Реферат за темою випускної роботи
Зміст
- Вступ, обгрунтування актуальності теми
- 1. Мета та задачі дослідження
- 2. Передбачувана наукова новизна
- 3. Практичне значення
- 4. Аналіз сучасного стану питання досліджень
- 4.1 Аналіз важкооброблюваних матеріалів
- 4.2 Аналіз остаточних методів обробки важкооброблюваних матеріалів
- Висновки
- Перелік посилань
Вступ, обгрунтування актуальності теми
Випуск конкурентоспроможної машинобудівної продукції в умовах ринкових відносин можливий за рахунок використання матеріалів, які відповідають рівню високих технологій. Сучасна промисловість використовує матеріали, які мають високу міцність, хімічну стійкість в агресивних середовищах, жароміцність, а найчастіше й комплекс цих властивостей. У процесі обробки таких матеріалів, що мають низьку теплопровідність і підвищені характеристики міцності, виникають висока температура та великий тиск на ріжучі кромки інструментів [1]. Ефективна абразивна обробка важкооброблюваних матеріалів (ВОМ) можлива за рахунок застосування різального інструменту з надтвердих матеріалів. Це пов'язано з тим, що в структурі сучасних ВОМ і сплавів знаходяться тверді карбіди та нітриди металів, фізико-механічні властивості яких наближені до властивостей абразивних матеріалів. Такі вироби обробляються лише інструментом з алмазу і кубічного нітриду бору [2].
Тож розробка технологічного забезпечення процесу шліфування виробів з ВОМ є актуальною темою для дослідження. Не достатньо вивченим залишається процес шліфування сталі Гадфільда, яка відрізняється високим рівнем зносостійкості.
1. Мета та задачі дослідження
Метою магістерської роботи є забезпечення заданої якості обробки поверхонь деталей за рахунок раціональних режимів обробки та раціонального вибору характеристики шліфувального інструменту.
Для досягнення мети поставлено наступні задачі:
- Виконати аналіз ВОМ з точки зору оброблюваності шліфуванням.
- Навести аналіз режимів обробки та шліфувального інструменту.
- Виконати імітаційне моделювання поведінки одиничного зерна в зв'язці шліфувального круга.
- Запропонувати рекомендації щодо технологічного забезпечення при обробці ВОМ.
Об'єктом досліджень у даній роботі є шліфувальний інструмент, який використовується для обробки ВОМ.
Предметом дослідження є процес шліфування стали Гадфільда.
2. Передбачувана наукова новизна
На підставі виконаного аналізу та перегляду досліджень з даної теми розроблено імітаційне моделювання поведінки одиничного зерна в зв'язці при шліфуванні стали Гадфільда.
3. Практичне значення
У даній роботі розроблено рекомендації щодо технологічної обробки сталі Гадфільда.
4. Аналіз сучасного стану питання досліджень
4.1 Аналіз важкооброблюваних матеріалів
Існує багато класифікацій ВОМ. Згідно з однією з них усі матеріали розділені на вісім груп, пізніше класифікація була розширена за рахунок додавання тугоплавких металів і склопластиків.
До групи I класифікації віднесено теплостійкі сталі (34ХНМ, Х6СМ тощо), які експлуатуються при температурі до 500 °С. Основний легуючий елемент – хром (до 6%), а також домішки нікелю (до 3%) та кремнію.
До групи II віднесені сталі з вмістом хрому більше 12% і невеликою кількістю інших легуючих елементів. Це високоміцні сталі (30X13, 14Х17Н2, 09Х16Н4Б), які зберігають свої властивості при температурі до 500-600 °С і коли є вплив не агресивних середовищ.
Сталі групи III за складом хромонікелеві. Типовий представник цієї групи – сталь 12Х18Н10Т.
Сталі групи IV за складом теж хромонікелеві з домішками інших легуючих елементів (45Х14Н14В2М, 10Х11Н23ТЗМР та ін.). Це жароміцні, жаростійкі і кислотостійкі матеріали.
