Abstract
- Introduction
- 1. Theme urgency
- 2. The purpose and objectives of the study, expected results
- 3. Review of research and development
- 4. Research of dynamic properties of an adjustable volume hydrodrive of mechanisms of cleaning combines dislocation
- Conclusions and directions of the further researches
- The list of the used litterature
Introduction
The rapid increase in the requirements for the competitiveness of products of coal production machinery makes leading engineering design and scientific research institutes to create a machine of high technical level.
Necessity to increase coal production volumes and lower its cost is a prerequisite for profitable operation of a coal mine.
Requirements for reliability and safe operation of mining machines in the complex conditions of sewage treatment works, speaks of the need to consider the requirements for operation at acceptable standards of vibro-acoustic characteristics and dust emission.
Along with the requirements of reliability and safety are restrictions on mass and size parameters of the machine.
Currently one of the most important issues is to reduce the power load subsystems based on optimization combines properties of the destruction of the complex structure of coal seams and moving them along the bottom.
All the instructions above requirements and limitations suggest the need to consider a comprehensive, systematic approach in the design of mining machinery to the management of all subsystems.
That’s why study options for removing combine cleaning power and average power of coal seams is an urgent scientific task.
1. Theme urgency
For the last 10–15 years in the world and domestic coal machinery there have been radical changes, they result in a significant increase in technical and economic indicators of coal mining. So, the average daily production from the working face reaches 15–20 thousand tons of coal. It is important to note that the significant increase in efficiency achieved without fundamental changes in technology of underground mining. Like 40 years ago, coal mining is mechanized wastewater treatment complexes of long working faces. Have not changed layout decisions of individual machines. At the same time working rate increased by 2 times, shunting movements – to 2.5–3 times, the installed capacity increased by 1.5–4 times, regulated resource – by 3–10 times. Size and weight of vehicles has increased slightly.
Implementation of the ever-increasing requirements for mining machinery can not be achieved without significant complications. in the first place, equipping them with various multi-motor electric drive systems, automatic control and technical diagnostics. Modern mining machines have a high level of "intelligence", the system ceased to be a "gear-motor" and consist of synergistically integrated mechanical, hydraulic, electronic, electrical and information components. Modern treatment complex is a complex mechatronic systems. Components are not only mechanically, but are united in a common information network.
When you create a modern mechatronic mining machines with high functional and parametric features is necessary to consider a number of specific features and requirements that are generally not typical of the sectors of mechanical engineering, where the mechatronic approach to design is a traditional (for example robotics, machine tools, aircraft and space industry, the exact mechanics of the computer, instrumentation, etc.). There is a need to combine all these features and requirements for taking into account when designing.
The important features of modern shearers and their working processes are:
1. High specific power available.
The need to increase productivity inevitably lead to a permanent increase in energy available for virtually unchanged dimensions. This is determined by geological conditions such kinds of coal seams. So, the vertical dimension of the body combine to develop a reservoir capacity of up to 1.5 m (typical of the Donbas) and type UKD300 UKD200-250 is 400 mm, and for the type KDK500 working in layers, starting with the power of 1.35 meters - 500 mm. This limits the vertical clearance of engines and electric unit, and considering the thickness of the walls of the buildings, the necessary clearances and design features, the diameters of gears, planetary gears in these conditions does not exceed 310 and 410 mm respectively. Width’s dimension is also limited. It is determined by the length console, roof supports, its limited carrying capacity, and regulated from the chest behind the console face. The complex hypsometry dip leads to a limitation of the length to provide a geometrical cross.
2. The random nature of the changing in a wide range and determined by physical and mechanical properties of rocks destroyed loads in the major subsystems of machines.
This requires a large overload capacity drives and substantial reserves of strength that is very problematic in narrow layers of low and medium power. The problem is aggravated by the formation of large dynamic loads on the machine (including a high breaking load transients), which along with the specific conditions of work are determined by the inability to use conventional methods in the design the a number of nodes.
