Реферат по теме выпускной работы
Содержание
- Введение
- 1. Актуальность темы
- 2. Цель и задачи исследования, планируемые результаты
- 3. Обзор исследований и разработок
- 4. Исследование динамических свойств регулируемого объёмного гидропривода механизмов перемещения очистных комбайнов
- Выводы и направления дальнейших исследований
- Список источников
Введение
Стремительное повышение требований к конкурентоспособности изделий угольного машиностроения заставляет ведущие проектно-конструкторские и научно–исследовательские институты создавать машины высокого технического уровня.
Необходимость повышения объемов добычи угля и снижение его себестоимости является необходимым условием рентабельной работы угольного предприятия.
Требования по надежности и безопасности эксплуатации добычных машин, в сложных условиях ведения очистных работ, обуславливают необходимость учета эксплуатационных требований по допустимым нормам виброакустических характеристик и пылевыделения. Наряду с требованиями по надежности и безопасности накладываются ограничения по массогабаритным параметрам машины.
Остро стоит вопрос снижения нагрузок силовых подсистем на основе оптимизации динамических свойств комбайнов при разрушении угольных пластов сложной структуры и неравномерности перемещения их вдоль забоя.
Все указанные выше требования и ограничения обуславливают применение комплексного рассмотрения, системного подхода при проектировании добычных машин с рациональной взаимоувязкой всех подсистем.
Поэтому обоснование параметров очистного комбайна для интенсивной выемки средней мощности и мощных угольных пластов является актуальной научной задачей и сферой рассмотрения широкого спектра вопросов по исследуемой теме.
1. Актуальность темы
За последние 10–15 лет в мировом и отечественном угольном машиностроении произошли коренные изменения, результатом которых стало существенное повышение технико-экономических показателей добычи угля. Так, среднесуточная добыча из очистного забоя достигает 15–20 тыс. тонн угля. Важно отметить, что существенное повышение эффективности достигнуто без принципиальных изменений технологии подземной добычи. Как и 40 лет назад, добыча угля осуществляется очистными механизированными комплексами из длинных очистных забоев. Практически не изменились и компоновочные решения отдельных машин. В то же время рабочие скорости возросли в 2 раза, маневровые – в 2,5-3 раза, установленная мощность возросла в 1,5-4 раза, регламентируемый ресурс - в 3-10 раз. При этом габариты и масса машин увеличились незначительно.
Выполнение все возрастающих требований к горным машинам невозможно обеспечить без их значительного усложнения, в первую очередь, в частности оснащения их различными системами многодвигательного электропривода, автоматического управления и технической диагностики. Современные горные машины отличаются высоким уровнем «интеллектуальности», перестали быть системой «редуктор-двигатель» и состоят из синергетически интегрированных механических, гидравлических, электронных, электротехнических и информационных компонент. Современный очистной комплекс представляет собой сложную мехатронную систему, составные части которой связаны не только механически, но и объединены в общую информационную сеть.
При создании современных мехатронных горных машин с высокими функционально-параметрическими характеристиками необходимо учитывать ряд специфических особенностей и требований, которые, как правило, не характерны для тех отраслей машиностроения, где мехатронный подход к проектированию является уже традиционным (например, робототехника, станкостроение, авиа-космическая отрасль, точная компьютерная механика, приборостроение и т.д.). Возникает необходимость обобщения этих особенностей и требований с целью их комплексного учета при проектировании.
Важными признаками современных очистных комбайнов и их рабочих процессов являются:
Высокая удельная энерговооруженность
Потребность в увеличении производительности неизбежно приводит к постоянному росту энерговооруженности при практически неизменных габаритах, что определяется горно-геологическими условиями отрабатываемых угольных пластов. Так, вертикальный габарит по корпусу комбайнов для разработки пластов мощностью до 1,5м (характерной для Донбасса) типа УКД300 и УКД200-250 составляет 400мм, а для комбайнов типа КДК500, работающих на пластах, начиная с мощности 1,35м - 500мм. Это ограничивает вертикальный габарит двигателей и электроблоков, а, учитывая толщины стенок корпусов, необходимые зазоры и конструктивные особенности, диаметры зубчатых колес, планетарных передач в этих условиях не превышают 310 и 410 мм соответственно. Ограничен и габарит по ширине, который определяется длиной консоли крепи, ограниченной ее несущей способностью, и регламентируемым отставанием консоли от груди забоя. Сложная гипсометрия залегания пластов приводит и к ограничению длины для обеспечения геометрической проходимости.