Сталі групи V – жароміцні на нікелевій і залізонікелевій основі (ХН70Ю, ХН67МВТЮ, ХН77ТЮР та ін.). Це одні з важкооброблюваних матеріалів.
Жароміцні ливарні сплави групи VI (ЖС6-К, ХН67ВМТЮЛ) також являють собою високолеговані матеріали на нікелевій основі. Їх оброблюваність гірша ніж у матеріалів попередньої групи.
Матеріали групи VII – це сплави на основі титану. Оброблюваність деталей з титанових сплавів при шліфуванні дуже низька.
До групи VIII входять низьколеговані високоміцні сталі (28ХЗСНМВФА, 42Х2ГСНМ та ін.). У відпаленому стані їх оброблюваність знаходиться на рівні оброблюваності звичайних конструкційних сталей, але після термообробки вона стрімко знижується.
У IX групу матеріалів об'єднані тугоплавкі метали і сплави. За оброблюваністю шліфуванням їх можна поділити на три групи. Найбільш ВОМ – вольфрам і молібден, сплави на основі берилію (відрізняються крихкістю та токсичністю, сприяють абразивному зносу інструменту) і сплави на основі танталу і ніобію (мають задовільну оброблюваність).
Групу X складають різного роду неметалеві матеріали (склопластики, слюда). Більшість деталей з цих матеріалів легко обробляються, але при шліфуванні виникають певні труднощі [1].
Гуревич Я.Л. наводить й іншу класифікацію для ВОМ:
I група. Сталі, які застосовуються для виготовлення впускних і випускних клапанів двигунів, лопаток і дисків турбін, що працюють при температурі до 500-600 °С.
II група. Сталі, які застосовуються, переважно, як нержавіючі сталі для виготовлення арматури, дисків і лопаток турбін, які працюють при температурі до 530-580 °С (1X13, 2X13, 15Х12ВМФ, ЕІ961 тощо), хірургічного інструменту, шарикопідшипників (3X13, 4X13) та інших деталей з високою корозійною стійкістю.
III група. Сталі цієї групи мають широке розповсюдження як кислототривкі, нержавіючі і жароміцні матеріали.
IV група. Високолеговані сталі аустенітного класу, які застосовуються для виготовлення дисків і лопаток газових турбін, кільцевих деталей і деталей для кріплення.
V група. Жароміцні сплави, які зазнають деформаційний вплив, на нікелевій і залізонікелевій основах. До них відносяться сплави ЕІ437, ЕІ437А, ЕІ437Б і високолеговані сплави ЕІ617, ЕІ445Р та інші.
VI група. Ливарні сплави, які застосовуються для виготовлення деталей, що працюють в умовах великих навантажень при температурі до 900-1000 °С.
VII група. Сплави на титановій основі (ВТ14, ВТ15, ВТ3-1, ВТ22 та ін.).
До групи VIII віднесено високоміцні сталі (28Х3СНМФА, 30Х2ГСН2ВМ, 35Х5МСФА, 42Х2ГСНМ, Н18К9М5Т) [3].
В останні роки виготовляються різальні інструменти, з безвольфрамовими твердими сплавами (БВТС) на основі карбідів або карбонітрідів титану та на нікель-молібденової зв'язці. У порівнянні з твердими сплавами, які містять вольфрам, БВТС мають менший коефіцієнт тертя та більшу зносостійкість.
Оскільки при обробці БВТС виникають великі значення складових сил різання й ефективної потужності шліфування, то існує можливість появи тріщин і сколів на поверхні що обробляється. При шліфуванні БВТС кругами на металевих та керамічних зв'язках спостерігається засалювання та згладжування рельєфу робочої поверхні круга. Тому більш доцільно шліфувати такі сплави алмазними кругами на органічних зв'язках [2].
