Реферат по теме выпускной работы
Содержание
- Введение
- 1. Актуальность темы
- 2. Цель и задачи исследования
- 3. Технология получения пьезокерамических элементов
- 4. Влияние некоторых технологических факторов на свойства пьезокерамики
- 4.1 Зависимость свойств пьезокерамики от вида оформления полуфабриката
- 4.2 Влияние состава свинецсодержащих засыпок и способа упаковки изделий при их использовании на свойства пьезокерамических элементов.
- 4.3 роль атмосферы спекания на формирование служебных характеристик пьезокерамических элементов при различных методах подготовки образцов.
- Выводы
- Список источников
Введение
В настоящее время сложно перечислить области науки и техники, где бы не использовались устройства на основе пьезокерамики. Широкое распространение получили высокоэффективные пьезокерамические материалы на основе твердых растворов цирконата и титаната свинца с разными модифицирующими добавками (система ЦТС).
Расширение областей применения и усиления эксплуатационных режимов пьезокерамических материалов требует знаний о ее стойкости к действию разных внешних факторов: температурных, влажностных, механических, электрических, радиационных и т.д.
Пьезокерамика не принадлежит к
классическим видам керамики, поскольку в ее состав не входит глинистое
вещество. Пьезокерамические материалы синтезируются из оксидов
металлов. Однако применение характерного для керамической технологии
приема – обжиг при высокой температуре –
оправдывает отнесение пьезокерамических материалов к семейству
керамики. Пьезо (от греческого пиезо
– давить) указывает на то, что этому виду керамики
принадлежит особенное свойство – пьезоэлектрический эффект.
Керамика на основе цирконата-титаната свинца (ЦТС) в последнее время привлекает все большее внимание как сегнетоэлектрик, который позволяет изготовлять разнообразные оригинальные приборы.
Несмотря на значительные достижения по повышению качества материалов на основе ЦТС, прогресс в совершенствовании указанных материалов в последние годы резко снизился. Это объясняется тем, что возможности улучшения электрофизических свойств пьезокерамики путем изменения химического состава, модификации практически исчерпаны. На первый план выступает задача поиска новых приемов совершенствования структуры уже существующих материалов, которая может решаться за счет интенсификации операций на отдельных стадиях технологического процесса, повышение активности реагирующих компонентов с целью повышения скорости гетерогенных процессов. Поэтому абсолютно очевидной является важность развития и усовершенствования методов получения пьезоматериалов, что максимально удовлетворяют требованиям производства и новых областей применения соединений системы ЦТС.
1. Актуальность темы
Пьезокерамические изделия находят широкое применение в разных областях народного хозяйства: в радиоэлектронной технике, акустике, ультразвуковых преобразователях, медицине и др. Однако, по мере расширения профиля использования возросли и ужесточились требования к ней, что предопределило наряду с поиском новых составов усовершенствование технологии производства.
Существует множество факторов, участвующих в формировании структурно-чувствительных свойств (рис. 1). Выяснение их роли и интенсификация технологии с целью улучшения параметров пьезокерамики является важной и актуальной проблемой.

Рисунок 1 – Факторы, влияющие на свойства пьезокерамических изделий. Курсивом выделены факторы, изучавшиеся в работе.
2. Цель и задачи исследования.
Цель работы – исследование влияния некоторых технологических факторов на электрофизические свойства пьезокерамики ЦТС для оптимизации технологии производства изделий.
При этом решались следующие задачи:
- Изучить влияние состава свинецсодержащих засыпок и способа упаковки изделий при их использовании на свойства пьезокерамических элементов.
- Исследовать зависимость свойств от вида прессования, температуры спекания и микроструктуры керамики.
- Установить взаимосвязь между видом модификаторов в составе и условиями спекания.
- Выяснить роль атмосферы спекания на формирование служебных характеристик пьезокерамических элементов при различных методах подготовки образцов.
- Определить пути оптимизации технологии производства пьезокерамических элементов.