Случайный характер изменяющихся в широком диапазоне и определяемых физико-механическими свойствами разрушаемых пород нагрузок в основных подсистемах машин
Это требует больших перегрузочных способностей приводов и значительных запасов прочности, что весьма проблематично в стесненных условиях пластов малой и средней мощности. Проблема усугубляется формированием значительных динамических нагрузок на машины (в том числе высокие экстренные нагрузки в переходных режимах), которые наряду со специфическими условиями работы определяются невозможностью применять общепринятые методы при проектировании ряда узлов.
Значительная роль износа режущего инструмента, исполнительных органов, звездочек, тяговых органов и других элементов в формировании нагрузок и ресурса горных машин
Износ резцов выемочных машин, периодичность их замены носят случайный характер, что обуславливает случайные изменения такого важного показателя исполнительного органа как его силовой неуравновешенности, которая в значительной степени определяет нагруженность и ресурс силовых подсистем машины [1].
Остаются нерешенные вопросы достижения:
- высоких уровней безотказности (наработки на отказ) и нормативного ресурса выемочных комбайнов, конвейеров и высоконапорных агрегатов насосных станций;
- безопасных уровней вибрации и шума на рабочих местах машинистов-операторов, а также санитарных норм пылеобразования.
Проблемы повышения надежности и снижения вибрации и шума машин с высоким уровнем энерговооруженности тесно связаны между собой. Уровень виброакустических характеристик технологических машин отражает, как известно, степень их технического совершенства. По данным академика Артоболевского И.И. [2], при высоком уровне динамического качества машин, в окружающую среду поступает в виде колебательной энергии (вибрация и шум) не более 10 в -9 - 10 в -10 части общей установленной мощности при водных двигателей. На сегодня, по данным работ [3-4], эти показатели в современных горных машинах (комбайнах, конвейерах, насосных станциях) еще не достигнуты. Это является одной из основных причин снижения фактических показателей их надежности в сравнении с проектными. Высокие уровни вибрации и шума снижают также безопасность труда обслуживающего персонала.
Большое количество взаимосвязанных и взаимодействующих между собой элементов характеризуют очистной комбайн как сложную, управляемую динамическую систему. Поэтому при проектировании и создании очистных машин с высоким уровнем энерговооруженности важно учитывать динамичность процесса перемещения, разрушения и погрузки угля.
Таким образом обоснование параметров для высокопроизводительной выемки угольных пластов является сложной и многокритериальной научной задачей. Что в свою очередь предполагает изучение данного вопроса на высоком интеллектуально-информационном уровне.
2. Цель и задачи исследования, планируемые результаты
Представим в виде блок-схемы (рис.1) цель и задачи исследования с возможными вариантами путей реализации последних.
Одной из задач является повышение производительности. Эта задача может быть реализована по-разному, как показано на блок схеме:
- путем повышения энерговооруженносnи (использование индивидуальных приводов для каждого шнека и для каждого механизма перемещения);
- путем повышение коэффициента машинного времени (устранение затрат времени на маневровые операции, безнишевая выемка и применение челноковой схемы работы);
- путем полного использования установленной мощности приводов (улучшение условий питания, обеспечение рациональных режимов работы комбайна, повышения качества управления).
Решение второй задачи сводится к частичному решению третьей задачи, поэтому на блок-схеме стрелкой показана связь этих двух задач.
Решение задачи о повышении производительности немыслимо без рассмотрения вопросов повышения надежности и ресурса. Так как, например, с ростом энерговооруженности непременно возрастает нагруженность всех подсистем машины, и, в частности, динамическая нагруженность. Выходят из строя детали и узлы машин, что влечет за собой простои, связанные с устранениями отказов, соответственно коэффициент готовности снижается. Применение виброзащитных устройств резко снижает динамическую нагруженность, но с учетом правильного выбора его типа и параметров, что представляет собой сложную исследовательскую задачу с проведением ряда опытов.
.png)
Рисунок 1 – Блок схема
Таким образом решение поставленных задач позволит обосновать параметры очистного комбайна для интенсификации процесса добычи угля и повышение рентабельности работы угольного предприятия.