Ванадієві штампові сталі Х12Ф4М, Х12Ф1, 9Х5Ф, Х6ВФ, Х6Ф4М, Х6В3ФМ, Х3Ф8, Х3Ф12 відносяться до класу ВОМ. Їх важка оброблюваність абразивними кругами при шліфуванні пов'язана з наявністю в їх структурі твердих карбідів хрому (HV 15 ГПа), вольфраму та молібдену (HV 16,5 ГПа), твердість яких порівнянна з твердістю електрокорунду (HV 18,9-23,5 ГПа) [4].
Важка оброблюваність шліфуванням нових марок швидкорізальних сталей (у порівнянні з Р18) пояснюється, як і у ванадієвих штампових сталей, наявністю в їх структурі твердих карбідів хрому, вольфраму, молібдену та ванадію. У цьому випадку зерна з білого електрокорунду, який зазвичай застосовується в абразивних кругах при шліфуванні інструменту та швидкорізальних сталей і має мікротвердість 20-21 ГПа, не в змозі конкурувати з карбідами хрому, ванадію тощо. Крім того, швидке затуплення кругів викликає додаткове підвищення температури в зоні шліфування. Відбувається утворення залишкового аустеніту, який створює додаткові напруження, що може призвести до утворення тріщин після шліфування [2].
ВОМ мають високу пластичність саме тому при їх обробці явище предеформування поверхневого шару виявляється в більшій мірі, ніж при обробці конструкційних вуглецевих сталей. При нерівномірному протіканні процесу пластичного деформування висока зміцненість оброблюваного матеріалу може призвести до збільшення вібрацій. Тому при обробці подібних матеріалів необхідно, щоб технологічна система мала високу жорсткість [5].
Одним з представників ВОМ є сталь Гадфільда. Вона характеризується високим рівнем зносостійкості, який зумовлений її здатністю до надзвичайно інтенсивного зміцнення при пластичній деформації, що відбувається в зоні фрикційного контакту [6]. Позначення марки сталі – 110Г13Л.
Хімічний склад сталі 110Г13Л згідно з ГОСТ 977-88: C вуглець 0,9-1,5%; Si кремній 0,3-1,00%; Mn марганець 11,5-15%; Ni нікель не більше 1%; Cr хром не більше 1%; S сірка не більше 0,05%; P фосфор не більше 0,12%. Призначена для виготовлення деталей, що працюють на знос в умовах тертя, тиску та ударних навантажень, коли відбувається самозміцнення (наклеп) сталі, а її міцність і зносостійкість значно зростає.
Сталь 110Г13Л має наступні механічні властивості:
- границя міцності (тимчасовий опір розриву) σв = 800-900 МПа;
- умовна межа плинності σ0,2 = 310-350 МПа;
- відносне подовження (пластичність) δ = 15-20%;
- відносне звуження ψ = 50-30%;
- модуль пружності Е = 200000 МПа;
- модуль зсуву G = 78000 МПа;
- густина 7820 кг/м³ [7].
Ця сталь так само має й особливі властивості. При охолодженні в звичайних умовах вона крихка, як скло; після швидкого охолодження у воді від 1000 °С виявляється виняткова тягучість і в'язкість.
Висока в'язкість і одночасно здатність цієї сталі самозміцнюватися надають їй стійкість проти зносу. При великих навантаженнях висока в'язкість призводить до плинності матеріалу, що в свою чергу надає сталі самозміцнення. Самозміцнення підвищує опір сталі зносу.
Виробництво сталі з великою кількістю домішок марганцю зводиться до легування низьковуглецевої сталі марганцем. Це найбільш просто досягається шляхом змішування низьковуглецевої сталі з розплавленим феромарганцем, витрата якого становить при цьому близько 20% маси сталі [8].
Завдяки високій твердості і зносостійкості сталь Гадфільда швидко завоювала визнання в промисловому світі: її почали використовувати для виготовлення тих деталей, які в процесі експлуатації постійно піддаються сильним ударам і зазвичай швидко виходять з ладу через стирання. Такі, наприклад, рейкові хрестовини, щоки та плити подрібнювача, кулі для кульових млинів, зуби і передні стінки ковшів екскаваторів, гусеничні траки і т.д. [9].
