Науковий керівник:
Реферат за темою випускної роботи
Зміст
Вступ
1 Джерела виникнення та характеристика стічних вод коксохімічного виробництва
2 Аналітичний огляд методів очистки стічних вод від органічних домішок
3 Властивості та структура волокнистих мінеральних матеріалів
4 Фізико-хімічні основи сорбційних методів очищення
5 Дослідження сорбційних властивостей мінеральних волокон по відношенню до смол і масел
6 Аналіз результатів експериментальних досліджень
Аналіз результатів експериментальних досліджень
Перелік посилань
ВСТУП
Розвиток хімічних галузей промисловості, виникнення значних кількостей стічних вод, забруднених різними хімічними речовинами, підвищення вимог до якості очищених стічних вод обумовлюють широке застосування різноманітних методів їх очищення.
Основними шляхами зменшення кількості та забрудненості стічних вод є: розробка і впровадження безводних технологічних процесів, вдосконалення існуючих технологічних процесів, використання комплексних схем очищення стічних вод, впровадження апаратів повітряного охолодження.
Найбільш широко поширеними забруднювачами стічних вод є нафтопродукти, масла коксохімічних виробництв, які за прийнятою на даний момент часу термінологією при аналізі стічних вод відносять до "нафтопродуктів".
Зараз проводиться значна робота, яка передбачає використання попередньо очищених стічних вод в технологічних процесах, в системах оборотного водопостачання. Впровадження ефективних методів очистки стічних вод, а також заходів з утилізації зі стоків цінних продуктів і скорочення кількості стічних вод, що скидаються у водойми, дозволить повністю запобігти забрудненню водоймищ промисловими стоками. В найближчому майбутньому багато підприємств хімічної промисловості будуть працювати взагалі без скидання стічних вод у водойми, зважаючи на розробки нових високоефективних способів тонкої очистки стічних вод коксохімічної і нафтової промисловості, впровадження яких на виробництві дадуть можливість виключити дану операцію з технологічного ланцюжка.
1 ДЖЕРЕЛА ВИНИКНЕННЯ ТА ХАРАКТЕРИСТИКА СТІЧНИХ ВОД КОКСОХІМІЧНОГО ВИРОБНИЦТВА
Основним джерелом утворення токсичних стічних вод в процесі коксування є волога палива або шихти і пірогенетична вода, що утворюється при термічному розкладанні палива, а також конденсат гострої пари, що вводиться в процесах переробки палив.
Газ з коксових печей відводиться в газозбірники, де охолоджується шляхом зрошення надсмольною водою. В охолоджуючій воді розчиняються кислі гази, аміак та ін.
Кінцеве охолодження газу відбувається також при безпосередньому зрошенні водою. При цьому з газу вимиваються нафталін, залишки фенолів, частина ціанистоводневої кислоти та ін.
При виділенні сирого бензолу з поглинального масла дистиляцією та ректифікацією використовується гостра пара, що призводить до утворення сепараторних стічних вод. Сепараторні стічні води утворюються також в процесі фракційної розгонки смоли.
При виділенні сирого бензолу з поглинального масла дистиляцією та ректифікацією використовується гостра пара, що призводить до утворення сепараторних стічних вод. Сепараторні стічні води утворюються також в процесі фракційної розгонки смоли.
Кількість і склад стічних вод залежать від якості коксованого вугілля, технологічних параметрів процесу коксування, конструкції коксових печей, і тому для різних коксохімічних підприємств різні. По суті, розглянуті стічні води, представляють собою розбавлені емульсії, в яких органічні речовини дисперговані у водній фазі. На сучасному коксохімічному заводі з печами великих об’ємів кількість стічних вод на 1 т коксу складає 0,2–0,3 м3 або близько 150 м3/год.