3. Обзор исследований и разработок
В работах [7,8,9] рассмотрены вопросы выбора и поддержания оптимальных режимов работы выемочных машин.
Регулирование становится особенно необходимым при разработке средств комплексной автоматизации и механизации, для которых осуществление оптимальных режимов, повышение надежности и долговечности является неотъемлемым требованием. Выполнение этой задачи в значительной степени зависит от динамических свойств регулируемых объектов и спектров внешних нагрузок, обусловленных физико-механическими свойствами разрушаемого массива.
В то же время, осуществляя автоматическое регулирование, т.е. воздействуя на параметры машины, изменяя режим работы в зависимости от условий эксплуатации, возможно получить наибольшую производительность, наивысшую скорость и более благоприятный режим.
Сложность задачи объясняется тем, что силы сопротивления горных пород разрушению, определяющие нагрузки во всех элементах выемочной машины и мгновенные законы их движения, представляют собой нестационарные случайные функции перемещения исполнительного органа, статистическое изучение и описание которых, необходимое для разработки систем автоматического регулирования, довольно трудоемкий процесс.
В книге [2] рассмотрены общие закономерности формирование нагрузок (в частности динамических) в элементах горных машин и их влияние на прочность и надежность.
Для всех горных машин одним из наиболее распространенных источников возмущения являются всякого рода кинематические несовершенства трансмиссии и систем, создающие неравномерность движения, и, следовательно, ускорения и динамические составляющие нагрузок. Это кинематика зубчатых и цепных передач, кинематика движения нагребающих лап, кинематическая неуравновешенность исполнительных органов комбайнов и т.д. Источником возмущения, характерным для горных машин являются также нестабильность характеристик источников энергоснабжения. Изменение уровня напряжения питания электросетей и давления в системах гидропривода приводят к изменению нагрузок на различные элементы горных машин, так, например, ток и момент на валу электродвигателя в зависимости от состояния питающей сети и напряжения могут изменяться в широких пределах.
Рабочий режим горных машин сложен, он сопровождается автоколебательными, резонансными и другими процессами в различных подсистемах этих машин.
Взаимосвязь динамических процессов, происходящих в различных подсистемах машины, создает сложную картину формирования нагрузок в этих системах, при этом нагрузки на некоторых частотах увеличиваются, вызывая перегрузки деталей и узлов.
Указанные особенности усложняют решение задач, которые выходят за пределы обычно рассматриваемых в общем машиностроении.
В работах [3,5,14,15,17,18,20,22,23,24] рассмотрены проблемы и некоторые результаты моделирования динамических процессов системы ‹‹очистной комбайн-забой››.
Для повышения технического уровня и качества сложных горных машин необходимым условием является создание научной базы их оптимального компьютерного проектирования. Эта проблема требует решения научных и практических задач по разработке и развитию математических моделей функционирования сложных технических систем, отражающих адекватно главные свойства машин и их рабочих процессов при имитационном моделировании и решении задач оптимизации.
Важными этапами разработки математических моделей (ММ) очистных комбайнов (ОК) являются проверка их адекватности реальному объекту исследования и выполнение необходимой ее калибровки. Анализ исследований, проведенных с использованием ММ ОК показал недостаточную степень адекватности данной ММ в области динамики перемещения ОК, что обусловило неадекватность соотношения дисперсий на характерных частотах некоторых динамических процессов.
В настоящее время повышение производительности очистных комбайнов влечет за собой стремительный рост энерговооруженности. Однако уже при производительности 3-6 т/мин мощность существующих приводов достигает 300 кВт и выше. Применение асинхронных короткозамкнутых электродвигателей на эту мощность требует повышения питающего их напряжения до 1140-3000 В, что приведет, к существенной реконструкции энергетического хозяйства шахты.
В свою очередь повышение мощности и быстроходности, а следовательно, и производительности горных машин сдерживается недостаточной изученностью их кинематических и динамических параметров и истинных режимов работы, фактических значений и распределений напряжений и деформаций в деталях со сложными конструктивными формами, а также ограничивается износостойкостью сопряженных деталей. Усиленный износ, появляющийся в отдельных сочленениях машин, вызывает либо необходимость снижения нагрузок, приходящихся на отдельные элементы, что приводит к увеличению габаритов и веса машин, либо к резкому удорожанию за счет применения в технологии изготовления деталей и узлов машин наноматериалов и нанотехнологий.