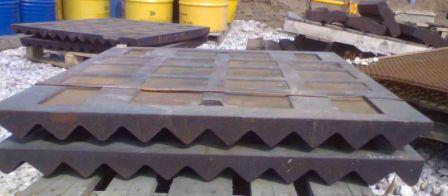
Рисунок 1 – Плити зі сталі 110Г13Л
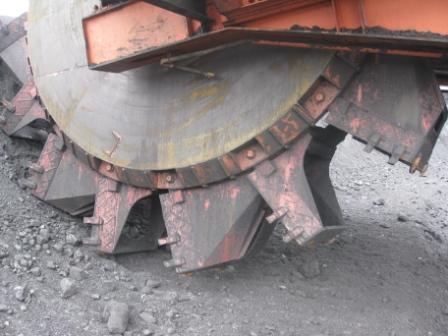
Рисунок 2 – Зуб ковша екскаватора зі сталі 110Г13Л
4.2 Аналіз остаточних методів обробки важкооброблюваних матеріалів
Існує безліч різноманітних методів остаточної обробки матеріалів, одним з них є шліфування.
Шліфування – один з видів обробки металів різанням. При шліфуванні припуск знімається абразивними інструментами – шліфувальними кругами. Шліфувальний круг являє собою пористе тіло, що складається з великої кількості дрібних зерен [10]. Шліфуванням можна обробляти практично будь-які матеріали тому, що твердість абразиву (НВ = 2200-3100) і алмазу (НВ = 7000) є дуже великою. Для порівняння слід відзначити, що твердість твердого сплаву НВ = 1300, цементиту НВ = 2000, загартованої сталі НВ = 600-700 [11].
Для операцій шліфування ВОМ стрімко зростають експлуатаційні вимоги до абразивних інструментів. Звичайні засоби та методи поліпшення показників операцій шліфування (застосування СОТС, зміна режимів різання, характеристика інструменту і т. д.) не завжди є достатньо ефективними.
Зараз багато уваги приділяється пошуку шляхів підвищення ріжучої здатності абразивного інструменту. Зокрема поширені способи, засновані на введення в зону різання речовин, які поліпшують оброблюваність матеріалів, використання не різальних елементів абразивного інструменту – зв'язки та пор. Різновиди цих способів об'єднані поняттям імпрегнування
(просочення). Імпрегнування шліфувальних кругів не має негативного впливу на їх фізико-механічні властивості, суттєво покращує їх різальну здатність [12].
Нині високопродуктивна обробка ванадієвих швидкорізальних сталей здійснюється за допомогою алмазного шліфування кругами на металевій зв'язці, після процесу правки електроерозійним методом, з підтриманням різальної здатності робочої поверхні круга в процесі обробки впливом електроерозії. Відомо також шліфування цих сталей ельборовими кругами на металевій зв'язці, що правлені абразивним способом [13]. При шліфуванні втрата різальної здатності круга відбувається в результаті випадіння найбільш виступаючих зерен, засалювання субмікрорельефа контактних площадок зерен і простору між зернами продуктами обробки, а також контактування зв'язки з оброблюваним матеріалом у результаті руйнування зерен. При шліфуванні кругами, після електроерозійної правки, зерна виступають зі зв'язки принаймні на одну третину діаметра зерна відповідної зернистості, що може призвести до їх руйнування [14].
Електроерозійна правка круга забезпечує його велику різальну здатність як на початку обробки, так і на протязі всього процесу шліфування. Пояснюється це тим, що в процесі електроерозійної правки електричні розряди впливають тільки на зв'язку, не руйнуючи зерен, як під час абразивної правки, завдяки чому зерна виступають із зв'язки і беруть участь в процесі різання з перших хвилин шліфування [13].
