Научный руководитель:
Реферат по теме выпускной работы
Содержание
Введение
1 Источники образования и характеристика сточных вод коксохимического производства
2 Аналитический обзор методов очистки сточных вод от органических примесей
3 Свойства и структура волокнистых минеральных материалов
4 Физико-химические основы сорбционных методов очистки
5 Исследование сорбционных свойств минеральных волокон по отношению смолам и маслам
6 Анализ результатов экспериментальных исследований
Заключение
Перечень ссылок
Введение
Развитие химических отраслей промышленности, образование значительных количеств сточных вод, загрязнённых различными химическими веществами, повышение требований к качеству очищенных сточных вод обуславливают широкое применение разнообразных методов их очистки.
Основными путями уменьшения количества и загрязнённости сточных вод являются: разработка и внедрение безводных технологических процессов, совершенствование существующих технологических процессов, использование комплексных схем очистки сточных вод, внедрение аппаратов воздушного охлаждения.
Наиболее широко распространенными загрязнителями сточных вод являются нефтепродукты, масла коксохимических производств, которые по принятой в настоящее время терминологии при анализе сточных вод относят к «нефтепродуктам» .
В настоящее время проводится значительная работа, предусматривающая использование предварительно очищенных сточных вод в технологических процессах, в системах оборотного водоснабжения. Внедрение эффективных методов очистки сточных вод, а также мероприятий по утилизации из стоков ценных продуктов и сокращению количества сточных вод, сбрасываемых в водоёмы, позволит полностью предотвратить загрязнение водоёмов промышленными стоками. В ближайшем будущем многие предприятия химической промышленности будут работать вообще без сброса сточных вод в водоёмы, ввиду разработок новых высокоэффективных способов тонкой очистки сточных вод коксохимической и нефтяной промышленности, внедрение которых на производстве дадут возможность исключить данную операцию из технологической цепочки.
1 ИСТОЧНИКИ ОБРАЗОВАНИЯ И ХАРАКТЕРИСТИКА СТОЧНЫХ ВОД КОКСОХИМИЧЕСКОГО ПРОИЗВОДСТВА
Основным источником образования токсичных сточных вод в процессе коксования является влага топлива или шихты и пирогенетическая вода, образующаяся при термическом разложении топлива, а также конденсат острого пара, вводимого в процессах переработки топлив.
Газ из коксовых печей отводится в газосборники, где охлаждается путем орошения надсмольной водой. В охлаждающей воде растворяются кислые газы, аммиак и т. д.
Конечное охлаждение газа происходит также при непосредственном орошении водой. При этом из газа вымываются нафталин, остатки фенолов, часть цианистоводородной кислоты и т. д.
При выделении сырого бензола из поглотительного масла дистилляцией и ректификацией используется острый пар, что приводит к образованию сепараторных сточных вод. Сепараторные сточные воды образуются также в процессе фракционной разгонки смолы.
Кроме того, сточные воды образуются при переливах из хранилищ, аварийных выпусках, смене воды в оборотных циклах водоснабжения, мойке оборудования и полов т. д.
Количество и состав сточных вод зависят от качества коксуемых углей, технологических параметров процесса коксования, конструкции коксовых печей, и поэтому для разных коксохимических предприятий различны. По сути, рассматриваемые сточные воды, представляют собой разбавленные эмульсии, в которых органические вещества диспергированы в водной фазе. На современном коксохимическом заводе с печами больших объемов количество сточных вод на 1 т кокса составляет 0,2–0,3 м3 или около 150 м3/ч.