Таким образом правильное определение динамических параметров и характеристики машины и обеспечение их в реальной машине в конечном итоге существенно скажется на ее работоспособности, надежности, долговечности и стоимости.
4. Исследование динамических свойств регулируемого объёмного гидропривода механизмов перемещения очистных комбайнов
В настоящее время в угольной отрасли Украины и странах, имеющих запасы угля, все более насущными становятся вопросы создания наиболее перспективных средств механизации угольных пластов.
Выемочные комбайны проектируются под высокую теоретическую производительность, реализация которой становится возможной при автоматизации их работы. В выемочных машинах в первую очередь должно применяться автоматическое плавное регулирование скорости подачи в зависимости от нагрузки двигателя. В качестве объекта регулирования используется механизм подачи на основе объемного гидропривода.
Схема автоматического регулирования скорости подачи "Эйкоматик" имеет вид представленный на рис. 2, где
1- трансформатор тока; 2- устройство сравнения; 3- задатчик тока;4- усилитель; 5- задатчик скорости; 6- гидравлический усилитель; 7- гидравлический установочный прибор; 8- гидравлический серводвигатель; 9- главный электродвигатель; 10- исполнительный орган; 11- подпиточный насос; 12- гидронасос; 13- гидродвигатель подачи; 14- ведущая звезда.
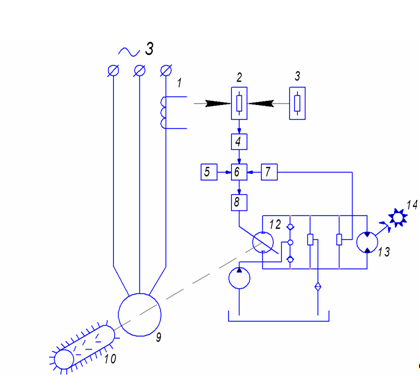
Рисунок 2 – Схема автоматического регулирования скорости подачи «Эйкоматик» (ФРГ)
В подсистемах механизмов перемещения (ПМП) очистных комбайнов с упругим (ЦСП) и жестким (БСП) тяговым органом находит широкое применение регулируемый объемный гидропривод. Обычно регулируемым параметром является переменный эксцентриситет радиально-плунжерного насоса или угол наклона диска аксиально-плунжерного насоса.
На рис.3 показаны принципиальная (а), расчетная (б) и структурная (в) схемы объемного гидропривода ПМП ОК.
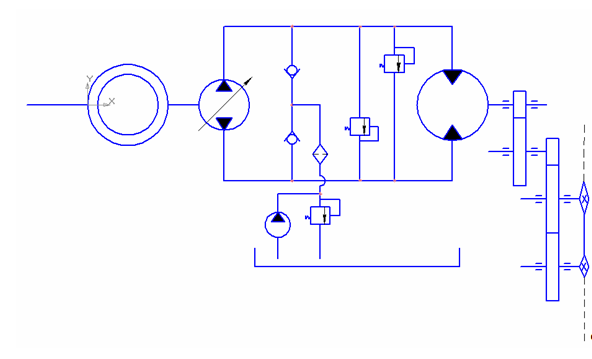
