Реферат по теме выпускной работы
Содержание
- Введение, обоснование актуальности темы
- 1. Цель и задачи исследования
- 2. Предполагаемая научная новизна
- 3. Практическое значение
- 4. Анализ современного состояния вопроса исследований
- 4.1 Анализ труднообрабатываемых материалов
- 4.2 Анализ окончательных методов обработки труднообрабатываемых материалов
- Выводы
- Список источников
Введение, обоснование актуальности темы
Выпуск конкурентоспособной машиностроительной продукции в условиях рыночных отношений возможен за счет использования материалов, отвечающих уровню высоких технологий. Современная промышленность использует материалы, обладающие высокой прочностью, химической стойкостью в агрессивных средах, жаропрочностью, а зачастую и комплексом этих свойств. В процессе обработки таких материалов, обладающих низкой теплопроводностью и повышенными прочностными характеристиками, возникают высокие температуры и большие давления на режущие кромки инструментов [1]. Эффективная абразивная обработка труднообрабатываемых материалов (ТОМ) возможна за счет применения режущего инструмента из сверхтвердых материалов. Это связано с тем, что в структуре современных ТОМ и сплавов находятся твердые карбиды и нитриды, физико-механические свойства которых приближаются к свойствам абразивных материалов. Такие изделия можно обрабатывать только инструментом из алмаза и кубического нитрида бора [2].
Поэтому разработка технологического обеспечения процесса шлифования изделий из ТОМ является актуальной темой для исследования. Мало изученным остается процесс шлифования стали Гадфильда, отличающейся высоким уровнем износостойкости.
1. Цель и задачи исследования
Целью магистерской работы является обеспечение заданного качества обработки поверхностей за счет рациональных режимов обработки и рационального выбора характеристики шлифовального инструмента.
Для достижения поставленной цели планируется выполнить следующие задачи:
- Выполнить анализ ТОМ с точки зрения шлифования.
- Привести анализ режимов обработки и шлифовального инструмента.
- Выполнить имитационное моделирование поведения единичного зерна в связке.
- Предложить рекомендации по технологическому обеспечению при обработке ТОМ.
Объектом исследований в данной работе является шлифовальный инструмент, используемый для обработки ТОМ.
Предметом исследования является процесс шлифования стали Гадфильда.
2. Предполагаемая научная новизна
На основе анализа и выполненного обзора исследований по данной теме разработано имитационное моделирование поведения единичного зерна в связке при шлифовании стали Гадфильда.
3. Практическое значение
В данной работе разработаны рекомендации по технологической обработке труднообрабатываемой стали Гадфильда.
4. Анализ современного состояния вопроса исследований
4.1 Анализ труднообрабатываемых материалов
Существует большое количество классификаций ТОМ. Согласно одной из них все материалы разбиты на восемь групп, позднее классификация была расширена за счет включения тугоплавких металлов и стеклопластиков.
В группу I классификации отнесены теплостойкие стали (34ХНМ, Х6СМ и др.), допускающие эксплуатацию при температуре 500 °С. Основной легирующий элемент – хром (до 6%), а также добавки никеля (до 3%) и кремния.
В группу II отнесены стали с содержанием хрома более 12% и небольшим количеством других легирующих элементов. Это высокопрочные стали (30X13, 14Х17Н2, 09Х16Н4Б), сохраняющие свои качества при температуре до 500-600 °С и при воздействии слабоагрессивных сред.
Стали группы III по составу хромоникелевые. Типичный представитель этой группы – сталь 12Х18Н10Т.
Стали группы IV по составу также хромоникелевые с добавкой других легирующих элементов (45Х14Н14В2М, 10Х11Н23ТЗМР и др.). Это жаропрочные, жаростойкие и кислотостойкие материалы.
Стали группы V – жаропрочные деформируемые на никелевой и железоникелевой основе (ХН70Ю, ХН67МВТЮ, ХН77ТЮР и др.). Это одни из самых труднообрабатываемых материалов.
Жаропрочные литейные сплавы группы VI (ЖС6-К, ХН67ВМТЮЛ и др.) также представляют собой высоколегированные материалы на никелевой основе. Их обрабатываемость хуже, чем материалов предыдущей группы.
Материалы группы VII – это сплавы на основе титана. Обрабатываемость деталей из титановых сплавов при шлифовании сильно снижена.
В группу VIII входят низколегированные высокопрочные стали (28ХЗСНМВФА, 42Х2ГСНМ и др.). В отожженном состоянии их обрабатываемость находится на уровне обрабатываемости обычных конструкционных сталей, после термообработки она резко падает.