На коксохімічному заводі основними стічними водами є фенольні. Крім того, в процесі очищення коксового газу від сірководню миш'яково-содовим методом утворюється 4 – 6 м3/год стічних вод. Уявлення про склад стоку коксохімічного заводу і його окремих складових дає таблиця 1.1, складена за матеріалами спеціальних обстежень коксохімічних заводів України (мг/л). [1]
Таблиця 1.1 – Таблиця 1.1-Характеристика стічних вод коксохімічних заводів
Сполука | Надсмоль- на вода після скру- бера |
Сепа- раторна вода бенз. відді- лення |
Вода циклу КГХ |
Загальн. стік цеху уловлю- вання |
Загальн. стік цеху ректи- фікації |
Сепа- раторні води |
Загальн. стік |
Типовий загальн. стік заводу |
Феноли: | ||||||||
летючі | 228 | - | 680 | 260 | - | 3460 | 800 | 290 |
многоатом ні |
190 | - | - | 200 | - | 380 | 42 | 125 |
Аміак: | ||||||||
летючий | 379 | - | - | - | - | - | - | - |
загальний | 2100 | 232 | 436 | 490 | - | 2320 | 835 | 980 |
Роданіди | 464 | 104 | 265 | 360 | - | - | - | 400 |
Цианіди | 14 | 103 | 78 | 56 | 11 | 80 | 25 | 28 |
Сульфіди | 28 | 251 | 82 | 15 | - | - | - | 12 |
Хлоріди | 3620 | - | 270 | 2450 | - | - | 262 | 1640 |
Сульфати | 920 | - | 400 | 2140 | 660 | - | - | 1480 |
Тіосульфати | 300 | 300 | 265 | 430 | - | - | - | 290 |
Смоли і масла | 58 | - | 77 | 117 | 85 | 145 | 175 | 110 |
Піридин. основи | 200 | 140 | 130 | 115 | 110 | 400 | 250 | 150 |
рН | 8.8 | 7.1 | 7.1 | 7.1 | 7.8 | 8.4 | 8.7 | 7.7 |
t,оC | 92 | 45 | 30 | 44 | 34 | 50 | 46 | 36 |
Окислюваність | 2020 | 1260 | 1620 | 1430 | 1550 | 7800 | 3560 | 2030 |
Компонентний склад, смолистої фази, що викликає інтерес, можна розглянути на прикладі типової хроматограми для аміачної води (рис 1.1).
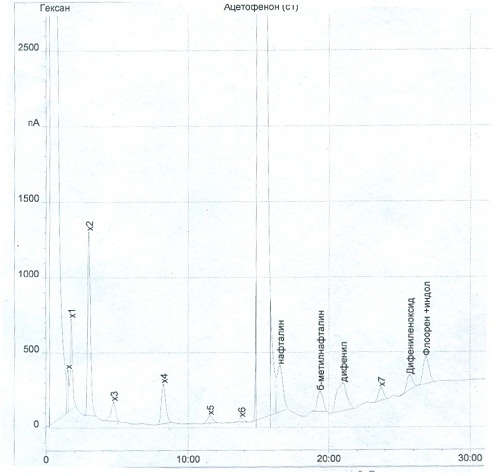
1 – бензол; 2 – толуол; 3 – м-ксилол; 4 – 3-метилбензол; 5 – інден; 6 – не ідентифікований; 7 – аценафтен.
Згідно отриманій хроматограмі (рис. 1.1), смолиста фаза містить переважно ароматичні вуглеводні: бензол і його гомологи, нафталін і його гомологи, дифеніл, діметилнафталін, аценафтен, аценафтилен, флуорен, індол, фенатрен, антрацен, сіро- і кісневмісні ароматічні сполуки.
Якщо порівняти склад смолистої фази надсмольної води і конденсату ПГХ, то компонентний склад їх однаковий. Відмінність у кількості компонентів. У конденсаті ПГХ більше бензолу і його гомологів, нафталіну і метилнафталіну (70,9% проти 57,6%). В надсмольній воді – важких ароматичних вуглеводнів (інден, дифеніл, аценафтен, аценафтилен, індол, флуорен, фенантрен, антрацен) – 42,4% проти 29,1% в конденсаті ПГХ [2].
Для зменшення кількості утворення стічних вод необхідно знижувати вологість шихти, зробити заміну пароінжекторних установок на газоінжекторні, удосконалити технологічні процеси переробки продуктів з метою зменшення кількості витрачання гострої пари і води, а також застосування апаратів повітряного охолодження замість водяного для первинного охолодження коксового газу, пари бензолу, масел та інших продуктів.