а)
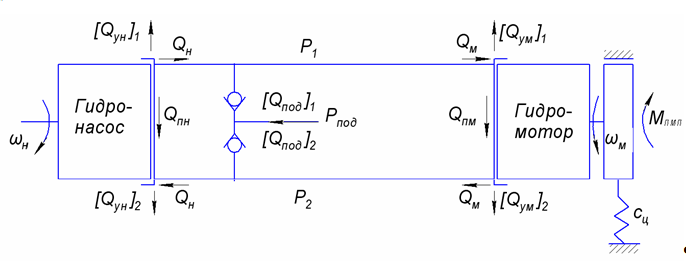
б)
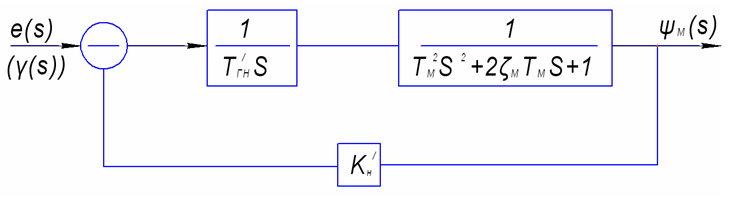
в)
Рисунок 3 - Принципиальная (а), расчетная (б) и структурная (в) схемы гидропривода ПМП
Зависимость скорости установившегося движения ненагруженного гидропривода от величины параметра регулирования статической скоростной характеристикой (или характеристикой регулирования скорости объемного гидропривода):

где Qн - теоретическая подача насоса; qгм - рабочий объем гидромотора;
Отношение рабочих объемов насоса и гидромотора (гидравлическое передаточное число гидропередачи):
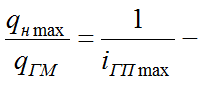
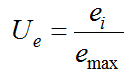
Для гидромотора с реверсируемым потоком жидкости

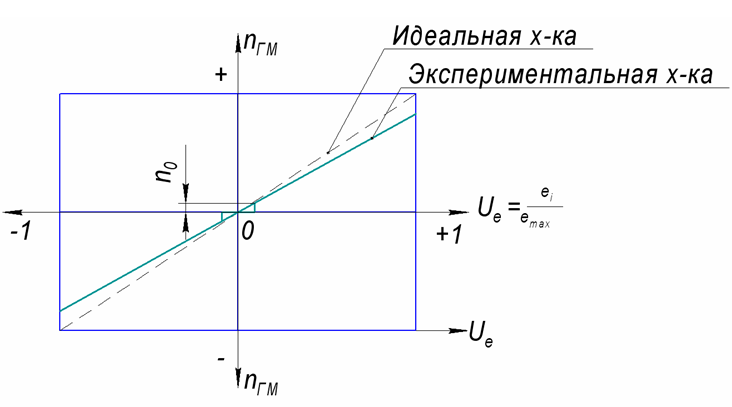
Рисунок 4 – Скоростная характеристика объемного гидропривода
На рис.4 через n0 обозначена минимальная устойчивая скорость гидромотора. Она обусловлена сжимаемостью и утечками жидкости, инерцией ротора и автоколебаниями в гидромоторе на "ползучих" скоростях, при «падающей» зависимости трения от скорости (разность между трением покоя и движения в поршневых группах и других элементах гидромотора). Таким образом, строго говоря, скоростная характеристика - нелинейная, однако зона ползучих скоростей (0-n0) не является рабочей, см. рис. 4.
Статическая механическая характеристика регулируемой гидропередачи показывает зависимость между скоростью вращения гидромотора и моментом его нагрузки при различных значениях параметра регулирования Ue, рис. 5.
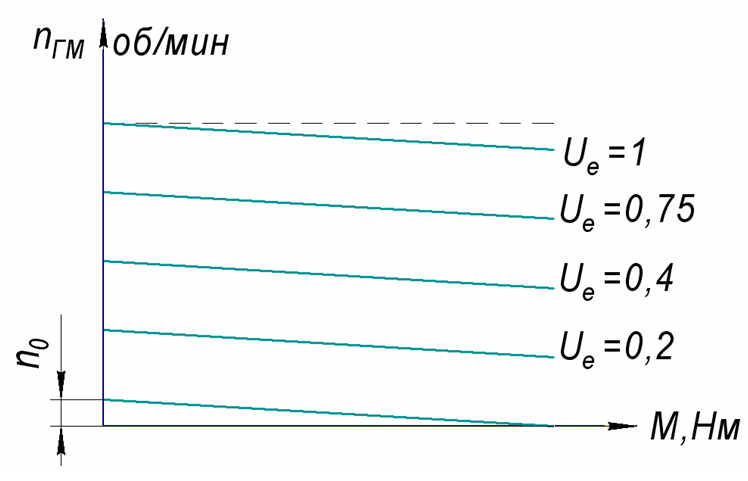
Рисунок 5 - Механическая характеристика объемной гидропередачи

или

где ан,агм - коэффициенты утечек в насосе и гидромоторе; Р=Р1-Р2 - перепад давления на гидромоторе; М и Км - момент гидромотора и коэффициент момента.
Уравнение нагрузки гидромотора механизма подачи МП очистного комбайна при
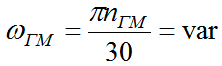

Оно соответствует режимам с ускоренным и замедленным вращением гидромотора.