На коксохимическом заводе основными сточными водами являются фенольные. Кроме того, в процессе очистки коксового газа от сероводорода мышьяково-содовым методом образуется 4 – 6 м3/ч сточных вод. Представление о составе стока коксохимического завода и его отдельных составляющих дает таблица 1.1, составленная по материалам специальных обследований коксохимических заводов Украины (мг/л). [1]
Таблица 1.1 – Характеристика сточных вод коксохимических заводов
Соеди- нения |
Надсмольн. вода после скруббера |
Сепараторн. вода бенз. отделения |
Вода цикла КГХ |
Общий сток цеха улавли- вания |
Общий сток цеха ректифи- кации |
Сепара- торные воды |
Общий сток |
Типичн. общий сток завода |
Фенолы: | ||||||||
летучие | 228 | - | 680 | 260 | - | 3460 | 800 | 290 |
многоатом ные |
190 | - | - | 200 | - | 380 | 42 | 125 |
Аммиак: | ||||||||
летучий | 379 | - | - | - | - | - | - | - |
общий | 2100 | 232 | 436 | 490 | - | 2320 | 835 | 980 |
Роданиды | 464 | 104 | 265 | 360 | - | - | - | 400 |
Цианиды | 14 | 103 | 78 | 56 | 11 | 80 | 25 | 28 |
Сульфиды | 28 | 251 | 82 | 15 | - | - | - | 12 |
Хлориды | 3620 | - | 270 | 2450 | - | - | 262 | 1640 |
Сульфаты | 920 | - | 400 | 2140 | 660 | - | - | 1480 |
Тиосульфаты | 300 | 300 | 265 | 430 | - | - | - | 290 |
Смолы и масла | 58 | - | 77 | 117 | 85 | 145 | 175 | 110 |
Пиридин. основания | 200 | 140 | 130 | 115 | 110 | 400 | 250 | 150 |
рН | 8.8 | 7.1 | 7.1 | 7.1 | 7.8 | 8.4 | 8.7 | 7.7 |
t,оC | 92 | 45 | 30 | 44 | 34 | 50 | 46 | 36 |
Окисляемость | 2020 | 1260 | 1620 | 1430 | 1550 | 7800 | 3560 | 2030 |
Компонентный состав, интересуемой смолистой фазы можно рассмотреть на примере типовой хроматограммы для аммиачной воды ( рис 1.1).
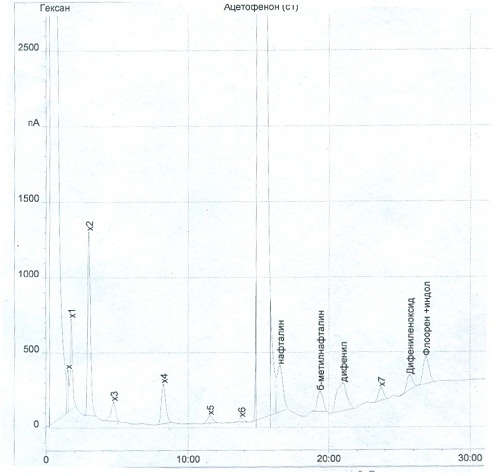
1 – бензол; 2 – толуол; 3 – м-ксилол; 4 – 3-метилбензол; 5 – инден; 6 – неидентифицированный ; 7 – аценафтен.
Согласно полученной хроматограмме (рис. 1.1 ), смолистая фаза содержит преимущественно ароматические углеводороды: бензол и его гомологи, нафталин и его гомологи, дифенил, диметилнафталин, аценафтен, аценафтилен, флуорен, индол, фенатрен, антрацен, серо– и кислородсодержащие ароматические соединения.
Если сравнить состав смолистой фазы надсмольной воды и конденсата ПГХ, то компонентный состав их одинаковый. Отличие в количестве компонентов. В конденсате ПГХ больше бензола и его гомологов, нафталина и метилнафталина (70,9% против 57,6%). В надсмольной воде – тяжелых ароматических углеводородов (инден, дифенил, аценафтен, аценафтилен, флорен, индол, флуорен, фенантрен, антрацен) – 42,4% против 29,1% в конденсате ПГХ. [2].
Для уменьшения количества образующихся сточных вод необходимо снижать влажность шихты, произвести замену пароинжекторных установок на газоинжекторные, усовершенствовать технологические процессы переработки продуктов с целью уменьшения количества расходуемого острого пара и воды, а также применение аппаратов воздушного охлаждения вместо водяного для первичного охлаждения коксового газа, паров бензола, масел и других продуктов.