Таким чином, в коксохімічній промисловості об’єм стічних вод, забруднених відходами виробництва, залежить від кількості і технічних параметрів коксованої шихти і становить близько 38% від кількості коксованої сухої шихти. Стічні води КХЗ використовують в основному для гасіння коксу. Проте вони містять значну кількість різних шкідливих домішок, які при зіткненні з розпеченим коксом випаровуються і потрапляють у навколишнє середовище. Масла і смоли, які також містяться у стічних водах, при оборотному водовикористанні осідають на стінках труб і апаратів, що значно ускладнює експлуатацію обладнання. Тому висуваються жорсткі вимоги до складу стічних вод.
2 АНАЛІТИЧНИЙ ОГЛЯД МЕТОДІВ ОЧИЩЕННЯ СТІЧНИХ ВОД ВІД ОРГАНІЧНИХ ДОМІШОК
Видалення смол і масел з стічних вод коксохімічних заводів можна здійснити різними способами. Вибір методу розділення маслоемульсійних стоків пов'язаний з розмірами масляних часток, складом смолистої фази, вимогами до якості очищеної води та іншими супутніми параметрами. Існують такі основні способи очистки стічних вод: механічний, фізико-хімічний, хімічний і біологічний.
Механічні способи очищення припускають використання проціджування, відстоювання і фільтрування виробничих стічних вод. Процес відстоювання застосовується для вод з високим вмістом смол і масел різного ступеня дисперсності, для чого застосовують найбільш прості апарати: різного типу відстійники і маслопастки. Даний спосіб очищення дозволяє витягти частинки діаметром 80–100 мкм. Для значної інтенсифікації відстоювання масляних глобул можна використовуючи центрифугування в гідроциклонах (напорні, безнапорні, багатоярусні, комбіновані), центрифугах і сепараторах. Але застосування відцентрових апаратів для очищення від емульгованих масел пов'язано зі значними енергетичними та експлуатаційними витратами. Тому центрифугування можна рекомендувати лише для локального очищення невеликих за об’ємом маслоемульсійних стоків.
Широко поширеним способом очищення стічних вод і конденсатів є фільтрація. В якості фільтруючого матеріалу використовують інертне зернисте завантаження: пісок, гравій, щебінь, а також різні відходи виробництва. При роботі зернистих фільтрів завантаження швидко забивається і для регенерації його від масел потрібна велика кількість промивних вод.
Фільтри дуже чутливі до гідравлічного режиму промивки. Застосування фільтрів в практиці очищення стічних вод стримується їхньою високою вартістю, необхідністю порівняно частої заміни завантаження і підтримки напору на вході у фільтр [3].
До основних хімічних способів очищення від органічних домішок відносяться методи з застосуванням окислювачів. За їх допомогою стічні води звільняються від токсичних та інших компонентів. Наприклад, метод окислення озоном не знаходить широкого застосування в промисловості. Висока вартість отримання озону, його токсичність, невисока якість озонаторного обладнання не дозволяє застосовувати цей метод для глибокого очищення стічних вод.
Біологічний (біохімічний) метод використовується для очищення господарсько-побутових і виробничих стічних вод целюлозно-паперових, нафтопереробних, коксохімічних і харчових підприємств. Цей метод заснований на здатності мікроорганізмів використовувати для свого розвитку органічні і деякі неорганічні сполуки, що містяться в стічних водах як забруднювачі. Біохімічна очистка проводиться за допомогою природних і штучних методів. Природні методи біоочищення здійснюються із застосуванням полів зрошування та фільтрації, а також біологічних ставків, а штучні методи - за допомогою метантенків, біофільтрів. Очищення в аеротенках освітлених в первинних відстійниках стічних вод здійснюється шляхом повільного пропускання крізь них стічних вод, збагачених киснем, і змішування їх з активним мулом. Активний мул являє собою сукупність гетеротрофних мікроорганізмів і дрібних безхребетних тварин (цвілі, дріжджів, водних грибів, коловерток та ін. ), а також твердого субстрату. При цьому важливо правильно підібрати температуру, реакцію середовища, що стимулюють добавки, ретельне перемішування та ефективний окислювач, для того щоб максимально сприяти інтенсифікації гідробіоценозів, що становить активний мул, який поглинає забруднення. Даний метод досить ефективний і застосовується тільки для доочищення стічних вод, оскільки високі концентрації компонентів-забруднювачів згубно впливають на життєдіяльність мікроорганізмів активного мулу.