где (Р1-Р2)qгм - момент гидромотора; Iгм - момент инерции гидромотора; m - масса комбайна; r - радиус ведущей звезды; i - передаточное число редуктора МП; Mcмп - момент сопротивления.
Уравнение движения комбайна можно представить в виде
где mx - сила инерции; Сц - коэффициент жесткости цепи (тягового органа); (rф-x) - упругая деформация тягового органа; Fтр - сила трения; Fпx - проекция на ось Х полезных сил сопротивления (резания и подачи); mg sin(a) - продольная составляющая силы тяжести комбайна в пласт с углом наклона a.
Момент сил сопротивления на валу гидромотора можно записать в виде:

Для гидрообъемной передачи и гидромотора нагрузку (момент) на его валу можно рассматривать как внешнее возмущение, действующее на «входе» в ПМП ОК.
Как известно [1,2], что даже при отсутствии полезной нагрузки на ИО комбайна, т.е. Fпx=0, момент Мспм, формирующийся на валу гидромотора, можно считать случайной функцией, так как, при изменяющемся случайным образом коэффициенте трения в опорах комбайна, кинетическая характеристика трения является стохастической не зависимо от жесткости тягового органа.
Общая закономерность падающей зависимости силы трения от скорости скольжения сохраняется, однако численные значения функции кинетической характеристике трения при одних и тех же значениях аргумента могут изменяться. Следует также отметить, что система «комбайн - конвейер - тяговый орган», является системой с переменным упругим параметром: с перемещением комбайна непрерывно изменяется длина рабочего участка тягового органа, а следовательно, и коэффициент жесткости, что приводит к изменению собственной частоты колебаний системы, см. рис.6.
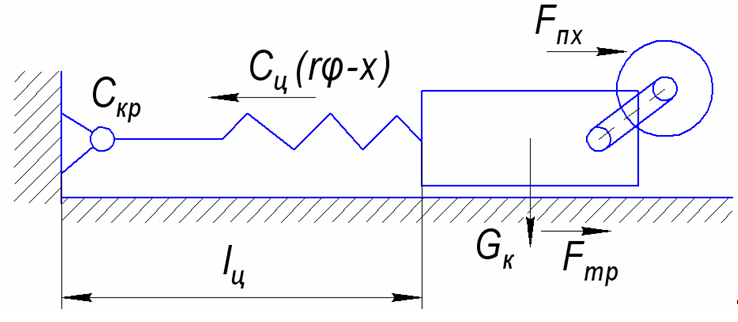
Рисунок 6 – Динамическая модель процесса перемещения ОК
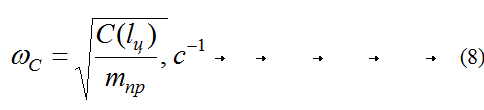

- коэффициент жесткости системы, зависит от длины тягового органа и жесткости узла крепления к головке конвейера рабочей ветви цепи.
Так, например, для комбайна 1ГШ-68 с Gк=14500 кг; Cц=5100000 кг/м; q=13,6 кг/м; Cкр=1000000 кг/м зависимость wс=(С(lц)/mпр)^1/2, графически можно представить в виде падающей кривой при увеличении длины цепи, рис.7.
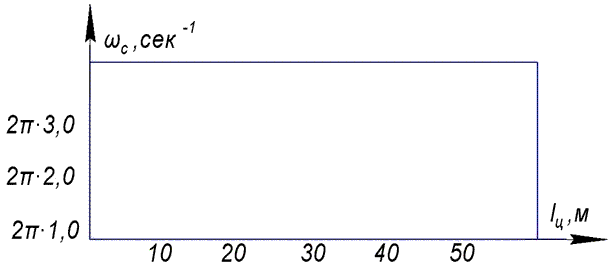
Рисунок 7 – Зависимость собственной частоты ОК от длины цепи
Таким образом, частота автоколебаний скорости подачи и момента изменяются в зависимости от длины рабочего участка тягового органа.
Составляющая суммарного момента сил сопротивления на валу гидромотора

где a и b - коэффициенты, отражающие конструктивные особенности ИО; т - время запаздывания.