Таким образом, в коксохимической промышленности объем сточных вод, загрязненных отходами производства зависит от количества и технических параметров коксуемой шихты и составляет около 38% от количества коксуемой сухой шихты. Сточные воды КХЗ используют в основном для тушения кокса. Однако они содержат значительное количество различных вредных примесей, которые при соприкосновении с раскаленным коксом испаряются и попадают в окружающую атмосферу. Масла и смолы, которые также содержаться в сточных водах при оборотном водоиспользовании оседают на стенках труб и аппаратов, что значительно затрудняет эксплуатацию оборудования. Поэтому предъявляются жесткие требования к составу сточных вод.
2 АНАЛИТИЧЕСКИЙ ОБЗОР МЕТОДОВ ОЧИСТКИ СТОЧНЫХ ВОД ОТ ОРГАНИЧЕСКИХ ПРИМЕСЕЙ
Удаление смол и масел из сточных вод коксохимических заводов можно осуществить различными способами. Выбор метода разделения маслоэмульсионных стоков связан с размерами масляных частиц, составом смолистой фазы, требованиями к качеству очищеннй воды и другими сопутствующими параметрами. Существуют следующие основные способы очистки сточных вод: механический, физико-химический, химический и биологический.
Механические способы очистки предполагают использование процеживания, отстаивания и фильтрования производственных сточных вод. Процесс отстаивания применяется для вод с высоким со¬держанием смол масел различной степени дисперсности, для чего применяют наиболее простые аппараты: различного типа отстойники и маслоловушки. Данный способ очистки позволяет извлечь частицы диаметром 80–100 мкм. Для значительной интенсификации отстаивания масляных глобул можно используя центрифугирование в гидроциклонах (напорные, безнапорные, многоярусные, комбинированные), центрифугах и сепараторах.
Но применение центробежных аппаратов для очистки от эмульгированных масел связано со значительными энергетическими и эксплуатационными затратами. Поэтому центрифугирование можно рекомендовать лишь для локальной очистки небольших по объему маслоэмульсионных стоков.
Широко распространенным способом очистки сточных вод и конденсатов является фильтрация. В качестве фильтрующего материала используют инертную зернистую загрузку: песок, гравий, щебень, а также различные отходы производства. При работе зернистых фильтров загрузка быстро забивается и для регенерации ее от масел требуется большое количество промывных вод.
Фильтры очень чувствительны к гидравлическому режиму промывки. Применение фильтров в практике очистки сточных вод сдерживается их высокой стоимостью, необходимостью сравнительно частой замены загрузки и поддержания напора на входе в фильтр. [3]
К основным химическим способам очистки от органических примесей относятся методы с применением окислителей. С их помощью сточные воды освобождаются от токсичных и других компонентов. К примеру, метод окисления озоном не находит широкого применения в промышленности. Высокая стоимость получения озона, его токсичность, невысокое качество озонаторного оборудования не позволяет применять этот метод для глубокой очистки сточных вод.
Биологический (биохимический) метод используется для очистки хозяйственно-бытовых и производственных сточных вод целлюлозно-бумажных, нефтеперерабатывающих, коксохимических и пищевых предприятий. Этот метод основан на способности искусственно вселяемых микроорганизмов использовать для своего развития органические и некоторые неорганические соединения, содержащиеся в сточных водах как загрязнители. Биохимическая очистка производится с помощью естественных и искусственных методов. Естественные методы биоочистки осуществляются с применением полей орошения и фильтрации, а также биологических прудов, а искусственные методы – с помощью метантенков, биофильтров. Очистка в аэротенках осветленных в первичных отстойниках сточных вод осуществляется путем медленного пропуска через них сточных вод, обогащенных кислородом, и смешивания их с активным илом. Активный ил представляет собой совокупность гетеротрофных микроорганизмов и мелких беспозвоночных животных (плесени, дрожжей, водных грибов, коловраток и др.), а также твердого субстрата. При этом важно правильно подобрать температуру, реакцию среды, стимулирующие добавки, тщательное перемешивание и эффективный окислитель, для того чтобы в максимальной степени способствовать интенсификации гидробиоценоза, составляющего активный ил, поглощающий загрязнения. Данный метод весьма эффективен и применяется только для доочистки сточных вод, так как высокие концентрации компонентов-загрязнителей губительно влияют на жизнедеятельность микроорганизмов активного ила.
Физико-химическая очистка сточных вод осуществляется в основном с применением таких методов, как коагуляция, флотация и сорбция.