3. Производство пьезокерамических изделий
К керамическим сегнетоэлектрикам относятся титанат бария и ряд твердых растворов на его основе, твердые растворы метаниобата свинца и бария, твердые растворы титаната и цирконата свинца, титанат свинца и др.
Особенностью этих материалов является то, что после воздействия на них постоянного электрического поля они становятся пьезоэлектриками (пьезокерамикой) и могут быть использованы в качестве электромеханических преобразователей.
Детали из сегнетокерамики представляют собой изделия различных геометрических форм: цилиндры, диски, призмы, полые сферы и др. Для изготовления сегнетоэлектрической керамики обычно применяют углекислые соли и окислы соответствующих металлов [1].
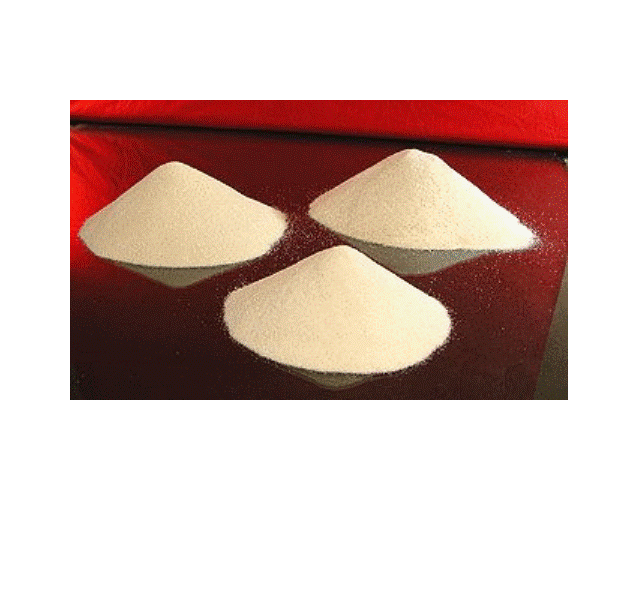
Рисунок 2 – Технология изготовления пьезокерамических изделий.
Исходные материалы, взятые в необходимом количестве, смешивают и подвергают синтезу при определенных температурах. Полученный после синтеза материал измельчают, пластифицируют и оформляют в деталь требуемой формы. Оформленные детали подвергают повторному нагреву, в процессе которого происходит спекание минеральных частиц и образование поликристаллической структуры [2].
После механической обработки до требуемых размеров на детали из сегнетокерамики наносят электроды методом вжигания, а затем поляризуют их постоянным высоким напряжением.
Технология производства предусматривает перемешивание и тонкий помол всех составов в вибромельнице. Простота конструкции вибромельниц, невысокая стоимость и компактность позволяют включать их в действующие технологические линии без ввода дополнительных площадей.
Тонкий помол в вибромельнице является наиболее общим способом увеличения поверхности взаимодействия твердого тела с окружающей средой. Кроме того, тонкое измельчение резко увеличивает число свободных твердых частиц. Эти обстоятельства приводят к повышению активности твердых тел в качестве структурообразующих материалов и значительно ускоряют растворение, спекание, фазовые и химические превращения.
При отсутствии вибромельницы и, особенно, в лабораторных условиях допускается применение шаровых мельниц для смешения и помола мокрым способом.
Перед оформлением керамической массы в деталь в нее вводят пластификаторы. В качестве последних можно применять водный раствор поливинилового спирта, парафин, декстрин и др [2].
Применение того или иного пластификатора определяется геометрической формой, размером детали и методом оформления. Так, при оформлении деталей простых геометрических форм (дисков, цилиндров, призм и т. д.) в качестве пластификатора целесообразно применять 3-6%-ный водный раствор поливинилового спирта.При изготовлении деталей сложной геометрической формы (полых сфер, конусов и т. д., подвергающихся механической обработке в необожженном состоянии, в качестве пластификатора применяют парафин. Этот же пластификатор в смеси с олеиновой кислотой или воском применяют при горячем литье под давлением.
Процесс оформления деталей может быть осуществлен разными методами: полусухим прессованием, горячим литьем под давлением и протягиванием через мундштук [3].