В IX группу материалов объединены тугоплавкие металлы и сплавы. По обрабатываемости шлифованием их можно разделить на три группы. Наиболее ТОМ – вольфрам и молибден, сплавы на основе бериллия (отличаются хрупкостью и токсичностью, способствуют абразивному изнашиванию инструмента) и сплавы на основе тантала и ниобия (обладают вполне удовлетворительной обрабатываемостью).
Группу X составляют различного рода неметаллические материалы (стеклопластики, слюда). Большинство деталей из этих материалов легко обрабатываются, но при шлифовании возникают определенные трудности [1].
Гуревич Я.Л. приводит и другую классификацию для ТОМ:
I группа. Стали, применяемые для изготовления впускных и выпускных клапанов двигателей, лопаток и дисков турбин, работающих при температурах до 500-600 °С.
II группа. Стали, применяемые в основном как нержавеющие стали для изготовление арматуры, дисков и лопаток турбин, работающих при температурах до 530-580 °С (1X13, 2X13, 15Х12ВМФ, ЭИ961 и др.), хирургического инструмента, шарикоподшипников (3X13, 4X13) и других деталей с высокой коррозионной стойкостью.
III группа. Стали этой группы получили широкое распространение как кислотоупорные, нержавеющие и жаропрочные материалы.
IV группа. Сложнолегированные стали аустенитного класса, которые применяются для изготовления дисков и лопаток газовых турбин, кольцевых и крепежных деталей.
V группа. Жаропрочные деформируемые сплавы на никелевой и железоникелевой основах. К ним относятся сплавы ЭИ437, ЭИ437А, ЭИ437Б и сложнолегированные сплавы ЭИ617, ЭИ445Р и др.
VI группа. Литейные сплавы, применяемые для изготовления деталей, работающих в условиях больших нагрузок при температуре до 900-1000 °С.
VII группа. Сплавы на титановой основе (ВТ14, ВТ15, ВТ3-1, ВТ22 и др.).
К группе VIII отнесены высокопрочные стали (28Х3СНМФА, 30Х2ГСН2ВМ, 35Х5МСФА, 42Х2ГСНМ, Н18К9М5Т) [3].
В последние годы изготавливают режущие инструменты, оснащенные безвольфрамовыми твердыми сплавами (БВТС) на основе карбидов или карбонитридов титана и на никель-молибденовой связке. По сравнению с вольфрамсодержащими твердыми сплавами, БВТС обладают меньшим коэффициентом трения и большей износостойкостью.
Поскольку при обработке БВТС возникают большие значения составляющих силы резания и эффективной мощности шлифования, то велика вероятность появления трещин и сколов на обработанной поверхности. При шлифовании БВТС кругами на металлических и керамических связках наблюдается засаливание кругов, сглаживание рельефа рабочей поверхности круга. Поэтому более целесообразно шлифовать такие сплавы алмазными кругами на органических связках [2].
Ванадиевые штамповые стали Х12Ф4М, Х12Ф1, 9Х5Ф, Х6ВФ, Х6Ф4М, Х6В3ФМ, Х3Ф8, Х3Ф12 относятся к классу ТОМ. Их плохая обработка шлифованием абразивными кругами связана с наличием в их структуре твердых карбидов хрома (HV 15 ГПа), вольфрама и молибдена (HV 16,5 ГПа), твердость которых сопоставима с твердостью электрокорунда (HV 18,9-23,5 ГПа) [4].
Плохая шлифуемость новых марок быстрорежущих сталей (по сравнению с Р18) объясняется также, как и у ванадиевых штамповых сталей, наличием в их структуре твердых карбидов хрома, вольфрама, молибдена и ванадия. В этом случае зерна из белого электрокорунда, обычно применяемого в абразивных кругах при шлифовании инструмента и быстрорежущих сталей и имеющего микротвердость 20-21 ГПа, оказываются не в состоянии конкурировать с карбидами хрома, ванадия и т.д. Кроме того, быстрое затупление кругов вызывает дополнительное повышение температуры в зоне шлифования. Происходит образование остаточного аустенита, который создает дополнительные напряжения, что может привести к образованию шлифовочных трещин [2].
ТОМ обладают высокой пластичностью и поэтому при их обработке явление наклепа проявляется в большей мере, чем при обработке конструкционных углеродистых сталей. При неравномерном протекании процесса пластического деформирования высокая упрочняемость обрабатываемого материала может привести к увеличению вибраций. Поэтому при обработке подобных материалов необходимо, чтобы технологическая система обладала высокой жесткостью [5].