Коагуляция производится путем введения в сточные воды коагулянтов (солей аммония, железа, меди, шламовых отходов и др.) для образования хлопьевидных осадков, которые затем легко удаляются.
Флотация осуществляется путем пропуска через сточные воды воздуха, пузырьки которого захватывают при движении вверх поверхностно-активные вещества, нефть, масла и другие загрязнения и образуют на поверхности воды легко удаляемый пенообразный слой. Данный способ очистки в промышленности применяют редко из-за его небольшой эффективности, высокой турбулентности потоков во флотационной камере, приводящей к разрушению хлопьевидных частиц и необходимости применять поверхностно-активные вещества.
Сорбция основана на способности некоторых веществ, называемых сорбентами (глины, активированный уголь, цеолиты, силикагель, торф и др.), поглощать загрязнения, в результате чего происходит извлечение из сточных вод не только вредных, но и ценных веществ. [4]
Среди сорбционных методов наибольшее развития получили адсорбционные, которые применяют для глубокой очистки сточных вод от растворённых органических и смолистых веществ перед биохимической очисткой.
Достоинством метода являются высокая эффективность, возможность очистки сточных вод, содержащих несколько веществ, а также рекуперация этих веществ, возможность очищать сточные воды без внесения каких-либо вторичных загрязнений, удаления биологически неразрушимых веществ, надёжность в условиях колебания объемов и состава сточных вод. [5]
Адсорбционная очистка может быть регенеративной, т.е. с извлечением вещества из адсорбента и его утилизацией, и деструктивной, при которой извлеченные из сточных вод вещества уничтожаются вместе с адсорбентом. Эффективность адсорбционной очистки зависит от химической природы адсорбента, величины адсорбционной поверхности и её доступности и от химического строения вещества.
В качестве адсорбентов применяют природные и искусственные пористые материалы. Используют асбестосодержащий материал – отход производства асбестовых бумаг и картона, пористый полимерный сорбент-сополимер стирола дивинилбензола, пенополеуритан, сорбент на основе базальтового волокна, древесные стружки, опилки, волокна, помещенные в пористые тканые оболочки, различные модификации активных углей и другие адсорбенты. Сорбентами также могут служить шлаки, кокс, зола.[6]
Адсорбция активными углями являются одним из методов очистки промышленных вод, содержащих органические примеси, и позволяет добиться глубокой очистки воды до норм ПДК вредных веществ в воде промышленного, оборотного использования с одновременной утилизацией или деструктивным разрушением извлечённых веществ. Адсорбционная способность активных углей является следствием сильно развитой поверхности и пористости. Удельная поверхность активных углей составляет 400–900 м2/г; адсорбционные свойства в значительной мере зависит от структуры, величины пор. [7]
Исходным сырьём для получения активного угля служат практически любые углеродсодержащие материалы: уголь, торф, древесина и др. Процесс изготовления высококачественных активных углей сложен и длителен, поэтому стоимость их достаточна высока. Это приводит к необходимости многократного использования активных углей или их использования в качестве вторичного сырья, например, как добавку к шихте для коксования [8]. Поэтому широкое применение активных углей при очистке сточных вод сдерживается экономическими рамками.
Достоинства данного метода – возможность проводить адсорбцию веществ из многокомпонентных примесей, а также высокая эффективность, особенно при очистке низкоконцентрированных сточных вод.
На наш взгляд, наиболее перспективным направлением сорбционной очистки сточных вод являются методы с использованием сорбентов на основе минеральных волокон. Необходимо отметить, что данные сорбенты (стекловолокно, минеральное волокно диабазовой группы) получают из дешевого сырья, поэтому стоимость готового изделия невелика; обеспечивают высокую поглощающую способность при фильтрование аммиачных сточных вод, содержащих смолистые органические вещества. Поэтому целесообразность проведения дальнейших исследований в этом направлении несомненна.
Аппаратурное оформление сорбционной очистки – общепринятые в химической технологии – напорные фильтры с плотным слоем гранулированных активных углей, перед которыми расположены механические фильтры. Двухступенчатое фильтрование применяется при глубокой очистки сточных вод, содержащих эмульгированные и растворенные нефтепродукты. Например, коалесцирующий фильтр, затем отстойник и фильтр с волокнистым адсорбентом.