Каждый из перечисленных выше методов оформления деталей имеет свои преимущества и недостатки. Наиболее производительным и легко осуществимым в производстве является полусухое прессование, но применимо оно только для получения деталей простых геометрических форм.
Горячее литье под давлением позволяет оформлять детали любой геометрической формы, однако вызванная при этом необходимость введения в процесс дополнительной операции – выжигания пластификатора, увеличивает производственный цикл на 70-80 ч и требует установки дополнительных печных агрегатов, что ограничивает возможность применения данного метода в производстве.
Метод протягивания через мундштук целесообразно применять только для оформления цилиндрических деталей небольших диаметров (3-5 мм). Окончательный обжиг деталей является важнейшей технологической операцией, в процессе которой происходит образование монолитного тела, называемого керамическим черепком [2].
Условием получения высококачественных деталей является правильная их укладка, равномерный нагрев с определенной скоростью до установленной температуры и выдержка при этой температуре.
Температура обжига зависит от вида и количества примесей, имеющихся в исходных материалах. Время нагревания и время выдержки при максимальной температуре определяется не только составом и технологией приготовления прессовочных порошков, но и размерами деталей, a также величиной садки.
Скорость нагрева целесообразно применять не выше 150 °С в час, а скорость охлаждения – в пределах 150-200 °С в час или охлаждать с печью (в случае обжига в камерных печах). Исключением являются крупногабаритные детали с толщиной стенки более 15 мм, скорость нагревания которых, так же как скорость охлаждения, не должна превышать 50-60 °С в час.
Перечисленные выше методы
оформления не могут обеспечить получение деталей из сегнетокерамики
требуемой геометрической формы и заданных размеров. Эта задача решается
при помощи механической обработки деталей (заготовок)
в сыром
(необожженном) и
обожженном состояниях. В необожженном состоянии обычно механически
обрабатываются отпрессованные заготовки с целью придания им требуемой
геометрической формы, получение которой другим методом не
представляется возможным.
Механическую обработку обожженных керамических деталей или заготовок можно производить точением или шлифованием на металлообрабатывающих станках.
Очень большое значение имеет механическая прочность сцепления серебряных электродов с поверхностью керамических деталей. Наиболее высокое значение этой прочности достигается при тщательном обезжиривании механически обработанных деталей, выполнении санитарно-технических требований в процессе нанесения серебряной пасты и соблюдении температурного режима вжигания серебра в керамику [3].
Завершающей операцией технологического процесса является поляризация деталей постоянным током высокого напряжения.Поляризацию можно проводить как при нормальной температуре, так и при температуре, близкой к температуре Кюри данного состава. Более рациональным является второй метод поляризации.
Существенными факторами в этом процессе являются подготовка деталей к поляризации (тщательная их очистка и обезжиривание), среда поляризации и нагрев деталей в случае поляризации в горячем состоянии [3].
4. Влияние некоторых технологических факторов на свойства пьезокерамики
4.1 Зависимость свойств пьезокерамики от вида оформления полуфабриката
Первостепенное значение в формировании структуры и свойств пьезокерамических элементов имеет метод оформления полуфабриката.
Существенное преимущество холодного полусухого прессования в пресс-формах по простоте технологического процесса, высокой производительности и возможности механизации ослабляется неоднородностью прессовок по плотности, невозможностью изготовления деталей сложной формы.
Изостатическое (гидростатическое) прессование позволяет преодолеть недостатки одноосного прессования, однако, в свою очередь, неточность размеров получаемых изделий, шероховатость поверхностей требует дополнительно трудоёмкой механической обработки.
Достоинства горячего прессования – совмещение процессов прессования и спекания, получение плотности образцов, близкой к теоретической, обеспечивающей повышение уровня свойств на 10-20%. Однако горячее прессование имеет ряд недостатков: низкая производительность, цикличность, увеличение износа матриц.
Горячее литье под давлением позволяет получать изделия очень сложной формы с большой точностью геометрических размеров, но по сравнению с другими методами отличается низкой производительностью [2].