Одним із шляхів підвищення продуктивності при механічній обробці є впровадження у виробництво глибинного шліфування, яке в більшості випадків більш ефективно, ніж обробка лезійним інструментом, особливо при виготовленні деталей з жароміцних і титанових сплавів, корозійностійких, високолегованих та інструментальних сталей [15].
Глибинне шліфування ще називають однопрохідним. Цей процес полягає в тому, що весь припуск на обробку знімають за один прохід круга. Глибинне шліфування відбувається на швидкості круга 30-40 м/с і застосовується при звичайному чи електролітичному алмазному заточуванні твердосплавних ріжучих інструментів, а також при плоскому шліфуванні деталей на верстатах з вертикальним і горизонтальним розташуванням шпинделя [16].
Глибинне шліфування характеризується значними поперечними подачами і малими поздовжніми подачами.
У цьому випадку круг правиться на конус і весь припуск (0,1 ... 0,4 мм) знімається за один прохід (рис. 3). Здійснювати глибинне шліфування можливо при наявності коротких жорстких деталей [17].
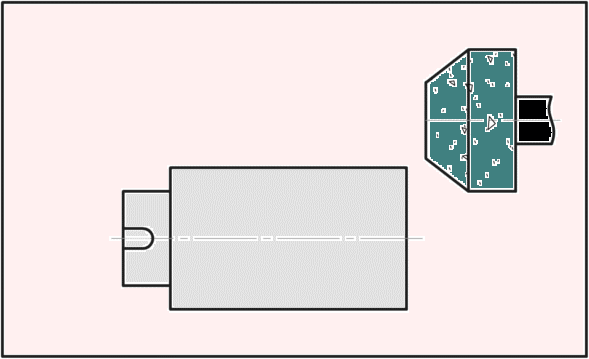
Рисунок 3 – Схема глибинного шліфування
(анімація: 8 кадрів, 10 циклів повторення, розмір анімації - 48 кілобайт)
Встановлено, що глибинне шліфування дозволяє при заданій якості обробки істотно підвищити продуктивність і знизити трудомісткість і вартість операції [16].
Збільшення швидкості різання при глибинному шліфуванні є суттєвим резервом підвищення продуктивності обробки. Особливо це важливо при обробці найбільш ВОМ – жароміцних сплавів на нікелевій основі [18].
При глибинному шліфуванні до системи охолодження висувають такі вимоги: висока змащувальна, миюча і проникаюча здатність мастильно-охолоджувальної рідини (МОР), найбільш повне відведення рідиною шламу із зони шліфування, високий рівень очищення МОР під час її подачі в зону обробки для подолання повітряного потоку, що виникає навколо шліфувального круга. На рис. 4 показані схеми подачі МОР при плоскому глибинному врізному шліфуванні.
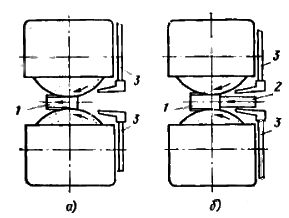
Рисунок 4 – Схеми подачі МОР у зону шліфування: а - неефективна подача, б - ефективна подача (1 - деталь, 2 - направляючі пристрої, 3 - сопла)
Результати впровадження глибинного шліфування довели, що верстати повинні мати електродвигуни шліфувальних шпинделів потужністю не менш ніж 10 кВт; великий діапазон малих швидкостей повздовжнього переміщення столу; досконалу систему подачі МОР в зону шліфування; автоматичний цикл правки круга і систему компенсації зносу шліфувального кругу [15].
На сучасному етапі технології одним з найважливіших шляхів вирішення проблеми обробки деталей з ВОМ є шліфування струмопровідними алмазними і абразивними кругами. Це забезпечує значний приріст продуктивності праці, зниження витрат і підвищення ефективності виробництва при досягненні високих експлуатаційних властивостей оброблених поверхонь.
Електрохімічне шліфування алмазними або абразивними кругами на струмопровідних металевих зв'язках являє собою комбінований процес, при якому матеріал знімається в результаті процесів, що протікають одночасно: анодного розчинення, механічного різання алмазними або абразивними зернами й електроерозійної дії.