Одним из представителей ТОМ является сталь Гадфильда. Она характеризуется высоким уровнем износостойкости, который обусловлен ее способностью к чрезвычайно интенсивному упрочнению при пластической деформации, происходящей в зоне фрикционного контакта [6]. Обозначение марки стали – 110Г13Л.
Химический состав стали 110Г13Л согласно ГОСТ 977-88: C углерод 0,9-1,5%; Si кремний 0,3-1,00%; Mn марганец 11,5-15%; Ni никель не более 1%; Cr хром не более 1%; S сера не более 0,05%; P фосфор не более 0,12%. Предназначена для изготовления деталей работающих на износ в условиях трения, давления и ударных нагрузок, при которых происходит самоупрочнение (наклёп) стали, а её прочность и износостойкость значительно возрастает.
Сталь 110Г13Л обладает следующими механическими свойствами:
- предел прочности (временное сопротивление разрыву) σв = 800-900 МПа;
- условный предел текучести σ0,2 = 310-350 МПа;
- относительное удлинение (пластичность) δ = 15-20%;
- относительное сужение ψ = 50-30%;
- модуль упругости Е = 200000 МПа;
- модуль сдвига G = 78000 МПа;
- плотность 7820 кг/м³ [7].
Эта сталь так же обладает и особыми свойствами. При охлаждении в обычных условиях она хрупка, как стекло; после быстрого охлаждения в воде от 1000 °С обнаруживается исключительная тягучесть и вязкость.
Высокая вязкость и одновременно способность высокомарганцовистой стали упрочняться придают ей устойчивость против износа. При большой нагрузке высокая вязкость вызывает течение материала, которое в свою очередь сообщает стали наклеп благодаря сильному упрочнению. Большой наклеп повышает сопротивляемость стали износу.
Производство высокомарганцовистой стали сводится к легированию низкоуглеродистой стали марганцем. Это наиболее просто достигается путем смешивания низкоуглеродистой стали с расплавленным ферромарганцем, расход которого составляет при этом около 20% массы стали [8].
Благодаря высокой твердости и износостойкости сталь Гадфильда быстро завоевала признание в промышленном мире: ее стали использовать для изготовления тех деталей, которые в процессе эксплуатации постоянно подвергаются сильным ударам и обычно быстро выходят из строя по причине истирания. Таковы, например, рельсовые крестовины, щеки и плиты дробилок, шары для шаровых мельниц, зубья и передние стенки ковшей экскаваторов, гусеничные траки и т.д. [9].
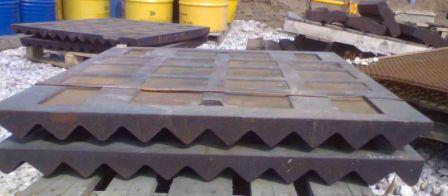
Рисунок 1 – Плиты дробящие из стали 110Г13Л
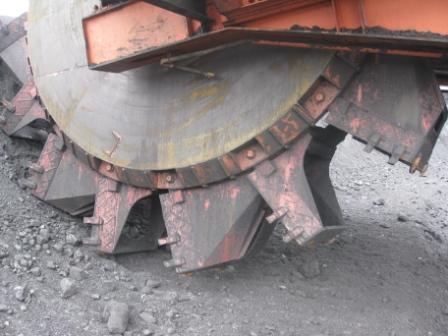
Рисунок 2 – Зуб ковша экскаватора из стали 110Г13Л
4.2 Анализ окончательных методов обработки труднообрабатываемых материалов
Существует множество методов окончательной обработки материалов, одним из них является шлифование.
Шлифование – один из видов обработки металлов резанием. При шлифовании припуск снимается абразивными инструментами – шлифовальными кругами. Шлифовальный круг представляет собой пористое тело, состоящее из большого количества мелких зерен [10]. Шлифованием можно обрабатывать практически любые материалы, так как твердость абразива (НВ = 2200-3100) и алмаза (НВ = 7000) очень велика. Для сравнения отметим, что твердость твердого сплава НВ = 1300, цементита НВ = 2000, закаленной стали НВ = 600-700 [11].
Для операций шлифования ТОМ резко возрастают эксплуатационные требования к абразивным инструментам. Обычные средства и методы улучшения показателей операций шлифования (применение СОТС, изменение режимов резания, характеристики инструмента и т. д.) не всегда достаточно эффективны.