Таким образом, поскольку данные методы могут обеспечивать глубокую очистку сточных вод от высокодисперсных и растворенных масел и смол, а требования к качеству очищаемой воды становятся все более жесткими, перспектива применения этих методов сохраняется.
3 СВОЙСТВА И СТРУКТУРА ВОЛОКНИСТЫХ МИНЕРАЛЬНЫХ МАТЕРИАЛОВ
Наиболее эффективным методом очистки от органических примесей является метод с использованием волокнистых материалов, которые бывают природного и искусственного происхождения. Среди волокон-сорбентов искусственного происхождения существует много разновидностей, которые используют в качестве как коалесцирующего, так и фильтрующего материала (волокнистый полипропилен, полиэтилен, волокнистый фторопласт и др.). Однако, приведенные материалы применяются для очистки сточных вод от нефтепродуктов, которые по своему составу отличаются от смолистой фазы сточных вод в коксохимии. Каменноугольные масла состоят в основном из ароматических углеводородов, в то время как обычные нефтепродукты – это смесь преимущественно алифатических, ациклических и в малой доле ароматических углеводородов. [8]
Можно отметить, что для поглощающей (фильтрующей) способности воловон имеет решающее значение диаметр волокна, инертность и сродство материала изделия к загрязняющим компонентам. Исходя из данных требований наиболее подходит для очистки от смолистой фазы коксохимических сточных вод минеральные волокна, подробное описание свойств и характеристик которых приводится ниже.
Минеральное волокно изготавливают на основе природных материалов. Выбранный материал представляет собой полимер с продольными связями, который может быть использован для тонкой очистки сточных вод в коксохимической промышленности от смолистых органических веществ.
Стекловолокно (СВ) – волокнистый материал, получаемый на основе силикатных расплавов горных пород, металлургических шлаков и других промышленных отходов или их смесей. Минеральная вата состоит из тончайших взаимно переплетающихся волокон, находящихся в стекловидном состоянии, и не волокнистых включений в виде капель застывшего расплава.
Для производства стеклянных волокон смешивают песок, соду, известняки, некоторые химические добавки и получают шихту. Расплавленная шихта в процессе производства становится стеклом. На следующем этапе расплав стекла раздувают паром, воздухом, на центрифуге или другими методами, получая волокно. Применяют для изготовления тепло- , звукоизоляционных, звукопоглощающих изделий, а также для фильтрации.
Минеральное волокно диабазовой группы (МВД) – это слой штапельных волокон перепутанных и скрепленных между собой в виде холста. Получают из расплава собственно базальта, а также некоторых близких к нему пород без каких либо дополнений в виде синтетических или минеральных веществ.
Работы по получению волокон из изверженных горных пород (базальтов, амфиболитов, порфиритов и др.) перспективны. Во-первых, эти породы широко распространены на территориях Украины и стран СНГ. Во-вторых, в отличие от шихт, используемых для производства стеклянных волокон, основные горные породы не требуют дефицитных добавок бора, соды, сульфата, глинозема и др. и исключают процессы приготовления шихты. Плавка пород происходит без стадии силикатообразования.
В таблице 3.1 приведены основные свойства и характеристики стекловолокна и минерального волокна диабазовой группы.
Таблица 3.1 – Характеристика СВ и МВД [9]
Показатели | Типы волокон | |
СВ | МВД | |
Кажущаяся плотность, кг/м3 | 12–25 | 15–23 |
Средний диаметр волокна, мкм, не более | 4–12 | 1–3 |
Длина волокон, мм | 15–50 | 40-70 |
Диапазон температур применения, оC | -60…+250 | -250…+700 |
Коэффициент теплопроводности, Вт/м оC | 0,038..0,042 | 0,031..0,034 |
Химическая устойчивость (потеря веса ) ,% | ||
в воде | 6.2 | 1,6 |
в щелочной среде | 6,0 | 2,75 |
в кислотной среде | 38,9 | 2,2 |
Волокнистые материалы находятся в довольно широком диапазоне температур применения и имеют высокую химическую стойкость к воде, солевым растворам, кислотным и щелочным средам; имеют большую поглощающую поверхность, которая обуславливает хорошие адсорбционные свойства. Поэтому работа была направлена на исследование возможности применения данного класса материалов для очистки сточных вод от органических примесей.