Fпx*r соответствует процессу резания угля и имеет, как известно, явно стохастический характер. Таким образом, нагрузка на входе гидромотора должна описываться вероятностными характеристиками, одной из которых является спектральная плотность нагрузки:

Согласно теории случайных функций и статистической динамики линейных систем, спектральная плотность нагрузки на выходе (в данном случае в гидронасосе):

где W(jw) - частотная характеристика системы «насос - гидромотор - движитель ОК».
Следовательно, дисперсия нагрузки в гидроприводе, характеризующая амплитуду переменной составляющей выходного параметра (например, давления) может быть вычислена по формуле:

Таким образом, динамические нагрузки в системе объемного гидропривода ПМП определяются не только внешним воздействием, но и в значительной степени динамическими свойствами привода, т.е. его амплитудно-частотными характеристиками.
Иными словами, соотношение между амплитудой колебаний давления в системе «насос-гидромотор» МП и амплитудой периодических составляющих момента нагрузки на валу гидромотора (ведущей звезды движителя) зависит от частоты нагрузки.
Выводы и направления дальнейших исследований
На основании изложенного материала применительно к задачам магистерской работы можно сделать следующие выводы:
- при исследовании путей повышения производительности очистного комбайна необходимо отдать предпочтение рассмотрению вопросов о повышении качества управления и обеспечению рациональных режимов работы, что повлечет за собой полное использование установленной мощности приводов;
- при исследовании динамической системы, отражающей неравномерность процесса перемещения необходимо рассмотреть вопросы демпфирования гидравлических опор комбайна, а также возможность применения в технологическом цикле фронтальной передвижки секций крепи;
- при исследовании динамической нагруженности основной особенностью привода режущей части современных машин является наличие двух основных масс, расположенных по концам трансмиссии привода - это маховая масса ротора электродвигателя и масса исполнительного органа. Причем в большинстве случаев масса последнего меньше массы ротора электродвигателя, но больше приводной массы любого промежуточного элемента трансмиссии. Поэтому основными определяющими колебаниями в трансмиссии привода режущей части при изучении формирования нагрузок рабочего режима будут колебания массы исполнительного органа вокруг массы ротора электродвигателя с податливостью, равной податливости всей трансмиссии.
Последнее необходимо учитывать при рассмотрении вопросов долговечности и повышении коэффициента готовности.
При написании данного реферата магистерская работа еще не завершена. Окончательное завершение: декабрь 2012 года. Полный текст работы и материалы по теме могут быть получены у автора или его руководителя после указанной даты.
Список источников
- Гуляев В.Г. Проектирование и конструирование горных машин и комплексов. Часть 1. Выемочные комбайны //ГВУЗ "ДонНТУ", Технопарк ДонНТУ "УНИТЕХ", 2011.-322с.
- Докунин А.В., Красников Ю.Д., Хургин З.Я. Статистическая динамика горных машин //М.: Машиностроение, 1978.-239с.
- Динамические процессы горных машин /А.В. Докунин, Ю.Д. Красников, З.Я. Хургин и др. //М.: Наука, 1972.-150с.
- Коваль П.В. Гидропривод горных машин. //М.: Недра, 1967.-387с.
- Верескунов З.Н., Фастовец Н.И. О динамических характеристиках привода добычных комбайнов с бесцепным механизмом подачи. /В сб.: "Совершенствование и повышение надежности горных машин и средств автоматизации" (Научные сообщения, вып.184), М.: ИГД им. А.А. Скочинского, 1980.
- Докукин А.В., Фролов А.Г., Позин Е.З. Выбор параметров выемочных машин. М.: Наука, 1976, 144 с.
- Позин Е.З, Меламед В.З. О параметрах выемочных комбайнов. Уголь, М.: Недра, 1980, №11, с. 31-34.
- Берон А.И., Позин Е.З. Принципы выбора и поддержания оптимальных режимов работы исполнительных органов угледобывающих машин. - В кн. Горнорудные машины и автоматика, М., Недра, 1965, вып.1, с. 18 - 44.
- Выравнивание скорости перемещения добычных комбайнов при помощи динамического гасителя колебаний. / Авт. Г.В. Малеев, В.Г. Гуляев, Н.Г. Бойко, А.К. Семенченко. - Известия вузов. Горный журнал, 1972, №5, с. 92-96.