Для выяснения роли методов оформления полуфабриката использовали одноосное прессование в пресс-формах и всестороннее гидростатическое прессование (табл. 1). Анализ полученных результатов, как и ожидалось, показывает о преимуществе всестороннего гидростатического прессования над холодным прессованием.
Таблица 1 – Сравнительные результаты средних значений электрофизических свойств в зависимости от способа прессования и температуры спекания керамики ЦТССт-3
Тсп°С | Давление | Партия | ρ, г/см3 | ε33/ε0 | tgδ,% | Kp | d31, 10-12Кл/Н | Qм |
1260 | одноосное | П-2 | 7,62 | 1330 | 0,56 | 0,595 | 131 | 700 |
1260 | ВГП | П-2/5 | 7,68 | 1120 | 0,54 | 0,599 | 122 | 780 |
1240 | одноосное | П-2 | 7,66 | 1320 | 0,57 | 0,578 | 125 | 970 |
1240 | ВГП | П-2/5 | 7,7 | 1190 | 0,48 | 0,592 | 125 | 1090 |
1220 | одноосное | П-2 | 7,90 | 1230 | 0,49 | 0,599 | 124 | 720 |
1220 | ВГП | П-2/5 | 7,68 | 1110 | 0,50 | 0,589 | 118 | 790 |
1220 | одноосное | П-2 | 7,91 | 1260 | 0,51 | 0,593 | 126 | 790 |
1200 | ВГП | П-2/5 | 7,75 | 1030 | 0,51 | 0,578 | 109 | 910 |
4.2 Влияние состава свинецсодержащих засыпок и способа упаковки изделий при их использовании на свойства пьезокерамических элементов.
Получение пьезокерамики, содержащей свинец, связано с большими трудностями, обусловленными термической диссоциацией этих соединений и. как следствие, потерями оксида свинца в процессе термической обработки. Оксид свинца начинает заметно возгоняться с температуры ~ 750°С.
Улетучивание оксида свинца приводит к нарушению стехиометрии и получению материала с неопределенными составом и свойствами [4].
Получить изделия заданного состава, казалось бы, можно, введя в состав исходной шихты избыток оксида свинца, равный потерям при термической обработке керамики. Однако этот путь не может дать желаемых результатов, поскольку испарение оксида свинца зависит не только от объема печи, но и от газообмена с окружающей средой, конфигурации изделий (поверхности испарения) и некоторых других факторов. Нельзя забывать также о сильном коррозионном действии паров оксида свинца на футеровку печи и силитовые нагреватели, а также о большой токсичности этих паров. Задача сохранения оксида свинца при получении свинецсодержащей пьезокерамики с заданными составом и свойствами привлекла внимание многих исследователей [1].
Уменьшения потерь оксида свинца в процессе спекания керамики можно достичь, если производить термическую обработку изделий в закрытом пространстве с дополнительным источником паров оксида свинца. В лабораторной практике, в опытных производствах и в промышленности нашел применение новый способ предупреждения потерь свинца при спекании пьезокерамических изделий, заключающийсяв использовании никелевых пакетов с засыпкой. Сущность данного способа состоит в следующем (рис. 2).

1- корпус пакета, 2 - крышка, 3 - экран. 4 - образцы. 5 - подсыпка. 6 - засыпка. 7 - уплотненный слой засыпки, 8 - алундовые пластины, 9- подставка
Рисунок 3 – Способ упаковки изделий в никелевый пакет и его размещение в печи [2].
В никелевый пакет, состоящий из корпуса и крышки, на дно укладывают алундовые пластины для предупреждения изменения поверхности дна при короблении корпуса. Пластины покрывают слоем засыпки, которую тщательно выравнивают и уплотняют. Устанавливают слой изделий, присыпая их засыпкой посредством просеивания ее через сито. Далее устанавливают последующие слои образцов или изделий, пересыпая их засыпкой для предупреждения припекания образцов между собой.
