримані суміші зберігають сипкість протягом 6 місяців, до кінця цього періоду утворюють невеликі грудки, легко руйнуються при натисканні пальцями.
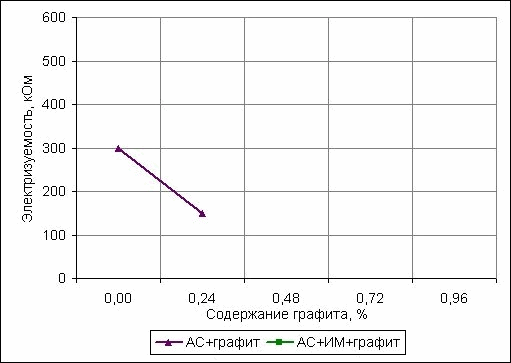
Оптимальним рекомендованим вмістом добавок можна вважати 0,5% ІМ і 0,8% графіту.
З точки зору нешкідливості продуктів вибуху при складанні вибухових сумішей необхідно прагнути до сумішей з нульовим кисневим балансом або з невеликим відхиленням, тому були проведені розрахунки [9] кисневого балансу і теплоти вибуху нового складу. Кисневий баланс вихідного грамонітів 79/21 становить +0,02, кисневий баланс вдосконаленою суміші за розрахунками становить -3,6. Теплота вибуху грамонітів до введення добавок становить 4280 кДж/кг, при введенні 0,5% ІМ і 0,8% графіту цей показник збільшився до 4710 кДж/кг.
Висновки
На даному етапі виконання роботи було розглянуто вплив різних окислювачів на властивості ВР. Найбільш високі показники мають суміші на основі рідких окислювачів, які перевершують амоніти по працездатності в 1,42-1,66 разів. Стехіометричні суміші селітри з тротилом мають теплоту вибуху 4190 кДж/кг, з парафіном – 3770 кДж/кг; ті ж горючі з перхлоратом амонію утворюють суміші з теплотою вибуху відповідно 5550 кДж/кг і 5230 кДж/кг. Але через незручність використання і велику чутливість такі ВР не знайшли широкого застосування.
В роботі розглянуті властивості найпоширенішого окислювача в складі промислових вибухових речовин – аміачної селітри. Її поширеність пояснюється доступністю селітри, широкої виробничою базою її виготовлення, а також порівняною безпекою переробки сумішей на її основі.
ПВР на основі аміачної селітри володіють наступними недоліками: злежуваність, запилення, електрізуємість. В ході роботи вдосконалили вибуховий склад грамоніт 79/21, шляхом введення добавок у вигляді індустріального масла И-20 і графіту С-1. Вдосконалений склад має меншу електрізуемость і злежуваність. Оптимальний вміст добавок складає: 0,5% індустріального масла і 0,8% графіту. Були проведені розрахунки енергетичних характеристик нового складу. Його кисневий баланс зменшився і становить -3,6, теплота вибуху збільшилася з 4280 до 4710 кДж/кг.
При написанні даного реферату магістерська робота ще не завершена. Остаточне завершення: грудень 2012 року. Повний текст роботи та матеріали по темі можуть бути отримані у автора або його керівника після зазначеної дати.
Перелік посилань
- Дубнов Л.В. Промышленные взрывчатые вещества/Дубнов Л.В., Бахаревич Н.С., Романов А.И. – М.: Недра, 1988. – 358 с: ил.
- Технология аммиачной селитры/ Под ред. В.М. Олевского – М.: Химия, 1978. – 312 с: ил.
- Пестов Н.Е. Физико-химические свойства зернистых и порошкообразных химических продуктов. – М.-Л. Изд. АН СССР, 1957. – 234 с.
- Куприн Н.П. Теория процесса слеживания гранулированной аммиачной селитры и возможные пути борьбы со слёживаемостью.– Томск: Известия Томского политехнического института им. Кирова. Том 71, 1952.– с. 25-51
- Терещенко А.В., Терещенко О.Г. Антислеживающие гигроскопичные добавки к солям и удобрениям. [Рукопись]. – Томск, 1985. – 22 с.
- Попок В.Н. К решению задачи фазовой стабилизации нитрата аммония. [Электронный ресурс]. – Режим доступа:Электронный научный журнал
Исследовано в России
- Светлов Б.Я. Теория и свойства промышленных взрывчатых веществ/Светлов Б.Я., Яременко Н.Е. – М.: Недра, 1973. – 208 с: ил.
- Топлива, смазочные материалы, технические жидкости. Ассортимент и применение. Справочник/ под ред. В.М. Школьникова. – М.: Издательский центр «Техинформ», 1999. – 598 с: ил.
- Бандурин М.К. Сборник задач по теории взрывчатых веществ/ Бандурин М.К., Рукин Л.Г. – М.: Оборонгиз, 1959 г. – 188 с.