При електрохімічному шліфуванні колами прямого профілю з поперечною подачею зона контакту круга з деталлю складається з двох ділянок. На ділянці (рис. 5,а), ширина якої дорівнює величині поперечної подачі Sпоп, умови шліфування визначаються тільки характеристикою інструменту та режимами обробки, а величина зазору, що визначає електричний опір ланцюга на даній ділянці, залежить переважно від зернистості абразиву та стану різальної поверхні круга. Для даних умов шліфування опір в зазорі на даній ділянці мінімальний, а щільність струму – максимальна. На останній ділянці величина зазору максимальна, опір ланцюга в зазорі також максимальний, а щільність струму має найменше для даних умов обробки значення (рис. 5,б). Таким чином, на висоті кола існують ділянки з різними щільностями тока.
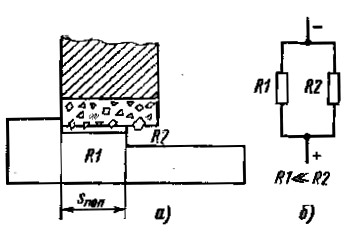
Рисунок 5 – Схема електричного опору на різних ділянках зони контакту під час електрохімічного шліфування периферією круга
Для шліфування деталей з твердих сплавів застосовуються тільки алмазні круги, а з жароміцних сплавів, нержавіючих і конструкційних сталей – алмазні та рідше абразивні круги на металевих зв'язках.
Використання абразивних кругів на металевій зв'язці можливо при шліфуванні з безперервною електрохімічної правкою круга. Перевагою цього методу шліфування є відсутність тертя зв'язки з оброблюваною поверхнею. Для цієї ж мети іноді використовують реверсивне джерело живлення, що дає зворотню півхвилю. Відомо використання електронейтрального абразивного інструменту, в якому електрохімічний та механічний процеси рознесено в просторі. Електрохімічне знімання з поверхні деталі здійснюється в цьому випадку додатковим кругом. Всі різновиди методів обробки з використанням анодних процесів можуть дуже ефективно використовуватися в промисловості [19].
Висновки
Підсумовуючи вищезазначене, необхідно відзначити, що високопродуктивна обробка ВОМ з досягненням необхідної якості деталі, є важливим завданням для досліджень. Велика розмаїтість ВОМ передбачає безліч способів їх обробки, але, як правило, як найбільш високопродуктивний і остаточний спосіб обробки таких виробів застосовується шліфування.
Перш за все, виходячи з властивостей оброблюваного матеріалу, форми і якості оброблюваної поверхні необхідно обрати характеристику і форму шліфувального круга. Так як в процесі шліфування ВОМ відбувається інтенсивне тепловиділення, що може негативно позначатися на характеристиках міцності оброблюваної поверхні, й утворення продуктів зносу заготовки та шліфувального круга – шламу, що може мати негативний вплив на якість обробленої поверхні, необхідна наявність більш досконалої системи СОТС.
Внаслідок високої твердості ВОМ, характер зносу ріжучої поверхні шліфувального круга відрізняється від зносу при шліфуванні вуглецевої сталі. Твердість матеріалу зерен шліфувального круга порівнянна з твердістю оброблюваної поверхні. Тому для обробки таких матеріалів використовують карбіди кремнію, штучні або природні алмази.
Багато дослідників пропонують управляти станом робочої поверхні шліфувального круга за допомогою його правки за для запобігання негативного впливу зростаючих сил різання в процесі шліфування.
Таким чином, процес шліфування ВОМ передбачає наявність більш досконалої системи СОТС і пристрою, який дозволяє управляти робочою поверхнею шліфувального круга. Такі пристрої відносяться до технологічного забезпечення процесу шліфування. Отже, тема Технологічне забезпечення процесу шліфування виробів з важкооброблюваних матеріалів
є актуальною і може бути обрана як тема магістерської роботи.