3. A significant role of the cutting tool wear, executive bodies stars, hauling bodies and other elements in the formation of load and resource mining machines.
Wear of cutting tools excavation machines, the frequency of their replacement are random in nature, that causes random changes in such an important indicator of the executive body -his force imbalance.
There remain outstanding issues to achieve:
- high levels of reliability and a normative resource harvesters, conveyors and high-pressure units of pumping stations;
- safe levels of vibration and noise in the workplace machinists and sanitation dust.
Improving the reliability and reduce vibration and noise machines with a high level of installed power are closely linked. The level of vibro-acoustic characteristics of technological machines reflects, as we know, their degree of technical perfection. According to academician Artobolevsky II [2], with a high level of dynamic quality machines in the environment comes in the form of vibrational energy (vibration and noise) is not a part of the total installed capacity in the water engine. For today, according to the papers [3,4], these figures in modern mining machinery (harvesters, conveyors, pumping stations) have not yet been achieved. This is one of the main reasons for reducing the of actual indicators of their reliability in comparison with the project. High levels of vibration and noise reduce also safety of staff.
A large number of interrelated and interacting elements characterize the shearer as a complex, dynamic system driven. Therefore, when designing and building cleaning machines with a high level of energy available is important to consider the dynamic process of moving, demolition and loading coal.
So, study of parameters for high-performance extraction of coal seams is a complex and multi-criteria scientific task. Which involves the study of the issue at a high intellectual level information.
2. The purpose and objectives of the study, expected results
Let's present in the form of the flowchart (pic. 1) the purpose and research problems with possible variants of paths of realisation of the last.
One of problems is capacity heightening. This problem can be realised differently, as is shown in the flowchart:
- by installed power per employee heightening (use of individual drive gears for each screw and for each gear of migration);
- a path heightening of factor of a machining time (elimination of expenditures of time for shunting processes, Without a niche flute and application The bilaterial operation circuits);
- by complete use of the fixed power of drive gears (improvement of conditions of power supply, security of rational modes of behaviour of a combine, control improvement in quality).
The decision of the second problem is reduced to the fractional decision of the third problem, therefore on the flowchart the arrow displays link of these two problems.
The decision of a problem on capacity heightening is impossible without consideration of questions of heightening of reliability and a resource. As, for example, with installed power per employee growth by all means increases Load all subsystems of the car, and, in particular, dynamic Load. Details Fail and nodes of cars that involves the idle times linked with Elimination of refusals, accordingly readiness factor decreases. Application Vibro-protective devices sharply reduces dynamic Load, but taking into account a correct choice of its type and parametеrs that represents a difficult research problem with holding of some experiences.
.png)
Picture 1 – block diagram
Thus the decision of tasks in view will allow to justify parametеrs of a clearing combine for an intensification of process of coal mining and heightening of profitability of operation of the coal operation.
3. Review of research and development
In operations [7,8,9]questions of a choice and maintenance of optimum modes of behaviour The coal cars are considered.
Adjusting becomes especially necessary by working out of means of complex automation and mechanisation for which realisation of optimum conditions, reliability and longevity heightening is the integral requirement.
Execution of this problem substantially depends on dynamic properties of adjustable plants and spectra of the external loads caused by physicomechanical properties of the destroyed array.
At the same time, realising autocontrol, i.e. effecting car parametres, changing a mode of behaviour depending on service conditions, probably to receive the greatest capacity, the highest rate and more favorable condition.
Complexity of a problem speaks that forces of resistance of rocks to collapse, defining loads in all elements of cars and instant laws of their movement, represent nonstationary random functions of migration of an executive office, statistical study and which exposition necessary for system engineering of autocontrol, labour-intensive process suffices.
In the book [2] the common regularities shaping of loads (in particular dynamic) in elements of mountain cars and their influence on strength and reliability are considered.