Спекание изделий в засыпке позволяет создавать более равномерные подачу и отбор тепла от обжигаемых изделий, а также необходимую газовую среду, которая оказывает значительное влияние на процесс формирования керамического черепка при спекании и может нарушить первоначальную структуру материала, из которого изготовлены спекаемые изделия [5 ].
Недостаток оксида свинца в засыпке, равно как и полное насыщение дают неудовлетворительные технологические результаты. В первом случае засыпка вступает в реакцию с материалом изделий, во втором– избыток оксида свинца способствует такому ее спеканию, при котором изделия не могут быть извлечены из нее. Нормальная засыпка легко отделяется от изделий.
Для предотвращения потерь PbO из изделий в работе подбирали и изучали применение 30 и 50% засыпки, представляющей собой смесь ZrO2 и PbO предварительно синтезированных при (1300±20) °С×0,5 ч.
Экспериментальные проверки показали предпочтительность засыпки с 30% PbO по сравнению с 50%-ными. Уровень свойств на пьезокерамических элементах наблюдается выше (табл. 2) и к тому же она сравнительно легко отделяется от спеченной керамики, что указывает на отсутствие взаимодействия между ними.
Таблица 2 – Влияние состава засыпок на свойства пьезокерамических элементов
Материал керамики | Тип засыпки | Т,°С×τ, час | ε33/ε0 | tgδ,% | d31, 10-12Кл/Н | Kp | Qм |
ЦТС-19 | 30%PbO + 70% ZrO2 | 1330×2 | 2120 | 2,92 | 173 | 0,590 | 78 |
ЦТСтБС-1 | 30%PbO + 70% ZrO2 | 1330×2 | 3950 | 3,50 | 310 | 0,628 | 43 |
ЦТС-19 | 50%PbO + 50% ZrO2 | 1330×2 | 1980 | 2,75 | 154 | 0,580 | 84 |
ЦТССтБС-1 | 50%PbO + 50% ZrO2 | 1330×2 | 3930 | 3,80 | 290 | 0,620 | 39 |
Существенное влияние оказывает
и способ упаковки изделий (табл.3).
Таблица 3 – Влияние количества засыпки на свойства пьезокерамических элементов
Материал керамики | Количество засыпки | Т,°С×τ, час | ε33/ε0 | tgδ,% | d31, 10-12Кл/Н | Kp | Qм |
ЦТССт-3 | образцы полностью в засыпке | 1240×2 | 1360 | 0,55 | 130 | 0,560 | 810 |
ЦТСтБС-4 | образцы полностью в засыпке | 1240×2 | 1050 | 0,65 | 110 | 0,540 | 920 |
ЦТСтБС-1 | образцы полностью в засыпке | 1330×2 | 4000 | 1,90 | 290 | 0,615 | 41 |
ЦТССт-3 | образцы присыпаны | 1240×2 | 1370 | 0,52 | 135 | 0,565 | 830 |
ЦТСтБС-4 | образцы присыпаны | 1240×2 | 1070 | 0,60 | 120 | 0,620 | 940 |
ЦТСтБС-1 | образцы присыпаны | 1330×2 | 4100 | 1,85 | 320 | 0,630 | 44 |
Полное засыпание пакета с изделиями по сравнению с их присыпкой приводит к ухудшению свойств пьезокерамических элементов, что связано с затруднением диффузии O2 из атмосферы.
4.3 роль атмосферы спекания на формирование служебных характеристик пьезокерамических элементов при различных методах подготовки образцов.
Для повышения свойств одноосноспрессованых образцов использовали технологию кислородного спекания.
Действенным способом активирования спекания оксидных керамических материалов и управления их свойствами является использование искусственных газовых сред с различным парциальным давлением кислорода. По литературным данным [6], величина Рo2 в газовой среде при спекании оказывает существенное влияние практически на все свойства пьезокерамики .