Перелік посилань
- Куприянов В.А. Мелкоразмерный инструмент для резания труднообрабатываемых материалов. – М.: Машиностроение, 1989. – 136 с.
- Прогрессивные методы абразивной обработки металлов / И.П. Захаренко, Ю.Я. Савченко, В.И. Лавриненко, С.М. Дегтяренко; Под ред. И.П. Захаренко. – К.: Техника, 1990. – 152 с.
- Режимы резания труднообрабатываемых материалов: Справочник / Я.Л. Гуревич, М.В. Горохов, В.И. Захаров и др. 2-е изд., перераб. и доп. – М.: Машиностроение, 1986. – 240 с.
- Основы проектирования и технология изготовления абразивного и алмазного инструмента. / Ю.М. Ковальчук, В.А. Букин, Б.А. Глаговский и др.; Под общей ред. Ю.М. Ковальчука – М.: Машиностроение, 1984. – 288 с.
- Труднообрабатываемые материалы [Электронный ресурс]. – Режим доступа: http://iron–lab.ru
- Иванов Ю.Ф., Алешина Е.А., Колубаев Е.А., Колубаев А.В., Сизова О.В., Громов В.Е. Закономерности формирования структуры поверхностного слоя стали Гадфильда при трении // Физ. мезомех. – 2006. – Т. 9. – № 6. – С. 83-90.
- Сталь 110Г13Л [Электронный ресурс]. – Режим доступа: http://www.bila.ru
- Производство высокомарганцовистой стали Гадфильда. Часть 1 [Электронный ресурс]. – Режим доступа: http://www.olvia.org
- Специи для стали [Электронный ресурс]. – Режим доступа: http://wolframpo.ru
- Лоскутов В.В. Шлифование металлов: Учебное пособие для профессинально-технических училищ. – М.: Машгиз, 1962. – 280 с.
- Ящерицын П.И., Еременко М.Л., Жигалко Н.И. Основы резания материалов и режущий инструмент. – Минск: Высшая школа, 1975. – 528 с.
- Никитин А.В. Шлифование труднообрабатываемых материалов импрегнированными кругами как способ их режущих свойств // Инструмент и технологии. – 2010. – №28. – Вып. 2 – С. 52-58.
- Матюха П.Г., Габитов В.В. Удельная себестоимость шлифования стали Р6М5Ф3 в зависимости от способа правки и электроэрозионных воздействий на рабочую поверхность кубонитового круга // Сверхтвердые материалы. – 2009. – № 5. – С. 63-69.
- Азарова Н.В., Матюха П.Г., Полтавец В.В. Удельная себестоимость процесса плоского шлифования ванадиевой быстрорежущей стали кругами из сверхтвердых материалов // Сверхтвердые материалы. – 2008. – № 2. – С. 65-71.
- Глубинное шлифование деталей из труднообрабатываемых материалов / С.С. Силин, В.А. Хрульков, А.В. Лобанов, Н.С. Рыкунов. – М.: Машиностроение, 1984. – 64 с.
- Абразивная и алмазная обработка материалов: Справочник / Под ред. А.Н. Резникова. – М.: Машиностроение, 1977. – 391 с.
- Маслов Е.Н. Основы теории шлифования металлов. – М.: Машгиз, 1951. – 190 с.
- Макаров В.Ф., Семиколенных В.В., Чигодаев Н.Е., Веснин Г.В. Интенсификация лезвийной и абразивной обработки труднообрабатываемых материалов на основе физической оптимизации процессов резания // Инструмент и технологии. – 2004. – №17. – С. 129-135.
- Вайнберг Р.Р., Васильев В.Г. Электрохимическое шлифование токопроводящими абразивными и алмазными кругами. – М.: Машиностроение, 1976. – 32 с.
Зауваження! При написанні даного реферату магістерська робота ще не завершена. Остаточне завершення: грудень 2012 року. Повний текст роботи та матеріали по темі можуть бути отримані у автора або його керівника після вказаної дати.