Фізико-хімічна очистка стічних вод здійснюється в основному із застосуванням таких методів, як коагуляція, флотація і сорбція.
Коагуляція проводиться шляхом введення в стічні води коагулянтів (солей амонію, заліза, міді, шламових відходів та ін. ) для виникнення осадів у вигляді пластівців, які потім легко видаляються.
Флотація здійснюється шляхом пропускання крізь стічні води повітря, бульбашки якого захоплюють при русі вгору поверхнево-активні речовини, нафту, масла та інші забруднення і утворюють на поверхні води піноподібний шар, що легко видаляється. Даний спосіб очищення в промисловості застосовують рідко через його невелику ефективність, високу турбулентність потоків у флотаційній камері, що призводить до руйнування пластівцеподібних частинок і необхідності застосовування поверхнево-активних речовин.
Сорбція заснована на здатності деяких речовин, які називаються сорбентами (глини, активоване вугілля, цеоліти, силікагель, торф тощо), поглинати забруднення, в результаті чого відбувається вилучення із стічних вод не тільки шкідливих, але і цінних речовин. [4]
Серед сорбційних методів найбільшого розвитку отримали адсорбційні, які застосовують для глибокого очищення стічних вод від розчинених органічних і смолистих речовин перед біохімічною очисткою.
Перевагою методу є висока ефективність, можливість очищення стічних вод, що містять кілька речовин, а також рекуперація цих речовин, можливість очищати стічні води без внесення будь-яких вторинних забруднень, видалення біологічно незруйнованих речовин, надійність в умовах коливання об’ємів і складу стічних вод [5].
Адсорбційна очистка може бути регенеративною, тобто з витяганням речовини з адсорбенту і його утилізацією, і деструктивною, при якій витягнуті зі стічних вод речовини знищуються разом з адсорбентом. Ефективність адсорбційної очистки залежить від хімічної природи адсорбенту, величини адсорбційної поверхні і її доступності та від хімічної будови речовини.
В якості адсорбентів застосовують природні і штучні пористі матеріали. Використовують азбестовмісний матеріал – відход виробництва азбестових паперів та картону, пористий полімерний сорбент-сополімер стиролу дивінилбензолу, пінополіуретан, сорбент на основі базальтового волокна, дерев’яні стружки, тирсу, волокна, поміщені в пористі ткані оболонки, різні модифікації активного вугілля і інші адсорбенти. Сорбентами також можуть служити шлаки, кокс, зола.[6]
Адсорбція активованим вугіллям є одним з методів очищення промислових вод, що містять органічні домішки, і дозволяє добитися глибокої очистки води до норм ГДК шкідливих речовин у воді промислового, оборотного використання з одночасною утилізацією або деструктивним руйнуванням витягнутих речовин. Адсорбційна здатність активного вугілля є наслідком сильно розвиненою поверхні і пористості. Питома поверхня активного вугілля становить 400–900 м2/г; адсорбційні властивості в значній мірі залежить від структури, величини пор. [7]
Початковою сировиною для отримання активного вугілля служать практично будь-які матеріали, що містять вуглець: вугілля, торф, деревина та ін. Процес виготовлення високоякісних активних вугілля складний і тривалий, тому вартість їх достатньо висока. Це призводить до необхідності багаторазового використання активного вугілля або їх використання як вторинної сировини, наприклад, як добавку до шихти для коксування [8]. Тому широке застосування активного вугілля при очищенні стічних вод стримується економічними рамками.
Переваги даного методу – можливість проводити адсорбцію речовин з багатокомпонентних домішок, а також висока ефективність, особливо при очищенні стічних вод з низькою концентрацією забруднювача.
На наш погляд, найбільш перспективним напрямком сорбційної очистки стічних вод є методи з використанням сорбентів на основі мінеральних волокон. Необхідно відзначити, що дані сорбенти (скляне волокно, мінеральне волокно діабазової групи) одержують з дешевої сировини, тому вартість готового виробу невелика; забезпечують високу поглинаючу здатність при фільтрування аміачних стічних вод, що містять смолисті органічні речовини. Тому доцільність проведення подальших досліджень у цьому напрямку безсумнівна.