For all mountain cars one of the most widespread sources of perturbation are any kinematic imperfections of transmission and the systems, movements creating non-uniformity, and, hence, speedups and dynamic components of loads. It is kinematics h-pole serrated and chain drives, movement kinematics the seizing paws, a kinematic unbalance of executive powers of combines etc. a perturbation Source, characteristic for mountain cars are also instability of performances of sources of power supply. Change of level of a supply voltage of electric mains and pressure in hydraulic drive systems lead to change of loads on various elements of mountain cars so, for example, the current and the moment on a motor shaft depending on a network and voltage condition can vary largely.
The operating duty of mountain cars is combined, it is accompanied by self-oscillatory, resonance and other processes in various subsystems of these cars.
The correlation of the dynamic processes occurring in various subsystems of the car, creates a difficult picture of shaping of loads in these systems, thus loads on some frequencies are augmented, calling overloads of details and nodes.
The specified features complicate problem solving which fall outside the limits usually considered in the common machine industry.
In operations [3,5,14,15,17,18,20,22,23,24]problems and some results of simulation of dynamic processes of system " a clearing combine-face " are considered.
For heightening of a technological level and quality of difficult mountain cars a necessary condition is creation of scientific base of their optimum computer projection. This problem demands the decision of scientific and practical problems on working out and development of mathematical sample pieces of functioning of the difficult technical systems reflecting adequately principal properties of cars and their working processes at a simulation modelling and problem solving of optimisation.
The important development cycles of mathematical models (MM) of cleaning combines (CC) are check of its adequacy to real object of research and performance of its necessary calibration. The analysis of the researches carried out with use of MM CC has shown insufficient degree of adequacy of the given MM in the field of dynamics of CC dislocation which has caused inadequacy of a parity of dispersions on characteristic frequencies of some dynamic processes.
Now increase of productivity of cleaning combines involves prompt growth of available power. However already with the productivity of 3-6 t/min the power of existing drives reaches 300 kw and above. Application of asynchronous short-circuited electric motors on this power demands increase of a stress feeding them to 1140-3000 In, that will result, to essential reconstruction of a power economy of mine.
In turn the increase of power and rapidity and consequently, productivity of mining machines is restrained by insufficient level of scrutiny of their kinematic and dynamic parametres and true operating modes, actual values and distributions of stresses and deformations in parts with difficult constructive forms, and also is limited to wear resistance of the interfaced parts. The strengthened deterioration appearing in separate joints of cars, causes either necessity of a decrease of the loadings falling to separate elements that leads to increase in dimensions and weight of machines, or to sharp rise in price at the expense of application of nano-materials and nano-technologies in manufacturing techniques of parts and knots of machines.
Thus correct definition of dynamic parametres and the characteristics of the machine and their maintenance in the real machine finally will essentially affect its working capacity, reliability, durability and cost.
Research of dynamic properties of an adjustable volume hydrodrive of mechanisms of cleaning combines dislocation
Now in coal branch of Ukraine and of the countries having reserves of coal, the questions of creation of the most perspective means of mechanisation of coal become more and more essential. Coal cutters are projected for high theoretical productivity the realisation of which becomes possible with the automation of their operation. First of all, in coal cutters automatic smooth regulation of feed rate depending on engine loading should be applied. As object of regulation the feeder is used on the basis of a volume hydrodrive. As an example we will consider the use of system of conveying speed automatic control.
The scheme of automatic control of feed rate "Ecomatic" looks like presented on pic. 2, where:
1 current transformer; 2 device of comparison; 3 current setting mechanism; 4 amplifier; 5 speeds setting mechanism; 6 hydraulic amplifier; 7 hydraulic adjusting device; 8 hydraulic Servomotor; 9 main electric motor; 10 executive device; 11 boost pump; 12 hydraulic pump; 13 hydraulic feed engine; 14 drive sprocket.