- Гуляев В.Г., Сивокобыленко В.Ф., Жуков К.В. Математическая модель двухдвигательного привода исполнительного органа очистного комбайна. //Тр. Донец. гос. тех. ун-та. Серия: горно-электромеханическая; Вып. 7. - Донецк, 1999.- С. 97-102.
- Гуляев В.Г., Жуков К.В. Определение кинематической характеристики трения очистного комбайна с цепным тяговым органом // Наук. вісн. нац. гірн. акад. України. - 1999.- №2.- С.54-57.
- Гуляев В.Г., Жуков К.В. Математическая модель для имитационного моделирования функционирования системы ‹‹очистной комбайн-забой›› // Горн. информ.-аналит. бюл.- М., 2000.- №4.- С.129-131.
- Гуляев В.Г., Жуков К.В. Некоторые результаты имитационного моделирования функционирования системы ‹‹очистной комбайн-забой›› // Наук. пр. Донец. держ. техн. ун-ту. Серія: гірничо-електромеханічна. Вип. 16.- Донецьк, 2000.- С.84-91.
- Гуляев В.Г., Жуков К.В. Результаты прогнозирования эксплуатационных и динамических характеристик очистного комбайна с высоким уровнем енерговооруженности // Вибрация в технике и технологиях.- 2001.- №3.- С.32-35.
- Гуляев В.Г., Жуков К.В. Имитационное моделирование рабочего процесса и обоснование параметров очистного комбайна нового технического уровня // Донбас-2020: наука і техніка - виробництву: Матеріали наук.-практ. конф., 5-6 лютого 2002 р., м. Донецьк / Донец. нац. техн. ун-т.- Донецьк, 2002.- С.156-161.
- Гуляев В.Г., Косарев В.В. Состояние и проблемы комплексной механизации при разработке пологонаклонных угольных пластов Донецкого бассейна // MATERIALY SZKOLY ECSPLOATACJI PODZIEMNEJ 2002. FORUM Polsko-Ukrainskie Szczyrk, 18-22 lutego 2002. Seria Wyklady nr21.- Krakow, 2002.- S.19-25.
- Гуляев В.Г. Исследование и учет взаимодействия силовых подсистем комбайна при разработке математических моделей системы ‹‹очистной комбайн-забой›› // Горная энергомеханика и автоматика: Тр. междунар. науч.-техн. конф.- Донецк, 2003.- Том 2.- С.73-79.
- Гуляев В.Г., Жуков К.В. Метод формирования математической модели функционирования системы ‹‹очистной комбайн-забой›› // Зб. наук. пр. НДІГМ ім. М.М. Федорова.- Донецьк, 2003.- Вып.96.- С.179-186.
- Гуляев В.Г, Потапов В.Г., Мотин Н.Н. Математические модели приводных асинхронных двигателей для исследования динамических свойств горных машин // Науч. тр. Донец. нац. техн. ун-та. Серия: горно-электромеханическая. Вып.99.- Донецк, 2005.- С.62-70.
- Васильев А.Ю., Гуляев В.Г Передаточные функции объёмного гидропривода механизмов подачи очистных комбайнов // Автоматизація технологічних об'єктів та процесів: Зб. наук. пр. V-й міжн. наук.-техн. конф., 16-19 травня 2005 р., м. Донецьк.- Донецьк,2005.- С.104-106.
- Кондрахин В.П., Гуляев В.Г., Головин В.Л. Имитационная математическая модель динамических процессов очистных комбайнов высокой энерговооруженности с вынесенной системой подачи / Наукові праці донецького національного технічного університету. Випуск 12 (113). Серія гірничо-електромеханічна. Донецьк,2006.- С.123-130.
- Guljaew W.G. Optimirung der dynamischen Eigenschaften von Bergbaumaschinen mit dem Ziel der Erhohung ihrer Zuverlassigkeit und Leistungfahigkeit: Vortrag auf wissenschaftlichen Kollogviums technische Hochschule Otto von Guericke.- 1981-24 s.
- Guljaew W.G. Untersuchung und Optimirung der dinamischen Eigenschaften von Bergbaukombines mit dem Ziel der Erhohung ihrer Zuverlassigkeit, Lebensdauer und Leistungfahigkeit. Magdeburg (DDR) // TECHNISCHE MECHANIK.- 1982.- N3, H1.- S.18-27. ...