Апаратурне оформлення сорбційної очистки – загальноприйняті в хімічній технології – напорні фільтри з щільним шаром гранульованого активного вугілля, перед якими розташовані механічні фільтри. Двоступеневе фільтрування застосовується для глибокого очищення стічних вод, що містять емульговані і розчинені нафтопродукти. Наприклад, коалесцуючий фільтр, потім відстійник та фільтр з волокнистим адсорбентом.
Таким чином, оскільки дані методи можуть забезпечувати глибоке очищення стічних вод від високодисперсних і розчинених масел і смол, а вимоги до якості води, що очищують, стають все більш жорсткими, перспектива застосування цих методів зберігається.
3 ВЛАСТИВОСТІ І СТРУКТУРА ВОЛОКНИСТИХ МІНЕРАЛЬНИХ МАТЕРІАЛІВ
Найбільш ефективним методом очищення від органічних домішок є метод з використанням волокнистих матеріалів, які бувають природного і штучного походження. Серед волокон-сорбентів штучного походження існує багато різновидів, які використовують в якості як коалесцуючого, так і фільтруючого матеріалу (волокнистий поліпропілен, поліетилен, волокнистий фторопласт та ін.) Однак, наведені матеріали застосовуються для очищення стічних вод від нафтопродуктів, які за своїм складом відрізняються від смолистої фази стічних вод в коксохімії. Кам'яновугільні масла складаються в основному з ароматичних вуглеводнів, у той час як звичайні нафтопродукти – це суміш переважно аліфатичних, ациклічних і в меншій мірі ароматичних вуглеводнів [8] .
Можна відзначити, що для поглинаючої (фільтруючої) здібності волокон має вирішальне значення діаметр волокна, інертність і спорідненість матеріалу виробу до забруднюючих компонентів. Виходячи з даних вимог, найбільш підходить для очищення від смолистої фази коксохімічних стічних вод мінеральні волокна, докладний опис властивостей і характеристик яких наводиться нижче.
Мінеральне волокно виготовляють на основі природних матеріалів. Обраний матеріал являє собою полімер з поздовжніми зв'язками, який може бути використаний для тонкої очистки стічних вод в коксохімічної промисловості від смолистих органічних речовин.
Скляне волокно (СВ) – волокнистий матеріал, який одержують на основі силікатних розплавів гірських пород, металургійних шлаків та інших промислових відходів або їх сумішей. Мінеральна вата складається з найтонших волокон, що взаємно переплітаються і знаходяться в склоподібному стані, і неволокнистих включень у вигляді крапель застиглого розплаву.
Для виробництва скляних волокон змішують пісок, соду, вапняки, деякі хімічні добавки і отримують шихту. Розплавлена шихта в процесі виробництва стає склом. На наступному етапі розплав скла роздмухують парою, повітрям, на центрифузі або іншими методами, одержуючи волокно. Застосовують для виготовлення тепло-, звукоізоляційних, звуковбирних виробів, а також для фільтрації.
Мінеральне волокно діабазової групи (МВД) – це шар штапельних волокон, переплутаних і скріплених між собою у вигляді полотна. Отримують з розплаву власне базальту, а також деяких близьких до нього порід без будь-яких доповнень у вигляді синтетичних або мінеральних речовин.
Роботи з отримання волокон із вивержених гірських порід (базальтів, амфіболіти, порфіритів тощо) перспективні. По-перше, ці породи широко поширені на територіях України та країн СНД. По-друге, на відміну від шихт, які використовуються для виробництва скляних волокон, основні гірські породи не вимагають дефіцитних добавок бору, соди, сульфату, глинозему та ін. і виключають процеси приготування шихти. Плавка порід відбувається без стадії силікатоутворення.
У таблиці 3.1 наведені основні властивості і характеристики скляного волокна та мінерального волокна діабазової групи.