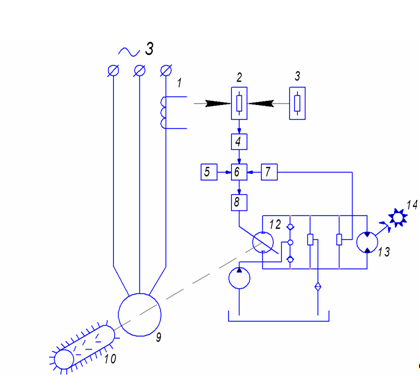
Picture 2 - the Scheme of automatic control of feed rate "Ecomatic" (Germany)
An adjustable volume hydrodrive finds wide application in subsystems of transfer mechanisms (STM) of cleaning combines with elastic and rigid traction mechanism. Usually adjustable parametre is variable eccentricity radial plunger pump or a corner of an inclination of a disk axial plunger pump.
On pic. 3 are shown basic (a), settlement (b) and structural (c) schemes of volume hydrodrive STM СС.
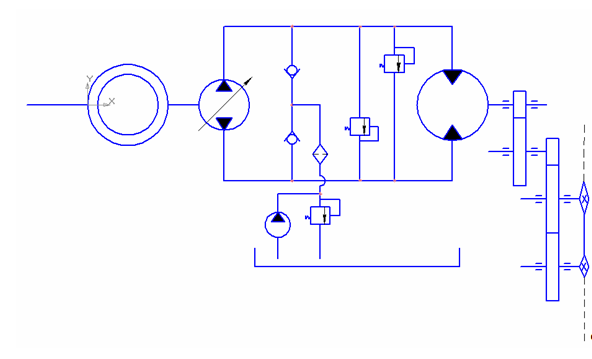
а)
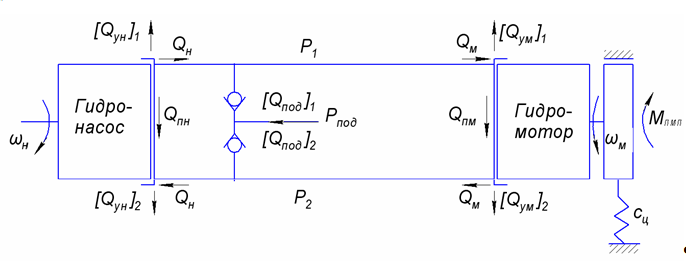
b)
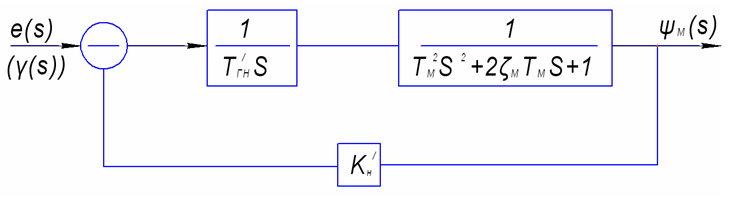
c)
Pic. 3 - Basic (a), settlement (b) and structural (c) schemes of hydrodrive STM
The dependence of established movement speed of not loaded hydrodrive on size of parametre of regulation by the static high-speed characteristic (or the characteristic of regulation of speed of a volume hydrodrive):

Where Qн - theoretical pump feed; qгм - operational hydromotor volume;
Relation of operational volumes of the pump and the hydromotor (hydraulic transfer number of hydrotransfer);
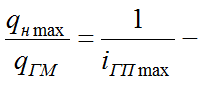
regulation parameter (pic. 4):
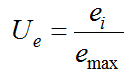
For the hydromotor with reversible liquid stream

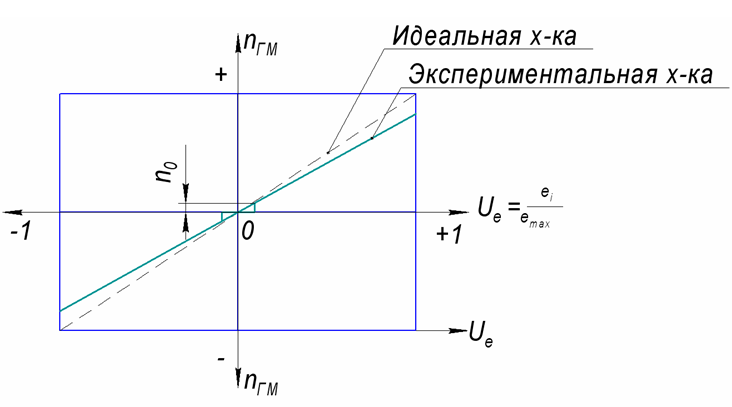
Picture 4 - The speed characteristic of a volume hydrodrive
On pic. 4 n0 indicates the minimum steady speed of hydromotor. It is caused by compressibility and liquid leaks, inertia of a rotor and self–oscillations in the hydromotor on "creeping" speeds, at "falling" dependence of a friction on speed (a difference between a friction of rest and movement in piston groups and other elements of the hydromotor). Thus, strictly speaking, the high-speed characteristic is nonlinear, however a zone of creeping speeds (0–n0) is not the operational, pic. 4 .