4 ФИЗИКО-ХИМИЧЕСКИЕ ОСНОВЫ СОРБЦИОННЫХ МЕТОДОВ ОЧИСТКИ
Адсорбция – это самопроизвольно протекающий диффузионный процесс, сопровождающийся уменьшением запаса энергии Гиббса системы, в результате которого происходит концентрирование растворённого вещества (адсорбента) или растворителя (адсорбтива) на поверхности твёрдого тела (адсорбента). В общем виде процесс адсорбции описывается уравнением Гиббса. Согласно современным представлениям, энергия адсорбции – это разность энергий взаимодействия с адсорбентом и соседними молекулами в адсорбционном слое.
По типу сил, в результате которых осуществляется адсорбция, указанный процесс можно разделить на две группы: физическая адсорбция и процесс связывания вещества за счёт химических взаимодействий - хемосорбция. Физическая адсорбция вызывается силами молекулярного взаимодействия. Физическую и химическую адсорбцию можно различить по теплоте адсорбции. Теплота физической адсорбции соизмерима с теплотой конденсации веществ и не превышает 80–120 кДж/моль. Теплота хемосорбции одного моля вещества достигает нескольких сотен килоджоулей.
Одной из основных характеристик адсорбентов и адсорбционных взаимодействий является изотерма адсорбции.
Простейшее уравнение изотермы адсорбции, называемое изотермой Генри, применимо при минимальных степенях заполнения поверхности адсорбатом при малых давлениях:
где а – величина адсорбции;
к – константа Генри;
р – давление.
Для мономолекулярной адсорбции применимо уравнение Ленгмюра:
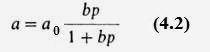
где а – количество вещества, адсорбированного при давлении р;
а0 – предельная концентрация поглощенного компонента;
в – коэффициент, зависящий от температуры.
При наличии взаимодействия адсорбированных комплектов между собой используют уравнения Гугенгейма:
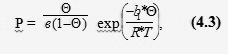
где Θ= а/а0;
в – константа, характеризующая взаимодействия адсорбат – адсорбент;
в1 – константа, характеризующая взаимодействия адсорбат –адсорбент в монослое.
В дальнейшем Брунауэр, Эммет и Теллер обосновали теорию полимолекулярной адсорбции:

где V – объем вещества, адсорбированного единицей массы адсорбента, м3⁄2 ;
Vm – объем вещества, адсорбированного единицей массы адсорбента, когда вся поверхность покрыта монослоем.
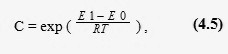
где E1 – теплота адсорбции в первом слое, кДж;
E0 – теплота конденсации, кДж.
Необходимо отметить, что применение уравнения может быть корректным при отсутствии микробов.
Широкое распространение в практических расчётах по адсорбции в области средних насыщений получено уравнение Фрейдлиха:
где а – количество адсорбированного вещества;
р – давление адсорбтива;
r и n – постоянные величины.
На процесс адсорбции влияет: физико-химические свойства материала насадки фильтра, заключающиеся в способности удерживать и накапливать на своей поверхности смолистые вещества за счёт адгезионного взаимодействия; физико-химические свойства воды, проявляющиеся в изменении гидрофобных свойств поверхности насадки; гидродинамический режим течения эмульсии в насадке.
5 ИССЛЕДОВАНИЕ СОРБЦИОННЫХ СВОЙСТВ МИНЕРАЛЬНЫХ ВОЛОКОН ПО ОТНОШЕНИЮ К СМОЛАМ И МАСЛАМ
На наш взгляд наиболее перспективным направлением сорбционной очистки сточных вод являются методы с использованием волокнистых минеральных материалов. Для исследования были выбраны следующие минеральные волокна – стекловолокно (СВ) и минеральное волокно диабазовой группы (МВД).
В лабораторных условиях исследовали сорбционную емкость (СЕ) минеральных волокон в статических условиях, для чего искусственно готовились эмульсии с различной концентрацией смолистой фазы.