Таблиця 3.1 – Характеристика СВ и МВД [9]
Показники | Типи волокон | |
СВ | МВД | |
Удавана щільність, кг/м3 | 12–25 | 15–23 |
Середній діаметр волокна, мкм, не більше | 4–12 | 1–3 |
Довжина волокон, мм | 15–50 | 40-70 |
Діапазон температур застосуван, оC | -60…+250 | -250…+700 |
Коефіцієнт теплопровідності, Вт/м оC | 0,038..0,042 | 0,031..0,034 |
Хімічна стійкість (втрата ваги) ,% | ||
в воді | 6.2 | 1,6 |
в лужному середовищі | 6,0 | 2,75 |
в кислотному середовищі | 38,9 | 2,2 |
Волокнисті матеріали знаходяться в досить широкому діапазоні температур застосування і мають високу хімічну стійкість до води, сольових розчинів, кислотних і лужних середовищ; мають велику поглинаючу поверхню, яка обумовлює високі адсорбційні властивості. Тому робота була спрямована на дослідження можливості застосування даного класу матеріалів для очищення стічних вод від органічних домішок.
4 ФІЗИКО-ХІМІЧНІ ОСНОВИ СОРБЦІЙНИХ МЕТОДІВ ОЧИЩЕННЯ
Адсорбція – це дифузійний процес, що протікає самодовільно і супроводжується зменшенням запасу енергії Гіббса системи, в результаті якого відбувається концентрування розчиненої речовини (адсорбенту) або розчинника (адсорбтиву) на поверхні твердого тіла (адсорбенту). В загальному вигляді процес адсорбції описується рівнянням Гіббса. Згідно сучасним уявленням, енергія адсорбції – це різниця енергій взаємодії з адсорбентом і сусідніми молекулами в адсорбційному шарі.
За типом сил, в результаті яких здійснюється адсорбція, зазначений процес можна розділити на дві групи: фізична адсорбція і процес зв'язування речовини за рахунок хімічних взаємодій - хемосорбція. Фізична адсорбція викликається силами молекулярної взаємодії. Фізичну і хімічну адсорбцію можна розрізнити за теплотою адсорбції. Теплота фізичної адсорбції у порівнянні з теплотою конденсації речовин і не перевищує 80–120 кДж/моль. ТТеплота хемосорбції одного моля речовини досягає декількох сотень кілоджоулів.
Однією з основних характеристик адсорбентів і адсорбційних взаємодій є ізотерма адсорбції.
Найпростіше рівняння ізотерми Генрі, застосовується при мінімальних ступенях заповнення поверхні адсорбатом при малих тисках:
де а – величина адсорбції;
к – константа Генрі;
р – тиск.
Для мономолекулярної адсорбції застосовується рівняння Ленгмюра:
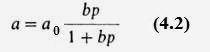
де а – кількість речовини, адсорбованої при тиску р;
а0 – гранична концентрація поглиненого компоненту;
в – коефіцієнт, що залежить від температури.
При наявності взаємодії адсорбованих комплектів між собою використовують рівняння Гугенгейма:
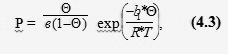
где Θ= а/а0;
в – – константа, що характеризує взаємодію адсорбат – адсорбент;
в1 – константа, що характеризує взаємодію адсорбат –адсорбент в моношарі.
Надалі Брунауер, Еммет і Теллер обгрунтували теорію полімолекулярної адсорбції:

де V – ооб'єм речовини, адсорбованої одиницею маси адсорбенту, м3⁄2 ;
Vm – об'єм речовини, адсорбованої одиницею маси адсорбенту, коли вся поверхня покрита моношаром.
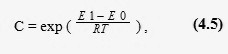
где E1 – теплота адсорбції в першому шарі, кДж;
E0 – теплота конденсації, кДж.
Необхідно зазначити, що застосування рівняння може бути коректним при відсутності мікробів.
Широке поширення в практичних розрахунках по адсорбції в області середніх насичень отримало рівняння Фрейдліха:
где а – кількість адсорбованої речовини;
р – тиск адсорбтиву;
r и n – постійні величини.
На процес адсорбції впливає: фізико-хімічні властивості матеріалу насадки фільтра, які полягають у здатності утримувати і накопичувати на своїй поверхні смолисті речовини за рахунок адгезійної взаємодії; фізико-хімічні властивості води, які проявляються в зміні гідрофобних властивостей поверхні насадки; гідродинамічному режимі руху емульсії в насадці.