In a working zone, according to Gamynina N.S., Bashty T.M., Prokofiev V. N. and other scientists' researches, both high-speed, and mechanical characteristics are practically linear, and, hence, for the description of dynamic properties of a hydrodrive it is possible to use peak-frequency and phase characteristics (PFP). The static mechanical characteristic of adjustable hydrotransfer shows dependence between speed of rotation of the hydromotor and the moment of its loading at various values of parametre of regulation Ue, pic. 5.
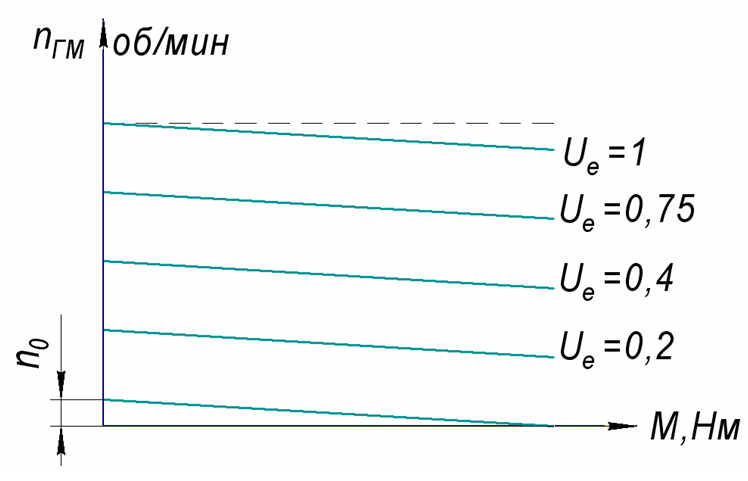
Picture 5 - Mechanical characteristic of volume hydrotransfer


where аn,аgm - coefficients of leaks in the pump and the hydromotor; Р=Р1-Р2 - pressure difference in the hydromotor, M и Км - the moment of hydromotor and the moment factor.
The equation of loading of the hydromotor of the feeder of a cleaning combine at
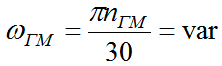

It corresponds to modes with the accelerated and slowed down rotation of the hydromotor.
where (Р1-Р2)qгм - moment of the hydromotor; Iгм - moment of inertia of the hydromotor; m - combine mass; r - radius of a sprocket; i - transmission ratio of a reducer of the feeder; Mcмп - moment of resistance.
It is possible to present the equation of movement of a combine as
where mx - inertial force; Сц - coefficient chain (traction body) rigidity; (rф - x) - rigide deformation of traction body; Fтр - friction force; Fпx - X component of useful resistance forces (cutting and giving); mg sin(a) - longitudinal component of combine gravitation in a seam with a corner of inclination a.