В водосмоляную эмульсию (100 мл) с различным содержанием смол и масел (0,1–10%) помещали 1 г исследуемого волокна. Выдерживали до полного насыщения, после чего определяли остаточное содержание смолистых веществ в водной фазе методом экстракции 4-х хлористым углеродом с последующим колориметрированием. Результаты исследований приведены в таблице 5.1.
Таблица 5.1 – Результаты исследования процесса сорбции смолистых веществ на минеральных волокнах
Содержание смолистой фазы, % | Остаточное содержание смолистых веществ, мг/л | СЕ, мг см. веществ/1 г волокна | Степень поглощения смолистых веществ волокном, % | |||
СВ | МВД | СВ | МВД | СВ | МВД | |
0,1 | - | 19 | - | 49 | - | 98,0 |
0,2 | - | 20 | - | 99 | - | 98,9 |
0,4 | 49 | - | 198 | - | 98,8 | - |
0,5 | - | 31 | - | 248 | - | 99,4 |
0,6 | 41 | - | 298 | - | 99,3 | - |
1 | 63 | 57 | 497 | 497 | 99,4 | 99,4 |
2 | 62 | - | 997 | - | 99,7 | - |
3 | - | 76 | - | 1496 | - | 99,8 |
5 | - | 144 | - | 2493 | - | 99,7 |
6 | 105 | - | 2995 | - | 99,8 | - |
7 | - | 175 | - | 3492 | - | 99,8 |
10 | 116 | 191 | 4995 | 4991 | 99,9 | 99,8 |
По полученным экспериментальным данным построены графики зависимости остаточного содержания смолистых веществ и СЕ от содержания смолистых веществ в эмульсиях первоначально до опыта и представлены на рисунках 5.1 и 5.2 соответственно.
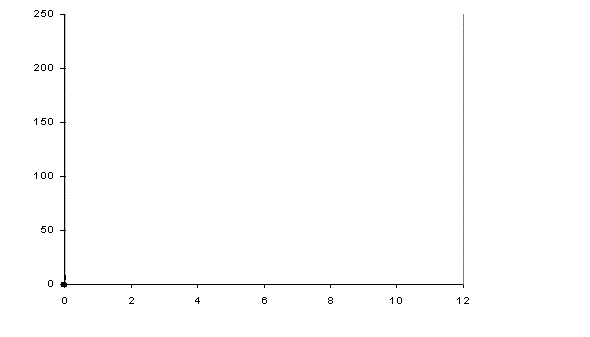
Рисунок 5.1 – График зависимости остаточного содержания смолистых веществ от их содержания в эмульсии до опыта (0,1 – 10%)
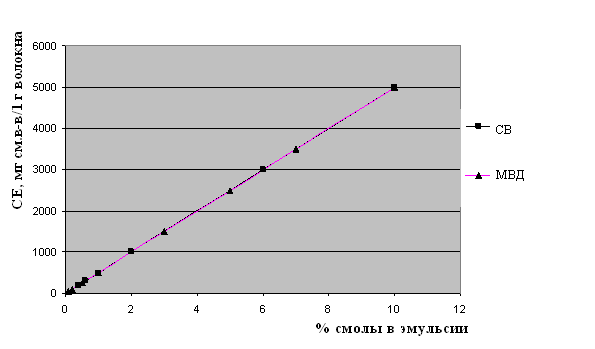
Рисунок 5.2 – График зависимости СЕ от содержания смолистых веществ в эмульсии
6 АНАЛИЗ РЕЗУЛЬТАТОВ ЭКСПЕРИМЕНТАЛЬНЫХ ИССЛЕДОВАНИЙ
Анализ результатов показал, что стекловолокно обладает более высокой сорбционной емкостью (рис.5.1), так как остаточное содержание смолистых веществ после проведения опыта ниже, чем у МВД. Для низкоконцентрированных эмульсий (0,1–1%) эта разница незначительна, а для высококонцентрированных ( 1 – 10% ) – приобретает существенные отличия. Например, для 10 %-ной эмульсии эта разница составляет 75 мг / л.