Сейчас большое внимание уделяется поиску путей повышения режущих свойств абразивного инструмента. В частности распространены способы, основанные на введение в зону резания веществ улучшающих обрабатываемость материалов, использование не режущих элементов абразивного инструмента – связки и пор. Различные разновидности этих способов объединены понятием «импрегнирование» (пропитка). Импрегнирование шлифовальных кругов не влияет отрицательно на их физико-механические свойства, существенно улучшая их режущую способность [12].
В настоящее время высокопроизводительная обработка ванадиевых быстрорежущих сталей осуществляется с помощью алмазного шлифования кругами на металлической связке, после правки электроэрозионным методом, с поддержанием режущей способности рабочей поверхности круга в процессе обработки электроэрозионными воздействиями. Известно также шлифование этих сталей эльборовыми кругами на металлической связке, правленными абразивным способом [13]. При шлифовании потеря режущей способности круга происходит в результате выпадения наиболее выступающих зерен, засаливания субмикрорельефа контактных площадок зерен и межзеренного пространства продуктами обработки, а также контактирования связки с обрабатываемым материалом в результате разрушения зерен. При шлифовании кругами, после электроэрозионной правки, зерна выступают из связки минимум на одну треть диаметра зерна соответствующей зернистости, что может привести к их разрушению [14].
Электроэрозионная правка круга обеспечивает его большую режущую способность как вначале обработки, так и в течение всего процесса шлифования. Объясняется это тем, что в процессе электроэрозионной правки электрические разряды воздействуют только на связку, не разрушая зерен, как во время абразивной правки, благодаря чему зерна выступают из связки и участвуют в процессе резания с первых минут шлифования [13].
Одним из путей повышения производительности при механической обработке является внедрение в производство глубинного шлифования, которое в большинстве случаев более эффективно, чем обработка лезвийным инструментом, особенно при изготовлении деталей из жаропрочных и титановых сплавов, коррозионно-стойких, высоколегированных и инструментальных сталей [15].
Глубинное шлифование называют еще однопроходным. Этот процесс заключается в том, что весь припуск на обработку снимают за один проход круга. Глубинное шлифование происходит на скорости круга 30-40 м/с и находит применение при обычной или электролитической алмазной заточке твердосплавных режущих инструментов, а также при плоском шлифовании деталей на станках с вертикальным и горизонтальным расположением шпинделя [16].
Глубинное шлифование характеризуется значительными поперечными подачами (0,1…0,4 мм/ход) и малыми продольными подачами (1…6 мм/об).
В этом случае круг правится на конус и весь припуск (0,1…0,4 мм) снимается за один проход (рис. 3). Осуществлять глубинное шлифование возможно при наличии коротких жестких деталей [17].
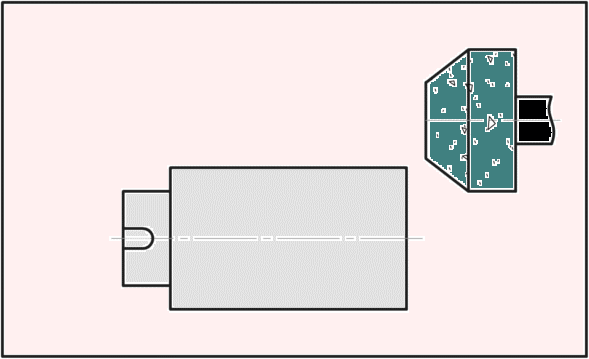
Рисунок 3 – Схема глубинного шлифования
(анимация: 8 кадров, 10 циклов повторения, размер анимации - 48 килобайт)
Установлено, что глубинное шлифование позволяет при заданном качестве обработки существенно повысить производительность и снизить трудоемкость и стоимость операции [16].
Увеличение скорости резания при глубинном шлифовании является существенным резервом повышения производительности обработки. Особенно это важно при обработке наиболее ТОМ – жаропрочных сплавов на никелевой основе [18].
При глубинном шлифовании к системе охлаждения предъявляют следующие требования: высокая смазочная, моющая и проникающая способность смазочно-охлаждающей жидкости (СОЖ), наиболее полный отвод жидкостью шлама из зоны шлифования, высокая степень очистки СОЖ при подаче ее в зону обработки для преодоления воздушного потока возникающего вокруг шлифовального круга. На рис. 4 показаны схемы подачи СОЖ при плоском глубинном врезном шлифовании.