5 ДОСЛІДЖЕННЯ СОРБЦІЙНИХ ВЛАСТИВОСТЕЙ МІНЕРАЛЬНИХ ВОЛОКОН ПО ВІДНОШЕННЮ ДО СМОЛ І МАСЕЛ
На наш погляд, найбільш перспективним напрямком сорбційної очистки стічних вод є методи з використанням волокнистих мінеральних матеріалів. Для дослідження були обрані наступні мінеральні волокна – скляне волокно (СВ) і мінеральне волокно діабазової групи (МВД).
У лабораторних умовах досліджували сорбційну ємність (СЄ) мінеральних волокон в статичних умовах, для чого штучно готувалися емульсії з різною концентрацією смолистої фази.
До водосмоляної емульсії (100 мл) з різним вмістом смол і масел (0,1-10%) поміщали 1г досліджуваного волокна. Витримували до повного насичення, після чого визначали залишковий вміст смолистих речовин у водній фазі методом екстракції 4-х хлористим вуглецем з наступним колориметруванням. Результати досліджень наведені в таблиці 5.1.
Таблиця 5.1 – Результати дослідження процесу сорбції смолистих речовин на мінеральних волокнах
Вміст смолистої фази, % | Залишковий вміст смолистих речовин, мг/л | СЄ, мг смол. реч./1 г волокна | Ступінь поглинання смолистих речовин волокном, % | |||
СВ | МВД | СВ | МВД | СВ | МВД | |
0,1 | - | 19 | - | 49 | - | 98,0 |
0,2 | - | 20 | - | 99 | - | 98,9 |
0,4 | 49 | - | 198 | - | 98,8 | - |
0,5 | - | 31 | - | 248 | - | 99,4 |
0,6 | 41 | - | 298 | - | 99,3 | - |
1 | 63 | 57 | 497 | 497 | 99,4 | 99,4 |
2 | 62 | - | 997 | - | 99,7 | - |
3 | - | 76 | - | 1496 | - | 99,8 |
5 | - | 144 | - | 2493 | - | 99,7 |
6 | 105 | - | 2995 | - | 99,8 | - |
7 | - | 175 | - | 3492 | - | 99,8 |
10 | 116 | 191 | 4995 | 4991 | 99,9 | 99,8 |
За отриманими експериментальними даними побудовані графіки залежності залишкового вмісту смолистих речовин і СЄ від змісту смолистих речовин в емульсіях спочатку до експерименту і представлені на рисунках 5.1 і 5.2 відповідно.
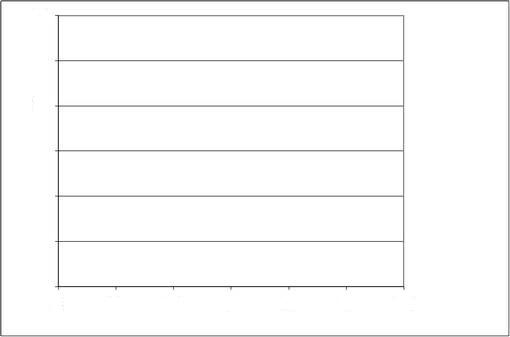
Рисунок 5.1 – Графік залежності залишкового вмісту смолистих речовин від їх вмісту в емульсії до експерименту (0,1 - 10%)
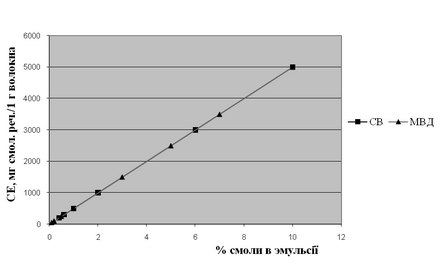
Рисунок 5.2 – Графік залежності СЄ від вмісту смолистих речовин в емульсії
6 АНАЛІЗ РЕЗУЛЬТАТІВ ЕКСПЕРИМЕНТАЛЬНИХ ДОСЛІДЖЕНЬ
Аналіз результатів показав, що скляне волокно має більш високу сорбційну ємність (рис.5.1), оскільки залишковий вміст смолистих речовин після проведення експерименту нижчий, ніж у МВД. Для низькоконцентрованих емульсій (0,1–1%) эця різниця незначна, а для висококонцентрованих ( 1 – 10% ) – набуває суттєві відмінності. Наприклад, для 10%-ної емульсії ця різниця становить 75 мг/л.