The moment of resistance forces on a hydromotor shaft can be recorded as:

For hydrovolume transfer and the hydromotor loading (moment) on its shaft can be considered as the external indignation operating on "input" in STM CC.
As it is known [1,2],even in the absence of useful loading on combine executive device, i.e.Fпx=0,the moment Мспм,forming on a hydromotor shaft, it is possible to consider as stochastic function as, at factor of a friction changing in a random way in combine support, the kinetic characteristic of friction is stochastic it is not dependent on rigidity of traction body.
The general law of falling dependence of force of a friction from speed of sliding remains, however numerical values of function at the same values of argument can change. It is alsonecessary to notice that the system "a combine - the conveyor - traction body", is a system with variable elastic parametre: with combine moving the length of a working site of traction body and consequently, and the factor of rigidity that leads to change of own frequency of fluctuations of system, see pic. 6 continuously changes.
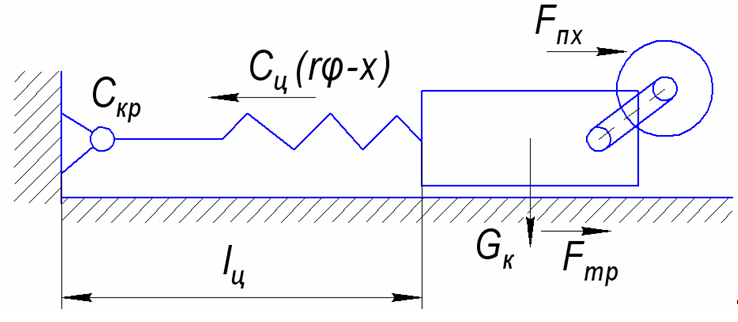
Picture 6 - Dynamic model of CC process of moving
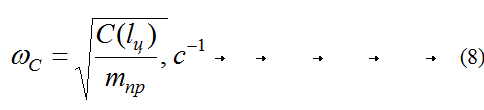

- the coefficient of system rigidity , depends on length of traction body and rigidity of knot of fastening to a head of the conveyor of a working branch of chain.
So, for example, for a combine 1GSH–68 with Gк=14500 kg; Cц=5100000 kg/m; q=13,6 kg/m; Cкр=1000000 kg/m dependence wс=(С(lц)/mпр)^1/2, is graphically possible to present dependence in the form of a falling curve at increase chain length, pic. 7.
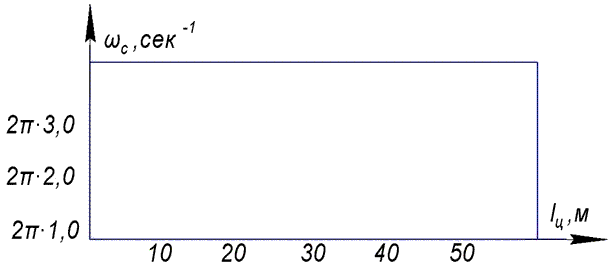
Picture 7 - Dependence of proper frequency of fluctuations ОК on length of a chain
Thus, frequency of self-oscillations of feed rate and moment change depending on length of a working site of traction body.
Component of the total moment of resistance forces on a hydromotor shaft

where a и b - coefficients, reflecting design features of the executive device; т - the time of delays.
Fпx*r corresponds to the process of cutting of coal also has, as is known, obviously stochastic character. Thus, loading on a hydromotor input should be described by the likelihood characteristics, one of which is the spectral density of loading:

According to the theory of stochastic functions and statistical dynamics of linear systems, spectral density of loading on an щгезге (in this case in a hydraulic pump):

where W(jw) - frequency characteristic of the system "the pump - the hydromotor - CC propulsion device".
Hence, the loading dispersion in a hydrodrive, characterising amplitude of a variable component of target parametre (for example, pressure ) can be calculated under the formula:

Thus, dynamic loadings in system of STM volume hydrodrive are defined not only by external influence, but also by substantially of dynamic properties of a drive, i.e. its peak-frequency characteristics.