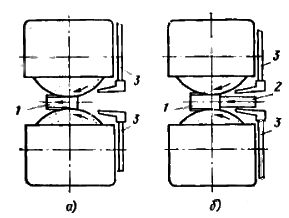
Рисунок 4 – Схемы подачи СОЖ в зону шлифования: а - неэффективная подача, б - эффективная подача ( 1 - деталь, 2 - направляющие устройства, 3 - сопла)
Результаты внедрения глубинного шлифования показали, что станки должны иметь электродвигатели шлифовальных шпинделей мощностью не менее 10 кВт; большой диапазон малых скоростей продольного перемещения стола; совершенную систему подачи СОЖ в зону шлифования; автоматический цикл правки круга и систему компенсации износа шлифовального круга [15].
На современном этапе технологии одним из важнейших путей решения проблемы обработки деталей из ТОМ является шлифование токопроводящими алмазными и абразивными кругами. Это обеспечивает значительный прирост производительности труда, снижение затрат и повышение эффективности производства при достижении высоких эксплуатационных свойств обработанных поверхностей.
Электрохимическое шлифование алмазными или абразивными кругами на токопроводящих металлических связках представляет собой комбинированный процесс, при котором материал снимается в результате одновременно протекающих процессов: анодного растворения, механического резания алмазными или абразивными зернами и электроэрозионных явлений.
При электрохимическом шлифовании кругами прямого профиля с поперечной подачей зона контакта круга с деталью состоит из двух участков. На участке (рис. 5,а), ширина которого равна величине поперечной подачи, условия шлифования определяются только характеристикой инструмента и режимами обработки, а величина зазора, определяющая электрическое сопротивление цепи на данном участке, зависит в основном от зернистости абразива и состояния режущей поверхности круга. Для данных условий шлифования сопротивление в зазоре на данном участке минимально, а плотность тока – максимальна. На оставшемся участке величина зазора максимальна, сопротивление цепи в зазоре также максимально, а плотность тока имеет наименьшее для данных условий обработки значение (рис. 5,б). Таким образом, по высоте круга существуют участки с различными плотностями тока.
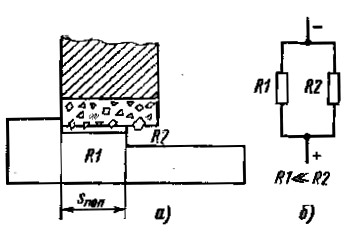
Рисунок 5 – Схема электрического сопротивления на различных участках зоны контакта при электрохимическом шлифовании периферией круга
Для шлифования деталей из твердых сплавов применяются только алмазные круги, а из жаропрочных сплавов, нержавеющих и конструкционных сталей – алмазные и реже абразивные круги на металлических связках.
Использование абразивных кругов на металлической связке возможно при шлифовании с непрерывной электрохимической правкой круга. Преимуществом этого метода шлифования является отсутствие трения связки с обрабатываемой поверхностью. Для этой же цели иногда используют реверсивный источник питания, дающий обратную полуволну. Известно использование электронейтрального абразивного инструмента, в котором электрохимический и механический процессы разнесены в пространстве. Электрохимический съем с поверхности детали осуществляется в этом случае дополнительным кругом. Все разновидности методов обработки с использованием анодных процессов могут весьма эффективно использоваться в промышленности [19].
Выводы
Подытоживая вышесказанное, необходимо отметить, что высокопроизводительная обработка ТОМ с достижением необходимого качества детали, является важной задачей для исследований. Большое разнообразие ТОМ предполагает множество способов их обработки, но, как правило, как наиболее высокопроизводительный и окончательный способ обработки таких изделий применяется шлифование.
Прежде всего, исходя из свойств обрабатываемого материала, формы и качества обрабатываемой поверхности, необходимо выбрать характеристику и форму шлифовального круга. Так как в процессе шлифования ТОМ происходит интенсивное тепловыделение (может негативно сказаться на прочности обрабатываемой поверхности) и образование продуктов износа заготовки и шлифовального круга – шлама (может негативно сказаться на качестве обработанной поверхности) – необходимо наличие более совершенной системы СОТС.
Вследствие высокой твердости ТОМ, характер износа режущей поверхности шлифовального круга отличается от износа при шлифовании углеродистой стали. Твердость материала зерен шлифовального круга соизмерима с твердостью обрабатываемой поверхности. Поэтому для обработки таких материалов используют карбиды кремния, искусственные или естественные алмазы.