Побудована залежність величини СЄ від вмісту смолистих речовин (рис.5.2), яка підпорядковується рівнянню Фрейдліха для аналітичного опису ізотерми адсорбції, при м = 1 (4.3). Величина сорбційної ємності має досить високі чисельні значення для відповідної концентрації смолистих речовин в емульсії.
Також розрахована величина поглинання смолистих речовин при використанні обраних сорбентів (табл. 5.1), чисельні значення якої при різному вмісті смолистих речовин в емульсії високе і складає 99,3 – 99,9 %. Це говорить про перспективність їх використання для ефективного очищення технологічних і стічних аміачних вод коксохімічного виробництва. Таким чином, використовувані сорбенти ефективні для подальшого застосування в якості фільтруючого завантаження від смолистих речовин. Тому доцільно проведення подальших досліджень у цьому напрямку.
ВИСНОВКИ
В роботі розглянуті джерела виникнення і характеристика стічних вод коксохімічного виробництва, вивчені властивості і структура мінеральних сорбентів, наведені фізико-хімічні основи процесу адсорбції.
На основі аналітичного огляду методів очищення стічних вод від органічних домішок був зроблений висновок про те, що найбільш економічно вигідним і ефективним є використання для цієї мети методу з застосуванням мінеральних волокнистих сорбентів.
У лабораторних умовах проведено 2 серії експериментів на штучно приготованих емульсіях. В результаті чого були отримані ізотерми адсорбції для двох матеріалів (скляне волокно і мінеральне волокно діабазової групи); визначена сорбційна ємність та проведено аналіз експериментальних досліджень. Перевагами обраних сорбентів є високий ступінь поглинання смолистих речовин і низька вартість мінеральних волокон. Досить велике значення величини сорбційної ємності даних сорбентів в умовах експерименту (10% емульсія – 4991,4 и 4995,2 мг см. . речовин/1 г волокна для МВД і СВ відповідно) також говорить про перспективність їх використання з подальшою оптимізацією параметрів процесу для більш високої ефективності роботи очисної установки з використанням мінерального волокна.
ПЕРЕЛІК ПОСИЛАНЬ
- Лазорин С.Н., Папков Г.И., Литвиненко В.И.Обезвреживание отходов коксохимических заводов / C.Н. Лазорин, Г.И. Папков, В.И. Литвиненко.– М.: Металлургия. – 1977.– 241 с.
- Крутько І.Г., Пульникова Ю.В. Визначення характеристик кам’яновугильних водних емульсій високотемпературного піролізу вугільної шихти // Углехимический журнал – Харьков: УХИН – 2011. – № 1–2. – с. 75–81.
- Зубахин Н.П., Клушин В.Н., Дмитриева Д.А., Зелькова Е.В. Оценка концентратов ископаемых углей // журнал Кокс и Химия – M.: Металлургиздат – 2011. – № 4.– с. 39.
- Чернявский А.Ю. Способы очистки сточных вод [электронный ресурс]. – Режим доступа:
http://www.isgod.ru - Кульский Л.А., Даль В.В., Кудельская Г.А., Кузнецова Л.Г. Методы очистки промышленных сточных вод / Л.А. Кульский, В.В. Даль, Г.А. Кудельская , Л.Г Кузнецова.– К.: УКР НИИ НТИ. – 1978. – 288 с.
- Кузубова Л.И., Морозов С.В. Очистка нефтесодержащих сточных вод / Л.И. Кузубова, С.В. Морозов. – Новосибирск.: ГПНТБ СО РАН. – 1992. – 72 c.
- Проскуряков В.А., Шмидт Л.И. Очистка сточных вод в химической промышленности / В.А. Проскуряков, Л.И. Шмидт. – Л.: Химия. – 1977.– 241с.
- Небольсина Л.А., Передерий О.Г., Харлампович Г.Д., Дербышева Е.К. Состояние перспективы очистки сточных вод коксохимических предприятий от эмульгированных масел // журнал Кокс и Химия – M.: Металлургиздат – 1985.– № 10.– с. 28.
- Сравнительные характеристики стеклянных, минеральных и базальтовых волокон и материалов на их основе [электронный ресурс]. – Режим доступа: http://www.proxima.com.ua