Differently, the parity between amplitude of fluctuations of pressure in system "pump-hydromotor" of MT and amplitude of periodic components of the moment of loading on a hydromotor shaft (a drive sprocket of the propulsion device) depends on frequency of loading.
Conclusions and directions of the further researches
On the basis of the stated material with reference to problems of my diploma thesis it is possible to draw following conclusions:
- in the research of ways of increase of productivity of a cleaning combine it is necessary to prefer consideration of questions on quality improvement of management and maintenance of rational operating modes that will cause complete use of the established power of drives;
- in the research of the dynamic system reflecting non-uniformity of process of moving it is necessary to consider questions on damping of hydraulic support of a combine, and also the possibility of application in a work cycle of face-to-face shifting of sections of a support;
- in the research of dynamic loading the basic feature of a drive of a cutting part of modern machines is the presence of two basic masses located on the ends of transmission of a drive - it is dynamic is the mass of a rotor of the electric motor and executive device mass. And in most cases the mass of the last is less than the mass of a rotor of the electric motor, but it is larger than the mass of any intermediate element of transmission. Therefore fluctuations of mass of an executive office round mass of a rotor of the electric motor with a pliability equal to a pliability of all transmission will be the basic defining fluctuations in transmission of a drive of a cutting part at analysis of formation of loadings of an operating duty.
The last fact is necessary to be considered while research of questions of durability and increase of availability ratio.
This master's work is not completed yet. Final completion: December 2012. The full text of the work and materials on the topic can be obtained from the author or his head after this date.
The list of the used litterature
- Гуляев В.Г. Проектирование и конструирование горных машин и комплексов. Часть 1. Выемочные комбайны //ГВУЗ "ДонНТУ", Технопарк ДонНТУ "УНИТЕХ", 2011.-322с.
- Докунин А.В., Красников Ю.Д., Хургин З.Я. Статистическая динамика горных машин //М.: Машиностроение, 1978.-239с.
- Динамические процессы горных машин /А.В. Докунин, Ю.Д. Красников, З.Я. Хургин и др. //М.: Наука, 1972.-150с.
- Коваль П.В. Гидропривод горных машин. //М.: Недра, 1967.-387с.
- Верескунов З.Н., Фастовец Н.И. О динамических характеристиках привода добычных комбайнов с бесцепным механизмом подачи. /В сб.: "Совершенствование и повышение надежности горных машин и средств автоматизации" (Научные сообщения, вып.184), М.: ИГД им. А.А. Скочинского, 1980.
- Докукин А.В., Фролов А.Г., Позин Е.З. Выбор параметров выемочных машин. М.: Наука, 1976, 144 с.
- Позин Е.З, Меламед В.З. О параметрах выемочных комбайнов. Уголь, М.: Недра, 1980, №11, с. 31-34.
- Берон А.И., Позин Е.З. Принципы выбора и поддержания оптимальных режимов работы исполнительных органов угледобывающих машин. - В кн. Горнорудные машины и автоматика, М., Недра, 1965, вып.1, с. 18 - 44.
- Выравнивание скорости перемещения добычных комбайнов при помощи динамического гасителя колебаний. / Авт. Г.В. Малеев, В.Г. Гуляев, Н.Г. Бойко, А.К. Семенченко. - Известия вузов. Горный журнал, 1972, №5, с. 92-96.
- Гуляев В.Г., Сивокобыленко В.Ф., Жуков К.В. Математическая модель двухдвигательного привода исполнительного органа очистного комбайна. //Тр. Донец. гос. тех. ун-та. Серия: горно-электромеханическая; Вып. 7. - Донецк, 1999.- С. 97-102.
- Гуляев В.Г., Жуков К.В. Определение кинематической характеристики трения очистного комбайна с цепным тяговым органом // Наук. вісн. нац. гірн. акад. України. - 1999.- №2.- С.54-57.