Многие исследователи предлагают управлять состоянием рабочей поверхности шлифовального круга посредством его правки во избежании негативного воздействия возрастающих сил резания в процессе шлифования.
Таким образом, процесс шлифования ТОМ предполагает наличие более совершенной системы СОТС и устройства, позволяющего управлять рабочей поверхностью шлифовального круга. Такие устройства относятся к технологическому обеспечению процесса шлифования. Следовательно, тема «Технологическое обеспечение процесса шлифования изделий из труднообрабатываемых материалов» является актуальной и может быть выбрана в качестве темы магистерской работы.
Список источников
- Куприянов В.А. Мелкоразмерный инструмент для резания труднообрабатываемых материалов. – М.: Машиностроение, 1989. – 136 с.
- Прогрессивные методы абразивной обработки металлов / И.П. Захаренко, Ю.Я. Савченко, В.И. Лавриненко, С.М. Дегтяренко; Под ред. И.П. Захаренко. – К.: Техника, 1990. – 152 с.
- Режимы резания труднообрабатываемых материалов: Справочник / Я.Л. Гуревич, М.В. Горохов, В.И. Захаров и др. 2-е изд., перераб. и доп. – М.: Машиностроение, 1986. – 240 с.
- Основы проектирования и технология изготовления абразивного и алмазного инструмента. / Ю.М. Ковальчук, В.А. Букин, Б.А. Глаговский и др.; Под общей ред. Ю.М. Ковальчука – М.: Машиностроение, 1984. – 288 с.
- Труднообрабатываемые материалы [Электронный ресурс]. – Режим доступа: http://iron–lab.ru
- Иванов Ю.Ф., Алешина Е.А., Колубаев Е.А., Колубаев А.В., Сизова О.В., Громов В.Е. Закономерности формирования структуры поверхностного слоя стали Гадфильда при трении // Физ. мезомех. – 2006. – Т. 9. – № 6. – С. 83-90.
- Сталь 110Г13Л [Электронный ресурс]. – Режим доступа: http://www.bila.ru
- Производство высокомарганцовистой стали Гадфильда. Часть 1 [Электронный ресурс]. – Режим доступа: http://www.olvia.org
- Специи для стали [Электронный ресурс]. – Режим доступа: http://wolframpo.ru
- Лоскутов В.В. Шлифование металлов: Учебное пособие для профессинально-технических училищ. – М.: Машгиз, 1962. – 280 с.
- Ящерицын П.И., Еременко М.Л., Жигалко Н.И. Основы резания материалов и режущий инструмент. – Минск: Высшая школа, 1975. – 528 с.
- Никитин А.В. Шлифование труднообрабатываемых материалов импрегнированными кругами как способ их режущих свойств // Инструмент и технологии. – 2010. – №28. – Вып. 2 – С. 52-58.
- Матюха П.Г., Габитов В.В. Удельная себестоимость шлифования стали Р6М5Ф3 в зависимости от способа правки и электроэрозионных воздействий на рабочую поверхность кубонитового круга // Сверхтвердые материалы. – 2009. – № 5. – С. 63-69.
- Азарова Н.В., Матюха П.Г., Полтавец В.В. Удельная себестоимость процесса плоского шлифования ванадиевой быстрорежущей стали кругами из сверхтвердых материалов // Сверхтвердые материалы. – 2008. – № 2. – С. 65-71.
- Глубинное шлифование деталей из труднообрабатываемых материалов / С.С. Силин, В.А. Хрульков, А.В. Лобанов, Н.С. Рыкунов. – М.: Машиностроение, 1984. – 64 с.
- Абразивная и алмазная обработка материалов: Справочник / Под ред. А.Н. Резникова. – М.: Машиностроение, 1977. – 391 с.
- Маслов Е.Н. Основы теории шлифования металлов. – М.: Машгиз, 1951. – 190 с.
- Макаров В.Ф., Семиколенных В.В., Чигодаев Н.Е., Веснин Г.В. Интенсификация лезвийной и абразивной обработки труднообрабатываемых материалов на основе физической оптимизации процессов резания // Инструмент и технологии. – 2004. – №17. – С. 129-135.
- Вайнберг Р.Р., Васильев В.Г. Электрохимическое шлифование токопроводящими абразивными и алмазными кругами. – М.: Машиностроение, 1976. – 32 с.
Замечание! При написании данного реферата магистерская работа еще не завершена. Окончательное завершение: декабрь 2012 г. Полный текст работы и материалы по теме могут быть получены у автора или его руководителя после указанной даты.