Спекаемость всех исследованных материалов значительно улучшается с повышением Рo2 в газовой среде. Если в кислородной среде плотность керамики достигает максимального значения при практически нулевой открытой пористости, то спекание в газовых средах с низким Рo2 приводит по сравнению с воздушной средой к снижению плотности керамики и возрастанию открытой пористости. Снижение Ро, при спекании вызывает увеличение кристаллитов. Спекание в кислороде приводит к повышению прочности всех исследованных марок пьезокерамики.
Использование метода гидростатического прессования и спекания в среде кислорода позволяет достичь почти теоретической плотности керамики, как и в случае использования горячего прессования. Что касается электрофизических свойств керамики, то в [7] отмечается незначительное увеличение коэффициента электромеханической связи.
Можно выделить следующие основные факторы, определяющие характер влияния Рo2 на свойства ЦТС.
Так как кислород способен в значительных количествах растворяться в твердой фазе ЦТС. заполняя структурные вакансии, а инертные газы, в частности азот воздуха, не обладают такой способностью, повышение величины Рo2, и особенно, спекание в чистом кислороде способствуют быстрому и эффективному залечиванию остаточной пористости. При спекании в кислороде возможно получить высокоплотную керамику ЦТС не уступающую по величине объемной плотности (до 99,5-99,9 теоретической) горячепрессованным керамическим изделиям.
Повышение Рo2 приводит к таким сдвигам концентрации собственных дефектов, которые вызывают смещение электрофизических параметров (до 5-7% для немодифицированного ЦТС) в сторону большей сегнетомягкости [8].
Изменения Рo2, вызывают изменения валентных состояний элементов переменной валентности, входящих в состав модифицирующих добавок. За счет этого фактора можно увеличить такие параметры, как пьезомодуль. до 15-25% по сравнению с обычным спеканием на воздухе.
Уменьшение концентрации кислородных вакансий снижает скорость массопереноса в ЦТС при температурах вторичного спекания. Это приводит к уменьшению скорости вторичной рекристаллизации и размера зерен в керамике. Наряду с повышением плотности этот фактор также способствует увеличению прочности пьезокерамических элементов.[2]
Выводы
На основании проведенных исследований можно сделать следующие выводы:
Доказана предпочтительность 30%-ных свинецсодержащих засыпок по сравнению с 50%-ными. Установлено, что присыпка образцов засыпкой обеспечивает более высокий уровень параметров по сравнению со свойствами образцов засыпанных полностью, что связано с затруднениями диффузии кислорода к изделиям.
Показано преимущество сочетания холодного прессования в пресс-формах со спеканием в кислородной среде в сравнении с технологией всестороннего гидростатического прессования в первую очередь по производительности при сопоставимых уровнях свойств.
Список источников
- Глозман, И.А. Пьезокерамика / И.А.Глозман. – М.: Энергия, 1967. – 272с.
- Прилипко, Ю.С. Функциональная керамика. Оптимизация технологии: Монография / Ю.С.Прилипко. – Донецк.: Норд-пресс, 2007. – 492с.
- Яффе, Б. Пьезоэлектрическая керамика / Б. Яффе , У.Кук, Г.Яффе. – М.: Мир, 1974. – 288с.
- Смажевская, Е.Г. Пьезоэлектрическая керамика / Е.Г.Смажевская , Н.Б. Фельдман. – М.: Советское радио, 1971. – 200с.
- Шишковский В.И. Влияние состава газовой фази при спекании на электрофизические свойства и прочность пьезокерамики ЦТС / В.И. Шишковский, В.В. Приседский, Н.А. Задорожная, В.В Климов // В сб.: Материалы для электронной техники. – М.: НИИТЭХИМ, 1979. – С. 8-13.
- Фесенко, Е.Г. Новые пьезокерамические материалы / Е.Г.Фесенко. – Изд. Ростовского университета, 1983. – 160с.
- Поляков, А.А. Технология керамических радиоэлектронных материалов/ А.А. Поляков. –М.: Радио и связь, 1989 –200с.
- Уорден. К. Новые интелектуальные материалы и конструкции. Свойства и прменение/ К. Уорден. – М.: Техносфера, 2006. –224с.