- Гуляев В.Г., Жуков К.В. Математическая модель для имитационного моделирования функционирования системы ‹‹очистной комбайн-забой›› // Горн. информ.-аналит. бюл.- М., 2000.- №4.- С.129-131.
- Гуляев В.Г., Жуков К.В. Некоторые результаты имитационного моделирования функционирования системы ‹‹очистной комбайн-забой›› // Наук. пр. Донец. держ. техн. ун-ту. Серія: гірничо-електромеханічна. Вип. 16.- Донецьк, 2000.- С.84-91.
- Гуляев В.Г., Жуков К.В. Результаты прогнозирования эксплуатационных и динамических характеристик очистного комбайна с высоким уровнем енерговооруженности // Вибрация в технике и технологиях.- 2001.- №3.- С.32-35.
- Гуляев В.Г., Жуков К.В. Имитационное моделирование рабочего процесса и обоснование параметров очистного комбайна нового технического уровня // Донбас-2020: наука і техніка - виробництву: Матеріали наук.-практ. конф., 5-6 лютого 2002 р., м. Донецьк / Донец. нац. техн. ун-т.- Донецьк, 2002.- С.156-161.
- Гуляев В.Г., Косарев В.В. Состояние и проблемы комплексной механизации при разработке пологонаклонных угольных пластов Донецкого бассейна // MATERIALY SZKOLY ECSPLOATACJI PODZIEMNEJ 2002. FORUM Polsko-Ukrainskie Szczyrk, 18-22 lutego 2002. Seria Wyklady nr21.- Krakow, 2002.- S.19-25.
- Гуляев В.Г. Исследование и учет взаимодействия силовых подсистем комбайна при разработке математических моделей системы ‹‹очистной комбайн-забой›› // Горная энергомеханика и автоматика: Тр. междунар. науч.-техн. конф.- Донецк, 2003.- Том 2.- С.73-79.
- Гуляев В.Г., Жуков К.В. Метод формирования математической модели функционирования системы ‹‹очистной комбайн-забой›› // Зб. наук. пр. НДІГМ ім. М.М. Федорова.- Донецьк, 2003.- Вып.96.- С.179-186.
- Гуляев В.Г, Потапов В.Г., Мотин Н.Н. Математические модели приводных асинхронных двигателей для исследования динамических свойств горных машин // Науч. тр. Донец. нац. техн. ун-та. Серия: горно-электромеханическая. Вып.99.- Донецк, 2005.- С.62-70.
- Васильев А.Ю., Гуляев В.Г Передаточные функции объёмного гидропривода механизмов подачи очистных комбайнов // Автоматизація технологічних об'єктів та процесів: Зб. наук. пр. V-й міжн. наук.-техн. конф., 16-19 травня 2005 р., м. Донецьк.- Донецьк,2005.- С.104-106.
- Кондрахин В.П., Гуляев В.Г., Головин В.Л. Имитационная математическая модель динамических процессов очистных комбайнов высокой энерговооруженности с вынесенной системой подачи / Наукові праці донецького національного технічного університету. Випуск 12 (113). Серія гірничо-електромеханічна. Донецьк,2006.- С.123-130.
- Guljaew W.G. Optimirung der dynamischen Eigenschaften von Bergbaumaschinen mit dem Ziel der Erhohung ihrer Zuverlassigkeit und Leistungfahigkeit: Vortrag auf wissenschaftlichen Kollogviums technische Hochschule Otto von Guericke.- 1981-24 s.
- Guljaew W.G. Untersuchung und Optimirung der dinamischen Eigenschaften von Bergbaukombines mit dem Ziel der Erhohung ihrer Zuverlassigkeit, Lebensdauer und Leistungfahigkeit. Magdeburg (DDR) // TECHNISCHE MECHANIK.- 1982.- N3, H1.- S.18-27. ....