Построена зависимость величины СЕ от содержания смолистых веществ (рис.5.2), которая подчиняется уравнению Фрейдлиха для аналитического описания изотермы адсорбции, при м=1 (4.3). Величина сорбционной емкости имеет достаточно высокие численные значения для соответствующей концентрации смолистых веществ в эмульсии.
Также рассчитана величина поглощения смолистых веществ при использовании выбранных сорбентов (табл. 5.1) численные значения которой при различном содержании смолистых веществ в эмульсии высокое и составляет 99,3 – 99,9 %. Это говорит о перспективности их использования для эффективной очистки технологических и сточных аммиачных вод коксохимического производства. Значит, используемые сорбенты эффективны для дальнейшего применения в качестве фильтрующей загрузки от смолистых веществ. Поэтому целесообразно проведение дальнейших исследований в этом направлении.
ЗАКЛЮЧЕНИЕ
В работе рассмотрены источники образования и характеристика сточных вод коксохимического производства, изучены свойства и структура минеральных сорбентов, приведены физико-химические основы процесса адсорбции.
На основе аналитического обзора методов очистки сточных вод от органических примесей был сделан вывод о том, что наиболее экономически выгодным и эффективным является использование для этой цели метода с применением минеральных волокнистых сорбентов.
В лабораторных условиях проведены 2 серии опытов на искусственно приготовленных эмульсиях. В результате чего были получены изотермы адсорбции для двух материалов (стекловолокно и минеральное волокно диабазовой группы); определена сорбционная емкость и проведен анализ экспериментальных исследований. Достоинствами выбранных сорбентов является высокая степень поглощения смолистых веществ и низкая стоимость минеральных волокон. Достаточно большое значение величины сорбционной ёмкости данных сорбентов в условиях эксперимента (10 % эмульсия – 4991,4 и 4995,2 мг см. веществ/1 г волокна для МВД и СВ соответственно) также говорит о перспективности их использования с дальнейшей оптимизацией параметров процесса для более высокой эффективности работы очистной установки с использованием минерального волокна.
ПЕРЕЧЕНЬ ССЫЛОК
- Лазорин С.Н., Папков Г.И., Литвиненко В.И.Обезвреживание отходов коксохимических заводов / C.Н. Лазорин, Г.И. Папков, В.И. Литвиненко.– М.: Металлургия. – 1977.– 241 с.
- Крутько І.Г., Пульникова Ю.В. Визначення характеристик кам’яновугильних водних емульсій високотемпературного піролізу вугільної шихти // Углехимический журнал – Харьков: УХИН – 2011. – № 1–2. – с. 75–81.
- Зубахин Н.П., Клушин В.Н., Дмитриева Д.А., Зелькова Е.В. Оценка концентратов ископаемых углей // журнал Кокс и Химия – M.: Металлургиздат – 2011. – № 4.– с. 39.
- Чернявский А.Ю. Способы очистки сточных вод [электронный ресурс]. – Режим доступа:
http://www.isgod.ru - Кульский Л.А., Даль В.В., Кудельская Г.А., Кузнецова Л.Г. Методы очистки промышленных сточных вод / Л.А. Кульский, В.В. Даль, Г.А. Кудельская , Л.Г Кузнецова.– К.: УКР НИИ НТИ. – 1978. – 288 с.
- Кузубова Л.И., Морозов С.В. Очистка нефтесодержащих сточных вод / Л.И. Кузубова, С.В. Морозов. – Новосибирск.: ГПНТБ СО РАН. – 1992. – 72 c.
- Проскуряков В.А., Шмидт Л.И. Очистка сточных вод в химической промышленности / В.А. Проскуряков, Л.И. Шмидт. – Л.: Химия. – 1977.– 241с.
- Небольсина Л.А., Передерий О.Г., Харлампович Г.Д., Дербышева Е.К. Состояние перспективы очистки сточных вод коксохимических предприятий от эмульгированных масел // журнал Кокс и Химия – M.: Металлургиздат – 1985.– № 10.– с. 28.
- Сравнительные характеристики стеклянных, минеральных и базальтовых волокон и материалов на их основе [электронный ресурс]. – Режим доступа: http://www.proxima.com.ua